Top 12 Welder Fabricator Skills to Put on Your Resume
In the competitive field of welding and fabrication, showcasing a robust set of skills on your resume can significantly enhance your employability and career prospects. A well-crafted list of welder fabricator skills demonstrates your proficiency, versatility, and readiness to tackle diverse challenges in this hands-on profession.
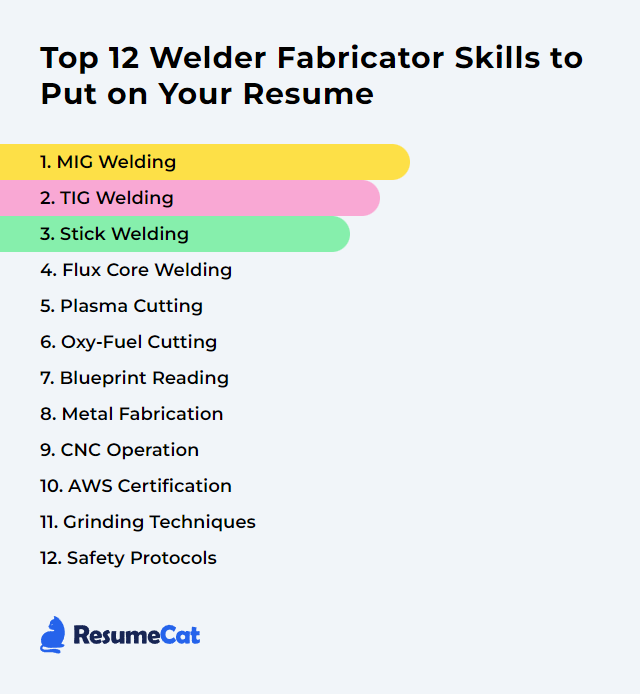
Welder Fabricator Skills
- MIG Welding
- TIG Welding
- Stick Welding
- Flux Core Welding
- Plasma Cutting
- Oxy-Fuel Cutting
- Blueprint Reading
- Metal Fabrication
- CNC Operation
- AWS Certification
- Grinding Techniques
- Safety Protocols
1. MIG Welding
MIG welding, or Metal Inert Gas welding, is a process where an electric arc forms between a consumable wire electrode and the workpiece metal(s), heating the workpiece metal(s), causing them to melt and join. It uses a shielding gas to protect the weld from atmospheric contamination. This method is favored for its versatility, speed, and ease of use, making it popular in both industrial and home settings.
Why It's Important
MIG welding is important for a Welder Fabricator because it allows for efficient, versatile, and high-quality welding of a wide range of metals with minimal cleanup, making it ideal for both production and custom fabrication projects.
How to Improve MIG Welding Skills
To improve MIG welding, focus on the following strategies:
Maintain a Consistent Travel Speed: Keeping a uniform speed ensures even weld bead formation. Lincoln Electric offers detailed tips on speed and technique.
Proper Work Angle and Electrode Stick-Out: Adjust the work angle and stick-out based on joint design. MillerWelds provides insights on angle adjustments for different types of joints.
Choose the Right Gas and Material Thickness: Select appropriate shielding gas and material thickness for your project. HobartWelders discusses gas choices and their impacts on weld quality.
Regular Equipment Maintenance: Keep your welding equipment in top condition. The American Welding Society (AWS) emphasizes the importance of regular maintenance for optimal performance.
Practice and Training: Continuous practice and seeking training can significantly improve skills. Explore courses and certifications at AWS Learning.
By adhering to these focal points, a welder fabricator can enhance their MIG welding technique and output quality.
How to Display MIG Welding Skills on Your Resume
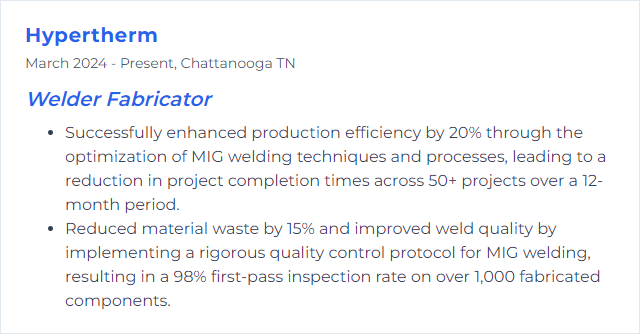
2. TIG Welding
TIG welding, or Tungsten Inert Gas welding, is a precision welding process that uses a non-consumable tungsten electrode to produce the weld. It allows for greater control over the weld than other methods, making it ideal for thin materials and intricate projects. This process can be used on a variety of metals and requires a skilled welder fabricator for best results.
Why It's Important
TIG welding is important for a Welder Fabricator because it allows for precise, high-quality welds on a variety of metals, including thin materials and exotic alloys, enabling fabrication of complex and detailed components with excellent finish and strength.
How to Improve TIG Welding Skills
Improving TIG welding, especially for a welder fabricator, involves enhancing precision, safety, and skill through practice, proper equipment setup, and understanding material properties. Here are concise tips:
Practice Consistency: Regular practice on scrap metal helps improve hand steadiness and control. Aim for uniform weld bead appearance.
Proper Equipment Setup: Ensure your TIG welder settings (amperage, gas flow, etc.) are optimized for the material you're welding. Miller Electric's guide provides excellent setup advice.
Correct Electrode Choice: Select the right electrode for your material and job, considering electrode diameter and material (e.g., 2% lanthanated tungsten). Lincoln Electric offers a selection guide.
Cleanliness is Key: Clean the base metal and filler rod with a dedicated stainless steel brush or appropriate solvent to prevent contamination. This American Welding Society article emphasizes the importance of cleanliness.
Proper Body Positioning: Maintain a comfortable, steady position to ensure consistent arc length and welding speed. Good posture reduces fatigue and increases weld quality.
Use a Filler Metal Chart: Matching the filler metal to the base metal is crucial for weld integrity. Hobart Brothers offer a selection chart.
Preheat and Post-Weld Heat Treat: Some materials require preheating and/or post-weld heat treatment to prevent cracking. Understand the thermal properties of your materials. The Fabricator provides insights on heat treatments.
Shielding Gas Optimization: Different materials and thicknesses require different shielding gases or mixtures for optimal results. Airgas gives an overview of shielding gases.
Enhancing TIG welding skills involves a mix of knowledge, practice, and attention to detail. Leveraging resources from reputable industry experts and manufacturers can significantly contribute to skill improvement and welding quality.
How to Display TIG Welding Skills on Your Resume
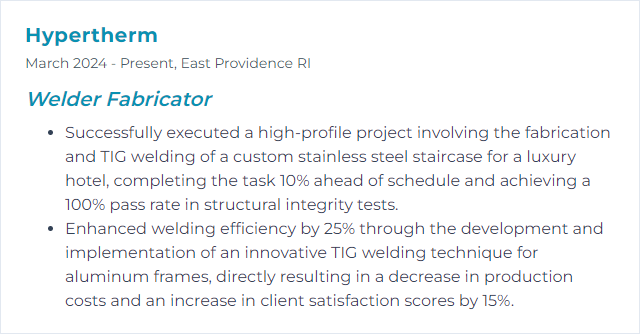
3. Stick Welding
Stick welding, also known as Shielded Metal Arc Welding (SMAW), is a manual welding process that uses a consumable electrode coated in flux to lay the weld. It's versatile, works on most metals, and is effective in outdoor conditions and on dirty or rusty materials, making it a staple in construction and repair work for a welder fabricator.
Why It's Important
Stick welding is crucial for a Welder Fabricator because it offers versatility in welding various materials and thicknesses, is effective outdoors or in windy conditions, and requires minimal equipment, making it ideal for field repairs and construction projects.
How to Improve Stick Welding Skills
Improving stick welding requires practice, understanding of techniques, and knowledge of equipment settings. Here are concise tips for a Welder Fabricator:
Select the Right Electrode: Choose an electrode appropriate for the material and welding position. American Welding Society (AWS) provides guidelines on electrode selection.
Proper Grip and Stance: Hold the electrode holder like a pencil for better control. Maintain a comfortable and stable stance to ensure steady welding.
Correct Amperage Setting: Adjust the welding machine to the right amperage based on electrode diameter and material thickness. Refer to the Lincoln Electric Welding Parameters Guide for recommendations.
Maintain Short Arc Length: Keep the arc as short as possible without allowing the electrode to stick to the workpiece. This improves penetration and reduces spatter.
Angle and Direction of Travel: For flat and horizontal positions, a 5 to 15-degree drag angle is recommended. In vertical welding, use an upward (vertical up) technique for better penetration, or downward (vertical down) for faster welding on thinner materials.
Clean the Workpiece: Before welding, clean the work area of any rust, paint, or contaminants to ensure a strong weld. Use a wire brush or grinder for preparation.
Practice Consistent Speed and Motion: Move steadily and at a consistent speed that matches the rate of melting of the electrode.
Overlap Passes Properly: In multi-pass welding, ensure each pass overlaps properly with the previous pass to avoid weak joints.
Cool Down Properly: Allow welded parts to cool down naturally. Rapid cooling can lead to material warping or increased brittleness.
Continuous Learning: Stay updated with the latest welding techniques and technologies through resources such as Welding Tips and Tricks and Miller Welding's Resources.
Improving in stick welding is a continuous process that combines knowledge, skill, and experience. Regular practice and adherence to these guidelines will significantly enhance a welder fabricator's proficiency in stick welding.
How to Display Stick Welding Skills on Your Resume
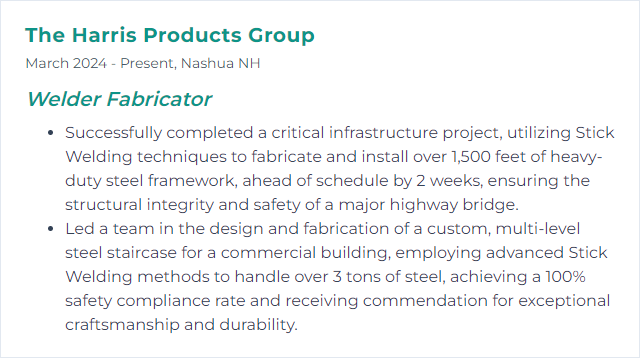
4. Flux Core Welding
Flux Core Welding (FCW) is a semi-automatic or automatic arc welding process used by welder fabricators that utilizes a tubular wire filled with flux to weld metals, offering high welding speeds and penetration without the need for external shielding gas.
Why It's Important
Flux core welding is crucial for a Welder Fabricator as it allows for high deposition rates, enabling efficient welding of thicker materials outdoors and in windy conditions without the need for external shielding gas. This versatility and productivity make it an indispensable technique in the fabrication industry.
How to Improve Flux Core Welding Skills
Improving Flux Core Welding involves focusing on technique, equipment settings, and preparation. Here's a concise guide:
Proper Preparation: Clean the workpiece to remove rust, oil, or dirt. Good contact between the wire and metal ensures a strong weld.
Correct Settings: Adjust your welder settings based on the material and wire diameter. A good starting point is the manufacturer's recommendations. Miller Electric provides guidelines for setting up your machine.
Right Technique: Use the correct grip and angle. Hold the torch at a 15-degree angle and use a consistent speed. Lincoln Electric offers insights on technique.
Select Appropriate Wire: Choose the right wire for your application. E71T-11 is versatile for many applications. For specific materials, consult your wire supplier's recommendations.
Practice: Consistent practice on scrap material can help refine your skills and adjust techniques as needed.
Safety First: Always wear appropriate safety gear, including a helmet, gloves, and protective clothing. OSHA provides safety guidelines for welding.
Improvement comes with understanding how changes in your approach affect the outcome. Experiment with different settings and techniques to see what works best for your specific applications.
How to Display Flux Core Welding Skills on Your Resume
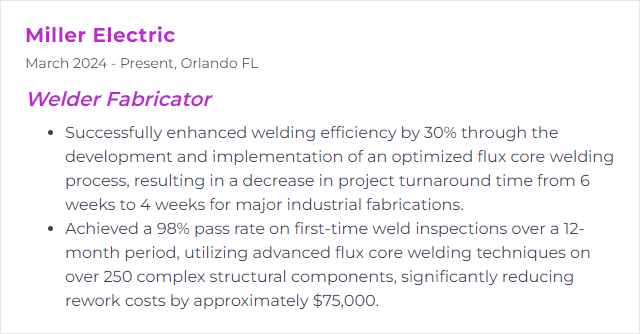
5. Plasma Cutting
Plasma cutting is a process used by welder fabricators to cut through conductive metals by using a jet of superheated, electrically ionized gas (plasma) to melt and eject material, creating precise cuts with high speed and accuracy.
Why It's Important
Plasma cutting is crucial for a Welder Fabricator as it allows for precise, efficient, and quick cutting of various metals, significantly enhancing productivity and the ability to tackle complex fabrication tasks with ease.
How to Improve Plasma Cutting Skills
Improving plasma cutting involves optimizing setup, technique, and maintenance. Here are concise tips:
Select the Right Consumables: Match consumables to the cutting task for better quality cuts and longer life. Hypertherm's Consumable Selection Guide offers detailed insights.
Maintain Correct Cutting Speed: Too fast or too slow affects cut quality. Lincoln Electric's Guide provides speed recommendations.
Proper Torch Height: Use the correct torch-to-work distance, typically controlled by the machine's THC (Torch Height Control). Refer to the Eastwood Blog for understanding THC adjustments.
Dry and Clean Air Supply: Moisture affects plasma performance. Install an air filter or dryer. Miller's Air Quality Solutions explain the importance of air quality.
Regular Maintenance: Clean and inspect torch parts regularly. This ESAB Maintenance Checklist outlines key maintenance steps.
Correct Power Settings: Adjust amperage based on material thickness. Overpowering or underpowering can reduce quality. Your machine's manual usually guides on optimal settings.
Use a Guide: For straight cuts, use a straight edge or roller guide. It enhances precision. Trick-Tools offers various guides.
By focusing on these areas, welder fabricators can significantly improve their plasma cutting results.
How to Display Plasma Cutting Skills on Your Resume
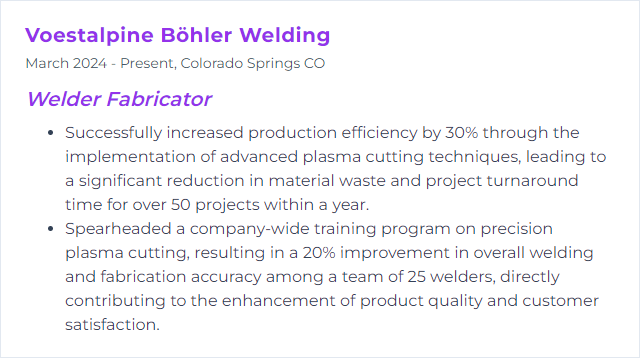
6. Oxy-Fuel Cutting
Oxy-fuel cutting is a process used by welder fabricators to cut through metal by using a torch to heat the metal to its kindling temperature, then using a stream of pure oxygen to trigger a chemical reaction with the metal, creating a narrow cutting path through the material.
Why It's Important
Oxy-fuel cutting is crucial for a welder fabricator because it allows precise cutting of metals, especially steel, with efficiency and speed, enabling the shaping and fitting of materials for fabrication and repair tasks.
How to Improve Oxy-Fuel Cutting Skills
To improve Oxy-Fuel Cutting, a Welder Fabricator can follow these concise steps:
Use Proper Equipment: Ensure torches, nozzles, and hoses are in good condition. Select the correct nozzle size for the thickness of the material (Lincoln Electric).
Optimize Gas Pressure and Flow: Adjust oxygen and fuel gas pressure according to the manufacturer’s recommendations for the material thickness (MillerWelds).
Maintain Proper Speed: Move the torch at the right speed; too fast can result in an incomplete cut, too slow can waste gas and cause excessive melting (Harris Products Group).
Ensure Clean Material Surface: Remove rust, paint, or any coatings from the surface to improve cutting quality and speed (ESAB).
Preheat Properly: The preheat flame should be adjusted to a neutral flame and applied until the metal glows a dull red, indicating it’s ready to be cut (Hypertherm).
Practice Safety: Always wear appropriate PPE, check for leaks, and ensure proper ventilation in the working area (OSHA).
Improving technique and adhering to these guidelines can significantly enhance the quality and efficiency of oxy-fuel cutting.
How to Display Oxy-Fuel Cutting Skills on Your Resume
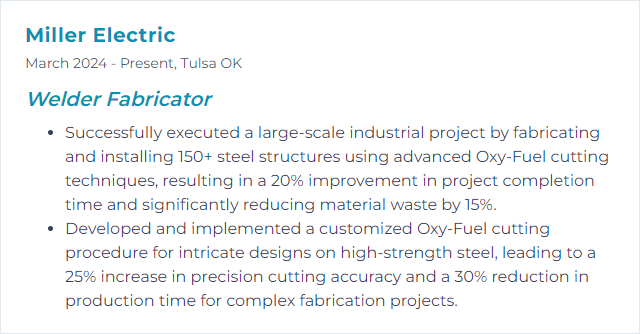
7. Blueprint Reading
Blueprint reading for a Welder Fabricator involves interpreting and understanding detailed technical drawings and plans that outline how to construct, assemble, or fabricate metal structures and components. It includes recognizing symbols, dimensions, and specifications related to welding and metalworking processes.
Why It's Important
Blueprint reading is crucial for a welder fabricator because it enables them to accurately interpret and follow technical drawings and specifications, ensuring precision in fabricating and assembling metal structures and components as designed.
How to Improve Blueprint Reading Skills
Improving blueprint reading skills as a Welder Fabricator involves understanding various symbols, dimensions, and notations specific to welding and fabrication. Here's a concise guide:
Familiarize with Basic Symbols: Start with learning the basic welding symbols and their meanings. This guide from the American Welding Society (AWS) can help.
Understand Dimensions and Tolerances: Knowing how to accurately read dimensions and tolerances is crucial. Practice with actual blueprints or use resources like Engineers Edge to get familiar.
Study Different Types of Welds: Learn about different types of welds and their applications. The Lincoln Electric Welding School offers resources and courses.
Practice Regularly: Like any skill, regular practice is key. Use online resources or books like "Blueprint Reading for Welders" by A.E. Bennett and Louis J Siy for practice.
Take a Course: Consider enrolling in a course specifically designed for welders looking to improve their blueprint reading skills. Many community colleges and trade schools offer relevant courses. American Welding Society often has information on courses and certifications.
Use Online Resources: Websites like Welding Tips and Tricks provide practical advice and video tutorials that can reinforce learning.
By consistently studying, practicing, and applying the skills learned, you can significantly improve your blueprint reading abilities as a Welder Fabricator.
How to Display Blueprint Reading Skills on Your Resume
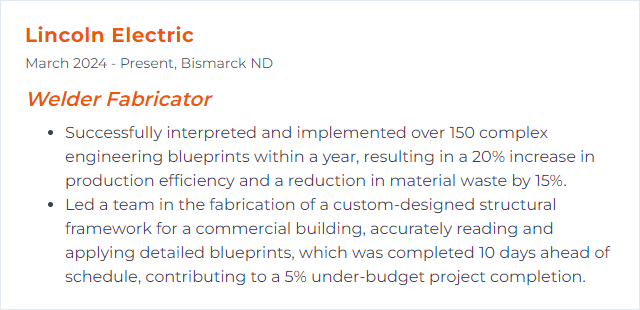
8. Metal Fabrication
Metal fabrication involves cutting, shaping, and assembling metal structures from various metal parts and pieces, utilizing techniques like welding, cutting, bending, and machining. For a Welder Fabricator, it specifically refers to the process of creating metal structures and components by cutting, shaping, and joining metal materials together using various welding methods.
Why It's Important
Metal fabrication is crucial for a Welder Fabricator because it involves cutting, bending, and assembling metal structures from various raw materials, enabling the creation of essential components and equipment across diverse industries, from construction and automotive to aerospace and beyond. This process is fundamental to building and maintaining the infrastructure and machinery that drive economic development and innovation.
How to Improve Metal Fabrication Skills
To improve metal fabrication, a Welder Fabricator should focus on the following key areas, each supported by resources for deeper exploration:
Enhance Skills: Continuously update and refine welding and fabrication skills through courses and certifications. Consider resources like American Welding Society (AWS) for courses and certifications.
Adopt New Technologies: Stay informed about the latest technologies in welding and metal fabrication, such as laser or ultrasonic welding. Websites like The Fabricator offer insights into new technologies and trends.
Implement Quality Control: Adopt quality control measures to ensure the consistency and reliability of your work. The International Organization for Standardization (ISO) provides guidelines specifically for welding quality.
Safety First: Always prioritize safety by staying updated with the latest safety standards and equipment. The Occupational Safety and Health Administration (OSHA) offers comprehensive guidelines on welding, cutting, and brazing safety practices.
Efficiency in Operation: Streamline your workflow and reduce waste by adopting lean manufacturing principles. The Lean Enterprise Institute offers resources on implementing lean practices in your operations.
By focusing on these areas and leveraging the provided resources, a Welder Fabricator can significantly improve their metal fabrication processes.
How to Display Metal Fabrication Skills on Your Resume
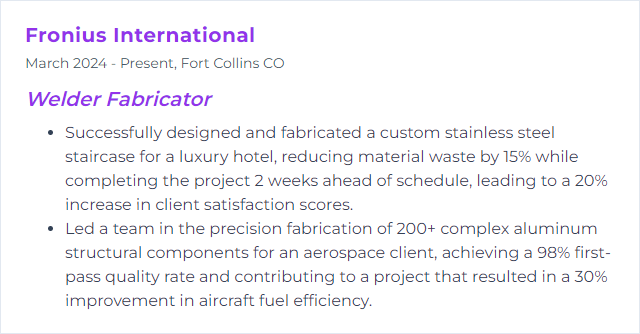
9. CNC Operation
CNC operation, in the context of a Welder Fabricator, involves the use of computer-controlled machines to precisely cut, shape, and fabricate metal components according to specified designs.
Why It's Important
CNC operation is important for a Welder Fabricator because it enables precise, repeatable, and efficient cutting and shaping of materials, significantly enhancing productivity, accuracy, and the quality of finished products.
How to Improve CNC Operation Skills
Improving CNC operation, especially for a Welder Fabricator, involves enhancing precision, efficiency, and safety. Here are concise strategies:
- Training: Continuous learning and training on CNC technology improves skills and operational efficiency.
- Maintenance: Regular maintenance of CNC machines ensures optimal performance and longevity.
- Tool Quality: Invest in high-quality cutting tools and replace them regularly to maintain accuracy and efficiency.
- Software Updates: Keep CNC software updated to leverage the latest features and improvements.
- Optimize Programming: Enhance programming techniques by using advanced CAM software, which can improve cutting paths and reduce operation time.
- Workflow Evaluation: Regularly review and optimize the workflow to identify bottlenecks and improve productivity.
- Safety Practices: Implement strict safety protocols to prevent accidents and ensure the well-being of operators.
By focusing on these areas, a Welder Fabricator can significantly enhance CNC operation efficiency, accuracy, and safety.
How to Display CNC Operation Skills on Your Resume
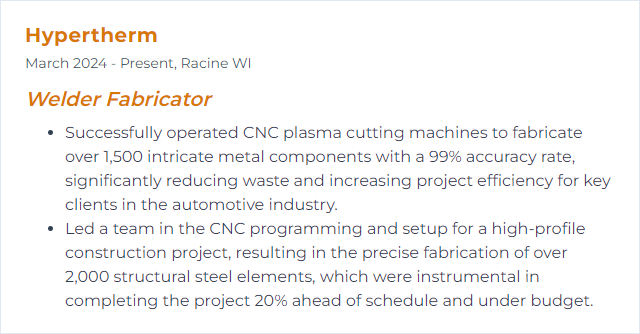
10. AWS Certification
AWS Certification for a Welder Fabricator refers to the credential awarded by the American Welding Society (AWS), certifying that the individual has met specific standards of welding skills and knowledge. This certification is recognized industry-wide and often required for advanced welding positions.
Why It's Important
AWS Certification for a Welder Fabricator is crucial as it verifies their expertise and proficiency in welding standards and practices, ensuring high-quality workmanship and adherence to safety regulations. It enhances their credibility, employability, and potential for higher earnings in the industry.
How to Improve AWS Certification Skills
To improve your AWS (American Welding Society) Certification as a Welder Fabricator, follow these concise steps:
Understand the AWS Certification Path: Get familiar with specific certifications like the Certified Welder (CW), Certified Welding Inspector (CWI), or others that align with your career goals. AWS Certification Paths
Enhance Your Skills: Continuously practice and improve your welding techniques. Consider taking additional courses or training programs. AWS Learning
Stay Updated: Keep abreast of the latest welding technologies and AWS standards. AWS Standards
Prepare for Exams: Utilize AWS study materials and participate in study groups. AWS Certification Preparation
Gain Practical Experience: Work on diverse projects to gain a wide range of experiences.
Network: Engage with other professionals through forums and AWS events. AWS Events
Apply for Certification/Recertification: Follow the guidelines for application or recertification meticulously. AWS Certification Application
By focusing on continuous learning and networking, you can significantly improve your AWS Certification as a Welder Fabricator.
How to Display AWS Certification Skills on Your Resume
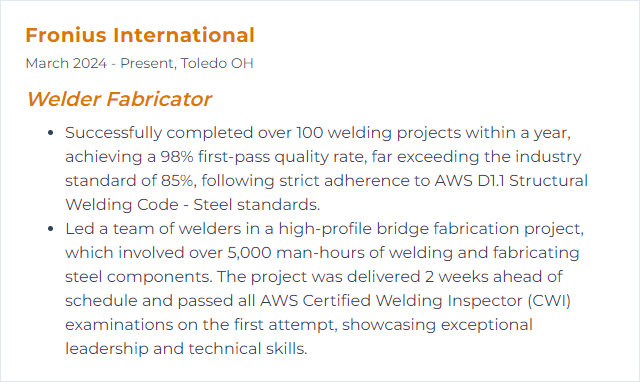
11. Grinding Techniques
Grinding techniques in welding and fabrication involve the use of abrasive tools to smooth, finish, or shape metal surfaces. This process removes excess material, sharp edges, or weld beads, preparing surfaces for further processing or ensuring a clean, polished finish. Techniques vary based on the material, desired finish, and tool type, including angle grinders, die grinders, and abrasive discs or belts.
Why It's Important
Grinding techniques are crucial for a Welder Fabricator because they ensure the proper preparation and finishing of metal surfaces, enabling precise welds, improving weld quality and appearance, and ensuring structural integrity and safety of the fabricated items.
How to Improve Grinding Techniques Skills
Improving grinding techniques as a welder fabricator involves enhancing efficiency, safety, and quality. Here's a concise guide:
Safety First: Always wear appropriate personal protective equipment (PPE) such as gloves, eye protection, and ear protection. OSHA Safety Standards
Right Tool and Attachment: Use the correct grinder and abrasive for the material and task. A comprehensive guide by 3M can help in selecting the right products.
Proper Technique: Maintain the correct angle (usually between 15°-30° to the workpiece) for efficient material removal and to avoid gouging. MillerWelds offers practical welding tips, including grinding.
Pressure and Speed: Apply consistent moderate pressure and use the appropriate speed setting for the material and grinding disc.
Regular Maintenance: Ensure grinders and accessories are in good condition. Lincoln Electric provides maintenance tips.
Surface Preparation: Clean the workpiece before and after grinding to ensure the best weld quality.
Post-Grinding Inspection: Examine the workpiece for any missed spots or uneven surfaces.
By focusing on these fundamental aspects, welder fabricators can enhance their grinding techniques for better results and efficiency.
How to Display Grinding Techniques Skills on Your Resume
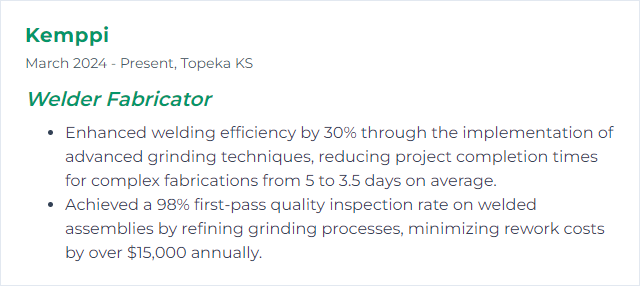
12. Safety Protocols
Safety protocols for a welder fabricator are guidelines and procedures designed to protect workers from hazards associated with welding and fabrication tasks, such as exposure to harmful fumes, burns, eye damage, and injuries from equipment use. These protocols encompass the use of personal protective equipment (PPE), proper ventilation, equipment maintenance, and adherence to safety standards and regulations.
Why It's Important
Safety protocols are crucial for a Welder Fabricator to prevent accidents, protect against harmful exposures, ensure the use of appropriate personal protective equipment, and maintain a safe working environment, ultimately minimizing the risk of injuries and health hazards associated with welding and fabrication tasks.
How to Improve Safety Protocols Skills
Improving safety protocols for a Welder Fabricator involves several key steps focused on training, equipment maintenance, and workspace management. Here's a concise guide:
Enhanced Training: Ensure all welders undergo regular safety training, including the latest techniques and knowledge on handling hazardous materials and emergency procedures. OSHA Training provides comprehensive resources.
Personal Protective Equipment (PPE): Mandate the use of appropriate PPE, like helmets with proper shading, fire-resistant clothing, gloves, and boots. Regular checks should be made to ensure their condition. The American Welding Society offers guidelines on the necessary PPE.
Ventilation and Fume Extraction: Implement effective ventilation systems or fume extraction solutions to minimize inhalation exposure. NIOSH has research and recommendations on ventilation systems.
Regular Equipment Maintenance: Schedule and document regular maintenance checks on welding equipment to prevent malfunctions that could pose safety risks. Lincoln Electric provides maintenance tips for welding equipment.
Workplace Safety Audits: Conduct periodic safety audits to identify and mitigate potential hazards in the work environment. The Occupational Safety and Health Administration (OSHA) offers guidelines for conducting effective safety audits.
Emergency Preparedness: Develop and regularly update emergency response plans, including fire safety protocols and first-aid procedures. Training resources can be found at Red Cross.
By focusing on these areas, welder fabricators can significantly enhance their safety protocols, creating a safer and more productive working environment.
How to Display Safety Protocols Skills on Your Resume
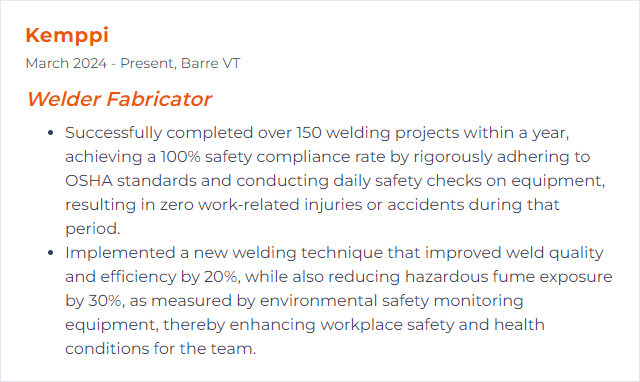