Top 12 Fabrication Engineer Skills to Put on Your Resume
In the competitive field of fabrication engineering, showcasing a robust set of skills on your resume can significantly elevate your job prospects. Mastering a diverse array of technical abilities, problem-solving skills, and innovative thinking is crucial for standing out to potential employers in this dynamic industry.
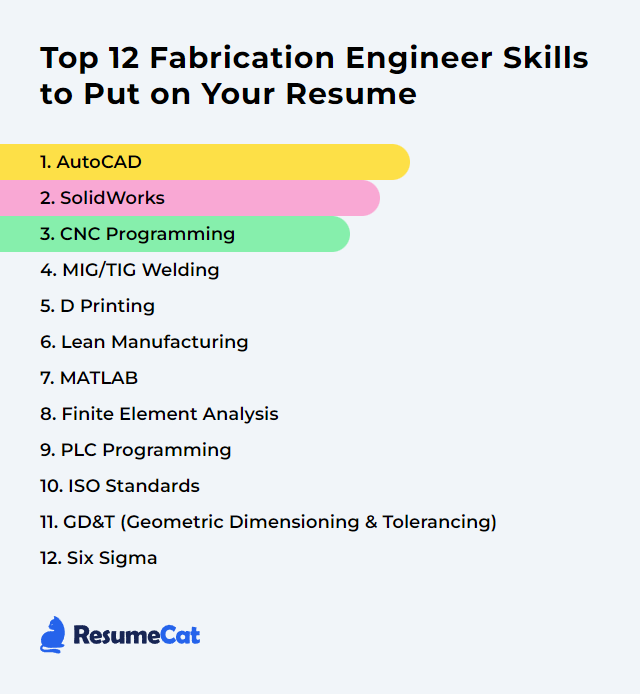
Fabrication Engineer Skills
- AutoCAD
- SolidWorks
- CNC Programming
- MIG/TIG Welding
- D Printing
- Lean Manufacturing
- MATLAB
- Finite Element Analysis
- PLC Programming
- ISO Standards
- GD&T (Geometric Dimensioning and Tolerancing)
- Six Sigma
1. AutoCAD
AutoCAD is a computer-aided design (CAD) software used extensively by fabrication engineers for creating precise 2D and 3D drawings and models of parts and assemblies in manufacturing processes.
Why It's Important
AutoCAD is crucial for a Fabrication Engineer as it enables precise design and drafting of complex components, ensuring accuracy, efficiency, and optimization in fabrication processes.
How to Improve AutoCAD Skills
Improving AutoCAD skills, especially for a Fabrication Engineer, involves focusing on precision, efficiency, and leveraging advanced features relevant to fabrication processes. Here are short, concise tips with inline links for further exploration:
Master Keyboard Shortcuts: Enhance your speed and efficiency by mastering AutoCAD keyboard shortcuts. Autodesk provides a comprehensive list here.
Utilize AutoCAD's Advanced Features: Dive into features like 3D modeling and AutoLISP for automation. Autodesk offers tutorials and guidance here.
Customize Your Workspace: Tailor your AutoCAD interface to better suit your workflow in fabrication design. Guidance on customization can be found here.
Participate in Online Forums and Communities: Engage with other professionals to share tips and solve challenges. The Autodesk forums are a great place to start, available here.
Regularly Update Your Skills with New Releases: Stay abreast of new features and improvements in the latest AutoCAD versions. Autodesk provides updates and resources here.
Apply Practical Projects: Practice your skills with real-world projects or simulations relevant to fabrication engineering to understand the application of tools in practical scenarios.
Focusing on these areas will help a Fabrication Engineer effectively utilize AutoCAD in their work, leading to improved design quality and productivity.
How to Display AutoCAD Skills on Your Resume
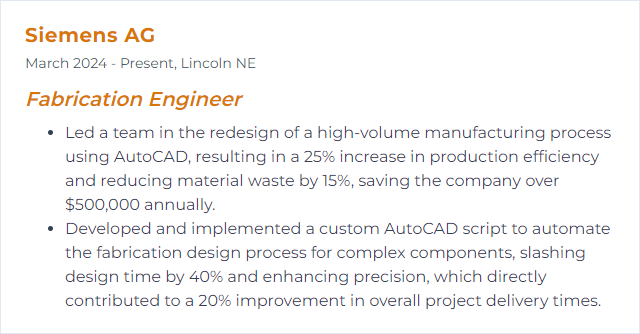
2. SolidWorks
SolidWorks is a computer-aided design (CAD) and engineering software tool that allows fabrication engineers to create 3D models, assemblies, and detailed drawings for manufacturing processes.
Why It's Important
SolidWorks is crucial for a Fabrication Engineer as it enables precise 3D modeling and simulation, facilitating the design and optimization of complex fabrications, improving accuracy, efficiency, and reducing material waste.
How to Improve SolidWorks Skills
Improving your SolidWorks skills as a Fabrication Engineer involves mastering both the software's core functionalities and the specific tools relevant to fabrication processes. Here’s a concise guide:
Undergo Advanced Training: Participate in SolidWorks-specific courses focused on fabrication and manufacturing. SolidWorks Training offers various programs that cater to different aspects of the software.
Practice Design for Manufacturing (DFM): Apply DFM principles directly within SolidWorks to ensure designs are optimized for fabrication. Utilize resources like the SolidWorks DFMXpress tool for guidance.
Leverage Sheet Metal Tools: Master the Sheet Metal module to streamline the design of fabricable parts. This Sheet Metal Design Guide is a valuable resource.
Use Weldments for Structural Designs: Explore the Weldments tool for designing and documenting welded structures efficiently. The Weldments Tutorial provides a good starting point.
Incorporate SolidWorks Simulation: Apply SolidWorks Simulation to test and validate designs under real-world conditions, reducing the need for physical prototypes. Begin with SolidWorks Simulation to understand its capabilities.
Join the SolidWorks Community: Engage with the SolidWorks Community Forums for peer advice, tips, and shared experiences relevant to fabrication engineering.
Stay Updated: SolidWorks frequently updates its software. Stay informed on the latest features and improvements by checking the What's New in SolidWorks section.
Consistently applying these strategies will significantly improve your proficiency and efficiency in using SolidWorks for fabrication engineering tasks.
How to Display SolidWorks Skills on Your Resume
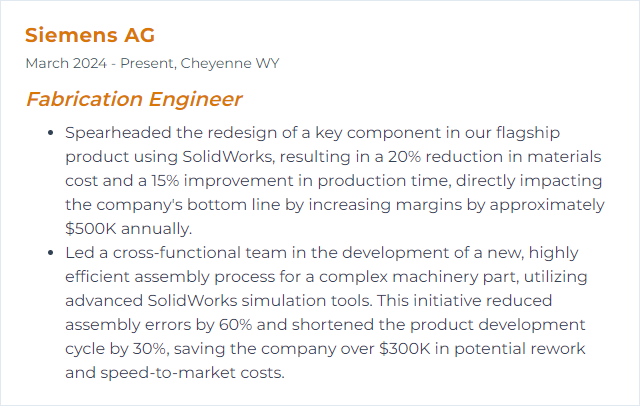
3. CNC Programming
CNC programming involves creating coded instructions that control the actions of computer numerical control (CNC) machines, guiding the cutting and shaping of materials into parts or products, tailored to the specifications needed in fabrication engineering projects.
Why It's Important
CNC programming is crucial for a Fabrication Engineer because it enables precise control over machining tools, ensuring high accuracy, repeatability, and efficiency in the fabrication of components, thereby optimizing production processes and product quality.
How to Improve CNC Programming Skills
Improving CNC programming involves enhancing efficiency, accuracy, and the quality of the machined parts. For a Fabrication Engineer, focusing on several key areas can lead to significant improvements:
Mastering CAD/CAM Software: Becoming proficient in CAD/CAM software allows for the efficient creation of complex designs and simplifies the programming process. Explore tutorials and courses specific to your software suite. Autodesk offers comprehensive guides and training modules for various proficiency levels.
Understanding Material Properties: Different materials react differently under machining processes. Having a deep understanding of material properties can guide the programming for optimal speeds, feeds, and tool paths. The American Society for Metals provides resources on material properties and their impact on machining.
Tool Selection and Optimization: Choosing the right tool and optimizing its path can significantly reduce machining time and improve surface finish. Resources like Sandvik Coromant's knowledge base offer insights into tool selection and optimization techniques.
Implementing Efficient Workholding Strategies: Secure and efficient workholding minimizes vibrations and machining time. Explore innovative workholding solutions and strategies through Mitee-Bite, which specializes in clamping and fixturing technologies.
Leveraging Simulation Software: Using simulation software to preview and adjust tool paths can prevent errors and material waste. Mastercam's simulation features allow for detailed previews of machining operations.
Continuous Learning: Technologies and techniques in CNC programming are constantly evolving. Stay updated with the latest trends and best practices by subscribing to industry-leading publications like Modern Machine Shop.
Networking and Collaboration: Join forums and professional networks such as Practical Machinist to exchange knowledge, tips, and experiences with other professionals in the field.
By focusing on these areas, a Fabrication Engineer can significantly improve their CNC programming skills, leading to more efficient and precise manufacturing processes.
How to Display CNC Programming Skills on Your Resume
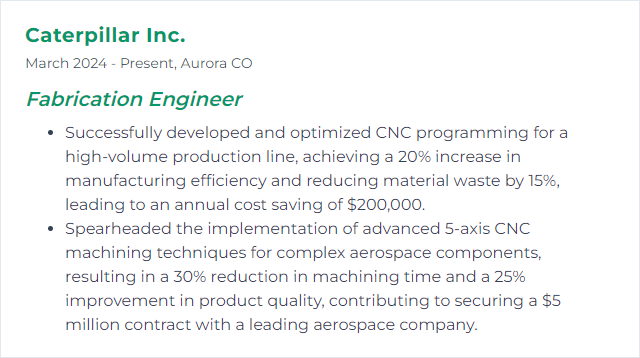
4. MIG/TIG Welding
MIG (Metal Inert Gas) welding, also known as GMAW (Gas Metal Arc Welding), uses a continuous solid wire electrode heated and fed into the weld pool, combined with an inert gas (usually argon) to protect the weld from contamination. It's versatile, easy to learn, and suitable for welding a wide range of metals and thicknesses.
TIG (Tungsten Inert Gas) welding, or GTAW (Gas Tungsten Arc Welding), involves using a non-consumable tungsten electrode to produce the weld. The weld area is protected from atmospheric contamination by an inert shielding gas (argon or helium), and filler metal is optionally added. TIG is highly precise, offering high-quality and clean welds, but it requires greater skill and is generally slower than MIG welding.
Why It's Important
MIG/TIG welding is crucial for a Fabrication Engineer because it allows for precise, high-quality, and versatile welding of a wide range of metals with increased efficiency and control, essential for creating strong, durable constructions and components in manufacturing and engineering projects.
How to Improve MIG/TIG Welding Skills
Improving MIG/TIG welding skills, especially for a Fabrication Engineer, involves a focus on technique, equipment understanding, and practice. Here's a concise guide:
Understand the Basics: Ensure you have a solid grasp of the fundamental principles of MIG (Metal Inert Gas) and TIG (Tungsten Inert Gas) welding. Lincoln Electric provides a good starting point.
Equipment Mastery: Familiarize yourself thoroughly with your welding equipment. Knowing your tools inside and out can significantly impact the quality of your welds. MillerWelds offers excellent resources.
Control and Technique: Practice controlling your hand steadiness, welding speed, and arc length. Consistency is key in welding. Welding Tips and Tricks has various tutorials and tips.
Material Knowledge: Understanding the materials you are working with will help in selecting the right filler material and welding parameters.
Safety First: Always prioritize safety by using appropriate protective gear and following safety protocols. OSHA’s Welding, Cutting, and Brazing guidelines are crucial.
Continuous Learning and Practice: Welding is a skill that improves with practice and continuous learning. Participate in workshops, online courses, and other training opportunities.
Feedback and Improvement: Seek feedback from experienced welders and be open to critique. Video recording your practice sessions can also provide insights into areas for improvement.
By focusing on these areas, a Fabrication Engineer can significantly enhance their MIG/TIG welding skills.
How to Display MIG/TIG Welding Skills on Your Resume
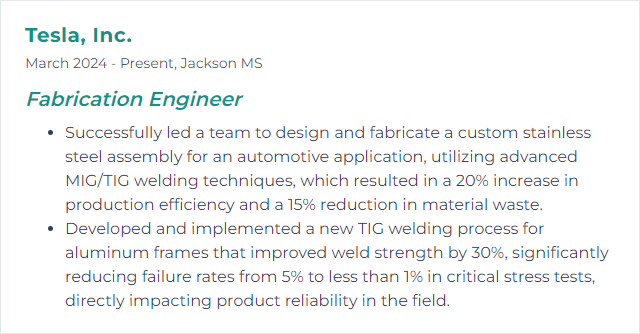
5. D Printing
3D printing, also known as additive manufacturing, is a process where three-dimensional objects are created by layering materials based on a digital model. For a Fabrication Engineer, it is a versatile tool for prototyping, manufacturing complex geometries, custom parts, and reducing material waste.
Why It's Important
3D printing is important for a Fabrication Engineer as it enables rapid prototyping, customizes parts with complex geometries, reduces material waste, and streamlines the manufacturing process, leading to increased efficiency and innovation.
How to Improve D Printing Skills
Improving 3D printing, from a Fabrication Engineer's perspective, involves focusing on optimization of material properties, print speed, resolution, and reliability. Consider these concise strategies:
Material Optimization: Explore advanced materials tailored for specific applications for improved strength, flexibility, or thermal resistance. Materialise offers insights on material selections.
Print Speed and Quality: Balance between speed and quality by adjusting the printer's settings. Techniques such as variable layer height can improve both. The Simplify3D Print Quality Guide provides tips on fine-tuning these aspects.
Machine Calibration: Regular calibration of your 3D printer ensures accuracy and repeatability. Prusa Printers offer comprehensive calibration guides.
Software Optimization: Utilize advanced slicing software for better support structure generation, slicing efficiency, and model repair capabilities. Ultimaker Cura is renowned for its versatility.
Post-Processing Techniques: Enhance the finish and properties of printed parts through techniques like sanding, chemical smoothing, or UV curing. Formlabs has a detailed guide on post-processing.
Continuous Learning: Stay updated with the latest trends, technologies, and materials in 3D printing by engaging with communities and platforms like 3D Printing Industry.
By focusing on these areas, a Fabrication Engineer can significantly improve the outcomes of 3D printing processes.
How to Display D Printing Skills on Your Resume
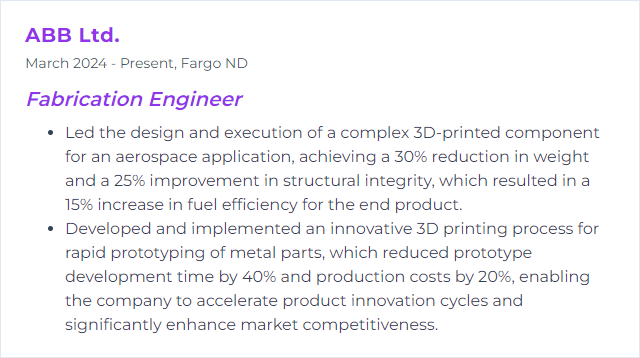
6. Lean Manufacturing
Lean Manufacturing is a systematic approach aimed at minimizing waste within manufacturing systems while simultaneously maximizing productivity. For a Fabrication Engineer, it involves continuously optimizing processes, reducing material wastage, improving quality, and streamlining production flows to deliver higher value to customers with fewer resources.
Why It's Important
Lean Manufacturing is important for a Fabrication Engineer because it optimizes production processes, reduces waste, and improves quality and efficiency, leading to cost savings, higher customer satisfaction, and increased competitiveness in the market.
How to Improve Lean Manufacturing Skills
Improving Lean Manufacturing, especially for a Fabrication Engineer, involves focusing on reducing waste, optimizing processes, and enhancing productivity while ensuring quality. Here's a concise guide:
Value Stream Mapping: Identify and map out all the processes involved in your manufacturing line to visualize waste and inefficiencies. More on Value Stream Mapping.
5S Methodology: Implement the 5S (Sort, Set in order, Shine, Standardize, Sustain) to organize the workplace, resulting in improved efficiency and safety. 5S Explained.
Continuous Improvement (Kaizen): Foster a culture of continuous improvement where small, incremental changes regularly occur. This approach encourages innovation and adaptability. Kaizen Guide.
Just-In-Time (JIT) Production: Aim to reduce inventory costs and waste by producing just what is needed, just in time. This requires precise planning and communication with suppliers. Understanding JIT.
Total Productive Maintenance (TPM): Focus on preventive maintenance to minimize downtime and defects. Engaging all employees in maintaining equipment can significantly improve productivity. TPM Overview.
Standard Work: Develop and implement standard operating procedures for all tasks to ensure consistency and efficiency. This also aids in training and cross-training employees. Standard Work Basics.
Use of Technology and Automation: Incorporate technology and automation where applicable to enhance efficiency, accuracy, and consistency. Manufacturing Technology.
Employee Engagement and Training: Invest in your workforce through regular training and engagement. Skilled, motivated employees are crucial for successful lean manufacturing. Employee Engagement.
By focusing on these key areas, a Fabrication Engineer can significantly improve lean manufacturing practices, leading to reduced costs, improved quality, and higher efficiency.
How to Display Lean Manufacturing Skills on Your Resume
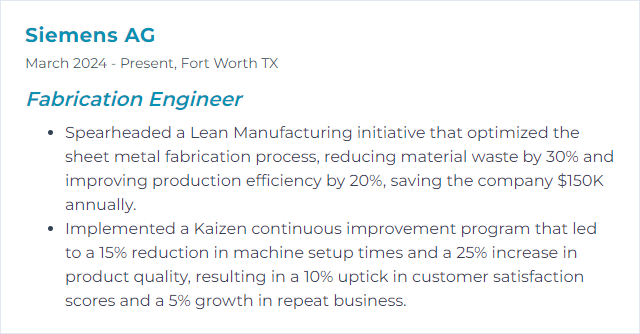
7. MATLAB
MATLAB is a high-level programming and numerical computing environment used for algorithm development, data analysis, visualization, and numerical simulation, particularly useful for fabrication engineers in tasks such as material property analysis, process optimization, and equipment control system design.
Why It's Important
MATLAB is important for a Fabrication Engineer because it provides powerful tools for designing, simulating, and optimizing fabrication processes and materials, enabling precise control and efficiency improvements in manufacturing operations.
How to Improve MATLAB Skills
Improving your MATLAB skills as a Fabrication Engineer involves focusing on areas that enhance your ability to model, simulate, and analyze fabrication processes and materials. Here’s a concise guide:
Learn MATLAB Basics: Start with MATLAB's own Getting Started guide to understand the basics if you're not already familiar.
Master Data Visualization: As a Fabrication Engineer, visualizing data can help in understanding material properties and process parameters. MATLAB offers extensive data visualization capabilities.
Simulate Materials and Processes: Use MATLAB's Simulink for simulating dynamic systems, which is crucial for modeling fabrication processes.
Automate Routine Tasks: Learn how to automate tasks in MATLAB to save time on repetitive calculations or data processing.
Dive into Material Science Toolkits: Explore MATLAB toolkits specific to material science and engineering. The Materials Informatics Toolbox is a good start for materials data analysis.
Enhance Skills with Online Courses: Platforms like Coursera, Udemy, and MATLAB Academy offer courses tailored to engineers. For instance, MATLAB's own training courses can be directly relevant.
Implement Advanced Numerical Methods: Fabrication engineering often requires solving complex equations and material behavior models. MATLAB's robust numerical analysis features can be very useful.
Join MATLAB Communities: Engage with other professionals and enthusiasts in MATLAB community forums and File Exchange, where you can find custom functions, toolboxes, and expertise shared by users worldwide.
Stay Updated: MATLAB is constantly updated. Keep an eye on the latest releases to make use of new functions and improvements.
Apply Knowledge in Projects: Finally, the best way to improve is by applying what you learn in real-world projects. Whether it’s a small task or a part of your job, using MATLAB to solve practical problems will enhance your skills significantly.
By focusing on these aspects, you can significantly improve your MATLAB skills in the context of fabrication engineering, thereby enhancing your ability to innovate and solve complex engineering challenges.
How to Display MATLAB Skills on Your Resume
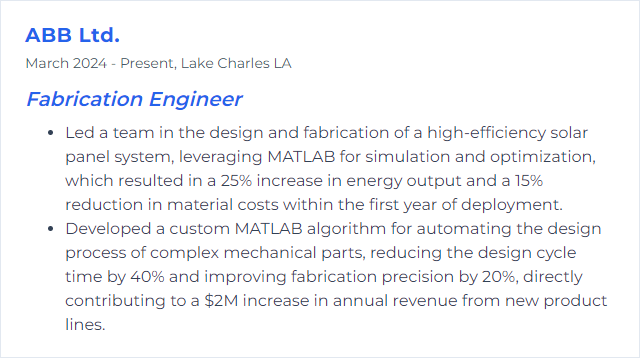
8. Finite Element Analysis
Finite Element Analysis (FEA) is a computerized method for predicting how a product reacts to real-world forces, vibration, heat, fluid flow, and other physical effects. For a Fabrication Engineer, FEA simulates the design process to identify potential problems and optimize the structure or component for strength, durability, and performance before manufacturing, reducing the need for physical prototypes and testing.
Why It's Important
Finite Element Analysis (FEA) is crucial for a Fabrication Engineer because it allows for the precise prediction of how a product will react to real-world forces, such as vibration, heat, and other physical effects, ensuring optimal design, material selection, and cost-effectiveness while minimizing the risk of failure during fabrication.
How to Improve Finite Element Analysis Skills
Improving Finite Element Analysis (FEA) involves enhancing model accuracy, computational efficiency, and result interpretation. For a Fabrication Engineer, this focuses on material properties, mesh refinement, and solver settings.
- Understand Material Properties: Accurate material data is crucial. Utilize databases like MatWeb for precise material properties.
- Mesh Refinement: Employ adaptive mesh refinement techniques to balance accuracy and computation time. Start with coarser meshes, refine in areas of high stress. COMSOL Blog provides practical tips.
- Solver Settings: Optimize solver settings for your analysis type. Ansys offers guidance on selecting appropriate solvers and settings.
- Validation and Verification: Validate your model against experimental or benchmark data. NAFEMS has resources on best practices.
- Continuous Learning: Stay updated with the latest FEA techniques and software improvements. Coursera and edX offer courses on FEA basics and advanced topics.
Implementing these strategies ensures more accurate, efficient, and reliable FEA outcomes, enhancing fabrication design and optimization processes.
How to Display Finite Element Analysis Skills on Your Resume
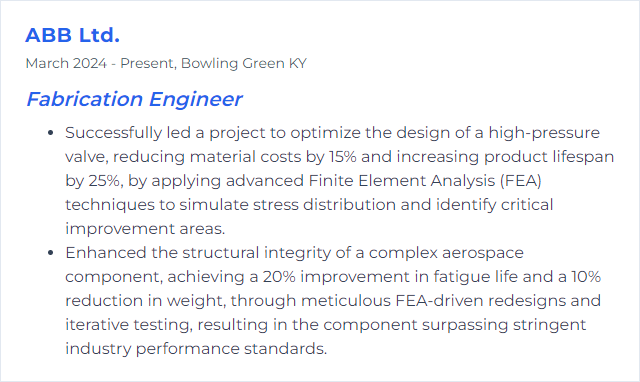
9. PLC Programming
PLC programming involves creating and implementing software instructions that control the automated processes and machinery in manufacturing and fabrication environments, enabling precise, reliable, and efficient operation of production systems.
Why It's Important
PLC programming is crucial for a Fabrication Engineer as it enables precise control and automation of machinery and processes, ensuring efficiency, reliability, and safety in manufacturing operations.
How to Improve PLC Programming Skills
To improve your PLC programming skills as a Fabrication Engineer, focus on these concise strategies:
- Understand the Basics: Start with a solid understanding of PLC basics. PLC Academy offers fundamental courses.
- Practice Regularly: Hands-on experience is crucial. Use simulation software like RSLogix 500 to practice without physical hardware.
- Learn from Examples: Analyze and dissect existing PLC programs. PLCdev provides sample programs for study.
- Stay Updated: Follow industry trends and updates. Websites like Automation.com offer the latest news and technologies.
- Network with Professionals: Join forums and groups. PLCTalk is a great community for advice and sharing experiences.
- Understand Your Machinery: Deep knowledge of your fabrication machinery will guide efficient program design.
- Safety First: Prioritize learning about safety standards relevant to PLC programming in fabrication. ISA provides resources on safety standards.
Incorporating these strategies into your learning routine will significantly enhance your PLC programming skills in the context of fabrication engineering.
How to Display PLC Programming Skills on Your Resume
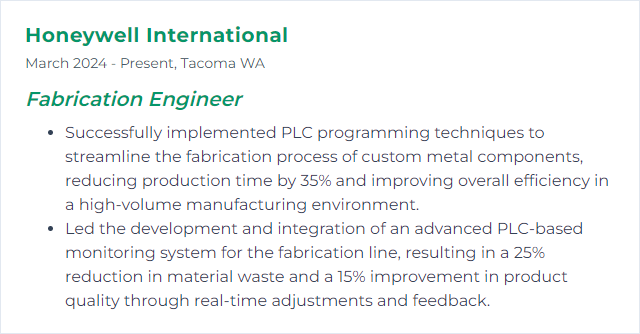
10. ISO Standards
ISO standards are a set of internationally recognized guidelines and specifications designed to ensure products, services, and systems are safe, reliable, and of consistent quality. For a Fabrication Engineer, these standards provide critical protocols for materials, processes, and safety, ensuring efficiency, productivity, and compliance with global best practices in manufacturing and engineering.
Why It's Important
ISO Standards are important for a Fabrication Engineer because they ensure quality, safety, and efficiency in the manufacturing processes, leading to consistent product quality, reduced waste, and increased customer satisfaction.
How to Improve ISO Standards Skills
Improving ISO Standards as a Fabrication Engineer involves a focus on quality management, continuous improvement, and staying updated with industry best practices. Here’s a concise guide:
Understand Current Standards: Deeply understand the requirements of ISO 9001 for quality management systems, focusing on those directly applicable to fabrication processes.
Engage in Continuous Learning: Stay informed about updates and revisions to ISO standards relevant to fabrication engineering through the ISO website and professional engineering bodies.
Implement Quality Management Systems (QMS): Adopt and tailor QMS principles to your operations. Resources like the American Society for Quality (ASQ) provide guidelines and tools for effective implementation.
Conduct Regular Audits: Regular internal and external audits assess compliance and identify areas for improvement. ISO provides a guide for auditing management systems (ISO 19011).
Engage with Stakeholders: Collaborate with suppliers, customers, and employees to gain insights into potential areas of improvement. This participatory approach fosters innovation and compliance.
Continuous Improvement: Adopt the Plan-Do-Check-Act (PDCA) cycle for continuous improvement in your processes. This iterative process is a cornerstone of ISO 9001 and can drive improvements in fabrication engineering practices.
Professional Development: Participate in ISO standard development if possible, and engage in professional development opportunities through organizations like The American Society of Mechanical Engineers (ASME) to stay at the forefront of industry trends and standards.
By focusing on these areas, a Fabrication Engineer can significantly contribute to improving and maintaining ISO standards within their organization.
How to Display ISO Standards Skills on Your Resume
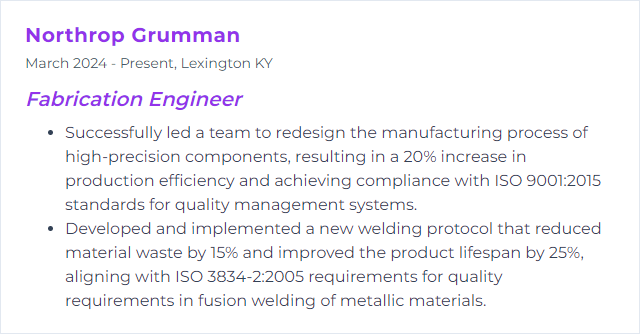
11. GD&T (Geometric Dimensioning and Tolerancing)
GD&T (Geometric Dimensioning and Tolerancing) is a system for defining and communicating engineering tolerances and design intent on mechanical parts and assemblies, focusing on geometry (shape, location, orientation) and allowable variation. It helps ensure parts fit and function together as intended, optimizing precision and manufacturing efficiency.
Why It's Important
GD&T is crucial for a Fabrication Engineer because it ensures parts are made with precise geometrical accuracy and functional fit, reducing manufacturing errors, costs, and ensuring interchangeability, thereby improving product quality and efficiency in fabrication processes.
How to Improve GD&T (Geometric Dimensioning and Tolerancing) Skills
Improving GD&T skills as a Fabrication Engineer involves a focused approach on understanding and applying geometric tolerances effectively. Here are concise steps and resources:
Fundamentals Mastery: Start with grasping the basics of GD&T principles. ASME's Y14.5 standard is an essential resource.
Practical Application: Practice applying GD&T to real-world projects. Autodesk has practical guides and tutorials that can help bridge theory with practice.
Training and Certification: Consider formal training or certification from recognized organizations. ASME offers courses that are industry-recognized.
Software Proficiency: Learn to use CAD software effectively, as they have built-in GD&T tools. SolidWorks tutorials can be particularly useful.
Join Forums and Groups: Engage with professional communities. The Eng-Tips Forums offer a place to ask questions and share knowledge.
Continuous Learning: Stay updated with the latest standards and practices. Reading industry publications and attending workshops or webinars are good strategies.
By following these steps and utilizing these resources, a Fabrication Engineer can significantly improve their GD&T skills, leading to more precise and efficient design and manufacturing processes.
How to Display GD&T (Geometric Dimensioning and Tolerancing) Skills on Your Resume
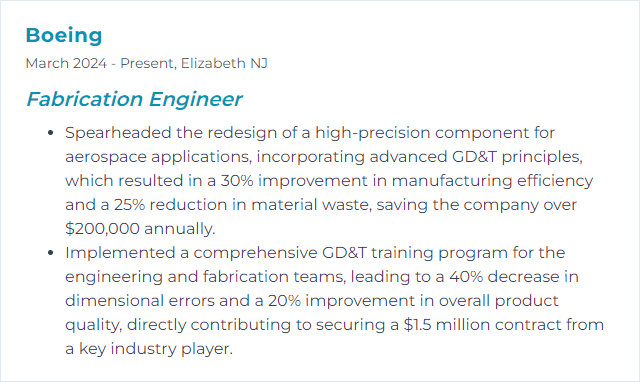
12. Six Sigma
Six Sigma is a data-driven methodology and set of techniques aimed at improving manufacturing processes, reducing defects, and ensuring quality control to achieve near-perfect products, particularly relevant for Fabrication Engineers in optimizing production efficiency and minimizing waste.
Why It's Important
Six Sigma is important for a Fabrication Engineer because it provides a systematic methodology to reduce defects, improve processes, and enhance product quality, leading to increased efficiency, customer satisfaction, and cost savings in manufacturing operations.
How to Improve Six Sigma Skills
To improve Six Sigma as a Fabrication Engineer, focus on these concise strategies:
Enhance Measurement Accuracy: Ensure all measurement tools and processes are calibrated regularly to reduce variability in fabrication processes.
Implement DMAIC Methodology: Follow the DMAIC process (Define, Measure, Analyze, Improve, Control) rigorously for systematic problem-solving and process improvement.
Leverage Statistical Tools: Utilize statistical tools like Minitab for data analysis to identify process inefficiencies and areas of improvement.
Engage in Continuous Learning: Stay updated with the latest Six Sigma and fabrication technologies through resources like iSixSigma and The American Society for Quality (ASQ).
Cross-Functional Teamwork: Foster collaboration between different departments (design, production, quality) to ensure holistic process improvements. Team collaboration techniques can be crucial here.
Customer Feedback Integration: Regularly gather and analyze customer feedback to align process improvements with customer requirements. Tools like SurveyMonkey can facilitate this process.
By focusing on these areas, you can significantly enhance the Six Sigma methodology's effectiveness within the fabrication engineering domain.
How to Display Six Sigma Skills on Your Resume
