Top 12 Tig Welder Skills to Put on Your Resume
Mastering the art of TIG welding requires a unique combination of technical prowess and artistic skill, making it a sought-after trade in various industries. To stand out in the competitive job market, highlighting your top TIG welder skills on your resume is crucial, showcasing your ability to not only perform precise welds but also solve complex fabrication challenges.
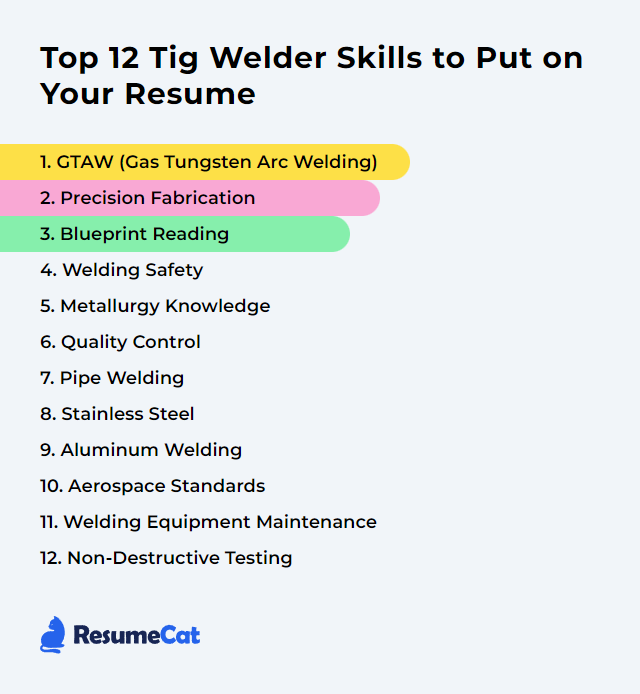
Tig Welder Skills
- GTAW (Gas Tungsten Arc Welding)
- Precision Fabrication
- Blueprint Reading
- Welding Safety
- Metallurgy Knowledge
- Quality Control
- Pipe Welding
- Stainless Steel
- Aluminum Welding
- Aerospace Standards
- Welding Equipment Maintenance
- Non-Destructive Testing
1. GTAW (Gas Tungsten Arc Welding)
GTAW (Gas Tungsten Arc Welding), also known as TIG (Tungsten Inert Gas) welding, is a process that uses a non-consumable tungsten electrode to produce the weld. The weld area is protected from atmospheric contamination by an inert shielding gas (argon or helium), and filler metal is optionally added to the weld pool. This method allows for precise control, producing high-quality and clean welds on a variety of metals.
Why It's Important
GTAW (Gas Tungsten Arc Welding), important for a TIG welder, offers precise, high-quality welds on a variety of metals with minimal spatter, making it ideal for thin materials and critical welds.
How to Improve GTAW (Gas Tungsten Arc Welding) Skills
Improving GTAW (Gas Tungsten Arc Welding) involves several key practices and considerations to enhance the quality and efficiency of your welding. Here are concise tips to improve your TIG welding:
Use the Correct Tungsten Electrode: Select the appropriate tungsten electrode for your material type and thickness. Here's a guide to choosing the right one.
Prepare the Electrode: Sharpen the electrode to a fine point for thin metals and a blunter tip for thicker materials. Electrode preparation tips.
Cleanliness: Ensure the base metal and filler rod are clean and free of contaminants. Use a dedicated stainless steel brush or appropriate chemical cleaner on the weld area. Cleaning for TIG welding.
Proper Shielding Gas: Typically, argon or an argon-helium mix is used. The right choice depends on the material and thickness. Shielding gas guide.
Gas Flow Rate: Adjust the gas flow rate appropriately, typically between 15-20 CFH, to protect the weld area without causing turbulence.
Control Heat Input: Use a foot pedal or fingertip control to precisely control the heat input, preventing warping and reducing defects.
Practice Hand Steadiness: TIG welding demands steady hands for precise welds. Practice controlling the torch and feeding the filler rod smoothly.
Correct Torch Angle: Maintain a 15-20 degree angle with the torch to the workpiece to optimize the weld pool's shape and penetration.
Filler Material: Use the correct filler material matching the base metal's properties. Filler metal selection.
Welding Technique: Practice different welding techniques (e.g., walking the cup, freehand) to improve your skill and adaptability.
PPE: Always use proper Personal Protective Equipment (PPE) to ensure safety while welding. PPE for welding.
By focusing on these aspects, you can significantly improve your GTAW skills and outcomes.
How to Display GTAW (Gas Tungsten Arc Welding) Skills on Your Resume
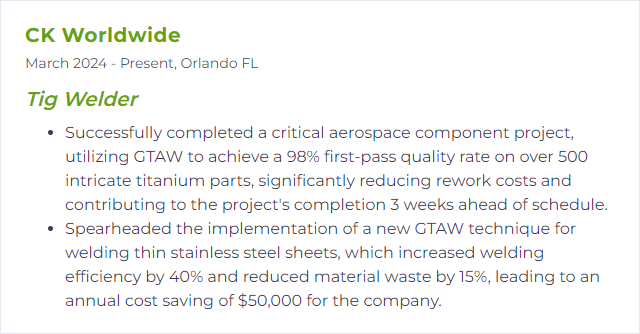
2. Precision Fabrication
Precision fabrication, in the context of a TIG welder, refers to the highly accurate and detailed process of joining metal parts using Tungsten Inert Gas welding, ensuring strong, clean, and precise welds for complex or delicate applications.
Why It's Important
Precision fabrication is crucial for a TIG welder because it ensures the welding process achieves high-quality, accurate, and clean welds with minimal defects, essential for applications demanding strict tolerances and aesthetic finishes.
How to Improve Precision Fabrication Skills
Improving precision in TIG welding involves refining your technique, choosing the right equipment, and understanding the material you're working with. Here are concise tips:
Select the Right Tungsten Electrode: Use an appropriate tungsten electrode for the material you're welding. American Welding Society (AWS) provides guidelines on electrode selection.
Control Your Arc Length: Maintain a consistent, short arc length to improve welding accuracy. This Lincoln Electric guide offers insights on arc control.
Use a Foot Pedal or Finger Control: For better heat control, use a foot pedal or finger control. This allows for adjustments during welding, improving precision. Miller Welds explains the benefits of each control type.
Practice Cleanliness: Keep your workspace, material, and tools clean. Contaminants can affect weld quality. Refer to Hobart Institute of Welding Technology for best practices in welding cleanliness.
Choose Appropriate Filler Material: Match the filler material closely with the base material. The AWS Filler Metal Selector can help in selection.
Optimize Gas Flow: Use the correct type and amount of shielding gas to protect your weld pool. Welding Design & Fabrication has resources on gas selection.
Post-Weld Treatment: Consider post-weld treatments like stress relieving or annealing for certain materials to improve weld quality. ASM International provides information on material properties and treatments.
By focusing on these areas, a TIG welder can significantly improve precision in fabrication.
How to Display Precision Fabrication Skills on Your Resume

3. Blueprint Reading
Blueprint reading for a TIG welder involves interpreting technical drawings and plans to understand the specifications for welding projects, including dimensions, materials, and weld symbols, to ensure accurate and precise fabrication and assembly of metal parts.
Why It's Important
Blueprint reading is crucial for a TIG welder because it enables accurate interpretation of welding symbols, dimensions, and specifications, ensuring precision in welds, adherence to design requirements, and quality control in fabrication processes.
How to Improve Blueprint Reading Skills
To improve Blueprint Reading for a TIG Welder, follow these concise steps:
Learn the Basics: Understand the foundational symbols, abbreviations, and drawing types used in welding blueprints. The American Welding Society (AWS) provides resources and courses on welding symbols and blueprints.
Practice Regularly: Apply your knowledge by practicing with actual blueprints. Websites like Welding Tips and Tricks offer practical advice and examples.
Use Online Resources: Explore online tutorials and courses specifically designed for welders. Platforms like LinkedIn Learning and Udemy offer courses on blueprint reading.
Join Forums and Groups: Engage with communities such as WeldingWeb to exchange knowledge and experiences with other professionals.
Get Hands-On Experience: Put theory into practice by working on projects that require blueprint reading, gradually increasing in complexity as your skills improve.
By consistently applying these steps, you'll enhance your blueprint reading skills as a TIG welder.
How to Display Blueprint Reading Skills on Your Resume
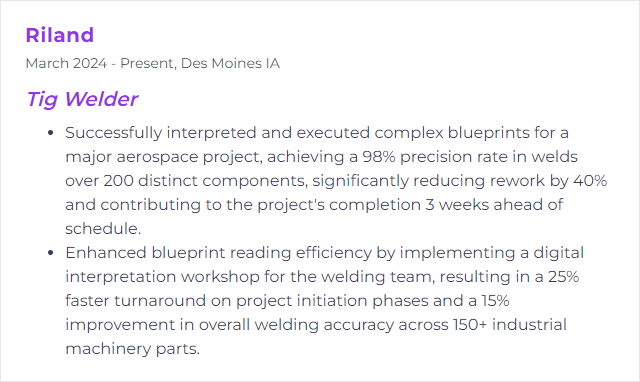
4. Welding Safety
Welding safety for TIG welders involves protecting against UV radiation, avoiding burns from hot metal, preventing inhalation of harmful fumes, ensuring electrical safety, and using appropriate personal protective equipment such as helmets with proper shading, gloves, and long-sleeve jackets. Proper ventilation and awareness of fire hazards are also crucial.
Why It's Important
Welding safety is crucial, especially for TIG welders, to prevent harmful exposure to intense ultraviolet light, toxic fumes, electric shock, and burns, ensuring the welder's health and safety during precise and quality welding operations.
How to Improve Welding Safety Skills
Improving welding safety, especially for TIG welders, involves several critical steps focused on protecting the welder from electrical hazards, harmful light radiation, and hazardous fumes. Here’s a concise guide:
Wear Appropriate PPE: Ensure wearing the right personal protective equipment (PPE) including a welding helmet with a suitable filter lens, fire-resistant clothing, gloves, and safety shoes. American Welding Society (AWS) provides guidelines on selecting appropriate PPE.
Ventilation and Fume Extraction: Use local exhaust ventilation or fume extraction systems to remove harmful welding fumes and gases from the breathing zone. OSHA’s Ventilation Guide offers detailed recommendations.
Electrical Safety: Follow the manufacturer’s guidelines for installing and grounding the TIG welder. Use insulated tools and wear dry, hole-free gloves to prevent electrical shocks. National Fire Protection Association (NFPA) 70E outlines standards for electrical safety in the workplace.
Proper Training: Receive comprehensive training on TIG welding techniques, equipment use, and emergency procedures. The American Welding Society’s Education programs can provide valuable resources and certifications.
Regular Equipment Maintenance: Regularly inspect and maintain the TIG welder and accessories to ensure they are in good working condition, following the manufacturer’s maintenance schedule.
Safe Work Environment: Keep the welding area well-lit, clean, and free of any combustible materials. Ensure that fire extinguishers and first-aid kits are easily accessible.
By meticulously following these safety practices, TIG welders can significantly reduce the risks associated with welding, ensuring a safer work environment.
How to Display Welding Safety Skills on Your Resume
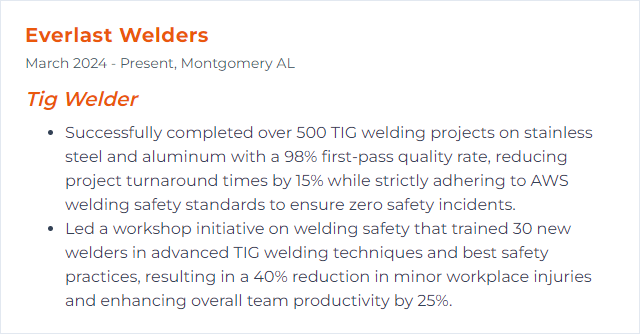
5. Metallurgy Knowledge
Metallurgy Knowledge for a TIG welder involves understanding the properties, behaviors, and reactions of different metals and alloys when subjected to high temperatures during welding. This includes knowledge of melting points, thermal conductivity, and how different materials respond to cooling, which is crucial for ensuring strong, durable welds and preventing defects such as cracking or distortion.
Why It's Important
Metallurgy knowledge is crucial for a TIG welder to understand the properties of metals being joined, ensuring optimal weld strength, avoiding defects (like cracks or porosity), and selecting appropriate filler materials and welding parameters for high-quality, durable welds.
How to Improve Metallurgy Knowledge Skills
To enhance your metallurgy knowledge as a TIG welder, focus on understanding the properties and behaviors of different metals during the welding process. Here's a concise guide:
Online Courses and Webinars: Platforms like Coursera and edX offer courses on materials science and engineering that include aspects of metallurgy.
Technical Books and eBooks: Refer to specialized books such as "Metallurgy for the Non-Metallurgist" available on Amazon, which covers fundamental concepts.
Industry Journals and Publications: Websites like ScienceDirect provide access to the latest research and articles on metallurgy.
Professional Associations: Join organizations like the American Welding Society (AWS), which offers resources, courses, and certifications tailored to welding professionals.
Hands-On Practice: Apply theoretical knowledge through practice and experimentation. Material suppliers and manufacturers often provide technical data sheets or guides, useful for understanding specific material characteristics.
Workshops and Seminars: Participate in industry-relevant workshops and seminars; these are often announced on professional platforms like LinkedIn.
By combining these resources with practical experience, you'll progressively deepen your understanding of metallurgy in relation to TIG welding.
How to Display Metallurgy Knowledge Skills on Your Resume
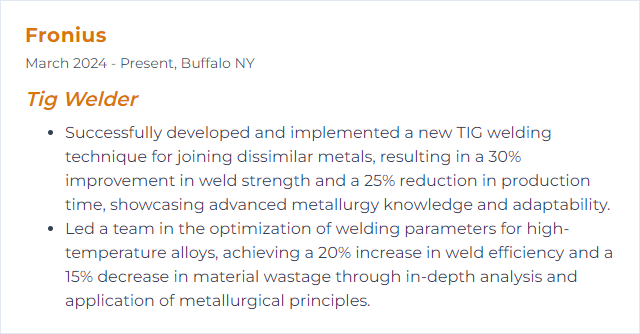
6. Quality Control
Quality Control (QC) in the context of TIG welding involves the systematic process of checking the welds to ensure they meet the specified standards for strength, durability, and appearance, including adherence to safety regulations and project specifications. This includes inspecting welds for defects like porosity, cracks, or incorrect dimensions.
Why It's Important
Quality control is crucial for a TIG welder to ensure welds are strong, consistent, and free from defects, guaranteeing the safety, reliability, and longevity of the welded structures or components.
How to Improve Quality Control Skills
Improving Quality Control for a TIG welder involves several key steps focused on equipment maintenance, skill enhancement, and process optimization. Here's a concise guide:
Regular Equipment Checks: Ensure the TIG welder and accessories are in optimal condition. Regular maintenance prevents defects caused by equipment failure.
Welder Training: Continuous training for welders on new techniques and materials enhances skill levels and adaptation to varying project requirements.
Use of Quality Materials: Employ high-grade welding materials to reduce contamination and improve weld integrity. This guide on materials can help in selection.
Implement Welding Standards: Adhere to industry standards like those from the American Welding Society (AWS) to ensure consistent quality and compliance.
Quality Inspection: Incorporate regular and thorough inspection processes using both visual and advanced techniques to detect and rectify issues promptly. Tools and methods for welding inspection are crucial.
Feedback Loop: Establish a feedback mechanism for continuous improvement. Analyzing errors and implementing corrective actions directly enhances quality control.
By focusing on these areas, TIG welders can significantly improve the quality control of their welding projects.
How to Display Quality Control Skills on Your Resume
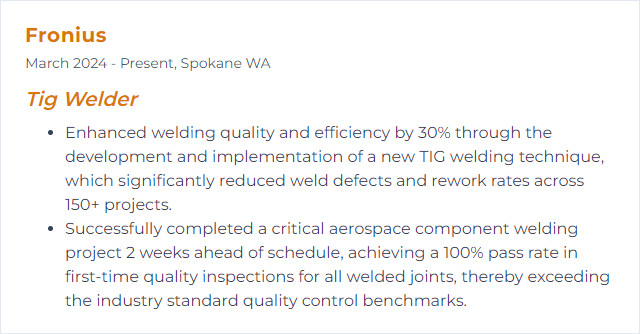
7. Pipe Welding
Pipe welding, in the context of TIG welding, involves joining cylindrical metal pieces using a tungsten electrode to produce high-quality, precise welds under a protective gas atmosphere. This process is commonly used for pipelines and tubing in various industries, requiring skilled manipulation of the welding torch and filler material.
Why It's Important
Pipe welding is crucial for ensuring the integrity and safety of pipelines that transport various substances, including water, gas, and oil. For a TIG welder, it involves precise and high-quality welding techniques to achieve strong, leak-proof joints essential for the reliable operation of pipeline systems.
How to Improve Pipe Welding Skills
Improving pipe welding, especially with TIG welding, involves practice, precision, and understanding the nuances of the welding process. Here are concise tips to enhance your skills:
Preparation: Ensure the pipe is clean and free from contaminants. Use a dedicated stainless steel wire brush for cleaning the area to be welded.
Equipment Setup: Choose the right tungsten electrode (2% lanthanated is versatile) and grind it to a point for precision. Tungsten Selection Guide.
Gas Choice: Use Argon as a shielding gas for its clean, high-quality weld characteristics. Shielding Gas for TIG.
Welding Technique: Maintain a steady hand and use a consistent travel speed to ensure even heat distribution. TIG Welding Techniques.
Heat Control: Manage the heat input by pulsing the pedal to prevent warping or blowing through the pipe.
Practice: Consistent practice on scrap pieces helps in mastering pipe angles and joint configurations.
Safety: Always prioritize safety by wearing appropriate gear and ensuring good ventilation. Welding Safety Tips.
Improving in TIG welding is a continuous process that combines knowledge with hands-on practice.
How to Display Pipe Welding Skills on Your Resume
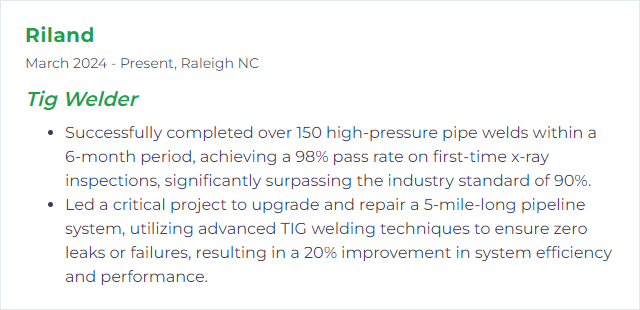
8. Stainless Steel
Stainless steel is a corrosion-resistant alloy of iron, chromium (at least 10.5%), and other elements, widely used in fabrication and suitable for TIG welding due to its durability and resistance to rust and tarnishing.
Why It's Important
Stainless steel is important for a TIG welder because it offers high strength, excellent corrosion resistance, and the ability to withstand high temperatures, making it ideal for creating durable, clean, and precise welds in a variety of applications.
How to Improve Stainless Steel Skills
To improve stainless steel welding using TIG (Tungsten Inert Gas) welding, follow these concise steps:
Cleanliness: Ensure the surface is free from contaminants. Use a dedicated stainless steel brush or solvent to clean the welding area. Cleaning Stainless Steel
Proper Equipment: Use a TIG welder with high-frequency start capability and a foot pedal for amperage control. Ensure you have a gas lens for better gas coverage. Choosing TIG Equipment
Appropriate Filler Material: Select a filler material that matches the stainless steel grade. Common choices include 308L, 309L, or 316L. Filler Metal Selection
Shielding Gas: Use a high-purity Argon gas for shielding to prevent oxidation and ensure clean welds. Understanding Shielding Gases
Right Technique: Maintain a sharp tungsten electrode, use a tight arc length, and keep a consistent travel speed to prevent overheating and warping. TIG Welding Techniques
Post-Weld Treatment: Depending on the application, consider post-weld treatments like passivation to restore the corrosion resistance of the heat-affected zone. Passivation of Stainless Steel
By focusing on these areas, you can significantly improve the quality of your stainless steel TIG welding.
How to Display Stainless Steel Skills on Your Resume
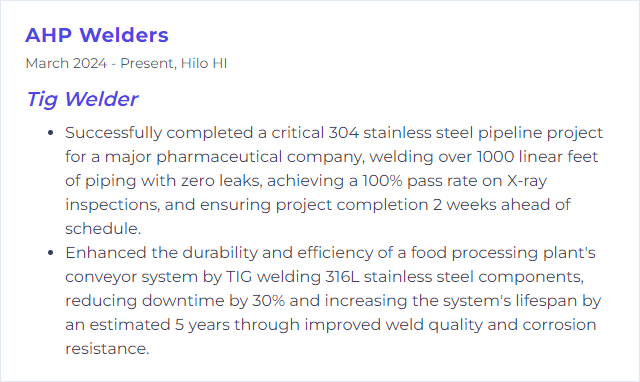
9. Aluminum Welding
Aluminum welding, specifically using a TIG (Tungsten Inert Gas) welder, involves the precise and clean fusion of aluminum parts by heating them with a tungsten electrode while protecting the weld area from atmospheric contamination with an inert gas, commonly argon.
Why It's Important
Aluminum welding, particularly with TIG (Tungsten Inert Gas) welders, is crucial because aluminum is a lightweight, corrosion-resistant metal widely used in various industries, including aerospace, automotive, and construction. TIG welding offers precise and clean welds for aluminum, essential for ensuring the structural integrity and performance of aluminum components in these critical applications.
How to Improve Aluminum Welding Skills
Improving aluminum welding with a TIG welder involves several key steps:
Cleanliness: Ensure the aluminum is clean before welding. Use a stainless steel brush and acetone or a dedicated aluminum cleaner to remove any oxide layer and contaminants. Cleaning Aluminum.
Equipment Setup: Use an AC (alternating current) setting on your TIG welder, and select the appropriate tungsten electrode, typically pure tungsten (green) or zirconiated (white) for aluminum. TIG Welding Aluminum.
Shielding Gas: Argon gas is preferred for its cleaning action and good arc stability. Ensure a proper flow rate to protect the weld pool adequately. Selecting the Right Shielding Gas.
Preheating: For thicker pieces, a gentle preheat can reduce the risk of cracking by minimizing the thermal gradient. Preheating Aluminum.
Practice & Technique: Maintain a steady hand and a consistent travel speed. Practice your technique to improve control and consistency, especially with the foot pedal for amperage control. TIG Welding Techniques.
By focusing on cleanliness, the correct setup, and refining your technique, you can significantly improve your TIG welding results on aluminum.
How to Display Aluminum Welding Skills on Your Resume
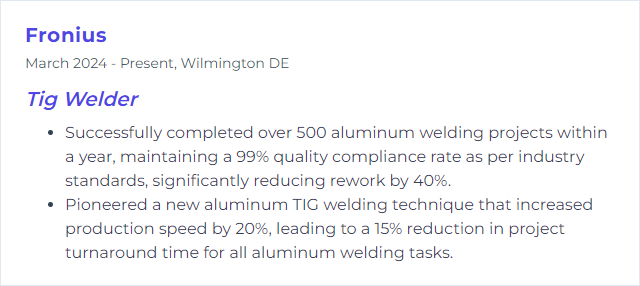
10. Aerospace Standards
Aerospace Standards for a TIG welder refer to the specific, stringent requirements and guidelines set for TIG welding processes, materials, and techniques used in the aerospace industry to ensure safety, reliability, and quality in the manufacturing and repair of aerospace components and structures.
Why It's Important
Aerospace standards are crucial for a TIG welder as they ensure the safety, reliability, and performance of aerospace components through precise specifications and quality requirements, directly affecting flight safety and operational efficiency.
How to Improve Aerospace Standards Skills
Improving aerospace standards, especially for a TIG welder, involves focusing on precision, safety, and adherence to international regulations. Key steps include:
Regular Training: Ensure continuous education and certification for welders in the latest aerospace materials and TIG welding techniques. FAA Training Standards.
Quality Control: Implement rigorous quality control measures, including inspections and non-destructive testing, to meet or exceed aerospace standards. ASTM International Standards.
Certification: Obtain and maintain relevant welding certifications, such as those from the American Welding Society (AWS) specifically for aerospace applications. AWS Aerospace Applications.
Adopt New Technologies: Integrate advanced welding technologies and materials, like high-strength alloys, to improve weld quality and efficiency. NASA Technical Standards.
Compliance: Stay updated and comply with international aerospace standards like those from the International Aerospace Quality Group (IAQG). IAQG Standards.
Safety Measures: Enhance safety protocols to protect welders from occupational hazards and ensure the integrity of welds in aerospace components. Occupational Safety and Health Administration (OSHA).
By focusing on these areas, aerospace standards can be significantly improved, ensuring the reliability and safety of aerospace components and systems.
How to Display Aerospace Standards Skills on Your Resume
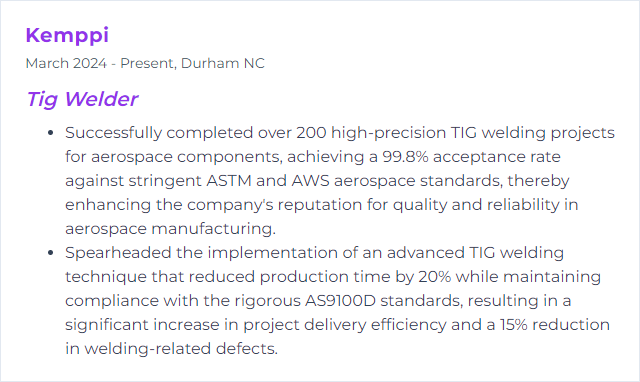
11. Welding Equipment Maintenance
Welding Equipment Maintenance, specifically for a TIG welder, involves regular inspection, cleaning, and repair of the welder and its components to ensure optimal performance, safety, and longevity. This includes checking and replacing tungsten electrodes, cleaning gas nozzles, inspecting gas hoses and electrical cables, and ensuring the cooling system functions properly.
Why It's Important
Welding equipment maintenance, especially for a TIG welder, is crucial to ensure consistent, high-quality welds, extend equipment lifespan, minimize downtime, and reduce the risk of accidents or equipment failure.
How to Improve Welding Equipment Maintenance Skills
Improving welding equipment maintenance, particularly for a TIG welder, involves regular inspections, timely repairs, and proper care. Here's a concise guide:
Daily Inspection: Before each use, inspect cables, connectors, and torch for wear or damage. Ensure the gas supply is sufficient and check for leaks.
Regular Cleaning: After use, clean the torch nozzle and electrode. Remove any accumulated spatter or debris to ensure smooth operation (Lincoln Electric).
Periodic Maintenance: Replace consumables like electrodes and nozzles as needed. Regularly check and replace gas hoses and regulators showing signs of wear (MillerWelds).
Correct Storage: Store the TIG welder in a dry, clean area. Cover the welder to protect it from dust and moisture.
Professional Servicing: Annually, have the welder inspected and serviced by a professional to address any internal issues and ensure optimal performance (ESAB Welding & Cutting).
By following these steps, you can extend the life of your TIG welder and maintain its performance.
How to Display Welding Equipment Maintenance Skills on Your Resume
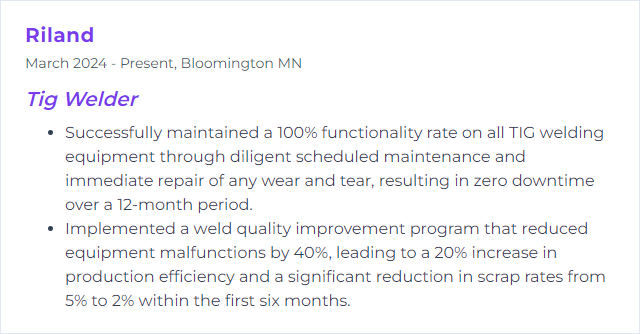
12. Non-Destructive Testing
Non-Destructive Testing (NDT) for a TIG welder involves evaluating the integrity and quality of welds without causing damage to the material. Techniques such as ultrasonic testing, radiography, and visual inspection are used to detect surface and subsurface defects, ensuring the weld meets safety and performance standards.
Why It's Important
Non-Destructive Testing (NDT) is crucial for a TIG welder as it ensures the integrity and safety of welds without causing damage, enabling the detection of defects or inconsistencies that may affect performance or lead to failure, thus guaranteeing the quality and reliability of the welded components.
How to Improve Non-Destructive Testing Skills
To improve Non-Destructive Testing (NDT) for TIG welding, consider the following concise strategies:
Enhance Training: Ensure operators are highly trained in NDT techniques specific to TIG welding, focusing on the nuances of detecting defects in finer welds. The American Welding Society (AWS) offers resources and courses on welding inspection and NDT.
Utilize Advanced Techniques: Incorporate advanced NDT methods like Phased Array Ultrasonic Testing (PAUT) and Digital Radiography (DR) for more detailed inspections. The American Society for Nondestructive Testing (ASNT) provides insights into these technologies.
Regular Calibration: Regularly calibrate NDT equipment to ensure accuracy in detecting flaws. Equipment manufacturers often provide calibration guidelines.
Implement Automated NDT: Consider automated NDT systems for consistent and repeatable inspections, especially in critical applications. This approach can be explored further through industrial automation resources.
Adopt a Multi-Method Approach: Use a combination of NDT methods (like Ultrasonic Testing (UT), Magnetic Particle Testing (MPT), and Visual Inspection (VI)) to cover the limitations of each technique. Diversifying methods increases detection rates of various types of defects.
Continuous Improvement: Engage in continuous improvement practices by regularly reviewing and updating NDT procedures based on new findings, technologies, and feedback from NDT operations.
For a deeper understanding and resources on improving NDT practices in TIG welding, refer to professional organizations such as the American Welding Society and the American Society for Nondestructive Testing.
How to Display Non-Destructive Testing Skills on Your Resume
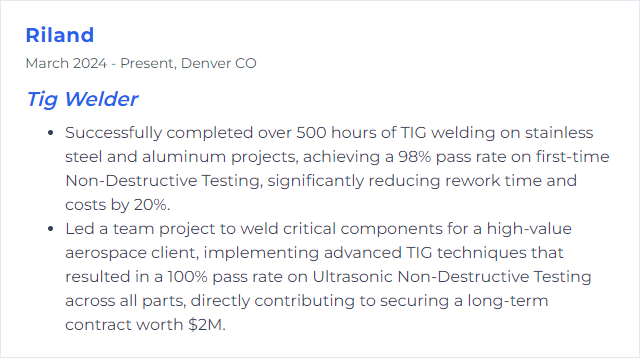