Top 12 Manufacturing Process Engineer Skills to Put on Your Resume
In today's competitive job market, standing out as a manufacturing process engineer requires showcasing a blend of technical proficiency and soft skills on your resume. Highlighting the top skills that demonstrate your ability to optimize manufacturing processes and drive efficiency is crucial for catching the eye of potential employers and advancing your career in this field.
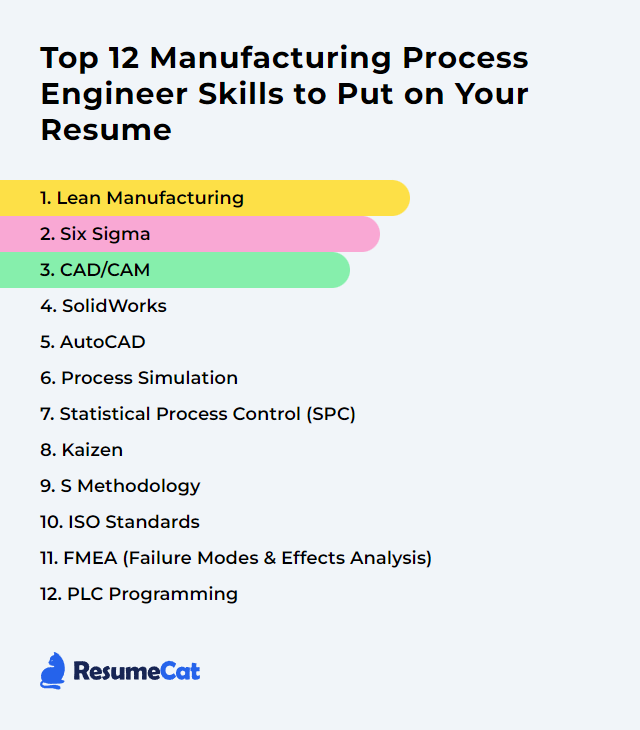
Manufacturing Process Engineer Skills
- Lean Manufacturing
- Six Sigma
- CAD/CAM
- SolidWorks
- AutoCAD
- Process Simulation
- Statistical Process Control (SPC)
- Kaizen
- S Methodology
- ISO Standards
- FMEA (Failure Modes and Effects Analysis)
- PLC Programming
1. Lean Manufacturing
Lean Manufacturing is a systematic approach aimed at minimizing waste within manufacturing systems while simultaneously maximizing productivity. It focuses on enhancing efficiency, reducing lead times, and improving overall quality through continuous improvement and respect for people.
Why It's Important
Lean Manufacturing is crucial because it enhances efficiency and quality by eliminating waste, reducing production time and costs, and improving product value, directly impacting a Manufacturing Process Engineer's ability to optimize processes, increase productivity, and meet customer demands effectively.
How to Improve Lean Manufacturing Skills
Improving Lean Manufacturing involves streamlining processes to reduce waste and enhance efficiency. As a Manufacturing Process Engineer, consider the following concise strategies:
Value Stream Mapping: Identify and map all steps in your manufacturing process, from raw material to customer delivery, to pinpoint waste and inefficiencies. Value Stream Mapping Guide
5S Methodology: Implement the 5S (Sort, Set in order, Shine, Standardize, Sustain) to organize the workplace, improve safety, and increase efficiency. 5S Details
Kaizen (Continuous Improvement): Foster a culture of continuous improvement through small, incremental changes involving all employees. Kaizen Techniques
JIT (Just-In-Time) Production: Reduce inventory costs and waste by producing only what is needed, when it is needed. JIT Explained
Root Cause Analysis: When problems occur, use tools like the 5 Whys or Fishbone Diagram to identify and address the underlying causes, rather than just the symptoms. Root Cause Analysis Techniques
Standard Work: Document and follow the most efficient way to complete each task, ensuring consistency and quality. Standard Work Basics
Automation and Technology: Integrate appropriate technologies to automate repetitive tasks and collect data for continuous improvement. Manufacturing Technology Insights
By focusing on these areas, you can drive significant improvements in your manufacturing processes.
How to Display Lean Manufacturing Skills on Your Resume
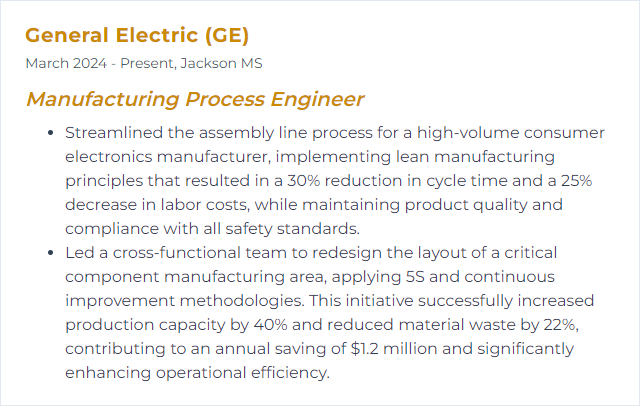
2. Six Sigma
Six Sigma is a data-driven methodology aimed at reducing defects and variability in manufacturing processes to improve quality and efficiency by identifying and eliminating the root causes of errors.
Why It's Important
Six Sigma is crucial for a Manufacturing Process Engineer as it provides a systematic methodology to reduce defects and variability in manufacturing processes, thereby increasing efficiency, improving product quality, and reducing costs.
How to Improve Six Sigma Skills
Improving Six Sigma in a manufacturing environment involves streamlining processes, enhancing quality control, and fostering a culture of continuous improvement. Here's a concise guide:
Strengthen Process Understanding: Deepen your knowledge of the manufacturing processes through tools like Process Mapping and Value Stream Mapping. This helps identify inefficiencies and areas for improvement. ASQ’s guide on Process Mapping
Implement DMAIC Rigorously: Follow the Define, Measure, Analyze, Improve, Control (DMAIC) methodology strictly to solve problems and improve processes. iSixSigma’s DMAIC overview
Utilize Statistical Tools: Apply statistical tools like Control Charts and Design of Experiments (DOE) to monitor process performance and identify factors affecting quality. More on Statistical Tools from NIST
Engage and Train Your Team: Six Sigma is a team effort. Engage your team in Six Sigma training and projects to foster a culture of continuous improvement. Six Sigma Training from ASQ
Leverage Technology: Use technology and software to streamline data collection and analysis for Six Sigma projects. This can improve accuracy and time efficiency. Minitab’s Six Sigma Software Solutions
Benchmark and Learn: Always look outside your organization for best practices and lessons learned. Benchmark against industry leaders to set realistic, yet challenging targets. Benchmarking Guidance from APQC
Improving Six Sigma in manufacturing requires a commitment to learning, process improvement, and employee engagement. By following these steps and leveraging the resources provided, you can enhance your Six Sigma initiatives and drive significant improvements in your manufacturing processes.
How to Display Six Sigma Skills on Your Resume
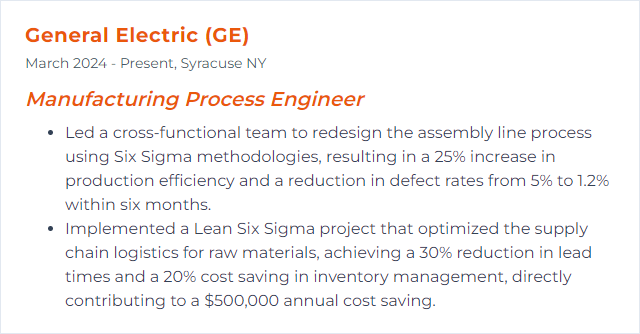
3. CAD/CAM
CAD/CAM stands for Computer-Aided Design/Computer-Aided Manufacturing. It is a technology used by engineers, including Manufacturing Process Engineers, for designing products and controlling manufacturing processes. CAD/CAM software allows for the creation of precise drawings and models of products, and the programming of manufacturing machines to automate the production process, enhancing efficiency, precision, and productivity.
Why It's Important
CAD/CAM is essential for a Manufacturing Process Engineer because it streamlines the design and manufacturing process, enhances precision, reduces errors, and allows for easy modifications, leading to improved efficiency, cost savings, and faster time-to-market for products.
How to Improve CAD/CAM Skills
To improve CAD/CAM in the context of Manufacturing Process Engineering, focus on the following strategies:
Training and Education: Invest in continuous learning to stay updated with the latest CAD/CAM technologies and techniques. Autodesk offers comprehensive training courses.
Integration of CAD/CAM Systems: Ensure seamless integration between CAD and CAM systems for more efficient workflows. PTC provides insights on enhancing CAD/CAM integration.
Automation of Design to Manufacturing Processes: Utilize CAD/CAM software that offers automation capabilities to reduce manual tasks and errors. Mastercam's automation tools can streamline operations.
Optimize Toolpaths and Machining Strategies: Use advanced toolpath strategies and simulation tools to optimize machining efficiency and material removal rates. Fusion 360 offers advanced CAM capabilities.
Customization and Scripting: Customize CAD/CAM processes through scripting to fit unique manufacturing needs. SOLIDWORKS' API and scripting options provide flexibility, learn more here.
Collaboration and Data Management: Facilitate better collaboration among teams and manage CAD/CAM data efficiently with PLM (Product Lifecycle Management) tools. Siemens offers Teamcenter for comprehensive data management.
Hardware Optimization: Ensure that your hardware is optimized for CAD/CAM operations for faster processing and rendering times. HP details some of the best practices for hardware optimization.
By focusing on these strategies, Manufacturing Process Engineers can significantly improve CAD/CAM processes, leading to more efficient and effective manufacturing operations.
How to Display CAD/CAM Skills on Your Resume
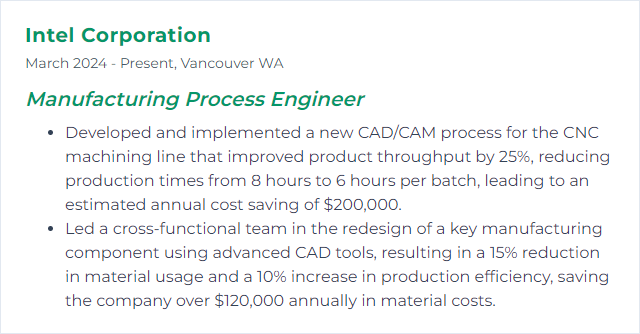
4. SolidWorks
SolidWorks is a computer-aided design (CAD) and engineering software used for creating 3D models and assemblies, facilitating the design and modification of products within manufacturing processes.
Why It's Important
SolidWorks is crucial for a Manufacturing Process Engineer because it enables precise 3D modeling and simulation of manufacturing processes, facilitating efficient design, optimization, and validation of products before production, thereby reducing costs and time-to-market.
How to Improve SolidWorks Skills
Improving SolidWorks proficiency, especially for a Manufacturing Process Engineer, involves enhancing both software skills and understanding its application in manufacturing processes. Here's a concise guide:
Master SolidWorks Basics: Ensure you're comfortable with the fundamentals. SolidWorks offers official training courses that cover everything from basic to advanced techniques.
Learn SolidWorks Simulation: Understand how to use SolidWorks Simulation to validate your designs. This feature helps in predicting performance before manufacturing. More information is available on the SolidWorks Simulation page.
Customize SolidWorks for Efficiency: Tailor the SolidWorks interface and functionality to suit your specific manufacturing engineering needs. Learn about customization through the SolidWorks API.
Integrate CAD with CAM: Leverage SolidWorks CAM or integrate with a preferred CAM solution to streamline the transition from design to manufacturing. Explore options at SolidWorks CAM.
Stay Updated: Always work with the latest version of SolidWorks to utilize new features and improvements. Attend SolidWorks World or similar events to stay informed.
Practice and Projects: Apply your skills in real-life projects. Challenges and practical applications improve problem-solving skills and software mastery.
Join SolidWorks Community: Engage with the SolidWorks Community to exchange knowledge, tips, and tricks with peers.
Explore Online Resources: Utilize online platforms like Lynda.com or Udemy for additional courses and tutorials tailored to manufacturing and process engineering.
Focusing on these areas will significantly enhance your SolidWorks skills, making you more efficient and effective in your role as a Manufacturing Process Engineer.
How to Display SolidWorks Skills on Your Resume
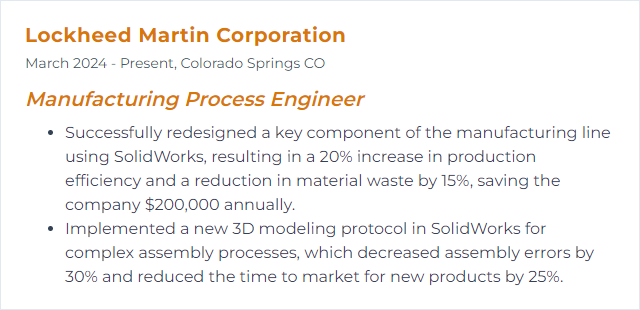
5. AutoCAD
AutoCAD is a computer-aided design (CAD) software used for creating precise 2D and 3D drawings and models, essential for manufacturing process engineers for designing, planning, and optimizing production processes.
Why It's Important
AutoCAD is crucial for a Manufacturing Process Engineer as it enables precise design, modification, and optimization of manufacturing processes and equipment layouts, ensuring efficiency, accuracy, and adherence to specifications.
How to Improve AutoCAD Skills
To enhance AutoCAD proficiency for a Manufacturing Process Engineer, focus on the following strategies:
Training and Continuous Learning: Regularly update your skills through Autodesk's official training courses and Lynda.com's AutoCAD tutorials.
Customization and Automation: Utilize AutoCAD's scripting capabilities for repetitive tasks. Learn about scripting and customization through AutoCAD's customization guide.
Utilize AutoCAD's Libraries and Toolsets: Leverage specialized toolsets for manufacturing available in AutoCAD. Explore them on AutoCAD's Toolsets page.
Incorporate CAD Standards: Apply industry-specific CAD standards to streamline workflows. National Institute of Building Sciences offers standards useful for various engineering fields.
Collaboration and Sharing: Use AutoCAD’s collaboration features to work efficiently with teams. Learn about collaboration options at AutoCAD's Collaboration Features guide.
Feedback and Continuous Improvement: Regularly review and optimize your CAD processes based on feedback from peers and project outcomes.
By focusing on these areas, a Manufacturing Process Engineer can significantly improve their efficiency and accuracy when working with AutoCAD.
How to Display AutoCAD Skills on Your Resume
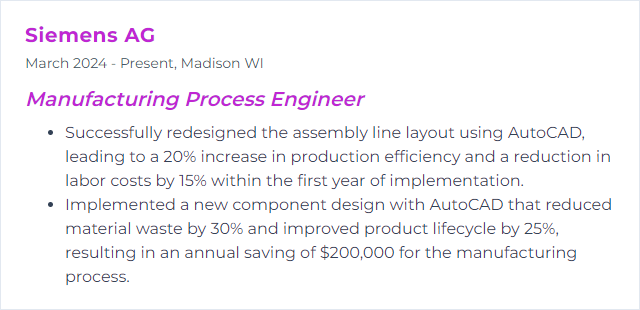
6. Process Simulation
Process simulation in the context of a manufacturing process engineer involves using computer models to replicate and analyze the performance of a manufacturing process. It allows for the examination of process behavior, assessment of efficiency, and identification of potential improvements without physically altering the production line, thereby saving time and resources.
Why It's Important
Process simulation is crucial for a Manufacturing Process Engineer because it enables the prediction and optimization of manufacturing processes, ensuring efficiency, minimizing costs, and enhancing product quality by identifying potential issues and opportunities for improvement before physical implementation.
How to Improve Process Simulation Skills
To improve process simulation as a Manufacturing Process Engineer, follow these concise steps:
Understand the Process: Deeply understand the manufacturing process, including input variables, output variables, and constraints. Learn More.
Select the Right Software: Choose simulation software that best fits your industry and specific process needs, such as Siemens Tecnomatix, AnyLogic, or Arena. Compare Software.
Gather Accurate Data: Collect precise and comprehensive data about your process, including machine parameters, process times, and failure rates. Data Collection Tips.
Model Calibration: Calibrate your model by adjusting it to closely reflect real-world outcomes. This may involve iterative testing and adjustments. Calibration Guide.
Validate and Verify: Ensure the model's accuracy by comparing its predictions with actual process results. Validation Techniques.
Optimize: Use the simulation to identify bottlenecks, waste, and opportunities for efficiency improvements. Implement changes and re-simulate to measure impact. Optimization Strategies.
Continuous Improvement: Regularly update the simulation model based on changes in the process or to explore new scenarios for further efficiency gains. Kaizen.
By following these steps and leveraging the right resources, you can significantly improve process simulation in manufacturing engineering.
How to Display Process Simulation Skills on Your Resume
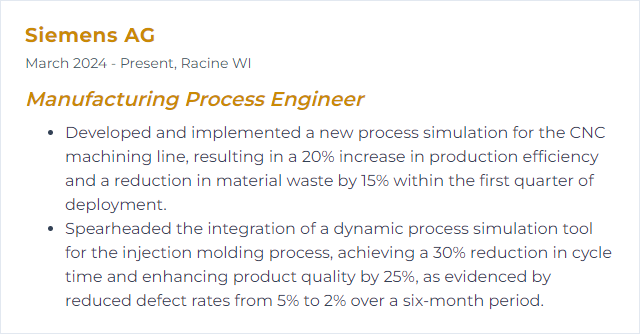
7. Statistical Process Control (SPC)
Statistical Process Control (SPC) is a method used by manufacturing process engineers to monitor and control production processes through statistical analysis, ensuring that the process operates at its full potential and produces goods that meet quality standards. It involves using control charts to detect and prevent process variability or defects before they occur, aiming to achieve and maintain product quality over time.
Why It's Important
Statistical Process Control (SPC) is vital for a Manufacturing Process Engineer because it enables real-time monitoring and control of manufacturing processes, ensuring product quality and consistency while reducing waste and costs by identifying variations and defects early.
How to Improve Statistical Process Control (SPC) Skills
Improving Statistical Process Control (SPC) in a manufacturing environment involves several key steps. As a Manufacturing Process Engineer, focus on:
Educating and Training: Ensure all team members understand SPC concepts and tools. ASQ’s SPC Resources offer valuable insights.
Implementing Real-Time Data Collection: Utilize SCADA systems for automatic data collection and analysis, facilitating immediate adjustments.
Choosing the Right SPC Tools: Select appropriate SPC tools (e.g., control charts, Pareto analysis) based on your process characteristics. The NIST/SEMATECH e-Handbook of Statistical Methods provides comprehensive guidance.
Regularly Reviewing and Adjusting SPC Parameters: Continually review control limits and process capabilities to adapt to process improvements or changes. Minitab’s Guide on understanding process capability is helpful.
Fostering a Culture of Continuous Improvement: Encourage a culture that seeks to improve processes through SPC. The Lean Enterprise Institute offers insights into embedding continuous improvement into your organizational culture.
Utilizing Software Tools Effectively: Deploy SPC software that allows for easy data analysis and visualization. InfinityQS and Minitab are prominent options.
Integrating SPC with Quality Management Systems: Ensure SPC efforts are aligned with overall quality objectives. ISO 9001 guidelines can provide a framework for integrating quality management systems with SPC practices.
Incorporating these strategies can significantly enhance SPC effectiveness in manufacturing, leading to improved process control, quality, and efficiency.
How to Display Statistical Process Control (SPC) Skills on Your Resume
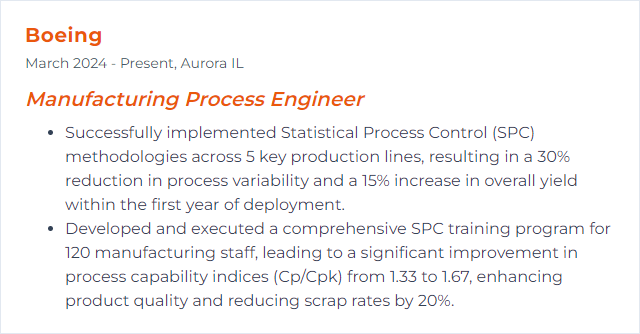
8. Kaizen
Kaizen is a Japanese philosophy emphasizing continuous, incremental improvement in manufacturing processes, focusing on efficiency, quality, and eliminating waste.
Why It's Important
Kaizen is important for a Manufacturing Process Engineer as it promotes continuous, incremental improvements in the manufacturing process, leading to increased efficiency, reduced waste, and enhanced product quality, thereby improving overall productivity and competitiveness.
How to Improve Kaizen Skills
To improve Kaizen, especially for a Manufacturing Process Engineer, focus on the following concise strategies:
Continuous Learning: Encourage continuous skill development and learning. MIT's free online courses on manufacturing and process engineering can be a good resource.
Employee Involvement: Actively involve all employees in the Kaizen process. Tools like Slack can facilitate communication and idea sharing.
Standardize Processes: Create and maintain clear documentation for processes. Asana can help in task and process management.
Root Cause Analysis: Regularly perform root cause analysis to identify and solve underlying issues. MindTools offers techniques and tools for effective analysis.
Use Technology: Leverage technology for data analysis and process automation. Tableau is useful for data visualization, while UiPath can help automate repetitive tasks.
Visual Management: Implement visual management tools for better communication and monitoring. Kanban Tool provides an effective way to visualize work and workflow.
Regular Reviews: Schedule regular review meetings to assess progress and adjust strategies. Calendar tools like Google Calendar can help organize these reviews efficiently.
By focusing on these strategies, a Manufacturing Process Engineer can significantly enhance the effectiveness of Kaizen in their operations.
How to Display Kaizen Skills on Your Resume
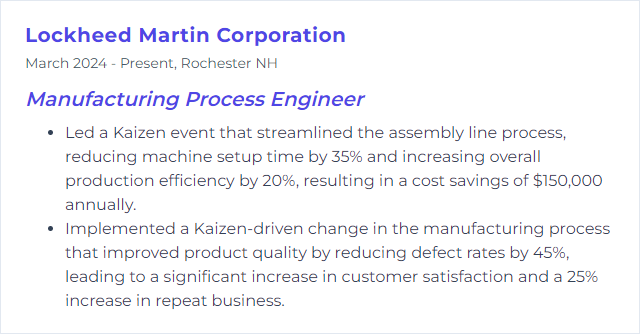
9. S Methodology
S Methodology is a systematic approach used in manufacturing to streamline processes, reduce waste, and improve product quality. It emphasizes standardization, simplification, and speed to enhance efficiency and productivity for Manufacturing Process Engineers.
Why It's Important
The S Methodology is important for a Manufacturing Process Engineer because it offers a systematic approach for process improvement, ensuring efficiency, quality control, and cost reduction in manufacturing operations.
How to Improve S Methodology Skills
Improving the S Methodology, particularly for a Manufacturing Process Engineer, involves streamlining systems, enhancing sustainability, and ensuring scalability. Here’s a very short, concise guide:
Streamline Systems: Focus on lean manufacturing principles to reduce waste and improve efficiency. Implement 5S (Sort, Set in order, Shine, Standardize, Sustain) to organize the workplace, making it more efficient and improving productivity.
Enhance Sustainability: Adopt sustainable manufacturing practices, such as reducing energy consumption and minimizing waste, to improve environmental performance and reduce costs.
Ensure Scalability: Use Six Sigma methodologies to improve process quality and efficiency, making it easier to scale operations up or down as needed.
By focusing on these three areas, Manufacturing Process Engineers can improve the S Methodology, leading to more efficient, sustainable, and adaptable manufacturing processes.
How to Display S Methodology Skills on Your Resume
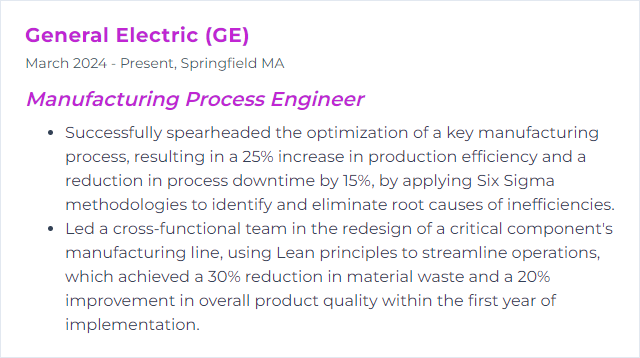
10. ISO Standards
ISO standards are internationally agreed-upon guidelines and specifications designed to ensure the quality, safety, and efficiency of products, services, and systems. For a Manufacturing Process Engineer, these standards provide a framework for establishing consistent processes, improving product quality, enhancing operational efficiency, and meeting regulatory requirements.
Why It's Important
ISO Standards ensure consistency, quality, safety, and efficiency in manufacturing processes, facilitating global trade, compliance, and customer satisfaction.
How to Improve ISO Standards Skills
Improving ISO standards within a manufacturing context, particularly from the perspective of a Manufacturing Process Engineer, involves a systematic approach focused on continuous improvement, compliance, and efficiency. Here are concise steps with inline linking for further exploration:
- Gap Analysis: Conduct a comprehensive ISO Gap Analysis to identify discrepancies between current processes and ISO requirements.
- Employee Training: Implement ongoing ISO Training Programs to ensure staff are up-to-date on standards and best practices.
- Process Optimization: Utilize Lean Manufacturing Principles to streamline operations, reduce waste, and enhance quality.
- Documentation Control: Establish a robust Document Management System for maintaining and updating ISO-related documents and records accurately.
- Internal Audits: Perform regular Internal ISO Audits to assess compliance, identify areas for improvement, and prepare for external audits.
- Corrective Actions: Develop a systematic approach for Corrective and Preventative Actions (CAPA) to address non-conformities and prevent their recurrence.
- Management Review: Engage top management in regular ISO Management Review Meetings to ensure continued alignment with business objectives and ISO standards.
- Customer Feedback: Incorporate Customer Feedback into the quality management process for continual improvement.
These steps encourage adherence to ISO standards, focusing on quality, efficiency, and continuous improvement within manufacturing processes.
How to Display ISO Standards Skills on Your Resume
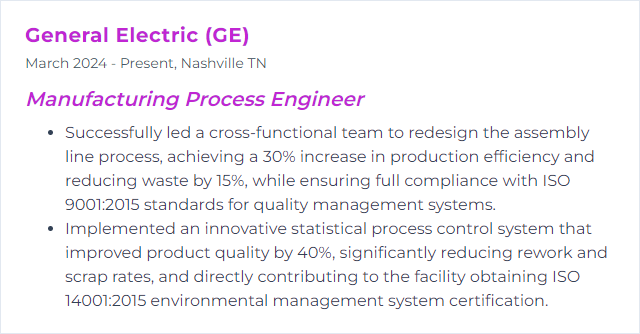
11. FMEA (Failure Modes and Effects Analysis)
FMEA (Failure Modes and Effects Analysis) is a systematic method used by Manufacturing Process Engineers to identify, evaluate, and prioritize potential failure modes in a manufacturing process, assess their impact on product quality and reliability, and implement corrective actions to mitigate risks.
Why It's Important
FMEA is crucial for a Manufacturing Process Engineer because it proactively identifies potential failures in manufacturing processes, assesses their impact on product quality and safety, and prioritizes corrective actions, thereby enhancing reliability, efficiency, and compliance while reducing costs and downtime.
How to Improve FMEA (Failure Modes and Effects Analysis) Skills
Improving FMEA in the context of Manufacturing Process Engineering can be achieved with the following concise strategies:
Training and Team Composition: Ensure all team members have adequate training in FMEA methodology. Diverse teams that include members from different departments can provide comprehensive insights. ASQ's FMEA Training offers a good starting point.
Up-to-Date Information: Utilize the most current standards and guidelines for FMEA, such as those provided by the AIAG & VDA FMEA Handbook.
Software Tools: Leverage FMEA software tools to streamline the process, ensure consistency, and facilitate easier updates. Siemens FMEA Solutions is an example.
Risk Priority Number (RPN) Refinement: Prioritize actions based on the RPN but also consider the severity of potential effects. Sometimes, actions must be taken for high-severity failures even if their RPN is lower. Quality-One offers guidance on this.
Integration with Other Quality Processes: Connect FMEA findings with other process improvement tools and quality systems within the organization for a holistic approach. Integrating FMEA with Six Sigma can be particularly effective.
Continuous Review and Update: FMEA is not a one-time activity. Regularly review and update the analysis to reflect changes in the manufacturing process, new types of failures, and lessons learned.
Feedback Loop: Establish a feedback loop from the manufacturing floor back to the FMEA team to continuously update the FMEA based on actual operational experiences. Here's a case study on the importance of feedback in FMEA.
By adhering to these strategies, a Manufacturing Process Engineer can enhance the effectiveness of FMEA in identifying and mitigating risks in manufacturing processes.
How to Display FMEA (Failure Modes and Effects Analysis) Skills on Your Resume
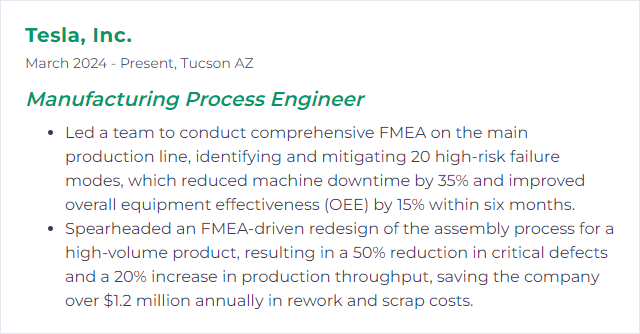
12. PLC Programming
PLC programming involves creating and inputting instructions into a Programmable Logic Controller (PLC) to automate and control machinery and processes in manufacturing environments, enhancing efficiency and precision.
Why It's Important
PLC programming is crucial for a Manufacturing Process Engineer because it enables precise control, automation, and optimization of manufacturing processes, leading to increased efficiency, safety, and flexibility in production operations.
How to Improve PLC Programming Skills
Improving your PLC programming skills, especially within the context of manufacturing processes, involves understanding both the fundamentals of PLCs and the specific applications relevant to your industry. Here are concise tips and resources for enhancing your proficiency:
Master the Basics: Solidify your understanding of PLC basics, including ladder logic, structured text, and function block diagrams. PLC Academy offers a comprehensive starting point.
Practice Real-World Problems: Apply your knowledge to solve actual manufacturing process issues. RealPars provides practical tutorials and case studies.
Understand Your Hardware: Familiarize yourself with the specific PLC hardware used in your facility. Manufacturers like Rockwell Automation and Siemens offer detailed guides and documentation.
Learn from Others: Join forums and communities, such as PLCTalk, to share experiences and solutions with other professionals.
Continuous Learning: Keep up with new technologies and programming methods through online courses on platforms like Udemy or Coursera.
Implement Best Practices: Focus on writing clean, understandable, and maintainable code. The ISA-88 and ISA-95 standards provide guidelines for batch process control and integration of enterprise and control systems, respectively.
Use Simulation Tools: Before applying changes to the live system, use simulation tools to test your programs. Software like Siemens PLCSim allows for safe testing of logic and process flow.
By following these steps and leveraging the provided resources, you can significantly improve your PLC programming skills and contribute more effectively to your manufacturing process.
How to Display PLC Programming Skills on Your Resume
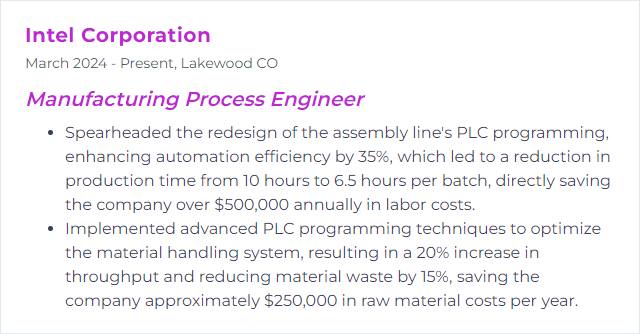