Top 12 Quality Control Assistant Skills to Put on Your Resume
In the competitive field of quality control, having a resume that stands out is essential for landing a desirable position. Highlighting the top skills of a Quality Control Assistant not only showcases your expertise but also demonstrates to potential employers your commitment to maintaining high standards and contributing effectively to their operations.
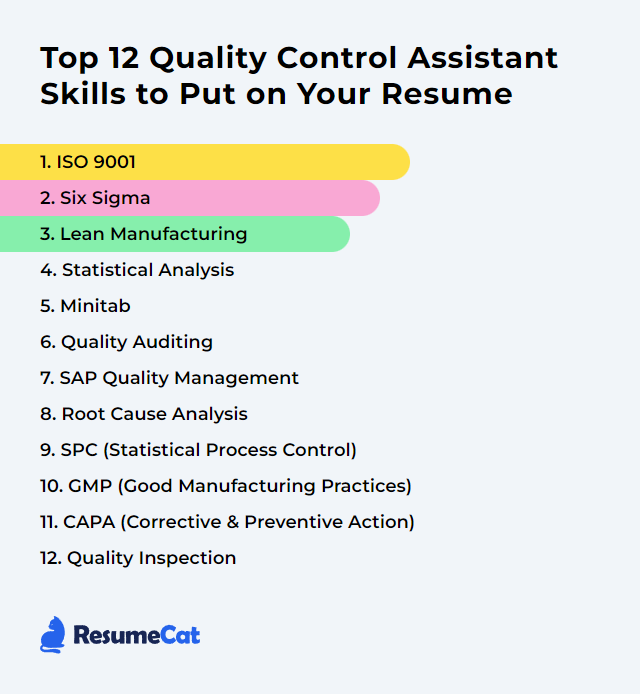
Quality Control Assistant Skills
- ISO 9001
- Six Sigma
- Lean Manufacturing
- Statistical Analysis
- Minitab
- Quality Auditing
- SAP Quality Management
- Root Cause Analysis
- SPC (Statistical Process Control)
- GMP (Good Manufacturing Practices)
- CAPA (Corrective and Preventive Action)
- Quality Inspection
1. ISO 9001
ISO 9001 is an international standard that specifies requirements for a quality management system (QMS). Organizations use the standard to demonstrate the ability to consistently provide products and services that meet customer and regulatory requirements. For a Quality Control Assistant, it guides the implementation and maintenance of processes, procedures, and responsibilities to achieve quality objectives and enhance customer satisfaction.
Why It's Important
ISO 9001 is important because it ensures a consistent quality of products and services, enhancing customer satisfaction and providing a solid foundation for continuous improvement within the organization. For a Quality Control Assistant, it offers clear guidelines for maintaining quality standards and improving processes.
How to Improve ISO 9001 Skills
Improving ISO 9001 as a Quality Control Assistant involves focusing on continuous improvement, enhancing customer satisfaction, and ensuring compliance with the standard’s requirements. Here's a concise guide:
Understand ISO 9001 Requirements: Familiarize yourself thoroughly with the ISO 9001 standard to ensure all processes meet the criteria. ISO 9001:2015 is the reference document.
Engage in Training: Participate in ISO 9001 training to understand the quality management system (QMS) processes deeply and how to improve them.
Implement a Continuous Improvement Process: Use tools like Plan-Do-Check-Act (PDCA) cycle to identify areas for improvement continuously. More about PDCA can be found on ASQ’s website.
Enhance Customer Satisfaction: Regularly gather and analyze customer feedback to improve products and services. Tools like customer satisfaction surveys can be beneficial.
Internal Audits: Conduct regular internal audits to ensure compliance with ISO 9001 standards and identify areas for improvement.
Management Review: Participate in management review meetings to discuss audit findings, customer feedback, and the performance of the QMS, aiming for strategic improvements.
Corrective and Preventive Actions: Implement corrective and preventive actions to address non-conformities and prevent their recurrence.
Documentation and Record Keeping: Maintain comprehensive documentation and records as evidence of compliance and improvement efforts.
Employee Engagement: Engage all employees in quality objectives and continuous improvement through training and communication.
Leverage Quality Management Tools: Utilize quality management tools such as Six Sigma, Kaizen, or 5S for systematic improvement. An overview of these can be found on MindTools.
Improving ISO 9001 involves a commitment to ongoing learning and adaptation, focusing on quality and customer satisfaction at every level of the organization.
How to Display ISO 9001 Skills on Your Resume
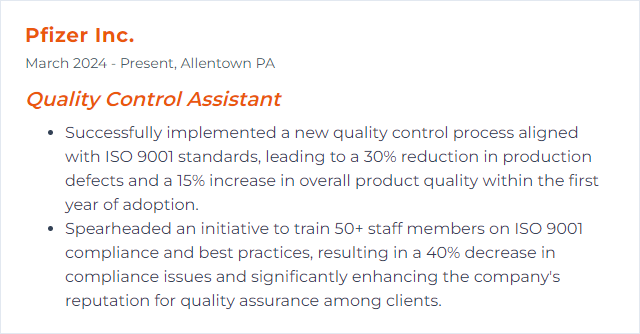
2. Six Sigma
Six Sigma is a data-driven methodology and set of tools aimed at process improvement by reducing variability and defects to improve quality and efficiency.
Why It's Important
Six Sigma is important as it provides a systematic approach to minimize errors, enhance process efficiency, and ensure consistent quality, thereby improving customer satisfaction and business profitability, crucial for a Quality Control Assistant to maintain high standards.
How to Improve Six Sigma Skills
Improving Six Sigma involves continuous learning, applying best practices, and leveraging tools effectively. As a Quality Control Assistant, focus on:
Enhance Your Knowledge: Stay updated with the latest Six Sigma methodologies and tools. Engage in Six Sigma certification courses relevant to your level (Yellow, Green, or Black Belt).
Utilize Six Sigma Tools Efficiently: Master tools like DMAIC (Define, Measure, Analyze, Improve, Control) and DMADV (Define, Measure, Analyze, Design, Verify) for problem-solving. Familiarize yourself with statistical software like Minitab for data analysis.
Collaborate and Communicate: Work closely with cross-functional teams. Sharing insights and learning from others can uncover new improvement opportunities. Tools like Slack can facilitate better communication.
Implement Quality Projects: Apply your knowledge by leading small-scale Six Sigma projects within your organization. Document your successes and lessons learned.
Seek Feedback and Iterate: Regularly seek feedback on the processes and your performance. Use this feedback to refine your approach and drive continuous improvement.
By focusing on these areas and engaging in continuous learning and application, you can significantly contribute to your organization's Six Sigma initiatives.
How to Display Six Sigma Skills on Your Resume
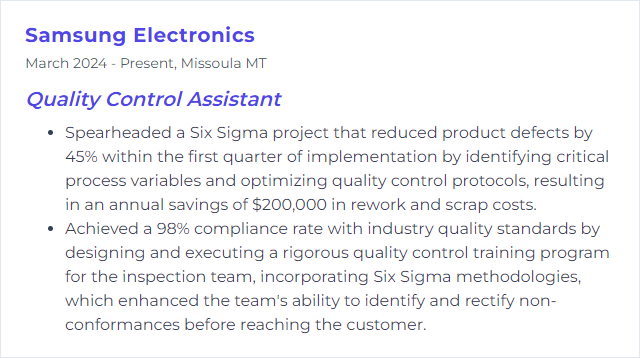
3. Lean Manufacturing
Lean Manufacturing is a systematic approach aimed at minimizing waste within manufacturing systems while maximizing productivity, primarily focusing on enhancing quality and efficiency from the perspective of a Quality Control Assistant.
Why It's Important
Lean Manufacturing is important because it optimizes production efficiency, reduces waste, and improves quality, directly supporting the goals of a Quality Control Assistant by enhancing product consistency and minimizing defects.
How to Improve Lean Manufacturing Skills
Improving Lean Manufacturing, especially from a Quality Control Assistant perspective, involves streamlining processes, reducing waste, and enhancing product quality. Here are concise strategies:
- Implement Continuous Improvement: Adopt Kaizen principles to encourage ongoing, incremental improvements in all aspects of the manufacturing process.
- Standardize Work Processes: Develop and utilize standard work procedures to ensure consistency and efficiency, reducing variability and defects.
- Utilize 5S Methodology: Apply the 5S system — Sort, Set in Order, Shine, Standardize, Sustain — to organize the workplace, leading to improved productivity and safety.
- Employ Visual Management: Use visual controls to make the flow of processes and current state of work visible, aiding in quicker identification and resolution of quality issues.
- Conduct Root Cause Analysis: When defects occur, use tools like the 5 Whys to investigate and address the underlying cause, preventing recurrence.
- Foster a Quality Culture: Promote an organizational culture that prioritizes quality, where every team member feels responsible for maintaining high standards. ASQ’s Quality Culture offers insights on building this environment.
- Leverage Quality Control Circles: Encourage the formation of quality control circles — small groups that regularly meet to identify, analyze, and solve work-related problems collectively.
- Apply Poka-Yoke (Error Proofing): Implement error-proofing techniques to prevent mistakes before they occur, enhancing overall product quality.
By focusing on these strategies, a Quality Control Assistant can significantly contribute to the improvement of Lean Manufacturing in their organization.
How to Display Lean Manufacturing Skills on Your Resume
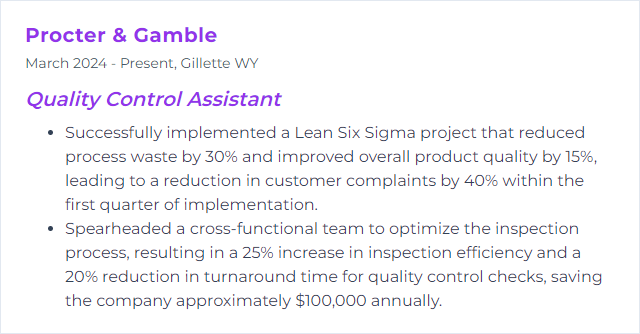
4. Statistical Analysis
Statistical analysis in the context of a Quality Control Assistant involves collecting, examining, and interpreting data to ensure products or processes meet established quality standards. It helps in identifying trends, anomalies, or deviations from the norm, allowing for informed decision-making to maintain or improve quality.
Why It's Important
Statistical analysis is crucial for a Quality Control Assistant because it enables precise measurement and control of product quality, identifies trends and anomalies in production processes, ensures compliance with quality standards, and facilitates data-driven decision-making to improve efficiency and reduce defects.
How to Improve Statistical Analysis Skills
Improving statistical analysis, especially in a Quality Control context, involves a few key steps focused on enhancing accuracy, reliability, and decision-making processes. Here's a concise guide:
Understand the Basics: Solidify your foundation in statistics and quality control principles. Khan Academy offers comprehensive lessons on statistics and probability.
Utilize Software Tools: Master statistical software tools like Minitab, R, or SPSS. Minitab provides a dedicated page for Quality Control features.
Implement SPC (Statistical Process Control): Apply SPC techniques to monitor and control quality during the manufacturing process. ASQ (American Society for Quality) has resources and information on SPC.
Lean on Descriptive and Inferential Statistics: Use descriptive statistics to summarize data. Apply inferential statistics to make predictions or decisions based on data sampling. This guide from Investopedia clarifies the concepts.
Embrace Continuous Learning: Quality control and statistical analysis evolve. Engage with platforms like Coursera or edX for courses on statistics and quality management. Coursera’s Statistics with Python is a good starting point.
Practical Application and Experimentation: Nothing beats hands-on experience. Implement what you've learned in real-world scenarios and learn from the outcomes.
Quality Control Forums and Communities: Join online forums or communities related to Quality Control and statistics. Engaging in discussions on platforms like Elsmar Cove Quality Forum can provide valuable insights and practical tips.
By focusing on these areas, you can significantly improve your statistical analysis skills in a Quality Control environment.
How to Display Statistical Analysis Skills on Your Resume
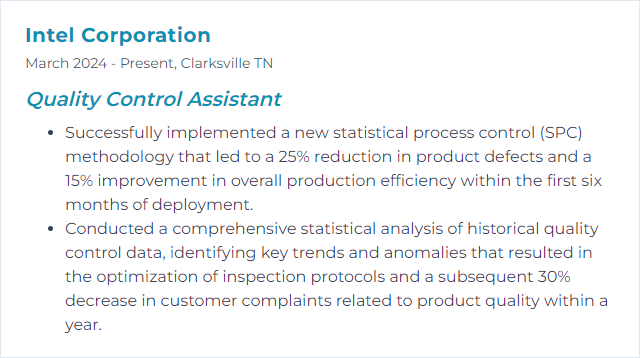
5. Minitab
Minitab is a statistical software package designed for data analysis and quality control. It provides tools for statistical analysis, visualization, and process improvement, helping Quality Control Assistants to analyze and interpret quality data efficiently.
Why It's Important
Minitab is important for a Quality Control Assistant because it provides advanced statistical analysis, visualizations, and predictive modeling tools to easily identify trends, solve problems, and make data-driven decisions to ensure product quality and process improvements.
How to Improve Minitab Skills
Improving your proficiency in Minitab as a Quality Control Assistant can enhance your data analysis and quality improvement initiatives. Here are concise steps to improve your Minitab skills:
Learn the Basics: Familiarize yourself with Minitab's interface and basic functions. Start with Minitab's Quick Start guide to understand the layout and basic operations.
Understand Statistics: Since Minitab is a statistical software, improving your statistical knowledge can help you use Minitab more effectively. Explore the Statistics Glossary on Minitab's support page.
Use Minitab Help and Support: Minitab’s help function is a great resource for understanding specific functions and features. Visit the Minitab Support page for tutorials, tips, and troubleshooting.
Take Online Courses: Enroll in online courses tailored to improving Minitab skills. Minitab offers training courses that range from beginner to advanced levels.
Practice Regularly: Apply what you learn in real-world scenarios or practice exercises. Regular use will enhance your familiarity and efficiency with the software.
Join Forums and Communities: Engage with Minitab forums and online communities to exchange knowledge, tips, and experiences. The Minitab Community is a great place to start.
Stay Updated: Minitab regularly updates its software. Stay informed about new features and updates by visiting the Minitab Blog.
By following these steps and actively seeking out resources and opportunities to apply your knowledge, you can significantly improve your Minitab skills and contribute more effectively to quality control efforts.
How to Display Minitab Skills on Your Resume
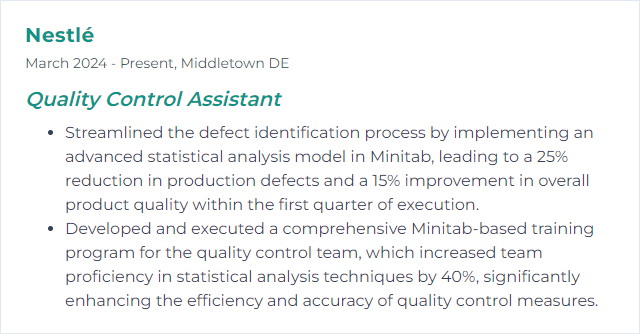
6. Quality Auditing
Quality auditing is the systematic examination of a quality system performed by an internal or external auditor or an audit team. It's an important part of an organization's quality management system and involves reviewing processes and procedures to ensure they meet defined standards of quality. For a Quality Control Assistant, it means actively participating in or supporting the audit process to verify that all quality requirements are being met within the organization.
Why It's Important
Quality auditing is crucial as it ensures that the products or services meet established standards and requirements, identifies areas for improvement, and enhances customer satisfaction by preventing defects and errors. For a Quality Control Assistant, it ensures their work aligns with both company and regulatory standards, safeguarding the company's reputation and compliance.
How to Improve Quality Auditing Skills
Improving quality auditing involves a focused approach on enhancing skills, processes, and tools to ensure thorough evaluations and compliance with applicable standards. Here are concise strategies tailored for a Quality Control Assistant:
Enhance Skills and Knowledge: Continuously update your knowledge on the latest quality standards and auditing techniques through reputable sources like ASQ (American Society for Quality).
Implement a Systematic Approach: Use a structured method for audits, such as checklists or software tools, to ensure all areas are covered systematically. Resources like ISO (International Organization for Standardization) offer guidelines and standards for developing effective audit systems.
Use Technology: Leverage technology like quality management software to streamline the auditing process, improve accuracy, and facilitate the storage and retrieval of audit documents. Explore platforms like Intelex for comprehensive solutions.
Continuous Improvement: Adopt a mindset of continuous improvement by regularly reviewing and updating auditing processes based on feedback and findings. The Plan-Do-Check-Act (PDCA) cycle is a useful framework for this.
Professional Development: Participate in professional development opportunities such as workshops, webinars, and certification programs offered by organizations like ASQ to stay current in the field and enhance your auditing skills.
Stakeholder Engagement: Engage actively with all stakeholders to understand their concerns and expectations. This collaborative approach can lead to more effective audits and buy-in for necessary changes.
By focusing on these strategies, a Quality Control Assistant can significantly improve their auditing effectiveness and contribute to the overall quality objectives of their organization.
How to Display Quality Auditing Skills on Your Resume
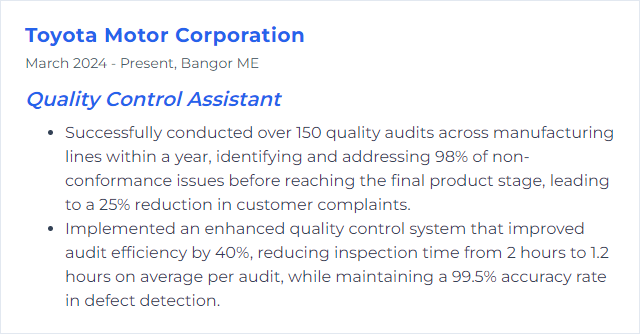
7. SAP Quality Management
SAP Quality Management (QM) is a component of the SAP ERP system that helps businesses manage their quality processes, including quality planning, inspection, control, and certification. It supports tasks such as defining quality requirements, monitoring quality control processes, and managing defects or non-conformities. For a Quality Control Assistant, it provides tools and data necessary to ensure products or services meet the defined quality standards and compliance requirements.
Why It's Important
SAP Quality Management (QM) is crucial for a Quality Control Assistant as it streamlines and automates the processes of quality planning, inspection, and control. This ensures consistent product quality, compliance with standards, and minimizes defects, leading to improved customer satisfaction and reduced costs related to rework and waste.
How to Improve SAP Quality Management Skills
Improving SAP Quality Management (QM) involves streamlining processes, enhancing data accuracy, and leveraging SAP's integrated features effectively. Here are concise strategies tailored for a Quality Control Assistant:
Understand SAP QM Modules: Deepen your knowledge of SAP QM modules to utilize them fully. SAP's official training can be a good start.
Automate Data Collection: Use SAP's data collection capabilities to automate the entry of quality data, reducing manual errors.
Implement Continuous Improvement: Adopt a Kaizen or continuous improvement approach by regularly reviewing SAP QM data and processes. Tools like SAP Fiori apps for QM can provide insights for improvement.
Enhance Collaboration: Facilitate better communication with other departments using SAP's collaboration tools. SAP Jam Collaboration can help streamline communication regarding quality issues.
Stay Updated: Regularly update your SAP system and stay informed about new features or updates in SAP QM that can benefit your role. The SAP Road Map Explorer can be useful for this.
Customize Reports: Customize SAP QM reports to meet your specific needs for data analysis and decision-making. SAP's Analytics Cloud can offer advanced analytics capabilities.
Quality Notifications: Utilize SAP's quality notification feature to efficiently manage and resolve quality issues. Learn more about configuring this feature from the SAP Help Portal.
Training and Support: Continuously improve your SAP skills and those of your team. Use the SAP Learning Hub for ongoing education and support.
By focusing on these areas, a Quality Control Assistant can significantly contribute to improving the quality management process within their SAP environment.
How to Display SAP Quality Management Skills on Your Resume
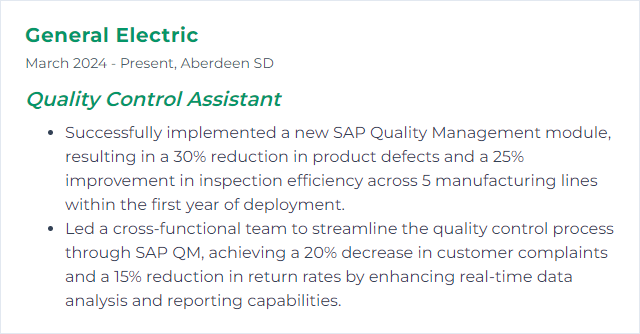
8. Root Cause Analysis
Root Cause Analysis (RCA) is a systematic process for identifying the underlying reasons for a problem or defect in a product or process, aiming to implement solutions that prevent recurrence. For a Quality Control Assistant, it involves pinpointing the fundamental issue(s) that led to a quality deviation, ensuring that corrective actions address the root cause rather than just the symptoms.
Why It's Important
Root Cause Analysis (RCA) is crucial for a Quality Control Assistant because it enables the identification and resolution of the fundamental problems causing defects or failures, ensuring the improvement and maintenance of product quality and process efficiency.
How to Improve Root Cause Analysis Skills
Improving Root Cause Analysis (RCA) in the context of a Quality Control Assistant role involves a systematic approach to identify the underlying reasons for a problem, with the aim of implementing long-term solutions. Here's a concise guide:
Define the Problem Clearly: Start with a precise description of the issue, including when and where it was observed. Use data and evidence to outline the problem's impact.
Gather Data: Collect relevant data around the problem, focusing on the "5 Ws" (Who, What, Where, When, Why) to build a comprehensive view of the issue.
Use RCA Tools: Employ RCA tools such as the 5 Whys Technique or the Fishbone Diagram to systematically identify potential root causes. These tools help in drilling down to the core of the problem.
Analyze and Identify Root Causes: Analyze the information gathered to distinguish between symptoms and root causes. This step may involve brainstorming sessions with team members and reviewing historical data.
Develop and Implement Solutions: Once the root causes are identified, develop solutions that address them directly. Prioritize solutions based on their potential impact and feasibility.
Monitor and Adjust: After implementing solutions, closely monitor the outcomes to ensure the problem is resolved. Be prepared to adjust your approach if the initial solutions don't fully address the issue.
Document and Share Learnings: Document the entire RCA process, including the findings, decisions made, and outcomes achieved. Sharing these learnings within the organization can prevent future occurrences of similar issues.
For more detailed guidance, the American Society for Quality (ASQ) offers resources and training on RCA and other quality control tools. Additionally, The International Organization for Standardization (ISO) provides standards and best practices that can enhance the quality control processes, including RCA.
How to Display Root Cause Analysis Skills on Your Resume
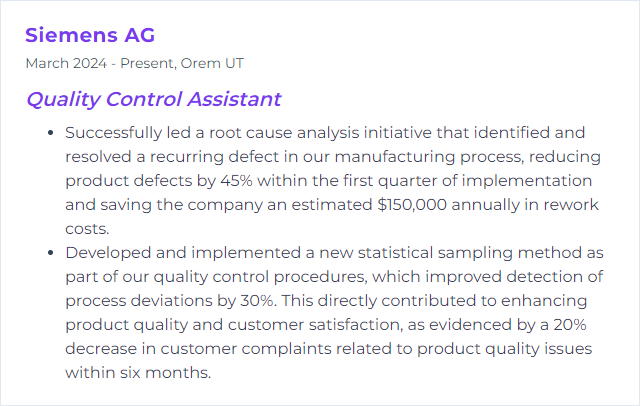
9. SPC (Statistical Process Control)
SPC, or Statistical Process Control, is a method used in quality control to monitor and control a process by using statistical techniques. It helps to ensure that the process operates efficiently, producing more specification-conforming products with less waste. SPC can be applied to any process where the "conforming product" (product meeting specifications) output can be measured. Key tools include control charts, which are used to detect performance trends, variations, and process stability over time, enabling proactive quality adjustments.
Why It's Important
SPC (Statistical Process Control) is crucial because it enables continuous monitoring and control of a process through statistical methods to ensure it operates at its fullest potential, minimizing variability and defects. This leads to higher quality, efficiency, and customer satisfaction, directly supporting the role of a Quality Control Assistant in maintaining product standards.
How to Improve SPC (Statistical Process Control) Skills
Improving Statistical Process Control (SPC) involves a focused approach on refining data collection, analysis, and process improvement strategies. Here’s a concise guide for a Quality Control Assistant seeking to enhance SPC:
Educate and Train: Ensure you and your team are well-versed in SPC principles and tools. Continuous learning is key. ASQ’s SPC resources offer a good starting point.
Data Integrity: Prioritize accurate data collection. Implement automated data collection systems where possible to reduce human error. NIST’s Engineering Statistics Handbook provides guidelines on ensuring data integrity.
Process Mapping: Understand your process thoroughly using process mapping. It helps in identifying critical points for SPC application. Lucidchart’s guide on process mapping can be a helpful resource.
Select Appropriate Tools: Use the right SPC tools (e.g., control charts, Pareto charts) tailored to your specific process requirements. Minitab’s guide helps in choosing the right control chart.
Implement and Monitor: Implement SPC on chosen processes and continuously monitor performance. Adjustments and refinements should be data-driven.
Analyze and Act: Regularly analyze SPC data to identify trends, shifts, or any signs of process variability. Implement corrective actions promptly to mitigate issues.
Engage the Team: SPC should be a team effort. Engage with all stakeholders, encouraging feedback and collaborative problem-solving.
Review and Adapt: SPC is not a set-and-forget system. Regularly review its effectiveness and adapt strategies as necessary. Continuous improvement should be the goal.
By focusing on these areas, a Quality Control Assistant can significantly contribute to improving SPC within their organization, leading to enhanced product quality and process efficiency.
How to Display SPC (Statistical Process Control) Skills on Your Resume
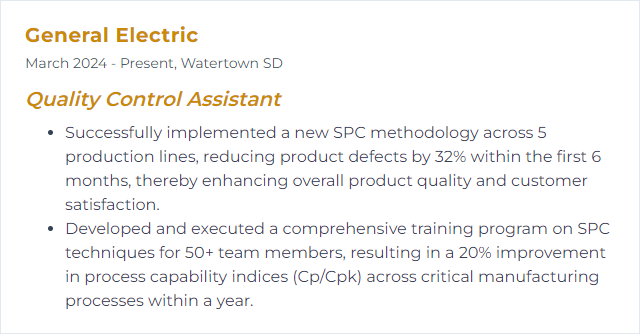
10. GMP (Good Manufacturing Practices)
GMP (Good Manufacturing Practices) are standardized guidelines ensuring products are consistently produced and controlled according to quality standards. They cover all aspects of production from the starting materials, premises, and equipment to the training and personal hygiene of staff. For a Quality Control Assistant, GMP involves ensuring these standards are met through monitoring, testing, and documenting processes to guarantee product safety and quality.
Why It's Important
GMP ensures that products are consistently produced and controlled according to quality standards, minimizing risks involved in production that cannot be eliminated through testing the final product. For a Quality Control Assistant, it's crucial for ensuring product safety, efficacy, and quality, thereby protecting consumers and upholding the company's reputation.
How to Improve GMP (Good Manufacturing Practices) Skills
Improving Good Manufacturing Practices (GMP) as a Quality Control Assistant involves focusing on several key areas to ensure product quality and safety. Here's a concise guide:
Education and Training: Continuously educate yourself and the team on GMP standards and updates. FDA and WHO provide resources and guidelines for training.
Documentation: Ensure all processes, changes, and deviations are accurately documented. Implement Document Control practices for maintaining and accessing records efficiently.
Quality Control Systems: Regularly review and update quality control procedures. Familiarize yourself with tools and systems that enhance Quality Management.
Auditing and Inspections: Conduct regular internal audits to identify areas for improvement. Utilize Audit Checklists to ensure comprehensive evaluations.
Feedback and Continuous Improvement: Encourage feedback from employees at all levels. Implement a Continuous Improvement process to address issues and enhance GMP practices.
Corrective and Preventive Actions (CAPA): Develop a robust CAPA system to address non-conformances. Learn more about CAPA from FDA’s guidance.
By focusing on these areas and leveraging the resources provided, you can significantly improve GMP practices in your role as a Quality Control Assistant.
How to Display GMP (Good Manufacturing Practices) Skills on Your Resume
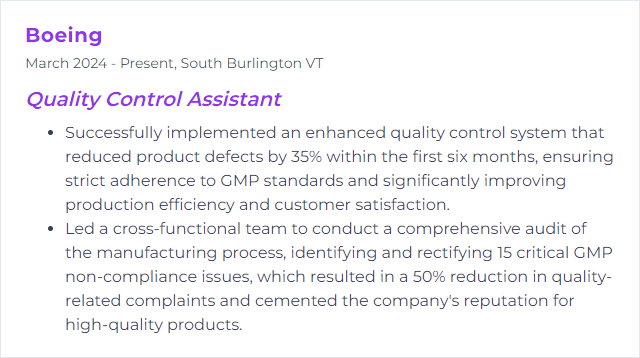
11. CAPA (Corrective and Preventive Action)
CAPA (Corrective and Preventive Action) is a process used in quality management to identify, address, and prevent the recurrence of non-conformities or issues. It involves taking corrective actions to fix immediate problems and preventive actions to mitigate the risk of such problems occurring in the future.
Why It's Important
CAPA is crucial for a Quality Control Assistant as it systematically identifies, addresses, and prevents defects in products or processes, ensuring compliance, enhancing product quality, and maintaining customer satisfaction.
How to Improve CAPA (Corrective and Preventive Action) Skills
Improving CAPA (Corrective and Preventive Action) involves a structured approach focusing on identifying, addressing, and preventing non-conformities. For a Quality Control Assistant, consider the following concise steps:
Identify and Document: Clearly define and document the issue or non-conformity. Use tools like root cause analysis to identify the underlying cause.
Evaluate and Plan: Assess the risk and impact of the identified issue. Develop a corrective and/or preventive action plan, setting clear objectives and timelines. The SMART criteria can guide setting effective goals.
Implement: Execute the action plan, ensuring all stakeholders are informed and involved as necessary. Utilize project management tools to track progress.
Review and Monitor: Regularly review the effectiveness of the action taken. Use quality management systems for ongoing monitoring and adjustments.
Documentation and Training: Document all steps taken and outcomes achieved. Provide training and updates to relevant staff to prevent recurrence. Explore resources like ASQ's Training for professional development.
Continuous Improvement: Incorporate lessons learned into the quality management system, promoting a culture of continuous improvement. The Plan-Do-Check-Act (PDCA) cycle can facilitate this process.
Remember, effective CAPA is about proactive prevention, not just reactive correction.
How to Display CAPA (Corrective and Preventive Action) Skills on Your Resume
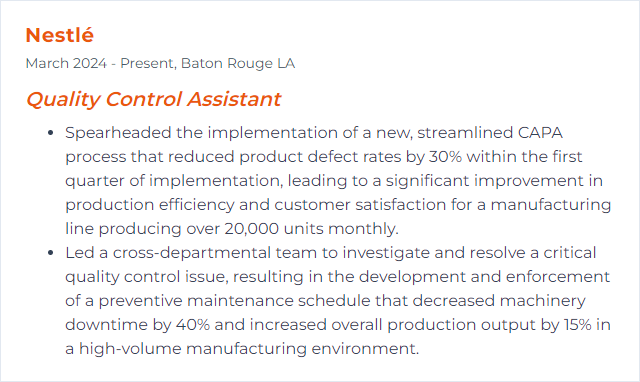
12. Quality Inspection
Quality Inspection is the process of evaluating and verifying products, components, or materials against specified standards or criteria to ensure they meet quality requirements before they are accepted or rejected. It is a critical task performed by a Quality Control Assistant to ensure that only products meeting the organization's quality standards are delivered to customers.
Why It's Important
Quality inspection ensures products meet established standards of excellence, minimizing defects, ensuring safety, and maintaining customer satisfaction, which are crucial for a Quality Control Assistant to uphold the integrity and reputation of the brand.
How to Improve Quality Inspection Skills
To improve Quality Inspection as a Quality Control Assistant, focus on the following strategies:
Implement Automation: Use automated inspection tools and software for more consistent and efficient checks. Tools like Cognex offer advanced imaging and artificial intelligence to enhance inspection quality.
Continuous Training: Regularly update your skills and knowledge on the latest quality control techniques and tools through platforms like Coursera or LinkedIn Learning.
Standardize Processes: Establish clear, standardized inspection procedures to ensure consistency. The ISO provides internationally recognized standards that can be adopted.
Implement Statistical Process Control (SPC): Use SPC techniques to monitor and control quality during the manufacturing process. Tools like Minitab offer comprehensive SPC solutions.
Engage with Suppliers: Work closely with suppliers to ensure materials meet your quality standards from the start. Resources like the ASQ offer guidelines on effective supplier management.
Foster a Quality Culture: Encourage a culture that prioritizes quality at all levels of the organization. The European Foundation for Quality Management (EFQM) provides frameworks to help organizations develop such cultures.
By focusing on these areas, a Quality Control Assistant can significantly improve the effectiveness of quality inspections.
How to Display Quality Inspection Skills on Your Resume
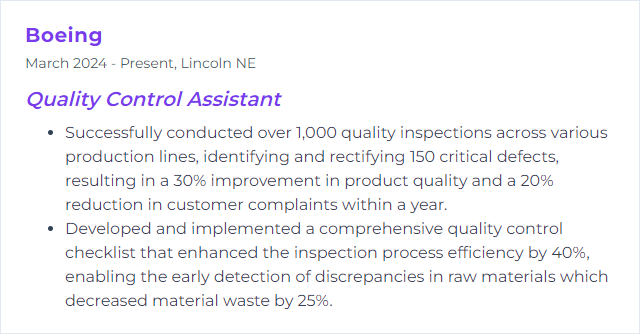