Top 12 MIG Welder Skills to Put on Your Resume
In today's competitive job market, standing out as a proficient MIG welder requires showcasing a unique set of skills on your resume. Highlighting the top MIG welder skills not only demonstrates your expertise but also positions you as a valuable asset to potential employers in the welding industry.
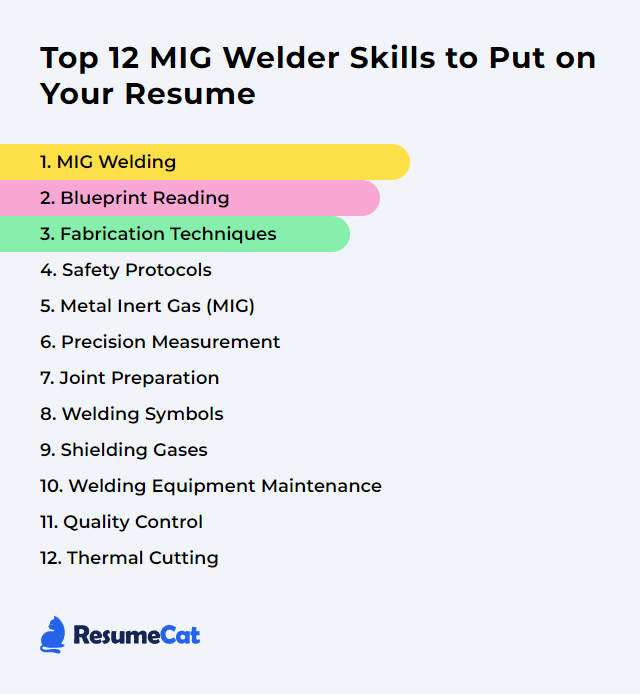
MIG Welder Skills
- MIG Welding
- Blueprint Reading
- Fabrication Techniques
- Safety Protocols
- Metal Inert Gas (MIG)
- Precision Measurement
- Joint Preparation
- Welding Symbols
- Shielding Gases
- Welding Equipment Maintenance
- Quality Control
- Thermal Cutting
1. MIG Welding
MIG welding, or Metal Inert Gas welding, is a process where an electric arc forms between a consumable wire electrode and the workpiece metal(s), heating the workpiece metal(s) and causing them to melt and join. It uses a shielding gas to protect the weld from atmospheric contamination.
Why It's Important
MIG welding is important because it offers a highly efficient and versatile method for creating strong, high-quality welds across a variety of metals, making it indispensable for manufacturing, automotive repair, and construction.
How to Improve MIG Welding Skills
Improving MIG welding involves refining technique, equipment settings, and maintenance. Here are concise tips:
Optimize Voltage and Wire Feed Speed: Balance voltage and wire feed speed for the material thickness. Lincoln Electric provides guidelines on settings.
Choose the Right Gas and Material: Use the appropriate shielding gas and wire type for the material being welded. MillerWelds offers advice on gas and material selection.
Maintain a Consistent Work Angle and Stick-Out: Keep the torch at a 15-20 degree angle to the workpiece and maintain a consistent wire stick-out length. Hobart Brothers shares technique improvements.
Properly Prepare the Material: Clean the material thoroughly before welding to improve contact and reduce contamination. Welding Tips and Tricks discusses material preparation.
Regular Equipment Maintenance: Regularly check and replace consumables, keep the machine clean, and ensure good ground connection. ESAB emphasizes the importance of equipment maintenance.
Practice and Experiment: Practice different techniques and settings on scrap material. Experimentation helps in understanding how changes affect the weld quality.
By focusing on these areas, you can significantly improve your MIG welding quality and efficiency.
How to Display MIG Welding Skills on Your Resume
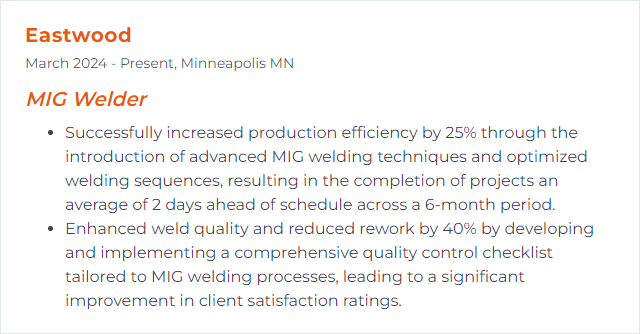
2. Blueprint Reading
Blueprint reading, in the context of an MIG (Metal Inert Gas) welder, involves interpreting and understanding detailed technical drawings and specifications of metal parts or structures to be welded. This skill includes recognizing dimensions, welding symbols, joint types, and material specifications to accurately prepare and weld components as per the design requirements.
Why It's Important
Blueprint reading is crucial for an MIG Welder as it enables accurate interpretation of welding symbols and specifications, ensuring precise fabrication, proper assembly, and compliance with design requirements.
How to Improve Blueprint Reading Skills
Improving blueprint reading as an MIG Welder involves enhancing your understanding of welding symbols, technical drawings, and specifications. Here’s a concise guide:
Learn the Basics: Familiarize yourself with basic symbols and terms used in welding blueprints. The American Welding Society (AWS) offers resources and a standardized set of symbols.
Practice Regularly: Consistent practice in interpreting different blueprints enhances your speed and accuracy. Websites like Lincoln Electric provide practical guides and examples.
Take a Course: Consider enrolling in a course focused on blueprint reading for welders. Community colleges and trade schools often offer relevant courses. Online platforms like Udemy also may have specific courses on blueprint reading.
Use Online Resources: Utilize online forums, YouTube tutorials, and welding communities. Channels like Weld.com on YouTube often share useful insights and practical tips.
Apply Knowledge: Apply your blueprint reading skills in real-world projects. Hands-on experience is invaluable for reinforcing what you’ve learned.
By focusing on these steps, you can significantly improve your blueprint reading skills, making you a more proficient and efficient MIG welder.
How to Display Blueprint Reading Skills on Your Resume
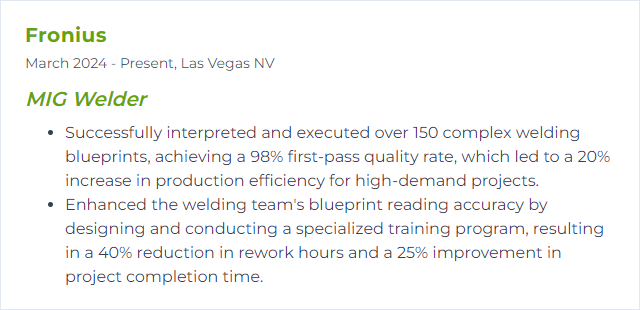
3. Fabrication Techniques
Fabrication techniques using an MIG (Metal Inert Gas) welder involve using a wire feed mechanism that continuously feeds a solid wire electrode through a welding gun into the weld pool, melting the two base materials together. An inert gas is also expelled from the gun to shield the weld pool from contamination by the atmosphere. This process is versatile, easy to learn, and can be used on various metals and thicknesses, making it a popular choice for both professional and DIY metal fabrication projects.
Why It's Important
Fabrication techniques are crucial for an MIG Welder because they determine the quality, strength, and appearance of the weld, ensuring that structures are safe, durable, and meet specified requirements. They also optimize the welding process for efficiency and cost-effectiveness.
How to Improve Fabrication Techniques Skills
Improving fabrication techniques, especially for MIG welding, involves a combination of practice, understanding the equipment, and applying best practices. Here's a concise guide:
Understand Your Equipment: Familiarize yourself with your MIG welder's settings and capabilities. MillerWelds offers a comprehensive guide on understanding different MIG welding settings.
Proper Maintenance: Regularly clean and maintain your MIG welder and accessories. Lincoln Electric provides maintenance tips that can help prevent common issues.
Correct Material Preparation: Ensure materials are clean and properly prepared before welding. Welding Tips and Tricks discusses the importance of material preparation for optimal welding results.
Practice Different Techniques: Experiment with various welding techniques such as push or pull methods, and adjust angles for better penetration and bead appearance. The Fabricator offers insights into push and pull welding techniques.
Control Heat Input: Managing the heat input is crucial to avoid warping and to control bead appearance. Hobart Brothers provides strategies for managing heat input during MIG welding.
Use the Right Gas and Wire: Select the appropriate shielding gas and wire type for your project. TWI Global explains the impact of different gases and wires on MIG welding.
Continuous Learning: Stay updated with new techniques and technologies in MIG welding. Websites like American Welding Society often have resources and courses to keep your skills sharp.
By focusing on these areas, you can significantly improve your MIG welding fabrication techniques.
How to Display Fabrication Techniques Skills on Your Resume
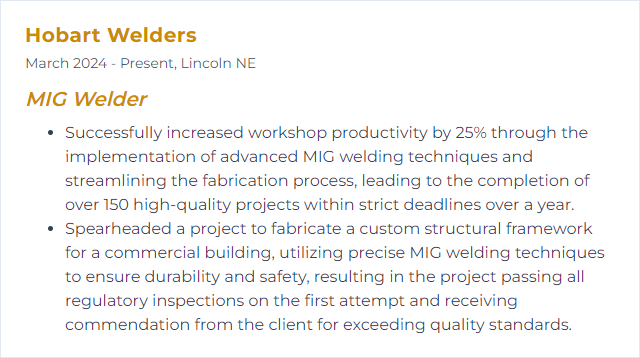
4. Safety Protocols
Safety protocols for an MIG welder include wearing appropriate personal protective equipment (PPE) such as a welding helmet, gloves, and protective clothing; ensuring proper ventilation to avoid inhaling harmful fumes; maintaining a clean work area to prevent fires; and following the manufacturer's instructions for equipment use and maintenance to avoid electrical and other hazards.
Why It's Important
Safety protocols are crucial for MIG welders to prevent accidents, minimize exposure to harmful fumes and radiation, ensure proper use of equipment, and protect against electrical hazards and burns, thereby ensuring the welder's well-being and maintaining a safe working environment.
How to Improve Safety Protocols Skills
Improving safety protocols for MIG welders involves a combination of equipment maintenance, proper usage techniques, and adherence to safety guidelines. Here are concise steps to enhance safety:
Training: Ensure all operators undergo comprehensive safety training specific to MIG welding, covering both theory and practical sessions.
Personal Protective Equipment (PPE): Use appropriate PPE including welding helmets, gloves, and fire-resistant clothing. Regularly inspect PPE for damage.
Equipment Maintenance: Follow a regular maintenance schedule for the welding machine and accessories. Consult the manufacturer's guidelines for specific maintenance advice.
Ventilation: Implement effective ventilation systems to remove harmful fumes and gases from the welding area.
Fire Safety: Keep fire extinguishers accessible and ensure the welding area is clear of flammable materials. Refer to NFPA 51B for fire prevention measures during welding.
Electrical Safety: Regularly inspect cables and connections for wear and damage. Follow OSHA's electrical safety standards for guidance.
Emergency Procedures: Develop and communicate clear emergency response procedures, including first aid and evacuation plans.
By focusing on these key areas, you can significantly improve the safety protocols for MIG welding operations.
How to Display Safety Protocols Skills on Your Resume
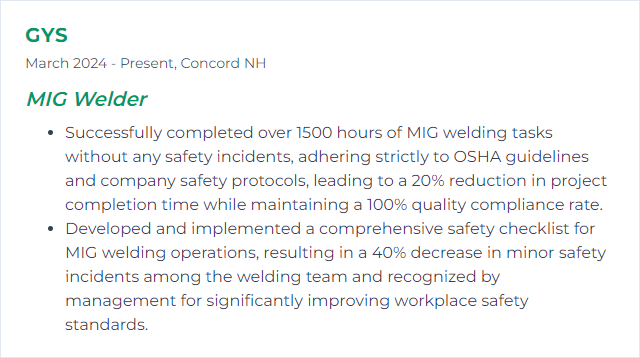
5. Metal Inert Gas (MIG)
Metal Inert Gas (MIG) welding, also known as Gas Metal Arc Welding (GMAW), is a process where an electric arc forms between a consumable wire electrode and the workpiece metals, heating the metals and causing them to melt and join. This process is shielded by an inert gas, typically argon or a mixture, which protects the weld from atmospheric contamination.
Why It's Important
Metal Inert Gas (MIG) welding is important because it offers a fast, efficient, and versatile method for joining metals with a high-strength weld, suitable for a wide range of materials and thicknesses. It's user-friendly and applicable in both industrial fabrication and hobbyist projects.
How to Improve Metal Inert Gas (MIG) Skills
Improving Metal Inert Gas (MIG) welding involves enhancing technique, equipment maintenance, and material preparation. Here’s a concise guide on how to achieve better MIG welding results:
Select the Right Wire: Use the appropriate wire type and diameter for your material. Hobart Brothers offers a selection guide for different materials.
Proper Machine Setup: Ensure your MIG welder is correctly set up, including voltage, wire feed speed, and gas flow rate. Miller Electric provides a comprehensive setup guide.
Clean Your Materials: Remove any rust, oil, or dirt from the surfaces to be welded. Lincoln Electric emphasizes the importance of cleanliness for optimal welding results.
Maintain Proper Technique: Keep a consistent angle and distance between the welding gun and the workpiece. Welding Tips and Tricks offers practical advice on technique improvement.
Regular Equipment Maintenance: Keep your MIG welder in top condition by regularly checking and replacing consumables like tips, nozzles, and liners. ESAB’s maintenance checklist is a helpful resource.
By focusing on these aspects, you can significantly improve the quality and efficiency of your MIG welding operations.
How to Display Metal Inert Gas (MIG) Skills on Your Resume
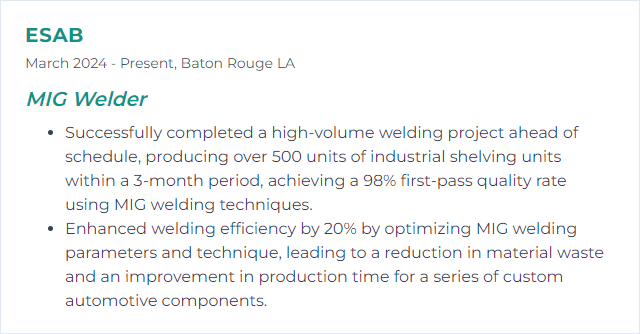
6. Precision Measurement
Precision measurement for an MIG welder refers to the highly accurate determination of welding parameters such as voltage, wire feed speed, and gas flow rate, ensuring consistent, high-quality welds.
Why It's Important
Precision measurement is crucial for an MIG welder to ensure accurate weld placement, consistent weld quality, and adherence to specified dimensions, thereby reducing material waste and ensuring the structural integrity and performance of the welded components.
How to Improve Precision Measurement Skills
Improving the precision of an MIG welder involves several key steps focused on equipment calibration, technique refinement, and environmental control. Here's a concise guide:
Calibrate Equipment: Regularly calibrate your MIG welder to ensure accurate voltage, wire feed speed, and gas flow. Use a calibration tool specific to your welder model.
Use High-Quality Consumables: Invest in high-quality welding wire and gas. Consistent material quality significantly impacts weld precision. Lincoln Electric and Miller Electric are reputable sources.
Control Your Environment: Minimize external variables like wind or humidity that can affect welding precision. Welding in a controlled environment ensures consistent results. AWS Welding Environment Guide offers detailed insights.
Practice Technique: Develop a steady hand and consistent speed. Consider courses or tutorials from American Welding Society (AWS) to refine your technique.
Maintain Your Equipment: Regular maintenance of your MIG welder, including cleaning and checking for wear and tear on components like the nozzle and contact tip, is crucial. Hobart Welders Maintenance Tips provides practical advice.
By focusing on these areas, you can significantly improve the precision of your MIG welding projects.
How to Display Precision Measurement Skills on Your Resume
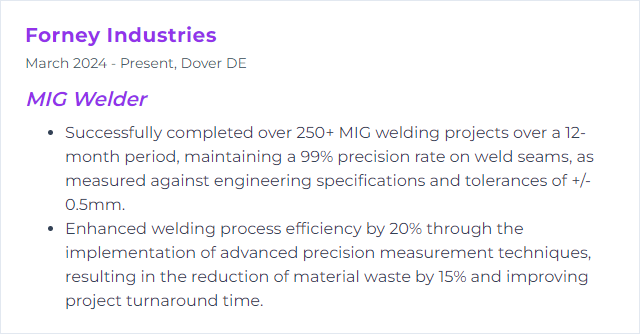
7. Joint Preparation
Joint preparation for MIG welding involves cleaning the metal surfaces to be welded, choosing the appropriate joint configuration (e.g., butt, lap, corner, edge, or tee), and ensuring proper alignment and fit-up to facilitate strong, defect-free welds.
Why It's Important
Joint preparation is crucial for an MIG welder because it ensures proper penetration and fusion of the metal, resulting in a strong, high-quality weld. It removes contaminants that could weaken the weld, guarantees correct alignment, and facilitates optimal welding conditions.
How to Improve Joint Preparation Skills
To improve joint preparation for MIG welding, follow these concise steps:
Clean the Surface: Remove rust, paint, oil, and dirt from the welding area using a wire brush or grinder. Clean metal ensures better welding penetration and strength.
Choose the Right Joint Design: Select the appropriate joint design (butt, lap, corner, edge, or T-joint) based on the thickness and type of metals being welded. This guide from Miller Welds can help in understanding joint types.
Cut Precisely: Ensure the metal pieces are cut precisely to fit tightly together. Use a proper cutting tool for accuracy.
Apply Proper Bevel: For thicker materials, bevel the edges to allow for deeper penetration of the weld. A 30° to 45° bevel angle is generally recommended.
Use the Right Electrode and Gas: Select the appropriate wire and shielding gas. For most MIG welding tasks, ER70S-3 for all-purpose welding and a mix of 75% Argon and 25% CO2 are recommended. More details can be found on Lincoln Electric's guide.
Adjust the Machine Settings: Properly set the voltage, amperage, and wire feed speed according to the material's thickness and type. This step is crucial for achieving good penetration and a strong weld.
Practice Proper Fit-Up: Align and clamp the pieces to be welded securely. Good fit-up ensures the gap is consistent and manageable across the joint.
Tack Weld: Apply small tack welds to hold the pieces in place before doing the full weld. This prevents distortion and maintains alignment.
By following these steps, you can improve joint preparation for MIG welding, leading to stronger, higher-quality welds.
How to Display Joint Preparation Skills on Your Resume
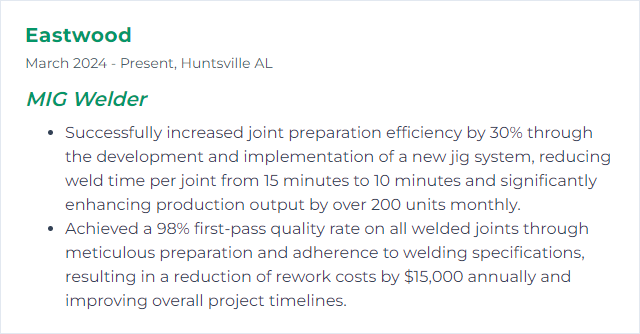
8. Welding Symbols
Welding symbols are standardized graphical representations used on blueprints or plans to specify the type of weld, size, length, and other details necessary for the welding process. For an MIG (Metal Inert Gas) welder, these symbols provide essential information on how to execute welds according to the design requirements, ensuring proper joint strength and integrity.
Why It's Important
Welding symbols are crucial for an MIG welder as they provide precise instructions on how to perform welds, ensuring consistency, quality, and safety in metal fabrication and repair tasks.
How to Improve Welding Symbols Skills
Improving your understanding and use of welding symbols, especially for MIG welding, involves a few concise steps. Welding symbols are essential for communicating how a weld should be made and what it should look like. Here are the key points to enhance your skills:
Learn the Basics: Start with understanding the basic elements of welding symbols, such as the reference line, arrow line, tail, and the symbols themselves. The American Welding Society (AWS) offers resources and a standard (AWS A2.4) detailing welding symbols.
Practice Reading Diagrams: Practice interpreting welding diagrams and symbols. Use resources from WeldingTipsAndTricks for practical examples and explanations.
Understand MIG-Specific Symbols: Since you're focusing on MIG welding, ensure you're familiar with symbols specific to MIG processes, such as the type of metal transfer (globular, short-circuit, etc.), and material thickness considerations.
Use Online Resources: Engage with online tutorials and courses. Websites like Miller Welds provide guides and tips specific to MIG welding, including how to read and use welding symbols effectively.
Practice and Apply: Lastly, practice applying welding symbols in your projects or practice pieces. The more you use them, the more familiar you will become.
By following these steps and consistently practicing, your proficiency with welding symbols, particularly in the context of MIG welding, will improve significantly.
How to Display Welding Symbols Skills on Your Resume
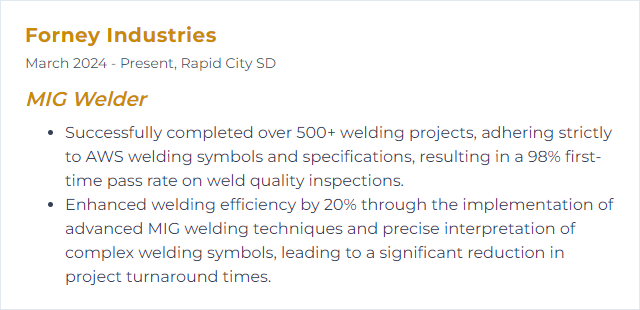
9. Shielding Gases
Shielding gases in MIG welding are inert or semi-inert gases that protect the weld area from atmospheric contaminants such as oxygen and nitrogen, ensuring a stronger and cleaner weld.
Why It's Important
Shielding gases are crucial in MIG welding because they protect the weld pool from atmospheric contamination, ensuring a stronger, cleaner weld by preventing oxidation and other reactions that can weaken the joint.
How to Improve Shielding Gases Skills
Improving shielding gases for MIG welding involves selecting the right gas or gas mixture to enhance weld quality, penetration, and spatter control. Here's a concise guide:
Understand Gas Types: Pure inert gases like Argon are great for non-ferrous metals, providing stable arcs and clean welds. For steel, Carbon Dioxide (CO2) is cost-effective, deep penetrating but can increase spatter. Mixtures like Argon/CO2 combine benefits, improving weld appearance and reducing spatter.
Adjust Gas Flow Rate: Optimal flow rates (typically 20-25 cubic feet per hour) prevent porosity and ensure adequate coverage. Too high can cause turbulence and introduce air into the shield.
Select the Right Mixture: For steel, a common mixture is 75% Argon and 25% CO2. This mixture offers a good balance between weld quality and cost. For aluminum, use 100% Argon for its cleaning action and deeper penetration.
Consider Specialty Mixtures: For specific applications, gases like Helium can be added to increase heat input and improve weld speed in thick materials.
For detailed guidelines on gas selection and usage:
- Lincoln Electric's guide on shielding gas selection provides a comprehensive overview.
- Miller Welds' article on MIG welding basics, including gas choices, offers practical tips.
Remember, the right shielding gas can significantly impact your weld's appearance, integrity, and overall success.
How to Display Shielding Gases Skills on Your Resume
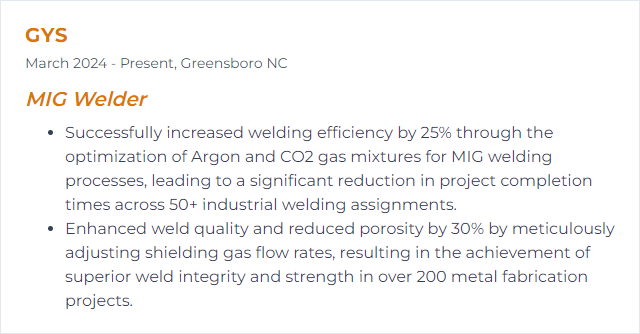
10. Welding Equipment Maintenance
Welding equipment maintenance, specifically for an MIG welder, involves regular inspection, cleaning, and repair of various components such as the wire feed system, gun, cables, and connections to ensure optimal performance and safety during welding operations.
Why It's Important
Welding equipment maintenance, especially for an MIG welder, is crucial to ensure consistent, high-quality welds, prolong the lifespan of the equipment, prevent unexpected downtime, and enhance safety by reducing the risk of accidents due to equipment failure.
How to Improve Welding Equipment Maintenance Skills
Improving maintenance for an MIG welder involves regular checks and clean-ups to ensure optimal performance and longevity. Here are concise steps:
Daily Inspection: Before each use, perform a visual inspection for any obvious damage or wear to cables, gun, and gas connections. Ensure all connections are tight and secure.
Regular Cleaning: After usage, clean the welder’s exterior with a clean cloth. Remove any dust or debris from the wire feeder and inspect the gun's nozzle and contact tip for spatter; replace if necessary. Use a spatter removal compound or tool for cleaning.
Check Consumables: Regularly inspect and replace consumables, including the contact tip, nozzle, and liner, as they wear out over time, affecting weld quality.
Wire Feeder Maintenance: Ensure the wire feeds smoothly. Occasionally, dismantle and clean the drive rolls and check the tension, adjusting as needed for consistent feeding.
Gas Supply Check: Regularly inspect the gas supply hoses for leaks and ensure the gas flow is correctly set for your application.
Software Updates: If your MIG welder has digital controls or software, check for updates from the manufacturer's website to ensure optimal performance.
Annual Servicing: Consider having a professional service the welder annually, especially to check internal components, electrical connections, and calibrate any digital controls.
For more detailed information and guidelines, always refer to your MIG welder’s manual and the manufacturer’s website:
Staying proactive with these maintenance steps will help ensure your MIG welder operates efficiently, safely, and lasts for years.
How to Display Welding Equipment Maintenance Skills on Your Resume
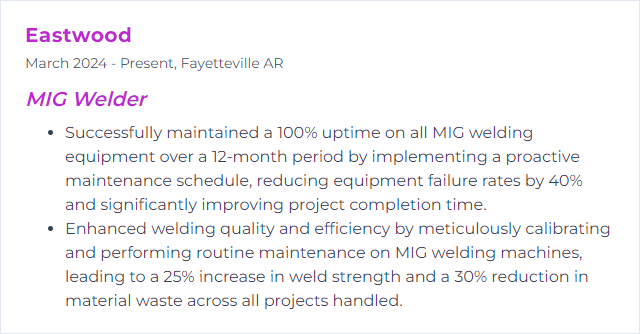
11. Quality Control
Quality Control for an MIG Welder involves systematic inspection, testing, and verification of the welding process and outcomes to ensure welds meet predefined standards for strength, appearance, and safety, adhering to relevant specifications and regulations.
Why It's Important
Quality control is crucial for an MIG welder to ensure weld integrity, strength, and safety, preventing costly rework, material wastage, and ensuring compliance with industry standards and specifications.
How to Improve Quality Control Skills
Improving quality control for an MIG welder involves several key steps focused on equipment maintenance, operator training, and process monitoring:
Regular Equipment Maintenance: Ensure the MIG welder and its components are regularly checked and maintained. This includes cleaning, checking wire feed mechanisms, and ensuring proper gas flow. Lincoln Electric's maintenance tips provide a comprehensive guide.
Skilled Operator Training: Invest in continuous training for operators to keep them updated on the latest welding techniques and safety practices. Miller Welds Training Solutions offers resources and courses for skill improvement.
Use of Quality Materials: Only use high-quality welding wire and gas to reduce the chances of weld defects. Information on selecting the right materials can be found through suppliers like Hobart Brothers Performance Welding Products.
Implement Welding Procedures: Develop and adhere to standardized welding procedures to ensure consistency. The American Welding Society (AWS) provides guidelines and standards for welding practices.
Continuous Quality Monitoring: Implement a system for continuous monitoring and inspection of welds using tools like visual inspection and non-destructive testing (NDT). The American Society for Nondestructive Testing (ASNT) offers resources on NDT techniques suitable for weld inspection.
Feedback and Corrective Actions: Establish a feedback loop for identifying defects and implementing corrective actions. Continuous improvement practices can lead to higher quality welds over time.
By focusing on these areas, you can significantly improve the quality control of MIG welding operations.
How to Display Quality Control Skills on Your Resume
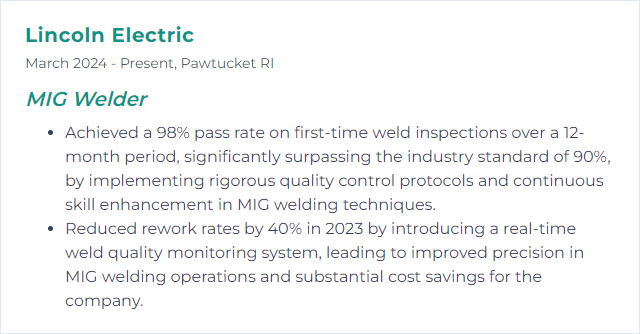
12. Thermal Cutting
Thermal cutting is a process that uses heat to cut through metal materials. In the context of MIG welding, it may involve the use of a separate cutting torch that employs a high-temperature flame or plasma to melt and sever metal, rather than the MIG welder itself, which is primarily designed for joining materials by melting a wire electrode and workpiece metal together.
Why It's Important
Thermal cutting is crucial for an MIG welder because it enables precise and efficient cutting of metals to prepare or fit parts for welding, ensuring high-quality welds and reducing material waste.
How to Improve Thermal Cutting Skills
Improving thermal cutting with an MIG welder involves several steps focusing on equipment optimization, technique refinement, and safety measures. Here’s a concise guide:
Select Appropriate Gas and Wire: Use a gas mixture optimized for cutting; argon and carbon dioxide (CO2) mixtures are common. Choose the correct wire diameter and material for the task (MillerWelds Guide).
Optimize Cutting Speed: Adjust the speed of your cut to avoid excessive melting or insufficient penetration. This depends on the thickness of the material and the power of your MIG welder (Lincoln Electric Cutting Guide).
Maintain Correct Torch Angle: Holding the torch at the right angle ensures efficient cutting and reduces the need for post-processing. A slight angle (around 15 degrees) is usually recommended for cutting applications.
Ensure Proper Equipment Maintenance: Regularly check and maintain your MIG welder and accessories. Clean and replace consumables as needed to ensure optimal performance (ESAB Welding & Cutting).
Use the Correct Power Settings: Adjust voltage and amperage based on the material thickness. Higher power is needed for thicker materials, but too much power can lead to excessive heat and lower cut quality.
Practice Proper Safety Measures: Always wear appropriate safety gear, including eye protection, gloves, and a respirator if necessary. Ensure good ventilation in your working area to avoid inhalation of harmful fumes (OSHA Safety Standards).
By focusing on these areas, you can significantly improve the quality and efficiency of your thermal cutting processes using an MIG welder.
How to Display Thermal Cutting Skills on Your Resume
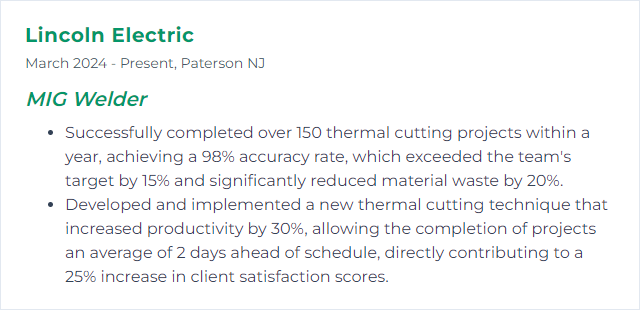