Top 12 Process Control Engineer Skills to Put on Your Resume
In the competitive field of process control engineering, showcasing a robust set of skills on your resume can significantly enhance your employability and set you apart from other candidates. This article outlines the top 12 skills that are crucial for process control engineers to possess, ensuring you present a well-rounded and compelling professional profile to potential employers.

Process Control Engineer Skills
- PLC Programming
- SCADA Systems
- DCS Configuration
- PID Tuning
- HMI Development
- Six Sigma
- MATLAB/Simulink
- AutoCAD
- Industrial Networking
- ISA Standards
- Safety Instrumented Systems
- Process Simulation
1. PLC Programming
PLC programming involves creating and inputting instructions into a Programmable Logic Controller (PLC) to automate and control industrial processes, machinery, and systems, optimizing efficiency, safety, and reliability in operations.
Why It's Important
PLC programming is crucial for Process Control Engineers as it enables the automation and control of manufacturing processes, ensuring efficiency, precision, and safety in industrial operations.
How to Improve PLC Programming Skills
Improving PLC programming skills involves a combination of understanding core concepts, practicing programming, and staying updated with the latest trends and technologies. Here’s a concise guideline:
Master the Basics: Ensure a strong understanding of fundamental PLC concepts such as ladder logic, structured text, and function block diagrams. Websites like PLC Academy offer tutorials and resources.
Hands-On Practice: Apply your knowledge through real-life projects or simulations. Tools like RSLogix 5000 provide environments to practice.
Learn from Industry Standards: Familiarize yourself with industry standards like IEC 61131-3. The IEC website contains valuable resources and documentation.
Continuous Learning: Technologies and best practices evolve. Platforms like LinkedIn Learning and Udemy offer courses on the latest PLC programming trends and tools.
Join Forums and Groups: Engage with communities on platforms like PLCTalk and Reddit’s /r/PLC to exchange knowledge and solve problems.
Understand Your Process: Deepen your knowledge of the specific processes you are controlling. This contextual understanding can significantly improve your programming efficiency and effectiveness.
Vendor Resources: Utilize learning materials and software demos from PLC manufacturers like Siemens or Allen-Bradley.
Certifications and Training: Consider certifications or formal training programs from recognized institutions or vendors to validate your skills and learn structured approaches to PLC programming.
By combining these resources and strategies, you can systematically enhance your PLC programming skills and adapt to the evolving demands of process control engineering.
How to Display PLC Programming Skills on Your Resume

2. SCADA Systems
SCADA (Supervisory Control and Data Acquisition) systems are software and hardware solutions used by process control engineers to monitor, control, and acquire data from industrial processes and machinery in real-time, enhancing operational efficiency and reliability.
Why It's Important
SCADA systems are crucial for Process Control Engineers as they enable the monitoring and control of industrial processes in real-time, ensuring efficiency, reliability, and safety in operations.
How to Improve SCADA Systems Skills
Improving SCADA (Supervisory Control and Data Acquisition) systems involves enhancing their reliability, efficiency, and security. For a Process Control Engineer, consider the following concise strategies:
Upgrade Hardware and Software: Regularly update to the latest versions to fix bugs, improve performance, and add new features. Consider sources like Siemens for hardware and software solutions.
Enhance Security Measures: Implement robust cybersecurity practices, including firewalls, intrusion detection systems, and regular security audits. The National Institute of Standards and Technology (NIST) provides guidelines for improving industrial control system security.
Optimize Network Architecture: Design a resilient network architecture with redundancy and failover capabilities to ensure system availability. Cisco’s Industrial Network and Security solutions can provide insights.
Implement Data Analytics: Use data analytics tools to analyze historical data for predictive maintenance and operational efficiency. Platforms like AVEVA offer predictive analytics for industrial operations.
Train Staff Regularly: Ensure that all users and operators are trained on the latest features, security practices, and troubleshooting procedures. Organizations like ISA offer specialized training for SCADA systems.
Regularly Review and Test the System: Conduct periodic reviews and tests of the SCADA system to ensure it meets current operational requirements and can recover quickly from failures.
By focusing on these areas, Process Control Engineers can significantly improve the performance and security of SCADA systems.
How to Display SCADA Systems Skills on Your Resume

3. DCS Configuration
DCS Configuration refers to the process of setting up and organizing the parameters, control logic, and user interfaces of a Distributed Control System (DCS) to manage and monitor industrial processes efficiently. This involves defining control strategies, input/output allocations, alarm settings, and operator displays to ensure optimal performance and safety of the process operation.
Why It's Important
DCS (Distributed Control System) configuration is crucial for a Process Control Engineer because it ensures optimal control, efficiency, and safety of industrial processes by accurately defining the parameters and logic for automation, process control, and monitoring.
How to Improve DCS Configuration Skills
Improving a Distributed Control System (DCS) configuration involves optimizing its design, implementation, and maintenance for better control and efficiency in industrial processes. Here are concise steps tailored for a Process Control Engineer:
Understand Requirements: Deeply analyze the process requirements, including safety, control strategies, and operational needs. ISA provides standards and resources for understanding control system requirements.
Optimize Control Strategies: Design robust control strategies that enhance process stability and efficiency. Consider advanced control methodologies and loop tuning techniques. Control Global offers insights into control strategies and optimization.
Leverage Simulation: Use simulation tools for testing and validating control strategies before deployment. This reduces risks and improves system reliability. MATLAB & Simulink are widely used for simulation in process control.
Standardize and Modularize: Adopt standard naming conventions, and modularize configurations for ease of maintenance and scalability. The IEC 61131-3 standard provides guidelines for software structuring and naming.
Implement Redundancy: Design the system with redundancy for critical components to enhance reliability and availability. This includes controllers, networks, and power supplies.
Regular Audits and Updates: Conduct regular system audits to identify optimization opportunities and ensure the system is updated to leverage new features and security patches.
Training and Documentation: Ensure comprehensive documentation is available and up-to-date. Conduct regular training sessions for operators and engineers. The ISA Training provides various courses on DCS and process control.
Cybersecurity Measures: Implement robust cybersecurity measures to protect the DCS from threats. NIST’s Guide for Industrial Control Systems Security provides comprehensive guidelines.
By following these steps, you can improve the efficiency, reliability, and security of a DCS configuration.
How to Display DCS Configuration Skills on Your Resume
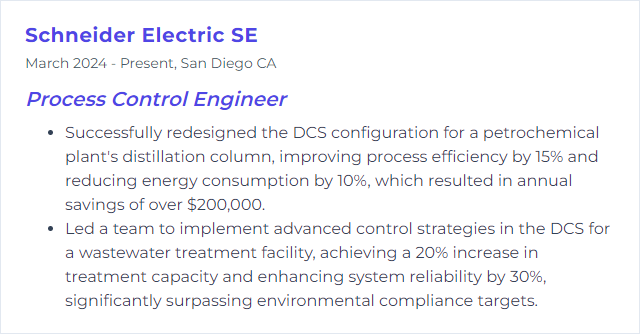
4. PID Tuning
PID tuning is the process of adjusting the parameters of a Proportional-Integral-Derivative (PID) controller to achieve optimal control performance, ensuring that a system responds quickly and accurately to changes while minimizing overshoot and settling time.
Why It's Important
PID tuning is crucial because it optimizes the control loop's response, ensuring stability, precision, and efficiency in reaching and maintaining the desired process variable, critical for maintaining operational safety, quality, and cost-effectiveness in process control systems.
How to Improve PID Tuning Skills
Improving PID tuning involves a systematic approach to optimize the control loop performance. Key steps include:
Understand the Process: Grasp the dynamics of the process including any dead time, process lag, and the type of control required (e.g., level, temperature).
Start with Manual Tuning: Initially, set Integral (I) and Derivative (D) gains to zero. Adjust the Proportional (P) gain until the loop oscillates, then halve the P gain.
Increment Integral Gain: Slowly increase the I gain until you achieve the desired speed of reaching the setpoint without causing instability.
Adjust Derivative Gain: D gain can be increased to improve the response time and reduce overshoot, but be cautious as too much D gain can induce noise and instability.
Use Software Tools: Consider using PID tuning software for more complex systems. These tools can simulate different tuning parameters and their impacts on the control loop.
Implement Feedback and Feedforward Control: If the process has significant disturbances, incorporating feedforward control along with PID feedback control can improve performance.
Continuous Monitoring and Adjustment: Regularly monitor the performance of the control loop and make adjustments as necessary. Process conditions can change over time.
Learn from Resources: There are numerous online resources and communities where you can learn more about PID tuning and share your experiences.
- Control Guru - Practical PID control and loop tuning fundamentals.
- PID Tuning Guide - A comprehensive guide to PID tuning.
- ISA - The International Society of Automation offers resources and certification for process control engineers.
Remember, PID tuning is an iterative process, and often a balance between competing requirements like speed of response and stability must be found.
How to Display PID Tuning Skills on Your Resume
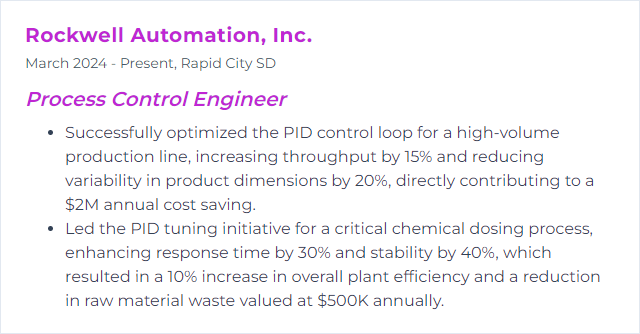
5. HMI Development
HMI Development involves creating and designing the user interface for industrial process control systems, allowing operators to interact efficiently and effectively with machinery and process operations through visualizations, controls, and monitoring tools.
Why It's Important
HMI (Human-Machine Interface) development is crucial for Process Control Engineers as it facilitates effective interaction between humans and process control systems, enabling intuitive monitoring, controlling, and diagnosing of industrial processes, thus ensuring operational efficiency, safety, and reliability.
How to Improve HMI Development Skills
Improving HMI (Human-Machine Interface) development, especially from a Process Control Engineer's perspective, involves focusing on user-centered design, simplicity, clarity, and system responsiveness. Here's a concise guide:
Emphasize User-Centric Design: Understand the end-users' needs and tasks. Nielsen Norman Group offers insights into user-centered design principles.
Simplify the Interface: Use clear and intuitive layouts. Minimize clutter to enhance usability. The Interaction Design Foundation provides guidelines on simplifying UI designs.
Ensure Clarity: Use straightforward language and symbols. Consistency in design elements is key. ISO 9241-210 provides guidance on ergonomics of human-system interaction.
Enhance System Responsiveness: Optimize system feedback and update times. Web.dev has resources on improving web performance and responsiveness.
Incorporate Feedback Loops: Regularly test the HMI with actual users and iteratively refine based on feedback. Usability.gov discusses the importance of user testing in interface design.
Adopt Industry Best Practices and Standards: Familiarize yourself with standards such as ISA 101.01 for HMI design in process control. ISA provides resources and standards for effective HMI implementation.
By focusing on these areas, a Process Control Engineer can significantly improve HMI development for better user experience and system efficiency.
How to Display HMI Development Skills on Your Resume
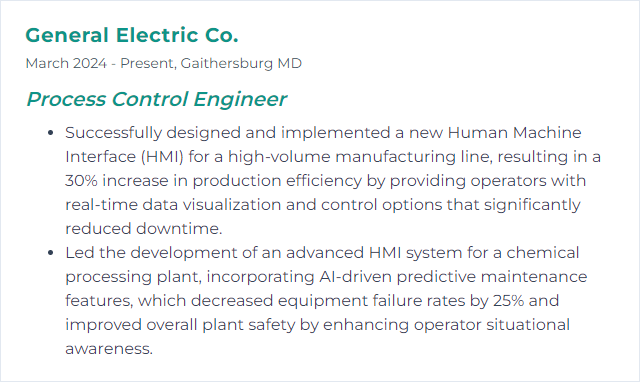
6. Six Sigma
Six Sigma is a data-driven, quality control methodology aimed at reducing defects and improving processes by systematically removing variability and inefficiencies in manufacturing and business operations.
Why It's Important
Six Sigma is important for a Process Control Engineer because it provides a systematic methodology to identify, analyze, and reduce variability and defects in processes, thus enhancing efficiency, quality, and reliability of production outcomes.
How to Improve Six Sigma Skills
Improving Six Sigma as a Process Control Engineer can be approached by focusing on advanced data analysis, enhancing process understanding, and integrating technology. Here are short, actionable steps:
Strengthen Statistical Analysis Skills: Deepen your understanding of statistical tools essential for Six Sigma projects. Khan Academy offers resources to sharpen these skills.
Leverage Process Simulation Tools: Utilize simulation software like Simul8 for visualizing and optimizing processes before actual implementation.
Continuously Learn about Lean Six Sigma: Stay updated with the latest trends, tools, and techniques in Lean Six Sigma. Websites like ASQ are great for resources and certification information.
Implement Advanced Data Analytics: Explore tools like Minitab for deeper data analysis, which is crucial for identifying process improvements.
Focus on Soft Skills: Effective communication and project management are key. Resources like LinkedIn Learning can help enhance these skills.
Participate in Professional Forums: Engage in forums such as iSixSigma to exchange ideas and best practices with professionals worldwide.
Automate Routine Tasks: Use automation tools to streamline data collection and analysis, allowing more time for strategic activities. Explore platforms like Zapier.
By focusing on these areas, Process Control Engineers can significantly impact their Six Sigma initiatives, leading to more efficient and effective process improvements.
How to Display Six Sigma Skills on Your Resume
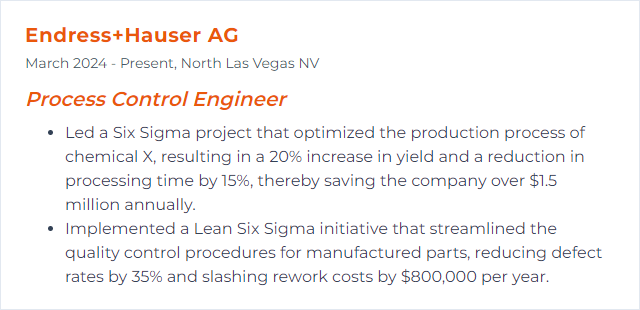
7. MATLAB/Simulink
MATLAB/Simulink is a computational software environment used for modeling, simulation, and analysis of dynamic systems, enabling Process Control Engineers to design and test control strategies, analyze system performance, and optimize processes in a virtual environment before implementation in real-world systems.
Why It's Important
MATLAB/Simulink is crucial for Process Control Engineers due to its powerful simulation capabilities, extensive library of tools for system modeling, analysis, and design, and its intuitive graphical interface for designing control strategies. This enables engineers to efficiently develop, test, and implement advanced control algorithms for optimizing process performance and stability.
How to Improve MATLAB/Simulink Skills
Improving your MATLAB/Simulink skills as a Process Control Engineer involves focusing on several key areas: mastering the fundamentals, understanding control system design and analysis, leveraging MATLAB/Simulink for process control simulations, enhancing model-based design capabilities, and staying updated with the latest features and resources. Here’s a concise guide:
Master the Fundamentals: Start with MATLAB Onramp for a free introduction to MATLAB basics. This will solidify your foundation in MATLAB programming and data analysis.
Learn Control System Design and Analysis: Dive into the Control System Toolbox in MATLAB. It provides algorithms and apps for systematically analyzing, designing, and tuning linear control systems.
Simulate Process Control Systems: Use Simulink for simulating dynamic systems. Begin with the Simulink Onramp to learn the basics of creating, editing, and simulating Simulink models relevant to process control engineering.
Enhance Model-Based Design: Explore the Model-Based Design approach for designing and implementing control systems. This integrates simulation, validation, and implementation of control algorithms.
Stay Updated: MATLAB and Simulink evolve constantly. Keep abreast of the latest features and training courses offered by MathWorks. Participate in webinars and user communities for insights and updates relevant to process control engineering.
Practice with Real-World Examples: Engage in projects that simulate real-world control problems. MathWorks provides examples and case studies directly applicable to process control engineering.
Utilize External Resources: Look for additional resources outside the MathWorks ecosystem. Books, academic courses, and online platforms like Coursera, EDX, or Udemy offer courses tailored to MATLAB/Simulink for process control.
By focusing on these areas, you can significantly improve your MATLAB/Simulink skills and apply them more effectively in process control engineering projects.
How to Display MATLAB/Simulink Skills on Your Resume
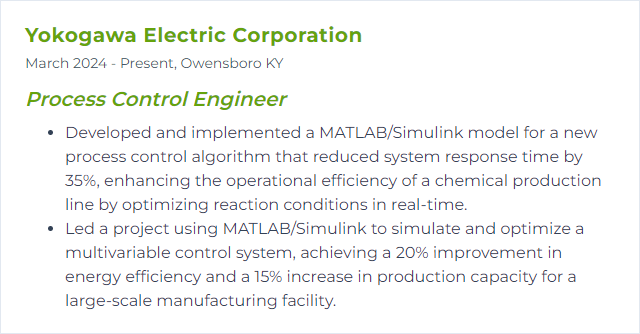
8. AutoCAD
AutoCAD is a computer-aided design (CAD) software used for creating and editing 2D and 3D drawings and models, essential for process control engineers for designing and planning layouts of control systems and process plants.
Why It's Important
AutoCAD is crucial for Process Control Engineers as it enables precise design and modification of control systems, facilitates the visualization of process flows, and ensures accurate layout planning for efficient and safe plant operations.
How to Improve AutoCAD Skills
To enhance your AutoCAD skills as a Process Control Engineer, focus on mastering specific features relevant to process control design and automation. Here's a concise guide:
Learn Dynamic Blocks and Parametric Constraints: Tailor components for process control systems efficiently. Autodesk's Dynamic Blocks and Parametric Constraints tutorials can be a good start.
Utilize AutoCAD P&ID: Improve your process diagrams. Autodesk offers resources to get started with AutoCAD P&ID, enhancing your ability to design complex process control systems.
Customize AutoCAD Using APIs: Automate repetitive tasks and create custom functions. Explore AutoCAD's APIs and Developer Documentation for customization and automation.
Embrace AutoCAD Electrical: For process control engineers, understanding electrical design is crucial. Dive into AutoCAD Electrical to integrate electrical systems into your control processes seamlessly.
Engage with the Community and Training: Autodesk's AutoCAD Community provides access to experts and peers for learning and troubleshooting. Additionally, consider official AutoCAD Training to enhance your skills systematically.
By focusing on these areas, you can significantly improve your AutoCAD proficiency for process control engineering tasks.
How to Display AutoCAD Skills on Your Resume
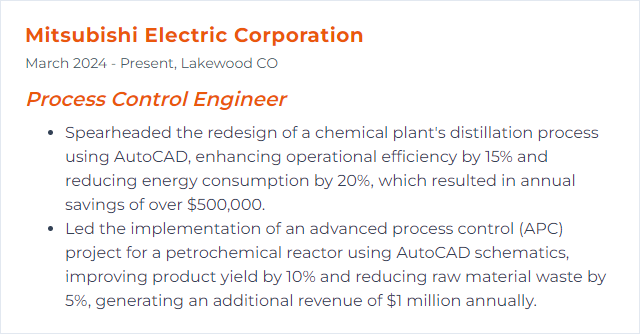
9. Industrial Networking
Industrial Networking in the context of a Process Control Engineer refers to the design and use of network systems to connect and control industrial equipment, sensors, and processes, facilitating real-time data exchange, monitoring, and automated control within industrial environments for improved efficiency and reliability.
Why It's Important
Industrial networking is crucial for a Process Control Engineer because it enables seamless communication and integration between various control systems and machinery, facilitating real-time monitoring, data exchange, and control over industrial processes for improved efficiency, reliability, and safety.
How to Improve Industrial Networking Skills
Improving industrial networking in the context of process control engineering involves enhancing reliability, security, and efficiency in communication systems used in industrial environments. Here are concise steps towards improvement:
Assess Network Architecture: Start by evaluating the current network infrastructure. Identify bottlenecks, unnecessary complexities, or vulnerabilities. Cisco's Industrial Networking offers insights and solutions tailored for industrial applications.
Implement Redundancy: Ensure network reliability by implementing redundant pathways. This minimizes downtime by providing alternative routes for data flow in case of a failure. Rockwell Automation discusses redundancy strategies within industrial networks.
Segment Networks: Use network segmentation to improve security and performance. This involves dividing the network into smaller, manageable segments, each with its own security policies. Siemens’ Industrial Security services offer guidance on secure network design and segmentation.
Apply Industrial Protocols: Utilize industrial communication protocols like EtherNet/IP, Profinet, or Modbus TCP, which are designed for high reliability and real-time performance in industrial environments. Profinet University provides resources on understanding and implementing Profinet.
Enhance Cybersecurity: Protect the network against cyber threats with firewalls, intrusion detection systems, and regular security audits. Applying patches and updates to network components is crucial. ISA/IEC 62443 standards framework offers comprehensive guidance on industrial network security.
Invest in Training: Ensure that staff are well-trained in network management, security practices, and emergency response procedures. Continuous education is key to adapting to evolving technologies and threats. ISA Training provides a variety of courses related to automation and industrial networking.
By taking these steps, a process control engineer can significantly improve the robustness, efficiency, and security of industrial networks, ensuring smoother and safer operations.
How to Display Industrial Networking Skills on Your Resume
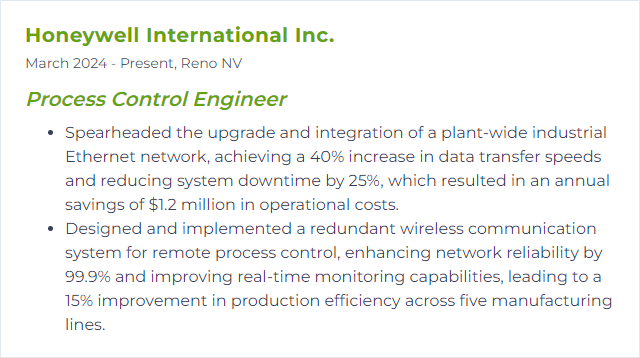
10. ISA Standards
ISA standards, developed by the International Society of Automation, are formal guidelines and best practices for automation and control systems. They cover aspects such as instrumentation symbols, safety, cybersecurity, and performance requirements, helping Process Control Engineers ensure system reliability, efficiency, and safety in industrial processes.
Why It's Important
ISA Standards are crucial for Process Control Engineers as they ensure interoperability, safety, and efficiency in automation and control systems, facilitating consistent, high-quality processes across industries.
How to Improve ISA Standards Skills
Improving ISA standards, particularly for a Process Control Engineer, involves staying updated with industry changes, actively participating in ISA committees, and contributing to the development and revision of standards. Here’s a concise guide:
Stay Informed: Regularly visit the ISA website to stay informed about the latest standards and amendments in process control engineering.
Participate in Committees: Join ISA standards development committees. Participation is open to anyone; you can apply by visiting the ISA Standards Participation page.
Continuing Education: Enroll in ISA’s training courses to enhance your expertise and stay current with best practices in process control.
Feedback and Proposals: Provide feedback on existing standards and propose new ideas through the channels provided by ISA. Engage in discussions and provide valuable insights based on your experience.
Collaborate: Work with other professionals and organizations to share knowledge and push for improvements. Collaboration can lead to more robust and widely applicable standards.
Advocacy: Promote the importance of ISA standards within your organization and the wider industry. Encouragement from multiple sources can lead to more resources being allocated towards the development and refinement of standards.
By actively engaging with the ISA and its community, Process Control Engineers can contribute significantly to the enhancement of ISA standards, ensuring they remain relevant and effective in addressing current and future challenges in the industry.
How to Display ISA Standards Skills on Your Resume
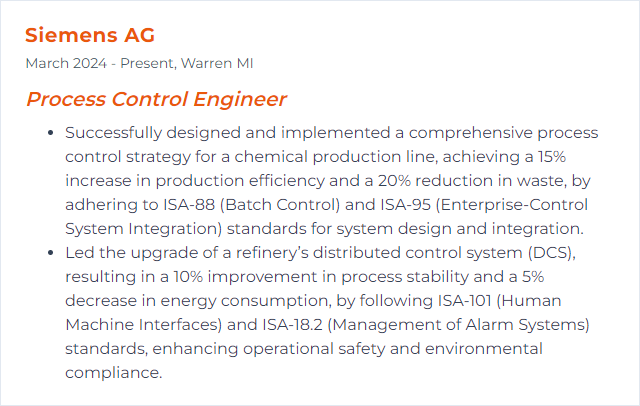
11. Safety Instrumented Systems
Safety Instrumented Systems (SIS) are specialized control systems implemented in process industries to monitor and manage the operational conditions of a plant or process. Their primary function is to ensure safety by bringing the process to a safe state in the event of certain predetermined conditions, thereby preventing accidents or mitigating hazardous events. They are an integral part of a process control engineer's toolkit for risk management and compliance with safety standards.
Why It's Important
Safety Instrumented Systems (SIS) are crucial because they provide an automated means to prevent hazardous events by bringing processes to a safe state in case of abnormal conditions, thereby protecting people, the environment, and assets while ensuring operational continuity.
How to Improve Safety Instrumented Systems Skills
Improving Safety Instrumented Systems (SIS) involves a systematic approach to ensure process safety and reliability. Here are concise steps tailored for a Process Control Engineer:
Risk Assessment: Conduct a thorough risk assessment to identify potential hazards and define the required Safety Integrity Level (SIL) for each safety function.
Design and Selection: Use industry standards (e.g., IEC 61511/ISA-84) for the design and selection of SIS components to meet the specified SIL requirements.
Redundancy and Diversity: Incorporate redundancy and diversity in system design to enhance fault tolerance and avoid common-cause failures.
Regular Testing and Maintenance: Implement a regular testing and maintenance schedule to ensure SIS components function correctly and to address wear and tear or software updates promptly.
Performance Monitoring: Use real-time performance monitoring tools to track the operational effectiveness of the SIS and identify areas for improvement.
Training and Documentation: Ensure ongoing training for operators and engineers and maintain comprehensive documentation for system configurations, modifications, and procedures.
Continuous Improvement: Adopt a continuous improvement mindset, leveraging lessons learned, audit findings, and industry best practices to enhance SIS performance over time.
By systematically addressing each of these areas, Process Control Engineers can significantly improve the safety, reliability, and effectiveness of Safety Instrumented Systems.
How to Display Safety Instrumented Systems Skills on Your Resume
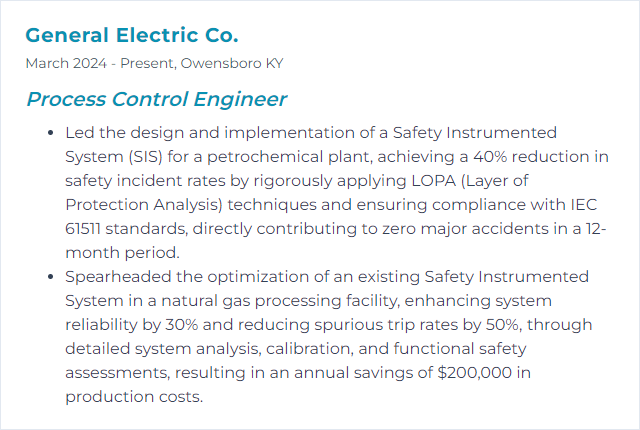
12. Process Simulation
Process simulation is a computer-based modeling technique used by process control engineers to replicate the behavior of a process system, allowing for analysis, design optimization, and control strategy testing without affecting the actual system.
Why It's Important
Process simulation is essential for a Process Control Engineer because it enables the design, analysis, and optimization of process systems virtually, ensuring safety, efficiency, and cost-effectiveness before physical implementation.
How to Improve Process Simulation Skills
Improving process simulation involves enhancing model accuracy, incorporating real-time data, and continuously validating the model. Here’s a concise guide:
Enhance Model Accuracy: Refine your simulation model by incorporating detailed and accurate physical property data and thermodynamic models. Use authoritative sources like NIST for data.
Incorporate Real-Time Data: Integrate real-time process data into your simulation to improve dynamic behavior prediction. Tools like OPC Foundation standards facilitate data acquisition from control systems.
Continuous Validation and Calibration: Regularly compare simulation outcomes with actual plant data to identify discrepancies. Adjust model parameters accordingly to improve fidelity. The International Society of Automation offers resources on best practices.
Utilize Advanced Control Strategies: Implement Model Predictive Control (MPC) or other advanced control strategies to enhance process control and simulation accuracy. Resources at IEEE Xplore provide in-depth research and case studies.
Training and Education: Stay updated with the latest simulation techniques and tools through continuous learning. Platforms like Coursera and edX offer courses related to process simulation and control engineering.
Collaborate and Share Knowledge: Engage with professional communities and forums such as Eng-Tips to share experiences and solutions with peers.
Improving process simulation is an ongoing effort that requires keeping abreast of the latest developments in simulation technology and process control strategies.
How to Display Process Simulation Skills on Your Resume
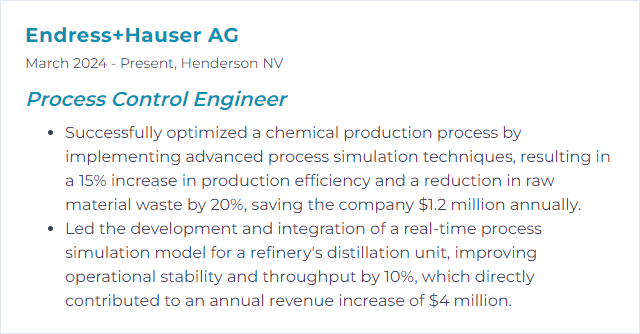