Top 12 Warehouse Material Handler Skills to Put on Your Resume
In the fast-paced and intricate world of logistics, having a finely tuned set of skills as a warehouse material handler can set you apart from the competition. This article will explore the top 12 skills you should highlight on your resume to demonstrate your proficiency and readiness to excel in this vital role.
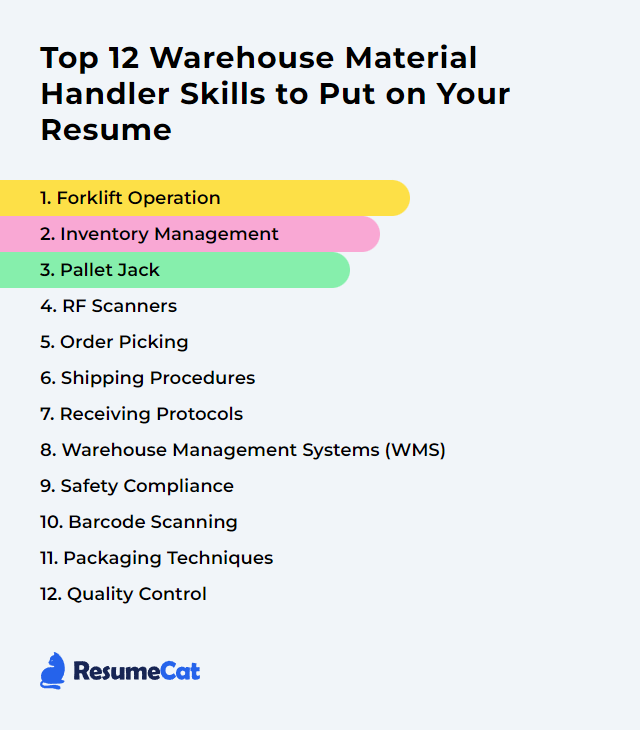
Warehouse Material Handler Skills
- Forklift Operation
- Inventory Management
- Pallet Jack
- RF Scanners
- Order Picking
- Shipping Procedures
- Receiving Protocols
- Warehouse Management Systems (WMS)
- Safety Compliance
- Barcode Scanning
- Packaging Techniques
- Quality Control
1. Forklift Operation
Forklift operation, in the context of a Warehouse Material Handler, involves safely using a forklift to move, load, unload, and stack goods or materials within a warehouse environment.
Why It's Important
Forklift operation is crucial for a Warehouse Material Handler because it enables the efficient movement of heavy and bulky goods, ensures safe handling of materials, and optimizes storage space, significantly enhancing productivity and operational flow in the warehouse.
How to Improve Forklift Operation Skills
Improving forklift operation, especially for a Warehouse Material Handler, involves a blend of safety practices, efficiency improvements, and ongoing training. Here are concise tips for enhancing forklift operation:
Safety First: Prioritize safety by adhering to OSHA’s forklift operational guidelines. This includes wearing seat belts, following speed limits, and ensuring load stability.
Regular Maintenance: Ensure forklifts are in top condition through regular maintenance checks. This includes checking brakes, steering, controls, and warning devices before use.
Proper Training: Invest in comprehensive training programs for operators. Training should cover safe operation, load handling, vehicle inspections, and refueling/recharging practices.
Efficient Layout: Optimize warehouse layout for smoother forklift operation. Ensure aisles are wide enough and clearly marked for forklift traffic. Efficient warehouse design can significantly improve operational efficiency.
Implement Technology: Use technology like telematics systems to track forklift operations, maintenance schedules, and operator behavior. This data can help identify areas for improvement.
Load Management: Train operators on proper load management techniques to prevent accidents and improve efficiency. Refer to guidelines on load handling for best practices.
Continuous Improvement: Foster a culture of continuous improvement by regularly reviewing and updating forklift operation practices. Engage with operators for feedback and implement suggestions where feasible.
By focusing on these areas, Warehouse Material Handlers can significantly improve forklift operation, enhancing safety, efficiency, and productivity in the warehouse.
How to Display Forklift Operation Skills on Your Resume
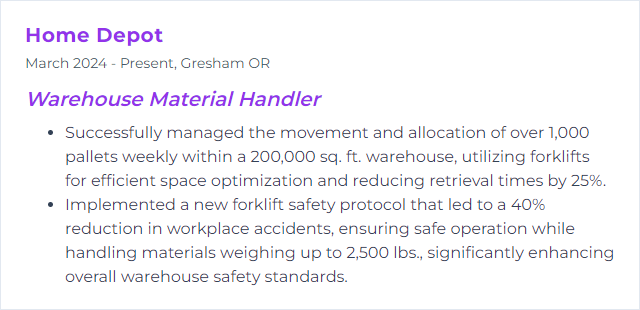
2. Inventory Management
Inventory management, in the context of a Warehouse Material Handler, involves overseeing and controlling the ordering, storage, and utilization of materials to ensure the right quantity of supplies is available to meet demand without excessive surplus.
Why It's Important
Inventory management is crucial for a Warehouse Material Handler as it ensures the right products are available in the correct quantities at the needed times, optimizing space, reducing costs, and preventing stockouts or excess inventory, ultimately enhancing customer satisfaction and operational efficiency.
How to Improve Inventory Management Skills
Improving inventory management, particularly for a Warehouse Material Handler, involves several strategic steps aimed at enhancing accuracy, efficiency, and organization. Here's a concise guide:
Implement an Inventory Management System: Use software that provides real-time tracking and management of stock levels, orders, sales, and deliveries. Shopify's guide on inventory management systems offers insights into selecting the right software.
Regular Audits: Regularly compare the actual stock in the warehouse to the recorded inventory to ensure accuracy. Square's inventory audit procedures can help streamline this process.
FIFO (First In, First Out): Ensure older stock is sold or used before newer stock. This is particularly crucial for perishable goods. TradeGecko’s FIFO explanation offers a deeper understanding.
Optimize Warehouse Layout: Arrange the warehouse to streamline the flow of goods, from receiving to shipping, minimizing handling and errors. Shopify’s warehouse layout guide provides strategies for efficiency.
Continuous Training: Provide ongoing training for warehouse staff on best practices in inventory management and the use of any implemented technologies. Camcode's guide on warehouse training highlights effective strategies.
Adopt Lean Inventory Practices: Minimize waste by keeping stock levels closely aligned with demand. Lean.org’s principles can help in understanding and implementing lean practices.
Utilize Data Analytics: Analyze data from your inventory management system to identify trends, forecast demand, and make informed decisions. IBM's guide on data analytics in inventory management explores the benefits and methods.
Implementing these strategies can significantly improve the efficiency and accuracy of inventory management in a warehouse setting.
How to Display Inventory Management Skills on Your Resume
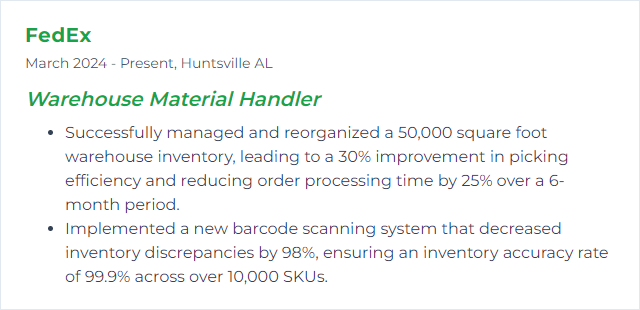
3. Pallet Jack
A pallet jack, in the context of a Warehouse Material Handler, is a tool used for lifting and moving pallets within a warehouse, facilitating the handling of goods and materials.
Why It's Important
A pallet jack is crucial for a Warehouse Material Handler because it efficiently moves heavy loads across the warehouse, enhancing productivity and reducing physical strain.
How to Improve Pallet Jack Skills
To improve the efficiency and safety of using a pallet jack in a warehouse setting, consider the following concise strategies:
Proper Training: Ensure all material handlers receive comprehensive training on pallet jack operation, focusing on safe handling, maneuvering, and load management.
Regular Maintenance: Implement a regular maintenance schedule for inspecting, cleaning, and repairing pallet jacks to prevent breakdowns and enhance performance.
Ergonomic Upgrades: Invest in ergonomic handles and controls to reduce strain on operators, which can be found through suppliers like Raymond Handling.
Use of High-Quality Wheels: Upgrade to high-quality, durable wheels that can handle the warehouse floor conditions better, improving maneuverability and reducing wear. Suppliers like Global Industrial offer a variety of options.
Efficiency Accessories: Add attachments or accessories, such as a skid adapter or a load stabilizer, to enhance the versatility and safety of pallet jack operations.
By focusing on training, maintenance, ergonomics, quality components, and useful accessories, warehouses can significantly improve the performance and safety of their pallet jacks.
How to Display Pallet Jack Skills on Your Resume
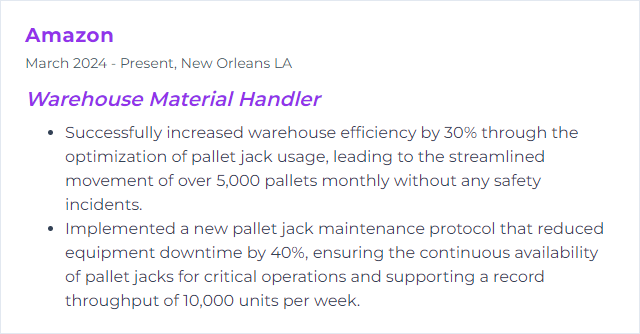
4. RF Scanners
RF scanners, in the context of a Warehouse Material Handler, are handheld electronic devices used to read and transmit data from radio frequency identification (RFID) tags attached to inventory items, enabling quick and accurate tracking, locating, and management of warehouse stock.
Why It's Important
RF scanners are crucial for Warehouse Material Handlers as they streamline inventory management by providing real-time data on stock levels, location, and movement, significantly enhancing accuracy, efficiency, and productivity in managing and tracking materials.
How to Improve RF Scanners Skills
Improving RF scanners for Warehouse Material Handlers involves enhancing their efficiency, accuracy, and user-friendliness. Key strategies include:
Upgrading to Advanced Technology: Opt for scanners with latest RF technology for faster and more reliable scanning. Consider devices that support Bluetooth for flexible connectivity.
Ergonomic Design: Choose scanners designed for comfort and ease of use during long shifts. This reduces fatigue and increases productivity. Zebra Technologies offers ergonomically designed scanners.
Implementing Wearable Scanners: Use wearable scanners to enable hands-free operation, improving efficiency. Honeywell provides wearable scanning solutions suitable for warehouse environments.
Enhancing Software Integration: Ensure your RF scanners are integrated with your Warehouse Management System (WMS) for real-time inventory tracking. Manhattan Associates offers advanced WMS solutions that can integrate with various RF scanners.
Training and Support: Regularly train staff on the optimal use of RF scanners and provide ongoing support to troubleshoot issues quickly.
By focusing on these areas, you can significantly improve the functionality and effectiveness of RF scanners for Warehouse Material Handlers, leading to increased accuracy, efficiency, and worker satisfaction.
How to Display RF Scanners Skills on Your Resume
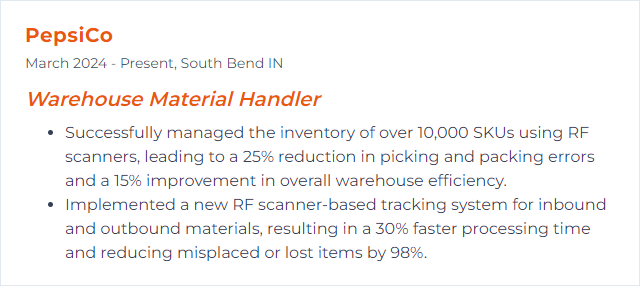
5. Order Picking
Order picking is the process by which a warehouse material handler retrieves items from storage locations to fulfill specific customer orders.
Why It's Important
Order picking is crucial for a warehouse material handler as it directly impacts the speed and accuracy of fulfilling customer orders, ensuring timely delivery and customer satisfaction while optimizing inventory management and reducing operational costs.
How to Improve Order Picking Skills
Improving order picking in a warehouse involves streamlining processes, implementing technology, and optimizing the layout for efficiency. Here are concise strategies:
Layout Optimization: Organize inventory based on demand, placing high-turnover items closer to packing areas to minimize travel time. Warehouse Layout Design
Batch Picking: Group similar orders to minimize trips around the warehouse. This reduces picking time significantly. Batch Picking Strategy
Technology Integration: Use Warehouse Management Systems (WMS) for real-time inventory tracking and order picking guidance. Barcode scanners and RFID technology speed up the picking process and reduce errors. Warehouse Management Systems Guide
Equipment and Tools: Equip pickers with the right tools, such as wearable devices, to increase mobility and efficiency. Consider automated solutions like Automated Guided Vehicles (AGVs) for transporting items. AGVs in Warehousing
Training and Incentives: Continuously train staff on best practices and use incentive programs to increase productivity and accuracy. Effective Warehouse Staff Training
Review and Adapt: Regularly review picking processes for bottlenecks and continuously adapt strategies based on data analytics. Lean Warehousing Principles
Implementing these strategies requires a balance of technology, efficient processes, and human resources management to improve order picking in a warehouse setting.
How to Display Order Picking Skills on Your Resume
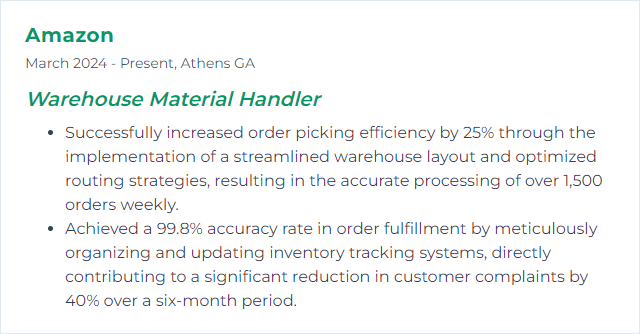
6. Shipping Procedures
Shipping procedures for a Warehouse Material Handler involve carefully selecting, packing, and labeling items for dispatch, ensuring accurate order fulfillment, coordinating with carriers for pickup, and updating inventory and tracking systems to reflect shipments.
Why It's Important
Shipping procedures are crucial for a Warehouse Material Handler as they ensure the accurate, timely, and safe delivery of goods, optimizing warehouse operations, minimizing errors, and enhancing customer satisfaction.
How to Improve Shipping Procedures Skills
Improving shipping procedures, particularly from the perspective of a Warehouse Material Handler, involves streamlining processes, enhancing accuracy, and ensuring safety. Here are concise steps to achieve this:
Automate Processes: Implement Warehouse Management Systems (WMS) to automate tasks such as inventory tracking and order picking, reducing errors and increasing efficiency.
Standardize Packaging: Use uniform packaging standards to improve handling efficiency and reduce damage. Resources like Packaging Guidelines by UPS can provide insights.
Optimize Layout: Design the warehouse layout to minimize the distance for picking and packing operations. The Warehouse Layout Design Guide by Shopify offers valuable tips.
Implement Quality Checks: Incorporate quality control checkpoints at various stages of the shipping process to ensure accuracy and reduce returns. Quality Management Systems (QMS) can help standardize these checks.
Enhance Safety Training: Provide regular safety training and ensure adherence to protocols to prevent accidents. The Occupational Safety and Health Administration (OSHA) offers resources and training programs.
Use Advanced Labeling and Tracking: Implement advanced labeling systems like RFID and barcode scanning for real-time tracking and inventory accuracy. Information on RFID technology can be found on RFID Journal.
Continuous Improvement: Regularly review and update shipping procedures based on feedback and new technologies. Lean methodologies and resources from the Lean Enterprise Institute can guide continuous improvement efforts.
Implementing these strategies can significantly enhance the efficiency and reliability of warehouse shipping procedures.
How to Display Shipping Procedures Skills on Your Resume
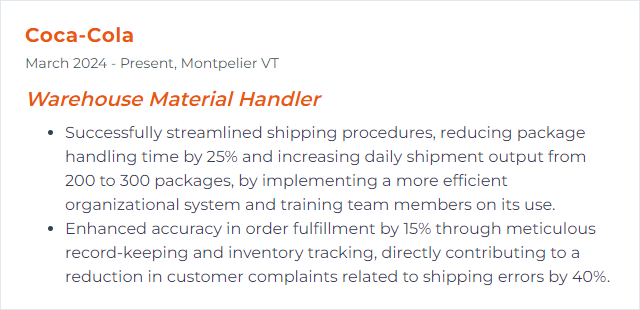
7. Receiving Protocols
Receiving Protocols for a Warehouse Material Handler involve the standardized procedures for accepting, inspecting, documenting, and storing incoming materials or products to ensure they meet quality and order specifications.
Why It's Important
Receiving protocols are crucial for a Warehouse Material Handler because they ensure accuracy in inventory, prevent damage or loss, and facilitate efficient storage and distribution of materials.
How to Improve Receiving Protocols Skills
Improving receiving protocols for a Warehouse Material Handler involves several straightforward steps to enhance efficiency, accuracy, and safety. Here's a very short and concise guide:
Standardize Processes: Create and implement standardized receiving protocols. This includes checklists and procedures for unloading, inspecting, and documenting shipments. OSHA provides guidelines for safe handling practices.
Training: Ensure all material handlers receive regular training on the latest receiving protocols and equipment operation. Resources like MHEDA offer industry-specific training.
Technology Integration: Utilize technology such as Warehouse Management Systems (WMS) to automate and track the receiving process. This improves accuracy and efficiency. Capterra offers a list of software options.
Quality Checks: Implement rigorous quality control checks upon receipt of goods to catch errors or damage early. The American Society for Quality provides resources on quality control standards.
Feedback Loop: Create a feedback loop with suppliers to report any recurring issues with shipments, aiming to prevent future occurrences.
Continuous Improvement: Regularly review and refine receiving protocols based on feedback and changing operational needs. Lean methodologies can be helpful here, with resources available from Lean Enterprise Institute.
Implementing these steps will create a more efficient, accurate, and safe receiving process in a warehouse setting.
How to Display Receiving Protocols Skills on Your Resume
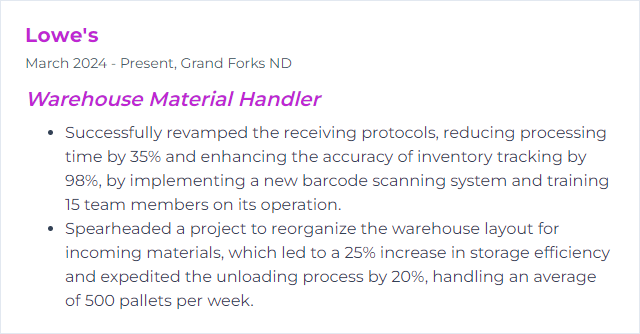
8. Warehouse Management Systems (WMS)
A Warehouse Management System (WMS) is a software solution designed to optimize and manage the operations within a warehouse. For a Warehouse Material Handler, it facilitates tasks such as inventory tracking, picking, receiving, and shipping, aiming to improve efficiency and accuracy in handling materials.
Why It's Important
Warehouse Management Systems (WMS) are crucial as they optimize inventory management, streamline picking and packing processes, and improve accuracy in order fulfillment, directly enhancing a Warehouse Material Handler's efficiency and productivity.
How to Improve Warehouse Management Systems (WMS) Skills
Improving Warehouse Management Systems (WMS) for a Warehouse Material Handler involves several key steps. Focus on the integration of real-time data, automation of manual tasks, customization to fit specific operational needs, and continuous training and support for staff. Here’s a concise guide:
Integrate with Real-Time Data: Ensure your WMS is integrated with real-time tracking systems for inventory and equipment. This improves accuracy and decision-making. Real-Time Data Integration in WMS.
Automate Manual Processes: Implement automation tools within your WMS to streamline tasks such as picking, packing, and sorting. This enhances efficiency and reduces human error. Benefits of Automation in WMS.
Customize and Configure: Tailor the WMS to meet the unique needs of your operations, including the specific roles of material handlers. Customization can optimize workflow and improve user experience. Customizing Your WMS.
Continuous Training and Support: Provide ongoing training and support for material handlers on how to effectively use the WMS. This ensures that the system is used to its full potential. Importance of Training in WMS Implementation.
Leverage Analytics and Reporting: Use the analytics and reporting tools within your WMS to gain insights into operations, identify trends, and make informed decisions to enhance productivity. Analytics in WMS.
By focusing on these areas, a Warehouse Material Handler can significantly contribute to the improvement of Warehouse Management Systems, leading to increased efficiency, accuracy, and productivity in warehouse operations.
How to Display Warehouse Management Systems (WMS) Skills on Your Resume
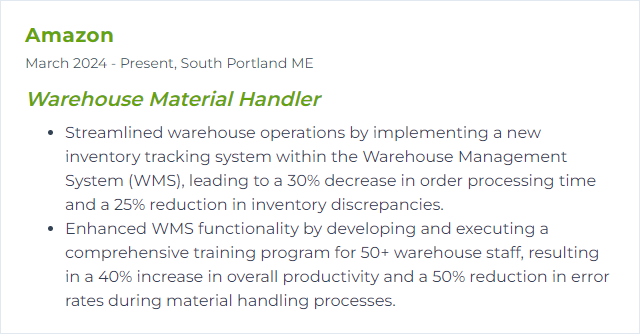
9. Safety Compliance
Safety Compliance for a Warehouse Material Handler involves adhering to established guidelines and regulations designed to prevent accidents and injuries, ensuring a safe working environment by properly handling materials, using equipment correctly, and following safety protocols.
Why It's Important
Safety compliance is crucial for warehouse material handlers to prevent accidents, ensure a safe working environment, protect against legal liabilities, and maintain productivity by minimizing injuries and equipment damage.
How to Improve Safety Compliance Skills
Improving safety compliance for a Warehouse Material Handler involves several key steps. Ensure all employees are thoroughly trained on safety protocols and handling procedures. Regularly conduct risk assessments to identify and mitigate potential hazards. Implement a robust system for reporting and addressing safety concerns. Foster a culture of safety where compliance is prioritized and rewarded. For more detailed guidelines, refer to resources from OSHA on warehouse safety standards and NIOSH for ergonomics best practices to prevent injuries.
How to Display Safety Compliance Skills on Your Resume
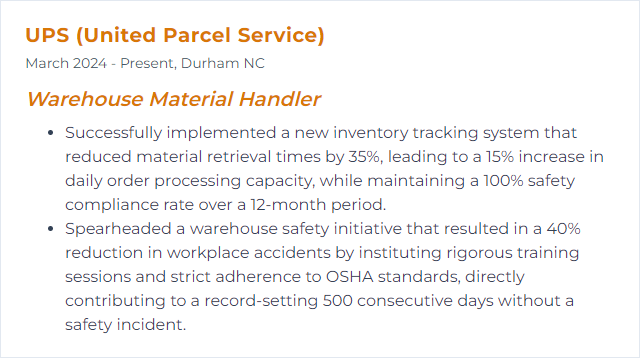
10. Barcode Scanning
Barcode scanning in the context of a Warehouse Material Handler involves using a device to read barcodes on items, which helps in tracking, managing inventory, and ensuring accurate picking, packing, and shipping processes.
Why It's Important
Barcode scanning is crucial for a Warehouse Material Handler as it ensures accurate tracking and management of inventory, speeds up the processing of goods, reduces errors, and enhances overall efficiency in the warehouse operations.
How to Improve Barcode Scanning Skills
Improving barcode scanning in a warehouse environment involves optimizing both technology and processes to ensure efficient and accurate operations. Here are concise strategies:
Upgrade Scanners: Invest in high-quality, durable scanners that are designed for warehouse conditions. Opt for devices with long battery life and high scanning speed. Zebra and Honeywell offer robust options.
Implement Wireless Scanning: Use wireless or Bluetooth-enabled scanners to allow material handlers more flexibility and range of movement. Socket Mobile provides good wireless options.
Enhance Barcode Quality: Ensure labels are high-contrast, undamaged, and placed in easily scannable locations. Consider durable labels for harsh environments. Avery offers a variety of label solutions.
Use 2D Barcodes: Transition to 2D barcodes like QR codes which can store more information and are scannable from any direction, increasing efficiency. QR Code Generator is a useful tool for creating them.
Train Staff: Regularly train material handlers on proper scanning techniques and ergonomics to prevent injuries and increase scanning accuracy. OSHA provides guidelines on ergonomics.
Implement Scanning Software: Use software that can manage and interpret barcode data efficiently, integrating with your Warehouse Management System (WMS) for real-time inventory tracking. Fishbowl Inventory is an example of such software.
Regular Maintenance: Schedule regular maintenance for your scanning equipment to ensure they are in optimal working condition, reducing downtime. Manufacturer websites often have maintenance guidelines.
Environmental Adaptation: Adapt scanning practices to your warehouse environment. In cold storage, use scanners designed for low temperatures. Panasonic Toughbook devices are built for extreme conditions.
By following these strategies, you can significantly improve barcode scanning efficiency and accuracy in your warehouse operations.
How to Display Barcode Scanning Skills on Your Resume
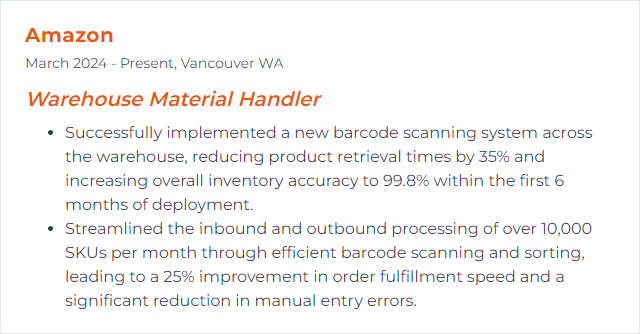
11. Packaging Techniques
Packaging techniques in the context of a Warehouse Material Handler involve the methods and materials used to protect, secure, and prepare goods for storage or shipment. This includes selecting appropriate containers, using padding and fillers, sealing and labeling packages, and ensuring items are packed efficiently and safely to minimize damage and optimize space.
Why It's Important
Packaging techniques are crucial for a Warehouse Material Handler as they ensure the protection of goods, minimize damage during handling and transportation, optimize space utilization, and enhance efficiency in storage and retrieval operations.
How to Improve Packaging Techniques Skills
Improving packaging techniques in a warehouse setting involves optimizing materials, processes, and technologies to enhance efficiency, reduce costs, and ensure product safety. Here are concise strategies:
Evaluate and Optimize Packaging Materials: Choose durable, lightweight, and cost-effective materials to reduce shipping costs and environmental impact. Packaging Digest offers insights on material innovations.
Implement Standardized Processes: Develop and enforce standard operating procedures for packaging to ensure consistency and efficiency. Training resources can be found at Packaging School.
Leverage Automation and Technology: Invest in packaging machinery and technology to increase speed and precision. Technologies like 3D printing for custom packaging solutions are discussed at Packaging World.
Conduct Regular Training: Ensure that material handlers are trained on the latest packaging techniques and technologies. Online courses are available at platforms like LinkedIn Learning.
Optimize Warehouse Layout: Design the warehouse to streamline the flow of materials from storage to packaging to shipping. Material Handling Institute provides resources on warehouse optimization.
Implement Quality Control Measures: Regularly inspect packaging processes and materials to ensure they meet required standards and reduce the risk of damage. Guidelines can be found at ISO for packaging standards.
By focusing on these strategies, warehouse material handlers can significantly enhance their packaging techniques, contributing to overall operational efficiency and customer satisfaction.
How to Display Packaging Techniques Skills on Your Resume
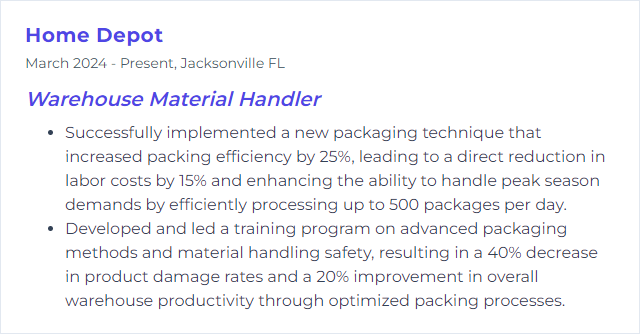
12. Quality Control
Quality Control (QC) for a Warehouse Material Handler involves systematically inspecting and verifying the condition and quantity of items received, stored, and dispatched to ensure they meet the required standards and specifications.
Why It's Important
Quality control is crucial for a Warehouse Material Handler to ensure that materials are handled properly, reducing damage, loss, and errors, ultimately maintaining inventory accuracy and customer satisfaction.
How to Improve Quality Control Skills
To improve Quality Control as a Warehouse Material Handler, consider the following concise strategies:
Implement a Standard Operating Procedure (SOP): Create and follow a standard operating procedure for handling materials to ensure consistency and reduce errors.
Regular Training: Ensure all staff undergo regular training on quality control measures, new protocols, and equipment handling to maintain high standards.
Use of Technology: Incorporate barcode scanning and inventory management software to track and manage stock levels accurately, reducing human error.
Frequent Audits: Conduct regular audits of warehouse operations to identify and rectify potential quality control issues.
Feedback Loop: Establish a system for receiving and acting on feedback from staff and customers to continuously improve processes and quality control measures.
By adhering to these strategies, a Warehouse Material Handler can significantly enhance quality control within their operations.
How to Display Quality Control Skills on Your Resume
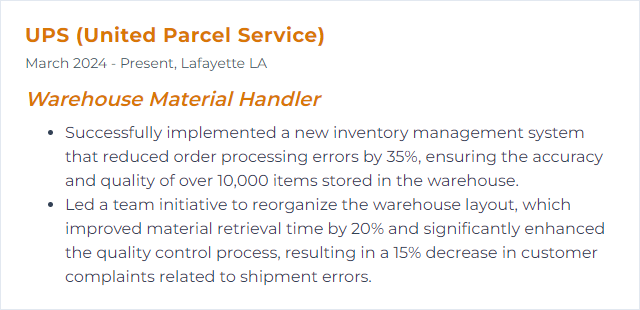