Top 12 Sheet Metal Mechanic Skills to Put on Your Resume
In the competitive field of sheet metal mechanics, showcasing the right set of skills on your resume can make a significant difference in landing your next job. This article highlights the top 12 skills that employers look for in a sheet metal mechanic, helping you to stand out in the job market and advance your career.
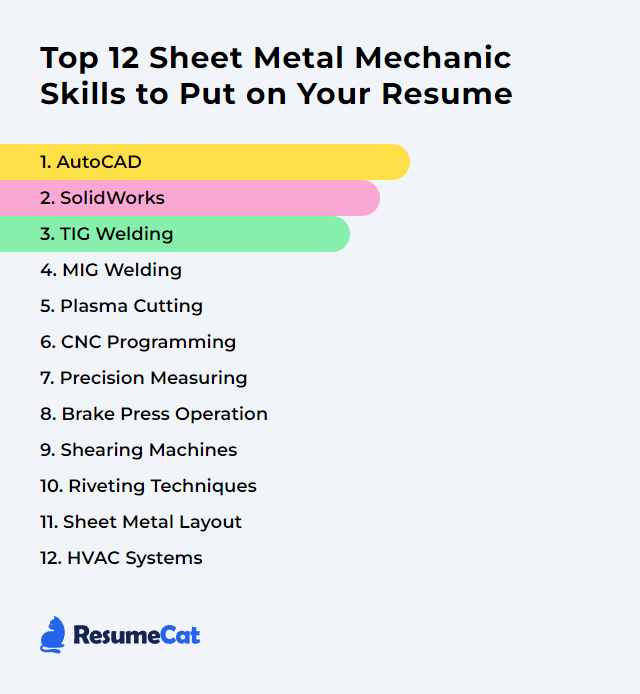
Sheet Metal Mechanic Skills
- AutoCAD
- SolidWorks
- TIG Welding
- MIG Welding
- Plasma Cutting
- CNC Programming
- Precision Measuring
- Brake Press Operation
- Shearing Machines
- Riveting Techniques
- Sheet Metal Layout
- HVAC Systems
1. AutoCAD
AutoCAD is a computer-aided design (CAD) software used for creating precise 2D and 3D drawings, including detailed fabrication designs and layouts for sheet metal components and assemblies.
Why It's Important
AutoCAD is crucial for a Sheet Metal Mechanic as it enables precise design and drafting of complex sheet metal parts and assemblies, ensuring accuracy, efficiency in fabrication, and customization, while minimizing material waste and errors in production.
How to Improve AutoCAD Skills
Improving your AutoCAD skills as a Sheet Metal Mechanic involves focusing on specific functionalities that enhance precision, efficiency, and the quality of your designs. Here's a concise guide:
Master Shortcuts: Learn and utilize AutoCAD keyboard shortcuts to speed up your workflow. Autodesk provides a comprehensive list.
Use Templates: Save time by creating and using templates for standard projects. Autodesk’s official guide on creating templates is a useful resource.
Customize Tool Palettes: Tailor tool palettes for sheet metal design tasks to streamline your process. Learn how from Autodesk’s Tool Palettes guide.
Learn 3D Modeling: Enhance your capability by learning 3D modeling. This skill is crucial for visualizing complex sheet metal parts. Start with the basics of 3D from Autodesk’s tutorials.
Utilize Sheet Metal Specific Software: Consider using AutoCAD extensions or other software designed for sheet metal work, such as AutoCAD Mechanical or specialized tools like Autodesk Inventor, which offers comprehensive sheet metal design capabilities.
Stay Updated and Practice: AutoCAD is constantly updated; staying informed about new features and practicing regularly will improve your proficiency. Autodesk’s AutoCAD blog is a great resource for updates and tips.
By focusing on these areas, you can significantly enhance your AutoCAD skills as a Sheet Metal Mechanic, leading to more efficient and higher-quality design work.
How to Display AutoCAD Skills on Your Resume
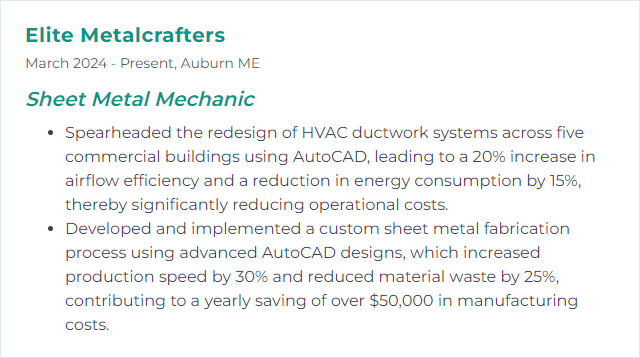
2. SolidWorks
SolidWorks is a computer-aided design (CAD) software used for creating 2D and 3D models, including specialized tools for designing and analyzing sheet metal components, making it valuable for sheet metal mechanics in planning, visualizing, and executing their projects.
Why It's Important
SolidWorks is important for a Sheet Metal Mechanic because it enables precise 3D modeling of sheet metal parts, allowing for the accurate design, simulation, and modification of complex geometries, thus streamlining fabrication processes and reducing material waste.
How to Improve SolidWorks Skills
Improving your SolidWorks skills, especially for tasks related to sheet metal mechanics, involves a blend of practice, leveraging resources, and integrating advanced tools. Here’s a concise guide to enhance your proficiency:
Master the Basics: Ensure you have a strong grasp of SolidWorks fundamentals. Use SolidWorks Tutorials for step-by-step guidance.
Sheet Metal Specific Training: Focus on sheet metal design features by exploring SolidWorks Sheet Metal Training to understand material properties, bending techniques, and manufacturing constraints.
Utilize Online Forums and Communities: Engage with SolidWorks Community Forums to ask questions, share experiences, and get tips from other sheet metal mechanics.
Incorporate Add-ons and Tools: Enhance your SolidWorks with sheet metal-specific add-ons for more efficient designing. Explore tools relevant to your work on the SolidWorks Partner Products page.
Keyboard Shortcuts and Customization: Customize your workflow with keyboard shortcuts and toolbars. SolidWorks Keyboard Shortcuts Cheat Sheet can significantly speed up your design process.
Practice with Real-World Projects: Apply your skills to real-world projects or simulations which can be found in resources like GrabCAD for diverse sheet metal design challenges.
Continuous Learning: Stay updated with the latest features and techniques by subscribing to SolidWorks Webinars.
By following these steps and regularly practicing, you can significantly improve your SolidWorks skills tailored to sheet metal mechanics.
How to Display SolidWorks Skills on Your Resume
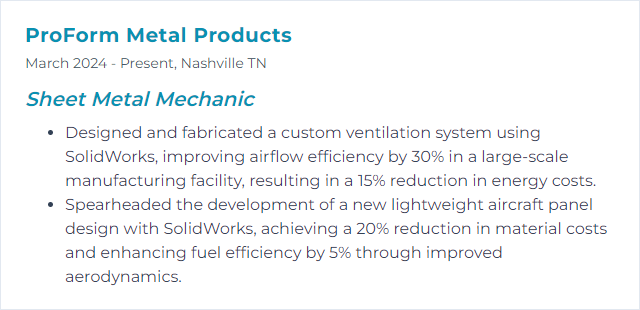
3. TIG Welding
TIG welding, or Tungsten Inert Gas welding, is a precise welding method where a tungsten electrode creates an arc to weld thin sheets of metal together, using an inert gas (usually argon) to protect the weld area from contamination. Ideal for detailed and high-quality work in sheet metal fabrication.
Why It's Important
TIG welding is crucial for a Sheet Metal Mechanic because it offers precise and high-quality welds on thin materials, essential for creating strong, clean joints in intricate sheet metal fabrications.
How to Improve TIG Welding Skills
To improve TIG welding as a Sheet Metal Mechanic, focus on the following key areas:
Equipment Setup: Ensure your TIG welder is correctly set up. This includes checking the gas flow, selecting the right tungsten electrode, and preparing your electrode with the appropriate tip shape. Miller Welds provides a comprehensive guide on setting up your equipment.
Material Preparation: Clean the material thoroughly before welding. Remove any contaminants like oil, dirt, or oxide layers to ensure a strong weld. Lincoln Electric emphasizes the importance of material prep.
Technique: Practice maintaining a consistent angle and distance between the welding torch and the workpiece. Keep a steady hand and feed the filler rod into the weld pool without directly touching the electrode. Welding Tips and Tricks offers technique tips.
Heat Management: Control the heat input by adjusting the amperage based on the thickness of the material. Avoid overheating to prevent warping and ensure penetration without burn-through. The American Welding Society discusses the importance of heat management.
Practice: Consistent practice on scrap material will help you refine your technique, control, and speed. Experiment with different angles, speeds, and materials. The Fabricator offers insights into honing your skills.
By focusing on these areas and seeking feedback from experienced welders, you can significantly improve your TIG welding skills.
How to Display TIG Welding Skills on Your Resume
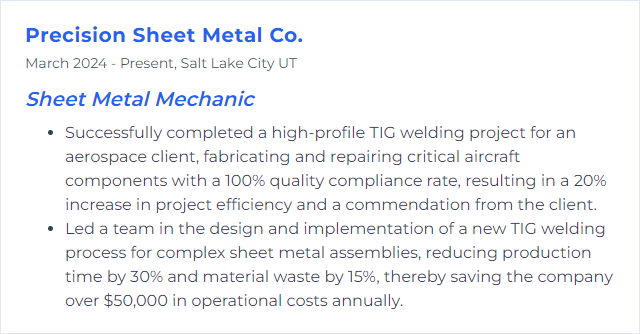
4. MIG Welding
MIG Welding, or Metal Inert Gas Welding, is a process where an electric arc forms between a consumable wire electrode and the workpiece metals, heating the metals and causing them to melt and join. It's widely used by sheet metal mechanics for its versatility, speed, and the high-quality welds it produces on a variety of metals.
Why It's Important
MIG welding is important for a Sheet Metal Mechanic because it provides a strong, efficient, and versatile method for joining metal sheets quickly and with high precision, essential for fabricating and repairing various metal structures and components.
How to Improve MIG Welding Skills
To enhance your MIG welding skills, especially as a Sheet Metal Mechanic, focus on these key areas:
Proper Preparation: Ensure metal surfaces are clean and free of contaminants. Use a metal brush or grinder for cleaning. Learn More
Correct Equipment Setup: Choose the right wire diameter and type. Adjust the voltage, wire feed speed, and gas flow rate according to the thickness of the metal. Equipment Setup Guide
Optimal Welding Technique: Maintain a consistent travel speed and angle. For thin metals, use a push technique for lesser penetration and a cleaner weld. Technique Tips
Control Heat Input: Prevent warping by using intermittent welding (stitch welding) or by employing a backstep technique. Heat Management
Practice and Experimentation: Experiment with different settings and techniques on scrap metal. Continuous practice improves steadiness and control. Practice Strategies
By focusing on these areas and leveraging resources for deep dives into each topic, you can significantly improve your MIG welding quality and efficiency.
How to Display MIG Welding Skills on Your Resume
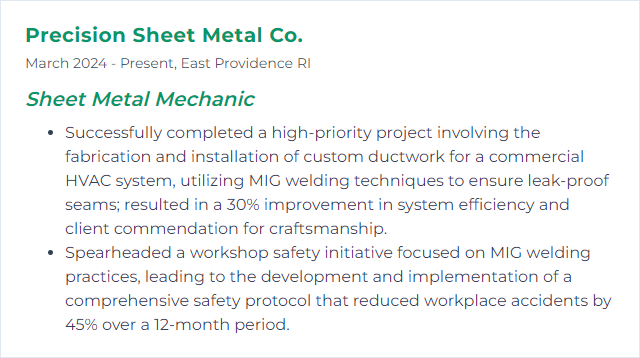
5. Plasma Cutting
Plasma cutting is a process used by sheet metal mechanics to precisely cut through various types of metal using a plasma torch, which generates a high-velocity jet of ionized gas heated to an extremely high temperature, capable of melting the metal upon contact and blowing away the molten material to create a clean cut.
Why It's Important
Plasma cutting is important for a Sheet Metal Mechanic because it allows for precise, efficient cutting of various metals regardless of their thickness, significantly enhancing fabrication speed and versatility in metalworking tasks.
How to Improve Plasma Cutting Skills
Improving plasma cutting, particularly for a Sheet Metal Mechanic, involves focusing on several key aspects such as equipment maintenance, cutting techniques, and material preparation. Here are concise tips:
Maintain Equipment: Regularly check and maintain your plasma cutter's components, ensuring consumables are replaced when needed. This includes electrodes, nozzles, and shields. Hypertherm's maintenance tips.
Optimal Settings: Use the correct settings for amperage and cutting speed based on the material thickness. Consult the cutter's manual for guidelines. Adjusting these settings can significantly improve the quality of the cut and reduce dross. Lincoln Electric's guide on setting up.
Proper Technique: Ensure the torch is held at the correct angle (usually perpendicular to the workpiece) and distance from the material. Use guides or CNC tables for precise cuts. Miller's cutting techniques.
Material Preparation: Clean the material surface before cutting to remove any contaminants that could affect the cut quality. Ensure the workpiece is flat and securely fastened. Eastwood's material prep advice.
Cooling and Safety: Proper cooling of the torch and workpiece can extend consumable life and improve cut quality. Always follow safety guidelines to protect yourself from fumes and ultraviolet light. Safety practices from OSHA.
Improving in these areas can lead to more efficient plasma cutting processes, better quality cuts, and longer equipment life.
How to Display Plasma Cutting Skills on Your Resume
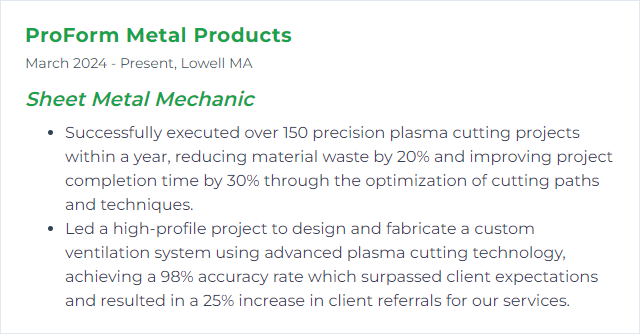
6. CNC Programming
CNC Programming for a Sheet Metal Mechanic involves creating and inputting instructions into a CNC machine to automatically cut, shape, and form sheet metal parts according to precise specifications.
Why It's Important
CNC programming is crucial for a Sheet Metal Mechanic because it allows for precise, efficient, and repeatable cutting, bending, and shaping of metal sheets, leading to high-quality parts and components with minimal waste and increased productivity.
How to Improve CNC Programming Skills
Improving CNC programming, especially for a Sheet Metal Mechanic, involves understanding the specifics of sheet metal work and the intricacies of CNC machines. Here are concise tips:
Learn and Apply CAD/CAM Software: Mastering CAD (Computer-Aided Design) and CAM (Computer-Aided Manufacturing) software is crucial. Programs like SolidWorks or Autodesk Fusion 360 (Fusion 360) offer specialized tools for sheet metal design and can automate the CNC programming process.
Understand Material Properties: Knowing the properties of the metal you're working with can affect programming, especially in terms of cutting speeds and feed rates. The American Iron and Steel Institute provides resources (AISI).
Optimize Toolpaths: Efficient toolpaths reduce machining time and wear on tools. Software often offers simulation tools to help visualize and optimize these paths.
Update CNC Machine Knowledge: Stay updated on the latest CNC technologies and practices. Websites like Modern Machine Shop (MMSONLINE) offer news and tips.
Practice G-code: While software often automates G-code generation, understanding and being able to manually adjust G-code (Learn G-code) can be crucial for troubleshooting and optimization.
Join Forums and Communities: Engaging with communities like Practical Machinist (Practical Machinist) can provide real-world advice and solutions from experienced professionals.
By focusing on these areas, a Sheet Metal Mechanic can significantly improve their CNC programming skills, leading to more efficient and accurate metal fabrication.
How to Display CNC Programming Skills on Your Resume
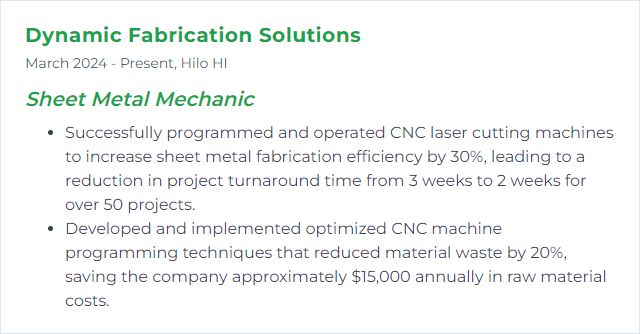
7. Precision Measuring
Precision measuring in the context of a Sheet Metal Mechanic involves the use of specialized tools (such as calipers, micrometers, and gauges) to obtain highly accurate measurements of material thickness, dimensions, and angles, ensuring that fabricated or modified sheet metal components meet exact specifications and tolerances required for their intended application.
Why It's Important
Precision measuring is crucial for a Sheet Metal Mechanic because it ensures the accuracy and fit of fabricated components, minimizing material waste and ensuring the structural integrity and functionality of the final product.
How to Improve Precision Measuring Skills
Improving precision in measuring for a Sheet Metal Mechanic involves several key practices:
Use of High-Quality Tools: Invest in high-quality, precision measuring tools like digital calipers, micrometers, and angle finders that offer higher accuracy.
Regular Calibration: Ensure measuring tools are regularly calibrated to maintain accuracy. Follow the manufacturer's guidelines for calibration intervals.
Proper Handling and Storage: Handle measuring tools with care and store them in a protected environment to prevent damage and wear.
Environmental Control: Perform measurements in a controlled environment. Temperature and humidity can affect both the metal being measured and the measuring tools. Use temperature and humidity control solutions if necessary.
Skill Development: Continuously improve skills through practice and training. Knowing how to correctly use measuring tools is crucial.
Use of Fixtures and Jigs: To ensure repeatability and accuracy, use fixtures and jigs when measuring and marking sheet metal.
Cross-Verification: Whenever possible, use more than one method or tool to verify measurements to increase confidence in the precision of the measurement.
By focusing on these areas, a Sheet Metal Mechanic can significantly improve the precision of their measurements, leading to higher quality work and reduced material waste.
How to Display Precision Measuring Skills on Your Resume
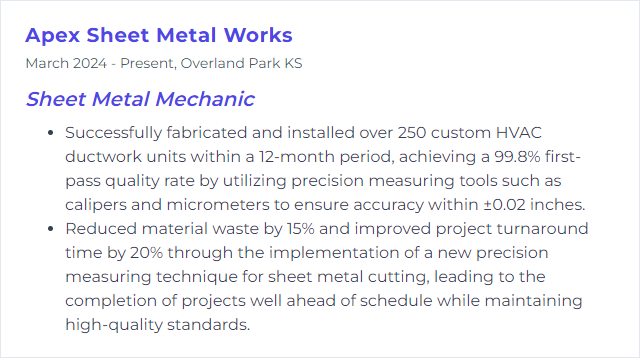
8. Brake Press Operation
Brake press operation involves using a brake press machine to bend and shape sheet metal into specific forms or angles by applying pressure, according to precise measurements and specifications set by a sheet metal mechanic.
Why It's Important
Brake press operation is crucial for a Sheet Metal Mechanic as it allows for the precise bending and shaping of metal sheets into specific forms and dimensions, essential for creating components that meet exact specifications and standards.
How to Improve Brake Press Operation Skills
Improving brake press operation for a sheet metal mechanic involves several key strategies aimed at enhancing efficiency, accuracy, and safety. Here's a very short and concise description:
Continuous Training: Ensure ongoing training on the latest brake press technologies and techniques. Tooling U-SME offers courses on press brake operation.
Regular Maintenance: Perform regular maintenance checks to prevent machine downtime and ensure consistent operation. The Fabricator provides a guide on press brake maintenance.
Tooling Management: Organize and maintain tools properly. Use the right tools for each job to improve efficiency and product quality. Mate Precision Technologies offers insights on selecting and managing press brake tooling.
Programming Software: Utilize the latest CAD/CAM software for precise bending calculations and simulations to reduce waste and improve accuracy. LVD Group provides advanced software solutions for press brakes.
Safety Measures: Implement and adhere to strict safety protocols to prevent accidents. OSHA offers guidelines and resources on machine safety.
By focusing on these areas, a sheet metal mechanic can significantly enhance brake press operation, leading to improved productivity and safety.
How to Display Brake Press Operation Skills on Your Resume
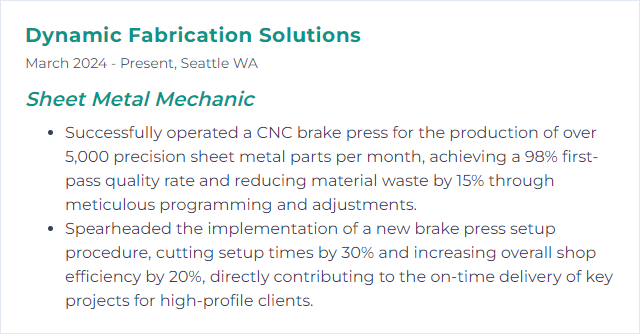
9. Shearing Machines
Shearing machines are tools used by sheet metal mechanics to cut large sheets of metal into smaller sizes or desired shapes with high precision and minimal waste, utilizing a straight cutting blade.
Why It's Important
Shearing machines are crucial for sheet metal mechanics as they provide a precise and efficient method for cutting large sheets of metal into smaller, manageable sizes or specific shapes, essential for fabricating metal parts and components accurately and with clean edges.
How to Improve Shearing Machines Skills
Improving shearing machines for a sheet metal mechanic involves enhancing safety, accuracy, maintenance, and operational efficiency. Here are concise ways to achieve these improvements:
Enhance Safety: Implement advanced safety features like light curtains and emergency stop buttons to protect operators. Safety Measures
Improve Accuracy: Upgrade to CNC (Computer Numerical Control) shearing machines for precise cuts and programmable operations. Retrofit older machines with modern control systems. CNC Technology
Regular Maintenance: Schedule regular maintenance and inspections to ensure optimal performance and longevity of the machine. Use predictive maintenance tools to detect wear and tear early. Maintenance Tips
Upgrade Blades: Use high-quality, industry-specific blades and regularly sharpen them to maintain efficiency and quality of cuts. Blade Selection
Implement Material Handling Systems: Integrate automated material handling systems to reduce manual loading and unloading time, improving overall efficiency. Material Handling
Energy Efficiency: Invest in energy-efficient models or upgrade existing machines with energy-saving components to reduce operational costs. Energy Efficiency Tips
Training and Education: Provide ongoing training for operators on the latest machine operations, safety protocols, and maintenance procedures to enhance performance and safety. Training Resources
By focusing on these areas, you can significantly improve the performance, safety, and longevity of shearing machines in a sheet metal fabrication setting.
How to Display Shearing Machines Skills on Your Resume
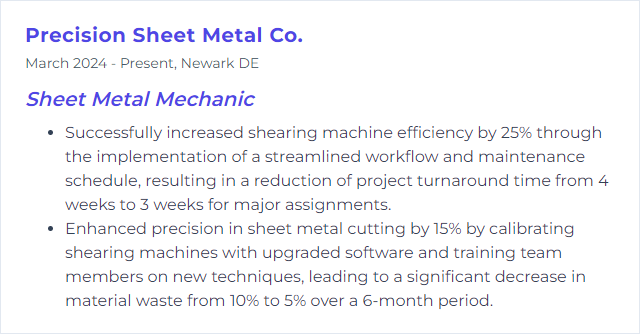
10. Riveting Techniques
Riveting techniques in sheet metal mechanics involve fastening two pieces of metal together by inserting a rivet (a metal pin or bolt) through pre-drilled holes in the sheets. The rivet's tail is then deformed or bucked to create a permanent hold, using tools such as a rivet gun and bucking bar. Common techniques include solid riveting and pop riveting, chosen based on the strength required and access to both sides of the metal sheets.
Why It's Important
Riveting techniques are crucial for a Sheet Metal Mechanic because they ensure the structural integrity and durability of metal assemblies, providing reliable and robust joints for a wide range of applications in manufacturing and repair work.
How to Improve Riveting Techniques Skills
Improving riveting techniques, especially for a Sheet Metal Mechanic, involves mastering precision, understanding material properties, and using the right tools. Here are concise tips to enhance your riveting skills:
Select the Correct Rivet and Tools: Match rivet material and size with your sheet metal. Use a rivet gun that fits your project's requirements for optimal control and efficiency.
Prepare Surfaces Properly: Clean and deburr the surfaces to be joined. Proper preparation ensures a tight, smooth fit. Refer to Metal Deburring for more on surface preparation.
Drill Accurate Holes: Use a drill press for uniform holes. Ensure the holes are the right size for your rivets, slightly larger than the rivet diameter for a snug fit. Drilling Techniques can guide you on speed and feed rates.
Use the Right Technique: Hold the rivet gun perpendicular to the workpiece and apply steady pressure. For manual riveting, learn the proper hammering technique to avoid work-hardening or damaging the materials. Rivet Gun Techniques provides insights into proper usage.
Inspect Rivets After Installation: Ensure rivets are properly formed and tight against the sheet metal, with no movement. This guide on Rivet Inspection from the FAA can be a valuable resource.
Practice and Continuous Learning: The more you practice, the better you become. Stay updated with new techniques and tools in the field. Online resources like AviationPros offer insights into the latest trends and tools in riveting.
By focusing on these areas, a Sheet Metal Mechanic can significantly improve their riveting techniques, leading to higher quality workmanship and efficiency on the job.
How to Display Riveting Techniques Skills on Your Resume
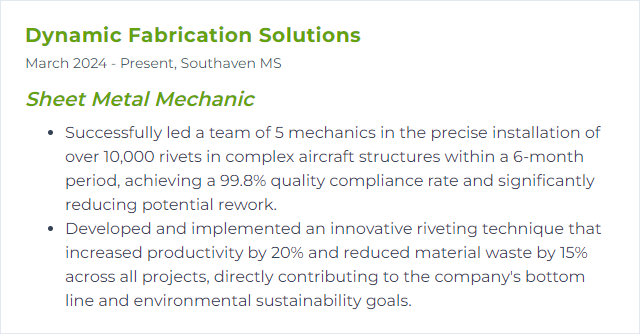
11. Sheet Metal Layout
Sheet metal layout is the process of planning and marking the cutting and bending lines on a flat sheet of metal before it is cut, bent, or formed into its final shape, ensuring accurate size and fit for its intended purpose.
Why It's Important
Sheet Metal Layout is crucial for a Sheet Metal Mechanic because it ensures accurate cutting, bending, and assembly of metal sheets, reducing material waste and ensuring the final product meets design specifications and quality standards.
How to Improve Sheet Metal Layout Skills
Improving sheet metal layout involves enhancing accuracy, efficiency, and material utilization. Here are concise strategies for a sheet metal mechanic:
Use Software Tools: Adopt CAD/CAM software specifically designed for sheet metal fabrication. This improves precision and speed. AutoCAD and SolidWorks are popular options.
Standardize Processes: Develop and follow standardized procedures for common tasks and layouts. This reduces errors and training time. SMACNA guidelines can be a valuable resource.
Optimize Material Usage: Utilize nesting software to maximize material utilization and minimize waste. SigmaNEST is an example of such a tool.
Enhance Skills and Knowledge: Continuously learn new techniques and stay updated with the latest in sheet metal fabrication. Online platforms like LinkedIn Learning offer courses on sheet metal design.
Implement Quality Control Measures: Use checklists and inspection tools to ensure accuracy at every stage, reducing the need for rework.
Invest in Proper Tools: High-quality tools and machinery lead to better precision and efficiency. Regular maintenance is also crucial.
Practice Lean Manufacturing Principles: Adopt lean principles to eliminate waste and streamline operations. The Lean Enterprise Institute provides resources on lean manufacturing.
By focusing on these strategies, a sheet metal mechanic can significantly improve layout processes, leading to better quality, reduced waste, and increased productivity.
How to Display Sheet Metal Layout Skills on Your Resume
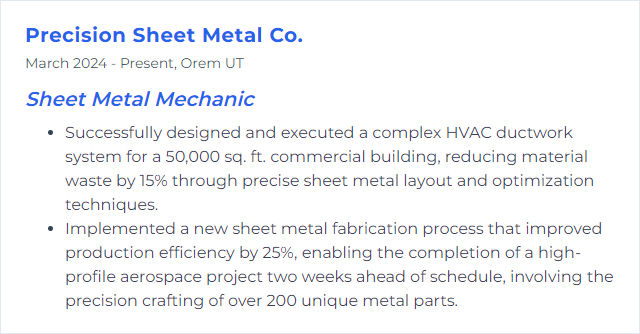
12. HVAC Systems
HVAC systems, short for Heating, Ventilation, and Air Conditioning, are essential climate control systems that regulate temperature, humidity, and air quality in buildings. For a Sheet Metal Mechanic, these systems involve fabricating, assembling, installing, and repairing the ductwork and other sheet metal components necessary for the efficient and effective distribution of warm or cool air throughout a structure.
Why It's Important
HVAC systems are essential for regulating indoor temperature, humidity, and air quality, ensuring comfort and a healthy environment. For a Sheet Metal Mechanic, these systems are crucial as they involve fabrication, installation, and maintenance of ductwork that efficiently distributes air throughout a building.
How to Improve HVAC Systems Skills
Improving HVAC systems involves enhancing their efficiency, durability, and performance. As a Sheet Metal Mechanic, here are concise strategies to achieve these improvements:
Ductwork Optimization: Ensure ducts are properly sealed and insulated to minimize energy loss. Focus on creating smooth duct paths for efficient airflow. Energy Star provides guidelines on duct sealing and insulation.
Proper Sizing and Design: Use Manual J and D calculations for accurate sizing and design of HVAC systems and ductwork to match the specific requirements of the space. ACCA (Air Conditioning Contractors of America) offers resources on proper sizing and design standards.
Installation of Variable Speed Drives: Installing variable speed drives on fans and motors can significantly reduce energy consumption by adjusting speed based on demand. U.S. Department of Energy discusses the efficiency benefits of variable speed drives.
Maintenance and Upkeep: Regular maintenance, including cleaning, adjusting, and replacing components as necessary, ensures the HVAC system operates at peak efficiency. The U.S. Department of Energy provides maintenance tips for air conditioners, applicable to broader HVAC maintenance.
Incorporate Automation and Controls: Use smart thermostats and automation systems for better control over heating and cooling, enhancing efficiency and comfort. ENERGY STAR lists certified smart thermostats.
By focusing on these areas, you can significantly improve the performance and efficiency of HVAC systems.
How to Display HVAC Systems Skills on Your Resume
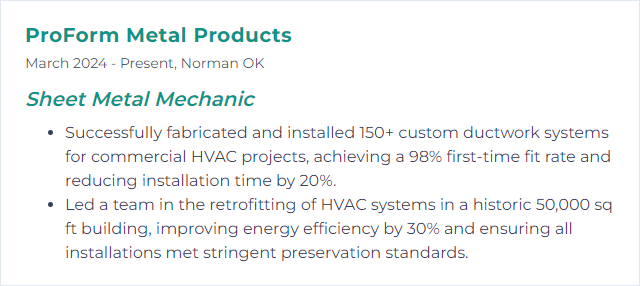