Top 12 Quality Control Coordinator Skills to Put on Your Resume
In today's competitive job market, standing out as a Quality Control Coordinator requires showcasing a unique set of skills on your resume that demonstrate your expertise and dedication to maintaining the highest standards of quality. This article outlines the top 12 skills you need to highlight, ensuring you capture the attention of potential employers and position yourself as a prime candidate for the role.
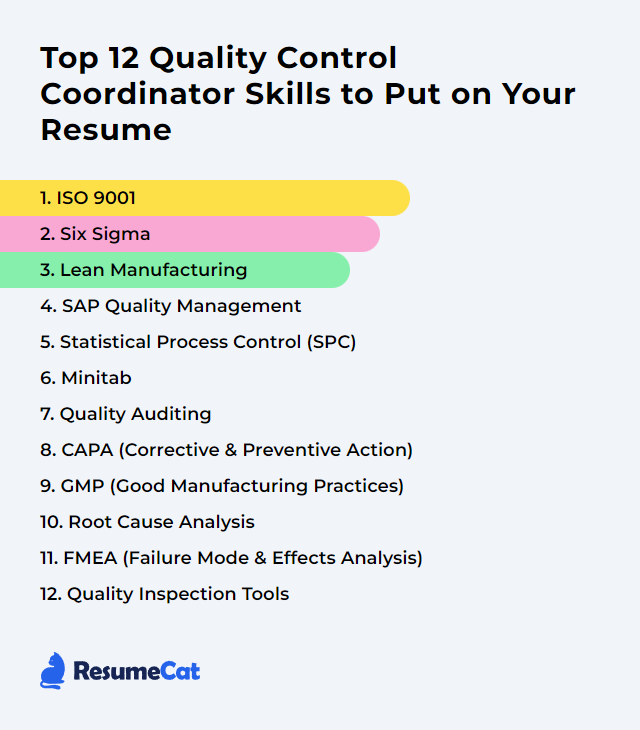
Quality Control Coordinator Skills
- ISO 9001
- Six Sigma
- Lean Manufacturing
- SAP Quality Management
- Statistical Process Control (SPC)
- Minitab
- Quality Auditing
- CAPA (Corrective and Preventive Action)
- GMP (Good Manufacturing Practices)
- Root Cause Analysis
- FMEA (Failure Mode and Effects Analysis)
- Quality Inspection Tools
1. ISO 9001
ISO 9001 is an international standard for quality management systems (QMS), providing a framework for companies to ensure they meet customer and regulatory requirements consistently and enhance customer satisfaction. For a Quality Control Coordinator, it guides establishing, implementing, and improving quality control processes to meet these standards.
Why It's Important
ISO 9001 is important for a Quality Control Coordinator because it provides a framework for consistent quality management practices, ensuring products and services meet customer and regulatory requirements, thereby enhancing customer satisfaction and operational efficiency.
How to Improve ISO 9001 Skills
Improving your ISO 9001 Quality Management System (QMS) involves a continuous process of evaluation and action to enhance quality and efficiency. As a Quality Control Coordinator, focusing on the following key areas can help you make impactful improvements:
Engage Leadership: Ensure top management actively supports and participates in the QMS processes. Leadership’s commitment is vital for fostering a quality-centric culture throughout the organization. ISO 9001 Leadership provides insights on leadership responsibilities.
Employee Involvement: Engage employees at all levels by providing appropriate training, resources, and motivation to participate actively in quality improvement. The ISO 9001 Training page from ASQ offers resources for enhancing employee involvement and competence.
Process Approach: Focus on understanding and managing processes interrelations within the QMS to enhance efficiency and effectiveness. Utilize process mapping and analysis tools. ISO's Process Approach provides guidance on implementing a process approach.
Continuous Improvement: Implement a culture of continuous improvement using tools such as Plan-Do-Check-Act (PDCA) and Six Sigma. Continuous improvement should be an ongoing effort to improve products, services, or processes. ASQ's Continuous Improvement section offers insights and tools.
Customer Focus: Regularly gather, analyze, and act on customer feedback to improve customer satisfaction and meet customer requirements efficiently. The ISO 9001 Customer Focus document details strategies for enhancing customer satisfaction.
Risk Management: Implement a risk management process to identify, assess, and mitigate risks associated with quality and compliance. ISO 31000 provides guidelines on risk management that can be integrated with your QMS. ISO 31000 Risk Management offers a detailed approach.
Performance Measurement: Establish key performance indicators (KPIs) to monitor and measure quality performance regularly. This data should inform decision-making and improvement initiatives. ISO 9001 Performance Evaluation can guide you in setting up effective performance evaluation mechanisms.
Supplier Management: Ensure your suppliers and external partners adhere to quality standards that align with your QMS requirements. Conduct audits and assessments to monitor their compliance. ISO 9001 Purchasing Process provides insights into managing the purchasing process and supplier relationships effectively.
Improving your ISO 9001 QMS is an ongoing journey that requires commitment, resources, and continuous effort. Leveraging the resources provided above and staying informed about best practices in quality management will help you enhance your organization's quality performance and customer satisfaction.
How to Display ISO 9001 Skills on Your Resume
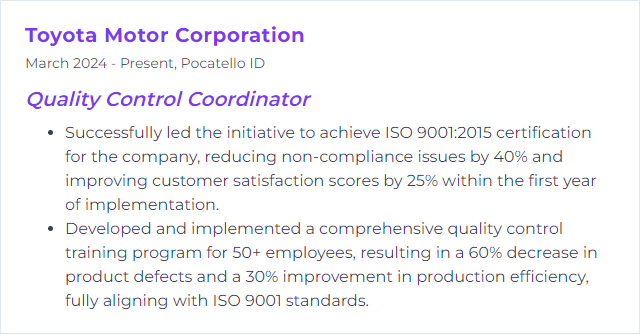
2. Six Sigma
Six Sigma is a data-driven methodology and set of tools aimed at improving business processes by reducing variability and defects to enhance product quality and customer satisfaction.
Why It's Important
Six Sigma is important for a Quality Control Coordinator because it provides a systematic methodology to reduce defects, improve processes, and enhance product quality, ultimately leading to increased customer satisfaction and reduced costs.
How to Improve Six Sigma Skills
Improving Six Sigma involves continuous learning, process optimization, and stakeholder engagement. As a Quality Control Coordinator, focus on the following concise strategies:
Enhance Skills and Knowledge: Invest in advanced Six Sigma training for yourself and your team. Stay updated with the latest trends and methodologies in quality control. ASQ and iSixSigma are great resources for learning and certification.
Implement DMAIC Rigorously: Ensure the Define, Measure, Analyze, Improve, and Control (DMAIC) methodology is applied meticulously in every project. This structured approach leads to significant improvements in process efficiency and quality.
Leverage Technology: Use quality management software and statistical analysis tools to streamline processes, improve accuracy, and facilitate decision-making. Tools like Minitab or SigmaXL can be very helpful.
Engage Stakeholders: Work closely with all stakeholders, including customers, to understand their needs and expectations. This can lead to more targeted quality improvements.
Foster a Culture of Continuous Improvement: Encourage a workplace culture where every employee feels responsible for quality control and is motivated to suggest improvements. Regular training and recognition programs can support this culture.
Benchmark and Learn from Best Practices: Compare your processes and performance with those of industry leaders. Benchmarking studies and industry forums can provide insights into best practices and innovative strategies.
Regular Audits and Reviews: Conduct frequent quality audits and process reviews to ensure compliance with standards and identify areas for improvement. Internal audits can be complemented with external ones for unbiased insights.
By focusing on these strategies, a Quality Control Coordinator can significantly enhance the effectiveness of Six Sigma projects within their organization.
How to Display Six Sigma Skills on Your Resume
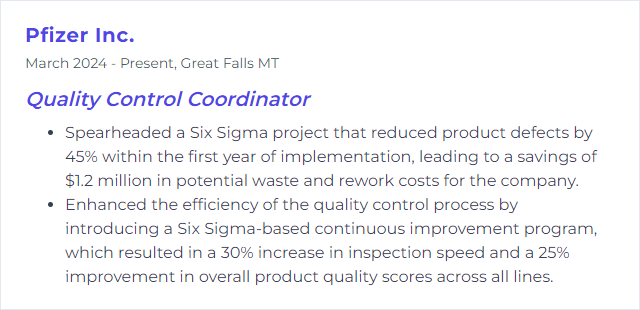
3. Lean Manufacturing
Lean Manufacturing is a systematic approach to minimizing waste within manufacturing systems while maximizing productivity, aimed at improving quality and efficiency, directly impacting the role of a Quality Control Coordinator by streamlining processes and enhancing product quality assurance.
Why It's Important
Lean Manufacturing is crucial for a Quality Control Coordinator because it focuses on minimizing waste while maximizing productivity, leading to more efficient production processes, higher quality products, and reduced costs, thereby directly supporting quality control objectives.
How to Improve Lean Manufacturing Skills
Improving Lean Manufacturing, particularly from a Quality Control Coordinator's perspective, involves focusing on continuous improvement, waste reduction, and process optimization. Here are concise strategies:
Implement Continuous Improvement (Kaizen): Encourage a culture of constant, incremental improvements. Kaizen focuses on eliminating waste and enhancing productivity. Kaizen Institute
Use 5S for Workplace Organization: Apply the 5S methodology (Sort, Set in order, Shine, Standardize, Sustain) to ensure a clean, organized, and efficient workspace. This supports quality control by minimizing errors and improving safety. 5S Guide
Adopt Six Sigma Techniques: Combine Lean Manufacturing with Six Sigma for data-driven quality control and process improvement. Six Sigma methodologies aim at reducing defects and variability in manufacturing processes. ASQ Six Sigma Resources
Value Stream Mapping: Analyze and design the flow of materials and information required to bring a product to a customer. This helps in identifying waste and opportunities for improvement in the production process. Value Stream Mapping Guide
Total Productive Maintenance (TPM): Involve employees in all aspects of maintenance to ensure maximum efficiency of equipment. This prevents downtime, defects, and accidents, directly benefiting quality control. TPM Overview
Root Cause Analysis: When defects occur, use tools like the 5 Whys or Fishbone Diagram to investigate and address the root cause, rather than just the symptoms. This prevents recurrence of the same issues. Root Cause Analysis Tools
Cross-Training Employees: Enhance flexibility and knowledge sharing among workers by cross-training them. This ensures quality is maintained even when the primary workforce is unavailable. Benefits of Cross-Training
Regular Feedback and Communication: Foster an environment where feedback is regularly exchanged between teams and individuals. Open communication channels help in identifying and resolving quality issues more rapidly. Effective Communication in the Workplace
Implementing these strategies requires a coordinated effort and commitment from all levels within the organization. Continuous monitoring, learning, and adapting are key to driving success in Lean Manufacturing initiatives.
How to Display Lean Manufacturing Skills on Your Resume
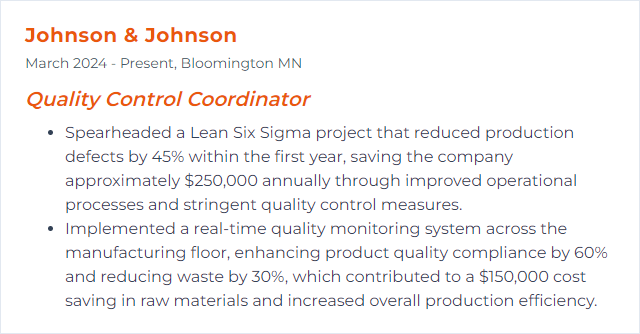
4. SAP Quality Management
SAP Quality Management (QM) is a component of the SAP ERP system that supports all aspects of quality control and assurance, including planning, execution, and recording of quality tests, as well as the management of issues and improvements. It enables a Quality Control Coordinator to oversee and ensure product compliance with quality standards and regulations, streamline inspection processes, and manage quality certificates, thus facilitating efficient quality management across the supply chain.
Why It's Important
SAP Quality Management (QM) is crucial as it enables a Quality Control Coordinator to seamlessly integrate quality control processes with production and procurement activities. This ensures consistent quality compliance, reduces defects, and minimizes waste, leading to improved product reliability and customer satisfaction.
How to Improve SAP Quality Management Skills
Improving SAP Quality Management (QM) involves optimizing processes, leveraging technology, and focusing on data-driven decision-making. For a Quality Control Coordinator, here are concise steps to enhance SAP QM efficiency:
Understand SAP QM Components: Familiarize yourself with core components such as Quality Planning, Quality Inspection, and Quality Control. SAP Help Portal offers detailed documentation.
Utilize SAP QM Reports: Leverage standard and custom reports for insights on quality performance. This SAP Community Link provides guidance on using QM reports effectively.
Implement Automation: Automate routine tasks within SAP QM to increase efficiency. Explore SAP Intelligent Robotic Process Automation for options.
Continuous Training: Ensure continuous learning for yourself and your team on SAP QM updates and best practices through SAP Training and Certification.
Data Analysis and Reporting: Utilize SAP's advanced analytics to interpret quality data for better decision-making. Check SAP Analytics Cloud for integrated analytics solutions.
Feedback Loop: Establish a feedback mechanism within SAP QM to capture insights from end-users and continuously improve processes. Engage with the SAP QM Community for shared experiences and tips.
Collaborate with IT: Work closely with your IT department or SAP consultants to ensure the SAP QM module is tailored to your organization's specific needs, enhancing usability and efficiency.
Quality Audits: Regularly conduct internal audits within SAP QM to ensure compliance with quality standards and identify areas for improvement.
Focusing on these areas will significantly enhance the effectiveness of SAP Quality Management in your role as a Quality Control Coordinator.
How to Display SAP Quality Management Skills on Your Resume
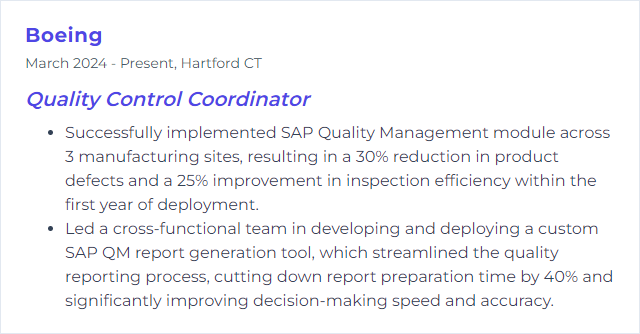
5. Statistical Process Control (SPC)
Statistical Process Control (SPC) is a method used in quality control to monitor and control a process by employing statistical techniques to detect and prevent poor quality during the manufacturing process. It involves using control charts to track process performance and identify variations that may indicate a problem, allowing for timely corrections to maintain product quality standards.
Why It's Important
Statistical Process Control (SPC) is essential for a Quality Control Coordinator because it enables the monitoring and control of process variability, ensuring products meet quality standards consistently, thereby reducing waste, improving efficiency, and enhancing customer satisfaction.
How to Improve Statistical Process Control (SPC) Skills
Improving Statistical Process Control (SPC) involves several key steps aimed at enhancing the efficiency and accuracy of quality control processes. Here's a concise guide for a Quality Control Coordinator:
Educate and Train Team Members: Ensure all team members are well-versed in SPC concepts and tools. Continuous training helps maintain high standards of quality control. ASQ’s Training Resources
Select Appropriate SPC Tools: Use the right SPC tools (e.g., control charts, Pareto charts) tailored to your specific processes. Selecting the right tool is crucial for effective monitoring and analysis. NIST/SEMATECH e-Handbook of Statistical Methods
Implement Real-Time Monitoring: Utilize real-time data collection and monitoring systems to promptly detect and address process variations. This proactive approach helps in maintaining process control. SPC Software Solutions
Analyze Data Effectively: Regularly analyze collected data to identify patterns, trends, and areas of improvement. Use statistical analysis to make informed decisions. Minitab’s Guide on Data Analysis
Engage in Continuous Improvement: Adopt a Kaizen (continuous improvement) mindset to consistently seek ways to improve processes. Engage teams in problem-solving and process optimization. Kaizen Institute
Standardize Processes: Develop and standardize best practices for SPC across all relevant processes. Consistency is key to maintaining quality over time. ISO’s Quality Management Standards
Utilize Automated SPC Software: Leverage automated SPC software to enhance accuracy and efficiency. Automation can help in reducing human error and improving data analysis. Quality Magazine’s Review on SPC Software
By focusing on these areas, Quality Control Coordinators can significantly improve the effectiveness of Statistical Process Control in their organizations, leading to higher quality products and more efficient processes.
How to Display Statistical Process Control (SPC) Skills on Your Resume
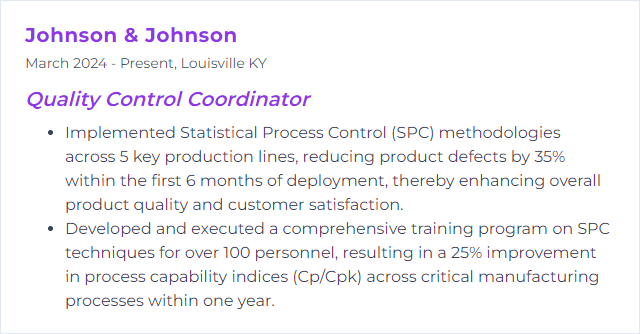
6. Minitab
Minitab is a statistical software package designed for data analysis, quality improvement, and process optimization, primarily used by Quality Control Coordinators for analyzing quality metrics and identifying trends, patterns, and anomalies in manufacturing or service processes.
Why It's Important
Minitab is important for a Quality Control Coordinator because it provides powerful statistical analysis, process improvement, and quality control tools, enabling efficient data analysis, visualization, and decision-making to ensure product quality and consistency.
How to Improve Minitab Skills
Improving your proficiency with Minitab as a Quality Control Coordinator involves enhancing your statistical analysis skills, understanding quality control processes deeply, and leveraging Minitab's resources. Follow these concise steps:
Master Statistical Tools: Focus on mastering statistical tools relevant to quality control, such as control charts, process capability analysis, and hypothesis testing. Minitab offers tutorials on these topics.
Utilize Minitab's Help and Support: Leverage the extensive Minitab Help section, which includes tutorials, case studies, and detailed instructions for various analyses.
Participate in Training Programs: Enroll in Minitab-specific training programs to enhance your understanding of the software and its application in quality control.
Apply Quality Control Principles: Integrate your quality control expertise with Minitab by applying the principles of Six Sigma or other quality methodologies within the software. Minitab’s blog often features case studies and examples.
Practice Continuously: Regular use and experimentation with Minitab will improve your proficiency. Set aside time to explore new features and practice analyzing real or simulated data sets.
Join User Groups: Engage with other Minitab users through forums or user groups. The Minitab Community is a great place to share insights and ask questions.
Stay Updated: Regularly update your Minitab software to utilize the latest tools and features. Keep an eye on Minitab’s official website for updates and resources.
By integrating these steps into your professional development, you'll enhance your ability to utilize Minitab effectively for quality control purposes.
How to Display Minitab Skills on Your Resume
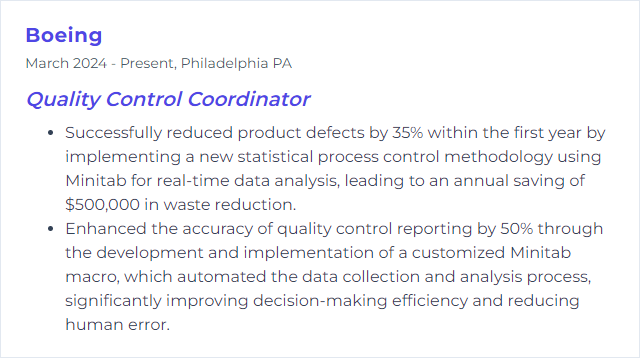
7. Quality Auditing
Quality auditing is the systematic examination of a quality system carried out by an internal or external quality auditor or audit team. It assesses whether the quality activities and results comply with planned arrangements and whether these arrangements are implemented effectively and are suitable to achieve objectives. For a Quality Control Coordinator, it involves verifying that the processes used to control and produce the product meet required quality standards.
Why It's Important
Quality auditing is crucial for ensuring that products or services meet established standards, regulations, and customer expectations, thereby enhancing satisfaction, trust, and compliance. For a Quality Control Coordinator, it provides a systematic review process to identify non-conformances, drive continuous improvement, and maintain the integrity of the quality management system.
How to Improve Quality Auditing Skills
To improve Quality Auditing, a Quality Control Coordinator should focus on these key areas:
Continuous Education: Stay updated with the latest quality standards and auditing techniques. ASQ offers various courses and certifications.
Implement Technology: Use software tools for better data management and audit tracking. Qualio is a popular choice for quality management software.
Enhance Communication Skills: Effective communication with the team ensures clear understanding and adherence to quality standards. Resources like MindTools can help improve communication skills.
Develop a Robust Audit Plan: Plan audits systematically to cover all critical areas regularly. The ISO website provides guidelines and resources for planning and conducting audits.
Promote a Culture of Quality: Encourage everyone in the organization to prioritize quality. Harvard Business Review offers insights on building a quality-focused culture.
By focusing on these areas, a Quality Control Coordinator can significantly enhance the efficiency and effectiveness of quality auditing.
How to Display Quality Auditing Skills on Your Resume
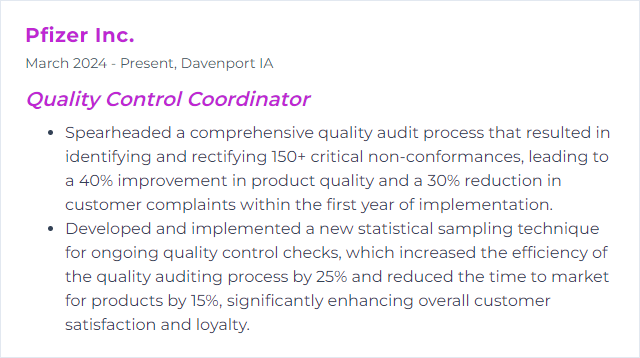
8. CAPA (Corrective and Preventive Action)
CAPA (Corrective and Preventive Action) is a quality management process that identifies, addresses, and eliminates the causes of detected nonconformities or other undesirable situations, to prevent their recurrence (corrective action) and to prevent their occurrence (preventive action), ensuring continuous improvement in quality control.
Why It's Important
CAPA is crucial for a Quality Control Coordinator as it identifies, corrects, and prevents defects and non-conformities in processes and products, ensuring continuous improvement and compliance with quality standards.
How to Improve CAPA (Corrective and Preventive Action) Skills
Improving CAPA involves a systematic approach to identify issues, analyze root causes, and implement corrective and preventive measures efficiently. Here's a concise guide for a Quality Control Coordinator:
Identify and Document Issues: Accurately identify non-conformances or potential issues. Use tools like Fishbone Diagrams and 5 Whys Analysis to ensure comprehensive documentation.
Analyze Root Cause: Employ root cause analysis (RCA) techniques to identify the underlying reasons for the non-conformance. Root Cause Analysis (RCA) provides methodologies for thorough investigation.
Develop Action Plan: Formulate a corrective and preventive action plan based on the RCA. Incorporate SMART goals (Specific, Measurable, Achievable, Relevant, Time-bound) to ensure effectiveness.
Implement Actions: Execute the action plan with clear responsibilities and timelines. Use project management tools like Trello or Asana for tracking and accountability.
Evaluate Effectiveness: Monitor the implementation and measure the effectiveness of the CAPA. KPIs (Key Performance Indicators) can help in objectively assessing the impact.
Document and Review: Maintain comprehensive records of the CAPA process. Regularly review CAPA procedures and outcomes for continuous improvement.
Training and Communication: Ensure all relevant stakeholders are trained and informed about the CAPA process and any changes implemented. Effective communication tools include Slack for team communication and Zoom for remote meetings and training sessions.
For a Quality Control Coordinator, focusing on precise documentation, thorough analysis, effective implementation, and continuous improvement are key to enhancing the CAPA process.
How to Display CAPA (Corrective and Preventive Action) Skills on Your Resume
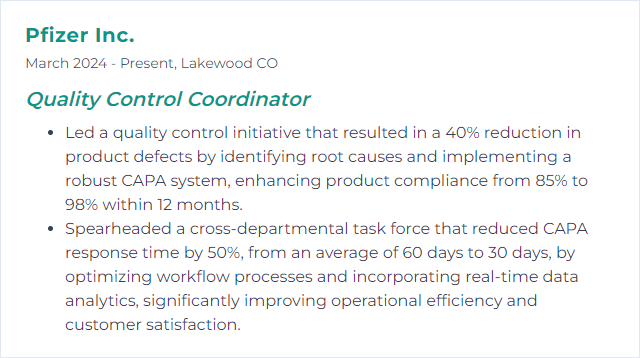
9. GMP (Good Manufacturing Practices)
GMP (Good Manufacturing Practices) are standardized guidelines ensuring that products are consistently produced and controlled according to quality standards. For a Quality Control Coordinator, GMP involves overseeing the adherence to these protocols to ensure product safety, efficacy, and quality throughout the manufacturing process.
Why It's Important
GMP ensures products are consistently produced and controlled according to quality standards, minimizing risks involved in pharmaceutical and food production that cannot be eliminated through testing the final product. This is crucial for a Quality Control Coordinator as it provides a framework for maintaining product integrity, safety, and efficacy throughout the manufacturing process.
How to Improve GMP (Good Manufacturing Practices) Skills
Improving Good Manufacturing Practices (GMP) involves a multifaceted approach focusing on compliance, training, documentation, and continuous improvement. As a Quality Control Coordinator, you can enhance GMP by:
Ensuring Compliance: Stay updated with the latest GMP regulations from relevant authorities (e.g., FDA for the United States) to ensure your practices meet all legal requirements.
Continuous Training: Implement ongoing GMP training programs for all employees to reinforce the importance of quality and compliance, adapting to updates in regulations and industry standards.
Robust Documentation: Maintain thorough documentation for all processes, audits, and quality checks. Utilize document management systems to ensure easy access and organization.
Quality Audits: Regularly conduct internal and external audits to identify areas for improvement, ensuring your manufacturing processes comply with GMP standards.
Feedback Loop: Establish a system for feedback from employees and customers to identify potential GMP issues. Use this feedback for continuous improvement.
Invest in Quality Systems: Implement or upgrade to a Quality Management System (QMS) that supports GMP by integrating quality control into all aspects of the manufacturing process.
Preventive Maintenance: Ensure equipment is regularly inspected and maintained to prevent contamination, errors, or product quality issues.
By focusing on these areas, you can significantly improve the GMP in your manufacturing processes, leading to enhanced product quality, reduced risk of non-compliance, and greater consumer trust.
How to Display GMP (Good Manufacturing Practices) Skills on Your Resume
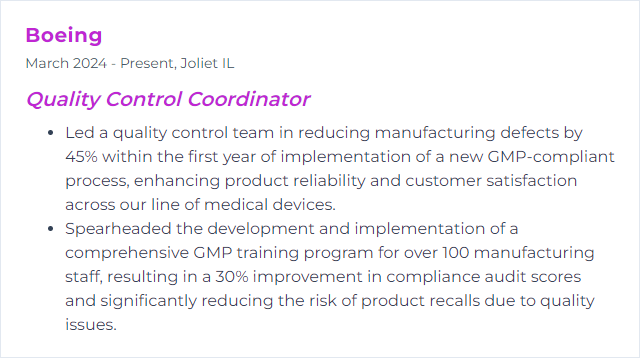
10. Root Cause Analysis
Root Cause Analysis (RCA) is a systematic process aimed at identifying the fundamental causes of problems or issues to prevent their recurrence, rather than simply addressing their immediate symptoms. For a Quality Control Coordinator, RCA is crucial for eliminating defects, enhancing product quality, and improving manufacturing processes.
Why It's Important
Root Cause Analysis (RCA) is crucial for a Quality Control Coordinator as it enables the identification and resolution of the fundamental issues causing defects or failures, preventing their recurrence, and ensuring product quality and customer satisfaction.
How to Improve Root Cause Analysis Skills
To improve Root Cause Analysis (RCA) as a Quality Control Coordinator, follow these concise steps:
Define the Problem Clearly: Start with a clear description of the actual problem. Use the 5 Whys technique to drill down to the root cause by asking "Why?" multiple times until the fundamental issue is identified.
Collect Data: Gather detailed, relevant data surrounding the problem. This could involve using Pareto Charts to identify the most significant issues.
Identify Possible Causal Factors: Brainstorm potential causes for the problem. Tools like the Fishbone (Ishikawa) Diagram can help map out potential sources of variation in processes.
Determine the Root Cause: Analyze the data and causal factors to pinpoint the root cause(s). Techniques such as the Failure Mode and Effects Analysis (FMEA) can be effective in identifying which causes must be addressed.
Implement Corrective Actions: Develop a plan to correct the root cause. Ensure actions are measurable and can be evaluated for effectiveness.
Verify the Effectiveness: Monitor the situation post-implementation to verify that the root cause has been effectively addressed and the problem is resolved.
Document and Share Learnings: Document the findings, actions taken, and outcomes. Share these learnings within the organization to prevent recurrence. Knowledge Management Systems can be useful for this purpose.
By methodically applying these steps and utilizing the linked tools and techniques, you can significantly improve the effectiveness of your Root Cause Analysis processes in a Quality Control context.
How to Display Root Cause Analysis Skills on Your Resume
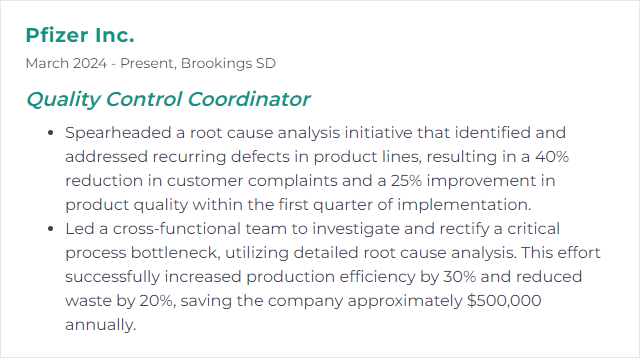
11. FMEA (Failure Mode and Effects Analysis)
FMEA (Failure Mode and Effects Analysis) is a systematic method used to identify potential failures in a product, process, or system, assess their impact, and determine actions to mitigate the risks, enhancing quality and reliability.
Why It's Important
FMEA is important because it proactively identifies potential failures in products or processes and their likely effects, allowing for preventive measures to be implemented, thereby enhancing product quality, safety, and customer satisfaction.
How to Improve FMEA (Failure Mode and Effects Analysis) Skills
To improve FMEA processes, follow these concise strategies:
Prioritize Training: Ensure all team members involved in the FMEA process are well-trained in its principles and application. ASQ's FMEA Training can be a valuable resource.
Cross-functional Teams: Utilize cross-functional teams to gain diverse perspectives on potential failure modes. Harvard Business Review's Insights on cross-functional teams provide guidance on effective collaboration.
Leverage Software Tools: Adopt specialized FMEA software to streamline the process, ensuring thorough analysis and documentation. PFMEA Software Solutions offer examples of available tools.
Update Regularly: FMEA is not a one-time activity. Regularly review and update your analyses to reflect changes in processes, materials, or design. Quality Digest emphasizes the importance of continuous improvement in FMEA.
Benchmark and Learn: Study FMEA examples from within your industry and beyond to identify best practices and innovative approaches. IndustryWeek discusses benchmarking for quality improvement.
Focus on Risk Priority Numbers (RPN): Prioritize actions based on the RPN to effectively allocate resources to the most critical areas. The American Society for Quality explains RPN in FMEA.
By integrating these strategies, a Quality Control Coordinator can enhance the effectiveness of FMEA processes within their organization.
How to Display FMEA (Failure Mode and Effects Analysis) Skills on Your Resume
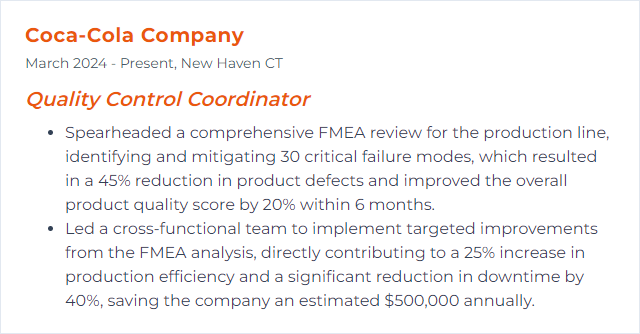
12. Quality Inspection Tools
Quality inspection tools are instruments and software used by Quality Control Coordinators to measure, examine, and test the quality of products or processes, ensuring they meet specified standards and requirements. These tools can include calipers, micrometers, gauges, CMMs (Coordinate Measuring Machines), and specialized software for statistical process control and quality analysis.
Why It's Important
Quality inspection tools are crucial as they enable a Quality Control Coordinator to accurately assess product conformity to standards, identify defects, ensure safety and reliability, and maintain customer satisfaction by consistently delivering high-quality products.
How to Improve Quality Inspection Tools Skills
Improving quality inspection tools involves several steps, focusing on accuracy, efficiency, and adaptability to meet the evolving needs of quality control processes. Here are some concise tips:
Upgrade Technology: Invest in the latest inspection technology to enhance precision and speed. This includes digital calipers, 3D scanners, and advanced imaging systems.
Implement Software Solutions: Utilize quality management software that integrates with your inspection tools for real-time data analysis and reporting, improving decision-making and trend analysis.
Regular Calibration and Maintenance: Ensure all inspection tools are regularly calibrated and maintained to avoid inaccuracies and equipment failures.
Training and Certification: Invest in training for staff to stay updated on the latest inspection techniques and tool handling. Certifications can also validate their expertise.
Standardization and Documentation: Develop and maintain clear standard operating procedures (SOPs) for tool usage, ensuring consistency and reliability across all inspections.
Feedback Loop: Establish a feedback system to continuously gather insights from the inspections and use this data to refine tools and processes.
Innovation and Adaptation: Stay informed about new technologies and methodologies in quality inspection by following relevant industry publications and forums, allowing you to adapt and innovate as needed.
By focusing on these areas, a Quality Control Coordinator can significantly enhance the effectiveness and efficiency of quality inspection tools.
How to Display Quality Inspection Tools Skills on Your Resume
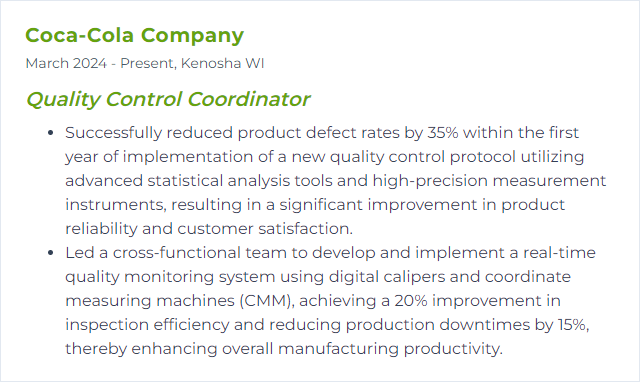