Top 12 Welder Helper Skills to Put on Your Resume
In the dynamic and highly specialized field of welding, having a well-crafted resume can set you apart as a welder helper. Highlighting the top skills that showcase your proficiency and readiness to support master welders is crucial for catching the eye of potential employers and advancing in this hands-on career path.
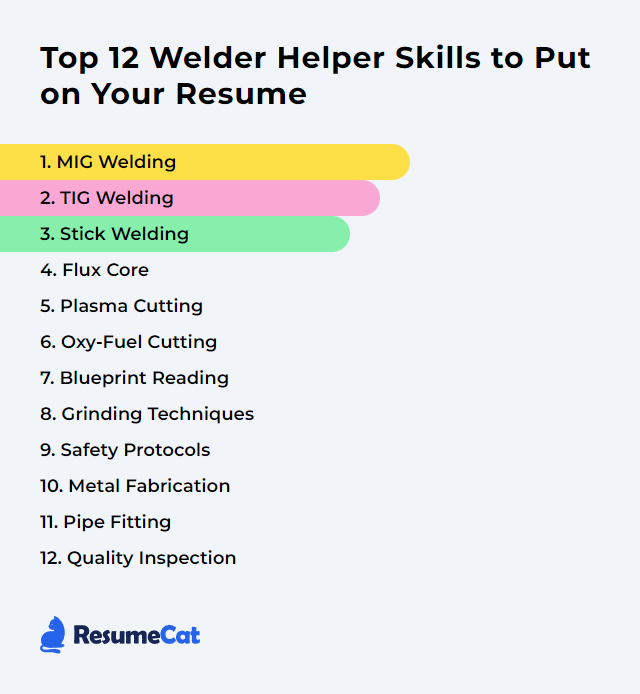
Welder Helper Skills
- MIG Welding
- TIG Welding
- Stick Welding
- Flux Core
- Plasma Cutting
- Oxy-Fuel Cutting
- Blueprint Reading
- Grinding Techniques
- Safety Protocols
- Metal Fabrication
- Pipe Fitting
- Quality Inspection
1. MIG Welding
MIG Welding, or Metal Inert Gas Welding, is a process where an electric arc forms between a consumable wire electrode and the workpiece, melting the metals together. A shielding gas is also expelled from the welding gun to protect the weld pool from atmospheric contaminants. As a Welder Helper, you'll assist in preparing materials, maintaining equipment, and ensuring a safe work environment.
Why It's Important
MIG welding is important because it provides a versatile, efficient, and relatively easy-to-learn method for joining metal parts quickly and durably, essential for a wide range of construction and manufacturing projects. For a Welder Helper, mastering MIG welding is crucial for assisting effectively in various tasks, ensuring high-quality welds, and progressing in the welding industry.
How to Improve MIG Welding Skills
Improving MIG welding involves focusing on technique, equipment setup, and practice. Here's a concise guide for a Welder Helper:
Proper Equipment Setup: Ensure your MIG welder is correctly set up. This includes selecting the right wire diameter and type for your material, adjusting the tension appropriately, and ensuring the gas flow is at the correct rate for the material being welded. Miller Welds provides a comprehensive guide on equipment setup.
Correct Welding Technique: Maintain a steady hand and keep the gun at a 10 to 15-degree angle from the workpiece. Use a consistent speed and motion, which can be a push or pull technique depending on the application. Lincoln Electric offers detailed techniques and tips.
Regular Practice: Practice on scrap material before starting on the actual workpiece. Try different speeds and angles to see what works best for the material and thickness.
Safety Measures: Always wear the appropriate safety gear, including a welding helmet with the correct shade, gloves, and protective clothing. Ensuring safety can also improve welding quality as it allows for better focus and control. OSHA provides safety guidelines for welding.
Clean the Workpiece: Before welding, clean the workpiece thoroughly to remove any contaminants like rust, paint, or oil, which can affect weld quality.
Seek Feedback and Learn: Ask for feedback from experienced welders and learn from their techniques. Additionally, online forums and tutorials can be valuable resources for tips and advice.
By focusing on these areas, a Welder Helper can significantly contribute to improving MIG welding quality and efficiency.
How to Display MIG Welding Skills on Your Resume
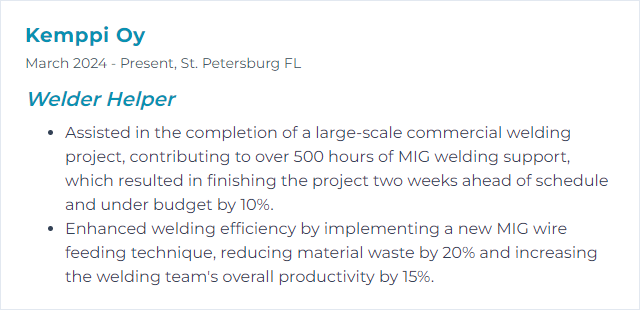
2. TIG Welding
TIG welding, or Tungsten Inert Gas welding, is a precise method of welding using a non-consumable tungsten electrode to produce the weld. It requires the welder to use both hands—one to hold the torch that produces the arc and the other to add the filler metal. It's known for its high-quality, clean welds and is used on a variety of materials, especially thin metals. As a Welder Helper, your role may involve preparing materials, maintaining equipment, and assisting with the setup for these detailed welding operations.
Why It's Important
TIG welding is important because it allows for precise, high-quality welds on a variety of metals, making it essential for applications requiring strong, clean joins without excessive heat damage or distortion.
How to Improve TIG Welding Skills
To improve TIG welding, focus on the following concise tips:
Maintain a Consistent Arc Length: Keeping the arc short and consistent helps in reducing the chances of contamination and improves the weld's appearance. Miller Welds offers detailed guidance.
Clean the Metal Thoroughly: Before welding, clean the base metal and filler rod with a dedicated brush to remove any oxide or contaminants. This step is crucial for avoiding weld contamination. Check out tips from Lincoln Electric for more on preparation.
Use the Right Tungsten Electrode: The choice of electrode (type and size) affects the weld quality significantly. For material-specific advice, Welding Tips and Tricks is a valuable resource.
Control Your Torch and Filler Rod Hand: Practice controlling your torch and filler rod hand to work in unison for a steady weld pool and bead formation. Weld.com offers tutorials and practice exercises.
Practice Foot Pedal Control: Mastery over the foot pedal allows better control over the heat input, affecting the weld's quality directly. Experiment with various settings to find what works best for the material you're working with.
Proper Gas Flow and Shielding: Ensure your gas flow is set correctly to protect your weld pool adequately. Too much or too little can affect weld quality. The Fabricator provides insights on gas flow and shielding techniques.
Post-Weld Cleaning: After welding, clean the weld and the heat-affected zone to prevent corrosion and maintain material integrity. The American Welding Society (AWS) offers publications with detailed post-weld cleaning practices.
Remember, consistent practice and learning from each welding experience are key to improvement.
How to Display TIG Welding Skills on Your Resume
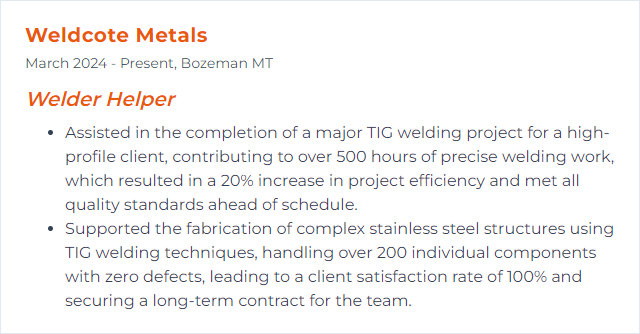
3. Stick Welding
Stick welding, also known as Shielded Metal Arc Welding (SMAW), is a manual welding process that uses a consumable electrode coated in flux to lay the weld. An electric current forms an arc between the electrode and the metals to be joined, melting the metals and the electrode to form the weld upon cooling.
Why It's Important
Stick welding is important because it offers versatility in welding various materials and positions, is cost-effective, and requires minimal equipment, making it indispensable for repair work, construction, and field jobs where conditions are variable or less controlled.
How to Improve Stick Welding Skills
Improving stick welding, especially for a Welder Helper, involves focusing on technique, preparation, and practice. Here are concise tips:
Clean the Metal: Ensure the surface is free from rust, paint, or dirt. Proper metal preparation is crucial for a strong weld.
Proper Electrode Selection: Choose the right electrode for the material and welding position. Lincoln Electric offers guidance on selecting electrodes.
Correct Amperage Setting: Too low or high amperage affects weld quality. Miller Welds has tips on finding the right settings.
Maintain a Short Arc Length: Keep the electrode close to the workpiece without touching it, as this affects penetration and weld quality.
Proper Angle and Speed: Hold the electrode at a 15 to 30-degree angle and move at a consistent speed that fills the joint adequately.
Practice Different Positions: Welding in flat, vertical, or overhead positions requires skill. Practice under supervision if possible.
Wear Appropriate Safety Gear: Always use safety glasses, gloves, and a welding helmet with the proper shade number. OSHA provides safety guidelines.
Inspect Your Work: Look for common defects like cracks or inclusions and learn how to correct them for future welds.
Remember, practice and patience are key to mastering stick welding.
How to Display Stick Welding Skills on Your Resume
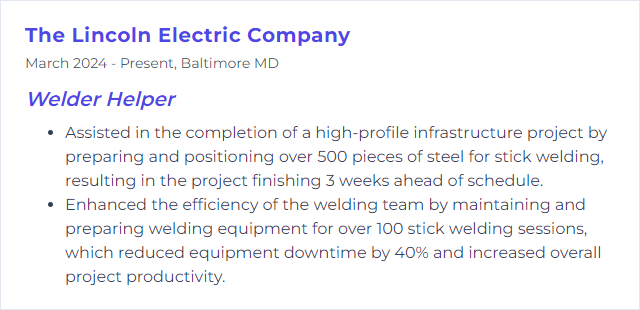
4. Flux Core
Flux core (FCAW or Flux Cored Arc Welding) is a welding process that uses a tubular wire filled with flux to weld metals. It allows for high welding speeds and is effective on thicker materials, often used in construction and repair work. This process can be performed outdoors as it does not require an external shielding gas.
Why It's Important
Flux core welding is crucial because it allows for high welding speed and efficiency in outdoor conditions, enhancing productivity and versatility for welders and their helpers.
How to Improve Flux Core Skills
To improve Flux Core welding, adhere to these concise guidelines tailored for a Welder Helper:
Clean the Surface: Ensure the welding surface is clean and free from rust, paint, or oil. Cleaning Techniques
Proper Equipment Setup: Adjust the welding machine settings (voltage and wire feed speed) according to the material thickness. Machine Setup Guide
Correct Wire Selection: Choose the right wire diameter and type for the job at hand. Wire Selection Tips
Optimal Stick Out: Maintain a stick-out (the wire extension from the contact tip) of 3/8-1/2 inch. Stick Out Explanation
Proper Technique: Use the right technique, such as the drag (pull) technique for most flux-cored welding applications. Welding Techniques
Maintain Clean Equipment: Regularly clean and inspect the welding gun, contact tips, and ensure the wire feeder operates smoothly. Maintenance Tips
By following these guidelines, you can significantly improve Flux Core welding performance and results.
How to Display Flux Core Skills on Your Resume
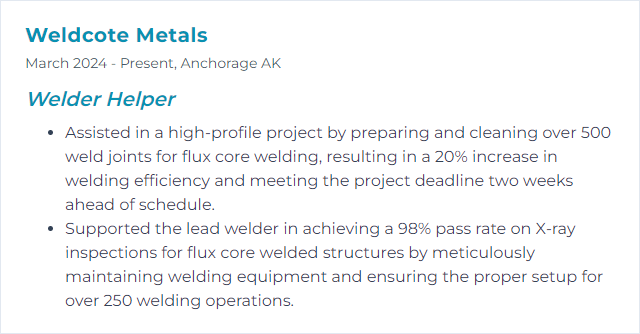
5. Plasma Cutting
Plasma cutting is a process used to cut metal using a plasma torch, where an electric arc superheats a gas into plasma, which then melts and ejects the metal to create precise cuts.
Why It's Important
Plasma cutting is essential for a Welder Helper as it allows for precise and efficient cutting of metal materials, facilitating the preparation and fabrication process in welding operations.
How to Improve Plasma Cutting Skills
To improve plasma cutting, focus on these key aspects:
Proper Setup: Ensure the plasma cutter is correctly set up according to the manufacturer's instructions. This includes checking gas flow, electrical connections, and the appropriate selection of consumables for the material being cut.
Correct Consumables: Use the right consumables for your material and cutting job. Different materials and thicknesses require specific types and sizes of electrodes, nozzles, and shields. Read more about selecting consumables.
Optimal Cutting Speed: Adjust your cutting speed for the material and thickness. Too fast or too slow can affect cut quality. Hypertherm provides a cutting speed chart.
Maintain Distance: Keep a consistent distance between the torch and the workpiece. Use a drag shield or guide if available for steady movement and optimal cut quality.
Regular Maintenance: Regularly inspect and replace worn consumables. Keep the torch, cables, and the machine clean and in good repair to prevent issues. MillerWelds offers maintenance tips.
Proper Technique: For angular cuts, learn to angle the torch correctly. Practice on scrap material to improve your technique for different types of cuts.
Safety First: Always wear appropriate protective gear, including safety glasses, gloves, and ear protection. Ensure proper ventilation in your working area.
By focusing on these areas, a Welder Helper can significantly improve the quality and efficiency of plasma cutting operations.
How to Display Plasma Cutting Skills on Your Resume
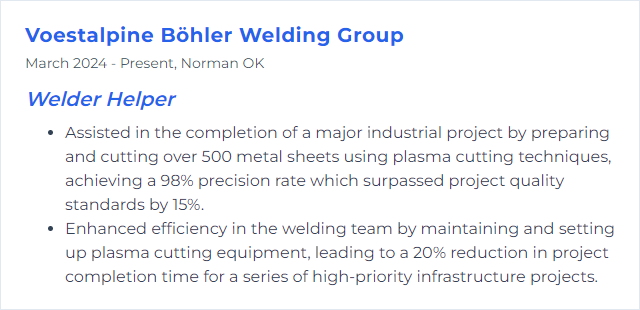
6. Oxy-Fuel Cutting
Oxy-fuel cutting is a process where a combination of fuel gas and oxygen is used to heat metal to its kindling temperature, making it malleable, and then a stream of oxygen is directed onto the heated area to burn through the metal, creating a separation or cut.
Why It's Important
Oxy-fuel cutting is essential for a welder helper as it enables precise and efficient cutting of metals, facilitating the preparation and fitting of materials for welding and repair tasks. This skill enhances job versatility and productivity in metal fabrication and repair projects.
How to Improve Oxy-Fuel Cutting Skills
To improve Oxy-Fuel Cutting, a Welder Helper can focus on these key points:
Proper Setup: Ensure the oxy-fuel equipment is correctly assembled and checked for leaks. Safety first.
Correct Gas Ratios: Use the appropriate oxygen and fuel gas mixture for the material being cut. Gas ratio guide.
Optimal Cutting Speed: Adjust the speed of the cut to avoid excessive slag formation and ensure a clean cut. Cutting speed chart.
Proper Tip Selection: Use the correct cutting tip size and type for the thickness and type of material. Tip selection guide.
Regular Maintenance: Regularly clean and inspect cutting equipment to prevent issues. Maintenance tips.
Remember, practice and patience are key to mastering oxy-fuel cutting techniques.
How to Display Oxy-Fuel Cutting Skills on Your Resume
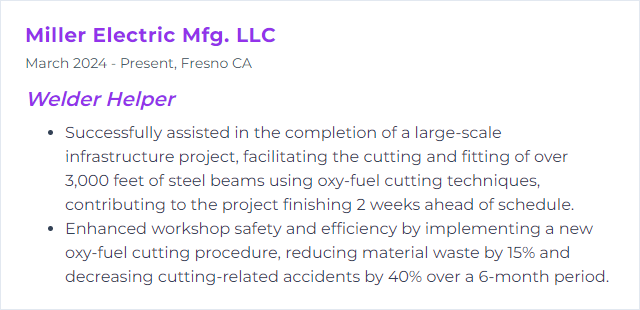
7. Blueprint Reading
Blueprint reading for a Welder Helper involves understanding and interpreting technical drawings and diagrams that outline the specifications, dimensions, and procedures for welding projects, enabling accurate construction and assembly of metal components as per the design requirements.
Why It's Important
Blueprint reading is crucial for a Welder Helper as it enables them to understand and follow the precise specifications for welding projects, ensuring accurate assembly, correct material usage, and adherence to safety standards.
How to Improve Blueprint Reading Skills
Improving blueprint reading, especially for a Welder Helper, involves developing a keen understanding of symbols, dimensions, and specifications commonly used in welding projects. Here's a concise guide:
Understand Basic Symbols: Start by familiarizing yourself with basic welding symbols as outlined by the American Welding Society (AWS). The AWS A2.4 Standard Symbols for Welding is a crucial resource.
Learn to Interpret Dimensions and Tolerances: Dimensional understanding is key. Resources like Engineering Drawings for Welders can be particularly helpful.
Practice with Real Blueprints: Hands-on practice by examining real welding blueprints and then observing or participating in the actual welding process will enhance your learning. Websites like Lincoln Electric offer practical insights and examples.
Take a Course: Enroll in a blueprint reading course tailored to welding. Many community colleges and trade schools offer such courses. Online platforms like Udemy may have relevant courses focusing on welding blueprints.
Use Visual Aids: Visual aids can simplify complex concepts. The book "Blueprint Reading for Welders" by A.E. Bennett and Louis J Siy is an excellent resource with detailed illustrations and explanations.
By incorporating these steps and consistently practicing, you'll progressively improve your blueprint reading skills, making you a more proficient Welder Helper.
How to Display Blueprint Reading Skills on Your Resume
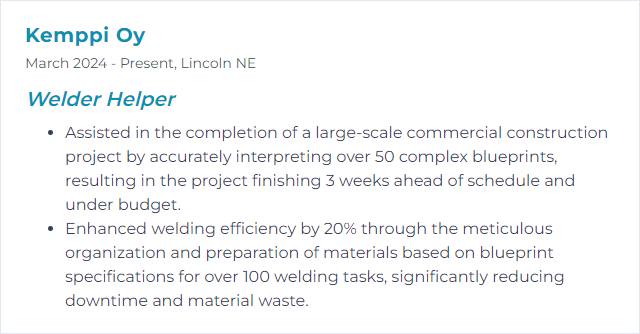
8. Grinding Techniques
Grinding techniques in the context of a Welder Helper involve using abrasive tools to smooth, finish, or cut metals and materials. This process includes selecting the appropriate grinding wheel or disc, applying the correct pressure, and employing safety measures to shape or clean welds and prepare surfaces for welding or finishing.
Why It's Important
Grinding techniques are crucial for a Welder Helper as they ensure the proper preparation and finishing of welds, removing excess material, smoothing out surfaces, and correcting imperfections to achieve strong, clean, and visually appealing welds.
How to Improve Grinding Techniques Skills
Improving grinding techniques, especially for a Welder Helper, involves focusing on safety, efficiency, and precision. Here are concise tips:
Safety First: Always wear appropriate PPE such as gloves, eye protection, and ear protection. OSHA Guidelines.
Proper Equipment: Use the right grinder and disc type for the material and job. Refer to the manufacturer's recommendations.
Correct Angle: Hold the grinder at the proper angle (usually between 15°-30°) to the workpiece for optimal efficiency and safety. Angle Grinding Guidance.
Consistent Pressure: Apply steady, moderate pressure to prevent gouges and ensure an even grind.
Inspect Equipment: Regularly check discs and the grinder for damage or wear. Safety Inspection Checklists.
Practice and Patience: Skill improvement comes with practice. Take your time to learn the nuances of different materials and tools.
By focusing on these areas, a Welder Helper can significantly improve their grinding techniques, contributing to safer and more efficient operations.
How to Display Grinding Techniques Skills on Your Resume
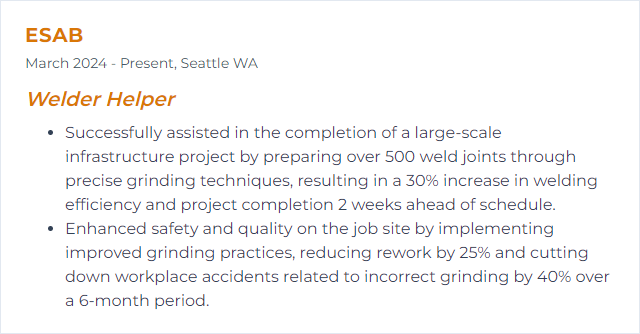
9. Safety Protocols
Safety protocols for a Welder Helper are guidelines and measures designed to protect against hazards associated with welding tasks, including wearing personal protective equipment (PPE), following proper handling and use of welding equipment, and adhering to fire safety and hazardous material handling procedures.
Why It's Important
Safety protocols are crucial for a Welder Helper to prevent accidents, minimize exposure to harmful fumes and radiation, and ensure a safe working environment, thereby protecting both the individual and coworkers from potential injuries or health issues.
How to Improve Safety Protocols Skills
To improve safety protocols for a Welder Helper, follow these concise strategies:
Enhance Training: Ensure comprehensive safety training that includes both theoretical knowledge and practical demonstrations on safe welding practices, fire prevention, and emergency response.
Regular Safety Audits: Conduct regular safety audits to identify and mitigate potential hazards in the workplace, focusing on equipment, work areas, and personal protective equipment (PPE).
PPE Compliance: Enforce strict adherence to PPE requirements, including helmets, goggles, gloves, and fire-resistant clothing, tailored to welding activities.
Ventilation and Fume Extraction: Install and maintain proper ventilation systems and fume extraction equipment to reduce the inhalation of harmful welding fumes and gases.
Emergency Preparedness: Develop and regularly update an emergency action plan, including fire safety procedures and first-aid measures, ensuring all employees are trained on the plan.
Equipment Maintenance: Implement a routine maintenance program for all welding equipment and machinery to prevent malfunctions and accidents caused by equipment failure.
By focusing on these areas, safety protocols for Welder Helpers can be significantly improved, leading to a safer work environment.
How to Display Safety Protocols Skills on Your Resume
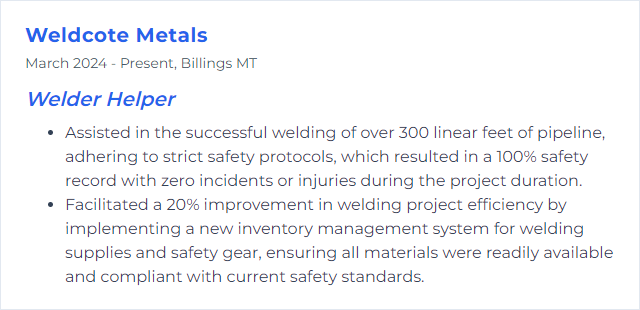
10. Metal Fabrication
Metal fabrication is the process of cutting, shaping, and assembling metal materials to create structures or components, often involving welding, by a Welder Helper.
Why It's Important
Metal fabrication is crucial because it involves cutting, shaping, and assembling metal parts to create structures or components. This process is essential for a Welder Helper as it enables the production of durable and high-quality metal products, which are foundational in construction, automotive, aerospace, and many other industries. It also allows for customization and repair, ensuring that specific project requirements are met efficiently.
How to Improve Metal Fabrication Skills
To enhance metal fabrication skills as a Welder Helper, focus on the following strategies:
Enhance Technical Skills: Enroll in welding courses or certifications to understand various welding techniques and metal properties. Websites like American Welding Society (AWS) offer resources and certifications.
Safety First: Prioritize learning about safety protocols from resources like OSHA’s Welding, Cutting, and Brazing guide.
Learn from Experience: Gain hands-on experience under skilled welders. Consider apprenticeships or on-the-job training programs.
Stay Updated with Technology: Familiarize yourself with the latest welding technologies and tools. Resources like Welding Digest provide updates on new equipment and techniques.
Physical Fitness: Welding can be physically demanding. Maintain physical fitness to handle the rigors of the job.
Join a Professional Network: Engage with communities or forums like Weld.com to exchange knowledge and experiences.
By focusing on continuous learning, safety, and staying updated with industry trends, you can significantly improve your capabilities in metal fabrication.
How to Display Metal Fabrication Skills on Your Resume
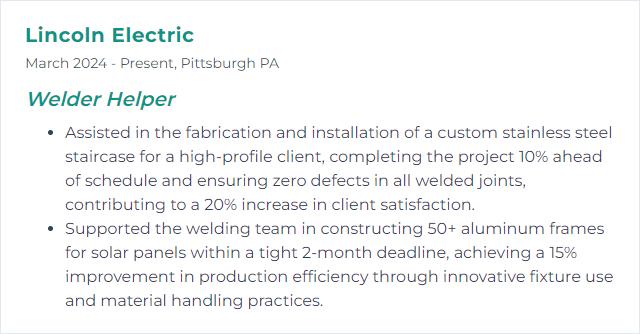
11. Pipe Fitting
Pipe fitting involves preparing and assembling piping systems for welding, including measuring, cutting, threading, and joining pipes to ensure a secure and efficient pipeline system.
Why It's Important
Pipe fitting is crucial because it ensures the secure and efficient assembly of piping systems for transporting liquids, gases, and sometimes solids, which is essential for the functionality and safety of various industrial and residential infrastructures. For a Welder Helper, understanding pipe fitting is vital for assisting in the precise preparation, alignment, and support of pipes before and during welding processes, ensuring high-quality and durable connections.
How to Improve Pipe Fitting Skills
Improving pipe fitting skills, especially for a Welder Helper, involves understanding the basics of pipe fitting, practicing precision in measurements and cuts, and enhancing one’s welding techniques. Here are concise steps and resources to help:
Understand Pipe Fitting Basics: Start with learning the types of pipes, fittings, and the tools used. Grasping the differences in materials and the purpose of various fittings is crucial. This guide provides a comprehensive overview of pipe fittings.
Measure Accurately: Precision in measuring and marking for cuts or welds cannot be overstated. Use quality measuring tools and always double-check your measurements. Here's a tutorial on precise measuring and cutting.
Practice Cutting and Prepping Pipes: Properly cutting and preparing pipes before welding is crucial for a good fit and seal. Practice using different cutting tools and techniques. This video demonstrates proper pipe cutting and preparation.
Improve Welding Techniques: As a Welder Helper, enhancing your welding skills is directly beneficial. Focus on the welding techniques specific to pipe fitting. MillerWelds offers resources for improving various welding techniques.
Learn from Experienced Pipefitters and Welders: Hands-on experience is invaluable. Work closely with professionals, observe their techniques, and ask for tips and feedback.
Stay Updated with Industry Standards: Pipe fitting and welding standards evolve. Stay informed about the latest codes and best practices. The American Welding Society (AWS) is a great resource for the latest in welding standards and education.
Practice, Practice, Practice: There’s no substitute for hands-on practice. Work on different projects, materials, and fittings to build your skills.
By focusing on these areas, a Welder Helper can significantly improve their pipe fitting skills, contributing more effectively to welding projects and advancing in their career.
How to Display Pipe Fitting Skills on Your Resume
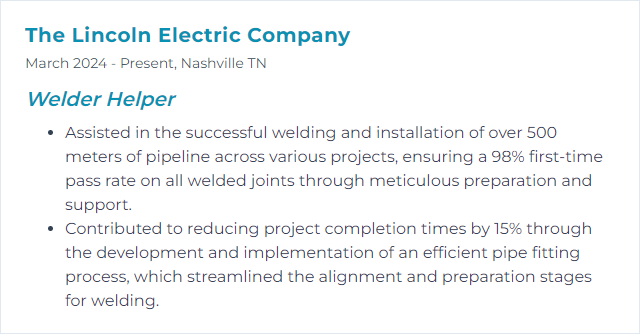
12. Quality Inspection
Quality Inspection, in the context of a Welder Helper, involves examining welding work to ensure it meets specified standards and criteria, checking for defects, adherence to blueprints, and compliance with safety regulations.
Why It's Important
Quality inspection is crucial for a Welder Helper to ensure the integrity, safety, and compliance of welded structures, prevent costly rework, and maintain high standards of craftsmanship.
How to Improve Quality Inspection Skills
To improve Quality Inspection for a Welder Helper, focus on the following concise steps:
Enhance Skills and Knowledge: Engage in continuous learning about welding techniques and quality standards. Online platforms like American Welding Society (AWS) offer courses and certifications.
Use Proper Tools and Equipment: Ensure the use of accurate measuring and inspection tools. Regular calibration and maintenance are essential. Grainger provides a wide range of quality inspection tools.
Follow Standard Procedures: Adhere to established welding and inspection protocols as outlined in standards from organizations like ASTM International.
Implement a Checklist: Develop and use a detailed inspection checklist tailored to specific welding tasks. This promotes consistency and thoroughness.
Regular Practice and Simulation: Practice inspection regularly, including the use of simulation tools where available, to hone skills in identifying defects and issues.
Feedback and Continuous Improvement: Seek feedback from experienced inspectors and incorporate lessons learned into practice.
By focusing on these areas, a Welder Helper can significantly contribute to improving the quality inspection process, ensuring higher standards of welding quality and safety.
How to Display Quality Inspection Skills on Your Resume
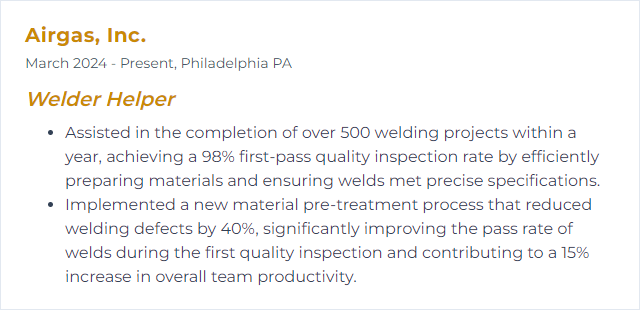