Top 12 Materials Coordinator Skills to Put on Your Resume
In today's competitive job market, showcasing the right set of skills on your resume can significantly enhance your prospects as a materials coordinator. Highlighting a blend of technical proficiency, organizational capabilities, and interpersonal attributes on your resume is crucial to demonstrate your comprehensive expertise and stand out to potential employers.
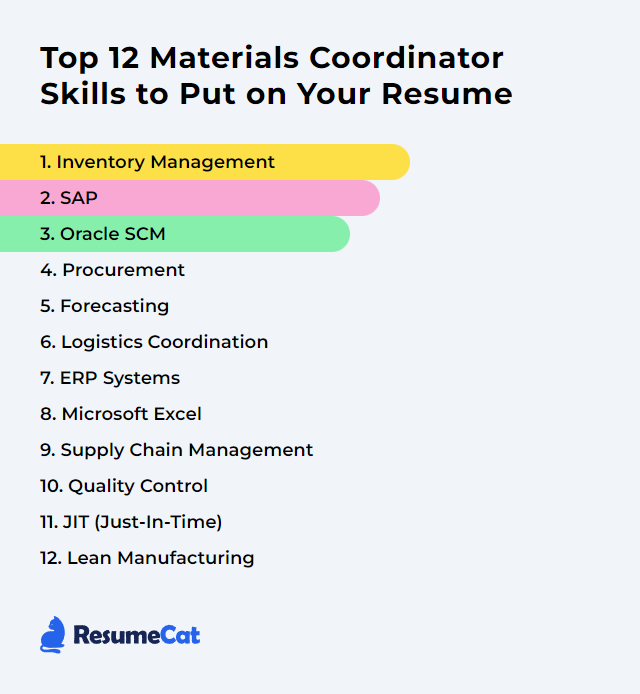
Materials Coordinator Skills
- Inventory Management
- SAP
- Oracle SCM
- Procurement
- Forecasting
- Logistics Coordination
- ERP Systems
- Microsoft Excel
- Supply Chain Management
- Quality Control
- JIT (Just-In-Time)
- Lean Manufacturing
1. Inventory Management
Inventory management is the process of ordering, storing, using, and selling a company's inventory, including the management of raw materials, components, and finished products, as well as warehousing and processing such items. For a Materials Coordinator, it involves overseeing and controlling the order, storage, and distribution of materials required in the production or delivery of goods.
Why It's Important
Inventory management is crucial for a Materials Coordinator as it ensures the right quantity of materials is available when needed, minimizes excess stock and storage costs, and prevents production delays due to material shortages, ultimately supporting efficient and cost-effective operations.
How to Improve Inventory Management Skills
Improving inventory management, especially from the perspective of a Materials Coordinator, involves a combination of strategies focused on accuracy, efficiency, and optimization. Here are concise steps to achieve this:
Implement a Real-time Inventory Tracking System: Utilize technology that allows for real-time tracking of inventory levels. Tools like RFID or barcode scanning can significantly reduce errors and improve visibility.
Adopt Lean Inventory Practices: Embrace principles of lean management to minimize waste and ensure you only stock what's necessary. Learn more about lean inventory practices through resources like the Lean Enterprise Institute.
Regularly Review and Optimize Inventory Levels: Conduct frequent analysis of inventory turnover rates and adjust stocking levels accordingly to prevent overstocking or stockouts. Tools like Inventory Optimization software can aid in these analyses.
Enhance Supplier and Vendor Relationships: Build strong relationships with suppliers for better communication and flexibility. This can lead to more accurate lead times and improved supply chain reliability. The Institute for Supply Management offers resources for enhancing these relationships.
Train Staff on Inventory Management Best Practices: Ensure all team members are knowledgeable about inventory procedures and the importance of accuracy. Resources for training can be found at APICS.
Implement a Continuous Improvement Process: Regularly review inventory processes for potential improvements. Frameworks like Six Sigma can provide a structured approach to continuous improvement.
By focusing on these strategies, a Materials Coordinator can significantly improve inventory management, leading to increased efficiency, reduced costs, and better fulfillment rates.
How to Display Inventory Management Skills on Your Resume
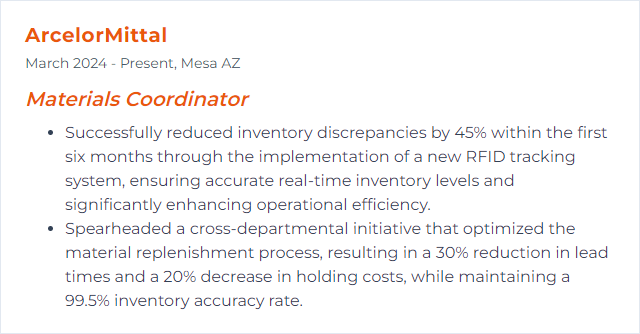
2. SAP
SAP (Systems, Applications, and Products in Data Processing) is a comprehensive enterprise resource planning (ERP) software used for managing business operations and customer relations, including materials management, inventory control, and supply chain processes, essential for a Materials Coordinator's role in organizing and tracking materials.
Why It's Important
SAP is crucial for a Materials Coordinator because it streamlines inventory management, procurement processes, and supply chain operations, ensuring accurate, real-time data for efficient material planning and allocation.
How to Improve SAP Skills
Improving your SAP skills as a Materials Coordinator involves focusing on modules relevant to supply chain and inventory management, understanding SAP's integration capabilities, and continuously updating your knowledge. Here’s a concise guide:
Understand SAP MM (Materials Management) Module: Dive deep into functionalities such as procurement processes, inventory management, and valuation of materials. SAP MM Training can provide foundational and advanced knowledge.
Learn SAP PP (Production Planning) Basics: Gain insights into production processes and how they integrate with material requirements. This knowledge is crucial for coordinating materials effectively. Explore SAP PP User Manuals.
Enhance Skills with SAP SCM (Supply Chain Management): Understand how to optimize, plan, and execute the logistics processes in SAP. Check SAP SCM Learning Journey for courses.
Utilize SAP EWM (Extended Warehouse Management): For advanced warehouse management, learning EWM can significantly improve efficiency in managing materials. Start with SAP EWM Overview.
Stay Updated with SAP S/4HANA Innovations: As SAP’s next-generation ERP, familiarizing yourself with S/4HANA will keep you ahead, particularly in areas related to materials management and logistics.
Join SAP Community & Forums: Engage with other professionals for tips, advice, and latest updates. The SAP Community is a great place to start.
Practice in SAP Sandbox Environment: Apply your learning in a practical environment. Many organizations provide access to SAP sandbox systems for training purposes.
Attend Workshops and Webinars: Participate in official SAP workshops and webinars to gain insights from experts.
By focusing on these areas and continuously learning, you can significantly improve your SAP skills as a Materials Coordinator.
How to Display SAP Skills on Your Resume
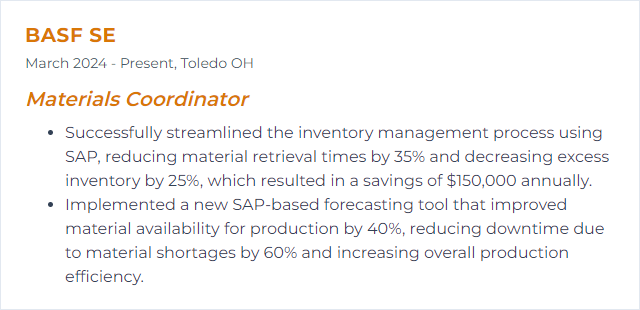
3. Oracle SCM
Oracle SCM (Supply Chain Management) is a comprehensive suite of applications designed to manage and optimize the end-to-end operations of a supply chain, including procurement, production, inventory management, and logistics. For a Materials Coordinator, it offers tools to efficiently track materials, manage inventory levels, and ensure timely procurement and delivery of components necessary for production.
Why It's Important
Oracle SCM (Supply Chain Management) is important for a Materials Coordinator as it offers a comprehensive suite of applications designed to manage and optimize supply chain processes. This includes procurement, inventory management, order fulfillment, and logistics, ensuring materials are available when needed and reducing costs through efficient supply chain operations.
How to Improve Oracle SCM Skills
Improving Oracle SCM, particularly from a Materials Coordinator's perspective, involves a few key strategies aimed at enhancing efficiency, visibility, and collaboration within supply chain processes. Here's a concise guide:
Leverage Oracle SCM Cloud: Transition to or optimize Oracle SCM Cloud for real-time visibility and collaboration across the supply chain. Oracle SCM Cloud provides comprehensive solutions for supply chain management, offering tools for procurement, product lifecycle management, and supply chain planning. Oracle SCM Cloud
Implement Automation: Automate repetitive tasks such as order processing, inventory tracking, and data entry to reduce errors and save time. Oracle SCM supports automation through various tools and integrations that streamline operations. Oracle Process Automation
Enhance Data Accuracy: Ensure data integrity by regularly auditing and cleaning SCM data. Accurate data is crucial for forecasting, planning, and decision-making. Utilize Oracle SCM's analytics and reporting tools to monitor and maintain data quality. Oracle SCM Analytics
Continuous Training: Invest in ongoing training and certification for the SCM team on Oracle SCM updates and best practices. This ensures the team can fully utilize the system's capabilities. Oracle offers a range of training resources and certification programs. Oracle University SCM Training
Integrate Supply Chain Partners: Enhance collaboration with suppliers, manufacturers, and other partners by integrating their systems with Oracle SCM. This facilitates seamless information exchange and improves supply chain responsiveness. Oracle SCM Integration
Utilize Advanced Planning Tools: Use Oracle SCM's advanced planning and forecasting tools to improve materials coordination. These tools help in predicting demand more accurately and planning resource allocation efficiently. Oracle Supply Chain Planning
By focusing on these areas, Materials Coordinators can significantly improve the efficiency and effectiveness of their supply chain operations with Oracle SCM.
How to Display Oracle SCM Skills on Your Resume
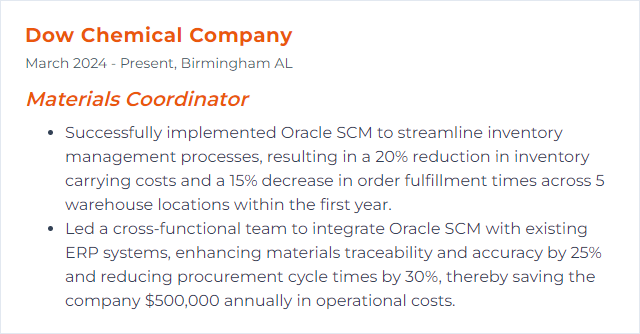
4. Procurement
Procurement is the process of acquiring goods and services necessary for a company's operations, involving selecting suppliers, negotiating contracts, and managing purchases, ensuring materials meet quality standards, are cost-effective, and are delivered on time.
Why It's Important
Procurement is crucial for a Materials Coordinator as it ensures the timely and cost-effective acquisition of quality materials necessary for production, maintaining operational efficiency and supporting the company's profitability and competitiveness.
How to Improve Procurement Skills
Improving procurement, especially from the perspective of a Materials Coordinator, involves streamlining processes, leveraging technology, and building strong relationships with suppliers. Here are concise steps to enhance procurement efficiency:
Automate Processes: Utilize procurement software to automate purchase orders, inventory tracking, and invoice management. SAP Ariba and Coupa offer comprehensive solutions.
Supplier Relationships: Cultivate strong, collaborative relationships with suppliers. This involves clear communication, performance feedback, and joint problem-solving. ISM provides resources on supplier relationship management.
Data-Driven Decisions: Use analytics to make informed procurement decisions. Analyze spend data to identify cost-saving opportunities and optimize inventory. Tableau can help visualize procurement data effectively.
Continuous Training: Stay updated with the latest procurement trends, technologies, and best practices through continuous learning. APICS offers courses relevant to materials coordination and procurement.
Lean Inventory Management: Implement lean inventory techniques like Just-In-Time (JIT) to reduce excess stock and minimize storage costs. This approach requires precise coordination with suppliers. Lean Enterprise Institute has resources on lean thinking and practices.
By focusing on these areas, a Materials Coordinator can significantly improve procurement processes, leading to cost savings, better supplier relationships, and more efficient operations.
How to Display Procurement Skills on Your Resume
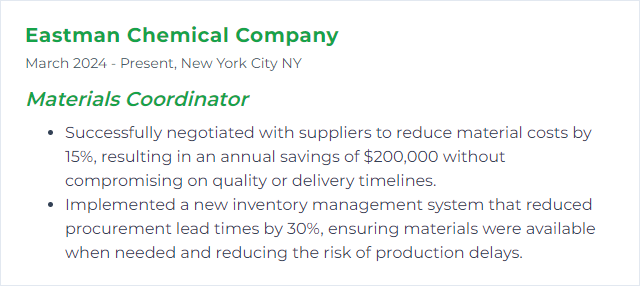
5. Forecasting
Forecasting, in the context of a Materials Coordinator, involves predicting the future demand for materials and supplies to ensure optimal inventory levels, avoiding shortages or excesses, and facilitating smooth production and supply chain operations.
Why It's Important
Forecasting is crucial for a Materials Coordinator as it enables efficient planning and allocation of resources, ensures timely availability of materials, minimizes waste and costs, and supports smooth production and operation processes.
How to Improve Forecasting Skills
Improving forecasting, especially for a Materials Coordinator, involves a mix of accurate data analysis, technology adoption, and continuous improvement. Here's a concise guide:
Leverage Historical Data: Analyze past demand and supply patterns to predict future needs accurately. Tools like Excel can be a good start for simple analyses. Excel Forecasting Functions.
Implement Forecasting Software: Utilize advanced forecasting software that incorporates AI and machine learning for more accurate predictions. Demand Planning Software.
Collaborate with Stakeholders: Work closely with sales, marketing, and suppliers to understand market trends and customer needs. This collaboration can improve forecast accuracy. Collaborative Planning, Forecasting and Replenishment (CPFR).
Continuously Review and Adjust: Regularly compare forecasts against actual demand to identify discrepancies and adjust your forecasting model accordingly. Continuous Improvement in Forecasting.
Educate and Train: Keep yourself and your team updated with the latest trends and tools in forecasting. Continuous learning is key. APICS Certification.
By following these steps and utilizing the resources provided, you can enhance your forecasting abilities, leading to better inventory management and operational efficiency.
How to Display Forecasting Skills on Your Resume
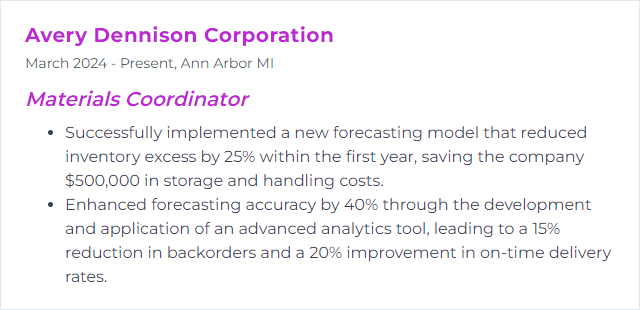
6. Logistics Coordination
Logistics coordination involves managing and overseeing the supply chain process to ensure the efficient and timely movement and delivery of materials. For a Materials Coordinator, it specifically entails organizing, tracking, and facilitating the procurement, storage, and transport of materials to meet project or operational requirements.
Why It's Important
Logistics coordination is crucial for a Materials Coordinator as it ensures the timely and efficient movement and storage of materials. This coordination is essential for meeting project deadlines, maintaining budget control, and ensuring the availability of necessary resources, ultimately supporting the smooth operation of projects and business activities.
How to Improve Logistics Coordination Skills
Improving logistics coordination, especially for a Materials Coordinator, involves enhancing efficiency, communication, and adaptability in managing and moving materials from suppliers to the destination. Here are concise strategies:
Implement Technology: Use logistics management software for real-time tracking and inventory management. Logistics software can streamline operations and improve accuracy.
Optimize Inventory: Adopt Just-In-Time (JIT) inventory management to reduce storage costs and increase turnover rates, ensuring materials are available when needed.
Improve Supplier Relationships: Develop strong, collaborative relationships with suppliers. Supplier relationship management is key to timely and reliable materials delivery.
Enhance Communication: Utilize collaborative tools and platforms for efficient communication among team members and with suppliers. Slack or Trello can facilitate seamless coordination.
Continuous Training: Regularly train staff on new technologies, processes, and best practices. LinkedIn Learning offers courses relevant to logistics and supply chain management.
By focusing on these areas, a Materials Coordinator can significantly improve logistics coordination, leading to more efficient, cost-effective, and reliable operations.
How to Display Logistics Coordination Skills on Your Resume
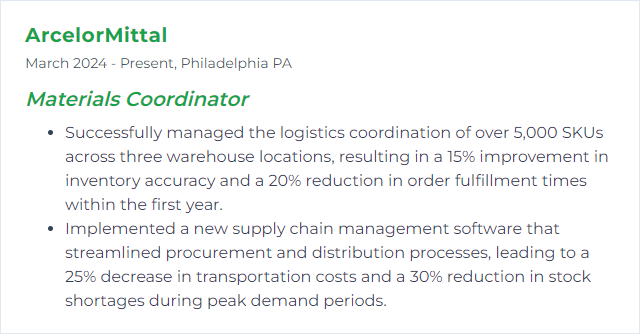
7. ERP Systems
ERP (Enterprise Resource Planning) systems are integrated software platforms that manage and automate core business processes, including supply chain, inventory, procurement, and production planning. For a Materials Coordinator, ERP systems facilitate real-time tracking, ordering, and management of materials and resources, ensuring efficient workflow and operations.
Why It's Important
ERP systems are crucial for a Materials Coordinator as they integrate and automate core business processes, ensuring efficient inventory management, procurement scheduling, and supply chain operations, leading to timely material availability and reduced costs.
How to Improve ERP Systems Skills
Improving ERP systems, especially from the perspective of a Materials Coordinator, involves enhancing data accuracy, streamlining processes, and integrating advanced functionalities. Here are concise strategies:
Data Accuracy: Ensure real-time data accuracy by implementing automatic data capture technologies like barcode scanning and RFID. This reduces manual entry errors and improves inventory management. Zebra Technologies offers solutions in this area.
Process Streamlining: Adopt lean management principles within the ERP to minimize waste and optimize workflows. Tools like Kanban boards can be integrated for better visualization and management of materials.
Advanced Forecasting: Implement advanced forecasting tools that utilize AI and machine learning to predict demand more accurately, aiding in better planning and stock management. SAP Integrated Business Planning is a good example.
Supplier Integration: Enhance supply chain collaboration by integrating ERP systems with suppliers for seamless information exchange, leading to improved lead times and inventory levels. Oracle Supply Chain Collaboration Cloud provides functionalities for this purpose.
Continuous Training: Offer continuous training and support for ERP users to ensure they can leverage all functionalities effectively, reducing errors and improving efficiency. Online platforms like Udemy have courses on various ERP systems.
Mobile Accessibility: Improve accessibility by adopting ERP solutions that offer mobile access, enabling materials coordinators to manage tasks and access information on-the-go. Microsoft Dynamics 365 has mobile capabilities for this need.
Implementing these strategies can significantly improve the effectiveness of ERP systems for materials coordinators and the broader organization.
How to Display ERP Systems Skills on Your Resume
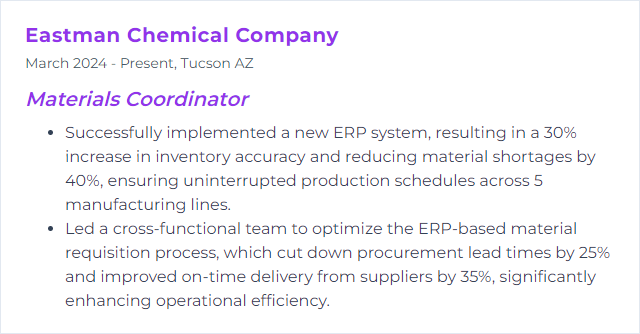
8. Microsoft Excel
Microsoft Excel is a spreadsheet software used for organizing, analyzing, and storing data, essential for a Materials Coordinator in managing inventory, tracking shipments, and forecasting supply needs.
Why It's Important
Microsoft Excel is important for a Materials Coordinator because it enables efficient organization, tracking, and analysis of inventory data, facilitating accurate materials planning, ordering, and allocation.
How to Improve Microsoft Excel Skills
To improve Microsoft Excel skills for a Materials Coordinator, focus on mastering these key areas:
Advanced Formulas: Understand complex formulas for inventory tracking and forecasting. Resource: ExcelJet Advanced Formulas Guide.
PivotTables: Learn to summarize large data sets for analysis. Tutorial: Microsoft PivotTable Guide.
Data Validation: Ensure data integrity by using Excel’s data validation features. How-to: Excel Data Validation.
VBA Macros: Automate repetitive tasks with VBA scripting. Starter: Excel Easy VBA Tutorial.
Conditional Formatting: Highlight critical inventory levels or deadlines. Guide: Conditional Formatting in Excel.
Power Query: Import and transform data from various sources. Overview: Getting Started with Power Query.
By enhancing these Excel skills, a Materials Coordinator can significantly improve efficiency, accuracy, and decision-making capabilities.
How to Display Microsoft Excel Skills on Your Resume

9. Supply Chain Management
Supply Chain Management (SCM) is the oversight of materials, information, and finances as they move from supplier to manufacturer to wholesaler to retailer to consumer. For a Materials Coordinator, SCM involves coordinating and managing the procurement, handling, scheduling, and delivery of materials required to meet production targets efficiently and cost-effectively.
Why It's Important
Supply Chain Management is crucial for a Materials Coordinator because it ensures the efficient and timely procurement and delivery of materials, minimizing costs and maximizing production efficiency. This enables the organization to meet customer demands effectively and maintain competitive advantage.
How to Improve Supply Chain Management Skills
Improving Supply Chain Management, especially from a Materials Coordinator's perspective, involves enhancing the efficiency and reliability of the supply chain through strategic planning, technology integration, and collaboration. Here are concise steps with relevant resources:
Streamline Processes: Optimize inventory management and streamline procurement processes to ensure timely delivery and reduce bottlenecks. APICS offers guidelines and courses that can be beneficial.
Leverage Technology: Implement supply chain management software for real-time tracking and automation. Tools like SAP SCM provide comprehensive solutions for managing complex supply chains.
Enhance Collaboration: Improve relationships with suppliers through regular communication and collaborative planning. The Institute for Supply Management provides resources for building effective supplier relationships.
Continuous Improvement: Adopt lean management principles and practices to continuously improve supply chain operations. Lean Enterprise Institute offers insights and tools for lean management.
Risk Management: Develop strategies to mitigate risks related to supply chain disruptions. The Supply Chain Risk Management Consortium has resources and tools for risk assessment and management.
Sustainability Practices: Integrate sustainable practices into the supply chain to meet regulatory requirements and customer expectations. The Sustainability Consortium offers guidance on sustainability in supply chains.
By focusing on these areas, a Materials Coordinator can significantly improve the efficiency and resilience of their supply chain operations.
How to Display Supply Chain Management Skills on Your Resume
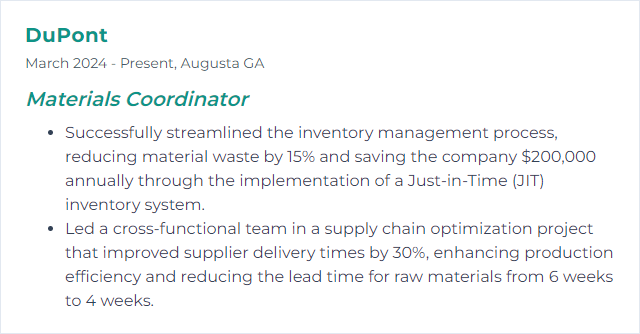
10. Quality Control
Quality Control (QC) involves the processes and procedures used to ensure that a product's quality meets the specified requirements. For a Materials Coordinator, QC focuses on overseeing the quality of materials received, stored, and dispatched, ensuring they meet the standards and specifications required for production or delivery.
Why It's Important
Quality Control is crucial for a Materials Coordinator as it ensures the materials meet required standards and specifications, minimizing waste, reducing costs, and enhancing the final product's reliability and safety.
How to Improve Quality Control Skills
Improving Quality Control, especially from the perspective of a Materials Coordinator, involves a strategic approach focused on enhancing the accuracy, reliability, and efficiency of materials handling and usage. Here are concise steps to achieve this:
Implement Standard Operating Procedures (SOPs): Develop and enforce SOPs for all materials-related activities to ensure consistency and minimize errors. ISO's guidelines can serve as a reference for establishing quality standards.
Supplier Quality Management: Collaborate closely with suppliers to ensure materials meet your quality standards. Utilizing tools like Supplier Scorecards can help monitor and evaluate supplier performance.
Regular Training: Conduct regular training sessions for staff on quality control practices and the importance of maintaining high standards. OSHA’s Training Guidelines offer a framework for developing effective training programs.
Continuous Improvement: Adopt a Kaizen or continuous improvement approach to regularly assess and enhance quality control processes. Lean methodologies can be particularly effective, as detailed by the Lean Enterprise Institute.
Utilize Technology: Implement technology solutions like Material Requirements Planning (MRP) systems or Quality Management Systems (QMS) to automate and improve accuracy in ordering, tracking, and managing materials. ASQ’s Quality Resources provide insights into selecting and implementing QMS.
Conduct Audits: Schedule regular internal and external audits to ensure compliance with SOPs and identify areas for improvement. Audit Guidelines by ISO offer a comprehensive approach to conducting effective audits.
Feedback Mechanism: Establish a robust feedback mechanism to learn from defects or issues and implement corrective actions promptly.
By focusing on these steps, a Materials Coordinator can significantly contribute to enhancing the quality control processes within their organization, leading to better efficiency, reduced waste, and higher customer satisfaction.
How to Display Quality Control Skills on Your Resume
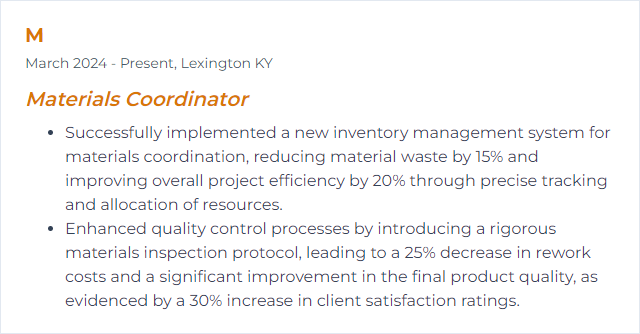
11. JIT (Just-In-Time)
JIT (Just-In-Time) is a supply chain management strategy aimed at reducing inventory costs by receiving materials only as they are needed in the production process, enhancing efficiency and minimizing waste. For a Materials Coordinator, JIT involves precise scheduling and coordination to ensure materials arrive exactly when required, avoiding excess stock and shortages.
Why It's Important
JIT (Just-In-Time) is important because it ensures the timely arrival of materials, minimizes inventory costs, reduces storage space requirements, and enhances production efficiency, directly supporting a Materials Coordinator in optimizing inventory management and meeting production schedules.
How to Improve JIT (Just-In-Time) Skills
Improving JIT (Just-In-Time) as a Materials Coordinator involves streamlining the supply chain, enhancing communication, and implementing real-time monitoring. Here's a concise guide:
Optimize Inventory Management: Use tools like Kanban to maintain minimal inventory levels without disrupting production.
Strengthen Supplier Relationships: Foster strong, reliable partnerships with suppliers. Implement a Vendor Managed Inventory (VMI) system for better collaboration and efficiency.
Leverage Technology: Adopt ERP systems for real-time tracking of materials and demand forecasting. This helps in timely decision-making and reducing lead times.
Continuous Improvement: Implement Lean Manufacturing principles to continuously identify and eliminate waste in the supply chain, improving overall efficiency.
Employee Training: Ensure all team members are trained in JIT practices and tools. APICS certification can be a valuable asset for a Materials Coordinator.
By focusing on these areas, a Materials Coordinator can significantly contribute to the effectiveness of JIT in their organization.
How to Display JIT (Just-In-Time) Skills on Your Resume
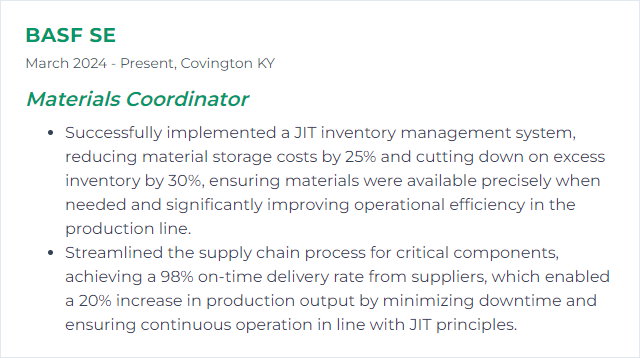
12. Lean Manufacturing
Lean Manufacturing is a systematic approach to minimizing waste within manufacturing systems while maximizing productivity, primarily focusing on enhancing value for the customer. For a Materials Coordinator, it involves ensuring materials are provided efficiently and as needed, reducing excess inventory and ensuring smooth production flow.
Why It's Important
Lean Manufacturing is important for a Materials Coordinator because it streamlines production processes, reduces waste, and ensures efficient use of resources, leading to cost savings, improved product quality, and faster delivery times. This enhances inventory management and ensures that materials are available when needed, supporting smooth operations and customer satisfaction.
How to Improve Lean Manufacturing Skills
Improving Lean Manufacturing, particularly from a Materials Coordinator's perspective, involves optimizing inventory management, streamlining supply chain processes, and enhancing collaboration with suppliers. Here are concise strategies:
Implement Just-In-Time (JIT) Inventory: Reduce waste by receiving goods only as they are needed in the production process. Learn more about JIT.
Adopt Kanban Systems: Utilize visual cues to signal when to reorder supplies, ensuring materials are replenished efficiently. Kanban Explained.
Enhance Supplier Relationships: Develop strong partnerships with suppliers for better reliability and quality of materials. Supplier Relationship Management.
Conduct Value Stream Mapping: Identify and eliminate waste in the supply chain by analyzing and optimizing material and information flow. Value Stream Mapping Guide.
Embrace Continuous Improvement (Kaizen): Foster a culture of ongoing, incremental improvements in every aspect of materials coordination. Introduction to Kaizen.
Leverage Technology for Better Inventory Management: Utilize ERP and MRP systems for real-time inventory tracking and demand forecasting. Understanding ERP.
Implementing these strategies can significantly enhance the efficiency of materials coordination in a lean manufacturing environment.
How to Display Lean Manufacturing Skills on Your Resume
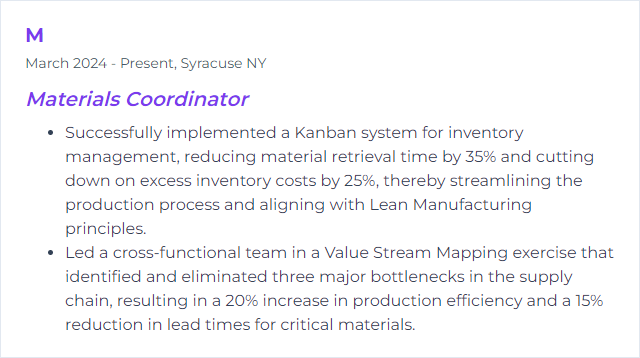