Top 12 Fabricator Skills to Put on Your Resume
In today's competitive job market, standing out as a skilled fabricator requires more than just the basics. Highlighting a robust set of technical and soft skills on your resume can significantly enhance your appeal to employers, making you a top candidate for fabrication positions across industries.
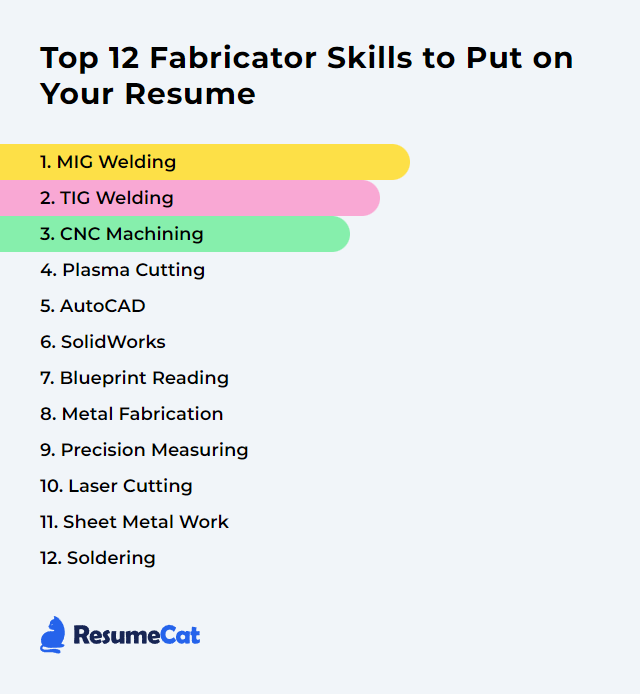
Fabricator Skills
- MIG Welding
- TIG Welding
- CNC Machining
- Plasma Cutting
- AutoCAD
- SolidWorks
- Blueprint Reading
- Metal Fabrication
- Precision Measuring
- Laser Cutting
- Sheet Metal Work
- Soldering
1. MIG Welding
MIG Welding, for a fabricator, is a versatile and efficient welding method where an electric arc forms between a consumable wire electrode and the workpiece, melting the metals and joining them as it continuously feeds the wire through a welding gun, using a protective gas shield to prevent contamination.
Why It's Important
MIG welding is important for a fabricator because it offers a versatile, fast, and efficient method to create strong, high-quality welds on a variety of metals, significantly enhancing productivity and the range of projects that can be undertaken.
How to Improve MIG Welding Skills
Improving MIG welding involves focusing on technique, equipment settings, and maintenance. Here's a concise guide:
Proper Preparation: Clean the workpiece to remove any contaminants. MillerWelds explains the importance of surface preparation.
Correct Equipment Settings: Adjust voltage and wire feed speed for material thickness. Lincoln Electric provides a guide on setting up your MIG welder.
Optimal Welding Technique: Maintain a consistent travel speed and angle. Hobart offers tips on technique improvement.
Choose the Right Gas and Wire: Use the appropriate shielding gas and wire type for your material. Welding-Direct provides a selection guide.
Practice: Regular practice improves skill and confidence. Consider different joint types and positions.
Equipment Maintenance: Keep your MIG welder and accessories clean and in good condition. Eastwood details maintenance tips.
Safety First: Always use proper safety gear and follow safe welding practices. OSHA outlines welding, cutting, and brazing safety guidelines.
By focusing on these areas, a fabricator can significantly improve their MIG welding quality and efficiency.
How to Display MIG Welding Skills on Your Resume

2. TIG Welding
TIG (Tungsten Inert Gas) welding, also known as GTAW (Gas Tungsten Arc Welding), is a precise welding process that uses a non-consumable tungsten electrode to produce the weld. It involves the use of an inert gas, typically argon, to shield the weld area from contamination. Ideal for thin materials and intricate work, TIG welding allows for strong, high-quality welds with clean finishes, making it a preferred method for precision fabrication tasks.
Why It's Important
TIG welding is crucial for fabricators because it provides precise, high-quality welds on a variety of metals, allowing for strong, clean joints in intricate and thin materials, essential for complex fabrication projects.
How to Improve TIG Welding Skills
To improve TIG welding, focus on the following concise tips:
- Equipment Check: Ensure your TIG welder settings are correct for the material. Regularly maintain equipment for optimal performance.
- Cleanliness: Clean all surfaces thoroughly before welding. Any contaminants can affect weld quality.
- Proper Shielding Gas: Use the correct type and flow rate of shielding gas (usually argon or an argon mix) for the material being welded. Miller Welds offers detailed guidance.
- Tungsten Electrode: Choose the right type and size of tungsten electrode for your application and ensure it's properly sharpened. Lincoln Electric provides insights into electrode selection.
- Practice Hand Control: Steady hand movement and control are crucial. Practice maintaining a consistent speed and arc length.
- Filler Rod Technique: Use the correct filler material and diameter. Feed the filler rod at a consistent speed and angle.
- Post-Weld Treatment: Understand the metallurgy of your materials to apply appropriate post-weld heat treatment if necessary.
- Safety First: Always use appropriate protective gear, including a welding helmet with the correct shade, gloves, and protective clothing.
Improving TIG welding skills comes down to practice, precision, and attention to detail. Visit the American Welding Society for further resources and certification programs.
How to Display TIG Welding Skills on Your Resume
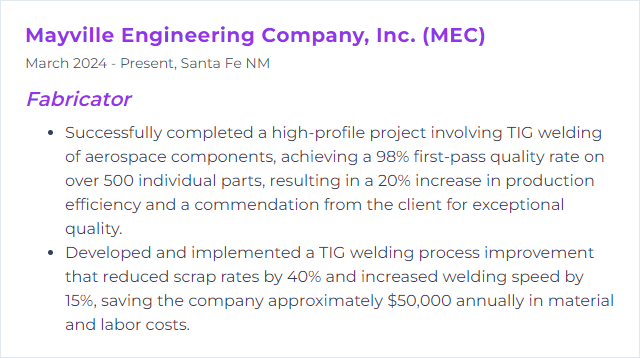
3. CNC Machining
CNC machining is a computer-controlled manufacturing process used by fabricators to precisely cut, mill, and drill materials into specific shapes and dimensions based on digital designs.
Why It's Important
CNC machining is crucial for a fabricator because it ensures precision, consistency, and efficiency in producing complex parts, allowing for high-quality fabrication with reduced material waste and labor costs.
How to Improve CNC Machining Skills
Improving CNC machining involves optimizing various aspects of the machining process to increase efficiency, accuracy, and part quality. For a fabricator, here are concise strategies to enhance CNC machining:
Material Selection: Choose materials that are suitable for the intended machining process and final application. Material properties affect machining speed, finish, and tool life. ASM International provides resources on material properties.
Tool Selection and Maintenance: Use the right cutting tools for the material and machining operation. Regularly inspect and maintain tools to ensure sharpness and precision. Sandvik Coromant offers insights into tool selection and maintenance.
Optimize Cutting Parameters: Adjust feed rate, spindle speed, depth of cut, and coolant flow to optimize cutting conditions. This reduces wear and improves surface finish. Machining Handbook can be a valuable resource for recommended parameters.
Programming Efficiency: Use efficient programming techniques and strategies to minimize machining time and improve part accuracy. Mastercam provides software and tips for efficient CNC programming.
Machine Maintenance: Perform regular maintenance on CNC machines to ensure they operate at peak efficiency. This includes lubrication, calibration, and checking for wear. Haas Automation offers maintenance tips.
Quality Control: Implement stringent quality control measures using precision measuring tools and software to detect and correct errors early in the machining process. Mitutoyo specializes in precision measuring equipment.
Training and Skills Development: Invest in ongoing training for operators and programmers to keep skills current with the latest machining technologies and techniques. Tooling U-SME provides online courses tailored for manufacturing professionals.
By focusing on these areas, fabricators can significantly improve the efficiency, accuracy, and output quality of their CNC machining operations.
How to Display CNC Machining Skills on Your Resume
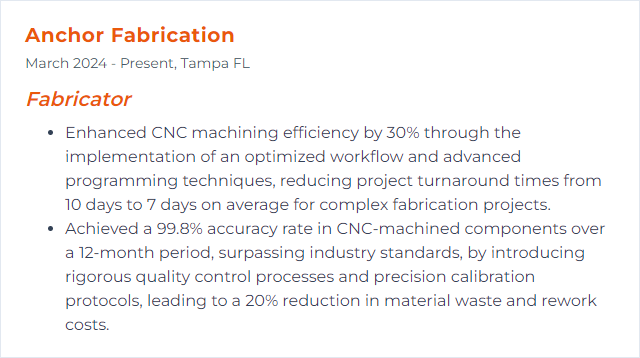
4. Plasma Cutting
Plasma cutting is a process used by fabricators to cut through electrically conductive materials by using an accelerated jet of hot plasma directed at the material to be cut. It's highly efficient for metal cutting, offering precision and speed for cutting steel, stainless steel, aluminum, and other metals.
Why It's Important
Plasma cutting is crucial for a fabricator because it offers rapid, precise cuts on various metals, enhancing efficiency and versatility in metal fabrication projects.
How to Improve Plasma Cutting Skills
To improve plasma cutting, a fabricator should focus on the following concise strategies:
Select the Right Equipment: Choose a plasma cutter that matches your material type and thickness requirements. Consider newer models with advanced features for improved precision and efficiency.
Maintain Proper Cutting Distance: Keep the torch at the correct distance from the workpiece. This distance varies with the type of torch and material but is typically around 1/8 inch (Lincoln Electric).
Use the Right Consumables: Select consumables that match your cutting application and replace them at the first sign of wear to maintain cut quality and prolong equipment life (Hypertherm).
Optimize Cutting Speed: Adjust the cutting speed for the material and thickness being cut. Too fast or too slow speeds can decrease cut quality. Refer to your equipment's guidelines for optimal speeds.
Ensure Good Air Quality: Use clean, dry air or nitrogen for plasma gas. Contaminated air can affect cut quality and consumable life. Installing an air filtration system can be beneficial (MillerWelds).
Proper Machine Setup and Maintenance: Regularly check and maintain your plasma cutter according to the manufacturer's guidelines. Ensure correct assembly of consumables and periodic inspection of all components.
Use CNC Technology: For repetitive cuts or complex shapes, consider using a CNC plasma cutting system. It can significantly improve cutting accuracy and efficiency (PlasmaCAM).
By focusing on these areas, a fabricator can achieve significant improvements in plasma cutting performance and outcomes.
How to Display Plasma Cutting Skills on Your Resume

5. AutoCAD
AutoCAD is a computer-aided design (CAD) software used by fabricators for drafting and designing detailed 2D or 3D structures, parts, and components, enabling precise fabrication planning and execution.
Why It's Important
AutoCAD is essential for fabricators as it allows for precise design and modification of plans, ensuring accuracy in measurements and cuts, ultimately leading to efficient material use and high-quality fabrications.
How to Improve AutoCAD Skills
Improving AutoCAD performance and efficiency, especially for a fabricator, involves optimizing settings, customizing tool palettes, utilizing external references (Xrefs), and integrating add-ons for fabrication-specific tasks. Here's a concise guide:
Optimize Settings: Adjust AutoCAD settings for performance. This includes reducing the graphic settings, managing file paths for quicker access to frequently used files, and optimizing the use of layers.
Custom Tool Palettes: Create custom tool palettes tailored to fabrication processes. This streamlines workflow by having frequently used blocks, commands, and tools readily available. Autodesk Help
Use External References (Xrefs): For large projects, using Xrefs can significantly reduce file size and improve performance by linking to external files without embedding them. External References Guide
LISP Routines for Automation: Automate repetitive tasks specific to fabrication using AutoLISP. This can drastically reduce manual input and errors, increasing efficiency. AutoLISP
Fabrication CADmep Integration: For those involved in MEP fabrication, integrating AutoCAD with Fabrication CADmep can streamline the creation of accurate fabrications drawings and models. Fabrication CADmep
Hardware Optimization: Ensure your hardware meets or exceeds Autodesk’s recommended system requirements for AutoCAD. Upgrading hardware components like SSDs, RAM, and graphic cards can offer significant performance improvements. System Requirements
Training and Continual Learning: Stay updated with the latest AutoCAD features and best practices through Autodesk’s official training resources or other reputable training platforms. Proficiency in software use directly impacts the quality and efficiency of output. Autodesk Learning
By focusing on these areas, fabricators can leverage AutoCAD more effectively, leading to improved productivity, accuracy, and project turnaround times.
How to Display AutoCAD Skills on Your Resume
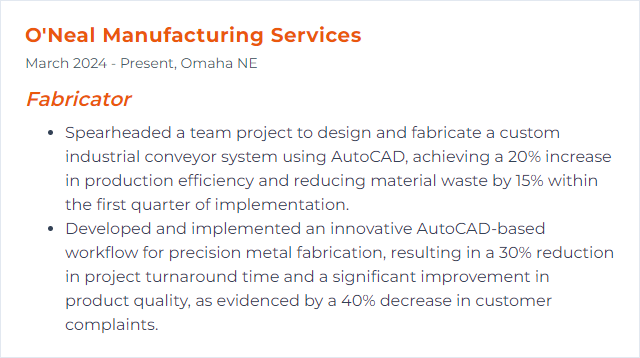
6. SolidWorks
SolidWorks is a computer-aided design (CAD) and engineering software used by fabricators to create detailed 3D models and drawings of parts and assemblies for manufacturing and assembly processes.
Why It's Important
SolidWorks is crucial for a fabricator because it enables precise 3D modeling and simulation of designs, ensuring accuracy, reducing material waste, and streamlining the fabrication process.
How to Improve SolidWorks Skills
Improving SolidWorks proficiency, especially for a fabricator, involves focusing on mastering features that streamline design-to-fabrication processes, enhance precision, and improve collaboration. Here are concise steps with resources:
Learn SolidWorks Sheet Metal Tools: Master the Sheet Metal module to efficiently design parts ready for fabrication. SolidWorks Sheet Metal Training
Utilize Weldments: Understand how to use the Weldments tool for creating welded structures with standard profiles. Weldments Training
Customize Material Database: Customize the material database for accurate material selection specific to your fabrication processes. Customize Material Database Guide
Implement Design for Manufacturing (DFM): Use DFM principles and SolidWorks DFMXpress to anticipate and solve manufacturing challenges early in the design phase. DFMXpress Tutorial
Use 3D Interconnect for Collaboration: Employ 3D Interconnect to work seamlessly with CAD files from other systems, improving collaboration with clients and suppliers. 3D Interconnect Overview
Explore SolidWorks CAM: Leverage SolidWorks CAM for integrated manufacturing planning and programming, from design to CNC machining. SolidWorks CAM Training
Practice and Certification: Regular practice and obtaining SolidWorks certifications can validate your skills and keep you updated on the latest features. Certification Program
By focusing on these areas, a fabricator can significantly improve their SolidWorks skills, leading to more efficient and accurate fabrication processes.
How to Display SolidWorks Skills on Your Resume
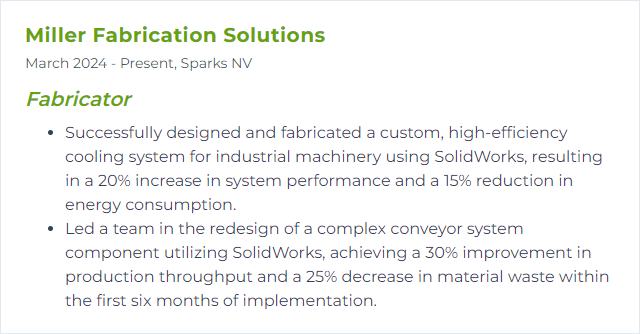
7. Blueprint Reading
Blueprint reading for a fabricator involves interpreting and understanding technical drawings and diagrams that specify dimensions, materials, and construction methods for manufacturing components or structures, ensuring accurate fabrication according to design specifications.
Why It's Important
Blueprint reading is crucial for a fabricator because it ensures precise understanding and execution of the design specifications, materials, and measurements necessary to construct or assemble a product accurately and efficiently.
How to Improve Blueprint Reading Skills
Improving blueprint reading skills is essential for a fabricator to ensure accuracy and efficiency in their work. Here's a concise guide:
Understand Basic Symbols and Notations: Familiarize yourself with the common symbols, lines, and notations used in blueprints. Engineering.com offers resources and articles that can help you get started.
Learn the Different Types of Views: Understand how to interpret plan, elevation, section, and detail views. The American Design Drafting Association (ADDA) provides guidelines and standards for drafting views.
Study Dimensions and Tolerances: Pay attention to dimensions, tolerances, and scales to ensure precise fabrication. Thomasnet has articles and resources that can deepen your understanding.
Practice Regularly: Apply your knowledge by practicing with real or sample blueprints. Websites like MyBlueprinter offer practice blueprints for various industries.
Take a Course: Consider enrolling in a blueprint reading course specific to your field. Coursera and Udemy offer online courses that cater to different learning needs.
Improvement comes with time and continuous learning, so make use of these resources and keep practicing.
How to Display Blueprint Reading Skills on Your Resume

8. Metal Fabrication
Metal fabrication is the process of cutting, shaping, and assembling metal materials to create structures or components. A fabricator performs these tasks to produce finished metal products or parts according to specified designs or blueprints.
Why It's Important
Metal fabrication is crucial because it allows fabricators to cut, shape, and assemble metal structures and components, enabling the creation of a vast array of products used in construction, machinery, transportation, and many other industries, thus playing a vital role in the global economy and technological advancement.
How to Improve Metal Fabrication Skills
Improving metal fabrication involves enhancing efficiency, quality, and safety. Here's a concise guide:
Adopt Lean Manufacturing: Streamline production processes to minimize waste and increase productivity. Learn more about Lean Manufacturing.
Invest in Technology: Utilize advanced machinery like CNC machines, laser cutters, and welding robots for precision and speed. Explore the latest in Fabrication Technology.
Implement CAD/CAM Software: Use computer-aided design and manufacturing software for accurate designs and reduced errors. CAD/CAM Software Information.
Continuous Training: Regularly update the skills of your workforce to keep up with new technologies and methodologies. Training Resources.
Quality Control: Adopt stringent quality control measures to ensure product consistency and reduce wastage. Quality Control Tips.
Safety Measures: Prioritize safety to prevent accidents and maintain a healthy workforce. OSHA Guidelines for Metal Fabrication.
Sustainable Practices: Opt for eco-friendly materials and processes to reduce environmental impact. Sustainability in Fabrication.
By focusing on these areas, a fabricator can significantly improve their metal fabrication process.
How to Display Metal Fabrication Skills on Your Resume
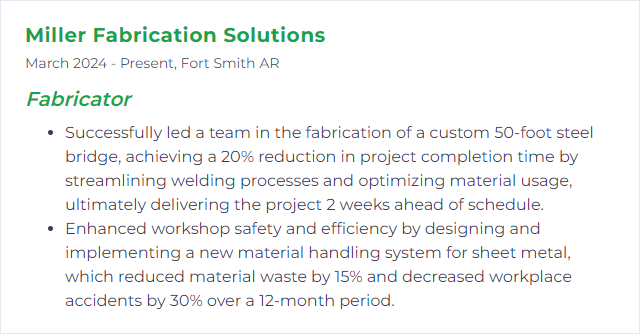
9. Precision Measuring
Precision measuring in the context of a fabricator refers to the use of specialized tools and techniques to obtain highly accurate measurements of materials and components, ensuring they meet exact specifications for fabrication processes.
Why It's Important
Precision measuring ensures that components are fabricated with exact dimensions, leading to a perfect fit, optimal performance, and high-quality final products. This minimizes material waste, reduces rework costs, and maintains customer satisfaction by delivering products that meet specified requirements.
How to Improve Precision Measuring Skills
Improving precision measuring in fabrication involves adopting practices and tools that enhance accuracy and repeatability. Here's a concise guide:
Calibrate Tools Regularly: Ensure measuring tools are calibrated according to the manufacturer's guidelines to maintain accuracy.
Use Appropriate Tools: Select the right measuring tool for the task, considering the level of precision required. Options range from calipers and micrometers to more sophisticated digital measuring devices.
Maintain a Controlled Environment: Environmental factors like temperature and humidity can affect measurements. Maintain a stable environment where possible, or account for variations.
Implement Quality Control Checks: Regularly perform quality control checks throughout the fabrication process to catch and correct errors early.
Educate and Train Staff: Ensure all team members are trained in precision measurement techniques, including the proper use and care of tools.
Adopt Digital Measurement Tools: Consider integrating digital measurement tools that offer higher precision and can easily interface with digital fabrication equipment.
Standardize Measurement Processes: Develop and follow standardized measurement processes to reduce variability and improve repeatability.
By focusing on these areas, fabricators can significantly improve the precision of their measurements, leading to better quality and efficiency in their work.
How to Display Precision Measuring Skills on Your Resume
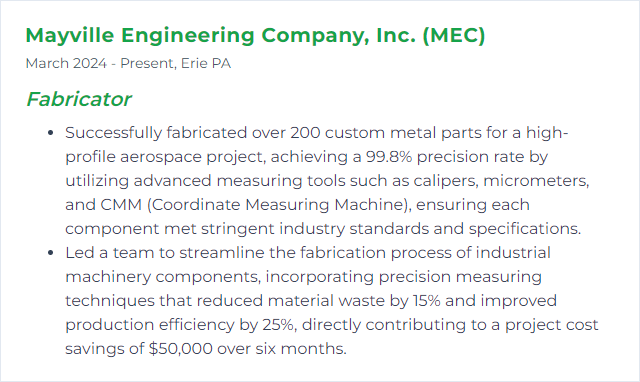
10. Laser Cutting
Laser cutting is a precision fabrication technique that uses a high-powered laser to cut or engrave materials into specific shapes, designs, or patterns, offering high accuracy and clean finishes.
Why It's Important
Laser cutting is important for a fabricator because it provides precise, clean, and fast cuts on a variety of materials, enabling highly detailed and complex designs with minimal waste and reduced production time.
How to Improve Laser Cutting Skills
Improving laser cutting involves optimizing various parameters and adopting best practices. Here are concise strategies for a fabricator:
Material Preparation: Ensure materials are clean and flat. Pre-clean surfaces to remove any contaminants that can affect cut quality.
Proper Material Handling: Use appropriate support to minimize vibrations and movements during cutting. Material handling systems can streamline this process.
Optimal Laser Settings: Adjust the laser power, speed, frequency (pulse), and focus according to the material type and thickness. Trumpf's TruTops Boost software can help optimize these settings.
Regular Maintenance: Perform routine checks and maintenance on the laser cutter. Clean lenses and mirrors, check alignments, and ensure the gas flow is correct. Amada provides maintenance services and guidelines.
Using Quality Assist Gases: The right type and purity of assist gas (e.g., nitrogen, oxygen) can significantly affect the cut quality. BOC's guide offers insights on choosing assist gases.
Software for Nesting and Path Optimization: Utilize advanced nesting software to minimize waste and optimize cutting paths. SigmaNEST is an example of software that can improve efficiency and material utilization.
Training and Experience: Invest in training for operators. Understanding the intricacies of laser cutting machines and materials can greatly improve outcomes. The Fabricators & Manufacturers Association, Intl. offers courses and certifications.
Implementing these strategies can lead to improved efficiency, quality, and cost-effectiveness in laser cutting operations.
How to Display Laser Cutting Skills on Your Resume
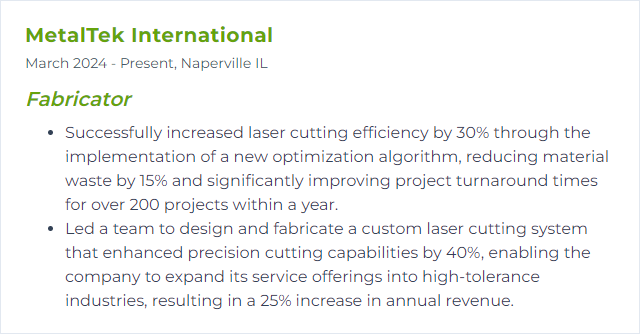
11. Sheet Metal Work
Sheet metal work involves cutting, bending, shaping, and assembling metal sheets into various parts and products, typically performed by a fabricator using specialized tools and machinery.
Why It's Important
Sheet metal work is crucial for a fabricator as it involves cutting, bending, and assembling metal to create diverse and precise parts for machinery, structures, and products, enabling the production of high-quality, durable, and customizable solutions for various industries.
How to Improve Sheet Metal Work Skills
Improving sheet metal work involves enhancing precision, efficiency, and quality in fabrication processes. Here are concise strategies for a fabricator:
Upgrade Equipment: Invest in modern machinery like precision laser cutters and CNC press brakes for higher accuracy and speed. Laser Cutting Guide.
Software Solutions: Utilize CAD/CAM software for precise design and programming, reducing errors and material waste. AutoCAD.
Skill Enhancement: Regular training for workers on the latest techniques and machinery helps in improving work quality. Fabricators & Manufacturers Association Intl.
Quality Materials: Use high-grade materials to ensure the longevity and durability of the fabricated products. Material Selection Guide.
Lean Manufacturing: Implement lean manufacturing principles to minimize waste and optimize workflow for better productivity. Lean Production.
Regular Maintenance: Ensure machinery and tools are well-maintained to prevent downtime and preserve precision. Maintenance Tips.
Quality Control: Adopt strict quality control measures at every stage of the fabrication process to ensure the highest standards. ISO Standards.
By focusing on these areas, a fabricator can significantly improve the efficiency, accuracy, and quality of sheet metal work.
How to Display Sheet Metal Work Skills on Your Resume
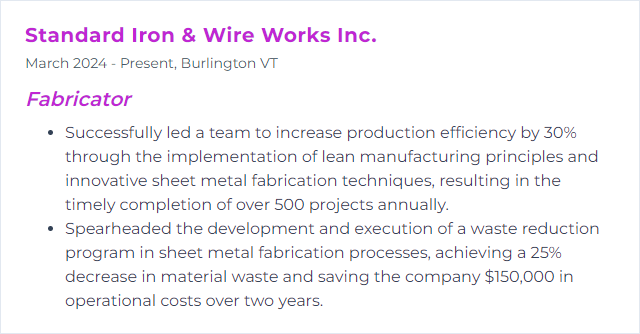
12. Soldering
Soldering is a process used by fabricators to join metal parts together by melting a filler metal, called solder, into the joint. The solder cools to form a strong electrical and mechanical connection.
Why It's Important
Soldering is crucial for a fabricator as it provides a reliable and precise method to join metal components, ensuring electrical connectivity and mechanical strength in electronic assemblies and fabricated metal products.
How to Improve Soldering Skills
Improving your soldering technique as a fabricator involves practice, precision, and the right tools. Follow these concise steps:
Use High-Quality Solder and Tools: Opt for a soldering iron with adjustable temperature and lead-free solder. SparkFun Electronics has a good selection.
Proper Iron Care: Keep the tip of your soldering iron clean and tinned. Adafruit’s guide offers excellent tips on care.
Correct Temperature: Use the right temperature for your solder; too hot can damage components, while too cold can lead to poor joints. EEVblog discusses finding the perfect balance.
Flux is Your Friend: Use quality solder flux to improve the flow and adhesion of your solder. This guide from Electronics Hub explains how.
Practice Makes Perfect: Practice on spare components or a practice PCB. Techniques improve with experience.
Inspect Your Work: Use a magnifying glass or a microscope to check your solder joints. This tutorial from IPC explains what good solder joints look like.
Continuous Learning: Stay updated with soldering techniques by following forums like Reddit’s r/soldering and Instructables.
Remember, each component and circuit board is unique, so adjust your technique as needed for the best results.
How to Display Soldering Skills on Your Resume
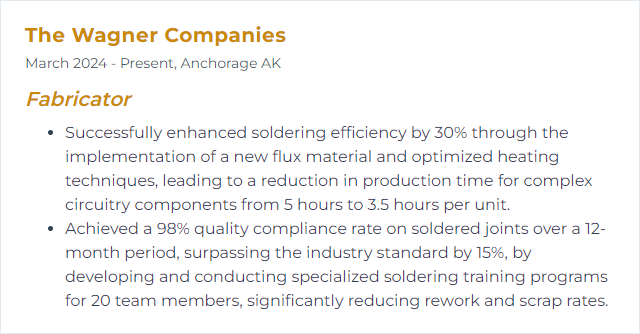