Top 12 Quality Control Auditor Skills to Put on Your Resume
In today's competitive job market, standing out as a Quality Control Auditor requires more than just technical know-how; it demands a unique blend of skills that can catch an employer's eye. This article delves into the top 12 skills you should highlight on your resume, showcasing your capability to ensure excellence and maintain the highest standards of quality in your field.
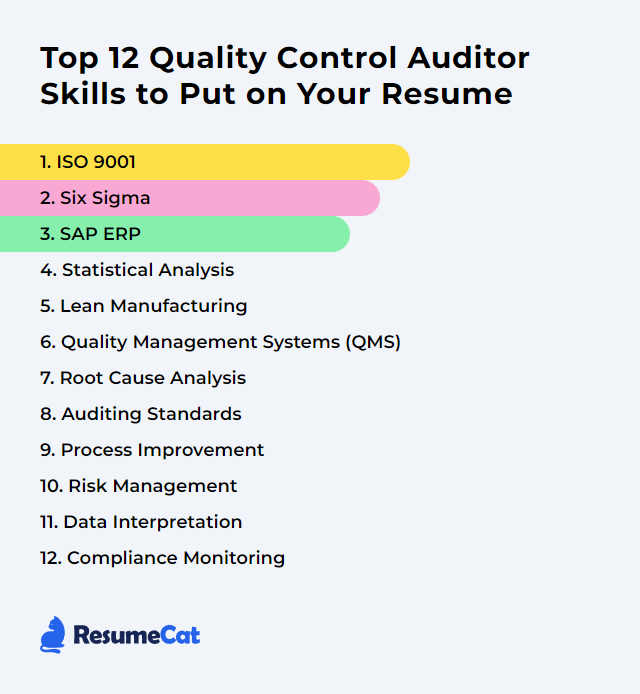
Quality Control Auditor Skills
- ISO 9001
- Six Sigma
- SAP ERP
- Statistical Analysis
- Lean Manufacturing
- Quality Management Systems (QMS)
- Root Cause Analysis
- Auditing Standards
- Process Improvement
- Risk Management
- Data Interpretation
- Compliance Monitoring
1. ISO 9001
ISO 9001 is an international standard that specifies requirements for a quality management system (QMS), focusing on meeting customer requirements and enhancing customer satisfaction. For a Quality Control Auditor, it provides a framework for consistent quality assurance and control processes to ensure products and services meet regulatory and customer standards.
Why It's Important
ISO 9001 is important for a Quality Control Auditor because it provides a standardized framework for quality management systems, ensuring consistent quality in products and services, enhancing customer satisfaction, and facilitating continuous improvement processes.
How to Improve ISO 9001 Skills
Improving ISO 9001 implementation, especially from a Quality Control Auditor's perspective, involves focusing on continuous improvement, effective audit planning, and enhancing the quality management system's effectiveness. Here are some concise strategies:
Continuous Improvement: Emphasize the Plan-Do-Check-Act (PDCA) cycle to identify areas for improvement continuously. ASQ offers insights on integrating continuous improvement with ISO 9001.
Effective Audit Planning: Develop comprehensive audit plans that focus on potential high-risk areas. Utilize the guidelines provided by ISO for conducting effective audits.
Employee Training: Ensure all employees are adequately trained on ISO 9001 standards and the importance of quality management. ISO 9001 Training Courses can be a resourceful guide.
Management Engagement: Engage top management in the quality management process to align organizational objectives with quality goals. The CQI provides strategies for engaging leadership.
Process Optimization: Streamline processes to eliminate waste and improve efficiency, applying lean principles. Lean Enterprise Institute has resources on lean principles.
Customer Feedback: Regularly gather and analyze customer feedback to identify areas for improvement. ISO 9001 Customer Satisfaction elaborates on this.
Utilize Technology: Adopt quality management software to streamline documentation, audit management, and corrective action processes. Capterra lists various software options.
Corrective Actions: Implement a robust process for corrective actions to address non-conformities identified during audits. Guidance can be found in ISO 9001 Corrective Action.
Risk Management: Incorporate risk management into the quality management system to proactively address potential issues. ISO 31000 provides standards on risk management.
Benchmarking: Regularly benchmark against best practices within the industry to identify improvement areas. Benchmarking in ISO 9001 offers insights on this.
By focusing on these areas, a Quality Control Auditor can significantly contribute to the improvement of the ISO 9001 implementation within their organization.
How to Display ISO 9001 Skills on Your Resume
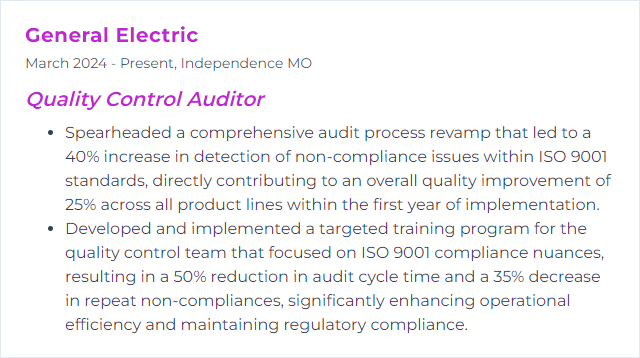
2. Six Sigma
Six Sigma is a data-driven methodology aimed at improving business processes by minimizing defects and variability, ensuring quality control and operational excellence. For a Quality Control Auditor, it provides tools and techniques for identifying, analyzing, and reducing quality issues to enhance product or service compliance and customer satisfaction.
Why It's Important
Six Sigma is important for a Quality Control Auditor because it provides a systematic, data-driven approach for reducing defects and improving quality, ensuring products or services meet or exceed customer expectations.
How to Improve Six Sigma Skills
To improve Six Sigma as a Quality Control Auditor, focus on the following key strategies:
Enhance Data Analysis Skills: Improve your ability to analyze data effectively. Master statistical tools and software used in Six Sigma methodologies like Minitab or JMP. ASQ’s Six Sigma Training offers comprehensive resources.
Continuous Learning: Stay updated with the latest trends and techniques in Six Sigma by enrolling in advanced courses and certifications. iSixSigma provides a wealth of knowledge and updates.
Strengthen Soft Skills: Develop communication and project management skills to better lead teams and manage projects. Project Management Institute offers courses that can be beneficial.
Implement Quality Tools: Familiarize yourself with and utilize Six Sigma tools like DMAIC (Define, Measure, Analyze, Improve, Control) and DMADV (Define, Measure, Analyze, Design, Verify) for quality improvement projects.
Engage in Peer Networking: Join forums and professional networks such as LinkedIn’s Six Sigma Group to exchange knowledge and experiences with peers.
Audit Regularly and Provide Feedback: Conduct regular audits to ensure adherence to Six Sigma methodologies and provide constructive feedback for continuous improvement.
By focusing on these strategies, you can significantly contribute to the enhancement of Six Sigma processes within your organization.
How to Display Six Sigma Skills on Your Resume
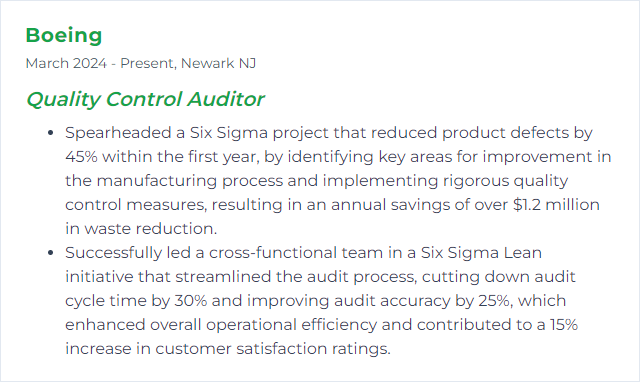
3. SAP ERP
SAP ERP is an integrated enterprise resource planning software that manages and automates core business processes, including quality control, providing tools for effective monitoring, analysis, and reporting to ensure product and service compliance with standards.
Why It's Important
SAP ERP is crucial for a Quality Control Auditor as it streamlines and integrates quality management processes, ensuring consistent compliance, real-time monitoring, and efficient analysis of quality-related data across the organization. This facilitates effective auditing, continuous improvement, and adherence to regulatory standards.
How to Improve SAP ERP Skills
Improving SAP ERP, especially from a Quality Control Auditor perspective, involves enhancing data accuracy, streamlining processes, and ensuring compliance. Here are concise strategies:
Implement Automated Data Validation: Use SAP's Data Quality Management tools to automate the validation of data inputs. This reduces errors and ensures high-quality data for decision-making.
Integrate Quality Management (QM) Module: Fully leverage SAP's QM module to streamline quality inspections, manage quality certificates, and monitor quality compliance across the supply chain.
Adopt SAP Fiori Apps for Quality Audits: Utilize SAP Fiori apps designed for quality management processes. These apps offer intuitive interfaces for performing audits, tracking non-conformances, and managing corrective actions on the go.
Leverage Advanced Analytics for Predictive Quality: Integrate SAP ERP with SAP Analytics Cloud to use advanced analytics and machine learning for predictive quality management. This can help in identifying potential quality issues before they occur.
Ensure Continuous Training and Support: Regular training sessions and easy access to SAP Learning Hub resources ensure that quality control auditors are up-to-date with the latest SAP functionalities and best practices.
By focusing on these areas, a Quality Control Auditor can significantly enhance the effectiveness and efficiency of SAP ERP systems in managing quality control and assurance processes.
How to Display SAP ERP Skills on Your Resume
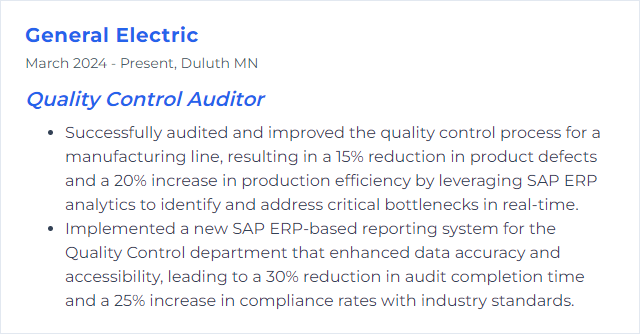
4. Statistical Analysis
Statistical analysis is the process of collecting, examining, summarizing, and interpreting data to identify patterns, trends, and relationships, enabling informed decisions and conclusions. For a Quality Control Auditor, it involves applying statistical methods to monitor and maintain product quality by identifying deviations, ensuring compliance with standards, and implementing continuous improvement strategies.
Why It's Important
Statistical analysis is crucial for a Quality Control Auditor as it enables the identification of trends, anomalies, and variations in product quality, ensuring consistency, reliability, and adherence to standards, thereby minimizing defects and enhancing customer satisfaction.
How to Improve Statistical Analysis Skills
Improving statistical analysis, particularly for a Quality Control Auditor, involves enhancing data collection, analysis, and interpretation skills. Here’s a concise guide:
Understand Statistical Fundamentals: Grasp basic statistical concepts and tests to apply them appropriately. Khan Academy offers comprehensive resources.
Utilize Software Tools: Master statistical software like Minitab or R for efficient data analysis.
Enhance Sampling Techniques: Learn about different sampling methods to ensure data representativeness. The American Society for Quality (ASQ) provides insights on sampling techniques.
Apply Quality Control Charts: Use control charts to monitor processes. The National Institute of Standards and Technology (NIST) offers guidelines on control chart selection and usage.
Continuous Learning: Stay updated with the latest trends in statistical analysis through webinars, courses, and articles on platforms like Coursera and LinkedIn Learning.
By focusing on these areas, a Quality Control Auditor can significantly improve their statistical analysis skills, leading to more accurate and reliable quality assessments.
How to Display Statistical Analysis Skills on Your Resume
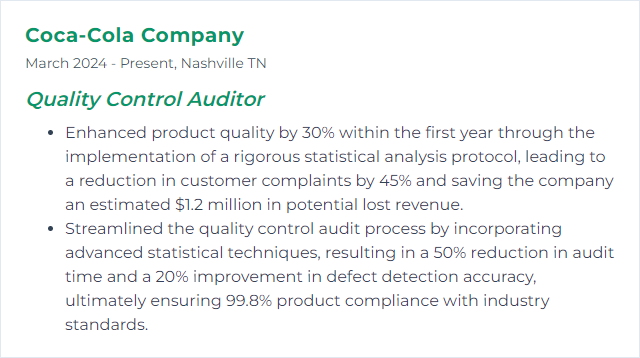
5. Lean Manufacturing
Lean Manufacturing is a systematic approach aimed at minimizing waste within manufacturing systems while simultaneously maximizing productivity. For a Quality Control Auditor, it focuses on ensuring consistent quality by identifying and eliminating defects and inefficiencies in the production process.
Why It's Important
Lean Manufacturing is important for a Quality Control Auditor because it focuses on minimizing waste and optimizing efficiency, leading to higher quality products, reduced defects, and improved customer satisfaction.
How to Improve Lean Manufacturing Skills
Improving Lean Manufacturing, especially from the perspective of a Quality Control Auditor, involves focusing on waste reduction, enhancing process efficiency, and ensuring continuous improvement. Here are concise strategies:
Embrace Kaizen: Promote continuous, incremental improvement by encouraging feedback from all employees. Kaizen helps identify and eliminate waste in processes.
Implement 5S Methodology: Organize and manage the workspace and workstations for efficiency and effectiveness by sorting, setting in order, shining, standardizing, and sustaining. 5S methodology improves safety, work efficiency, and reduces waste.
Adopt Value Stream Mapping: Analyze and design the flow of materials and information required to bring a product or service to a consumer. Value Stream Mapping helps identify waste and streamline production processes.
Enhance Process Standardization: Develop and use standard operating procedures for all tasks to ensure consistency and quality. Process Standardization minimizes variability and improves efficiency.
Focus on Preventive Maintenance: Implement a scheduled maintenance plan to prevent machinery and equipment failures. Preventive Maintenance ensures operational efficiency and reduces downtime.
Utilize Root Cause Analysis: When defects occur, identify and address the root cause rather than symptoms. Root Cause Analysis tools like the 5 Whys or Fishbone Diagram can prevent recurrence of quality issues.
Employ Quality Circles: Facilitate small groups of workers who perform similar duties to discuss and solve problems affecting their work area, enhancing product quality and productivity. Quality Circles promote worker involvement and ownership.
By focusing on these strategies, a Quality Control Auditor can significantly contribute to the enhancement of Lean Manufacturing in their organization.
How to Display Lean Manufacturing Skills on Your Resume
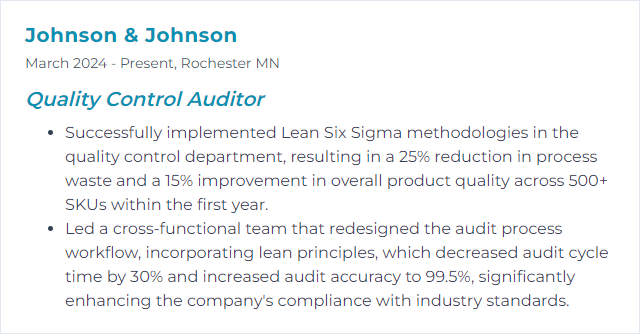
6. Quality Management Systems (QMS)
A Quality Management System (QMS) is a structured framework of policies, procedures, and processes used by an organization to ensure that its products or services meet and maintain quality standards. For a Quality Control Auditor, a QMS provides the criteria for audits, guiding the systematic examination of the organization's adherence to these quality standards and regulatory requirements.
Why It's Important
Quality Management Systems (QMS) are crucial as they provide a structured framework for consistently meeting customer requirements and enhancing their satisfaction by systematically managing and improving all aspects of quality control and assurance processes. For a Quality Control Auditor, it ensures standardized procedures, reduces errors, and facilitates continuous improvement, making the audit process more efficient and effective.
How to Improve Quality Management Systems (QMS) Skills
Improving Quality Management Systems (QMS) involves continuous assessment and refinement. Here are concise steps tailored for a Quality Control Auditor:
Conduct Regular Audits: Regularly evaluate your QMS to identify areas of improvement. Utilize the ISO 19011 guidelines for auditing management systems.
Engage in Continuous Learning: Stay informed about the latest quality management trends and standards through resources like ASQ (American Society for Quality).
Implement Corrective Actions: When issues are identified, promptly address them. Utilize tools like the 8D Problem-Solving Process for effective resolution.
Emphasize Employee Training: Ensure all team members are trained on QMS procedures and updates. Online platforms like Coursera offer relevant courses.
Utilize Technology: Adopt QMS software for better data management and process automation. Research options on Capterra’s QMS Software Directory.
Gather Feedback: Collect insights from stakeholders and customers to identify areas for improvement. Tools like SurveyMonkey can facilitate this process.
Review and Update Documentation: Regularly update QMS documents to ensure they reflect current practices. Guidance can be found through ISO 9001 requirements.
Monitor Performance Metrics: Establish and monitor key performance indicators (KPIs) to track QMS effectiveness. Learn more about KPIs through KPI.org.
Foster a Quality Culture: Promote a culture where quality is everyone’s responsibility. Resources at ASQ can offer further insights.
Benchmarking: Compare processes with those of leading organizations in your industry. Explore benchmarking resources through The Benchmarking Network.
By following these steps and leveraging the provided resources, a Quality Control Auditor can effectively contribute to the enhancement of their organization's QMS.
How to Display Quality Management Systems (QMS) Skills on Your Resume
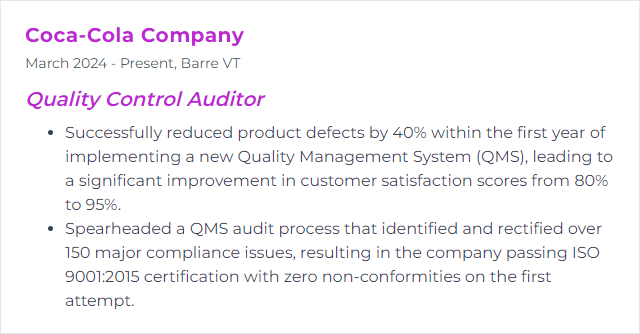
7. Root Cause Analysis
Root Cause Analysis (RCA) is a systematic process used by Quality Control Auditors to identify the underlying reasons for a defect or problem, aiming to implement solutions that prevent recurrence.
Why It's Important
Root Cause Analysis (RCA) is crucial for a Quality Control Auditor as it identifies the underlying reasons for defects or problems, enabling the implementation of effective corrective actions to prevent recurrence, thereby ensuring product quality and customer satisfaction.
How to Improve Root Cause Analysis Skills
Improving Root Cause Analysis (RCA) involves a systematic approach to identify the underlying causes of problems to prevent their recurrence. For a Quality Control Auditor, enhancing RCA skills can be achieved through the following steps:
Define the Problem Clearly: Use precise and clear language to define the problem, ensuring everyone understands the issue. ASQ’s guidelines on problem definition can be helpful.
Collect Data: Gather comprehensive data related to the problem. Utilize tools like Fishbone Diagrams to categorize potential causes.
Identify Potential Causes: Use techniques like the 5 Whys to drill down to the root cause by asking "Why?" multiple times.
Analyze Data: Employ tools like Pareto Charts to identify which causes are having the most significant effect.
Identify Solutions: Develop solutions that address the root causes. The PDCA Cycle can guide the process of planning, doing, checking, and acting on these solutions.
Implement and Monitor: Implement the solutions and monitor their effectiveness over time. Adjust as necessary.
Document and Share Findings: Document the RCA process and share your findings with relevant stakeholders to prevent recurrence of the issue. Utilize platforms like RootCause.org for insights and sharing.
Continuous Learning: Stay informed on best practices and new tools in RCA by engaging with resources like The Cause Mapping Method for more detailed guidance.
By following these steps and utilizing the recommended resources, a Quality Control Auditor can significantly improve their RCA process, leading to more effective identification and mitigation of root causes.
How to Display Root Cause Analysis Skills on Your Resume
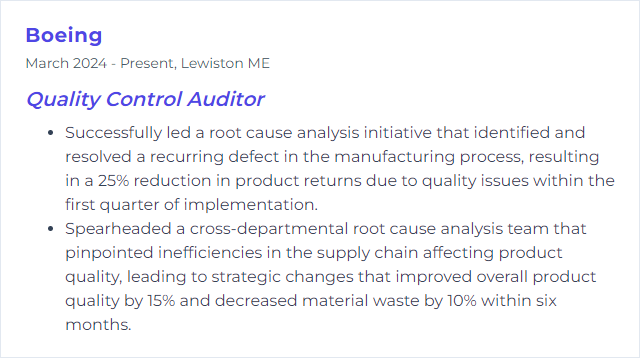
8. Auditing Standards
Auditing Standards are formal guidelines established by authoritative bodies, outlining the principles and procedures for auditors to follow when conducting an audit. They ensure the quality, consistency, and reliability of audit processes and reports, particularly focusing on the integrity, objectivity, and professionalism of auditors. For a Quality Control Auditor, these standards guide the systematic review of the effectiveness and efficiency of an organization's quality management system, ensuring it meets specified requirements and standards.
Why It's Important
Auditing Standards are crucial as they ensure consistency, reliability, and quality in audit processes, enabling Quality Control Auditors to effectively assess and enhance the integrity and accuracy of financial information and compliance with applicable laws and regulations.
How to Improve Auditing Standards Skills
Improving auditing standards, particularly for a Quality Control Auditor, involves a multi-faceted approach that focuses on enhancing the quality, reliability, and effectiveness of audit processes. Here are concise strategies to achieve this:
Continuous Education: Auditors should commit to lifelong learning to stay updated with the latest best practices, standards, and regulatory changes. Organizations like the American Institute of CPAs (AICPA) offer resources and courses for ongoing education.
Leverage Technology: Adopt advanced audit technologies for data analysis and automation to improve accuracy and efficiency. Tools like ACL and Idea can enhance data analytics capabilities.
Strengthen Ethics and Independence: Reinforce ethical guidelines and the importance of independence in auditing. The International Ethics Standards Board for Accountants (IESBA) provides frameworks and resources to uphold these principles.
Peer Reviews and External Quality Assessments: Regularly undergo peer reviews and external quality assessments to ensure compliance with standards and identify areas for improvement. The Peer Review Program by AICPA is a good reference.
Feedback Mechanisms: Implement feedback loops with stakeholders to gather insights on auditing performance and areas needing enhancement. This involves both internal feedback from the audit team and external feedback from clients and regulatory bodies.
Adopt International Standards: Where applicable, align auditing practices with international standards like those set by the International Auditing and Assurance Standards Board (IAASB), to ensure global consistency and quality.
Risk Management Focus: Shift towards a more risk-based audit approach to better identify and address areas of significant risk. This involves ongoing risk assessment throughout the audit process.
Professional Judgment and Skepticism: Cultivate a culture of professional skepticism and judgment, encouraging auditors to critically evaluate evidence and make informed decisions.
By incorporating these strategies, Quality Control Auditors can enhance auditing standards, contributing to more reliable, transparent, and effective audit processes.
How to Display Auditing Standards Skills on Your Resume
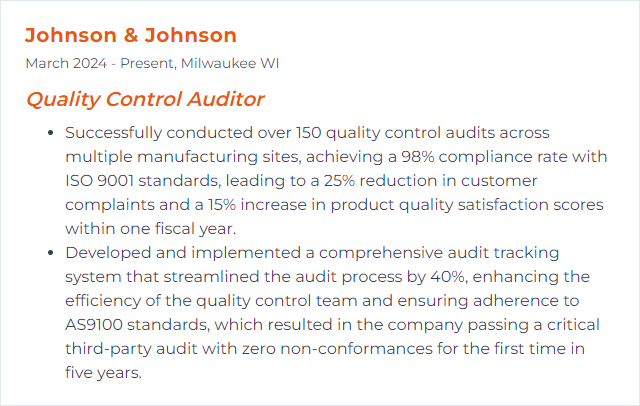
9. Process Improvement
Process Improvement, in the context of a Quality Control Auditor, involves the systematic approach to enhance an organization's procedures, workflows, and practices to increase efficiency, reduce waste, and ensure product or service quality meets established standards.
Why It's Important
Process improvement is crucial for a Quality Control Auditor as it enhances efficiency, reduces errors, and ensures consistent quality, ultimately leading to higher customer satisfaction and competitive advantage.
How to Improve Process Improvement Skills
To improve Process Improvement, especially from a Quality Control Auditor perspective, focus on these concise strategies:
Benchmarking: Compare your processes against industry best practices to identify areas for improvement. ASQ's benchmarking guide offers a solid foundation.
Root Cause Analysis (RCA): Implement RCA methods like the 5 Whys to delve deep into process issues and devise effective solutions.
Continuous Training: Ensure ongoing education for staff on the latest quality control techniques and tools. ASQ’s Training Courses are a good resource.
Lean Six Sigma: Adopt Lean Six Sigma methodologies to streamline processes, reduce waste, and enhance quality. iSixSigma provides comprehensive insights into integrating these practices.
Customer Feedback: Regularly gather and analyze customer feedback to align process improvements with customer expectations. Tools like SurveyMonkey can facilitate this.
Technology Utilization: Leverage technology, such as process automation tools and quality management software, to enhance efficiency and accuracy. Explore options like Smartsheet for Quality Management.
Monitoring and Review: Continuously monitor processes post-implementation and review their impact to ensure sustained improvement. KPI Library can help identify relevant performance indicators.
Focusing on these strategies will foster a culture of continuous improvement, enhancing overall quality and efficiency.
How to Display Process Improvement Skills on Your Resume
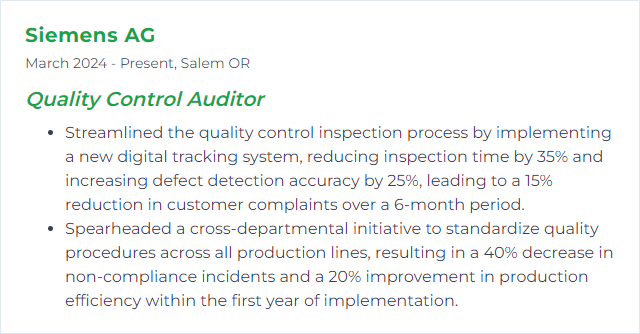
10. Risk Management
Risk management, in the context of a Quality Control Auditor, involves the process of identifying, assessing, and prioritizing potential risks to the quality of products or services, and implementing strategies to minimize or control the impact of these risks on the organization's objectives.
Why It's Important
Risk management is crucial for a Quality Control Auditor as it enables the identification, assessment, and prioritization of potential risks, ensuring the integrity, safety, and compliance of products and processes, thereby preventing defects, minimizing losses, and enhancing customer satisfaction.
How to Improve Risk Management Skills
Improving risk management, especially for a Quality Control Auditor, involves a strategic approach focused on identifying, assessing, and mitigating risks to enhance decision-making processes and operational efficiency. Here's a concise guide:
Identify Risks: Begin by systematically identifying potential risks that could impact quality. Use tools like SWOT analysis and risk assessments to uncover hidden risks.
Assess Risks: Evaluate the likelihood and impact of identified risks using methods like Failure Mode and Effects Analysis (FMEA) or risk matrices. This helps prioritize risks based on severity.
Mitigate Risks: Develop and implement strategies to reduce the likelihood and impact of high-priority risks. This could involve process changes, quality checks, or adopting new technologies. The Plan-Do-Check-Act (PDCA) cycle is a useful framework for continuous improvement.
Monitor and Review: Continuously monitor risk management processes and outcomes. Use Key Performance Indicators (KPIs) to measure effectiveness and make adjustments as needed.
Communication and Reporting: Ensure transparent communication and reporting mechanisms are in place to keep all stakeholders informed about risk management activities and outcomes. Tools like risk dashboards can facilitate this.
Continuous Learning: Foster a culture of continuous learning by regularly reviewing risk management strategies and outcomes. Engage in professional development and stay updated with industry best practices.
For a Quality Control Auditor, focusing on these areas can significantly improve the effectiveness of risk management efforts, contributing to higher quality outcomes and operational excellence.
How to Display Risk Management Skills on Your Resume
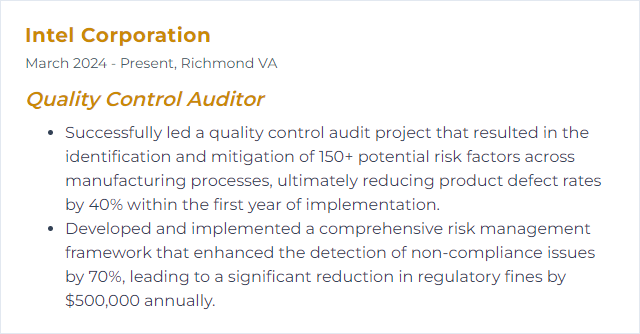
11. Data Interpretation
Data Interpretation, in the context of a Quality Control Auditor, involves analyzing and making sense of collected data to evaluate the quality and consistency of products or processes, ensuring they meet specified standards and identifying areas for improvement.
Why It's Important
Data interpretation is crucial for a Quality Control Auditor as it enables the accurate assessment of product quality, identification of trends and anomalies in manufacturing processes, and informs decision-making for process improvements and compliance with quality standards.
How to Improve Data Interpretation Skills
Improving data interpretation skills, especially for a Quality Control Auditor, involves enhancing your ability to critically analyze, understand, and communicate data findings effectively. Below are concise steps and resources to guide you:
Strengthen Statistical Knowledge: Understanding statistical methods is crucial for accurate data interpretation. Refresh your knowledge on basics and advanced statistics. Khan Academy offers comprehensive lessons.
Practice Data Visualization: Learn to represent data visually for easier interpretation. Tools like Tableau provide training on creating impactful data visualizations.
Develop Analytical Skills: Engage in exercises that boost your ability to analyze complex datasets. Websites like DataCamp offer courses tailored to improving analytical skills.
Understand Quality Control Standards: Familiarize yourself with the latest quality control standards relevant to your field. ASQ (American Society for Quality) is a good starting point for resources and training.
Engage in Continuous Learning: The field of data interpretation and quality control is always evolving. Stay updated with the latest trends and techniques by subscribing to relevant journals and websites like Quality Magazine.
Practical Application: Apply your skills in real-world scenarios. Participate in projects or simulations that allow you to practice data interpretation. This hands-on experience is invaluable.
By following these steps and utilizing the resources provided, you can enhance your data interpretation skills, making you a more effective Quality Control Auditor.
How to Display Data Interpretation Skills on Your Resume
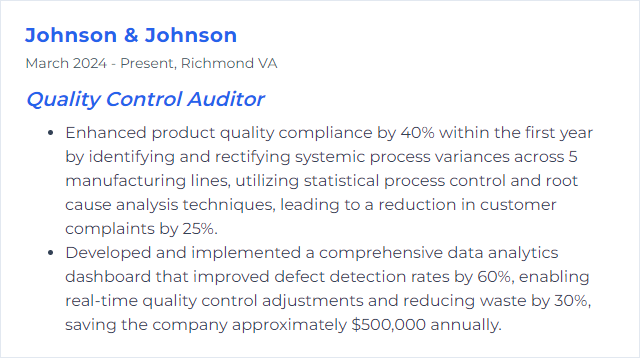
12. Compliance Monitoring
Compliance Monitoring, in the context of a Quality Control Auditor, refers to the systematic process of assessing and ensuring that the operations and procedures of an organization adhere to established regulations, standards, and internal policies to maintain quality and mitigate risks.
Why It's Important
Compliance monitoring is crucial for a Quality Control Auditor as it ensures adherence to regulatory standards and internal policies, mitigating risks, preventing legal penalties, and maintaining product quality and safety.
How to Improve Compliance Monitoring Skills
Improving Compliance Monitoring as a Quality Control Auditor involves a strategic approach aimed at enhancing the efficiency and effectiveness of compliance checks. Here's a concise guide:
Develop a Robust Compliance Framework: Establish clear, up-to-date compliance standards and procedures. This involves understanding regulatory requirements and integrating them into company policies. Compliance Management Guide provides insights on setting up a comprehensive framework.
Implement Risk-Based Monitoring: Focus more resources on high-risk areas. This approach ensures that efforts are concentrated where they're needed most, improving overall compliance. The Institute of Internal Auditors offers guidance on risk-based auditing strategies.
Leverage Technology: Utilize compliance monitoring software to automate routine checks, track compliance levels, and flag non-compliance issues. Software like LogicManager can streamline compliance tasks and improve accuracy.
Regular Training and Education: Keep the team updated with the latest regulatory changes and compliance best practices through ongoing training. Resources like ComplianceOnline offer various training modules on regulatory compliance.
Continuous Improvement: Adopt a continuous improvement mindset by regularly reviewing and updating compliance processes. Solicit feedback from audits and use it to strengthen your compliance monitoring efforts. The Plan-Do-Check-Act (PDCA) Cycle is a useful methodology for this purpose.
Stakeholder Engagement: Engage regularly with stakeholders to ensure that compliance goals align with business objectives and that there is support across the organization. The Project Management Institute discusses strategies for effective stakeholder engagement.
By following these strategies, Quality Control Auditors can enhance their compliance monitoring efforts, ensuring that their organizations remain in line with regulatory standards and avoid potential non-compliance issues.
How to Display Compliance Monitoring Skills on Your Resume
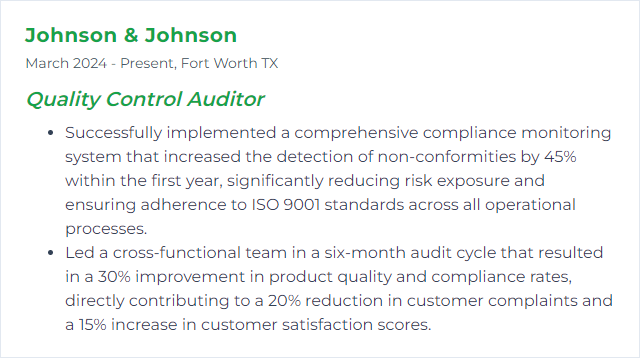