Top 12 Structural Welder Skills to Put on Your Resume
Crafting an effective resume as a structural welder requires showcasing a blend of technical proficiency and soft skills that demonstrate your capability to tackle complex projects with precision and collaboration. Highlighting the top structural welder skills on your resume not only underscores your expertise but also positions you as a valuable asset to potential employers in the competitive construction and manufacturing industries.
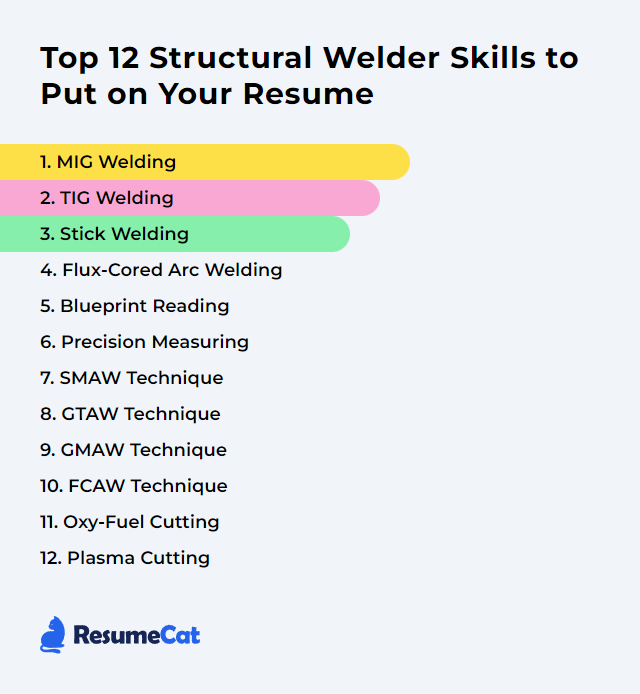
Structural Welder Skills
- MIG Welding
- TIG Welding
- Stick Welding
- Flux-Cored Arc Welding
- Blueprint Reading
- Precision Measuring
- SMAW Technique
- GTAW Technique
- GMAW Technique
- FCAW Technique
- Oxy-Fuel Cutting
- Plasma Cutting
1. MIG Welding
MIG Welding, for a structural welder, involves using a continuously feeding wire electrode and a shielding gas through a welding gun to fuse metal components together, suitable for strong, durable constructions in steel and aluminum structures.
Why It's Important
MIG welding is important for a Structural Welder because it provides a strong, versatile, and efficient method for joining various types and thicknesses of metals, crucial for the integrity and durability of structural components.
How to Improve MIG Welding Skills
Improving MIG welding, especially for a structural welder, involves fine-tuning techniques, equipment maintenance, and continuous learning. Here are concise tips:
Maintain a Consistent Travel Speed: Ensure uniform weld bead and penetration by keeping a steady travel speed. Miller Welds offers insights on adjusting speed for various thicknesses.
Correct Stick-Out Length: Aim for a stick-out length of 3/8 to 1/2 inch. This affects the welding current and bead shape. Lincoln Electric provides guidance on selecting the right wire and optimizing stick-out.
Choose the Right Gas and Material: Use the appropriate shielding gas; CO2 for deeper penetration or Argon-CO2 mixes for a smoother bead profile. Select the correct wire type for your material. Welding Material Sales can guide on material selection.
Proper Machine Set-Up: Optimize your MIG welder settings based on material thickness and type. Consult your welder's manual and experiment on scrap material first. Hobart Welders discusses adjustments for voltage and wire feed speed.
Regular Equipment Maintenance: Keep your MIG welder and accessories in top condition. Cleanliness and proper storage contribute to performance. Esab Welding & Cutting details MIG gun maintenance tips.
Practice Different Positions: Welding in various positions (flat, vertical, overhead) is crucial for structural work. Practice makes perfect. The Welder Magazine highlights tips for welding in different positions.
Continuing Education: Stay updated with new techniques, materials, and technologies. Online resources, workshops, and certifications can bolster your skills. American Welding Society offers courses and certifications for professional development.
By focusing on these areas, you can significantly improve your MIG welding skills, contributing to higher quality work in structural applications.
How to Display MIG Welding Skills on Your Resume
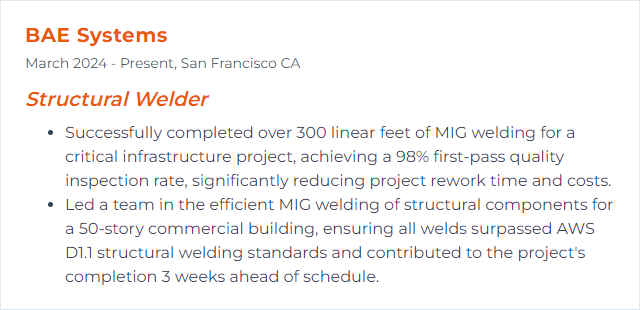
2. TIG Welding
TIG welding, or Tungsten Inert Gas welding, is a precise welding technique using a non-consumable tungsten electrode to produce high-quality, spatter-free welds on a variety of metals, ideal for thin materials and complex structures in structural welding applications.
Why It's Important
TIG welding is important for a structural welder because it provides precise, high-quality welds essential for the strength and integrity of critical structures, allowing for the welding of a wide range of metals with minimal distortion and maximum durability.
How to Improve TIG Welding Skills
Improving TIG welding, particularly for a structural welder, involves focusing on precise technique, understanding material properties, and practicing consistently. Here are concise tips with relevant resources:
Cleanliness: Ensure your material and tungsten are clean to prevent contamination. Use a dedicated stainless steel brush for cleaning metals and properly grind your tungsten. Miller Electric
Tungsten Preparation: Sharpen tungsten electrodes appropriately for the type and thickness of the metal. The angle and tip shape can significantly affect the arc. Lincoln Electric
Control and Posture: Maintain a comfortable and steady posture to ensure a steady hand. Use both hands or support devices if necessary. Welding Tips and Tricks
Heat Management: Master the control of heat input by adjusting amperage and travel speed to avoid warping or overheating the metal. American Welding Society
Practice Different Positions: As a structural welder, practice welding in various positions (flat, horizontal, vertical, overhead) to adapt to real-world scenarios. Hobart Institute of Welding Technology
Use of Filler Material: Correctly choose and use filler material based on the base metals being welded. Match the filler to the base material for better strength and aesthetics. ESAB
Pulse Welding Technique: For thin materials or when precision is paramount, learn pulse welding to control heat input and reduce distortion. Welding.com
Consistent practice, combined with the study of materials and techniques from these resources, will significantly improve TIG welding skills.
How to Display TIG Welding Skills on Your Resume
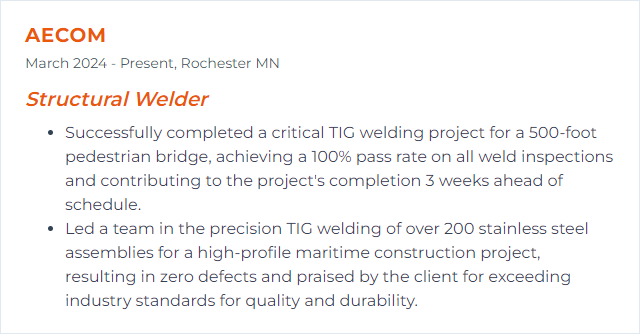
3. Stick Welding
Stick welding, also known as Shielded Metal Arc Welding (SMAW), is a manual welding process that uses a consumable electrode coated in flux to lay the weld. It's widely used in structural welding due to its versatility, ability to weld thick materials, and effectiveness in outdoor and windy conditions.
Why It's Important
Stick welding, essential for a structural welder, offers versatility in welding various materials and positions, crucial for the diverse needs of structural construction and repair, even in challenging environments or with limited access.
How to Improve Stick Welding Skills
To improve stick welding, especially for a structural welder, focus on these key areas:
Equipment Setup: Ensure your welder is properly set up, with correct amperage based on the electrode and material thickness. Miller Welds Guide provides insight into setting up your equipment.
Electrode Choice: Select the appropriate electrode for your material type and welding position. The Lincoln Electric Stick Electrode Guide can help you choose.
Cleanliness: Clean the workpiece thoroughly before welding; any contaminants can cause defects. Hobart Welding Guide emphasizes the importance of preparation.
Technique: Practice maintaining a consistent arc length, travel speed, and angle. For technique improvement tips, visit Welding Tips and Tricks.
Practice: Regular practice on scrap pieces or in different positions will improve your skill. Focus on vertical, overhead, and out-of-position welding, as these are crucial for structural welders.
Safety: Always prioritize safety by wearing the correct PPE and ensuring a safe workspace. Familiarize yourself with safety guidelines at OSHA Welding, Cutting, and Brazing.
Improving stick welding requires attention to detail, understanding of materials, and continuous practice. Utilize these resources and focus on mastering the fundamentals for significant improvement.
How to Display Stick Welding Skills on Your Resume
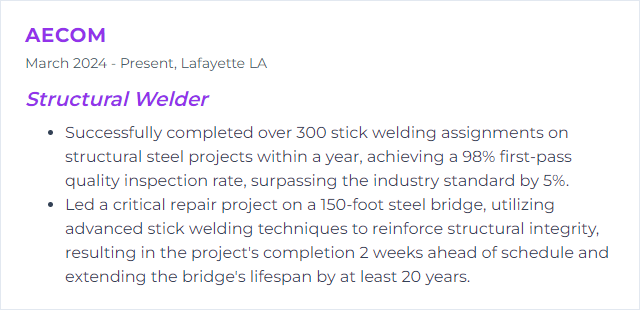
4. Flux-Cored Arc Welding
Flux-Cored Arc Welding (FCAW) is a semi-automatic or automatic arc welding process used by structural welders. It involves using a continuously-fed tubular electrode filled with flux to produce the weld, providing deep penetration for thick materials, and allowing for welding in all positions. FCAW is known for its high welding speed and portability, making it suitable for construction and repair work.
Why It's Important
Flux-Cored Arc Welding (FCAW) is important for a Structural Welder because it provides high welding speed and efficiency, excellent penetration, and superior weld strength, crucial for constructing durable and safe structures.
How to Improve Flux-Cored Arc Welding Skills
Improving Flux-Cored Arc Welding (FCAW) involves a combination of technique refinement, proper equipment maintenance, and the use of quality materials. Here's a concise guide for a Structural Welder looking to enhance their FCAW skills:
Technique Optimization: Focus on maintaining a consistent stick-out length and travel speed. Proper manipulation of the welding gun can significantly affect bead appearance and penetration. Lincoln Electric offers detailed insights on technique.
Equipment Maintenance: Regularly inspect and clean your welding machine, gun, and contact tips to prevent feeding issues or electrical problems. Proper care ensures consistent electrical conductivity and arc stability. Miller Welds provides maintenance tips for welding equipment.
Material Selection: Use high-quality filler metals and gas shielding (when applicable) appropriate for the base material and welding position. This can significantly impact the weld's mechanical properties. ESAB explains the differences in flux-cored wires and their applications.
Practice and Training: Continuously practice different welding positions and joint types. Education on advanced welding techniques and technologies can also be beneficial. American Welding Society (AWS) offers courses and certifications for welders at all levels.
Preparation and Cleanliness: Ensure surfaces are clean and properly prepared before welding to reduce the potential for defects. Proper joint preparation can also improve weld quality.
By focusing on these areas, a Structural Welder can achieve significant improvements in Flux-Cored Arc Welding performance.
How to Display Flux-Cored Arc Welding Skills on Your Resume
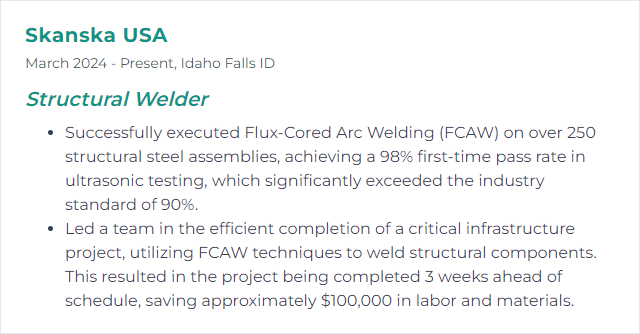
5. Blueprint Reading
Blueprint reading for a structural welder involves interpreting and understanding detailed technical drawings that specify the design, dimensions, materials, and welding specifications required for constructing and assembling structural components and frameworks.
Why It's Important
Blueprint reading is crucial for a structural welder because it ensures accurate interpretation of design specifications and weld symbols, leading to precise fabrication and assembly of structural components, ultimately ensuring the integrity and safety of the constructed structure.
How to Improve Blueprint Reading Skills
Improving blueprint reading skills, especially for a structural welder, involves understanding symbols, dimensions, and specifications related to welding projects. Here's a concise guide:
Familiarize with Symbols: Learn the basic and advanced welding symbols as per the American Welding Society (AWS) standards. AWS Symbols offer a detailed guide.
Understand Scales: Practice interpreting scales on blueprints to ensure accurate dimensions and layouts.
Study Specifications: Pay attention to specifications detailing materials, weld types, and sizes necessary for the project.
Practice: Regularly practice reading different blueprints to improve speed and accuracy.
Courses and Certifications: Consider enrolling in courses or obtaining certifications focused on blueprint reading. American Welding Society Courses provide specialized training.
Use Resources: Utilize online resources and books for further learning. Lincoln Electric offers a variety of educational materials.
By continuously practicing and utilizing available resources, you can significantly improve your blueprint reading skills as a structural welder.
How to Display Blueprint Reading Skills on Your Resume
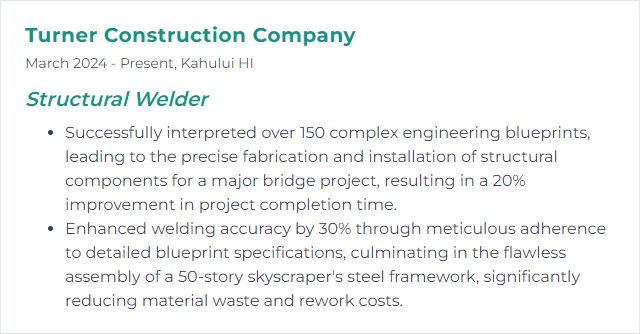
6. Precision Measuring
Precision measuring in the context of a structural welder refers to the use of specialized tools and techniques to accurately determine the dimensions, angles, and alignment of components to ensure they meet specified tolerances and structural requirements before, during, and after welding.
Why It's Important
Precision measuring is crucial for a structural welder to ensure that welded structures are dimensionally accurate and fit perfectly, maintaining structural integrity and safety.
How to Improve Precision Measuring Skills
Improving precision in measuring for a structural welder involves enhancing both technique and the use of appropriate tools. Here's a concise guide:
Use High-Quality Tools: Opt for high-precision tools like digital calipers, micrometers, and laser levels. Lincoln Electric and Miller Electric are reputable brands offering precision tools suitable for welding applications.
Regular Calibration: Ensure your measuring tools are regularly calibrated. Follow the manufacturer's guidelines for calibration to maintain accuracy. NIST provides standards and guidelines for calibration.
Proper Tool Usage: Understand and follow best practices for each measuring tool. Misuse can lead to inaccurate measurements. AWS (American Welding Society) offers resources and courses on proper tool usage and welding techniques.
Environment Control: Minimize external factors such as temperature fluctuations and vibrations that can affect measurements. Implementing controlled conditions can improve the precision of your measurements.
Training and Continuous Learning: Engage in ongoing training and education to stay updated on the latest measuring techniques and tools. Hobart Institute of Welding Technology provides courses that can enhance your skills.
By focusing on these areas, a structural welder can significantly improve the precision of their measurements, contributing to higher-quality and more reliable welding outcomes.
How to Display Precision Measuring Skills on Your Resume
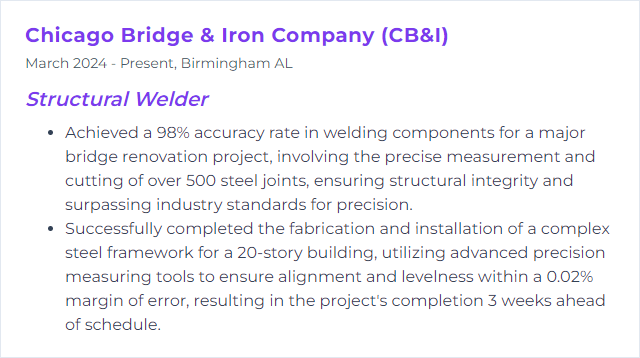
7. SMAW Technique
SMAW (Shielded Metal Arc Welding) is a manual arc welding process that uses a consumable electrode coated in flux to lay the weld. It's commonly used in structural welding for its versatility in welding various types and thicknesses of steel and iron.
Why It's Important
The SMAW (Shielded Metal Arc Welding) technique is important for a Structural Welder because it offers versatility in welding various types and thicknesses of metals, is suitable for outdoor and indoor use, and requires minimal equipment, making it highly adaptable and practical for constructing and repairing structures in diverse environments.
How to Improve SMAW Technique Skills
Improving your SMAW technique as a structural welder involves practice and understanding key concepts. Here’s a concise guide:
Position and Angle: Maintain a comfortable stance. Hold the electrode at a 15° to 45° angle to the workpiece. Miller Welds provides detailed guides on positioning.
Electrode Choice: Use the appropriate electrode for your material and job type. The American Welding Society (AWS) offers resources on electrode selection.
Travel Speed and Arc Length: Keep a consistent travel speed and short arc length. Practice maintaining a steady hand. Resources at Lincoln Electric can help understand these concepts.
Cleanliness: Ensure surfaces are clean and free of contaminants before welding. Hobart Institute of Welding Technology offers insights on preparation.
Practice Different Positions: Weld in flat, vertical, overhead, and horizontal positions. Welding Tips and Tricks has practical advice for various positions.
Heat Management: Learn to manage heat input to avoid warping or excessive penetration. Guidance can be found through The Fabricator.
Inspect and Adjust: Regularly inspect your welds and adjust your technique as necessary. The Welding Institute (TWI) can help with understanding weld quality and defects.
By focusing on these areas and seeking out resources from reputable sources, you can significantly improve your SMAW welding technique.
How to Display SMAW Technique Skills on Your Resume
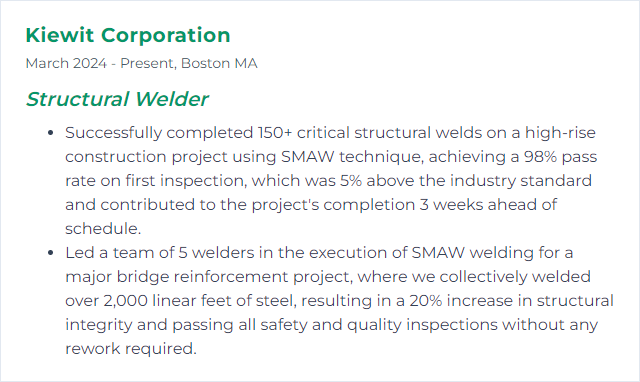
8. GTAW Technique
GTAW (Gas Tungsten Arc Welding), also known as TIG (Tungsten Inert Gas) welding, is a technique where a non-consumable tungsten electrode is used to produce the weld. For a Structural Welder, GTAW is valued for its ability to produce high-quality, precise welds on thinner materials or when welding at complex angles, particularly on stainless steel, aluminum, and other non-ferrous metals. The process involves the use of an inert gas shield, typically argon or helium, to protect the weld pool from atmospheric contamination.
Why It's Important
The GTAW (Gas Tungsten Arc Welding) technique is crucial for a Structural Welder because it provides high-quality, precision welds with superior strength and cleanliness, essential for the integrity and safety of structural components.
How to Improve GTAW Technique Skills
Improving your Gas Tungsten Arc Welding (GTAW) technique as a structural welder involves practice, understanding of the fundamentals, and refinement of your skills. Here are concise tips with resources for further exploration:
Maintain a Consistent Electrode Angle: Keep a consistent angle of 15-20 degrees to the workpiece. This helps in achieving a stable arc and uniform weld bead. WeldingTipsandTricks offers practical insights.
Control Arc Length: Keep the arc length short, about the diameter of the electrode. This improves arc stability and heat input control. The American Welding Society provides in-depth guidelines.
Use the Right Filler Material: Match the filler material with the base metals. This ensures compatibility and strength of the weld. Lincoln Electric has a selection guide for filler materials.
Cleanliness is Key: Ensure both the base material and filler rod are clean before welding to prevent contamination. MillerWelds emphasizes the importance of material preparation.
Practice Heat Control: GTAW is all about controlling the heat input. Use a foot pedal or fingertip control to manage the amperage and thus the heat. Precise heat control prevents warping and improves penetration. Hobart Institute of Welding Technology offers courses that focus on mastering heat control.
Posture and Hand Steadiness: Practice a comfortable welding position and steady your hand. This ensures consistent welds and reduces fatigue. The Fabricator provides tips on improving hand steadiness and posture.
Use a Tungsten Electrode Suitable for the Job: Selecting the right type of tungsten electrode (e.g., 2% lanthanated for steel and aluminum) affects the arc stability and welding performance. Welding Tips and Tricks has a guide on choosing tungsten electrodes.
By focusing on these areas and regularly seeking feedback on your work, you can enhance your GTAW technique significantly. Remember, mastering welding takes time and consistent practice.
How to Display GTAW Technique Skills on Your Resume
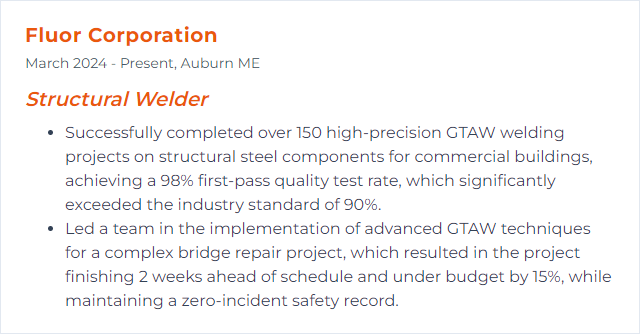
9. GMAW Technique
GMAW (Gas Metal Arc Welding) is a welding technique where an electric arc forms between a consumable wire electrode and the workpiece metals, which heats and melts them, forming a joint. This process is done under a shield of gas to prevent contamination. It's commonly used by structural welders for its efficiency and versatility in welding various types of structures.
Why It's Important
The GMAW (Gas Metal Arc Welding) technique is important for a structural welder because it offers high welding speed, efficiency, and versatility, enabling strong, continuous welds for a variety of metals and thicknesses essential in structural welding applications.
How to Improve GMAW Technique Skills
Improving your Gas Metal Arc Welding (GMAW) technique as a structural welder involves focusing on key areas such as equipment setup, body positioning, welding speed, and bead consistency. Here are concise tips for enhancement:
Equipment Setup: Ensure the correct setup of your welding machine. Adjust voltage and wire feed speed according to the material thickness. MillerWelds offers comprehensive guides on equipment settings.
Body Positioning: Maintain a comfortable stance that allows for steady hand movement. Keep the welding gun at a 10 to 15-degree angle in the direction of the weld. Lincoln Electric provides insights on ergonomic welding positions.
Welding Speed and Angle: Move at a consistent speed that matches the rate of weld metal deposition. Adjust travel speed to avoid weld defects. The angle of the torch can significantly affect penetration and bead shape. Hobart Institute of Welding Technology offers detailed tutorials on speed and angle adjustments.
Bead Consistency: Practice laying beads of consistent size, shape, and penetration. Consistency comes from maintaining uniform speed and gun angle. American Welding Society provides guidelines on achieving consistent bead quality.
Practice and Feedback: Continuous practice on scrap metal and seeking feedback from experienced welders can lead to significant improvements. Online forums like WeldingWeb offer a platform for sharing work and receiving constructive criticism.
By concentrating on these areas and leveraging resources from reputable welding authorities, structural welders can enhance their GMAW technique effectively.
How to Display GMAW Technique Skills on Your Resume
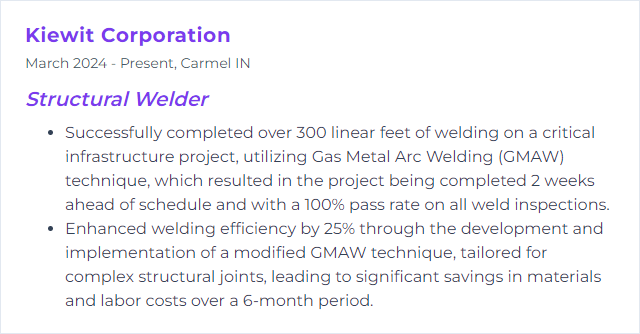
10. FCAW Technique
FCAW (Flux-Cored Arc Welding) is a semi-automatic or automatic arc welding process used by structural welders. It involves using a continuously-fed consumable tubular electrode filled with a flux to create the weld. This method provides high welding speed and portability, making it suitable for construction and repair of steel structures.
Why It's Important
The FCAW (Flux-Cored Arc Welding) technique is important for a structural welder because it offers high welding speed and efficiency, excellent penetration, and is versatile for welding in all positions, making it ideal for robust and complex structural applications.
How to Improve FCAW Technique Skills
Improving your Flux-Cored Arc Welding (FCAW) technique as a structural welder involves focusing on several key aspects. Here's a short and concise guide:
Equipment Setup: Ensure your welding machine is correctly set up for FCAW, including polarity, voltage, and wire feed speed. Lincoln Electric provides a comprehensive guide on settings.
Proper Technique: Maintain a steady travel speed and angle. Keep the wire stick-out consistent, generally around 3/4 inch. MillerWelds offers insights on mastering your technique.
Cleaning and Preparation: Clean the workpiece thoroughly before welding to reduce contamination. Proper joint preparation is crucial. WeldingTipsAndTricks has practical tips on preparation.
Practice Different Positions: FCAW often requires welding in various positions. Practice vertical, overhead, and horizontal welding to improve your skills. Welding.com is a resource for learning about different welding positions.
Adjust Parameters Based on Feedback: Listen to the sound of the weld and watch the bead formation. Adjust parameters as needed for optimal performance. American Welding Society (AWS) is a great resource for understanding welding parameters.
Safety First: Always follow safety guidelines to protect yourself from fumes, electric shock, and burns. OSHA’s welding, cutting, and brazing guidelines provide a comprehensive safety checklist.
Improving your FCAW technique is an ongoing process that requires practice, attention to detail, and a willingness to learn and adapt.
How to Display FCAW Technique Skills on Your Resume
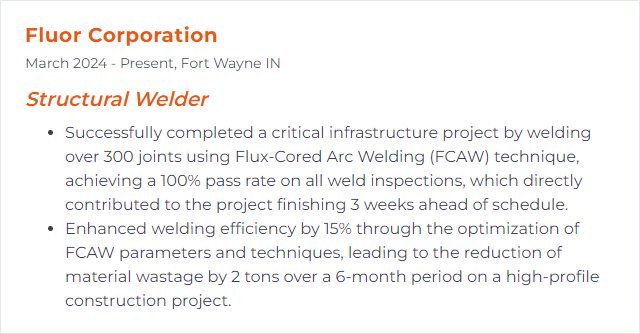
11. Oxy-Fuel Cutting
Oxy-fuel cutting is a process used by structural welders to cut through metals by utilizing a torch to heat the metal to its ignition temperature and then applying a stream of oxygen to oxidize and blow away the molten material, creating a cut.
Why It's Important
Oxy-fuel cutting is crucial for a structural welder because it provides a precise, efficient method for cutting and shaping steel components, essential for constructing strong and accurate structural frameworks.
How to Improve Oxy-Fuel Cutting Skills
To enhance Oxy-Fuel Cutting performance as a Structural Welder, focus on:
Proper Equipment Setup: Ensure the correct selection of nozzle size and gas pressures for your specific cutting task. Harris Products Group provides a comprehensive guide on equipment selection.
Optimal Gas Mixture: Use the right oxygen and fuel gas mixture (acetylene, propane, or others) for efficient cutting. The Lincoln Electric guide elaborates on gas mixtures and their applications.
Correct Cutting Speed: Adjust your cutting speed to avoid low-quality cuts. Too fast or too slow speeds can affect the cut quality. MillerWelds offers insights into adjusting cutting speed for optimal results.
Maintain Equipment: Regularly clean and maintain your cutting torch, nozzle, and hoses to prevent obstructions and ensure safety. ESAB provides maintenance tips for oxy-fuel equipment.
Safety Protocols: Always adhere to safety guidelines to prevent accidents. American Welding Society (AWS) outlines safety standards for welding and cutting.
Focusing on these areas will lead to improved efficiency, quality, and safety in oxy-fuel cutting operations.
How to Display Oxy-Fuel Cutting Skills on Your Resume
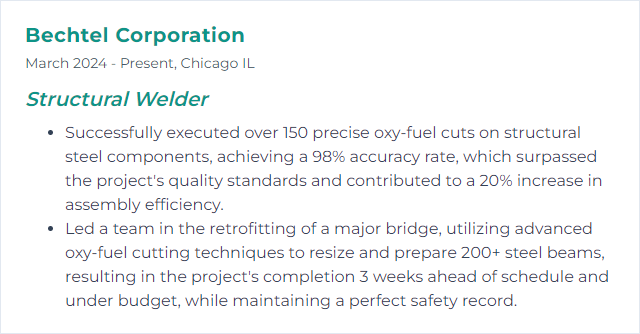
12. Plasma Cutting
Plasma cutting is a process used by structural welders to precisely cut through metal materials by using a plasma torch. The tool ionizes gas at high temperatures to create plasma, which then melts the metal, allowing for clean and swift cutting of steel and other conductive metals.
Why It's Important
Plasma cutting is important for a structural welder because it offers a quick and precise method to cut through various types of metals, including thick and thin plates, enabling efficient preparation of materials for welding and facilitating intricate cutting tasks in structural projects.
How to Improve Plasma Cutting Skills
Improving plasma cutting for a structural welder involves optimizing setup, maintenance, and cutting techniques to enhance precision and efficiency. Below are concise tips:
Choose the Right Consumables: Match consumables to the material type and thickness for optimal performance. Hypertherm's Guide provides detailed information on selecting the right consumables.
Proper Machine Setup: Ensure correct air pressure and electrical settings as per manufacturer's recommendations. Lincoln Electric's Setup Guide offers insights into machine setup.
Maintain a Consistent Speed: Move the torch at a uniform speed to avoid uneven cuts. MillerWelds' Technique Tips provide advice on maintaining the right speed.
Use a Guide or Template: For straight cuts or specific shapes, utilizing a guide or template can significantly enhance precision. Eastwood's Cutting Guide demonstrates how to use guides for better accuracy.
Regular Maintenance: Clean and inspect your equipment regularly to prevent performance issues. ESAB's Maintenance Checklist outlines key maintenance tasks.
By focusing on these aspects, a structural welder can significantly improve their plasma cutting quality and efficiency.
How to Display Plasma Cutting Skills on Your Resume
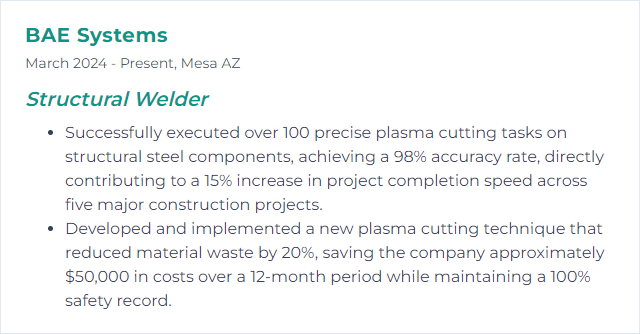