Top 12 Quality Control Engineer Skills to Put on Your Resume
In the competitive field of quality control engineering, showcasing a blend of technical expertise and soft skills on your resume can significantly elevate your job candidacy. Here are the top 12 skills that demonstrate your proficiency in ensuring product excellence and operational efficiency, making you a standout applicant in this specialized area.
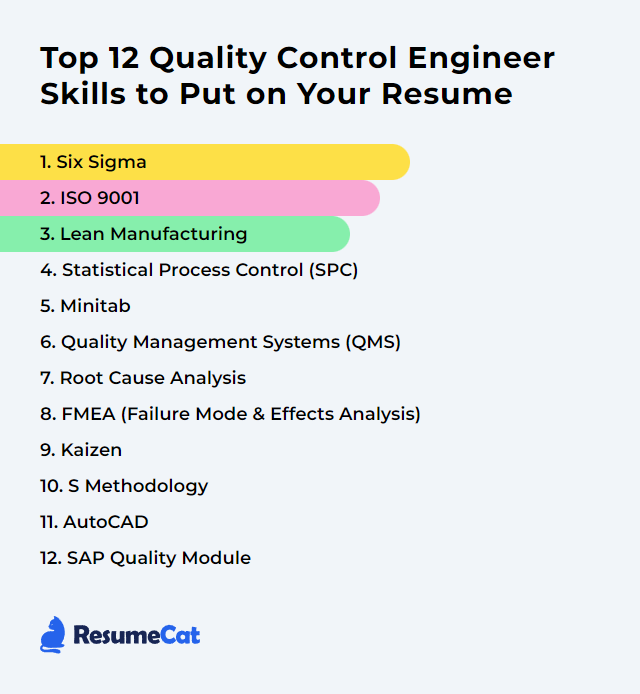
Quality Control Engineer Skills
- Six Sigma
- ISO 9001
- Lean Manufacturing
- Statistical Process Control (SPC)
- Minitab
- Quality Management Systems (QMS)
- Root Cause Analysis
- FMEA (Failure Mode and Effects Analysis)
- Kaizen
- S Methodology
- AutoCAD
- SAP Quality Module
1. Six Sigma
Six Sigma is a data-driven approach and methodology for eliminating defects and improving quality in processes, focusing on variance reduction and process optimization, highly relevant for Quality Control Engineers to enhance product reliability and efficiency.
Why It's Important
Six Sigma is important for a Quality Control Engineer because it provides a systematic methodology (DMAIC: Define, Measure, Analyze, Improve, Control) for identifying, analyzing, and reducing defects and variations in processes, thereby improving the quality, efficiency, and customer satisfaction in production and service delivery.
How to Improve Six Sigma Skills
Improving Six Sigma as a Quality Control Engineer involves continuous learning and application of best practices. Here are succinct strategies:
Enhance Your Statistical Knowledge: Deepen your understanding of statistical tools essential for Six Sigma projects. Platforms like Khan Academy offer free resources to sharpen your skills.
Get Certified: Pursue higher Six Sigma certifications (Green Belt, Black Belt, Master Black Belt). Organizations like ASQ provide certification details and resources.
Implement DMAIC Rigorously: Ensure strict adherence to the Define, Measure, Analyze, Improve, Control (DMAIC) methodology in projects for systematic improvements. ASQ's DMAIC guide provides a comprehensive overview.
Use Quality Control Tools: Master and utilize quality control tools effectively. Learn more about tools like FMEA, Control Charts, and Pareto Analysis at MindTools.
Lean Integration: Incorporate Lean principles to eliminate waste and streamline processes. Lean Enterprise Institute offers insights into integrating Lean with Six Sigma.
Continuous Learning: Stay updated with the latest trends and advancements in quality control and Six Sigma methodologies through webinars, workshops, and conferences. iSixSigma is a great platform for resources and community interaction.
Practical Application: Apply Six Sigma principles in real-world projects and document your successes and lessons learned. This hands-on experience is invaluable.
By focusing on these areas, Quality Control Engineers can significantly improve their Six Sigma expertise and contribute more effectively to their organizations' quality improvement efforts.
How to Display Six Sigma Skills on Your Resume
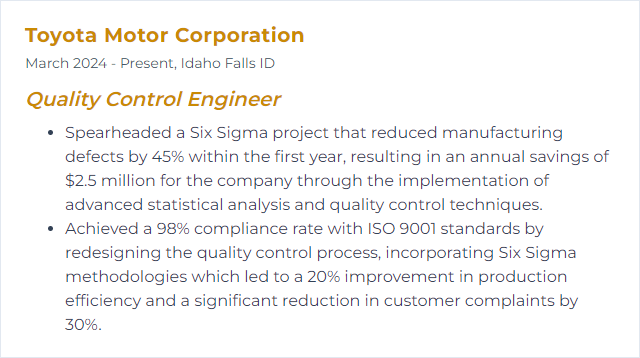
2. ISO 9001
ISO 9001 is an international standard that specifies requirements for a quality management system (QMS). It enables organizations to ensure consistent quality in their products and services, meet customer expectations, and comply with regulatory requirements. For a Quality Control Engineer, it provides a framework for setting up, maintaining, and improving quality control processes to enhance product quality and reliability.
Why It's Important
ISO 9001 is important because it provides a systematic framework for ensuring consistent quality in products and services, essential for a Quality Control Engineer to meet customer expectations and regulatory requirements efficiently.
How to Improve ISO 9001 Skills
Improving ISO 9001 involves a continuous effort to enhance the Quality Management System (QMS) focusing on customer satisfaction, process optimization, and adherence to quality standards. Here's a concise guide for a Quality Control Engineer:
Engage Leadership: Ensure top management's involvement in the QMS to align quality objectives with business strategy (ISO 9001 Clause 5).
Risk Management: Implement a risk-based thinking approach to foresee and mitigate potential quality issues (ISO 9001 Clause 6).
Continuous Improvement: Adopt the Plan-Do-Check-Act (PDCA) cycle for ongoing QMS improvements (ISO 9001 Clause 10).
Employee Competence: Regularly train and evaluate employees to ensure they meet the competency requirements necessary for maintaining quality standards (ISO 9001 Clause 7.2).
Customer Feedback: Systematically gather and analyze customer feedback to identify areas for improvement and enhance customer satisfaction (ISO 9001 Clause 9.1.2).
Internal Audits: Conduct periodic internal audits to assess compliance with ISO 9001 standards and identify opportunities for improvement (ISO 9001 Clause 9.2).
Process Optimization: Streamline processes to increase efficiency, reduce waste, and improve quality (ISO 9001 Clause 4.4).
Documentation Control: Maintain accurate records and document control to ensure consistency and traceability (ISO 9001 Clause 7.5).
Supplier Management: Evaluate and select suppliers based on their ability to supply products and services in accordance with the organization's requirements (ISO 9001 Clause 8.4).
Performance Evaluation: Regularly review the performance and effectiveness of the QMS through metrics and indicators to guide improvements (ISO 9001 Clause 9).
For further detailed guidance, refer to the ISO 9001:2015 standards on the International Organization for Standardization website.
How to Display ISO 9001 Skills on Your Resume
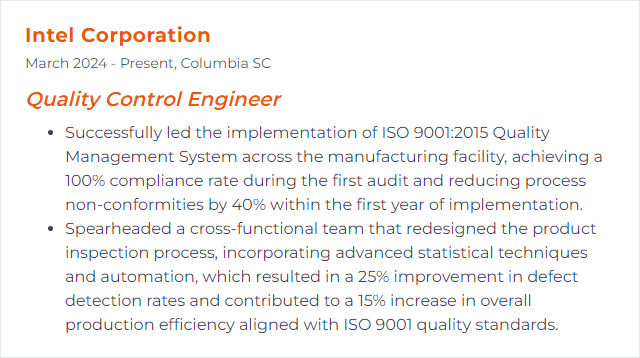
3. Lean Manufacturing
Lean Manufacturing is a systematic approach aimed at minimizing waste without sacrificing productivity. For a Quality Control Engineer, it involves continuously improving processes and quality by identifying inefficiencies, ensuring consistent standards, and reducing variability in production.
Why It's Important
Lean Manufacturing is important for a Quality Control Engineer because it focuses on minimizing waste and maximizing value, leading to higher quality products, reduced defects, and more efficient production processes.
How to Improve Lean Manufacturing Skills
Improving Lean Manufacturing, especially from the perspective of a Quality Control Engineer, involves focusing on waste reduction, process optimization, and continuous improvement. Here are concise strategies:
Map the Value Stream: Identify and map out all steps in your process, highlighting where value is added and where waste occurs. This visibility helps in eliminating non-value-adding activities. Value Stream Mapping Guide
Implement 5S: Use the 5S framework (Sort, Set in order, Shine, Standardize, Sustain) to organize the workplace, ensuring efficiency and safety. This foundational step improves quality by reducing errors and defects. 5S Explained
Adopt Kaizen: Encourage continuous, incremental improvements involving every employee. Small, regular enhancements in processes can lead to significant quality improvements over time. Kaizen Guide
Utilize Poka-Yoke: Implement mistake-proofing techniques to prevent errors before they occur, directly contributing to higher quality and reliability. Poka-Yoke Examples
Apply Six Sigma within Lean: Integrate Six Sigma methodologies to reduce process variability and defects, focusing on quality control and improvement. Lean Six Sigma Overview
Focus on Customer Feedback: Regularly gather and analyze customer feedback to align quality improvements with customer expectations and requirements. Importance of Customer Feedback
Invest in Training: Continuously educate and train employees on lean principles, quality control techniques, and the importance of their role in the process. This empowers them to contribute effectively to lean initiatives. Lean Training Solutions
By implementing these strategies, a Quality Control Engineer can significantly contribute to enhancing Lean Manufacturing processes, leading to improved efficiency, reduced waste, and higher product quality.
How to Display Lean Manufacturing Skills on Your Resume
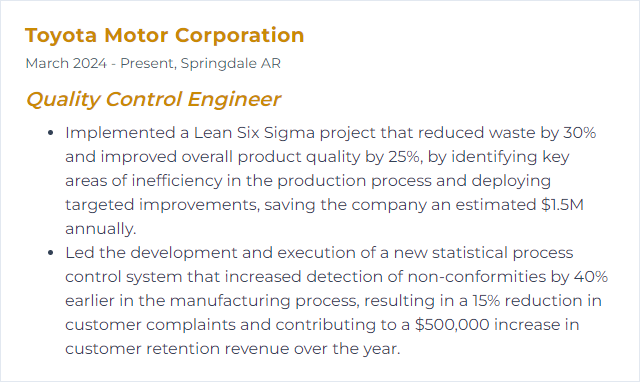
4. Statistical Process Control (SPC)
Statistical Process Control (SPC) is a method used by quality control engineers to monitor and control a process using statistical techniques to ensure it operates at its fullest potential, minimizing variability and defects to meet quality standards.
Why It's Important
Statistical Process Control (SPC) is crucial for a Quality Control Engineer because it enables the monitoring and control of production processes in real-time, ensuring product quality meets specified standards, reducing waste, and preventing defects. This data-driven approach facilitates continuous improvement and consistent delivery of high-quality products.
How to Improve Statistical Process Control (SPC) Skills
To improve Statistical Process Control (SPC) as a Quality Control Engineer, focus on these key steps:
Educate and Train: Ensure all team members understand SPC principles and tools. Utilize resources like the American Society for Quality (ASQ) for training materials.
Select Appropriate Control Charts: Choose the right type of control chart for your data and process. The National Institute of Standards and Technology (NIST) offers guidance on selecting control charts.
Establish Baseline Measurements: Use historical data to establish process capability and performance baselines. Refer to the Institute of Industrial and Systems Engineers (IISE) for process capability analysis techniques.
Implement Real-Time Monitoring: Use software tools for real-time data collection and monitoring. Explore solutions from Minitab for software options.
Engage in Continuous Improvement: Apply the Plan-Do-Check-Act (PDCA) cycle for continuous process improvement. The Environmental Protection Agency (EPA) provides a simple overview of the PDCA cycle.
Analyze and Act on Data: Regularly review control charts and process data to identify trends or shifts in the process. Take corrective actions as needed based on data analysis.
Collaborate with Suppliers: Work with suppliers to ensure quality materials and components, using SPC in supplier quality management. The Supply Chain Resource Cooperative (SCRC) provides insights on integrating SPC in supplier quality management.
By focusing on these steps and utilizing available resources, Quality Control Engineers can significantly improve their SPC practices, leading to enhanced process control and product quality.
How to Display Statistical Process Control (SPC) Skills on Your Resume
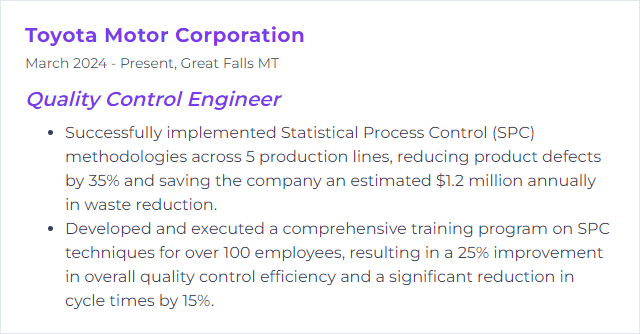
5. Minitab
Minitab is a statistical software package commonly used by Quality Control Engineers for analyzing data related to quality improvement projects, including process optimization, defect reduction, and control charting.
Why It's Important
Minitab is crucial for a Quality Control Engineer because it offers powerful statistical analysis, process improvement, and quality control tools, enabling efficient data analysis, problem-solving, and decision-making to ensure product quality and process optimization.
How to Improve Minitab Skills
Improving your proficiency with Minitab as a Quality Control Engineer involves a combination of gaining in-depth understanding of its statistical tools, practicing its application in real-world quality control scenarios, and keeping abreast of the latest features and best practices. Here's a concise guide:
Learn the Basics: Start with the foundational aspects of Minitab, understanding its interface, and basic statistical functions. Minitab offers Quick Start tutorials to help you get familiar with the software.
Advanced Training: Dive deeper into specific tools relevant to Quality Control, such as Control Charts, Capability Analysis, and Design of Experiments. Minitab provides advanced training courses which are very beneficial.
Practice with Real Data: Apply what you've learned by working on projects that use real data. This practical experience is invaluable. Consider using datasets related to your field or public domain datasets for practice.
Utilize Online Forums and Communities: Engage with online communities and forums such as the Minitab Community to share knowledge, ask questions, and learn from the experiences of others.
Stay Updated: Minitab periodically updates its software with new features and tools. Keep yourself updated by visiting the Minitab Blog and subscribing to their newsletter.
Feedback and Suggestions: If you encounter limitations or have ideas for features that could improve your workflow, consider providing feedback to Minitab. They often consider user feedback for future updates.
By following these steps and actively seeking out opportunities to use Minitab in your quality control projects, you can significantly improve your proficiency and leverage the software's capabilities to enhance quality outcomes.
How to Display Minitab Skills on Your Resume

6. Quality Management Systems (QMS)
A Quality Management System (QMS) is a formalized system that documents processes, procedures, and responsibilities for achieving quality policies and objectives. It helps coordinate and direct an organization's activities to meet customer and regulatory requirements and improve its effectiveness and efficiency on a continuous basis. For a Quality Control Engineer, it provides a structured framework for ensuring product and service quality, compliance, and continuous improvement.
Why It's Important
Quality Management Systems (QMS) are crucial for a Quality Control Engineer as they provide a structured framework for consistently meeting customer requirements, enhancing satisfaction, and facilitating continuous improvement in processes and products.
How to Improve Quality Management Systems (QMS) Skills
Improving a Quality Management System (QMS) involves a continuous process of evaluation and enhancement to meet and exceed customer expectations. Here's a very short and concise guide tailored for a Quality Control Engineer:
Assess and Analyze Current QMS: Regularly review your current system's effectiveness using audits and process evaluations. ISO 9001:2015 provides a framework for quality management principles.
Engage Stakeholders: Involve all relevant stakeholders, including employees, suppliers, and customers, to gather insights and feedback. This collaborative approach ensures the system meets everyone's needs.
Continuous Training: Invest in ongoing training programs for staff to keep up with the latest quality standards and practices.
Implement Technology: Leverage quality management software tools to streamline processes, enhance document control, and improve data analysis.
Set Clear Objectives: Define clear, measurable goals aligned with customer expectations and business objectives. Use SMART criteria to ensure goals are specific, measurable, achievable, relevant, and time-bound.
Root Cause Analysis: When issues arise, employ root cause analysis techniques to identify and address the underlying causes instead of just treating symptoms. Techniques include 5 Whys and Fishbone Diagrams.
Continuous Improvement: Adopt a culture of continuous improvement, utilizing methodologies like Kaizen, Six Sigma, and Lean Manufacturing to systematically improve processes and eliminate waste.
Monitor and Review: Regularly review the system's performance against the set objectives and standards, using tools like internal audits and management reviews.
By following these steps and adopting a proactive approach, a Quality Control Engineer can significantly enhance the effectiveness of a Quality Management System, contributing to overall organizational success.
How to Display Quality Management Systems (QMS) Skills on Your Resume
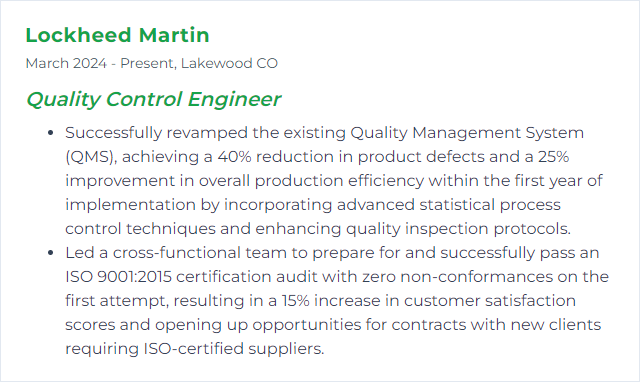
7. Root Cause Analysis
Root Cause Analysis (RCA) is a systematic process used by Quality Control Engineers to identify and determine the underlying causes of defects or problems in a product or process, aiming to implement corrective actions that prevent recurrence.
Why It's Important
Root Cause Analysis (RCA) is crucial for a Quality Control Engineer because it systematically identifies the underlying reasons for defects or problems, enabling the implementation of effective corrective actions to prevent recurrence, thereby ensuring product quality and customer satisfaction.
How to Improve Root Cause Analysis Skills
Improving Root Cause Analysis (RCA) for a Quality Control Engineer involves several key strategies:
Strengthen Team Collaboration: Foster a multidisciplinary team approach, ensuring diverse perspectives are considered. Team Collaboration Guide
Enhance Data Collection: Utilize both qualitative and quantitative data gathering methods for a comprehensive analysis. Data Collection Techniques
Implement Systematic Methods: Adopt structured RCA methodologies like the 5 Whys, Fishbone Diagram, or FMEA for systematic analysis. RCA Tools
Leverage Technology: Use software tools for data analysis and visualization to identify patterns and correlations. Quality Management Software
Focus on Training: Continuously educate the team on RCA techniques and critical thinking skills. Quality Training Resources
Establish a Knowledge Base: Document and share lessons learned to prevent future occurrences. Creating a Knowledge Base
Continuous Improvement: Regularly review and refine the RCA process based on feedback and outcomes. Continuous Improvement Guide
By incorporating these strategies, a Quality Control Engineer can significantly enhance the effectiveness of Root Cause Analysis within their organization.
How to Display Root Cause Analysis Skills on Your Resume
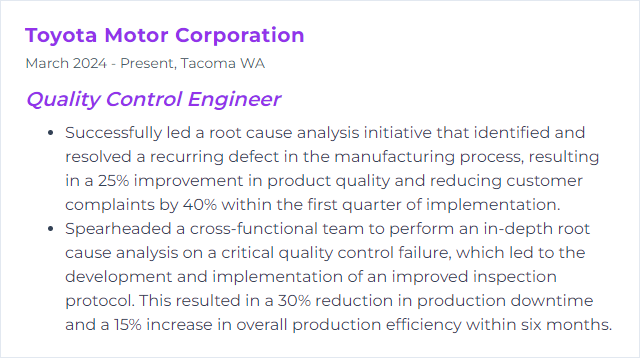
8. FMEA (Failure Mode and Effects Analysis)
FMEA (Failure Mode and Effects Analysis) is a systematic, step-by-step approach for identifying all possible failures in a design, a manufacturing or assembly process, or a product or service, analyzing the potential causes and effects of those failures, and prioritizing the necessary actions to mitigate the risks associated with these failures. For a Quality Control Engineer, it serves as a proactive method to improve product reliability and quality by preventing defects, enhancing safety, and increasing customer satisfaction.
Why It's Important
FMEA is important for a Quality Control Engineer because it proactively identifies potential failures in processes or products, assesses their impact, and prioritizes corrective actions, enhancing product quality, safety, and reliability while reducing costs and preventing defects.
How to Improve FMEA (Failure Mode and Effects Analysis) Skills
To improve FMEA (Failure Mode and Effects Analysis), follow these concise steps:
Cross-Functional Team: Build a diverse team with members from different departments (e.g., design, manufacturing, quality control) to provide comprehensive perspectives. ASQ provides insights on team roles.
Training: Ensure all team members have adequate training on the FMEA process and tools. AIAG offers FMEA training.
Historical Analysis: Leverage historical data and past FMEAs to identify recurring failure modes. Learn more about historical data analysis.
Risk Priority Number (RPN) Enhancement: Beyond traditional RPN, consider factors like detectability and customer impact for a more nuanced risk assessment. Quality-One discusses advanced RPN considerations.
Action Priority: Use an action priority table to prioritize issues based on severity, occurrence, and detection scores. AIAG & VDA FMEA Handbook provides guidelines.
Dynamic Document: Treat FMEA as a living document, regularly updating it as changes occur in design, process, or upon finding new failure modes. ASQ emphasizes the importance of updating FMEA.
Software Tools: Adopt specialized FMEA software for efficiency and consistency. PFMEA software options.
Integration with Other Quality Tools: Integrate FMEA with other quality tools like Control Plans and SPC for a more comprehensive quality strategy. Quality Digest discusses integration strategies.
By focusing on these areas, a Quality Control Engineer can significantly enhance the effectiveness of the FMEA process, leading to reduced risks and improved product quality.
How to Display FMEA (Failure Mode and Effects Analysis) Skills on Your Resume
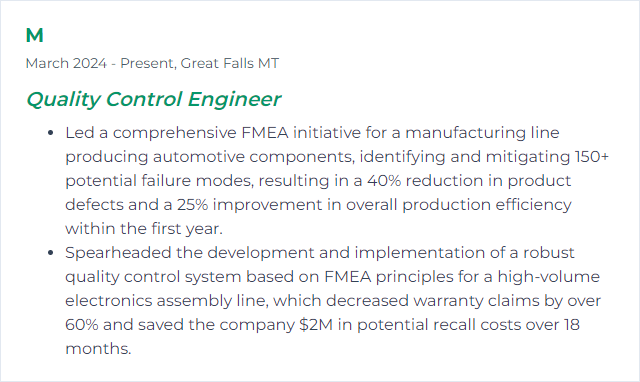
9. Kaizen
Kaizen is a Japanese philosophy and approach focusing on continuous, incremental improvements in productivity, efficiency, and quality, emphasizing eliminating waste and optimizing processes, particularly relevant for Quality Control Engineers in enhancing product quality and manufacturing workflows.
Why It's Important
Kaizen is important because it promotes continuous, incremental improvements in processes, enhancing quality, efficiency, and productivity, directly aligning with a Quality Control Engineer's goal of maintaining high standards in product and process quality.
How to Improve Kaizen Skills
To improve Kaizen, a Quality Control Engineer should focus on continuous, incremental improvements by engaging in the following actions:
Identify Areas for Improvement: Regularly assess processes to pinpoint inefficiencies or quality gaps. Tools like Pareto Charts can help in identifying the most significant areas to focus on.
Set Clear, Achievable Goals: Establish specific, measurable, achievable, relevant, and time-bound (SMART) goals to guide improvement efforts. More on SMART goals can be found at MindTools.
Engage the Team: Foster a culture of continuous improvement by involving all team members in Kaizen activities. Techniques such as brainstorming sessions can help in generating ideas and solutions from the entire team.
Implement Small Changes: Start with small, manageable changes to processes or procedures. This approach reduces resistance and makes it easier to adjust or refine solutions as needed.
Measure Results and Adjust: Use data to evaluate the effectiveness of implemented changes. Tools like Control Charts can be useful for monitoring performance before and after improvements.
Standardize Successful Practices: Once a change proves successful, standardize the new process across the relevant areas of operation to ensure consistency and long-term benefits.
Repeat the Process: Kaizen is a continuous cycle of improvement. Regularly review and refine processes to foster ongoing improvement.
By systematically applying these steps and adopting a mindset of continuous improvement, a Quality Control Engineer can effectively improve Kaizen in their operations.
How to Display Kaizen Skills on Your Resume
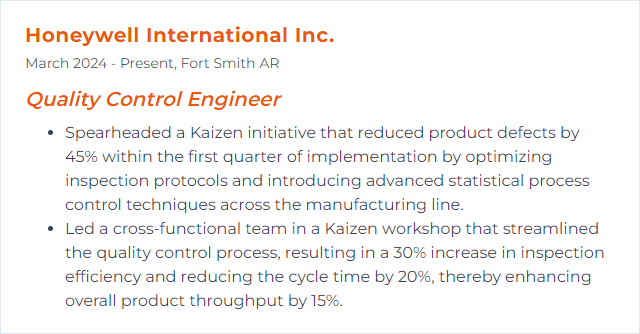
10. S Methodology
S Methodology, in the context of a Quality Control Engineer, refers to a systematic approach for improving and maintaining quality through standard procedures, statistical techniques, and continuous process control. It emphasizes on identifying, reducing, and eliminating variability in manufacturing processes to ensure product quality and reliability.
Why It's Important
The S Methodology is important for a Quality Control Engineer because it provides a structured approach to identify, analyze, and resolve quality issues, ensuring products meet specified standards and customer expectations efficiently and consistently.
How to Improve S Methodology Skills
Improving the S Methodology, particularly for a Quality Control Engineer, involves a focus on enhancing standardization, systematization, and simplification processes to improve quality and efficiency. Here’s a concise guide:
Standardization: Develop and implement clear, standardized procedures and criteria for all quality control processes. Utilize resources like ISO for international standards to ensure consistency and quality across operations.
Systematization: Leverage technology to create systematic approaches to quality control. Tools like Six Sigma provide a structured methodology for process improvement, minimizing variability, and enhancing quality.
Simplification: Identify and eliminate unnecessary steps in quality control processes to reduce complexity and improve efficiency. Techniques like Value Stream Mapping can help visualize and streamline processes, removing non-value-added activities.
By focusing on these areas, a Quality Control Engineer can significantly enhance the effectiveness of the S Methodology in their operations.
How to Display S Methodology Skills on Your Resume
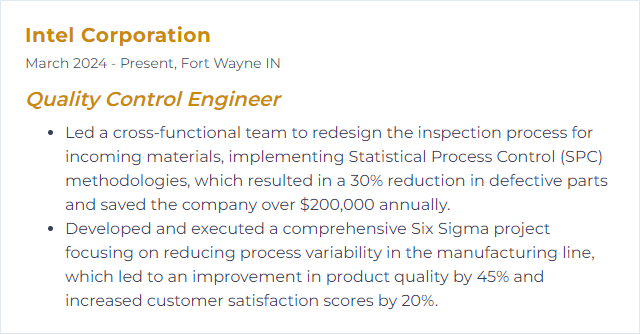
11. AutoCAD
AutoCAD is a computer-aided design (CAD) software used for creating precise 2D and 3D drawings and models, beneficial for Quality Control Engineers in designing, inspecting, and modifying engineering plans to ensure accuracy and compliance with standards.
Why It's Important
AutoCAD is crucial for Quality Control Engineers as it enables precise design and drafting, ensuring accuracy in specifications and tolerances, essential for maintaining high-quality standards in manufacturing and construction processes.
How to Improve AutoCAD Skills
Improving AutoCAD skills, particularly for a Quality Control Engineer, involves focusing on precision, efficiency, and leveraging advanced features. Here’s a concise guide:
Master Precision Tools: Understanding and utilizing AutoCAD's precision tools like Object Snaps, Object Snap Tracking, and Polar Tracking can significantly improve the accuracy of your drawings. Autodesk's tutorial on precision drawing provides a great starting point.
Use Templates and Standards: Implement and use standardized templates and layers for consistent quality across all drawings. This ensures that all designs adhere to the same quality and specification standards, crucial for a Quality Control Engineer. Autodesk's guide on creating templates can be helpful.
Automate Repetitive Tasks: Learning to write basic AutoLISP scripts or using AutoCAD's Action Recorder can automate repetitive tasks, increasing efficiency and reducing errors. Autodesk provides resources on getting started with AutoLISP.
Stay Updated: Keeping up-to-date with the latest AutoCAD versions and features can ensure you're leveraging the most advanced and efficient tools available. Autodesk often adds features that can improve workflow and quality. What’s new in AutoCAD is a good place to check annually.
Enhance Your Skills with Advanced Training: Participating in advanced AutoCAD training courses specifically designed for engineering professionals can sharpen your skills and introduce you to industry-specific best practices. Websites like LinkedIn Learning and Udemy offer courses tailored to different skill levels and specializations.
By focusing on these areas, a Quality Control Engineer can significantly improve their proficiency and efficiency in AutoCAD, leading to higher quality designs and more effective quality control processes.
How to Display AutoCAD Skills on Your Resume
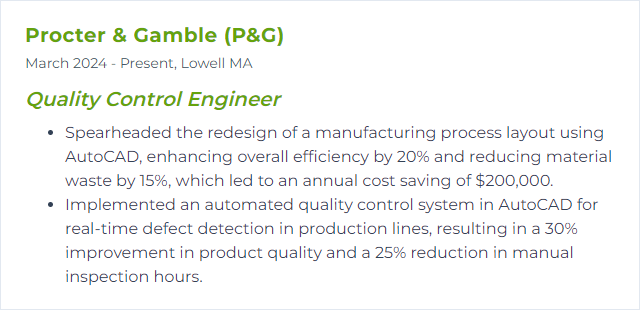
12. SAP Quality Module
The SAP Quality Management (QM) module is a comprehensive software solution designed for managing all aspects of quality control and assurance processes within manufacturing and service industries. It enables Quality Control Engineers to plan, execute, and track quality inspections and tests on materials and products, manage defects, and ensure compliance with quality standards, thereby facilitating continuous improvement in product quality and customer satisfaction.
Why It's Important
The SAP Quality Module is crucial for a Quality Control Engineer as it streamlines and automates the processes of planning, executing, and tracking quality control activities, ensuring product compliance with industry standards and enhancing customer satisfaction.
How to Improve SAP Quality Module Skills
Improving the SAP Quality Module (QM) involves optimizing its functionalities to enhance quality management processes. Here are concise strategies tailored for a Quality Control Engineer:
Integrate with Other Modules: Ensure seamless integration with modules like MM (Materials Management), PP (Production Planning), and SD (Sales and Distribution) for real-time data sharing and process efficiency. SAP Integration Guide.
Customize Quality Inspections: Tailor inspection plans, quality notifications, and inspection lot processing to meet specific industry standards and regulatory requirements. SAP QM Configuration.
Leverage Data Analytics: Utilize SAP’s advanced analytics to monitor quality trends, predict issues, and implement preventive measures. SAP Analytics Cloud.
Automate Processes: Implement automation for repetitive tasks such as data entry and report generation to increase efficiency and reduce human error. SAP Intelligent Robotic Process Automation.
Continuous Training: Invest in ongoing training and support for users to ensure they are leveraging the full capabilities of the SAP QM module. SAP Training and Certification.
Feedback Loop: Establish a feedback loop with end-users and stakeholders to continuously identify areas for improvement and adapt the QM module accordingly.
By focusing on these key areas, a Quality Control Engineer can significantly enhance the effectiveness of the SAP Quality Module within their organization.
How to Display SAP Quality Module Skills on Your Resume
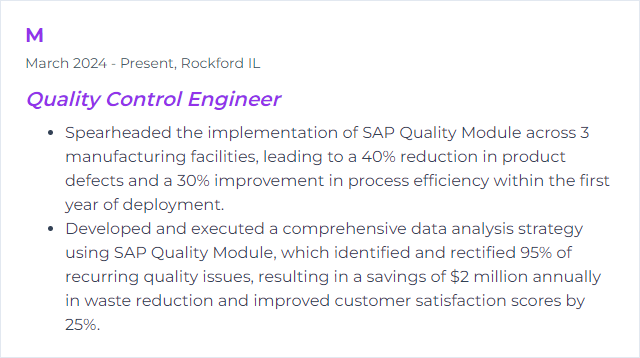