Top 12 Manufacturing Engineer Skills to Put on Your Resume
In today's competitive job market, standing out as a manufacturing engineer requires a robust set of skills that showcases your ability to improve processes, design efficient systems, and contribute to the overall productivity of a manufacturing environment. Highlighting these top skills on your resume is crucial for capturing the attention of potential employers and demonstrating your capability to drive innovation and operational success in the dynamic field of manufacturing engineering.
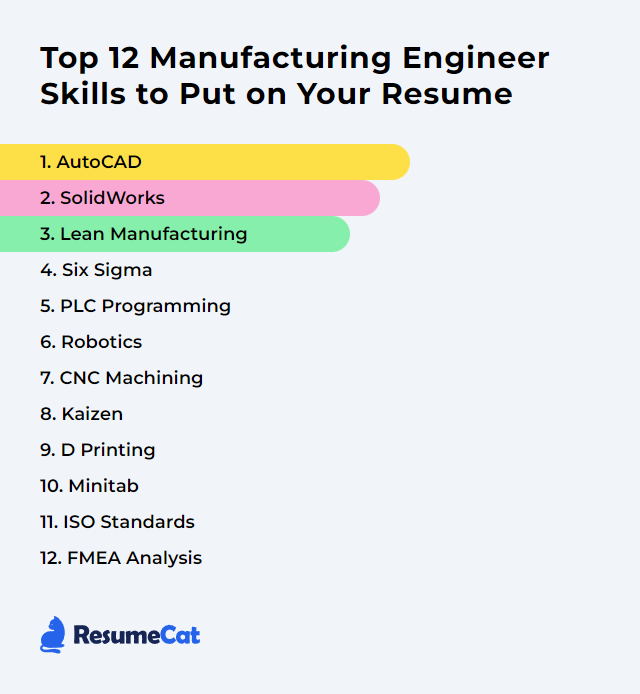
Manufacturing Engineer Skills
- AutoCAD
- SolidWorks
- Lean Manufacturing
- Six Sigma
- PLC Programming
- Robotics
- CNC Machining
- Kaizen
- D Printing
- Minitab
- ISO Standards
- FMEA Analysis
1. AutoCAD
AutoCAD is a computer-aided design (CAD) software used extensively by manufacturing engineers for creating precise 2D and 3D drawings and models of parts and assemblies, facilitating the design, visualization, and simulation of products before manufacturing.
Why It's Important
AutoCAD is crucial for Manufacturing Engineers because it enables precise design, modification, and optimization of products and manufacturing processes, ensuring efficiency, accuracy, and the ability to quickly adapt to changes.
How to Improve AutoCAD Skills
Improving your proficiency in AutoCAD, especially from a manufacturing engineering perspective, involves focusing on key areas such as mastering 3D modeling, automating repetitive tasks, and enhancing collaboration. Here's a concise guide:
Master 3D Modeling: Transition from 2D drafting to 3D modeling to better visualize and design parts. Autodesk offers tutorials to ease this transition.
Learn AutoLISP or Dynamo: Automate repetitive tasks to save time. Start with AutoLISP, AutoCAD's native programming language. Autodesk provides a basic guide to get you started.
Use Data Extraction: Streamline the creation of bill of materials (BOMs) or parts lists directly from your drawings. Learn more through Autodesk's Data Extraction guide.
Enhance Collaboration with AutoCAD Web and Mobile: Utilize AutoCAD's web and mobile applications for easy sharing and reviewing of drawings with teams. Explore AutoCAD Web and Mobile for seamless collaboration.
Stay Updated and Educate Continuously: The manufacturing industry evolves rapidly, and staying updated with the latest AutoCAD features is crucial. Autodesk University offers free courses and talks by industry professionals.
Join Forums and Communities: Engage with the AutoCAD community for tips, tricks, and troubleshooting. Autodesk Community Forums are a good place to start: Autodesk Forums.
By focusing on these areas, you can significantly improve your AutoCAD skills, making your engineering processes more efficient and effective.
How to Display AutoCAD Skills on Your Resume

2. SolidWorks
SolidWorks is a computer-aided design (CAD) and computer-aided engineering (CAE) software program used by manufacturing engineers to create 3D models and technical drawings of parts and assemblies for manufacturing processes.
Why It's Important
SolidWorks is crucial for a Manufacturing Engineer as it provides powerful 3D CAD tools for design and analysis, enabling efficient product development, visualization, and simulation, which streamline manufacturing processes, reduce errors, and speed up time to market.
How to Improve SolidWorks Skills
Improving your SolidWorks skills, especially as a Manufacturing Engineer, involves continuous learning and practical application. Here are concise tips with relevant resources:
Master the Basics: Ensure a strong foundation by mastering basic functionalities and shortcuts. SolidWorks offers an Official Training page.
Learn Advanced Features: Dive into advanced features relevant to manufacturing, like Sheet Metal Design, Weldments, and Mold Design. SolidWorks' Tutorials section is a great resource.
Customize Your Workspace: Tailor your toolbars and menus for efficiency. Guidance can be found in the SolidWorks Knowledge Base.
Use Simulation Tools: Leverage SolidWorks Simulation to validate designs and reduce prototyping needs. Explore the Simulation Training courses.
Stay Updated: Keep up with new features and updates. The SolidWorks Blog offers news and tips.
Join the Community: Engage with the SolidWorks community through forums and user groups to exchange tips and tricks. The SolidWorks Community is a good place to start.
Practice Regularly: Like any skill, proficiency comes with practice. Undertake personal or work-related projects to apply new techniques.
Seek Feedback: Collaborate with colleagues and mentors to review your designs and suggest improvements.
By following these steps and continuously exploring new functionalities and best practices, you can significantly enhance your SolidWorks skills and efficiency in a manufacturing engineering context.
How to Display SolidWorks Skills on Your Resume
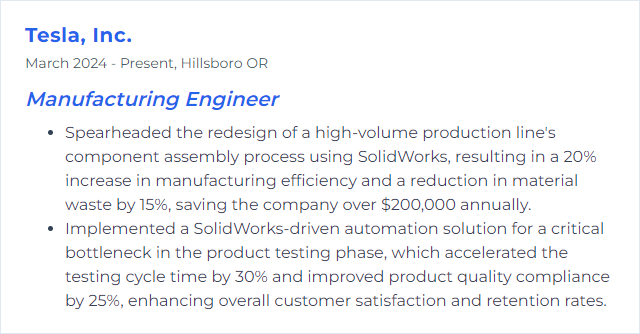
3. Lean Manufacturing
Lean Manufacturing is a systematic approach aimed at minimizing waste within manufacturing systems while simultaneously maximizing productivity. It focuses on improving overall efficiency, quality, and customer value through continuous improvement practices and the elimination of non-value-added activities.
Why It's Important
Lean Manufacturing is important because it enhances operational efficiency by minimizing waste, reducing costs, and improving product quality and delivery times, directly contributing to increased competitiveness and customer satisfaction in a manufacturing environment.
How to Improve Lean Manufacturing Skills
Improving Lean Manufacturing focuses on minimizing waste within manufacturing systems while simultaneously maximizing productivity. Here are concise strategies for a Manufacturing Engineer:
Value Stream Mapping: Identify and map out all the steps in your process, highlighting value-added and non-value-added activities. This overview helps in understanding and eliminating waste. Lean Enterprise Institute.
Continuous Improvement (Kaizen): Foster a culture of continuous improvement by encouraging small, incremental changes to processes. This involves everyone in the organization. ASQ Kaizen.
5S Workplace Organization: Implement the 5S method (Sort, Set in order, Shine, Standardize, Sustain) to organize and manage the workspace efficiently, leading to a more productive environment. EPA Lean 5S.
Jidoka (Autonomation): Implement technology that automatically stops the manufacturing process when defects are detected. This ensures that only quality products move to the next stage. Toyota Jidoka.
Just-In-Time (JIT) Production: Align production schedules closely with demand to reduce inventory costs and increase efficiency. This requires a well-organized supply chain. Lean Production JIT.
Root Cause Analysis: When problems occur, use tools like the 5 Whys or Fishbone Diagram to identify and address the root cause, preventing recurrence. ASQ Root Cause Analysis.
Standard Work: Develop and implement standard operating procedures for all tasks to ensure consistency and efficiency. Regularly review and update these standards. Lean Enterprise Institute - Standard Work.
Cross-Training: Cross-train employees to perform multiple tasks, enhancing flexibility and capacity to respond to changing demands. SHRM Cross-Training.
Focusing on these principles and continuously seeking ways to reduce waste and improve efficiency is key to advancing Lean Manufacturing in any environment.
How to Display Lean Manufacturing Skills on Your Resume
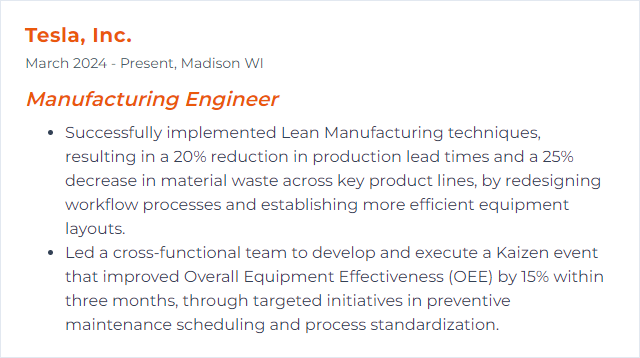
4. Six Sigma
Six Sigma is a data-driven methodology aimed at reducing defects and improving processes to near perfection, focusing on quality control and efficiency in manufacturing operations.
Why It's Important
Six Sigma is important for a Manufacturing Engineer because it provides a systematic approach to identifying and eliminating defects in manufacturing processes, leading to improved quality, efficiency, and customer satisfaction.
How to Improve Six Sigma Skills
Improving Six Sigma as a Manufacturing Engineer involves continuously enhancing process efficiency and quality. Here are concise steps:
Understand the Basics: Ensure a solid understanding of Six Sigma principles and methodologies. ASQ’s Six Sigma resources are excellent for foundational knowledge.
Lean Integration: Incorporate Lean Manufacturing techniques to reduce waste and streamline processes. Lean Enterprise Institute provides insights on lean principles.
Advanced Training: Pursue higher Six Sigma certifications (Green Belt, Black Belt, Master Black Belt). IASSC offers internationally recognized certifications.
Use Software Tools: Utilize Six Sigma software tools for data analysis and process improvement. Minitab is widely used for statistical analysis in Six Sigma projects.
Practical Application: Apply Six Sigma methodologies to real-world manufacturing problems. Document case studies and share solutions within the industry community.
Continuous Learning: Stay updated with the latest trends in Six Sigma and manufacturing technologies. SME offers resources and events for professional development.
Networking: Join Six Sigma and professional manufacturing networks for knowledge exchange and collaboration. LinkedIn groups and ASQ community are great places to start.
By focusing on these areas, Manufacturing Engineers can enhance their Six Sigma expertise and drive significant improvements in manufacturing processes.
How to Display Six Sigma Skills on Your Resume
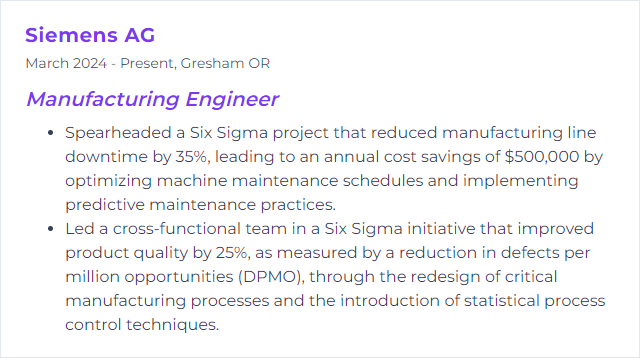
5. PLC Programming
PLC programming involves creating and implementing software algorithms on Programmable Logic Controllers (PLCs) to automate industrial and manufacturing processes, controlling machinery and production lines efficiently and reliably.
Why It's Important
PLC programming is crucial for a Manufacturing Engineer as it enables the automation of industrial machinery and processes, ensuring precise control, efficiency, and flexibility in manufacturing operations.
How to Improve PLC Programming Skills
Improving PLC programming involves enhancing both your technical skills and understanding of best practices in industrial automation. Here's a concise guide for a Manufacturing Engineer:
Understand the Basics: Ensure a strong foundation in electrical principles, logic circuits, and programming concepts. Learn PLC Basics.
Master the Software: Each PLC brand has its software. Dive deep into the one you use, mastering its features and shortcuts. Rockwell Automation and Siemens TIA Portal are common examples.
Structured Programming: Adopt structured programming practices like using functions, function blocks, and structured text for easier troubleshooting and maintenance. PLC Academy Structured Programming.
Learn from Examples: Analyze and learn from example programs and templates. This can accelerate your learning curve. PLC Programming Examples.
Stay Updated: Automation technology evolves rapidly. Stay informed about the latest trends and technologies in PLC programming. Automation World is a great resource.
Hands-on Practice: Practical experience is crucial. Use simulation software or a small PLC setup at home to practice. PLCSimulator.net offers a free simulator.
Networking and Community: Join forums and groups related to PLC programming. Sharing experiences and solutions with peers can provide insights and solutions to common challenges. PLC Talk is a valuable forum.
Training and Courses: Consider professional training or online courses to improve specific skills or learn about advanced topics. Udemy PLC Programming Courses offer a variety of options.
By focusing on these areas, you can significantly improve your PLC programming skills, making you a more effective Manufacturing Engineer in the process.
How to Display PLC Programming Skills on Your Resume
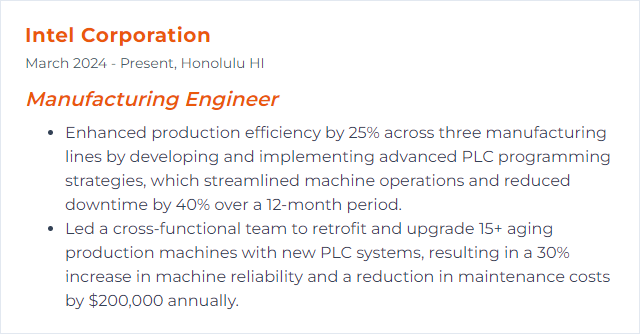
6. Robotics
Robotics, in the context of manufacturing engineering, refers to the design, construction, operation, and application of robots to automate and optimize production processes, enhancing efficiency, precision, and safety.
Why It's Important
Robotics is crucial for a Manufacturing Engineer as it enhances efficiency, precision, and safety in production processes, significantly reducing costs and improving product quality while minimizing human error and workplace injuries.
How to Improve Robotics Skills
Improving robotics in a manufacturing setting involves enhancing efficiency, reliability, and adaptability of robotic systems. Here’s a concise guide:
Integrate Advanced Sensors: Use advanced sensors for better precision and adaptability. Sensors Magazine has insights on the latest sensor technologies.
Implement Machine Learning: Incorporate machine learning for predictive maintenance and adaptive control. MIT News discusses recent advancements.
Upgrade to Collaborative Robots: Utilize collaborative robots (cobots) that work safely alongside humans. Robotics Business Review provides updates on cobot technology.
Enhance Connectivity: Leverage IoT for real-time monitoring and control. IoT For All offers resources on IoT integration.
Optimize Energy Efficiency: Adopt energy-efficient designs and practices. The IEEE Xplore database has research articles on energy-efficient robotic systems.
Focus on Modularity: Design systems with modular components for easy upgrades and repairs. RoboDK blogs about the benefits of modular robots.
Invest in Training: Continuously train staff on the latest robotic technologies. SME provides training resources related to advanced manufacturing technologies.
Improving robotics is an ongoing process that requires staying updated on technological advancements and best practices.
How to Display Robotics Skills on Your Resume
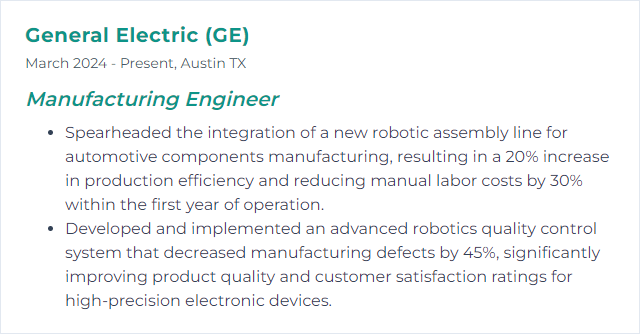
7. CNC Machining
CNC machining is a manufacturing process where pre-programmed computer software dictates the movement of factory tools and machinery, allowing for high-precision cutting, milling, drilling, and turning of materials.
Why It's Important
CNC machining is crucial for a Manufacturing Engineer because it provides precise, efficient, and repeatable production of parts with complex geometries, enhancing product quality while reducing waste and production time.
How to Improve CNC Machining Skills
Improving CNC machining involves optimizing the process for efficiency, accuracy, and cost-effectiveness. Here are concise strategies for a Manufacturing Engineer:
Tool Selection and Management: Use the right tools for each job and maintain them properly. Implement a tool management system to track tool life and performance.
Material Preparation: Ensure materials are prepared correctly for machining, including proper selection, pre-treatment, and securing on the machine bed to minimize errors and waste.
Programming Efficiency: Utilize advanced CAM software for efficient programming. Optimize tool paths to reduce machining time and improve surface finish.
Process Optimization: Apply Lean Manufacturing principles to CNC machining processes to reduce waste and improve productivity. Continuously analyze and refine processes.
Machine Maintenance: Implement a preventive maintenance schedule for machines to reduce downtime and extend equipment life.
Quality Control: Use precision measuring tools and quality control software to monitor product quality in real-time, allowing for immediate adjustments.
Training and Skills Development: Invest in ongoing training for operators and programmers to keep skills updated with the latest CNC machining technologies and techniques.
Experiment with Cutting-edge Technologies: Explore new advancements such as 5-axis machining and High-Speed Machining (HSM) to enhance capabilities and efficiency.
Improving CNC machining is an ongoing process that involves a combination of technology, skills, and process optimization.
How to Display CNC Machining Skills on Your Resume
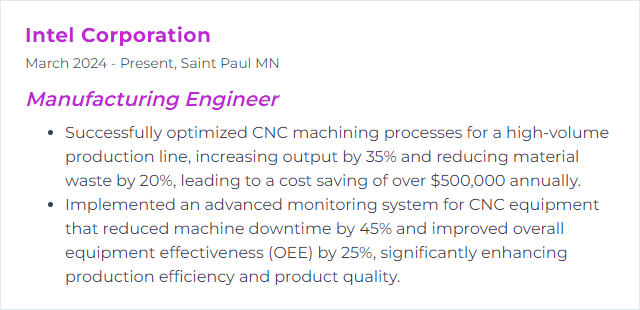
8. Kaizen
Kaizen is a Japanese philosophy emphasizing continuous, incremental improvement in manufacturing processes, focusing on efficiency, quality, and eliminating waste.
Why It's Important
Kaizen, a philosophy emphasizing continuous improvement, is crucial for Manufacturing Engineers as it fosters innovation, efficiency, and quality enhancement in manufacturing processes, leading to reduced waste, cost savings, and increased competitiveness.
How to Improve Kaizen Skills
To improve Kaizen for a Manufacturing Engineer, follow these concise steps:
Educate and Train: Continuously educate and train your team on Kaizen principles and tools. Kaizen Institute offers resources and training programs.
Standardize Processes: Document and standardize current processes to establish a baseline for improvements. The American Society for Quality (ASQ) provides guidelines on standardization.
Engage Employees: Foster a culture of continuous improvement by actively engaging employees in identifying inefficiencies and suggesting improvements. Lean Production has tips on employee engagement.
Implement 5S: Apply the 5S method (Sort, Set in order, Shine, Standardize, Sustain) to organize and maintain a productive work environment. Graphic Products explains the 5S methodology.
Use Visual Management: Implement visual management tools to make processes, standards, and improvements visible to all employees. The Lean Enterprise Institute discusses various lean tools, including visual management.
Measure and Analyze: Collect data to measure the impact of Kaizen activities and use it to guide further improvements. iSixSigma offers a guide on measuring Kaizen impact.
Iterate and Innovate: Continuously iterate on improvements and encourage innovative solutions to challenges. MIT Sloan Management Review provides insights into iterative improvement.
By following these steps and leveraging the resources provided, a Manufacturing Engineer can effectively enhance Kaizen practices within their organization.
How to Display Kaizen Skills on Your Resume
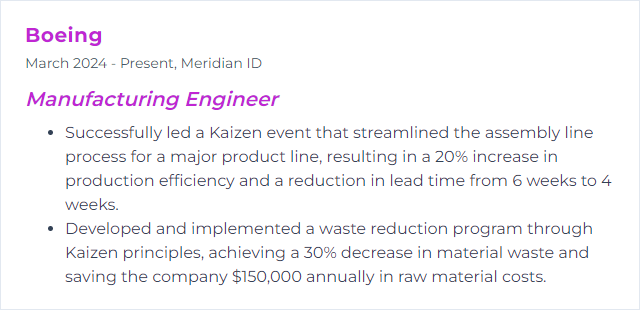
9. D Printing
3D printing, in a manufacturing engineering context, is an additive manufacturing process that creates physical objects from digital models by successively layering material until the desired shape is achieved. This technology allows for rapid prototyping, complex geometries, and customized production with reduced material waste and tooling costs.
Why It's Important
3D printing is important for a Manufacturing Engineer because it enables rapid prototyping, reduces material waste, allows for the production of complex and customized designs with high precision, and streamlines the manufacturing process by reducing the number of steps and tools required.
How to Improve D Printing Skills
Improving 3D printing, particularly for a manufacturing engineer, involves optimizing the process for efficiency, accuracy, and material properties. Here's a concise guide:
Material Selection: Choose the appropriate material for the desired properties and application. Material Guide
Printer Calibration: Regularly calibrate your printer for accurate dimensions and better surface finish. Calibration Tips
Layer Height and Orientation: Adjust layer height and part orientation for the optimal balance between print speed and detail. Optimization Guide
Post-Processing: Implement post-processing techniques like sanding, painting, or chemical smoothing for improved aesthetics and functionality. Post-Processing Techniques
Software Tools: Use advanced slicing and simulation software to predict and correct potential issues before printing. Software Selection
Hardware Upgrades: Upgrade printer components, such as the nozzle or extruder, for better performance and reliability. Upgrade Guide
Quality Control: Implement a quality control system to monitor and maintain the consistency of the prints. Quality Control Basics
Training and Education: Continuously learn about new materials, technologies, and techniques in 3D printing. Educational Resources
By adopting these strategies, manufacturing engineers can significantly improve the efficiency, quality, and applicability of 3D printed parts in manufacturing contexts.
How to Display D Printing Skills on Your Resume
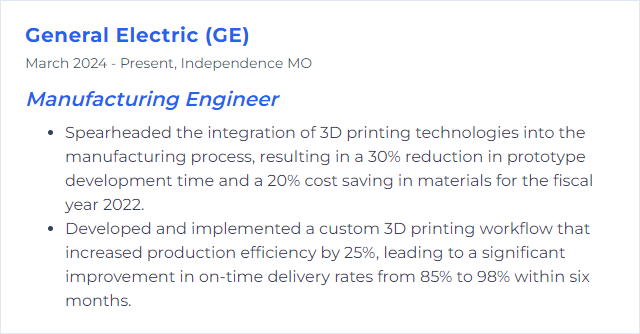
10. Minitab
Minitab is a statistical software tool designed for data analysis and quality improvement, widely used by manufacturing engineers for process optimization, Six Sigma initiatives, and quality control.
Why It's Important
Minitab is important for a Manufacturing Engineer because it provides powerful statistical analysis tools to optimize processes, improve quality control, and reduce defects in manufacturing operations, ultimately enhancing productivity and efficiency.
How to Improve Minitab Skills
Improving your proficiency with Minitab as a Manufacturing Engineer involves enhancing your statistical analysis and data-driven decision-making skills. Here are concise steps with resources to help you get started:
Master the Basics: Start with understanding the core functionalities of Minitab, including data entry, manipulation, and basic statistical analysis. The Minitab Quick Start Guide is a solid foundation.
Learn Through Courses: Enroll in specialized courses. Minitab's Training offers practical, hands-on courses tailored for manufacturing professionals.
Practice with Real Data: Apply what you've learned using your manufacturing data or datasets provided in online forums. Practice helps in understanding the nuances of analysis.
Join Forums and Communities: Engage with Minitab users in forums such as The Minitab Blog for tips, tricks, and advice specific to manufacturing.
Stay Updated: Minitab regularly updates its software. Keep abreast with the latest features and how they can be applied in manufacturing engineering through the Minitab Release Notes.
Utilize Add-Ons and Extensions: Explore Minitab's add-ons and extensions designed for specific analyses in manufacturing. This enhances the software's utility beyond its out-of-the-box capabilities.
By following these steps and utilizing these resources, you'll significantly improve your Minitab skills, enabling more effective and efficient data analysis in your manufacturing engineering role.
How to Display Minitab Skills on Your Resume
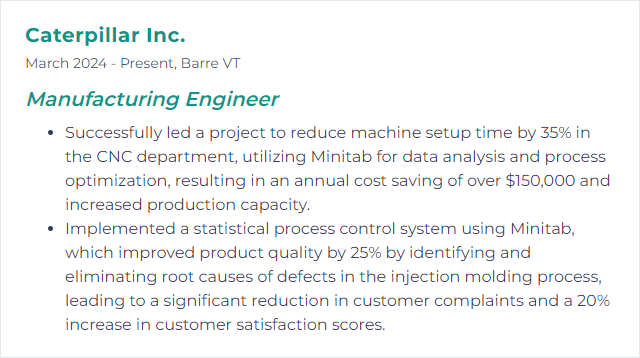
11. ISO Standards
ISO standards are internationally recognized guidelines and specifications designed to ensure the quality, safety, and efficiency of products, services, and systems. For a Manufacturing Engineer, these standards provide frameworks for consistent production processes, product quality, and continuous improvement, enhancing competitiveness and customer satisfaction.
Why It's Important
ISO Standards are crucial for a Manufacturing Engineer as they ensure quality, safety, and efficiency in manufacturing processes, leading to increased productivity, reduced costs, and enhanced customer satisfaction. They facilitate international trade by standardizing specifications for products, services, and systems.
How to Improve ISO Standards Skills
Improving ISO standards as a Manufacturing Engineer involves a proactive approach focused on process optimization, continual improvement, and stakeholder engagement. Here’s a very short and concise guide:
Understand the Requirements: Familiarize yourself with the specific ISO standards applicable to your manufacturing process (e.g., ISO 9001 for Quality Management). This understanding is crucial for identifying areas of improvement. ISO provides a comprehensive list of standards.
Conduct Gap Analysis: Assess current processes against ISO requirements to identify gaps. This analysis helps in prioritizing areas needing improvement.
Engage Stakeholders: Involve team members, suppliers, and customers in the process. Their feedback is invaluable for identifying practical improvements and ensuring the changes meet their needs. ASQ offers resources on quality improvement that emphasize stakeholder engagement.
Implement Process Improvements: Based on the gap analysis, develop and implement a plan to address deficiencies. This may involve revising procedures, investing in new technology, or training staff.
Monitor and Measure: Establish Key Performance Indicators (KPIs) to monitor the effectiveness of implemented changes. Continuous monitoring helps in identifying further improvement opportunities.
Regularly Review and Update Documentation: Ensure that all process modifications are reflected in your documentation. Regular reviews keep your ISO compliance up-to-date.
Prepare for Audits: Regular internal and external audits are essential for maintaining ISO certification. Use audit findings to drive continuous improvement.
Leverage Continuous Improvement Tools: Adopt tools like Six Sigma, Kaizen, or 5S to foster a culture of continuous improvement. Lean Enterprise Institute provides resources on lean principles that can complement ISO efforts.
Engage in Training and Education: Continual learning about ISO standards and best practices in manufacturing engineering is crucial. Purdue Online offers certification programs that can enhance your expertise in quality engineering.
Network with Industry Peers: Join professional networks or forums to share best practices and learn from the experiences of others. Platforms like LinkedIn Groups are useful for connecting with industry peers.
By following these steps, Manufacturing Engineers can enhance their ISO standards compliance, contributing to improved product quality, customer satisfaction, and operational efficiency.
How to Display ISO Standards Skills on Your Resume
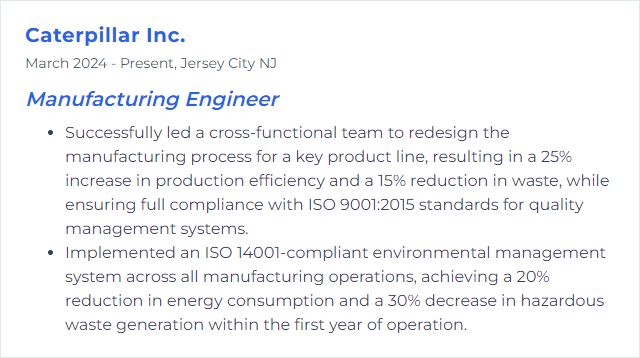
12. FMEA Analysis
FMEA (Failure Modes and Effects Analysis) is a systematic, proactive method for evaluating a process or product to identify where and how it might fail and to assess the relative impact of different failures, in order to identify the parts of the process that are most in need of change. For a Manufacturing Engineer, it helps in anticipating potential failures in manufacturing processes and designing those processes to minimize risks, improve quality, and ensure reliability.
Why It's Important
FMEA (Failure Modes and Effects Analysis) is crucial for a Manufacturing Engineer as it proactively identifies potential failures in manufacturing processes and product designs, allowing for the implementation of preventive measures to reduce risks, improve reliability, and ensure quality, ultimately leading to cost savings and customer satisfaction.
How to Improve FMEA Analysis Skills
Improving Failure Modes and Effects Analysis (FMEA) in a manufacturing context involves several key strategies aimed at enhancing its effectiveness and efficiency. Here are concise steps for a Manufacturing Engineer to improve FMEA Analysis:
Prioritize Training: Ensure all team members involved in the FMEA process are well-trained and understand the methodology thoroughly. ASQ's FMEA Training offers comprehensive resources.
Leverage Software Tools: Utilize specialized FMEA software tools to streamline the analysis process, ensuring consistency and ease of updating. Siemens FMEA Tool is an example that facilitates efficient FMEA execution.
Cross-Functional Teams: Involve a cross-functional team in the FMEA process to bring diverse perspectives and expertise, enhancing the identification and analysis of potential failures. MDPI discusses the importance of cross-functional teams in improving FMEA analysis.
Historical Data Review: Analyze historical data and past FMEAs to identify recurring issues and apply lessons learned. This can prevent the repetition of past mistakes.
Risk Priority Number (RPN) Reevaluation: Regularly review and update the RPN to reflect any changes in the manufacturing process or new information. This ensures that the most critical issues are always prioritized.
Action Follow-Up: Implement a robust system for tracking corrective actions and verify their effectiveness over time to ensure that identified issues are resolved.
Continuous Improvement: Adopt a mindset of continuous improvement for the FMEA process itself, soliciting feedback and making adjustments as necessary.
By following these steps, a Manufacturing Engineer can significantly improve the effectiveness of FMEA analysis in identifying and mitigating potential failures within manufacturing processes.
How to Display FMEA Analysis Skills on Your Resume
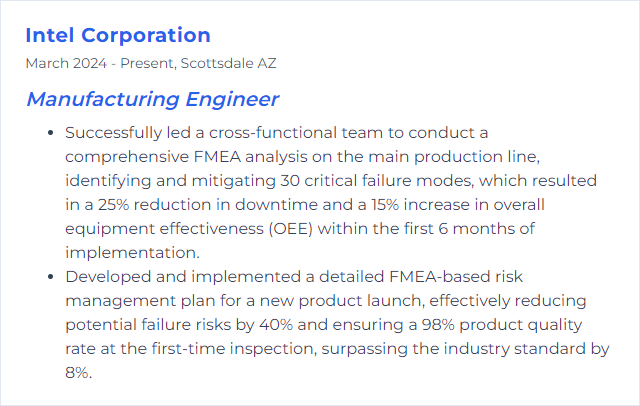