Top 12 Welder Skills to Put on Your Resume
In today’s competitive job market, having a standout resume is crucial for welders aiming to secure their desired positions. Highlighting the top 12 welder skills on your resume not only showcases your expertise and adaptability in the field but also sets you apart as a highly qualified candidate in the eyes of potential employers.
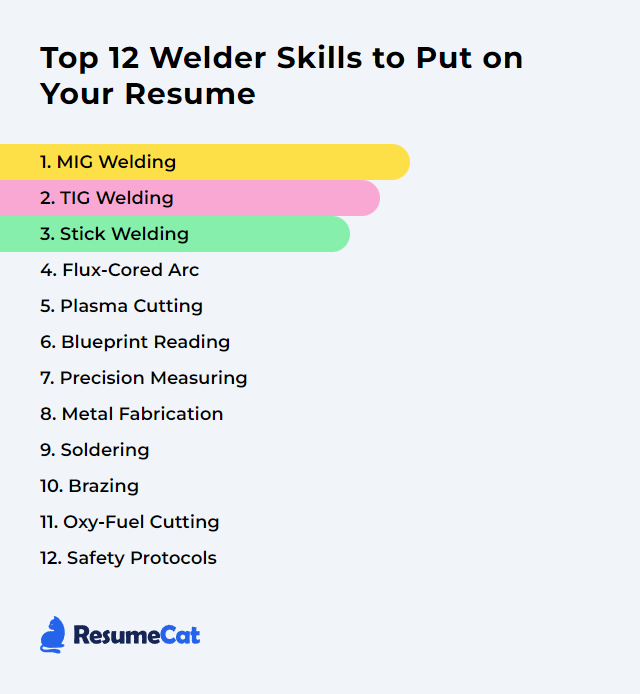
Welder Skills
- MIG Welding
- TIG Welding
- Stick Welding
- Flux-Cored Arc
- Plasma Cutting
- Blueprint Reading
- Precision Measuring
- Metal Fabrication
- Soldering
- Brazing
- Oxy-Fuel Cutting
- Safety Protocols
1. MIG Welding
MIG Welding, or Metal Inert Gas Welding, is a welding process where a continuous solid wire electrode is fed through a welding gun and into the weld pool, joining two base materials together. A shielding gas is also expelled from the gun to protect the weld pool from contamination. It's widely used for its speed, versatility, and ease of use.
Why It's Important
MIG welding is important for welders because it allows for versatile, efficient, and relatively easy welding of a wide range of materials with high-quality, strong welds, making it suitable for both beginner and advanced welding applications.
How to Improve MIG Welding Skills
To improve MIG welding, follow these concise tips:
- Settings Adjustment: Properly adjust your welder settings including voltage and wire feed speed for material thickness. Miller Welds offers a comprehensive guide.
- Correct Gas and Material: Use the right shielding gas and wire type for your project. Lincoln Electric provides insights on choices.
- Maintain Cleanliness: Ensure your base metal is clean and free from contaminants. Welding Tips and Tricks emphasizes its importance.
- Proper Technique: Maintain a consistent travel speed and angle. Hobart Brothers offers technique improvement tips.
- Regular Equipment Check: Regularly inspect and maintain your welding equipment. ESAB provides maintenance advice.
By focusing on these areas, you can significantly improve your MIG welding quality and efficiency.
How to Display MIG Welding Skills on Your Resume
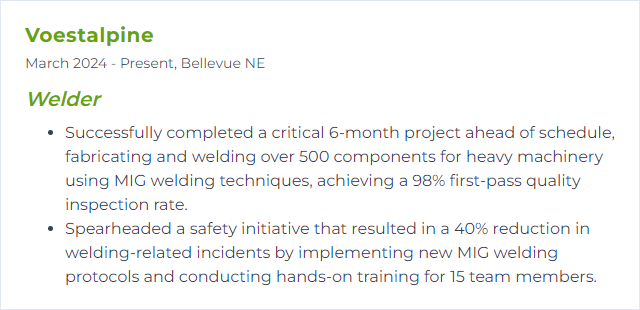
2. TIG Welding
TIG welding, or Tungsten Inert Gas welding, is a precise arc welding process that uses a non-consumable tungsten electrode to produce the weld. It involves using an inert gas, typically argon, to shield the weld area from contamination. This method allows for strong, high-quality welds on a variety of metals, offering great control over the weld.
Why It's Important
TIG welding is important for a welder because it allows for precise, high-quality welds on a variety of metals, including thin materials and alloys, enabling versatility and craftsmanship in welding projects.
How to Improve TIG Welding Skills
Improving TIG welding involves practice, precision, and understanding the fundamentals of the process. Here are concise tips along with external links for in-depth learning:
Understand the Basics: Start with a strong foundation by understanding TIG welding principles. Miller Welds provides a comprehensive guide.
Select the Right Equipment: Use the appropriate tungsten electrode and filler material. Welding Tips and Tricks offers advice on equipment selection.
Control Heat Input: Mastering heat control is crucial. Practice maintaining a consistent arc length. Lincoln Electric has tips on heat management.
Improve Hand Stability: Develop a comfortable and stable hand position. Practice can be guided by techniques from The Fabricator.
Cleanliness is Key: Ensure your base metal and filler rod are clean. American Welding Society highlights the importance of cleanliness.
Practice Different Positions: Work on welding in various positions to increase versatility. Weld Guru breaks down the welding positions and tips for each.
Analyze Your Work: Regularly inspect your welds for consistency and defects. Learning from mistakes improves skills.
Seek Feedback: Join forums or groups like WeldingWeb to share your work and get advice from experienced welders.
Remember, consistent practice and learning from every weld are key to improvement in TIG welding.
How to Display TIG Welding Skills on Your Resume
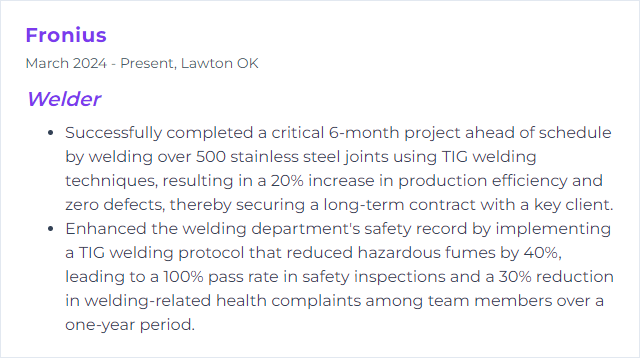
3. Stick Welding
Stick welding, also known as Shielded Metal Arc Welding (SMAW), is a manual welding process that uses a consumable electrode coated in flux to lay the weld. An electric current forms an arc between the electrode and the metals to be joined, melting the metals and the electrode to form a strong weld.
Why It's Important
Stick welding is important for welders because it is versatile, allowing for welding in various positions and environments, including outdoors or in windy conditions. It is also effective on dirty or rusty metals, making it valuable for maintenance, repair, and construction work.
How to Improve Stick Welding Skills
To improve your stick welding skills, follow these concise tips:
Choose the Right Electrode: Match the electrode type to the welding position and the material being welded. American Welding Society provides guidelines on electrode selection.
Correct Amperage Setting: Adjust your welder's amperage based on the electrode's diameter and the thickness of the material. Refer to the electrode's specifications for guidance.
Proper Angle and Movement: Hold the electrode at about a 15-degree angle in the direction of the weld. Move steadily and at a consistent speed. Lincoln Electric offers detailed tips on technique.
Clean the Work Surface: Ensure the surface to be welded is clean and free of rust, paint, or dirt. This improves weld quality significantly.
Practice Consistently: Stick welding requires skill and precision, which come with practice. Regular practice on scrap metal can help hone your skills.
Safety First: Always wear appropriate safety gear, including a helmet, gloves, and protective clothing. OSHA provides safety guidelines for welding.
By focusing on these areas and consistently practicing, you can significantly improve your stick welding skills.
How to Display Stick Welding Skills on Your Resume
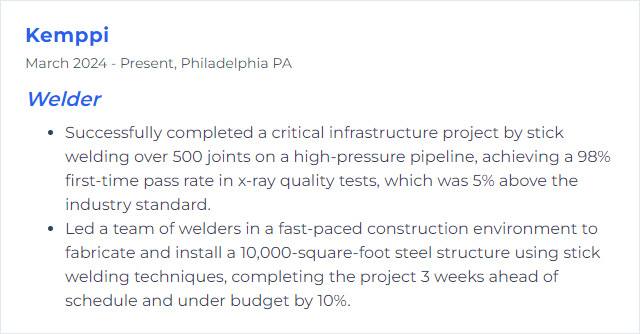
4. Flux-Cored Arc
Flux-Cored Arc Welding (FCAW) is a semi-automatic or automatic arc welding process using a continuously fed consumable tubular electrode filled with a flux. It is used for welding thick materials in a variety of positions and environments.
Why It's Important
Flux-Cored Arc Welding (FCAW) is important for welders because it allows for high deposition rates, excellent penetration, and versatility in welding various materials, including thick and out-of-position work, enhancing productivity and quality in diverse welding applications.
How to Improve Flux-Cored Arc Skills
To improve Flux-Cored Arc Welding (FCAW), focus on these key points:
Equipment Maintenance: Regularly inspect and maintain your welding equipment. Ensure the drive rolls and liner are suitable for the diameter of wire being used.
Proper Technique: Maintain a steady gun angle, typically between 15 and 45 degrees. Adjust your travel speed to ensure the weld bead is correctly formed.
Wire Selection: Use the appropriate wire type and diameter for your application. E71T-1 is commonly used for flat, horizontal, overhead, and vertical-up positions.
Shielding Gas: For dual shield flux-cored welding, select the correct type of shielding gas, typically a mix of 75% Argon and 25% CO2, to optimize weld quality and minimize spatter.
Correct Parameters: Set the right voltage, amperage, and wire feed speed for your specific welding situation. Consult the wire’s specification sheet for guidance.
Cleanliness: Ensure the workpiece is clean and free of rust, oil, and dirt. Proper preparation can significantly reduce defects.
For in-depth techniques and tips:
By adhering to these guidelines, you can enhance your FCAW process for better, more consistent welds.
How to Display Flux-Cored Arc Skills on Your Resume
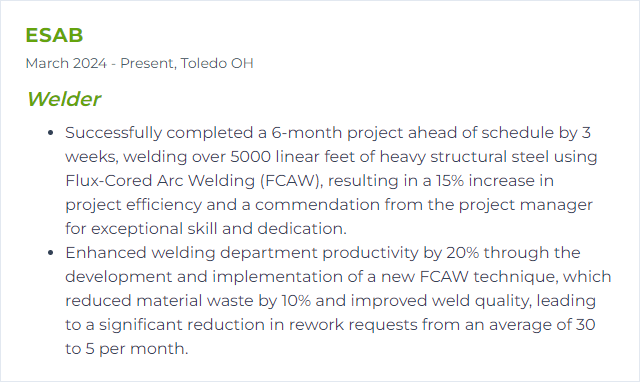
5. Plasma Cutting
Plasma cutting is a process used by welders to cut through electrically conductive materials by utilizing a jet of hot plasma. This method is effective for cutting steel, stainless steel, aluminum, brass, and copper, offering high speed and precision with minimal distortion.
Why It's Important
Plasma cutting is important for welders because it allows for precise, efficient, and fast cutting of conductive metals, facilitating the preparation and fabrication of materials for welding projects with minimal thermal distortion.
How to Improve Plasma Cutting Skills
Improving plasma cutting involves enhancing precision, speed, and safety. Follow these concise tips:
Maintain Equipment: Regularly check and replace worn components. Hypertherm's maintenance tips offer guidance on keeping your system in top condition.
Choose the Right Consumables: Select the appropriate consumables for the material and thickness. Lincoln Electric provides insights on choosing consumables for optimal performance.
Proper Torch Height: Maintain the correct distance between the torch and the workpiece. ESAB's cutting guide explains the importance of torch height control.
Optimize Cutting Speed: Adjust speed for the material and thickness to reduce dross and improve cut quality. Miller's guide on plasma cutting provides strategies for speed adjustments.
Use a Guide: For straight cuts, use a guide or CNC table for enhanced accuracy. CNC Plasma Cutting Systems by Hypertherm offer advanced precision.
Safety First: Always wear appropriate safety gear and follow safety guidelines. OSHA's Welding, Cutting, and Brazing guidelines cover important safety practices.
By focusing on these areas, welders can achieve cleaner cuts, faster processing times, and safer working conditions.
How to Display Plasma Cutting Skills on Your Resume
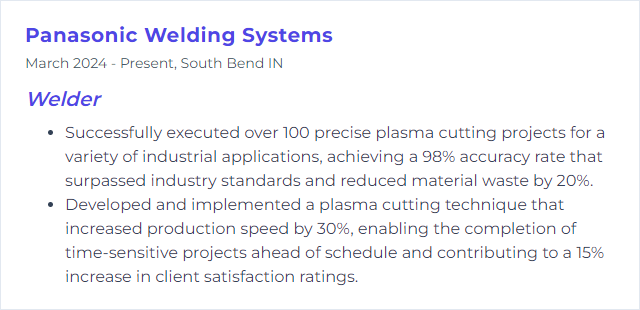
6. Blueprint Reading
Blueprint reading for a welder involves understanding and interpreting detailed technical drawings and schematics that specify the dimensions, welding symbols, materials, and processes required to fabricate and assemble metal components and structures.
Why It's Important
Blueprint reading is crucial for welders as it enables them to understand detailed technical drawings, ensuring accurate fabrication and assembly of metal components according to specified designs and dimensions.
How to Improve Blueprint Reading Skills
Improving blueprint reading for a welder involves developing a keen understanding of symbols, dimensions, and specifications used in welding blueprints. Here's a concise guide to enhance your skills:
Understand Welding Symbols: Familiarize yourself with the basic and advanced welding symbols as they are the primary language of a blueprint. American Welding Society (AWS) offers resources and standards on welding symbols.
Learn Basic Drafting Techniques: Grasping the fundamentals of drafting can help you understand the perspectives and dimensions in blueprints. Online courses on platforms like Coursera or Udemy can be a good start.
Practice Reading Blueprints: Practice is key. Use online resources or textbooks that contain sample blueprints. Websites like Lincoln Electric provide practical examples and exercises.
Take a Course: Consider enrolling in a blueprint reading course specific to welding. Community colleges or technical schools often offer such courses. Online platforms like American Welding Society also provide relevant courses.
Use Software Tools: Familiarize yourself with CAD (Computer-Aided Design) software commonly used in the industry, as modern blueprints are often digital. Tutorials on software like AutoCAD from Autodesk can be beneficial.
Improving blueprint reading skills is a continuous process that combines learning with practical application.
How to Display Blueprint Reading Skills on Your Resume

7. Precision Measuring
Precision measuring for a welder involves using specialized tools (such as calipers, micrometers, and gauges) to accurately determine the dimensions and tolerances of materials before, during, and after welding, ensuring that weldments meet specified standards and fitment requirements.
Why It's Important
Precision measuring is crucial for a welder to ensure that welded components fit accurately, meet specified dimensions, maintain structural integrity, and achieve desired aesthetics, thereby guaranteeing the safety, functionality, and quality of the final product.
How to Improve Precision Measuring Skills
Improving precision measuring in welding involves enhancing accuracy and consistency in measurements to ensure weld quality and compliance with specifications. Here are concise steps with resources:
Use the Right Tools: Select high-quality, appropriate measuring instruments like calipers, micrometers, and angle finders. Regularly calibrate tools for accuracy. Mitutoyo offers a range of precision instruments.
Understand Measurement Techniques: Learn proper techniques for using measuring tools. This includes knowing how to read scales correctly and positioning tools for accurate readings. Miller Welds provides insights on welding and measurements.
Regular Calibration: Ensure measuring tools are regularly calibrated according to the manufacturer's recommendations or industry standards. NIST offers guidelines on calibration standards.
Practice Consistency: Use the same measuring tools and methods to maintain consistency across measurements. Consistent practices lead to more reliable results.
Educational Resources: Engage with educational content and training programs to stay updated on best practices in precision measuring. American Welding Society (AWS) offers resources and courses for welders.
Quality Control Checks: Implement routine quality control checks to monitor and adjust processes as needed, ensuring continuous improvement in precision measuring.
Improving precision in welding measurements is a combination of using the right tools, applying correct techniques, and ongoing education.
How to Display Precision Measuring Skills on Your Resume
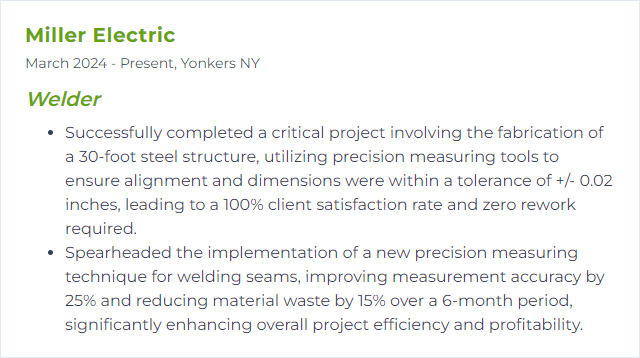
8. Metal Fabrication
Metal fabrication is the process of cutting, shaping, and assembling metal structures or parts, often involving welding, to create final products or components.
Why It's Important
Metal fabrication is crucial for a welder as it involves the cutting, bending, and assembling of metals to create structures or components, enabling the welder to construct or repair a wide variety of items with precision and strength, from industrial machinery to everyday products.
How to Improve Metal Fabrication Skills
To improve metal fabrication, a welder can focus on:
Enhancing Skills: Continuously updating and refining welding techniques through courses and certifications from reputable organizations like the American Welding Society (AWS).
Using Advanced Equipment: Invest in high-quality, modern welding equipment and tools for better precision and efficiency. Researching options through industry-leading suppliers like Lincoln Electric can provide insights.
Implementing Quality Control: Adopting rigorous quality control measures, including pre-welding inspections and post-welding testing. Guidelines and standards can be found through ASTM International.
Adopting New Technologies: Staying abreast of the latest technologies in metal fabrication, such as laser welding or friction stir welding, to increase capabilities. Resources and updates can be found on The Fabricator.
Focusing on Safety: Prioritizing workplace safety by following recommended practices and using protective gear. Comprehensive safety standards and tips are available on OSHA’s Welding, Cutting, and Brazing page.
By focusing on these areas, welders can significantly improve the quality, efficiency, and safety of their metal fabrication projects.
How to Display Metal Fabrication Skills on Your Resume
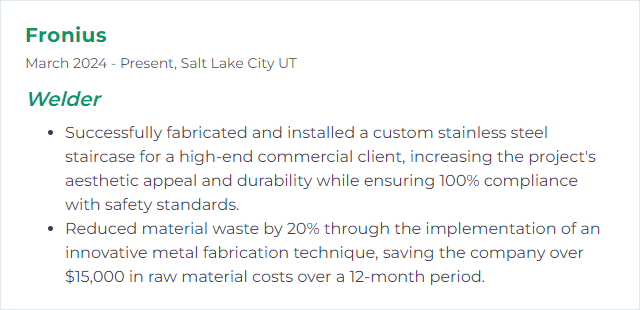
9. Soldering
Soldering is a process of joining two or more metal items by melting and flowing a filler metal (solder) into the joint, which has a lower melting point than the workpieces. Unlike welding, soldering does not melt the workpieces themselves.
Why It's Important
Soldering is important for a welder as it allows for precise, low-temperature bonding of smaller or delicate components, such as electronics or thin metals, where traditional high-heat welding could cause damage or distortion.
How to Improve Soldering Skills
Improving soldering skills involves practice, the right tools, and understanding the materials. Here are succinct tips:
Use Quality Solder and Flux: High-quality solder and flux make for better joints. Flux cleans the metal surfaces and improves solder flow.
Proper Iron Temperature: Ensure your soldering iron is at the correct temperature for the solder you are using. Too hot can damage components, too cold can lead to poor joints.
Clean Tip: Keep the soldering iron tip clean using a wet sponge or brass tip cleaner. A clean tip improves heat transfer and solder flow.
Proper Soldering Technique: Heat the joint, not the solder, and apply solder to the joint. This ensures the components are hot enough for the solder to flow properly.
Practice: Like any skill, practice improves performance. Start with simple projects and progress to more complex ones.
Resources for further improvement:
- Adafruit Guide to Excellent Soldering for basics and tips.
- NASA Soldering Standards provides insights into high-quality soldering standards.
- EEVblog Soldering Tutorial on YouTube for visual learning through tutorials.
Focusing on these aspects will significantly improve your soldering skills.
How to Display Soldering Skills on Your Resume
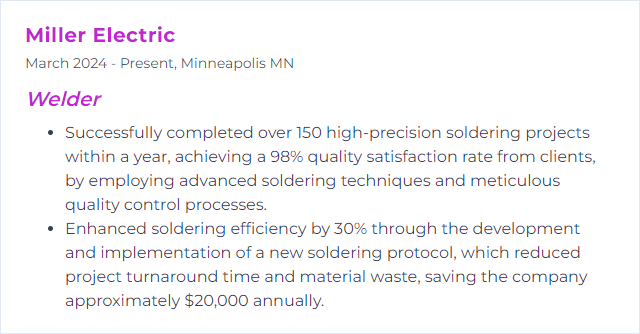
10. Brazing
Brazing is a metal-joining process where a filler metal with a lower melting point than the base metals is melted and drawn into the joint by capillary action to bond the pieces without melting them.
Why It's Important
Brazing is important for a welder because it allows for the joining of different metals at lower temperatures without melting the base materials, ensuring strong, sealed joints with minimal thermal distortion and maintaining the integrity of the components being joined.
How to Improve Brazing Skills
Improving brazing involves focusing on preparation, material selection, and technique. Here are concise steps with inline links to enhance your brazing process:
Clean Surfaces: Ensure surfaces to be brazed are clean and free of oils, grease, or oxides. Use a suitable cleaning method such as brushing, grinding, or using a chemical cleaner. Cleaning for Brazing
Proper Fit and Fixturing: Maintain a close fit between the parts to be brazed, typically 0.001-0.003 inches. Use fixtures to hold parts in alignment during the brazing process. Brazing Fundamentals
Correct Filler Material: Choose a filler material compatible with the base metals and suitable for the service conditions. The melting point of the filler metal should be lower than that of the base metals. Filler Metal Selection
Proper Heat Application: Apply heat evenly to both the base metals and the filler metal. The heat source could be a torch, furnace, or induction heating, depending on the application. Brazing Techniques
Use of Flux: If required, apply flux to prevent oxidation during heating. The choice of flux depends on the metals being joined and the brazing environment. Understanding Flux
Cooling and Cleaning: Allow the brazed joint to cool naturally. Avoid rapid cooling techniques that can induce thermal stresses. After cooling, clean the joint to remove any flux residue. Post-Braze Cleaning
Inspection: Inspect the brazed joint for quality assurance, checking for complete filler metal flow, absence of voids, and ensuring joint strength. Brazing Inspection
Adhering to these steps can significantly improve the quality and consistency of your brazing operations.
How to Display Brazing Skills on Your Resume
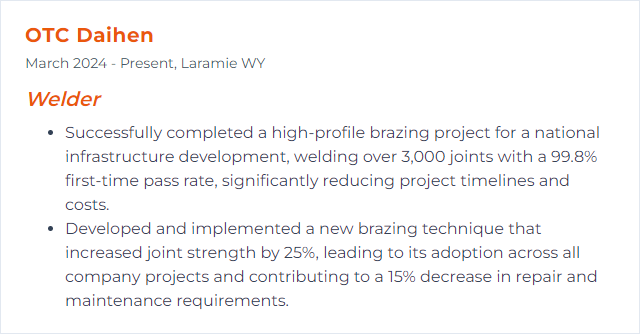
11. Oxy-Fuel Cutting
Oxy-fuel cutting is a process used by welders that involves the use of oxygen and a fuel gas (like acetylene) to generate a flame hot enough to melt and cut through metals.
Why It's Important
Oxy-fuel cutting is important for a welder because it efficiently cuts through thick metals, prepares edges for welding, and performs demolition or dismantling tasks, using a portable and versatile tool.
How to Improve Oxy-Fuel Cutting Skills
Improving Oxy-Fuel Cutting involves a combination of equipment maintenance, technique refinement, and safety considerations. Here are concise tips:
Use Proper Equipment: Ensure your cutting torch and tips are appropriate for the material thickness American Welding Society.
Regular Maintenance: Clean and inspect your equipment regularly, focusing on nozzles and hoses for any signs of wear or blockage Lincoln Electric.
Correct Gas Pressures and Mix: Adjust oxygen and fuel gas pressures according to the manufacturer's recommendations for the material thickness Harris Products Group.
Optimal Speed: Move the torch at a speed that ensures a continuous, smooth cut, avoiding too slow or too fast movements that affect cut quality Miller Welds.
Preheat Properly: A uniform preheat flame around the cutting area helps in efficient and clean cuts, especially for thicker materials ESAB.
Practice Safety: Always wear appropriate safety gear and work in a well-ventilated area to avoid inhaling fumes Occupational Safety and Health Administration (OSHA).
Continuous Learning: Stay updated with the latest techniques and safety standards by engaging in workshops and training sessions American Welding Society Education.
By focusing on these areas, welders can significantly improve their oxy-fuel cutting performance and safety.
How to Display Oxy-Fuel Cutting Skills on Your Resume
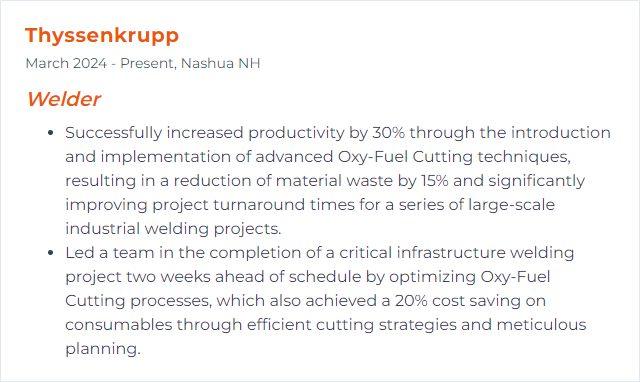
12. Safety Protocols
Safety protocols for a welder include wearing appropriate personal protective equipment (PPE) such as helmets with visors, gloves, and fire-resistant clothing, ensuring proper ventilation to avoid inhaling harmful fumes, following guidelines for handling and storing flammable materials, and using welding equipment correctly to prevent accidents and injuries.
Why It's Important
Safety protocols are crucial for welders to prevent accidents, minimize exposure to harmful fumes and radiation, ensure proper use of equipment, and protect against burns and electrical shocks, thereby ensuring their health and safety in a high-risk environment.
How to Improve Safety Protocols Skills
Improving safety protocols for welders involves continuously assessing and updating practices to minimize risks. Follow these concise steps:
- Regular Training: Ensure all welders undergo regular safety training that includes updates on new safety equipment and procedures.
- Personal Protective Equipment (PPE): Mandate the use of appropriate PPE, including helmets with proper shading, fire-resistant clothing, and gloves.
- Ventilation and Fume Extraction: Implement effective ventilation systems to minimize exposure to hazardous fumes.
- Regular Equipment Maintenance: Schedule regular maintenance checks on welding equipment to prevent malfunctions that could pose safety risks. Lincoln Electric provides guidelines on maintenance best practices.
- Safety Signs and Labels: Clearly mark all hazardous areas with safety signs and labels to remind workers of potential dangers.
- Emergency Preparedness: Develop and regularly update an emergency response plan tailored to welding incidents, including fires and exposure to toxic fumes.
- Health Monitoring: Offer regular health screenings for welders to detect any adverse effects from exposure to welding fumes or radiation.
By continuously improving and adhering to these protocols, a safer welding environment can be established and maintained.
How to Display Safety Protocols Skills on Your Resume
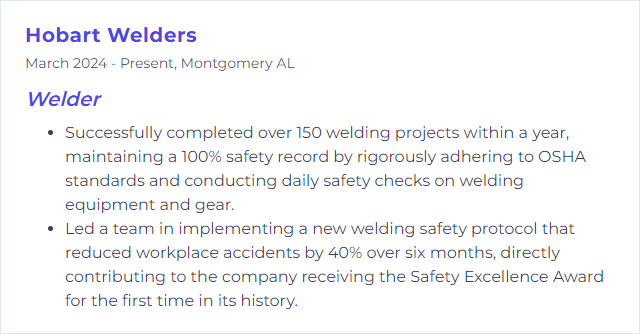