Top 12 Control Engineer Skills to Put on Your Resume
In the rapidly evolving field of control engineering, possessing a robust set of technical and soft skills can significantly elevate your marketability and career prospects. This article delves into the top 12 skills that control engineers should highlight on their resumes, underscoring the blend of expertise and personal attributes essential for excelling in this dynamic discipline.
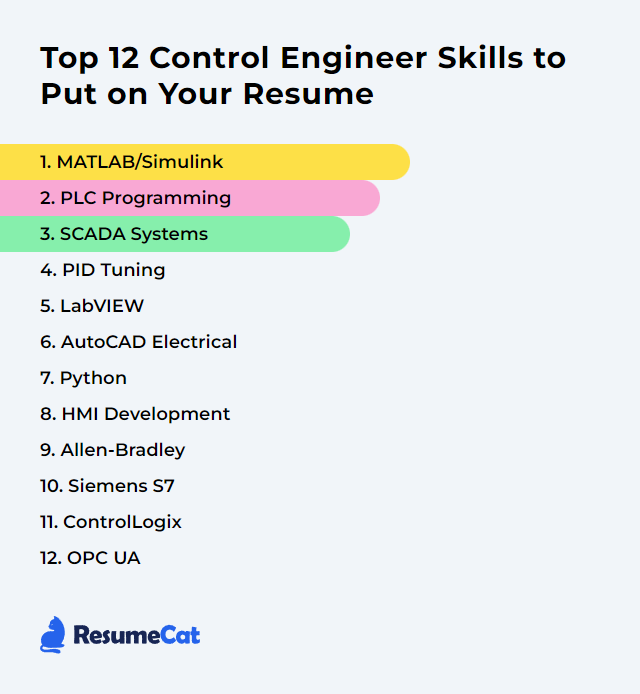
Control Engineer Skills
- MATLAB/Simulink
- PLC Programming
- SCADA Systems
- PID Tuning
- LabVIEW
- AutoCAD Electrical
- Python
- HMI Development
- Allen-Bradley
- Siemens S7
- ControlLogix
- OPC UA
1. MATLAB/Simulink
MATLAB/Simulink is a software platform used by control engineers for designing, simulating, and analyzing dynamic systems, enabling the modeling of control algorithms, system simulations, and implementation of control strategies in a graphical and intuitive environment.
Why It's Important
MATLAB/Simulink is important for Control Engineers because it offers a powerful and intuitive environment for designing, simulating, and analyzing dynamic systems and control algorithms, enabling rapid development and testing of control strategies across various industries.
How to Improve MATLAB/Simulink Skills
To enhance your MATLAB/Simulink skills as a Control Engineer, focus on the following strategies:
Master the Basics: Start with MATLAB's official tutorials to solidify your understanding of the fundamentals.
Simulink for Control Systems: Utilize the Simulink Control Design tool for modeling and simulation of control systems.
MATLAB Central: Engage with the MATLAB Central community, where you can find answers to specific questions, share your knowledge, and download user-contributed code.
Control System Toolbox™: Explore the Control System Toolbox™ for designing and analyzing control systems within MATLAB.
Automate Tasks: Learn to write scripts to automate repetitive tasks. MATLAB's documentation and scripting tutorials are great resources.
Online Courses: Consider enrolling in online courses on platforms like Coursera or Udemy that specialize in MATLAB/Simulink for control engineering.
Project-Based Learning: Apply your skills to real-world projects or simulations. This hands-on approach solidifies understanding and uncovers gaps in knowledge.
Stay Updated: MATLAB and Simulink are constantly being updated with new features. Keep an eye on the official MathWorks Blog for updates and tips.
By combining these resources and approaches, you'll significantly improve your MATLAB/Simulink skills pertinent to control engineering.
How to Display MATLAB/Simulink Skills on Your Resume
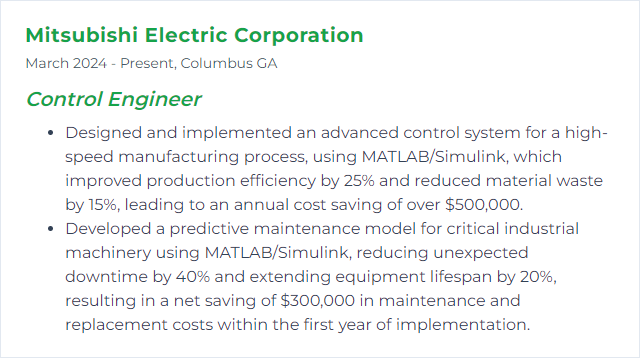
2. PLC Programming
PLC Programming involves creating and implementing software algorithms on a Programmable Logic Controller (PLC) to automate industrial and manufacturing processes, control machinery, and manage operations in a reliable, flexible, and efficient manner. It uses specific languages such as Ladder Logic, Function Block Diagrams, Structured Text, and others, tailored to the needs of control engineering.
Why It's Important
PLC programming is crucial for Control Engineers as it enables the automation of industrial processes, enhances system reliability and efficiency, and allows for precise control and monitoring of machinery and production lines, thereby optimizing operations and ensuring safety.
How to Improve PLC Programming Skills
Improving PLC programming, especially for a Control Engineer, involves continuous learning and practical application. Here are concise steps with resources:
Understand Basics Thoroughly: Ensure a strong grasp of PLC basics, including hardware components and programming fundamentals. PLC Academy is a great starting point.
Learn Ladder Logic Proficiently: Mastering Ladder Logic is crucial. Practice by solving real-world problems. PLCdev has resources and examples.
Explore Advanced Programming Techniques: Dive into structured text, function block diagrams, and sequential function charts. AutomationDirect provides tutorials on these topics.
Understand Industry Standards: Familiarize yourself with IEC 61131-3 and other relevant standards. The IEC website offers comprehensive insights.
Practice Safety and Security: Learn about safety PLCs and cybersecurity in industrial networks. ISA offers resources and training on these topics.
Use Simulation Tools: Before implementing on actual hardware, use simulation tools like Siemens PLCSIM or Rockwell's Studio 5000 Logix Emulate. This practice saves time and reduces errors.
Stay Updated: Technology evolves rapidly. Follow industry blogs, forums, and publications. Control Engineering is a useful resource for latest trends and technologies.
Join Forums and Communities: Engage with communities like PLCTalk for troubleshooting, advice, and sharing experiences.
Continuous Learning: Enroll in advanced courses on platforms like Udemy or Coursera that offer specialized PLC programming courses.
Apply Knowledge Practically: Work on projects, either personal or professional. Applying what you learn in real-world scenarios is invaluable.
By following these steps and leveraging the recommended resources, a Control Engineer can significantly improve their PLC programming skills.
How to Display PLC Programming Skills on Your Resume
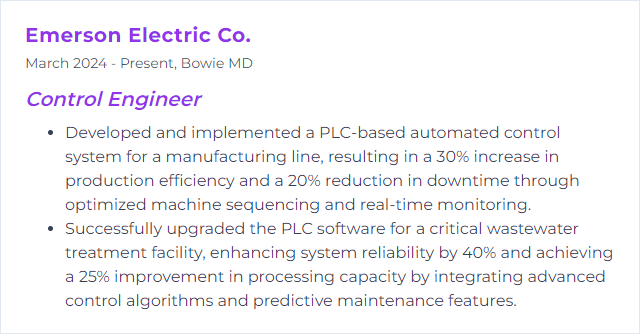
3. SCADA Systems
SCADA (Supervisory Control and Data Acquisition) systems are computer-based systems used by control engineers to monitor and control industrial processes remotely. They collect real-time data from sensors and equipment, allowing for efficient process control, data analysis, and automation within various industries.
Why It's Important
SCADA (Supervisory Control and Data Acquisition) systems are crucial for Control Engineers as they provide the ability to monitor and control industrial processes and facilities from a centralized location, ensuring efficiency, reliability, and safety in operations.
How to Improve SCADA Systems Skills
Improving SCADA (Supervisory Control and Data Acquisition) systems, crucial for industrial control systems, involves enhancing reliability, security, interoperability, and efficiency. Here’s a concise guide for Control Engineers:
Enhance Security: Implement robust cybersecurity measures to protect against threats. Regularly update security protocols and use secure communication channels. ISA provides standards for industrial automation and control systems security.
Improve Data Management: Optimize data collection and analysis for better decision-making. Implementing advanced data analytics tools can provide deeper insights. OSIsoft PI System is an example of an efficient data management tool.
Increase System Reliability: Ensure redundancy and fault tolerance within the SCADA architecture to minimize downtime. Continuous monitoring and preventive maintenance are key. IEC 61508 outlines standards for the functional safety of electrical/electronic/programmable electronic safety-related systems.
Upgrade Hardware and Software: Regularly updating SCADA hardware and software components can enhance performance and security. Consider adopting open standards for better interoperability. OPC Foundation promotes open connectivity via OPC standards.
Implement Scalable Solutions: Design systems that can easily adapt to future expansions in both scale and functionality. This ensures longevity and flexibility of the SCADA system.
Enhance User Training: Regular training for operators and engineers on the latest technologies and best practices can significantly improve system efficiency and safety.
Adopt Wireless Technologies: Incorporating wireless communication can improve the flexibility and reduce the installation costs of SCADA systems. However, ensure robust security measures are in place. IEEE 802.15.4 is a standard that specifies the operation of low-rate wireless personal area networks.
Utilize Cloud Computing: Leverage cloud technologies for better scalability, data management, and analysis capabilities. Ensure secure cloud practices to protect data integrity. Amazon Web Services and Microsoft Azure offer industrial IoT solutions that can be integrated with SCADA systems.
By focusing on these key areas, Control Engineers can significantly improve the performance, security, and reliability of SCADA systems.
How to Display SCADA Systems Skills on Your Resume
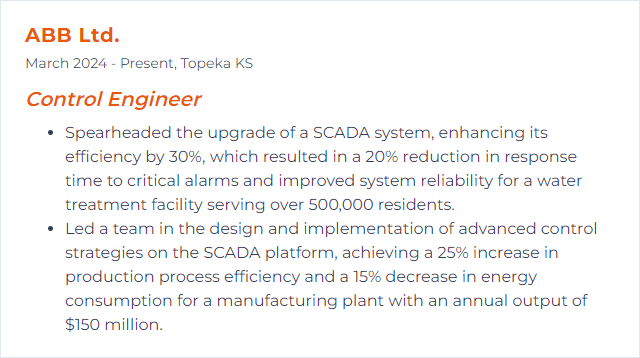
4. PID Tuning
PID tuning is the process of adjusting the parameters of a PID controller (Proportional, Integral, Derivative) in a control system to achieve optimal performance, ensuring the system responds correctly to changes in setpoint or disturbances, with minimal overshoot, settling time, and steady-state error.
Why It's Important
PID tuning is crucial for optimizing a control system's performance by adjusting the proportional, integral, and derivative parameters to achieve a desired response, minimizing error, and ensuring stability and efficiency.
How to Improve PID Tuning Skills
Improving PID tuning involves optimizing the proportional (P), integral (I), and derivative (D) gains to achieve a desired control response. Here's a very short and concise guide tailored for a Control Engineer:
Start with identifying the process: Understand the dynamics of the system you are controlling. This is critical for selecting an appropriate tuning method.
Select a tuning method: Common methods include Ziegler-Nichols, Cohen-Coon, and Lambda tuning. Choose based on your system's response (e.g., first-order, second-order) and performance requirements.
Implement and test initial settings: Apply the initial PID parameters suggested by your selected tuning method. Use simulation tools if available to predict the system's response.
Iterate based on performance: Adjust the PID parameters based on the system's performance. Focus on reducing overshoot, settling time, and steady-state error. Use performance metrics like Integral of Absolute Error (IAE) or Integral of Squared Error (ISE) for a more quantitative approach.
Utilize software tools: Consider using PID tuning software tools like MATLAB’s PID Tuner or PID Loop Simulator for more complex systems or if manual tuning proves challenging.
Monitor and adjust: PID tuning is not a one-time task. Continuously monitor the system's performance and be prepared to retune as process conditions change.
For more detailed guidance, consider visiting the ISA (International Society of Automation) website for resources and professional courses on control systems and PID tuning.
How to Display PID Tuning Skills on Your Resume
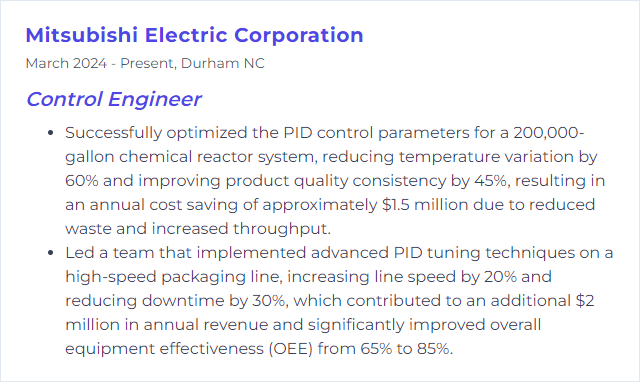
5. LabVIEW
LabVIEW (Laboratory Virtual Instrument Engineering Workbench) is a graphical programming platform used by control engineers for designing, simulating, and implementing control systems and signal processing applications through an intuitive visual interface, significantly aiding in data acquisition, instrument control, and automation.
Why It's Important
LabVIEW is important for Control Engineers because it provides an intuitive, graphical programming environment for designing, simulating, and implementing control systems, enabling rapid development and testing of sophisticated control algorithms and system integration.
How to Improve LabVIEW Skills
Improving your LabVIEW skills as a Control Engineer involves focusing on areas that enhance your ability to design, simulate, and implement control systems efficiently. Here's a concise guide to help you get started:
Understand Core Concepts: Start with the fundamentals of LabVIEW. National Instruments (NI) offers LabVIEW Core 1 and Core 2 training materials, which are crucial for building a solid foundation.
Learn LabVIEW Control Design and Simulation Module: This module is essential for Control Engineers. It allows you to design, simulate, and deploy control systems. NI provides a comprehensive guide on Control Design and Simulation.
Practice with Real-World Projects: Hands-on experience is invaluable. Try to work on projects that require you to apply control algorithms or simulate control systems. Project ideas and examples can be found in the NI Community.
Utilize Libraries and Toolkits: Explore and integrate LabVIEW toolkits and libraries specifically designed for control systems, such as the LabVIEW Robotics Module for robotics applications or the LabVIEW MathScript RT Module for mathematical computations.
Join Workshops and Webinars: NI and other educational institutions regularly conduct workshops and webinars. Keep an eye on the Events at NI page for opportunities to learn and network with other professionals.
Engage in the Community: The NI Community forums are an excellent place to ask questions, share knowledge, and learn from experienced users and NI engineers.
Continuous Learning: Stay updated with the latest LabVIEW features and best practices by subscribing to NI’s Learning Resources, which offers a variety of learning materials, including tutorials and webinars.
By focusing on these areas, you can significantly improve your proficiency in LabVIEW, making it a powerful tool in your Control Engineering toolkit.
How to Display LabVIEW Skills on Your Resume
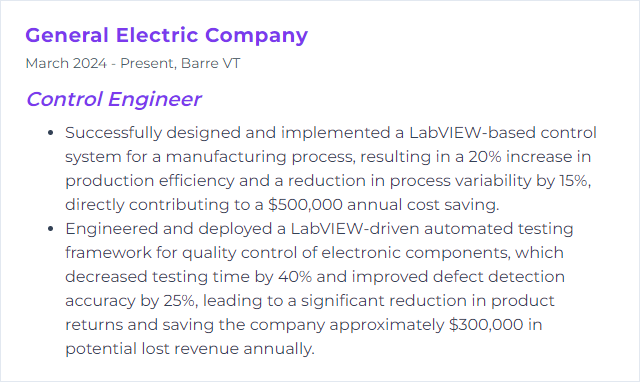
6. AutoCAD Electrical
AutoCAD Electrical is a specialized software tool designed for electrical control designers. It offers enhanced drafting features and automations specifically aimed at creating electrical control systems, schematics, panel layouts, and project documentation efficiently.
Why It's Important
AutoCAD Electrical is crucial for Control Engineers because it streamlines the creation of accurate and standardized electrical control designs, enhancing productivity, reducing errors, and ensuring compliance with industry standards.
How to Improve AutoCAD Electrical Skills
Improving your AutoCAD Electrical skills, especially from a Control Engineer's perspective, involves a combination of understanding electrical design principles, mastering AutoCAD Electrical tools, and keeping up with industry trends. Here’s a concise guide:
Learn the Basics Thoroughly: Start with the fundamentals of electrical design and AutoCAD Electrical. Autodesk provides an official tutorial.
Master Schematic Design: Focus on creating and interpreting electrical control schematics efficiently. Use Autodesk's schematic components tutorial as a starting point.
Understand PLC Module Integration: As a control engineer, it’s crucial to efficiently incorporate PLC I/O modules into your designs. Autodesk offers guidance on PLC layout modules.
Utilize Wire Numbering and Component Tagging: Automate wire numbering and component tagging for efficient circuit design and troubleshooting. This feature is detailed in the AutoCAD Electrical toolset.
Customize and Use the Symbol Library: Enhance your productivity by customizing and using the symbol library effectively. Autodesk's content library provides a solid foundation.
Stay Updated with New Features: AutoCAD Electrical is regularly updated. Keep abreast of the latest features and how they can benefit your work. The AutoCAD Electrical blog is a good resource for updates and tips.
Participate in Forums and Communities: Engage with other professionals through forums and communities. The Autodesk forums offer a platform for sharing knowledge and solving problems.
Undergo Advanced Training: Consider advanced training courses to deepen your expertise. Autodesk’s Learning and Certification page provides information on available courses and certifications.
By focusing on these areas, you can significantly improve your AutoCAD Electrical skills and enhance your effectiveness as a Control Engineer.
How to Display AutoCAD Electrical Skills on Your Resume
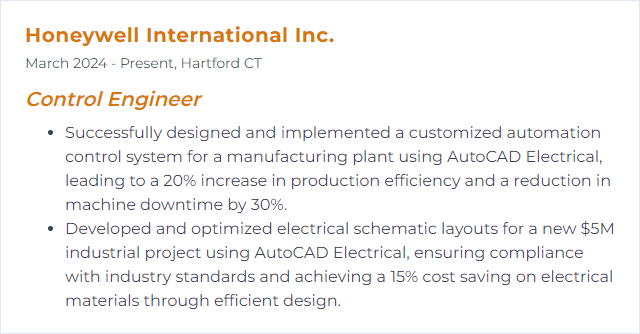
7. Python
Python is a high-level, versatile programming language widely used in control engineering for developing automation scripts, data analysis, system simulations, and designing control algorithms due to its simplicity, extensive libraries (like NumPy, SciPy, and Matplotlib), and strong community support.
Why It's Important
Python is important for a Control Engineer because it offers powerful libraries (like NumPy, SciPy, and Matplotlib) for mathematical computations, data analysis, and visualization, simplifying the development and simulation of control systems.
How to Improve Python Skills
To improve your Python skills as a Control Engineer, focus on mastering libraries relevant to control systems, practicing problem-solving with real-world projects, and staying updated with the Python community's latest advancements. Here's a concise plan:
Learn Core Python: Ensure a strong grasp of Python basics. The official Python tutorial is a great starting point.
Master Control Engineering Libraries:
- NumPy: Foundation for numerical computations. NumPy's official guide is essential.
- SciPy: For advanced math, signal processing, and more. Start with SciPy's tutorials.
- Matplotlib: For plotting and visualization. Matplotlib's tutorials help in data representation.
- Control Systems Library: Specifically designed for control engineering. Python-Control Documentation provides valuable resources.
- Scikit-learn: For machine learning applications in control systems. Explore Scikit-learn's user guide.
Engage in Projects: Apply your skills in real-world projects or simulations that interest you. Websites like GitHub are great for finding project ideas and collaborating.
Stay Updated and Network:
- Join Python and Control Engineering communities (e.g., r/Python on Reddit, Control System Society within IEEE).
- Follow Python Weekly for the latest news in Python.
Practice and Feedback:
- Regularly practice on platforms like LeetCode using Python.
- Seek feedback from peers or mentors to identify and work on your weak areas.
Remember, consistent practice and application of Python in your control engineering projects will significantly enhance your proficiency.
How to Display Python Skills on Your Resume
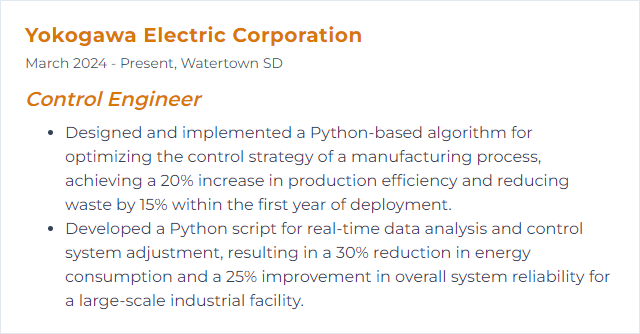
8. HMI Development
HMI Development involves designing and implementing Human-Machine Interfaces (HMIs) that allow control engineers to interact, monitor, and manage industrial processes or machinery effectively, ensuring clear, efficient, and user-friendly operation control.
Why It's Important
HMI (Human-Machine Interface) development is crucial for Control Engineers as it provides a user-friendly platform for monitoring and controlling complex systems, enabling efficient operation, quick problem diagnosis, and enhanced safety by facilitating clear communication between human operators and machinery.
How to Improve HMI Development Skills
Improving HMI (Human-Machine Interface) development, especially from a Control Engineer's perspective, involves focusing on usability, efficiency, and effective communication between the operator and the machine. Here’s a concise guide:
Understand User Needs: Engage with end-users to gather requirements and understand their workflow. This ensures the HMI design is intuitive and tailored to user needs. Nielsen Norman Group offers insights on capturing user requirements effectively.
Simplify Design: Adopt a minimalist design approach. Ensure screens are uncluttered, use consistent symbols, and colors meaningfully. Interaction Design Foundation provides principles on minimalist design.
Ensure Responsiveness: Design HMIs to be responsive across devices. This enhances user experience and accessibility. Smashing Magazine outlines ground rules for responsive design.
Incorporate Feedback Loops: Implement immediate feedback for user actions to confirm commands or indicate errors. This reduces user errors and increases system transparency. UX Design elaborates on the importance of feedback in UX.
Prioritize Safety and Security: Ensure the HMI design incorporates safety alerts and secure access controls to protect users and data. ISA provides standards and guidelines on ensuring safety and security in control systems.
Test and Iterate: Conduct usability testing with real users to identify issues and areas for improvement. Iterate based on feedback to enhance the HMI. Usability.gov is a resource for conducting usability testing.
Stay Updated with Trends: Keep abreast of the latest trends in HMI design, such as adaptive interfaces and augmented reality, to continuously improve user experience. Gartner offers research on emerging tech trends.
By focusing on user-centric design, simplifying interactions, ensuring safety and security, and continuously iterating based on user feedback, control engineers can significantly improve HMI development for better user experience and operational efficiency.
How to Display HMI Development Skills on Your Resume
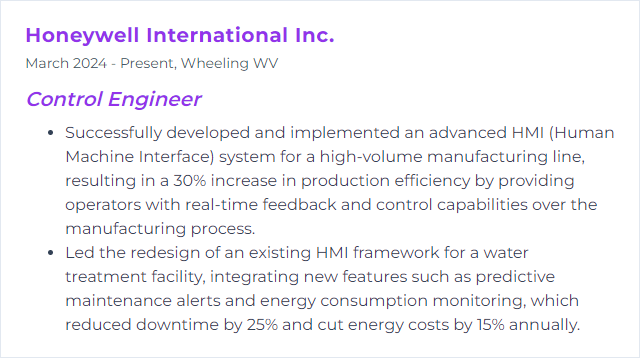
9. Allen-Bradley
Allen-Bradley is a brand name of Rockwell Automation, which manufactures a wide range of industrial automation equipment including programmable logic controllers (PLCs), human-machine interfaces (HMIs), sensors, and safety components, widely used by control engineers for designing and implementing automated control systems.
Why It's Important
Allen-Bradley, a brand under Rockwell Automation, is important for Control Engineers because it offers a wide range of reliable and innovative automation and control products. These include programmable logic controllers (PLCs), human-machine interfaces (HMIs), and variable frequency drives (VFDs), which are essential for designing, implementing, and managing automated systems in various industries.
How to Improve Allen-Bradley Skills
Improving your skills and knowledge with Allen-Bradley systems, a brand of Rockwell Automation, involves understanding both the hardware and software components of their automation solutions. Here's a concise guide:
Get Familiar with the Hardware: Understand the range of Allen-Bradley products, including PLCs (like the ControlLogix and Micro800 series), HMI, sensors, and drives. Start with the Rockwell Automation Product Directory for an overview.
Learn RSLogix 5000/Studio 5000: This is the primary software used for programming Allen-Bradley ControlLogix and CompactLogix PLCs. Focus on mastering ladder logic, structured text, and function block diagram programming. Explore the Studio 5000 page for details.
Explore Connected Components Workbench (CCW): For programming Micro800 series PLCs, Component Class Drives, and other connected components. Visit the CCW page for resources.
Utilize the Knowledgebase: Rockwell Automation provides a comprehensive Knowledgebase with articles, troubleshooting tips, and documentation. Access requires a support contract. Check the Support section for more.
Online Training and Webinars: Rockwell Automation offers e-learning courses and webinars that cover various aspects of their products and software. Explore the Training Services section.
Practice with Simulation Software: Before implementing on actual hardware, use simulation tools like Studio 5000 Logix Emulate. This allows you to test and debug your programs in a virtual environment.
Join Forums and Communities: Engage with other professionals through forums and online communities. The PLC Talk forum is an excellent place to start, with many discussions on Allen-Bradley products.
Official Documentation and Manuals: Always refer to the official manuals and user guides for in-depth understanding and troubleshooting. The Literature Library on Rockwell's website is a valuable resource.
By following these steps and actively engaging with the resources and communities available, Control Engineers can significantly improve their proficiency with Allen-Bradley systems.
How to Display Allen-Bradley Skills on Your Resume
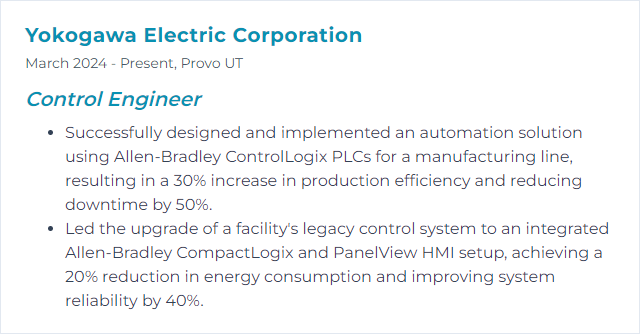
10. Siemens S7
Siemens S7 is a family of programmable logic controllers (PLCs) used for automation and control in various industrial applications, offering a range of hardware and software solutions for efficient process control and monitoring.
Why It's Important
The Siemens S7 is a crucial tool for Control Engineers due to its reliability in automating complex industrial processes, its scalable and flexible design accommodating varied control needs, and its widespread industry acceptance ensuring compatibility and support.
How to Improve Siemens S7 Skills
Improving the performance and efficiency of Siemens S7 PLC systems involves optimizing both the hardware and software aspects of the control system. Here’s a concise guide for Control Engineers:
Update Firmware: Ensure your Siemens S7 PLC and all connected devices are running the latest firmware versions. This can enhance performance, add new features, and fix known bugs. Refer to Siemens Support (Siemens Support) for firmware updates.
Optimize Code: Write efficient and optimized code. Use blocks efficiently, minimize scan cycles, and use efficient data types. Siemens provides guidelines for optimizing STEP 7 code (Optimizing STEP 7 Code).
Proper Hardware Configuration: Ensure your PLC hardware configuration is optimized for your application. This includes selecting the right CPU, setting appropriate cycle times, and using appropriate memory and communication modules. Siemens TIA Selection Tool can assist in hardware selection and configuration (TIA Selection Tool).
Network Optimization: Optimize your PROFINET or industrial Ethernet network for lower latency and higher throughput. Use Siemens network planning tools and follow best practices for network configuration (PROFINET Network Design).
Use Advanced Features: Leverage the advanced features of your S7 PLC, like predictive maintenance, integrated safety, and energy management functionalities. Siemens offers various modules and software solutions to integrate these features into your system (Siemens Industry Mall).
Training and Resources: Continuously update your knowledge and skills through Siemens training and resources. Siemens offers a range of training courses for engineers to stay updated on the latest technologies and best practices (Siemens SITRAIN).
Performance Monitoring: Regularly monitor the performance of your S7 system using Siemens diagnostic and monitoring tools. Early detection of issues can prevent downtimes and improve system reliability (Siemens Diagnostic Tools).
By following these strategies and utilizing Siemens resources, Control Engineers can significantly improve the performance and efficiency of Siemens S7 PLC systems.
How to Display Siemens S7 Skills on Your Resume
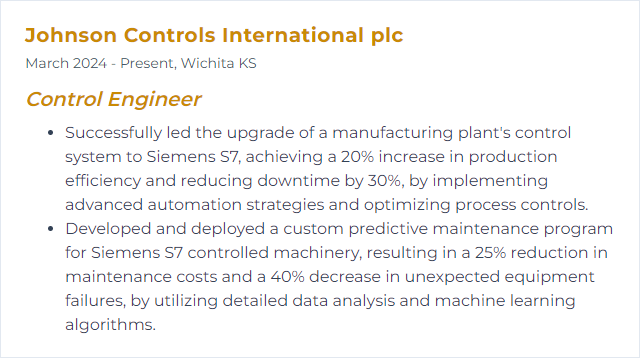
11. ControlLogix
ControlLogix is a modular, programmable automation controller (PAC) system developed by Rockwell Automation, primarily used for industrial control and automation applications. It offers advanced control capabilities, high-speed communication, and scalability, making it suitable for a wide range of control engineering applications.
Why It's Important
ControlLogix, developed by Rockwell Automation, is crucial for Control Engineers because it offers a robust, scalable, and integrated control system. This platform enables efficient design, implementation, and operation of complex automation solutions, improving system performance and productivity in industrial environments.
How to Improve ControlLogix Skills
Improving ControlLogix systems involves enhancing performance, reliability, and efficiency, primarily through strategic hardware upgrades, software optimization, and network enhancements. Here are concise strategies tailored for Control Engineers:
Firmware and Software Updates: Regularly update the ControlLogix firmware and accompanying Rockwell Software to ensure compatibility, security, and access to the latest features. Rockwell Automation Product Compatibility and Download Center provides the necessary resources.
Optimize Logic and Data Handling: Streamline your ladder logic and structured text for efficiency. Minimize processor load by optimizing data handling and logic execution. Rockwell Automation's Logix 5000 Controllers General Instructions Reference Manual offers guidance on best practices.
Network Improvements: Enhance communication efficiency by segmenting networks, using managed switches, and prioritizing traffic. This reduces latency and improves data integrity. Design Considerations for Securing Industrial Automation and Control System Networks provides insights into network design and security.
Hardware Upgrades: Evaluate and upgrade I/O modules, processors, and power supplies to newer versions for improved performance and extended lifecycle support. Rockwell Automation's Selection Guide for ControlLogix 5580 Controllers helps in choosing the right components.
Preventive Maintenance: Implement a preventive maintenance schedule for hardware and software components to avoid unexpected downtimes. This includes regular inspections, cleaning, and diagnostic checks.
Training and Support: Enhance team skills through official Rockwell Automation training courses and utilize their support community for troubleshooting and optimization tips. Rockwell Automation Training Services and Rockwell Automation Community are valuable resources.
Leverage Add-On Instructions (AOIs): Create or use existing AOIs for common functions to simplify program structure and enhance code reusability. Creating and Using Add-On Instructions provides a comprehensive guide.
Utilize Advanced Features: Take advantage of advanced features such as Produced and Consumed Tags, and Add-On Profiles (AOPs) for enhanced system integration and simplified configuration. Rockwell Automation's Logix 5000 Controllers Produced and Consumed Tags offers detailed information.
By focusing on these eight areas, Control Engineers can significantly improve the performance, reliability, and efficiency of ControlLogix systems.
How to Display ControlLogix Skills on Your Resume

12. OPC UA
OPC UA (Open Platform Communications Unified Architecture) is an industrial communication standard designed for secure, reliable, and platform-independent information exchange between devices, systems, and services in industrial automation. It enables seamless interoperability and data sharing across different manufacturers and technologies, facilitating the integration and control of complex systems.
Why It's Important
OPC UA (Open Platform Communications Unified Architecture) is important for a Control Engineer because it provides a standardized, platform-independent, and secure communication protocol for exchanging data and information between various industrial automation devices and systems, enhancing interoperability, and facilitating efficient and reliable control processes.
How to Improve OPC UA Skills
Improving OPC UA (OPC Unified Architecture) for control engineers involves enhancing security, interoperability, and real-time performance. Here are concise strategies for each:
Enhance Security:
- Implement the latest security policies for encryption and authentication.
- Regularly update and patch OPC UA servers and clients to protect against vulnerabilities.
Improve Interoperability:
- Use OPC UA Companion Specifications for standardized information models in your industry.
- Validate systems with OPC UA Compliance Test Tools to ensure compatibility.
Boost Real-Time Performance:
- Implement OPC UA PubSub (Publish-Subscribe) for efficient, scalable communications, especially in real-time and at scale.
- Optimize network infrastructure and consider using Time Sensitive Networking (TSN) for deterministic communication.
Educate and train engineering teams on OPC UA best practices and updates through resources like the OPC Foundation’s webinar series and training.
By focusing on these areas, control engineers can significantly improve the performance, reliability, and security of OPC UA-based systems.
How to Display OPC UA Skills on Your Resume
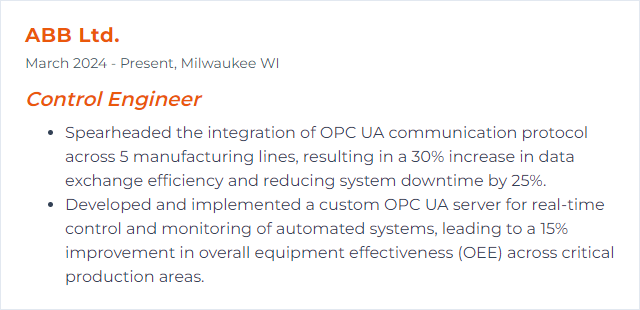