Top 12 Rig Welder Skills to Put on Your Resume
In the competitive field of rig welding, showcasing a robust set of skills on your resume can be the key to standing out among other applicants and securing your desired position. This article highlights the top 12 rig welder skills that are essential to highlight on your resume, catering to the demands of employers looking for proficient and versatile welders in today’s industry.
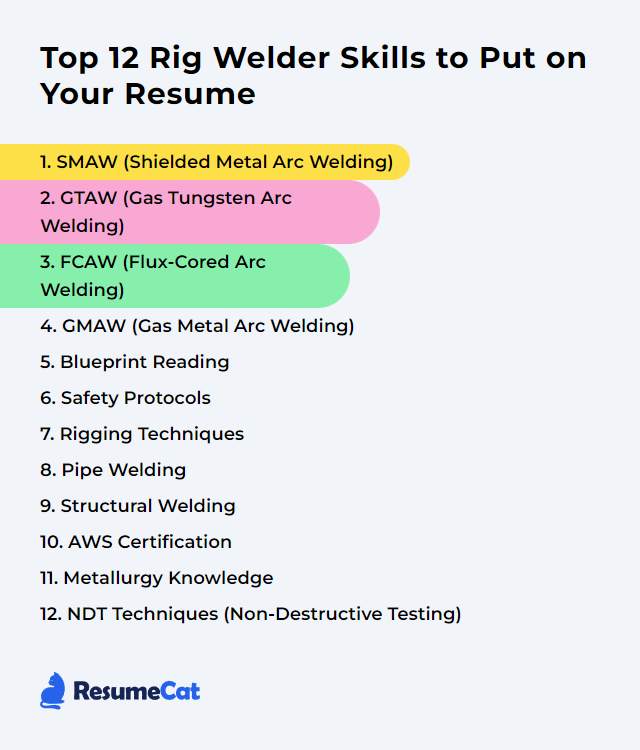
Rig Welder Skills
- SMAW (Shielded Metal Arc Welding)
- GTAW (Gas Tungsten Arc Welding)
- FCAW (Flux-Cored Arc Welding)
- GMAW (Gas Metal Arc Welding)
- Blueprint Reading
- Safety Protocols
- Rigging Techniques
- Pipe Welding
- Structural Welding
- AWS Certification
- Metallurgy Knowledge
- NDT Techniques (Non-Destructive Testing)
1. SMAW (Shielded Metal Arc Welding)
SMAW, or Shielded Metal Arc Welding, is a manual welding process that uses a consumable electrode coated in flux to lay the weld. It's commonly used by rig welders for its versatility in welding various types and thicknesses of metals in construction and repair work, often in challenging outdoor environments.
Why It's Important
SMAW is crucial for a rig welder because it offers versatility and efficiency in repairing or fabricating on diverse metals in challenging outdoor environments, ensuring structural integrity and safety in critical infrastructure.
How to Improve SMAW (Shielded Metal Arc Welding) Skills
Improving SMAW skills, especially for a Rig Welder, involves practice, understanding the nuances of the technique, and adapting to various working conditions. Here are concise tips for enhancement:
Equipment Familiarity: Know your welding machine settings and capabilities. Adjust amperage based on electrode size and material thickness. Miller Welds offers a comprehensive guide on settings and adjustments.
Electrode Choice: Select the right electrode for the job based on material type and welding position. For a guide on electrode selection, see Lincoln Electric.
Cleanliness: Ensure the welding surface is clean and free of contaminants to prevent defects. The American Welding Society emphasizes the importance of surface preparation.
Practice Different Positions: Rig welding often requires welding in challenging positions. Practice in all positions (flat, horizontal, vertical, overhead) to improve skill and adaptability. Welding Tips and Tricks provides tips on mastering these positions.
Control Arc Length: Keep a consistent, short arc length to prevent spatter and ensure strong welds. This Hobart Brothers resource offers insight into arc control, applicable to SMAW.
Travel Speed and Angle: Maintain a steady travel speed and appropriate angle to avoid weld defects. For angle and speed techniques, refer to The Fabricator.
Heat Management: Manage heat input to prevent warping and maintain weld integrity. This ESAB article provides strategies for heat control.
Continuous Learning: Stay updated with new techniques, materials, and safety standards. The American Welding Society offers resources for ongoing education.
By focusing on these areas, a Rig Welder can significantly improve their SMAW skills, leading to better quality welds and increased job opportunities.
How to Display SMAW (Shielded Metal Arc Welding) Skills on Your Resume
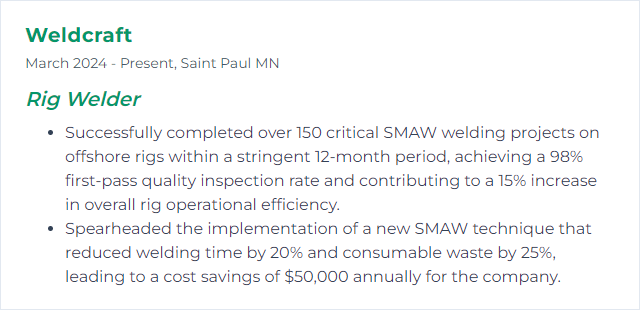
2. GTAW (Gas Tungsten Arc Welding)
GTAW, or Gas Tungsten Arc Welding, is a precision welding process where a non-consumable tungsten electrode is used to produce the weld, with an inert gas like argon shielding the weld area from contamination. It's particularly valued by rig welders for its ability to produce high-quality, clean welds on a variety of metals without requiring filler material, though filler can be used if needed.
Why It's Important
GTAW (Gas Tungsten Arc Welding) is important for a Rig Welder due to its ability to produce high-quality, precise welds on a variety of metals, including thin materials and alloys, with minimal spatter and clean results, essential for the demanding environments and safety requirements of rig construction and maintenance.
How to Improve GTAW (Gas Tungsten Arc Welding) Skills
Improving GTAW (Gas Tungsten Arc Welding) for a Rig Welder involves focusing on technique, equipment setup, and material preparation. Here's a concise guide:
Equipment Check: Regularly inspect your welding equipment, including the torch, cables, and gas supply. Ensure optimal performance by maintaining clean and undamaged components. MillerWelds offers detailed insights on equipment maintenance.
Material Preparation: Clean the base material and filler rod to remove any contaminants. Proper cleaning improves weld quality significantly. Lincoln Electric provides thorough guidance on material prep.
Proper Shielding Gas: Use the correct type and mixture of shielding gas, which can vary depending on the material. Argon is commonly used, but mixtures can reduce spatter and improve arc stability. Consult Airgas for specifics on shielding gases.
Welding Technique: Practice and refine your technique, focusing on steady torch movement, arc length, and angle. Consistency is key to high-quality welds. American Welding Society offers technique improvement tips.
Parameter Settings: Optimize your welding machine settings, including amperage, voltage, and travel speed, based on the material and thickness. Welding Tips and Tricks has useful advice on setting adjustments.
PPE and Safety: Always use proper personal protective equipment and follow safety guidelines to prevent accidents and health hazards. OSHA outlines safety practices for welding.
By concentrating on these areas, a Rig Welder can achieve significant improvements in GTAW quality and efficiency.
How to Display GTAW (Gas Tungsten Arc Welding) Skills on Your Resume
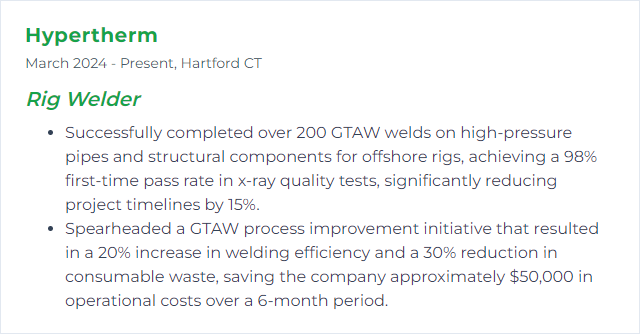
3. FCAW (Flux-Cored Arc Welding)
FCAW (Flux-Cored Arc Welding) is a semi-automatic or automatic arc welding process used by rig welders, utilizing a consumable tubular electrode filled with flux to produce the weld, offering high welding speed and penetration with minimal cleanup.
Why It's Important
FCAW (Flux-Cored Arc Welding) is important for a Rig Welder because it offers high welding speed, excellent penetration, and is versatile, suitable for welding in all positions. This method enhances productivity and quality, even in challenging outdoor or windy conditions, making it ideal for rig construction and maintenance tasks.
How to Improve FCAW (Flux-Cored Arc Welding) Skills
Improving FCAW (Flux-Cored Arc Welding) involves several steps focusing on technique, equipment maintenance, and material preparation. Here's a concise guide:
Choose the Right Wire: Select the appropriate wire type (gas-shielded or self-shielded) and diameter based on the welding position and metal thickness. Lincoln Electric provides detailed guidance on wire selection.
Proper Machine Setup: Ensure the welding machine settings (voltage, amperage, and wire feed speed) are optimized for the job. Consult the wire's specification sheet for initial settings. MillerWelds offers advice on parameter adjustments.
Maintain Good Contact Tip Condition: Regularly inspect and replace the contact tip to prevent arc instability and poor wire feeding. Tips on maintenance can be found in ESAB’s maintenance checklist.
Use the Correct Stick-Out Length: Stick-out length can influence deposition rate and bead shape. Adjust according to the wire manufacturer's recommendations.
Control Travel Speed and Angle: Maintain a consistent travel speed and angle to ensure even heat distribution and penetration. Welding Tips and Tricks offers practical advice on travel speed and technique.
Prevent Porosity: Clean the base metal thoroughly to remove any contaminants. Adjust shielding gas flow rate if using gas-shielded FCAW to prevent porosity caused by air entrapment.
Practice and Experiment: Practice different techniques and settings on scrap metal to find what works best for your specific applications.
By adhering to these guidelines and continuously seeking ways to refine your technique, you can significantly improve your FCAW results. Remember, the key to mastering FCAW, like any welding process, lies in understanding the nuances of your equipment, materials, and the welding environment.
How to Display FCAW (Flux-Cored Arc Welding) Skills on Your Resume
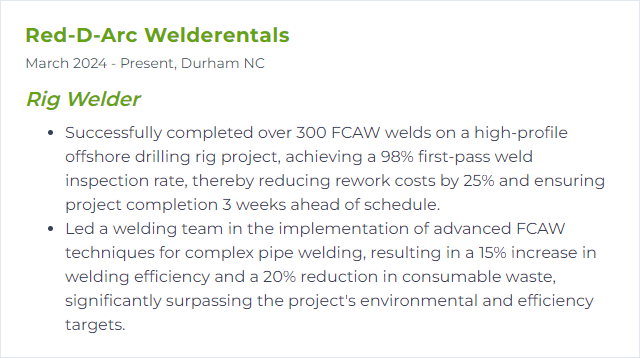
4. GMAW (Gas Metal Arc Welding)
GMAW (Gas Metal Arc Welding) is a welding process where an electric arc forms between a consumable wire electrode and the workpiece metal(s), heating the workpiece metal(s) and causing them to melt and join. For a rig welder, it involves using a shielding gas along the wire electrode, which helps protect the weld pool from atmospheric contamination.
Why It's Important
GMAW (Gas Metal Arc Welding) is important for a rig welder due to its efficiency, versatility in welding various metals, and ability to produce clean, high-quality welds with minimal cleanup, significantly enhancing productivity and safety on demanding job sites.
How to Improve GMAW (Gas Metal Arc Welding) Skills
Improving GMAW (Gas Metal Arc Welding) involves focusing on technique, equipment maintenance, and parameter optimization. Here are concise tips for a Rig Welder aiming to enhance GMAW performance:
Select the Correct Wire and Gas: Choose the appropriate wire diameter and type for your material. Use a shielding gas that suits your application, often a mix of Argon and CO2 for steel (MillerWelds Guide).
Optimize Welding Parameters: Adjust voltage, wire feed speed, and amperage based on material thickness and welding position for optimal penetration and bead appearance (Lincoln Electric Parameter Guide).
Maintain a Consistent Work Angle: Keep the welding gun at a 10 to 15-degree angle to the direction of welding for better penetration and a cleaner weld pool (Hobart Institute of Welding Technology Tips).
Control Stick-Out Length: Maintain a short stick-out length (1/4" to 3/8") to prevent excess spatter and ensure stable arc control.
Regular Equipment Maintenance: Regularly clean and inspect your welding gun, replace consumables before they are completely worn out, and ensure your gas flow rate is correctly set (20-25 cubic feet per hour is typical) to prevent porosity (ESAB Welding & Cutting).
Practice and Review: Continuously practice different welds and review your work, focusing on controlling speed and gun movement to ensure consistent bead quality.
By implementing these strategies, a Rig Welder can significantly improve their GMAW process, leading to stronger, higher-quality welds.
How to Display GMAW (Gas Metal Arc Welding) Skills on Your Resume
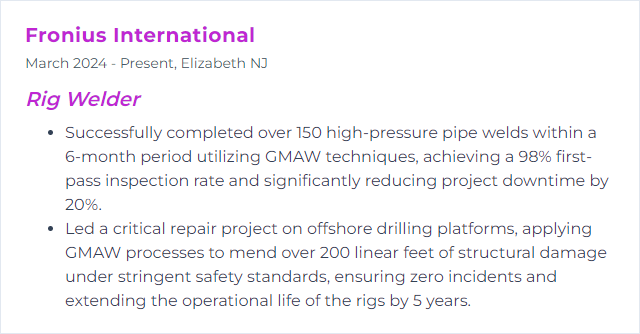
5. Blueprint Reading
Blueprint reading for a rig welder involves interpreting and understanding detailed drawings and diagrams that outline the specifications, dimensions, and construction procedures for welding projects on rigs, ensuring accurate and safe fabrication, assembly, and repair of structures or components.
Why It's Important
Blueprint reading is crucial for a Rig Welder as it enables accurate interpretation of technical drawings and specifications for constructing or repairing structures, ensuring precision, safety, and adherence to design requirements.
How to Improve Blueprint Reading Skills
Improving blueprint reading skills as a Rig Welder involves enhancing your ability to understand and interpret the various symbols, dimensions, and notations used in welding blueprints. Here's a very short and concise guide to get you started:
Familiarize with Symbols: Start with learning the basic welding symbols and their meanings. The American Welding Society (AWS) offers resources and standards that are crucial for understanding welding symbols.
Understand Dimensions and Tolerances: Grasp how dimensions and tolerances are represented in blueprints to ensure accurate construction and fitting.
Learn Orthographic Projections: Understand how different views of an object are represented in blueprints (top, front, side) to get a comprehensive 3D understanding from 2D drawings.
Study Welding Codes: Get familiar with relevant welding codes and standards. These dictate the specifications for the types of welds required, materials, and testing procedures.
Practice Regularly: The best way to improve is by practice. Regularly interpreting blueprints and applying your knowledge on the job will enhance your skills over time.
Take a Course: Consider enrolling in a course specifically designed for blueprint reading in welding. Websites like Udemy or Coursera offer courses that might cater to your needs.
Join Forums and Groups: Engage with communities on platforms like Reddit or specialized forums. Sharing knowledge and asking questions in such communities can offer practical insights and tips.
Remember, improving your blueprint reading skills is a continuous process that will enhance your efficiency and accuracy as a Rig Welder.
How to Display Blueprint Reading Skills on Your Resume
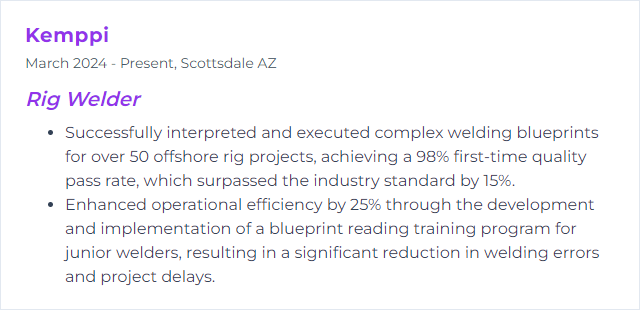
6. Safety Protocols
Safety protocols for a rig welder encompass a set of guidelines and procedures designed to prevent accidents and injuries during welding operations on rigs. These include wearing appropriate personal protective equipment (PPE), following proper welding techniques, ensuring good ventilation, and adhering to specific safety standards for handling welding equipment and materials.
Why It's Important
Safety protocols are crucial for rig welders to prevent accidents, minimize exposure to hazardous materials, ensure proper equipment handling, and protect against fires and explosions, thereby safeguarding the welder's health and ensuring operational continuity.
How to Improve Safety Protocols Skills
Improving safety protocols for a rig welder involves a multi-faceted approach focusing on training, equipment maintenance, and environmental assessment. Here’s a concise guide:
Enhanced Training: Ensure rig welders undergo comprehensive safety training including the latest OSHA guidelines. This should cover not just welding techniques but also emergency response, hazard recognition, and the use of personal protective equipment (PPE).
Regular Equipment Checks: Implement a strict schedule for inspecting and maintaining welding equipment and PPE. This helps identify potential hazards like gas leaks or malfunctioning welding guns before they cause accidents.
Environmental Assessments: Conduct regular safety audits of the work area to identify and mitigate potential hazards such as flammable materials, inadequate ventilation, or unstable structures.
Emergency Preparedness: Develop and regularly update an emergency response plan specific to welding incidents, ensuring all workers are familiar with it. Include procedures for fire, medical emergencies, and hazardous material exposure.
Continuous Learning and Feedback: Foster an environment where workers are encouraged to report unsafe conditions and suggest improvements. Implement a system for reviewing and updating safety protocols based on feedback and new industry standards.
By focusing on these areas, you can build a robust safety culture that minimizes risks for rig welders.
How to Display Safety Protocols Skills on Your Resume
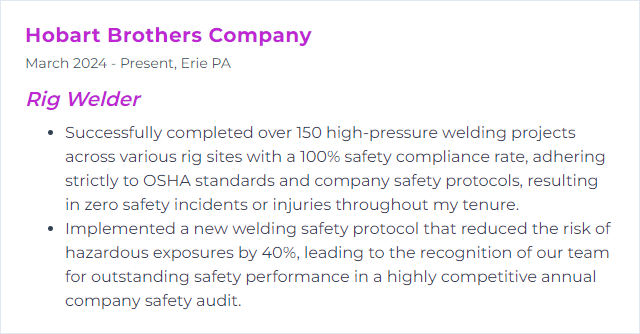
7. Rigging Techniques
Rigging techniques, in the context of a rig welder, refer to the methods and practices used to safely and efficiently assemble, position, and secure welding equipment and materials at a job site. This involves the use of cranes, hoists, slings, and other gear to lift and move heavy components into place for welding, ensuring stability and worker safety throughout the process.
Why It's Important
Rigging techniques are essential for a Rig Welder because they ensure the safe and efficient positioning and securing of materials and equipment needed for welding tasks, especially in challenging environments. This proficiency minimizes the risk of accidents, enhances workplace safety, and improves job quality and productivity.
How to Improve Rigging Techniques Skills
Improving rigging techniques, especially for a Rig Welder, involves understanding best practices, safety procedures, and continuously updating skills with the latest technology and methods. Here are concise tips:
Safety First: Always prioritize safety by adhering to OSHA rigging safety guidelines. Understanding and implementing these can prevent accidents.
Continuous Learning: Stay updated with the latest rigging techniques and equipment. Online platforms like Lincoln Electric offer resources and courses.
Proper Equipment Use: Ensure you're using the right tools for the job. Manufacturer guides, like those from Miller Welds, provide invaluable information on equipment usage and maintenance.
Practice Precision: Work on precise measurements and cuts. Resources like American Welding Society offer standards and guidelines to improve accuracy.
Efficiency in Setup: Streamline your setup and breakdown processes. Efficient organization can significantly reduce time and increase productivity.
Peer Learning: Engage with community forums and platforms (WeldingWeb) to exchange tips, experiences, and advice with fellow rig welders.
Certification and Training: Regularly update your certifications and seek advanced training. Institutions like the Hobart Institute of Welding Technology offer advanced courses.
By focusing on these areas, you can enhance your rigging techniques, ensuring higher quality, efficiency, and safety in your welding projects.
How to Display Rigging Techniques Skills on Your Resume
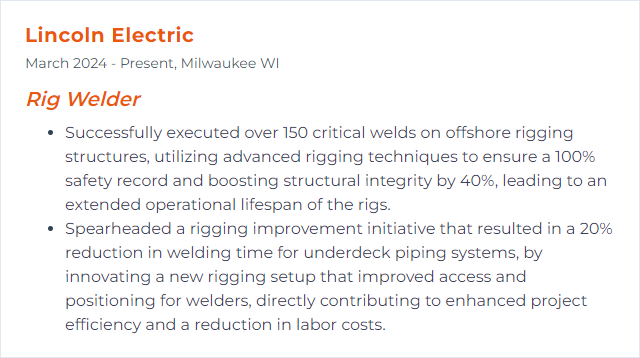
8. Pipe Welding
Pipe welding, in the context of a rig welder, involves joining metal pipes together using heat and filler material to ensure the structural integrity and safety of pipelines, often within oil, gas, or construction rigs. It requires specialized skills to handle varying pipe materials, thicknesses, and environments.
Why It's Important
Pipe welding is crucial for rig welders as it ensures the integrity and safety of pipelines that transport essential materials like oil, gas, and water under high pressure, directly impacting the rig's operational efficiency and environmental safety.
How to Improve Pipe Welding Skills
Improving pipe welding, especially for rig welders, involves focusing on technique, equipment, and ongoing learning. Here are concise strategies:
Practice Consistently: Regular practice on different pipe positions (1G through 6G) enhances skill and confidence. Miller Welds offers projects and tips.
Use the Right Equipment: Invest in high-quality welding machines and accessories. Proper tools, like auto-darkening helmets, can improve weld quality. Check Lincoln Electric for equipment options.
Prep Thoroughly: Ensure pipe ends are properly beveled and cleaned. A good preparation leads to better welds. Hobart Institute of Welding Technology provides insights on preparation techniques.
Control Heat Input: Mastering heat control prevents warping and ensures penetration. This is crucial in achieving strong, durable welds in pipe welding.
Welding Techniques: Familiarize with different welding techniques (e.g., TIG, MIG, Stick) and when to use them. American Welding Society is a great resource for learning about various techniques.
Safety Practices: Always adhere to safety protocols to prevent accidents. Proper ventilation and wearing the right PPE are essential.
Continuous Learning: Stay updated with new technologies and methodologies in welding through online courses and certifications. Welding Tips and Tricks is a helpful site for learning new techniques and tips.
By focusing on these areas, rig welders can significantly improve their pipe welding skills, leading to higher-quality welds and increased job opportunities.
How to Display Pipe Welding Skills on Your Resume
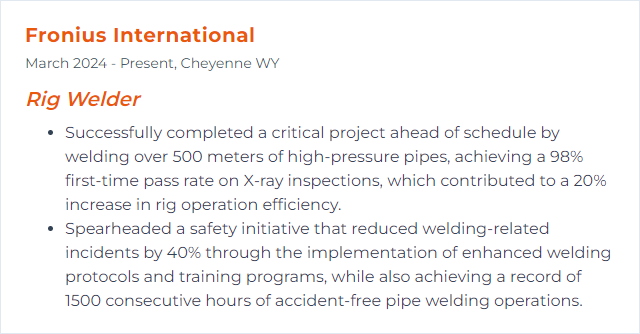
9. Structural Welding
Structural welding, in the context of a rig welder, involves joining metal components to form the frameworks or supports in structures such as buildings, bridges, or oil rigs. It requires precise skill to ensure durability, strength, and safety of the structures.
Why It's Important
Structural welding is crucial for a Rig Welder because it ensures the integrity, strength, and safety of the rig's framework and components, which are essential for the rig's performance and the prevention of catastrophic failures in demanding operational environments.
How to Improve Structural Welding Skills
Improving structural welding, especially for a rig welder, involves enhancing skills, ensuring safety, and using proper equipment. Here are concise strategies:
Upgrade Skills: Regularly attend welding certification courses and workshops to stay updated with the latest welding techniques and standards.
Follow Safety Protocols: Always adhere to OSHA welding safety guidelines to prevent accidents and ensure a safe working environment.
Use Quality Equipment: Invest in high-quality welding gear and materials. Ensure your welding machine is suitable for the job and regularly maintained. For equipment, check Lincoln Electric or Miller Electric.
Pre-Welding Preparation: Properly clean and prepare the materials before welding. This includes removing rust, paint, or any contaminants that can affect weld quality.
Welding Technique Improvement: Practice different welding positions and techniques to become more versatile. Focus on mastering both speed and accuracy.
Post-Welding Inspection and Testing: Learn about non-destructive testing (NDT) methods to inspect your welds without damaging the components.
Peer Review and Feedback: Collaborate with experienced welders or join welding forums like WeldingWeb to gain insights and advice on improving your work.
By focusing on these areas, you can significantly improve your structural welding skills and outcomes as a rig welder.
How to Display Structural Welding Skills on Your Resume
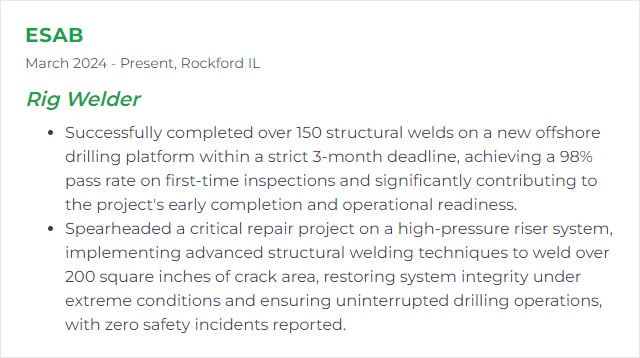
10. AWS Certification
AWS Certification for a Rig Welder typically refers to qualifications from the American Welding Society, which certify an individual's skills and knowledge in welding practices, safety standards, and techniques relevant to rig welding operations. It is not related to Amazon Web Services (AWS).
Why It's Important
AWS Certification for a Rig Welder is important because it validates the welder's skills and knowledge in accordance with industry standards, ensuring high-quality workmanship and safety on job sites.
How to Improve AWS Certification Skills
Improving your AWS Certification, especially as a Rig Welder, involves a combination of practical experience, targeted study, and understanding the certification process. Here are concise steps to enhance your AWS Certification:
Understand the Requirements: Familiarize yourself with the AWS certification process and requirements for welders by visiting the American Welding Society (AWS) website.
Gain Practical Experience: More hands-on experience in rig welding will improve your skills and understanding, essential for certification.
Study AWS Welding Codes: Study the relevant AWS welding codes and standards, which are crucial for certification. AWS provides resources and manuals, which can be found here.
Take AWS-Approved Courses: Enroll in AWS-approved courses or workshops that focus on rig welding techniques and standards. Check the AWS Learning section for Certification Preparation.
Practice Exams: Use AWS practice exams to familiarize yourself with the certification test format and identify areas for improvement. AWS offers some practice materials here.
Seek Mentorship: Connect with certified AWS welders or mentors who can provide insights, tips, and support through platforms like LinkedIn or local welding communities.
Apply for Certification: Once prepared, apply for your AWS Certification examination through the AWS website, ensuring you meet all prerequisites and have gathered any necessary documentation.
By following these steps and utilizing the resources provided, you can significantly improve your AWS Certification as a Rig Welder.
How to Display AWS Certification Skills on Your Resume

11. Metallurgy Knowledge
Metallurgy Knowledge for a Rig Welder involves understanding the properties, behaviors, and treatment of metals and alloys used in welding processes, including how heat affects metal, the selection of appropriate welding materials and methods for joining specific metal types, and techniques for preventing or repairing defects such as cracks or porosity to ensure strong, durable welds.
Why It's Important
Metallurgy knowledge is crucial for a Rig Welder to select appropriate materials and welding techniques, ensuring structural integrity, safety, and longevity of welded components under various operational stresses and environmental conditions.
How to Improve Metallurgy Knowledge Skills
Improving your metallurgy knowledge as a rig welder involves understanding the properties of metals, welding techniques, and how materials react under different conditions. Here's a concise guide:
Online Courses: Platforms like Coursera and edX offer courses in materials science and metallurgy basics tailored for various skill levels.
YouTube Tutorials: Channels such as WeldingTipsAndTricks provide practical welding advice, including metallurgy for welders.
Reading Materials: Books like "Metallurgy Fundamentals" by Daniel A. Brandt and J.C. Warner offer a solid introduction. Websites like ASM International publish articles and resources on the latest in materials science.
Professional Associations: Join organizations like the American Welding Society (AWS) for access to workshops, certifications, and networking with professionals in the field.
Hands-On Practice: Apply what you learn in real-world scenarios. Experiment with different metals and welding techniques to understand their properties and reactions.
By blending theoretical knowledge with practical experience, you'll significantly improve your understanding of metallurgy relevant to your work as a rig welder.
How to Display Metallurgy Knowledge Skills on Your Resume
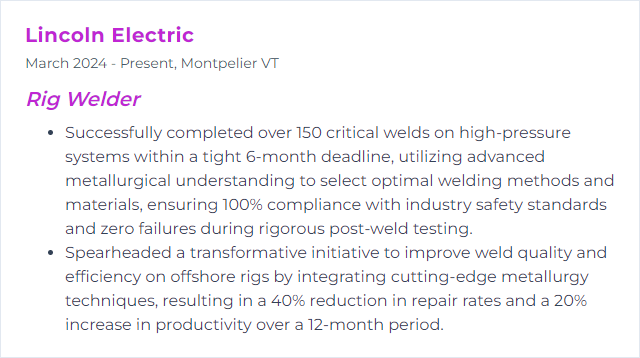
12. NDT Techniques (Non-Destructive Testing)
Non-Destructive Testing (NDT) techniques are methods used to inspect and evaluate materials, components, or assemblies for discontinuities, or differences in characteristics without causing damage to the original part. For a Rig Welder, NDT is crucial for ensuring the integrity, safety, and reliability of welds on drilling rigs without compromising the material's usability. Common NDT methods include Visual Inspection, Ultrasonic Testing, Magnetic Particle Testing, and Radiographic Testing.
Why It's Important
NDT techniques are crucial for rig welders because they enable the detection of defects or inconsistencies in welded joints without damaging the components being tested. This ensures the structural integrity and safety of the welding work on rigs, where failures can have severe consequences.
How to Improve NDT Techniques (Non-Destructive Testing) Skills
Improving Non-Destructive Testing (NDT) techniques, especially for a Rig Welder, involves adopting advanced technologies, enhancing operator skills, and implementing best practices in inspection processes. Here are concise strategies to achieve these improvements:
Incorporate Advanced Technologies: Utilize the latest NDT technologies such as Phased Array Ultrasonic Testing (PAUT) (ASNT) and Digital Radiography (DR) (NDT Global). These methods offer clearer images, better defect detection, and more detailed analysis.
Operator Training and Certification: Ensure rig welders and inspectors are well-trained and certified in the NDT methods being used. Certifications from recognized bodies like the American Society for Nondestructive Testing (ASNT) (ASNT Certification) can enhance the skill set and credibility of NDT personnel.
Adopt Best Practices in NDT: Implement industry best practices for NDT inspections, including proper planning of inspection intervals, calibration of equipment, and adherence to international standards like those from the American Welding Society (AWS) (AWS Standards).
Regular Calibration and Maintenance of NDT Equipment: Ensure all NDT equipment is regularly calibrated and maintained according to the manufacturer's recommendations to guarantee accurate readings and reliable performance.
Peer Review and Continuous Learning: Encourage a culture of peer review and continuous learning among NDT technicians. Sharing insights, challenges, and solutions can lead to improvements in NDT techniques and outcomes. Online forums and professional networks (LinkedIn Groups for NDT Professionals) can be valuable resources.
By following these strategies, rig welders and their teams can significantly enhance the effectiveness and reliability of NDT techniques used in their operations.
How to Display NDT Techniques (Non-Destructive Testing) Skills on Your Resume
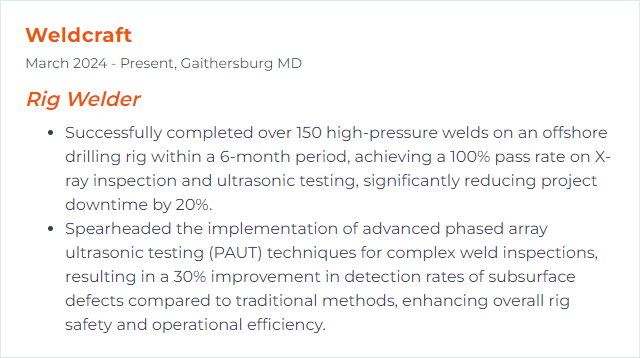