Top 12 Wafer Fab Operator Skills to Put on Your Resume
In today's competitive semiconductor industry, standing out as a wafer fab operator requires showcasing a blend of technical prowess and soft skills on your resume. Highlighting the top skills in your application not only demonstrates your expertise and readiness for the role but also positions you as a prime candidate in the eyes of potential employers.
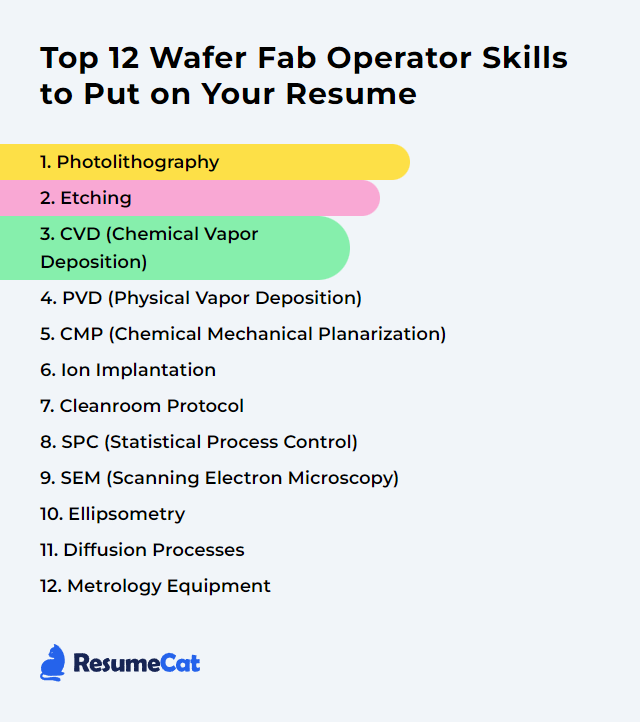
Wafer Fab Operator Skills
- Photolithography
- Etching
- CVD (Chemical Vapor Deposition)
- PVD (Physical Vapor Deposition)
- CMP (Chemical Mechanical Planarization)
- Ion Implantation
- Cleanroom Protocol
- SPC (Statistical Process Control)
- SEM (Scanning Electron Microscopy)
- Ellipsometry
- Diffusion Processes
- Metrology Equipment
1. Photolithography
Photolithography is a process used in wafer fabrication to transfer geometric shapes on a mask to the surface of a silicon wafer. It involves applying a light-sensitive material (photoresist) to the wafer, exposing it to ultraviolet light through a patterned mask, and developing the image to create a physical pattern on the wafer for subsequent processing steps.
Why It's Important
Photolithography is crucial in wafer fabrication because it precisely patterns microscopic circuits on semiconductor wafers, enabling the mass production of complex electronic devices with high performance and reliability.
How to Improve Photolithography Skills
To improve photolithography in a wafer fabrication setting, focus on optimizing the following key areas:
Resolution Enhancement: Employ advanced photomasks and resolution enhancement techniques (RETs), such as optical proximity correction (OPC) and phase shift masks, to improve pattern fidelity and resolution.
Photoresist Selection and Processing: Choose photoresists with optimal characteristics for your application (e.g., sensitivity, contrast, resolution). Optimize coating, baking, and development processes to reduce defects and improve uniformity.
Exposure Optimization: Use immersion lithography to increase numerical aperture and resolution. Explore multiple patterning techniques for critical layers to bypass the optical resolution limit.
Equipment Maintenance and Calibration: Regularly maintain and calibrate lithography equipment to ensure optimal performance, focusing on the alignment and exposure systems to minimize errors and improve overlay accuracy.
Cleanroom Environment Control: Strictly manage the cleanroom environment to reduce particulate contamination on wafers, which can affect the photolithography process's outcome.
Process Monitoring and Optimization: Implement a robust process control and monitoring system to quickly identify and correct deviations in the photolithography process, enhancing yield and efficiency.
By focusing on these areas, a Wafer Fab Operator can significantly improve the photolithography process's outcomes, contributing to higher yields and better device performance.
How to Display Photolithography Skills on Your Resume
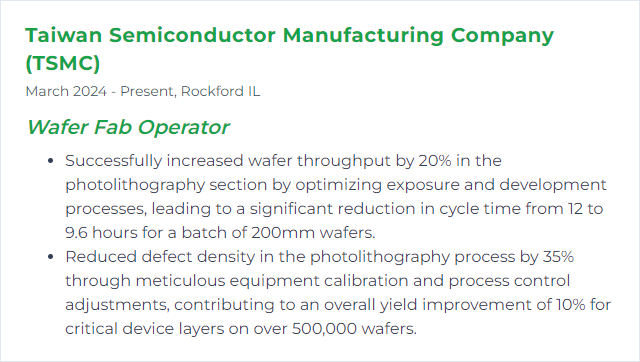
2. Etching
Etching in the context of a wafer fab operator involves using chemical or plasma-based processes to selectively remove layers from the surface of a silicon wafer, creating the desired patterns for electronic circuits.
Why It's Important
Etching is crucial in wafer fabrication because it precisely removes layers from the silicon wafer to create the intricate patterns needed for circuits, thereby defining the microstructures of semiconductor devices.
How to Improve Etching Skills
Improving etching in a wafer fabrication setting involves optimizing various parameters and processes to enhance efficiency, accuracy, and the quality of the etched patterns. Here are concise steps for a Wafer Fab Operator:
Optimize Etching Parameters: Adjust and fine-tune the etching parameters such as gas flow rates, pressure, power, and time to match the specific requirements of the material and design (Semiconductor Digest).
Regular Equipment Maintenance: Ensure etching equipment is regularly maintained and calibrated to prevent defects and ensure consistent performance (Semi Engineering).
Use High-Quality Masks: Employ high-resolution masks to achieve precise etching patterns, reducing the possibility of errors (SPIE).
Monitor and Control the Environment: Keep the etching environment (temperature, humidity) controlled and consistent to prevent variations in etching rates and outcomes (IEEE Xplore).
Implement Real-Time Inspection: Utilize real-time inspection techniques to identify and correct issues promptly, minimizing defects and improving yield (Nature Electronics).
Continuous Process Improvement: Adopt a continuous improvement approach, using etching results and feedback to refine and optimize the process over time (Journal of Micro/Nanolithography, MEMS, and MOEMS).
Employee Training: Ensure operators are well-trained in the latest etching techniques and technologies to maximize efficiency and quality (ASM International).
By focusing on these areas, a Wafer Fab Operator can significantly improve the etching process, leading to better product quality and higher operational efficiency.
How to Display Etching Skills on Your Resume

3. CVD (Chemical Vapor Deposition)
CVD (Chemical Vapor Deposition) is a semiconductor manufacturing process where a solid material is deposited on a substrate (wafer) through the reaction of vapor-phase chemicals. This technique is used to create high-quality, high-performance, thin films crucial in semiconductor device fabrication.
Why It's Important
CVD is crucial in wafer fabrication because it enables the precise deposition of thin films of materials on a substrate, essential for creating semiconductor devices with consistent and high-quality electrical properties.
How to Improve CVD (Chemical Vapor Deposition) Skills
Improving Chemical Vapor Deposition (CVD) in a wafer fabrication setting involves optimizing process parameters, ensuring equipment maintenance, and enhancing material quality. Here’s a concise guide:
Optimize Process Parameters: Fine-tuning temperature, pressure, gas flow rates, and chemical ratios can enhance film uniformity and deposition rates. Use real-time monitoring and control software for adjustments. SEMI provides standards and guidelines on optimal process conditions.
Equipment Maintenance: Regular maintenance and calibration of CVD equipment ensure consistent performance. Focus on cleaning deposition chambers and verifying the accuracy of measurement tools. Applied Materials offers maintenance insights for CVD systems.
Quality Control of Precursor Materials: Use high-purity precursor materials to reduce defects. Ensure materials are stored and handled to prevent contamination. The American Chemical Society publishes research on precursor materials and their impact on film quality.
Implement Advanced Techniques: Explore advanced CVD techniques like Plasma-enhanced CVD (PECVD) for better film properties at lower temperatures. IEEE Xplore provides access to research on advanced CVD techniques and their applications.
Continuous Training: Ensure operators are knowledgeable about the latest CVD technologies and best practices through ongoing training. SEMI offers courses and certifications relevant to wafer fabrication and CVD processes.
By focusing on these areas, wafer fab operators can significantly improve the efficiency and quality of the CVD process.
How to Display CVD (Chemical Vapor Deposition) Skills on Your Resume
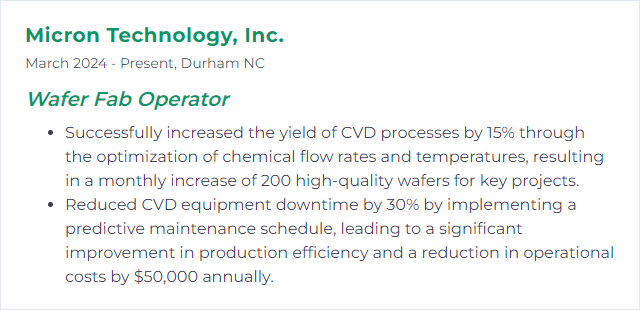
4. PVD (Physical Vapor Deposition)
PVD (Physical Vapor Deposition) is a coating process used in wafer fabrication to deposit thin films of material onto semiconductor wafers through the condensation of a vaporized form of the desired film material onto the wafer surface.
Why It's Important
PVD (Physical Vapor Deposition) is crucial in a wafer fab operation because it allows for the precise deposition of thin films of materials onto semiconductor wafers, enhancing the electrical, optical, and mechanical properties of the devices being manufactured. This process is key to producing high-performance, reliable semiconductor devices.
How to Improve PVD (Physical Vapor Deposition) Skills
Improving Physical Vapor Deposition (PVD) in a wafer fabrication setting involves optimizing several key aspects of the process to enhance coating uniformity, adhesion, and throughput. Here's a concise guide for a Wafer Fab Operator:
Process Optimization: Regularly review and adjust PVD parameters like deposition rate, substrate temperature, and chamber pressure to ensure optimal coating quality. ASM International provides resources on material properties and processing parameters.
Equipment Maintenance: Perform routine maintenance and calibration of PVD equipment to prevent defects and ensure consistent performance. SEMI offers standards and guidelines for equipment maintenance.
Substrate Preparation: Ensure substrates are properly cleaned and prepared to improve adhesion and reduce defects. The Surface Engineering Division of IOM3 provides insights on surface engineering and preparation techniques.
Material Purity: Use high-purity target materials to reduce contamination and improve film properties. Suppliers like Sigma-Aldrich offer high-purity materials.
Process Monitoring and Control: Implement real-time monitoring and control systems to adjust process parameters for consistent results. Resources like IEEE Xplore offer access to the latest research and developments in process control technologies.
Training and Development: Continuous learning and training on the latest PVD technologies and practices can lead to process improvements. SEMI provides industry-specific training courses.
By focusing on these areas, a Wafer Fab Operator can significantly contribute to the improvement of PVD processes within their facility.
How to Display PVD (Physical Vapor Deposition) Skills on Your Resume
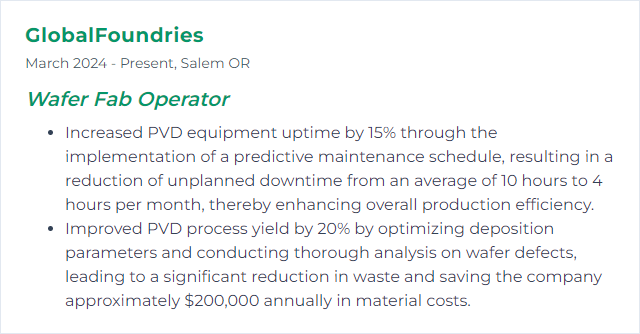
5. CMP (Chemical Mechanical Planarization)
CMP, or Chemical Mechanical Planarization, is a process used in semiconductor manufacturing to smooth and flatten the surface of silicon wafers using a combination of chemical slurry and mechanical polishing. It ensures layers are even for more layers to be built on top accurately.
Why It's Important
CMP (Chemical Mechanical Planarization) is crucial in wafer fabrication because it smoothens the wafer's surface, ensuring uniform thickness and removing defects. This process is vital for achieving the high precision and reliability required for advanced semiconductor devices.
How to Improve CMP (Chemical Mechanical Planarization) Skills
Improving Chemical Mechanical Planarization (CMP) in a wafer fabrication setting involves optimizing several key parameters and practices to enhance the planarity and surface quality of wafers. Here are concise strategies for a Wafer Fab Operator:
Pad Conditioning: Regularly condition the CMP pad to maintain its effectiveness and ensure consistent removal rates. (More on Pad Conditioning)
Slurry Optimization: Optimize the slurry composition and flow rate for the material being polished to achieve the desired removal rate and surface finish. (Slurry Optimization)
Downforce and Velocity Control: Precisely control the downforce and platen/carrier velocities to minimize defects and improve uniformity. (Downforce and Velocity)
Process Monitoring: Implement real-time monitoring and post-process inspection to quickly identify and correct process deviations. (Process Monitoring Technologies)
Regular Maintenance: Perform regular maintenance on CMP equipment to prevent unexpected downtime and maintain process stability. (Equipment Maintenance)
Training and SOPs: Ensure operators are well-trained and follow standardized operating procedures (SOPs) to maintain consistency across different shifts and operators. (Operator Training)
By focusing on these areas, a Wafer Fab Operator can significantly improve the outcomes of the CMP process, leading to better wafer quality and yield.
How to Display CMP (Chemical Mechanical Planarization) Skills on Your Resume
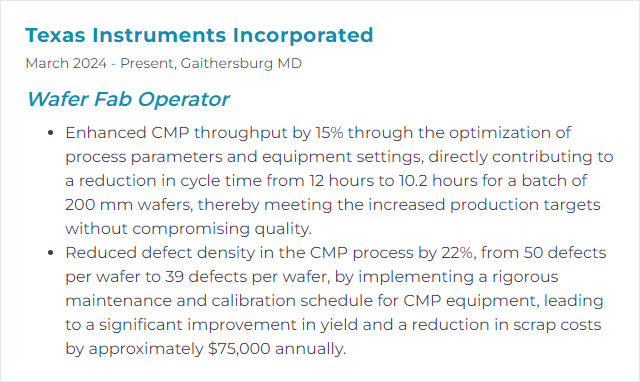
6. Ion Implantation
Ion implantation is a process used in semiconductor manufacturing where ions of a specific element are accelerated and implanted into the surface of a semiconductor wafer to alter its electrical properties, such as conductivity or dopant concentration. This process is crucial for creating various regions within a microchip with different electrical characteristics, essential for the functionality of electronic devices.
Why It's Important
Ion implantation is important in wafer fabrication because it precisely introduces dopants into semiconductor materials, controlling their electrical properties to create specific device structures essential for integrated circuits. This process is key to manufacturing high-performance, reliable electronic devices.
How to Improve Ion Implantation Skills
Improving ion implantation in a wafer fab setting involves optimizing several key factors to enhance uniformity, depth, and throughput while minimizing defects. Here are concise strategies tailored for a Wafer Fab Operator:
Optimize Dose and Energy: Adjusting the ion dose and energy levels can improve implant uniformity and junction depth. Use simulation tools like SRIM for precise adjustments.
Enhance Beam Control: Implement advanced beam scanning techniques and real-time monitoring to improve the ion beam's uniformity and minimize channeling effects. Resources like Ion Beam Services may offer insights into state-of-the-art beam control technologies.
Maintain Equipment: Regular maintenance and calibration of the implanter ensure consistent performance. Manufacturer guides and SEMI Standards provide comprehensive maintenance protocols.
Implement Cooling Techniques: Use wafer cooling technologies to manage thermal effects during implantation, which can affect dopant distribution and wafer integrity. Explore innovations in cooling methods through IEEE Xplore.
Utilize Advanced Masks: Employ precision masks for selective implantation, enhancing pattern fidelity. Detailed techniques can be found in specialized publications like Journal of Micro/Nanolithography, MEMS, and MOEMS.
Adopt Real-Time Monitoring: Utilize in-situ monitoring systems to adjust parameters on the fly for optimal implantation results. Systems and methodologies are detailed in semiconductor technology publications accessible through ScienceDirect.
Implementing these strategies requires a balance of technical knowledge, precision equipment handling, and continuous learning. Stay updated with the latest advancements and best practices in ion implantation technology by regularly consulting semiconductor processing forums and attending workshops or seminars offered by industry leaders.
How to Display Ion Implantation Skills on Your Resume
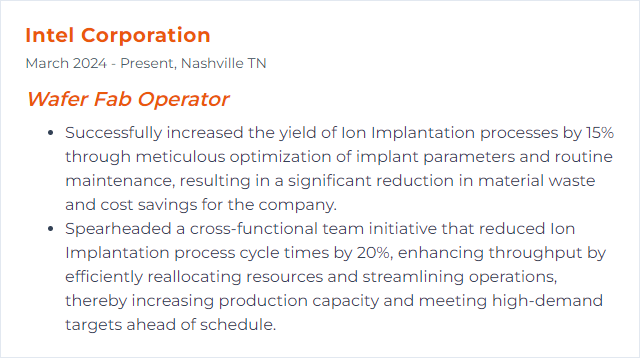
7. Cleanroom Protocol
Cleanroom Protocol for a Wafer Fab Operator involves strict procedures to minimize contamination in the fabrication environment, including wearing specialized garments, adhering to cleanliness standards, controlling airborne particles, and following specific processes for handling materials and equipment.
Why It's Important
Cleanroom protocol is crucial for a Wafer Fab Operator as it prevents contamination of wafers, ensuring high-quality semiconductor production and minimizing costly defects or failures in electronic devices.
How to Improve Cleanroom Protocol Skills
Improving cleanroom protocol for a Wafer Fab Operator involves enhancing cleanliness and minimizing contamination risks. Here’s a concise guide:
Training and Awareness: Regularly update and train all personnel on cleanroom protocols and contamination control practices. Cleanroom Training
Proper Gowning Procedures: Follow strict gowning and degowning procedures to minimize human-borne contamination. This includes using appropriate cleanroom garments and following the correct order of donning and doffing. Proper Gowning Protocol
Equipment and Tool Handling: Ensure all equipment and tools entering the cleanroom are properly cleaned and, if required, sterilized. Equipment Handling Guidelines
Regular Cleaning and Maintenance: Implement a rigorous schedule for cleaning and maintenance of the cleanroom environment, including surfaces, equipment, and air filtration systems. Cleanroom Maintenance
Air Quality Control: Monitor and control particle count, temperature, humidity, and air flow to maintain required cleanroom standards. Use HEPA or ULPA filters for air filtration. Air Quality Control Standards
Contamination Control: Adopt strategies to control contamination sources, such as material and personnel flow, to minimize cross-contamination. Contamination Control Strategies
Regular Audits and Monitoring: Conduct regular audits of cleanroom protocols and practices. Use monitoring equipment to continuously assess environmental and equipment parameters. Cleanroom Monitoring Systems
By focusing on these key areas, Wafer Fab Operators can significantly improve their cleanroom protocols, ensuring higher product quality and compliance with industry standards.
How to Display Cleanroom Protocol Skills on Your Resume
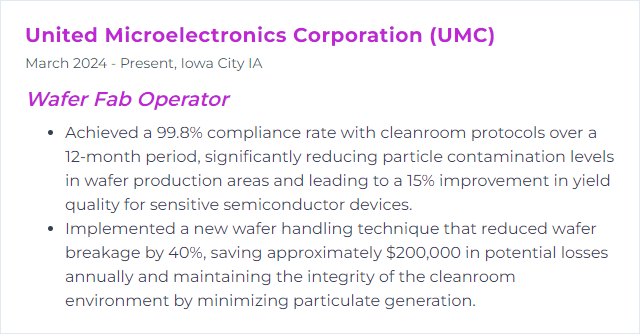
8. SPC (Statistical Process Control)
Statistical Process Control (SPC) is a method used in manufacturing, including by Wafer Fab Operators, to monitor and control a process through data analysis to ensure it operates at its fullest potential, producing consistent, high-quality products with minimal waste. It involves using statistical techniques to measure and analyze the variation in processes to detect and correct problems proactively.
Why It's Important
SPC (Statistical Process Control) is crucial for a Wafer Fab Operator as it ensures consistent quality and reliability in semiconductor manufacturing by identifying process variations and deviations early, allowing for timely adjustments and minimizing defects. This boosts efficiency, reduces waste, and ensures customer satisfaction.
How to Improve SPC (Statistical Process Control) Skills
Improving Statistical Process Control (SPC) in a Wafer Fab environment involves several key steps focused on enhancing data quality, analysis, and process optimization. Here's a concise guide:
Educate and Train Staff: Ensure all operators and engineers understand SPC principles and tools. SPC Training can improve data collection and interpretation.
Implement Real-Time Monitoring: Use technology for real-time data collection and monitoring to quickly identify and address process deviations. Systems like SEMI Standards can be adopted for consistency.
Standardize Processes: Develop and follow standardized procedures for all processes to reduce variability. ISO Standards for semiconductor manufacturing can guide process standardization.
Regular Calibration and Maintenance: Ensure all measurement instruments are regularly calibrated and maintained to prevent inaccurate data that could skew SPC analysis. Equipment Calibration guidance by NIST is useful.
Use Advanced SPC Software: Leverage advanced SPC software tools designed for semiconductor manufacturing to analyze data more effectively. Semiconductor SPC Software like Cornerstone offers tailored solutions.
Engage in Continuous Improvement: Adopt a Kaizen or continuous improvement approach, using SPC data to identify areas for process optimization regularly. Kaizen in Manufacturing provides strategies for continuous improvement.
Root Cause Analysis: When variances occur, perform thorough root cause analysis to prevent recurrence. Techniques like 5 Whys can be effective.
By focusing on these areas, a Wafer Fab Operator can significantly improve SPC efforts, leading to better quality control, efficiency, and product reliability.
How to Display SPC (Statistical Process Control) Skills on Your Resume
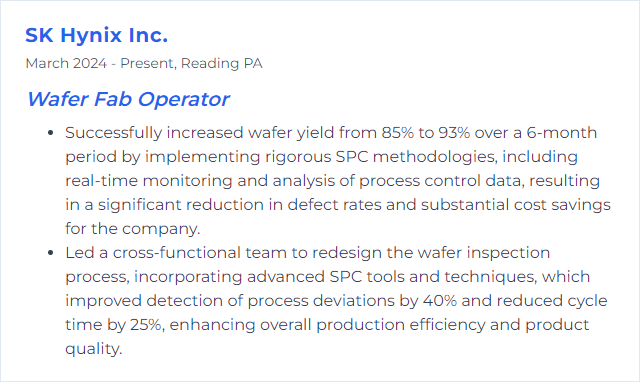
9. SEM (Scanning Electron Microscopy)
Scanning Electron Microscopy (SEM) is a powerful imaging technique used in wafer fabrication to magnify and analyze the surface structure and composition of semiconductor devices at very high resolutions, aiding in the detection of defects and ensuring quality control.
Why It's Important
SEM (Scanning Electron Microscopy) is crucial for a Wafer Fab Operator because it allows for the high-resolution imaging of wafer surfaces to detect and analyze defects, ensuring the quality and reliability of semiconductor devices.
How to Improve SEM (Scanning Electron Microscopy) Skills
Improving SEM (Scanning Electron Microscopy) performance, especially for a Wafer Fab Operator, involves focusing on sample preparation, equipment optimization, and image processing techniques. Here’s a concise guide:
Sample Preparation: Ensure the sample is clean and properly mounted. Use critical point drying to minimize damage for delicate samples. Microscopy Today provides insights on sample preparation.
Equipment Optimization: Regularly calibrate the SEM for accurate voltage, current, and focus settings. Adjust the working distance and aperture to optimize resolution. JEOL offers a guide on SEM operation.
Image Processing: Enhance image quality through software by adjusting brightness, contrast, and utilizing filtering techniques. ImageJ is a useful tool for SEM image processing.
By focusing on these areas, a Wafer Fab Operator can significantly improve SEM performance, leading to better imaging results and analysis.
How to Display SEM (Scanning Electron Microscopy) Skills on Your Resume
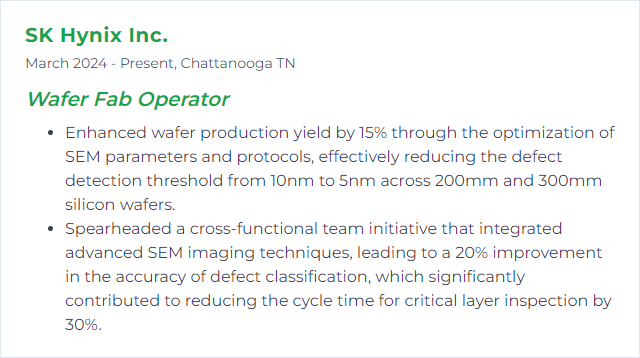
10. Ellipsometry
Ellipsometry is a non-destructive, optical technique used in wafer fabrication to measure the thickness and optical properties of thin films on semiconductor wafers by analyzing the change in polarization as light reflects off the film surface.
Why It's Important
Ellipsometry is crucial in a wafer fab environment because it accurately measures film thickness and optical properties on semiconductor wafers, enabling precise control over manufacturing processes and ensuring high-quality device fabrication.
How to Improve Ellipsometry Skills
To improve ellipsometry, particularly in the context of a wafer fabrication setting, consider the following concise strategies:
Calibration and Maintenance: Regularly calibrate ellipsometers to ensure accurate measurements. This includes checking the light source, detector sensitivity, and alignment. Ellipsometry Calibration Guide.
Environmental Controls: Minimize environmental variables such as temperature, humidity, and vibrations, as they can affect measurements. Semiconductor Environment Standards.
Sample Preparation: Ensure wafer surfaces are clean and free from contaminants before measurement, as surface conditions can significantly impact results. Wafer Cleaning Techniques.
Software Upgrades: Utilize the latest software for data analysis to take advantage of improved algorithms and models for material characterization. Software Solutions for Ellipsometry.
Training and Education: Continuous training for operators on the latest ellipsometry techniques and best practices ensures the most accurate and reliable data collection. Ellipsometry Training Courses.
Implementing these strategies can lead to more precise and reliable ellipsometry measurements, enhancing wafer fabrication quality and efficiency.
How to Display Ellipsometry Skills on Your Resume
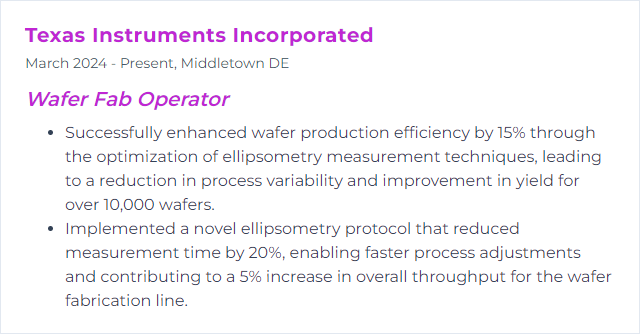
11. Diffusion Processes
Diffusion processes in a wafer fab involve the controlled movement of atoms or molecules into silicon wafers to alter their electrical properties. This is crucial for creating semiconductor devices, as it allows for the precise doping of the wafers with impurities to achieve desired conductivity characteristics.
Why It's Important
Diffusion processes are crucial in wafer fabrication because they enable the precise doping of semiconductor materials, adjusting their electrical properties to create the essential p-n junctions for semiconductor devices. This process is vital for manufacturing transistors, diodes, and integrated circuits, directly impacting device performance and functionality.
How to Improve Diffusion Processes Skills
Improving diffusion processes in a wafer fabrication setting involves optimizing various parameters to enhance efficiency, yield, and device performance. Here are concise strategies:
Temperature Uniformity: Ensure precise control of the temperature across the diffusion furnace to improve dopant penetration uniformity. Temperature Control in Diffusion Furnaces
Gas Flow Stability: Maintain stable gas flow rates and compositions to achieve consistent dopant profiles. Gas Flow Dynamics in CVD Processes
Pre-Diffusion Cleaning: Implement rigorous wafer cleaning protocols before diffusion to reduce contaminants that can affect diffusion uniformity. Wafer Cleaning Techniques
Process Time and Temperature: Optimize diffusion times and temperatures based on dopant species and desired junction depths, leveraging simulation tools for precision. Diffusion Process and Simulation
Atmosphere Control: Control the ambient atmosphere in the diffusion furnace to prevent unwanted oxidation or other reactions that could impact dopant profiles. Atmosphere Control in Diffusion Furnaces
Equipment Calibration: Regularly calibrate diffusion furnaces and monitoring equipment to ensure accurate temperature and gas flow readings. Calibration in Semiconductor Manufacturing
Use of SOG (Spin-On Glass): For better uniformity and step coverage, consider using spin-on glass doping methods where applicable. Spin-On Glass for Semiconductor Devices
Advanced Simulation Tools: Utilize advanced simulation tools for process optimization, allowing for the predictive modeling of diffusion profiles under various conditions. Process Simulation in Microelectronics
Continuous Improvement: Implement a continuous improvement program, utilizing SPC (Statistical Process Control) to monitor, control, and optimize the diffusion processes. SPC in Semiconductor Manufacturing
By focusing on these areas, wafer fab operators can enhance diffusion process outcomes, leading to improved device performance and yield.
How to Display Diffusion Processes Skills on Your Resume
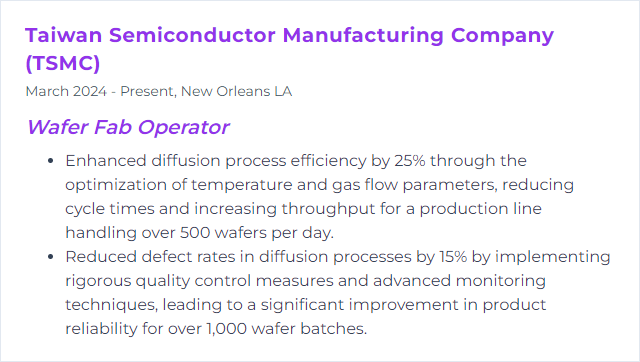
12. Metrology Equipment
Metrology equipment in the context of a wafer fab operator refers to precision tools and instruments used to measure and analyze the physical characteristics of semiconductor wafers, such as thickness, topography, and defect density, ensuring they meet strict manufacturing standards and specifications.
Why It's Important
Metrology equipment is crucial for a Wafer Fab Operator because it ensures the precision and quality of semiconductor devices by measuring and verifying dimensions, properties, and alignment of materials and layers throughout the fabrication process, thereby optimizing performance and yield.
How to Improve Metrology Equipment Skills
Improving metrology equipment in a wafer fab environment involves enhancing accuracy, reliability, and throughput. Here are concise strategies:
Regular Calibration: Ensure metrology equipment is calibrated regularly against certified standards to maintain accuracy. NIST offers guidelines on calibration procedures.
Upgrade Software: Keep software up-to-date to utilize the latest algorithms and data processing techniques for improved measurement accuracy and speed. SEMI provides standards that can guide software upgrades.
Implement Automation: Automate the measurement process to reduce human error and increase throughput. IEEE Xplore offers resources on the latest automation technologies in semiconductor metrology.
Environmental Control: Improve environmental controls in the metrology area to reduce variability caused by temperature and humidity fluctuations. ASHRAE has guidelines for environmental control in precision manufacturing spaces.
Employee Training: Regularly train operators on the latest metrology techniques and equipment usage to ensure measurements are performed accurately and efficiently. SEMI provides industry-specific training courses.
Preventive Maintenance: Adhere to a strict preventive maintenance schedule to minimize equipment downtime and ensure consistent measurement performance. ISO 17025 outlines general requirements for the competence of testing and calibration laboratories, including equipment maintenance.
By focusing on these areas, wafer fab operators can significantly improve the performance and reliability of their metrology equipment.
How to Display Metrology Equipment Skills on Your Resume
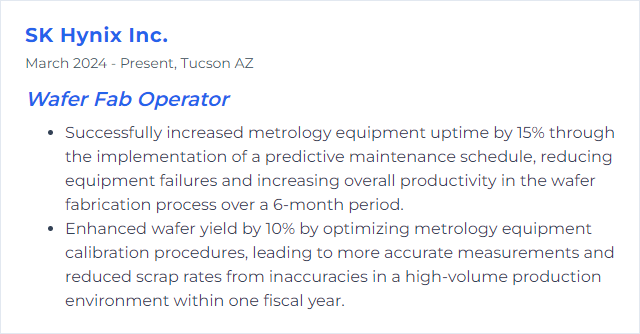