Top 12 Metal Fabricator Skills to Put on Your Resume
In the competitive field of metal fabrication, showcasing a strong set of specialized skills on your resume can significantly elevate your chances of securing your desired position. This article highlights the top 12 skills that employers in the metal fabrication industry value most, setting you apart from other candidates and demonstrating your proficiency and adaptability in this dynamic workspace.
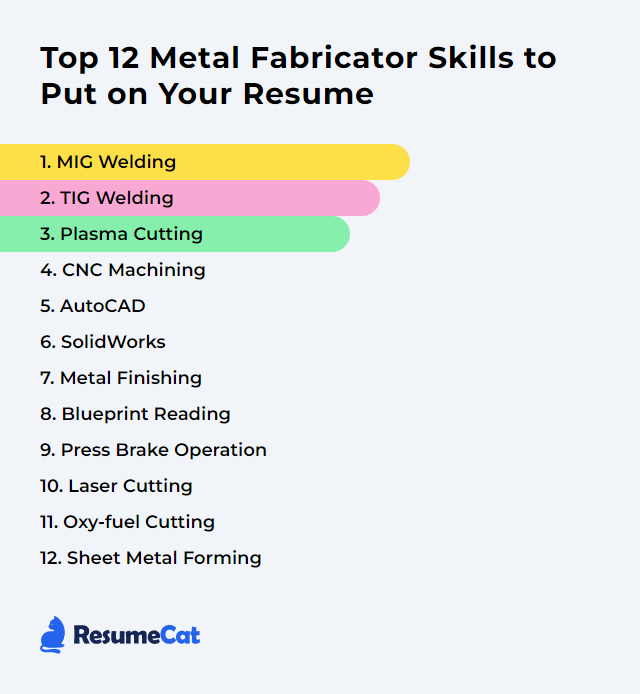
Metal Fabricator Skills
- MIG Welding
- TIG Welding
- Plasma Cutting
- CNC Machining
- AutoCAD
- SolidWorks
- Metal Finishing
- Blueprint Reading
- Press Brake Operation
- Laser Cutting
- Oxy-fuel Cutting
- Sheet Metal Forming
1. MIG Welding
MIG Welding, also known as Gas Metal Arc Welding (GMAW), is a process where an electric arc forms between a consumable wire electrode and the metal workpiece, melting the metals and joining them together. It is commonly used by metal fabricators for its versatility, efficiency, and the high-quality welds it produces on a variety of metals.
Why It's Important
MIG welding is important for a Metal Fabricator because it offers a fast, efficient, and versatile method for joining metals with high strength and excellent finish, suitable for both thin and thick materials.
How to Improve MIG Welding Skills
Improving MIG welding involves refining technique, equipment maintenance, and selecting appropriate materials. Here are concise tips:
Maintain a Consistent Speed and Angle: Keep the welding gun at a 15-20 degree angle to the workpiece and move at a consistent speed for even welds. Lincoln Electric offers detailed guidelines.
Proper Equipment Setup: Ensure your MIG welder is correctly set up, including wire feed speed and power settings based on the material you're welding. Miller Welds provides a comprehensive setup guide.
Use the Right Gas and Material: Argon and CO2 gas mixtures are commonly used for MIG welding. The choice of wire is crucial too, with ER70S-3 being a common choice for all-purpose welding. Hobart Brothers offers insights on material selection.
Regular Equipment Maintenance: Keep your welder and accessories in top condition. This includes regularly checking and replacing the contact tip, ensuring the wire feeds smoothly, and keeping the nozzle clean. Welding Tips and Tricks discusses maintenance and troubleshooting.
Practice and Training: Continuous practice and learning are key to mastering MIG welding. Consider formal training or online tutorials to enhance your skills. American Welding Society (AWS) offers resources and certifications for welders.
By focusing on these areas, you can significantly improve the quality of your MIG welding projects.
How to Display MIG Welding Skills on Your Resume
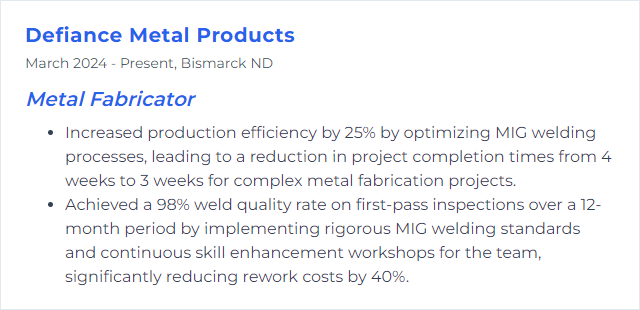
2. TIG Welding
TIG welding, short for Tungsten Inert Gas welding, is a precision welding process that uses a non-consumable tungsten electrode to produce the weld. It is characterized by the use of an inert gas, typically argon, to shield the welding area from contamination. This method allows for greater control over the weld, making it suitable for thin materials and high-quality, clean welds. It's widely used in metal fabrication for stainless steel, aluminum, and other metals where finish and detail are important.
Why It's Important
TIG welding is crucial for a metal fabricator because it provides high-quality, precise welds on a variety of metals, allowing for strong, clean joins even in intricate or delicate projects.
How to Improve TIG Welding Skills
Improving TIG welding involves several key practices and considerations for metal fabricators aiming for high-quality welds. Here are concise tips:
Preparation: Ensure the metal surfaces and tungsten electrode are clean and free from contaminants. Use a dedicated stainless steel brush for cleaning the metal surfaces.
Equipment Check: Regularly inspect your TIG welder, cables, and torch for any damage. Ensure your gas flow is correctly set for the type of metal you're welding.
Proper Technique: Maintain a consistent angle and distance between the tungsten electrode and the workpiece. Focus on steady hand movement and uniform travel speed to avoid uneven welds.
Tungsten Electrode Choice: Select the correct type and size of tungsten electrode for the material being welded. Sharpen the electrode appropriately for the type of weld required.
Practice: Consistent practice on scrap material will help improve hand steadiness, control, and overall welding technique.
For more detailed guidance, consider exploring resources from reputable welding organizations and manufacturers:
Remember, safety is paramount. Always wear appropriate protective gear and work in a well-ventilated area.
How to Display TIG Welding Skills on Your Resume
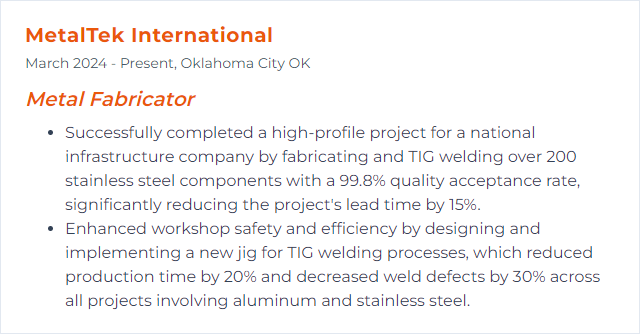
3. Plasma Cutting
Plasma cutting is a process used by metal fabricators to cut through electrically conductive materials by using a jet of hot plasma. It provides precise cuts on metals such as steel, stainless steel, aluminum, brass, and copper, making it ideal for fabrication tasks requiring detailed shapes and high-quality edges.
Why It's Important
Plasma cutting is crucial for a metal fabricator because it offers a fast, precise, and efficient method for cutting various types of metals, allowing for intricate shapes and designs, enhancing productivity, and reducing material waste.
How to Improve Plasma Cutting Skills
Improving plasma cutting quality and efficiency involves optimizing cutting parameters, maintaining equipment, and utilizing advanced technology. Here's a concise guide:
Select Appropriate Cutting Parameters: Adjust cutting speed, power settings, and gas flow based on material type and thickness for optimal cuts. Hypertherm offers detailed cut charts for specific settings.
Maintain Equipment Regularly: Perform routine inspections and maintenance on your plasma cutter and components. Regularly check and replace consumables to prevent poor cut quality. Lincoln Electric provides maintenance tips for plasma systems.
Use CNC Technology: Integrating CNC (Computer Numerical Control) with plasma cutting enhances precision and repeatability. Messer Cutting Systems specializes in CNC plasma cutting solutions.
Implement Proper Cutting Techniques: Maintain correct torch height, angle, and movement speed. Educate operators on best practices. MillerWelds offers practical plasma cutting tips.
Choose High-Quality Consumables: Invest in high-quality torches and consumables for longer life and better performance. ESAB discusses how selecting the right consumables can improve performance.
Utilize Software Solutions: Software for design and process optimization can streamline operations and reduce waste. SigmaNEST is an example of software that improves efficiency in metal fabrication.
By focusing on these areas, metal fabricators can achieve significant improvements in plasma cutting performance and output quality.
How to Display Plasma Cutting Skills on Your Resume
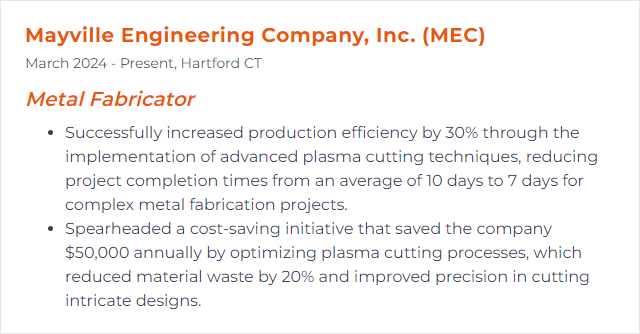
4. CNC Machining
CNC machining is a manufacturing process where pre-programmed computer software dictates the movement of factory tools and machinery, allowing for precise cutting, milling, and shaping of metal materials into finished parts or products.
Why It's Important
CNC machining is crucial for a metal fabricator because it allows for precise, consistent, and efficient production of complex metal parts, optimizing both quality and productivity.
How to Improve CNC Machining Skills
Improving CNC machining for a metal fabricator involves enhancing precision, efficiency, and productivity through various strategies. Here are concise tips:
Optimize Tool Paths: Use advanced CAD/CAM software to create efficient and precise tool paths, reducing machining time and wear on tools.
Use High-Quality Tools: Invest in high-quality cutting tools designed for the specific materials you're working with to improve performance and finish.
Implement Regular Maintenance: Schedule regular maintenance routines for your CNC machines to prevent downtime and ensure consistent accuracy.
Upgrade CNC Machine Components: Consider upgrading components such as spindle, tool holders, and fixtures for better precision and efficiency. Renishaw offers advanced solutions for enhancing machine performance.
Adopt Lean Manufacturing Principles: Streamline your manufacturing process to reduce waste and improve productivity, focusing on continuous improvement.
Train Your Workforce: Ensure your operators and programmers are well-trained on the latest CNC technologies and techniques for optimal machine utilization.
Use Predictive Maintenance Tools: Leverage IoT and predictive maintenance tools to preemptively address machine issues before they cause downtime.
By focusing on these areas, metal fabricators can significantly improve their CNC machining operations.
How to Display CNC Machining Skills on Your Resume
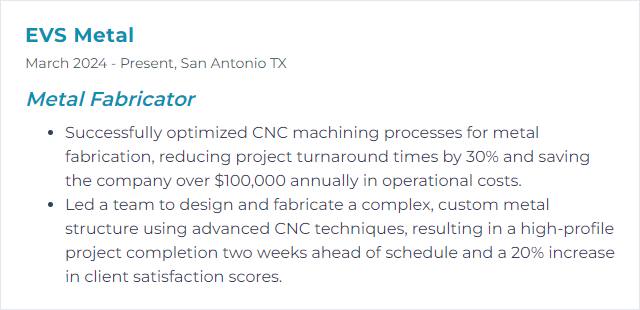
5. AutoCAD
AutoCAD is a computer-aided design (CAD) software used by metal fabricators to create precise 2D and 3D drawings and models of metal parts and assemblies for manufacturing and construction purposes.
Why It's Important
AutoCAD is crucial for metal fabricators because it allows for precise and efficient design, planning, and modification of metal components, ensuring accuracy, minimizing material waste, and streamlining the fabrication process.
How to Improve AutoCAD Skills
Improving AutoCAD efficiency for a metal fabricator involves enhancing precision, speed, and collaboration. Here are concise strategies:
Customize Tool Palettes: Tailor AutoCAD's interface to include tools and commands you frequently use, streamlining your workflow. Autodesk's guide on customizing tool palettes can help.
Use AutoLISP for Automation: Automate repetitive tasks specific to metal fabrication through AutoLISP scripts. Autodesk provides resources on getting started with AutoLISP.
Implement Sheet Sets: Organize your drawings into sheet sets for efficient management and printing. This Sheet Set Manager tutorial is useful.
Leverage Data Extraction: Extract object data to tables for accurate part lists and material estimates. Learn how through this data extraction guide.
Utilize CAD Standards: Ensure consistency across drawings with CAD standards, crucial for collaboration and quality control. See Autodesk's CAD standards tool.
Invest in Training: Regularly update skills through Autodesk's AutoCAD training and certification programs.
Collaborate in the Cloud: Use AutoCAD's cloud capabilities for seamless collaboration with project stakeholders. Explore AutoCAD's cloud collaboration.
By implementing these strategies, a metal fabricator can significantly enhance their AutoCAD efficiency, ensuring more accurate and faster project completions.
How to Display AutoCAD Skills on Your Resume
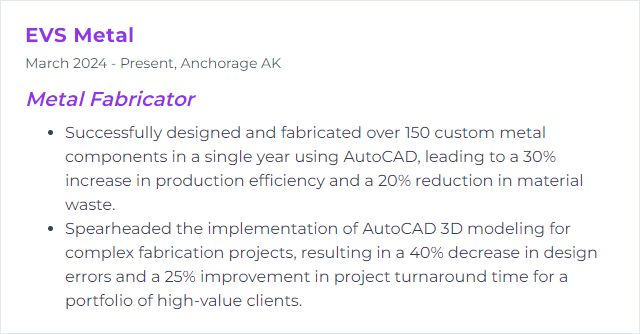
6. SolidWorks
SolidWorks is a computer-aided design (CAD) and engineering software used by metal fabricators to create, simulate, and manage 3D models and drawings of metal parts and assemblies, facilitating design, visualization, and manufacturing processes.
Why It's Important
SolidWorks is important for a Metal Fabricator as it allows for precise 3D modeling and simulation of metal parts and assemblies, ensuring accuracy and efficiency in fabrication processes, and reducing material waste and production time.
How to Improve SolidWorks Skills
Improving your SolidWorks skills as a metal fabricator involves focusing on specific features and workflows that streamline the design-to-fabrication process. Here are concise tips with resources for deeper exploration:
Master Sheet Metal Tools: Understanding the Sheet Metal tools in SolidWorks allows for efficient design of metal parts. Learn to use the Base Flange, Edge Flange, and Miter Flange features for accurate fabrication-ready designs. SolidWorks Sheet Metal Tutorial.
Utilize Weldments: SolidWorks Weldments streamline the creation of welded structures with a comprehensive library of standard profiles. Mastering these can significantly reduce design time. Weldments Training.
Work with 3D Sketching: For complex metal fabrications, 3D sketching can simplify the creation of wireframes for paths and frameworks. Improve your 3D sketching skills for better modeling of custom parts. 3D Sketching Guide.
Customize Material Properties: Accurate material properties ensure realistic simulation and weight estimation. Learn to customize and apply materials reflecting those used in metal fabrication. Material Database Customization.
Leverage Assembly Features: For metal fabricators, understanding how different parts will fit together is crucial. Use SolidWorks Assembly features to check fit, clearance, and functionality. Assembly Modeling.
Optimize for CNC Machining: Familiarize yourself with features and design considerations specific to CNC machining. This includes understanding tolerances, surface finishes, and suitable geometries for machining. CNC Machining Best Practices.
Invest in Training and Certification: Continuous learning is key. SolidWorks offers specific training courses and certifications that can enhance your expertise as a metal fabricator. SolidWorks Training and Certification.
By focusing on these areas and taking advantage of the resources provided, metal fabricators can significantly improve their proficiency and efficiency in using SolidWorks for their projects.
How to Display SolidWorks Skills on Your Resume
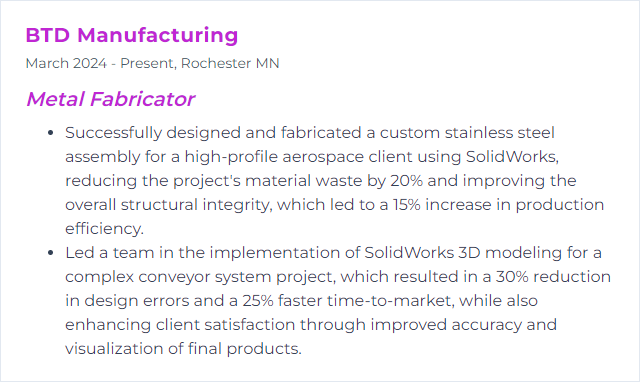
7. Metal Finishing
Metal finishing is the process of applying a coating or altering the surface of a metal component to enhance its durability, appearance, corrosion resistance, or electrical conductivity. For a metal fabricator, it is a crucial final step to ensure the product meets specific performance and aesthetic requirements.
Why It's Important
Metal finishing is crucial for a metal fabricator as it enhances the durability, corrosion resistance, and aesthetic appeal of metal products, while also improving surface properties for better adhesion or electrical conductivity.
How to Improve Metal Finishing Skills
Improving metal finishing involves several strategies aimed at enhancing the quality, durability, and appearance of metal products. Here are concise tips for a metal fabricator to improve metal finishing:
Surface Preparation: Ensure thorough cleaning and preparation of the metal surface. Use appropriate methods like sandblasting, pickling, or chemical cleaning to remove impurities. Surface Preparation Guidelines.
Choose the Right Technique: Select the most suitable finishing technique based on the metal type and desired outcome. Common methods include electroplating, powder coating, and anodizing. Explore different methods in Metal Finishing Techniques.
Control Process Parameters: Precisely control parameters like temperature, voltage, and time during finishing processes. This ensures consistency and quality in the final finish. Learn more about parameter control in Electroplating Essentials.
Use High-Quality Materials: Employ high-quality chemicals, coatings, and consumables. The quality of these materials significantly affects the finish. Materials Selection in Metal Finishing.
Regular Equipment Maintenance: Maintain and calibrate finishing equipment regularly to ensure optimal performance and avoid defects. Maintenance Best Practices.
Implement Quality Control: Incorporate stringent quality control measures at each stage of the finishing process. This includes visual inspections and using thickness gauges. Quality Control in Metal Finishing.
Employee Training: Invest in training for employees to keep them updated on the latest techniques and safety standards in metal finishing. Metal Finishing Training Resources.
By focusing on these key areas, a metal fabricator can significantly improve the quality and efficiency of their metal finishing processes.
How to Display Metal Finishing Skills on Your Resume
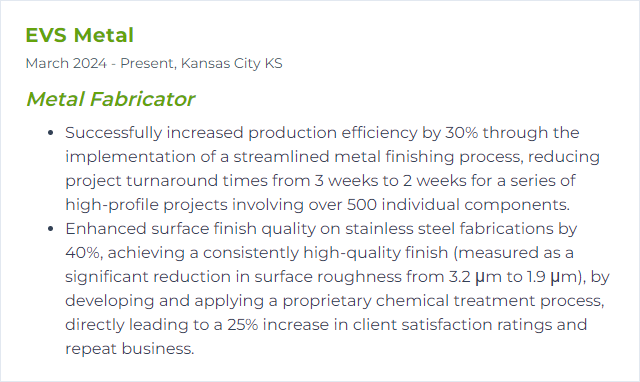
8. Blueprint Reading
Blueprint reading for a metal fabricator involves interpreting and understanding detailed technical drawings and diagrams that specify the design, dimensions, materials, and processes required to fabricate metal products or components. This skill enables fabricators to accurately cut, shape, and assemble metal parts as per the specifications outlined in the blueprints.
Why It's Important
Blueprint reading is essential for a metal fabricator because it enables precise interpretation of design specifications and dimensions necessary to accurately cut, shape, and assemble metal parts, ensuring the final product meets the required standards and fits perfectly with other components.
How to Improve Blueprint Reading Skills
Improving blueprint reading skills, especially for a Metal Fabricator, involves understanding symbols, dimensions, and specifications unique to metal fabrication and engineering drawings. Here are concise steps and resources to guide you:
Familiarize with Basic Symbols and Notations: Learn the standard symbols and notations used in metal fabrication drawings. The Fabricator offers resources and articles that can help you understand these basics.
Understand Scales and Dimensions: Practice reading and interpreting different scales and dimensions used in blueprints. The Engineers Edge provides tutorials and tools for engineering fundamentals.
Study Technical Drawings: Examine various technical drawings related to metal fabrication to get accustomed to the diversity in blueprints. Engineering.com has a library of technical drawings and design resources.
Take a Course: Consider enrolling in a course specifically designed for blueprint reading in metal fabrication. LinkedIn Learning offers courses that cover a wide range of topics, including blueprint reading.
Practice Regularly: Regular practice is key. Try interpreting different blueprints, starting with simple ones and gradually moving to more complex drawings.
By combining these resources and continuously practicing, you'll improve your blueprint reading skills tailored to metal fabrication.
How to Display Blueprint Reading Skills on Your Resume
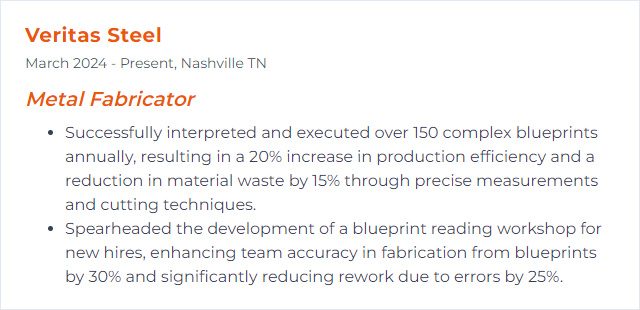
9. Press Brake Operation
Press brake operation involves using a press brake machine to bend and shape metal sheets into specific angles or forms by applying force through a top die pushing the metal into a bottom die, enabling precise and custom metal fabrication.
Why It's Important
Press brake operation is crucial for a metal fabricator because it allows for precise bending and shaping of metal sheets and plates, enabling the creation of complex parts and structures with high accuracy and efficiency.
How to Improve Press Brake Operation Skills
Improving press brake operation for a metal fabricator involves enhancing efficiency, accuracy, and safety during the bending process. Here are concise strategies:
Proper Training: Ensure operators are well-trained in modern bending techniques and understand the machinery's capabilities and limitations.
Regular Maintenance: Implement a regular maintenance schedule to prevent breakdowns and ensure the machine operates at peak performance.
Use of Correct Tooling: Select the appropriate tooling for the material and job. Tooling choice can significantly affect bend accuracy and finish quality.
Software Utilization: Leverage CAD/CAM software for precise bending simulations and efficient programming, reducing waste and improving part consistency.
Material Preparation: Ensure materials are properly prepared and free of lubricants or other substances that might affect bending accuracy or cause tooling damage.
Optimize Machine Settings: Adjust and fine-tune the press brake settings according to the specific job requirements. This includes ram speed, backgauge position, and pressure adjustments.
By focusing on these aspects, a metal fabricator can significantly improve the operation of their press brake, leading to increased productivity, better-quality bends, and reduced operational costs.
How to Display Press Brake Operation Skills on Your Resume
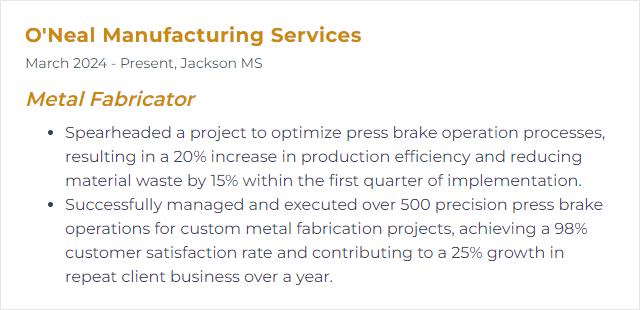
10. Laser Cutting
Laser cutting is a precision fabrication process that uses a high-powered laser beam to cut or engrave materials, such as metals, with high accuracy and speed, producing clean and precise edges.
Why It's Important
Laser cutting is important for a metal fabricator because it allows for precise, efficient, and versatile cutting of various metals, enabling high-quality production with reduced waste and increased speed.
How to Improve Laser Cutting Skills
Improving laser cutting for a metal fabricator involves enhancing precision, speed, and material efficiency. Here are concise strategies:
Optimize Laser Parameters: Adjust the laser power, cutting speed, and focus position based on the material type and thickness. This article from The Fabricator offers insights on optimizing settings for different materials.
Use High-Quality Assist Gas: High-purity assist gases (like nitrogen or oxygen) can improve cut quality and speed. This SPI Lasers guide discusses their effects on laser cutting performance.
Maintain Laser System: Regular maintenance of the laser system, including cleaning of lenses and mirrors and checking the alignment, ensures consistent cutting quality. TRUMPF provides maintenance guidelines for laser systems.
Implement Automated Nesting Software: Use advanced nesting software to maximize material utilization and reduce waste. SigmaNEST is an example of software that optimizes layout.
Upgrade to Fiber Laser Technology: If using CO2 lasers, consider upgrading to fiber lasers for faster cutting speeds, lower maintenance, and better efficiency with metals. This comparison by Lincoln Electric highlights the advantages of fiber lasers.
Train Operators: Ensure operators are well-trained on the latest laser cutting techniques and software functionalities. Continuous education can lead to more efficient operation and troubleshooting skills.
By focusing on these areas, a metal fabricator can significantly improve the efficiency, quality, and profitability of their laser cutting operations.
How to Display Laser Cutting Skills on Your Resume
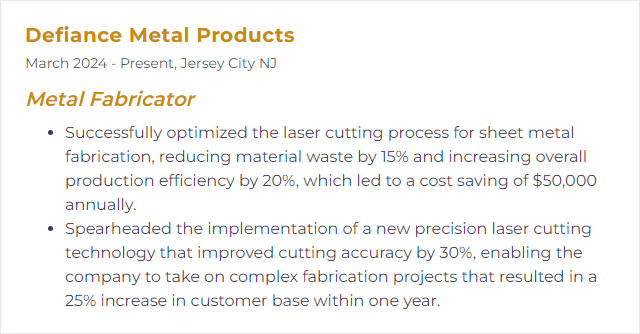
11. Oxy-fuel Cutting
Oxy-fuel cutting is a process used by metal fabricators to cut through steel and other alloys by utilizing a flame produced by a mix of oxygen and a fuel gas, typically acetylene. The metal is preheated to its ignition temperature then rapidly oxidized by a stream of pure oxygen, resulting in a precise and clean cut.
Why It's Important
Oxy-fuel cutting is crucial for a metal fabricator as it enables precise and efficient cutting of thick metals, essential for shaping materials accurately in fabrication projects.
How to Improve Oxy-fuel Cutting Skills
Improving oxy-fuel cutting involves enhancing safety, efficiency, and cut quality through optimized equipment usage and cutting techniques. Follow these concise steps for better results:
Equipment Check: Regularly inspect and maintain cutting torches, hoses, and regulators. Ensure all components are clean and in good working order. Lincoln Electric provides insights into equipment maintenance.
Correct Gas Ratios: Use the appropriate oxygen and fuel gas mixture. A proper balance ensures efficient cutting and fuel usage. Harris Products Group offers guidance on gas ratios.
Proper Cutting Speed: Adjust the cutting speed to avoid excessive kerf width and ensure a smooth cut surface. Too slow or too fast speeds can affect cut quality. TWI Global discusses the impact of cutting speed on quality.
Nozzle Selection: Use the correct nozzle size for the thickness of the metal being cut. This choice affects the precision and efficiency of the cut. ESAB details the importance of selecting the right nozzle.
Proper Technique: Maintain a steady hand and an appropriate angle (typically around 45 degrees) for the torch to ensure a clean cut. Practice and consistency are key. MillerWelds provides technique tips.
Safety Practices: Adhere to safety guidelines, including wearing protective gear, ensuring good ventilation, and handling gases properly to prevent accidents. OSHA outlines safety practices for oxy-fuel cutting.
By focusing on these areas, metal fabricators can achieve more efficient, precise, and safer oxy-fuel cutting operations.
How to Display Oxy-fuel Cutting Skills on Your Resume
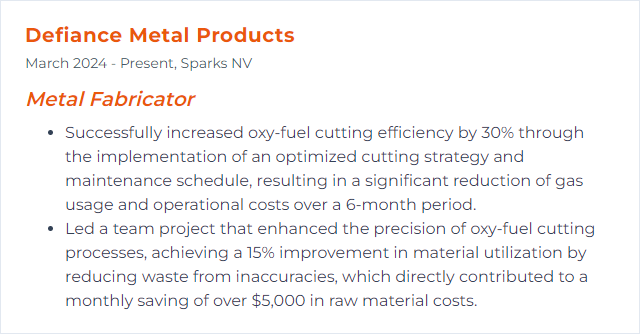
12. Sheet Metal Forming
Sheet metal forming is a manufacturing process used by metal fabricators to shape flat sheets of metal into specific geometries through mechanical deformation, utilizing techniques such as bending, drawing, and stretching, without removing material.
Why It's Important
Sheet metal forming is crucial for a metal fabricator as it enables the efficient shaping of metal sheets into various parts and components, allowing for the creation of a wide range of products with precision and cost-effectiveness.
How to Improve Sheet Metal Forming Skills
Improving sheet metal forming involves optimizing various aspects of the process to enhance efficiency, reduce waste, and improve product quality. Here's a concise guide for metal fabricators:
Material Selection: Choose the right material for the job, considering its formability, strength, and cost. Metals Magazine offers insights on material properties and selection.
Tool and Die Design: Invest in high-quality tools and dies, and design them to reduce stress concentrations and ensure uniform material flow. The Fabricator provides valuable information on tool and die design best practices.
Lubrication: Use appropriate lubricants to reduce friction between the die and the workpiece, which can improve material flow and prevent defects. Machinery Lubrication offers guidance on selecting and applying lubricants.
Process Control: Implement advanced process control systems to monitor and adjust the forming process in real-time, ensuring consistent quality. Control Engineering covers the latest in process control technologies.
Operator Training: Invest in training for operators to ensure they understand the nuances of the sheet metal forming process and can troubleshoot issues effectively. Tooling U-SME provides industry-recognized training programs.
Maintenance: Regularly maintain tools, dies, and machinery to prevent unexpected downtimes and extend equipment life. Plant Engineering offers maintenance tips and best practices.
Lean Manufacturing: Adopt lean manufacturing principles to minimize waste and optimize the entire production process. Lean Enterprise Institute is a great resource for learning about lean principles and practices.
By focusing on these key areas, metal fabricators can significantly improve their sheet metal forming operations, leading to higher quality products, reduced costs, and more satisfied customers.
How to Display Sheet Metal Forming Skills on Your Resume
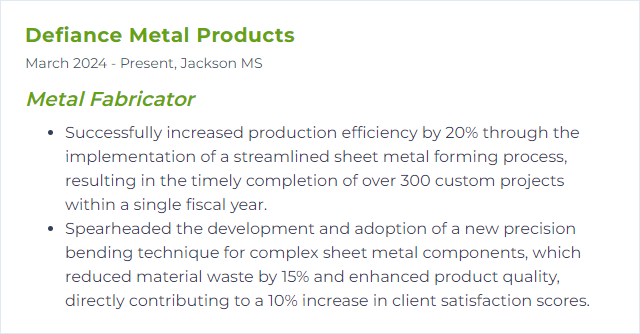