Top 12 Materials Planner Skills to Put on Your Resume
In the intricate world of supply chain and production, a Materials Planner plays a pivotal role in ensuring the seamless flow of materials essential for manufacturing processes. Highlighting a robust set of skills on your resume can significantly elevate your appeal to potential employers, showcasing your capability to effectively manage resources, predict demands, and contribute to the efficient operation of the production cycle.
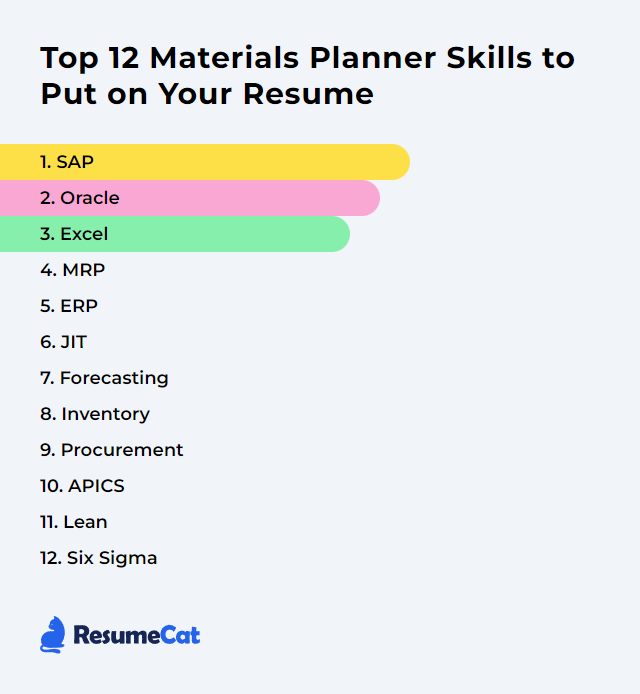
Materials Planner Skills
1. SAP
SAP (Systems, Applications, and Products in Data Processing) is an enterprise resource planning (ERP) software used by materials planners to manage and monitor the entire supply chain process, including procurement, inventory, production planning, and distribution, ensuring efficient and coordinated operations.
Why It's Important
SAP is important for a Materials Planner because it provides real-time data integration and automation across supply chain processes, enabling efficient inventory management, accurate demand forecasting, and optimized production planning.
How to Improve SAP Skills
Improving SAP performance for a Materials Planner involves optimizing system settings, streamlining processes, and leveraging SAP's advanced features. Here’s a concise guide:
Enhance System Performance: Regularly review and adjust SAP system parameters to ensure optimal performance. Consider SAP's recommendations for system administration.
Data Accuracy and Integrity: Maintain high data quality in material master records, BOMs, and inventory levels. SAP's Master Data Governance can help standardize and streamline data management.
Process Optimization: Utilize SAP's MRP (Material Requirements Planning) more effectively by customizing MRP parameters to match your specific planning needs. Learn about MRP configuration.
Training and Knowledge Sharing: Enhance skills in SAP's advanced planning tools through official SAP training courses. Explore SAP Learning Hub for materials planning and SCM (Supply Chain Management) modules.
Leverage Advanced Features: Utilize advanced SAP tools like APO (Advanced Planning and Optimization) or the more recent SAP IBP (Integrated Business Planning) for sophisticated planning capabilities. Discover more on SAP IBP.
Custom Reports and Analytics: Develop custom reports that match your specific needs for more insightful analytics and decision-making. SAP's Business Intelligence can provide powerful reporting tools.
Automation and AI: Implement SAP's AI and machine learning features to automate routine tasks and gain predictive insights, improving efficiency. Explore possibilities with SAP AI Business Services.
Feedback Loop: Establish a feedback loop with users to continuously improve SAP usage and address challenges promptly. Engage with the SAP community for shared solutions and tips at SAP Community.
By focusing on these areas, a Materials Planner can significantly improve their SAP system's effectiveness, leading to more efficient planning, reduced costs, and better decision-making.
How to Display SAP Skills on Your Resume
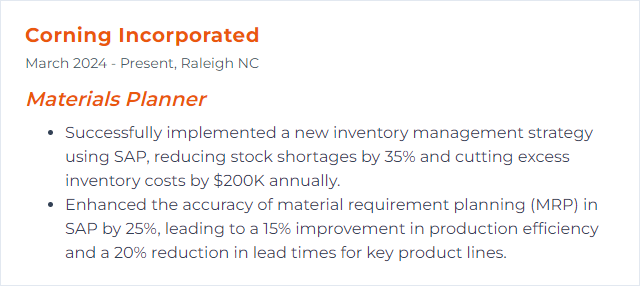
2. Oracle
Oracle is a comprehensive software system that provides solutions for enterprise resource planning (ERP), including materials planning and supply chain management, to optimize inventory levels, forecast demand, and improve production planning processes.
Why It's Important
Oracle is crucial for a Materials Planner because it provides advanced tools for demand forecasting, inventory management, and supply chain planning, enabling efficient materials planning and optimized resource allocation.
How to Improve Oracle Skills
Improving Oracle for a Materials Planner involves enhancing data accuracy, integrating advanced planning tools, and streamlining processes. Here's a concise guide:
Data Accuracy: Ensure all material data in Oracle is accurate and up-to-date. Implement regular audits and validations. Oracle Data Quality offers solutions for maintaining high-quality data.
Advanced Planning Tools: Utilize Oracle's Advanced Supply Chain Planning (ASCP) to optimize planning and scheduling. It provides a comprehensive overview and detailed insights for better decision-making. Oracle ASCP for more details.
Streamline Processes: Automate routine tasks using Oracle's automation features. This reduces manual errors and frees up time for strategic planning. Oracle Process Automation can guide you through automation capabilities.
Training and Skills Development: Continually upgrade your skills and knowledge of Oracle's features and best practices. Oracle University offers courses specifically designed for materials planners. Oracle University for training options.
Collaboration Tools Integration: Integrate Oracle with external collaboration tools to improve communication with suppliers and stakeholders. This ensures everyone is on the same page and can react quickly to changes. Explore Oracle's Cloud Marketplace for compatible tools.
By focusing on these areas, a Materials Planner can significantly improve the effectiveness of Oracle in managing materials and planning processes.
How to Display Oracle Skills on Your Resume
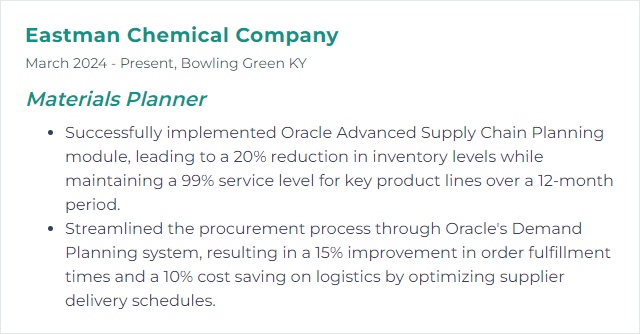
3. Excel
Excel is a spreadsheet software developed by Microsoft, widely used for organizing, analyzing, and storing data in tabular form, essential for materials planners for inventory tracking, demand forecasting, and order scheduling.
Why It's Important
Excel is crucial for a Materials Planner for efficient inventory tracking, demand forecasting, data analysis, and report generation, enabling optimized production planning and supply chain management.
How to Improve Excel Skills
To improve Excel skills for a Materials Planner, focus on the following concise strategies:
Master Key Formulas: Become proficient in formulas critical for materials planning, such as VLOOKUP, INDEX(MATCH), and SUMIFS. ExcelJet offers clear examples.
Leverage Pivot Tables: Enhance your data analysis capabilities for inventory management through pivot tables. Microsoft Support has tutorials.
Use Conditional Formatting: Improve data visualization for better decision-making by using conditional formatting. Ablebits provides practical guides.
Incorporate Data Validation: Ensure data integrity in your planning sheets by using data validation techniques. Contextures offers easy-to-follow instructions.
Automate with Macros: Save time on repetitive tasks by learning to record and write simple VBA macros. Excel Easy introduces VBA in an accessible manner.
Explore Power Query: Import and transform data from various sources efficiently with Power Query. Excel Campus has comprehensive guides.
Continuous Learning: Stay updated with the latest Excel features and tips through platforms like LinkedIn Learning and Udemy.
By focusing on these areas, you can significantly enhance your Excel skills as a Materials Planner, leading to more efficient and effective planning processes.
How to Display Excel Skills on Your Resume
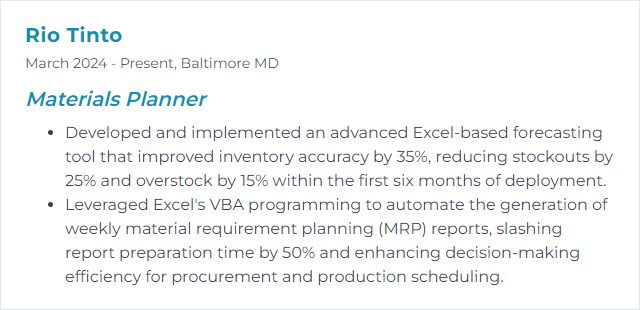
4. MRP
MRP, or Material Requirements Planning, is a system used by materials planners to manage inventory, plan production, and schedule procurement by forecasting the materials and components needed to manufacture products, ensuring that materials are available for production and products are available for delivery to customers on time.
Why It's Important
MRP (Material Requirements Planning) is crucial for a Materials Planner because it ensures optimal inventory levels, minimizes waste, and improves production efficiency by accurately forecasting material needs and scheduling procurement accordingly.
How to Improve MRP Skills
Improving Material Requirements Planning (MRP) involves enhancing accuracy, efficiency, and responsiveness in managing materials in manufacturing. For a Materials Planner, consider these concise strategies:
Data Accuracy: Ensure all data inputs (BOMs, inventory records, lead times) are accurate and up-to-date. Inaccurate data can lead to incorrect material orders. MRP Data Management
Demand Forecasting: Collaborate with the sales team to improve demand forecasting. Accurate forecasts lead to better planning. Demand Forecasting Strategies
Supplier Relationships: Develop strong relationships with suppliers to ensure reliable lead times and flexibility. This is crucial for adjusting plans based on changing demands. Supplier Relationship Management
Continuous Improvement: Implement a continuous improvement process to regularly review and optimize MRP performance. This includes using feedback loops and KPIs to identify and act on areas for improvement. Lean Manufacturing Principles
MRP Software Utilization: Leverage advanced MRP software that offers real-time analytics, automation, and integration capabilities. This enhances decision-making and operational efficiency. Choosing MRP Software
Education and Training: Invest in ongoing education and training for the planning team to ensure they are proficient in using MRP systems and understanding best practices. APICS Certification
Inventory Optimization: Balance inventory levels to avoid excess stock and shortages. Use techniques like safety stock calculation and ABC analysis for effective inventory management. Inventory Optimization Techniques
Implementing these strategies effectively requires a blend of technology, processes, and people. Continuous monitoring and adaptation to changes in demand, supply, and internal processes will help in maintaining an efficient MRP system.
How to Display MRP Skills on Your Resume
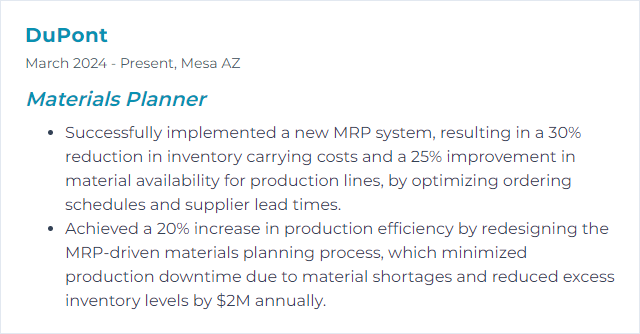
5. ERP
ERP (Enterprise Resource Planning) is a software system that integrates and manages core business processes, such as inventory and order management, to optimize resources and streamline operations for materials planning and overall organizational efficiency.
Why It's Important
ERP (Enterprise Resource Planning) is crucial for a Materials Planner as it integrates all facets of an operation, including supply chain, procurement, and inventory management, enabling real-time visibility, improved forecasting, and efficient resource allocation. This ensures materials are available when needed, reducing waste and optimizing production schedules.
How to Improve ERP Skills
To improve ERP for a Materials Planner, focus on these key areas:
Data Accuracy: Ensure all material data in the ERP system is accurate and up-to-date. This includes specifications, lead times, and supplier information. Data Accuracy Importance
Integration: Integrate ERP with other systems (e.g., SCM, CRM) for seamless information flow. This enhances visibility and decision-making. ERP Integration Guide
Training: Invest in comprehensive training for users to leverage the ERP system's full potential, focusing on materials management functionalities. ERP Training Benefits
Customization: Tailor the ERP system to fit the unique needs of materials planning, such as custom reports or alerts for inventory levels. ERP Customization vs. Standardization
Process Optimization: Continuously review and optimize materials planning processes within the ERP system to improve efficiency and reduce waste. Process Optimization Steps
By focusing on these areas, a Materials Planner can significantly enhance the effectiveness of an ERP system.
How to Display ERP Skills on Your Resume
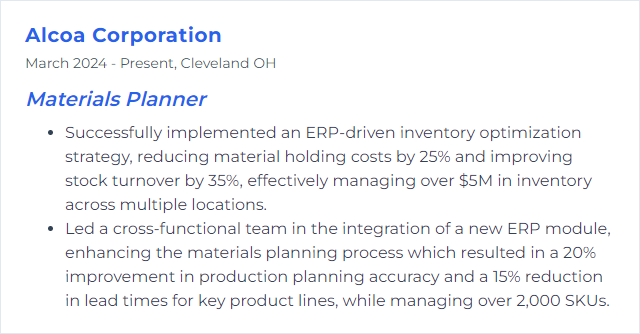
6. JIT
JIT, or Just-In-Time, is a supply chain management strategy aimed at reducing inventory costs by receiving goods only as they are needed in the production process, thereby minimizing inventory levels and reducing waste. For a Materials Planner, JIT involves precise planning and coordination with suppliers to ensure timely delivery of materials, aligning with production schedules without maintaining large stockpiles.
Why It's Important
JIT, or Just-In-Time, is crucial for a Materials Planner as it streamlines inventory management, reduces storage costs, and ensures materials are available precisely when needed, thus enhancing efficiency and reducing waste.
How to Improve JIT Skills
Improving JIT (Just-In-Time) in the context of a Materials Planner involves optimizing inventory levels, enhancing supplier relationships, and streamlining production schedules. Here are concise steps with relevant external links for deeper insights:
Demand Forecasting: Improve accuracy with advanced analytics tools. IBM's guide on demand forecasting offers insights into leveraging data for better predictions.
Supplier Collaboration: Foster strong, transparent relationships with suppliers for reliable, timely deliveries. APICS's guide (search for supplier collaboration) discusses strategies for effective collaboration.
Inventory Management: Adopt lean inventory techniques to minimize waste and storage costs. The Lean Enterprise Institute provides resources on implementing lean principles.
Process Automation: Use ERP and SCM software for real-time tracking and automated ordering. Oracle's ERP guide and SAP SCM highlight how technology can streamline operations.
Continuous Improvement: Implement Kaizen and other continuous improvement methodologies to enhance every aspect of JIT. The Kaizen Institute offers resources on continuous improvement practices.
By focusing on these areas, a Materials Planner can significantly improve the efficiency and responsiveness of JIT systems.
How to Display JIT Skills on Your Resume
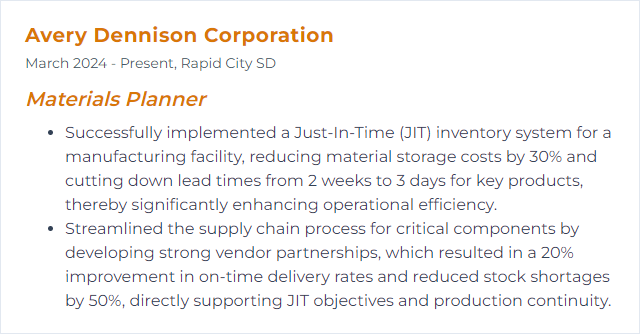
7. Forecasting
Forecasting, in the context of a Materials Planner, is the process of predicting future demand for materials based on historical data, current market trends, and other influencing factors to ensure optimal inventory levels and meet production requirements efficiently.
Why It's Important
Forecasting is crucial for a Materials Planner as it helps in predicting future demand, ensuring optimal inventory levels, reducing excess stock, minimizing shortages, and improving overall supply chain efficiency. This leads to cost savings and better customer satisfaction.
How to Improve Forecasting Skills
Improving forecasting, especially for a Materials Planner, involves a combination of accurate data collection, utilization of advanced forecasting tools, and continuous process evaluation. Here are concise steps to enhance forecasting accuracy:
Data Accuracy: Ensure the data used for forecasting is accurate and up-to-date. This involves regular audits of inventory levels, lead times, and sales data.
Use Advanced Tools: Implement advanced forecasting tools and software that incorporate artificial intelligence (AI) and machine learning (ML) to predict demand more accurately. Forecast Pro and SAP Integrated Business Planning are examples.
Collaborative Planning: Engage in collaborative planning with suppliers and customers to improve forecast accuracy by sharing data and insights. Tools like Kinaxis RapidResponse facilitate such collaboration.
Continuous Improvement: Regularly review forecasting performance and adjust processes and models based on feedback and new data. Utilize methodologies like Six Sigma to reduce errors and improve efficiency.
Training and Development: Continuously train staff on new tools, technologies, and methods in forecasting. This ensures that your team's skills remain sharp and relevant.
By focusing on these areas, Materials Planners can significantly enhance their forecasting capabilities, leading to improved inventory management, reduced costs, and better customer satisfaction.
How to Display Forecasting Skills on Your Resume
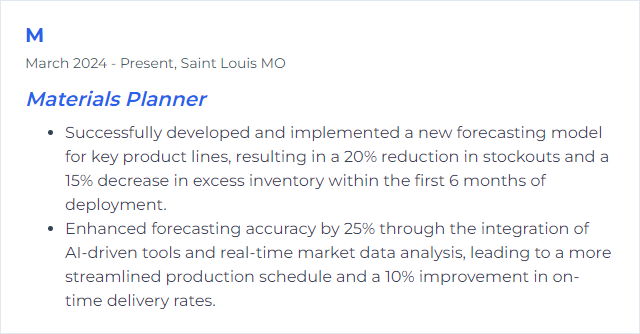
8. Inventory
Inventory refers to the stock of raw materials, work-in-progress, and finished goods that a company holds to support production, sales, and service activities. For a Materials Planner, it is essential for ensuring uninterrupted production and meeting customer demand efficiently.
Why It's Important
Inventory is crucial for a Materials Planner as it ensures the right materials are available in the correct quantities at the right time to meet production schedules, minimizing downtime and maximizing efficiency.
How to Improve Inventory Skills
Improving inventory management, particularly from a Materials Planner perspective, involves optimizing stock levels to meet production demands while minimizing costs. Here are concise steps with relevant resources:
Forecast Demand Accurately: Use historical data and market analysis to predict future needs. Tools like Demand Forecasting can aid in this process.
Implement an Inventory Management System: Use software that offers real-time tracking and analysis. Solutions like Oracle NetSuite can streamline operations.
Adopt Just-In-Time (JIT) Inventory: Reduce waste by receiving goods only as needed for production. Learn more about JIT at The Balance Small Business.
Regular Audits: Conduct regular physical counts to verify stock levels. This guide on Inventory Audits explains the process in detail.
Supplier Relationship Management: Foster good relationships with suppliers for better terms and reliability. Insights can be found at CIPS.
Improve Forecast Accuracy: Utilize advanced forecasting methods and tools. Forecast Pro is a specialized tool for improving forecast accuracy.
Lean Inventory Management: Embrace lean principles to minimize waste and increase efficiency. An introduction is available at Planview.
Safety Stock Calculation: Maintain optimal safety stock levels to buffer against demand variability. Investopedia offers a basic understanding of safety stock.
By following these steps and leveraging the provided resources, a Materials Planner can significantly improve inventory management, leading to increased efficiency and reduced costs.
How to Display Inventory Skills on Your Resume
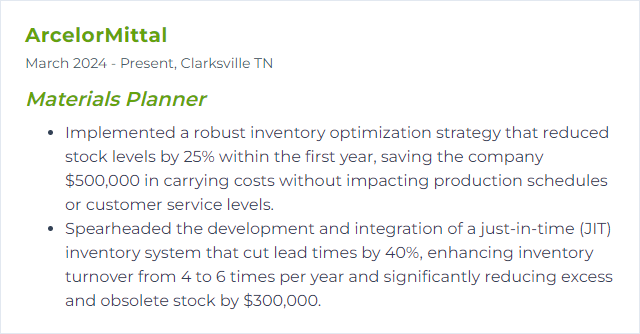
9. Procurement
Procurement, in the context of a Materials Planner, refers to the process of sourcing, negotiating, and purchasing goods and services needed to produce products, ensuring the right quality, quantity, timing, and cost.
Why It's Important
Procurement is crucial for a Materials Planner as it ensures the timely and cost-effective acquisition of the necessary high-quality materials, enabling efficient production, meeting customer demands, and maintaining competitive advantage.
How to Improve Procurement Skills
Improving procurement, especially from the perspective of a Materials Planner, involves enhancing efficiency, reducing costs, and ensuring the timely availability of materials. Here are concise strategies:
Supplier Relationship Management (SRM): Develop strong relationships with suppliers to improve communication, negotiate better terms, and ensure reliable supply. Institute for Supply Management
Demand Forecasting: Use advanced tools and techniques for accurate demand forecasting to avoid overstocking or stockouts. APICS
Process Automation: Implement procurement software for automating routine tasks, reducing errors, and speeding up the procurement cycle. Gartner
Strategic Sourcing: Identify and evaluate suppliers to find the best match for quality, cost, and delivery performance. CIPS
Inventory Management: Adopt just-in-time (JIT) inventory practices to minimize holding costs and reduce waste. Lean Enterprise Institute
Continuous Improvement: Regularly review procurement processes and supplier performance for ongoing optimization. American Society for Quality
Incorporating these strategies can lead to more efficient, cost-effective procurement processes that support the overall goals of the organization.
How to Display Procurement Skills on Your Resume
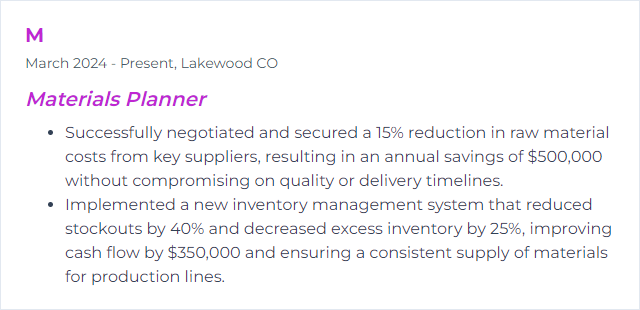
10. APICS
APICS, now part of the Association for Supply Chain Management (ASCM), is a professional association for supply chain management and logistics professionals. It offers education, certification (like CPIM, CSCP), and career development resources to individuals involved in materials planning, production, inventory management, and the broader fields of supply chain and logistics.
Why It's Important
APICS, now known as the Association for Supply Chain Management (ASCM), is important for a Materials Planner because it provides essential education, certification (e.g., CPIM), and industry standards, enhancing their ability to manage inventory, plan material requirements, and optimize supply chain efficiency effectively.
How to Improve APICS Skills
Improving your APICS knowledge and skills as a Materials Planner involves continuous learning and practical application. Here are concise strategies:
Enroll in APICS Certification Programs: Focus on CPIM (Certified in Production and Inventory Management) or CSCP (Certified Supply Chain Professional) for in-depth knowledge in materials and supply chain management.
Utilize APICS Resources: Access APICS's resources including webinars, articles, and tools for ongoing learning.
Join APICS Community: Engage with the APICS community for networking, mentorship, and sharing best practices.
Practical Application: Implement your learning in real-world scenarios at work to reinforce concepts and improve efficiency.
Stay Updated: Keep abreast of the latest trends and updates in materials planning and supply chain management through APICS publications.
By following these steps, you can enhance your capabilities as a Materials Planner through APICS’s comprehensive resources and community support.
How to Display APICS Skills on Your Resume
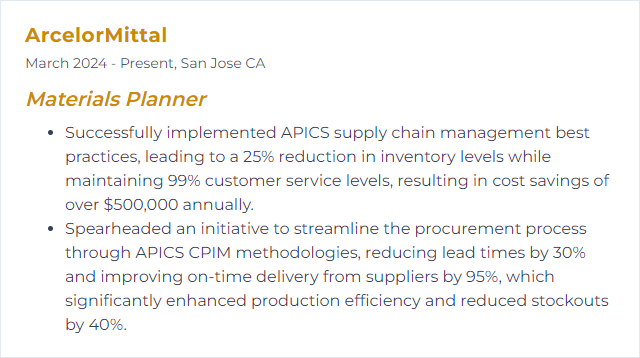
11. Lean
Lean is a systematic approach to minimizing waste within a manufacturing system without sacrificing productivity, focusing on improving overall customer value. For a Materials Planner, it means efficiently managing inventory levels, ensuring timely material availability for production while reducing excess and obsolescence.
Why It's Important
Lean is important for a Materials Planner because it streamlines inventory management, reduces waste, and ensures efficient use of resources, leading to cost savings, improved delivery performance, and increased customer satisfaction.
How to Improve Lean Skills
Improving Lean for a Materials Planner involves streamlining processes, optimizing inventory, and enhancing supplier relationships to ensure efficient material flow and minimize waste. Here are concise strategies:
Visualize Material Flow: Use tools like Kanban boards to visualize material requirements and inventory levels. Kanbanize explains how Kanban can streamline materials planning.
Adopt JIT Principles: Implement Just-In-Time (JIT) inventory management to reduce waste and storage costs. The Balance Small Business offers insights on JIT implementation.
Continuous Improvement (Kaizen): Regularly review and improve materials planning processes. ASQ provides a guide on incorporating Kaizen for continuous improvement.
Supplier Integration: Collaborate closely with suppliers for seamless supply chain integration. SCMDOJO discusses the benefits and strategies of supplier integration.
Use Lean Tools: Apply Lean tools like 5S, Value Stream Mapping, and PDCA (Plan-Do-Check-Act) to optimize operations. LeanProduction is a resourceful site detailing these tools.
Enhance Forecasting Accuracy: Improve demand forecasting to minimize overproduction and underproduction. GMDH highlights software solutions for accurate forecasting.
Employee Empowerment: Encourage team input in identifying inefficiencies and problem-solving. Lean.org emphasizes the importance of engaging everyone in Lean principles.
Incorporating these strategies will lead to more efficient materials planning and contribute to the overall Lean improvement within the organization.
How to Display Lean Skills on Your Resume
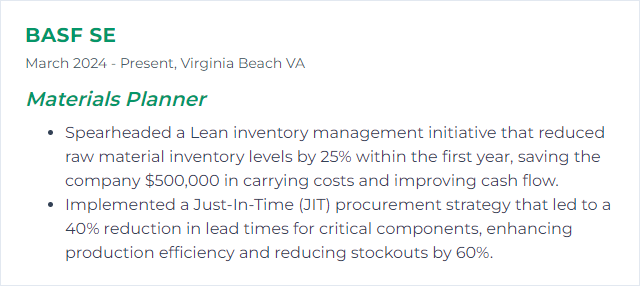
12. Six Sigma
Six Sigma is a data-driven methodology and set of tools designed to improve processes by minimizing defects and variability, aiming for near perfection in product quality and efficiency, which is crucial for a Materials Planner in ensuring optimal inventory levels and reducing waste in supply chain operations.
Why It's Important
Six Sigma is important for a Materials Planner as it rigorously focuses on reducing variability and errors in processes, leading to more efficient inventory management, optimal resource allocation, and improved supply chain performance, resulting in higher customer satisfaction and lower costs.
How to Improve Six Sigma Skills
Improving Six Sigma as a Materials Planner involves enhancing process efficiency, reducing variability, and increasing predictability in the supply chain. Here’s a succinct guide:
Define Objectives Clearly: Begin by defining clear, measurable goals for improvement in material planning processes. SMART goals can provide a structured approach.
Measure Current Performance: Use Six Sigma’s DMAIC methodology starting with the Measure phase to accurately understand current performance.
Analyze Data: Employ statistical tools to analyze data and identify root causes of inefficiencies. Tools like Fishbone Diagrams and Pareto Analysis can be particularly useful.
Implement Solutions: Based on analysis, implement targeted solutions. Techniques like Kanban can help in materials planning by improving workflow and reducing waste.
Control and Sustain Improvements: Use control charts and establish standard operating procedures (SOPs) to maintain improvements. Regular reviews and Kaizen for continuous improvement should be part of the culture.
Leverage Technology: Invest in ERP systems and Six Sigma software that can help in better forecasting, inventory management, and process optimization.
Training and Certification: Continuous learning through Six Sigma Certification can deepen expertise in quality management and process improvement.
Collaboration: Foster a collaborative environment with suppliers and stakeholders to ensure alignment and responsiveness. Tools like SCM software can enhance collaboration and visibility across the supply chain.
By systematically applying these steps, a Materials Planner can significantly improve processes, contributing to the overall efficiency and effectiveness of the supply chain operations.
How to Display Six Sigma Skills on Your Resume
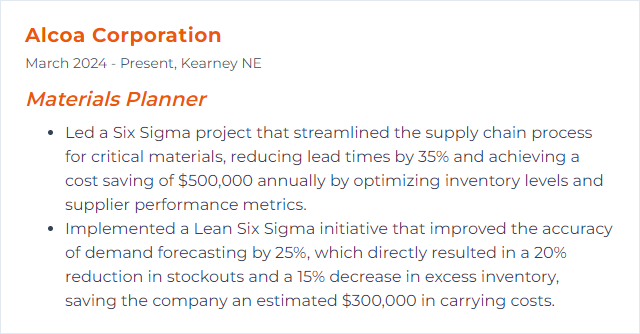