Top 12 Controls Engineer Skills to Put on Your Resume
In today’s competitive job market, standing out as a controls engineer requires more than just technical know-how; it demands a unique set of skills that showcase your ability to design, manage, and improve automated systems. Crafting your resume with these top skills not only highlights your expertise but also positions you as a prime candidate for cutting-edge engineering roles.
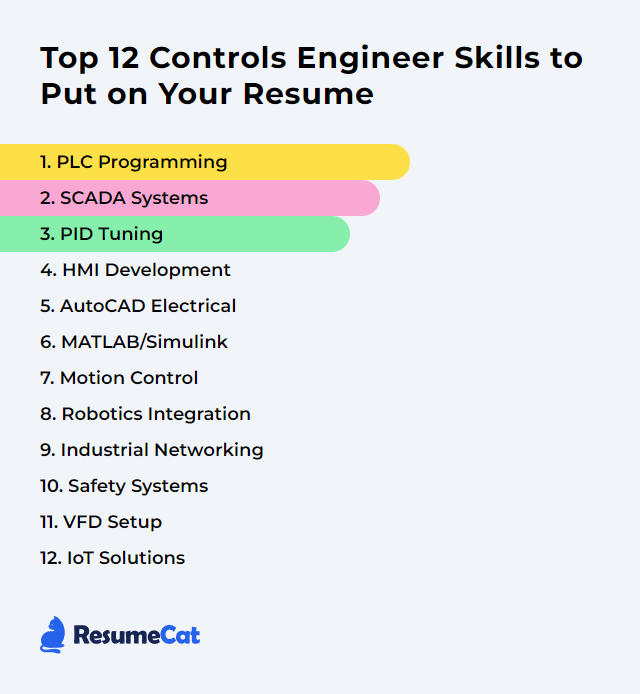
Controls Engineer Skills
- PLC Programming
- SCADA Systems
- PID Tuning
- HMI Development
- AutoCAD Electrical
- MATLAB/Simulink
- Motion Control
- Robotics Integration
- Industrial Networking
- Safety Systems
- VFD Setup
- IoT Solutions
1. PLC Programming
PLC programming involves creating and implementing software instructions to control machines and processes within industrial settings, enabling automation, monitoring, and control of manufacturing operations.
Why It's Important
PLC programming is crucial for a Controls Engineer as it enables the design, implementation, and modification of automated control systems for machinery and processes, ensuring efficiency, reliability, and safety in industrial environments.
How to Improve PLC Programming Skills
Improving PLC (Programmable Logic Controller) programming skills involves continuous learning and practice. Here are concise tips for a controls engineer:
Understand the Basics: Solidify your understanding of PLC fundamentals, including hardware components and software operation. PLC Academy offers comprehensive tutorials.
Learn Ladder Logic: Master Ladder Logic, the most popular PLC programming language. Ladder Logic World provides excellent resources.
Get Hands-on Experience: Practice programming with real PLCs or simulation software. PLCSimulator.net offers a free simulator.
Study Real-world Applications: Analyze case studies and real-world examples to understand practical applications. AutomationDirect has a vast library of application stories.
Stay Updated: Technologies and standards evolve, so keep learning about new PLC features and programming techniques. Control Engineering is a great resource for industry news and trends.
Join Forums and Groups: Engage with online communities for PLC programming. PLCTalk is an active forum where you can ask questions and share knowledge.
Take Advanced Courses: Enroll in courses that cover advanced topics or specific PLC brands. Udemy offers a variety of PLC programming courses.
By implementing these strategies and utilizing the linked resources, you can significantly improve your PLC programming skills.
How to Display PLC Programming Skills on Your Resume
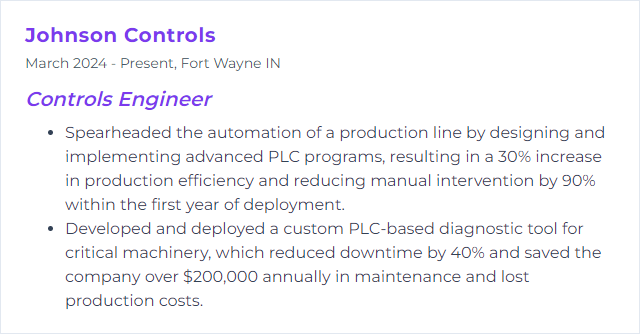
2. SCADA Systems
SCADA (Supervisory Control and Data Acquisition) systems are computer-based systems used by controls engineers to monitor and control industrial processes and infrastructure in real-time. They collect data from sensors and equipment, allowing for remote control of systems, optimization of operations, and early detection of issues.
Why It's Important
SCADA systems are crucial for Controls Engineers because they enable real-time monitoring and control of industrial processes and machinery, ensuring efficiency, safety, and reliability in operations.
How to Improve SCADA Systems Skills
Improving SCADA (Supervisory Control and Data Acquisition) systems involves enhancing their efficiency, security, and functionality. For a Controls Engineer, here are concise strategies:
Enhance Security: Implement robust cybersecurity measures to protect against threats. This includes regular updates, secure communication protocols, and multi-factor authentication. (Source: ISA)
Optimize Performance: Use high-performance hardware and optimize your network infrastructure to handle data efficiently and reduce latency. (Source: IEEE)
Upgrade Software: Keep your SCADA software up to date to benefit from the latest features and security patches. (Source: Inductive Automation)
Implement Redundancy: Ensure system reliability through redundancy in hardware and communications to minimize downtime. (Source: Schneider Electric)
Data Analytics: Utilize advanced data analytics tools to predict failures and optimize operations. (Source: Rockwell Automation)
User Training: Regularly train system users and operators on new features, security practices, and efficiency improvements. (Source: ISA Training)
Integration with IoT: Integrate with IoT devices for enhanced monitoring and control capabilities. (Source: Siemens)
These strategies aim to bolster the efficiency, reliability, and security of SCADA systems, ensuring they meet modern demands.
How to Display SCADA Systems Skills on Your Resume
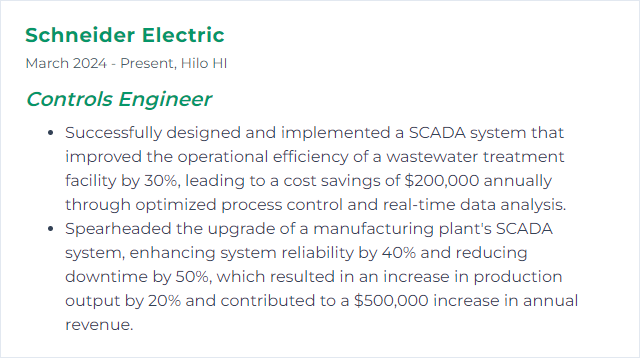
3. PID Tuning
PID tuning involves adjusting the proportional (P), integral (I), and derivative (D) control gains of a PID controller to achieve optimal system performance, ensuring stability, and minimizing error by fine-tuning the response to meet specific control objectives like quick settling time, minimal overshoot, and steady-state error.
Why It's Important
PID tuning is crucial for a Controls Engineer as it optimizes the control loop's performance, ensuring stability, reducing overshoot, and achieving the desired response time, thereby enhancing the efficiency and reliability of the system.
How to Improve PID Tuning Skills
Improving PID tuning involves systematic adjustments to the Proportional (P), Integral (I), and Derivative (D) gains to optimize the control system's performance. Here's a concise guide:
Start with a Baseline: Begin with known good settings or use a Ziegler-Nichols method to establish a starting point.
Adjust Proportional Gain (P): Increase P until the system starts to oscillate, then reduce until it operates smoothly. P reduces the rise time and settles time but may increase overshoot.
Tune Integral Gain (I): Adjust I to eliminate steady-state error. Be cautious; too high I can lead to instability and slow response. Integral Windup is a consideration.
Set Derivative Gain (D): Fine-tune D to reduce overshoot and improve stability. D predicts system behavior, helping mitigate P and I limitations. However, too much D can amplify noise.
Iterative Refinement: Use an iterative approach, adjusting each parameter slightly from the previous settings based on performance.
Implement Advanced Techniques: Consider advanced methods like PID Loop Tuning Software for more complex systems or when optimal performance is critical.
Continuous Monitoring and Adjustment: Systems can change over time. Regularly review and adjust PID settings to maintain optimal performance.
For further reading and detailed guides:
- PID Controller Tuning Techniques by National Instruments offers insights into PID theory and practical tuning advice.
- Control Guru provides practical control tips for process control engineers, including PID tuning strategies.
Remember, PID tuning is as much an art as it is a science. Experience, understanding of the specific system, and iterative adjustments are key to achieving optimal control performance.
How to Display PID Tuning Skills on Your Resume
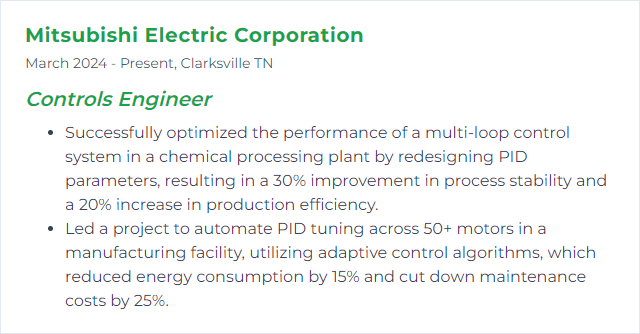
4. HMI Development
HMI Development involves creating user interfaces for industrial control systems, allowing operators to interact with machinery and processes through graphical representations, monitoring tools, and control elements, to manage and optimize operations efficiently.
Why It's Important
HMI (Human-Machine Interface) development is crucial for a Controls Engineer because it enables efficient, intuitive interaction between the operator and the machinery, ensuring safe, effective control and monitoring of complex systems, thereby optimizing operational performance and productivity.
How to Improve HMI Development Skills
Improving HMI (Human-Machine Interface) development involves focusing on user experience, system functionality, and iterative design. Here's a concise guide for Controls Engineers:
Understand User Needs: Engage with end-users to gather requirements and understand their workflow. Nielsen Norman Group offers insights on collecting user requirements.
Simplify Design: Aim for a clean, intuitive design that prioritizes important information. Use The Principles of Design by Interaction Design Foundation for guidelines.
Ensure Responsiveness: Design interfaces that are responsive across devices. Bootstrap is a popular framework for developing responsive projects.
Implement Standardization: Use industry standards for symbols, colors, and terminology. ISA-101 provides guidelines for HMI design and implementation.
Focus on Safety: Incorporate safety features and alarms. The EEMUA Publication 201 offers guidance on designing alarm systems.
Iterate and Test: Prototype rapidly and conduct usability testing. Usability.gov is a resource for usability testing practices.
Seek Feedback and Improve: Continuously gather user feedback and refine the HMI. SurveyMonkey can be used for quick feedback collection.
By focusing on these areas, Controls Engineers can significantly enhance the effectiveness and user-friendliness of HMI systems.
How to Display HMI Development Skills on Your Resume
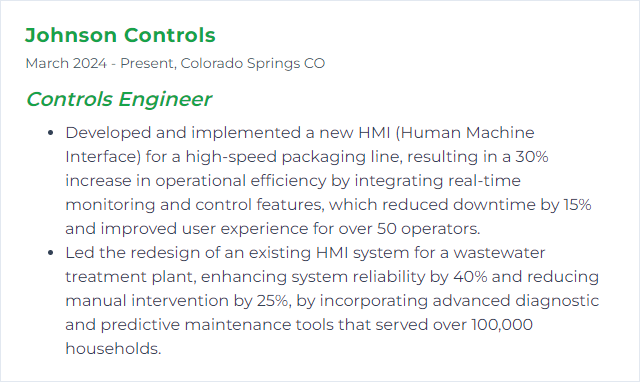
5. AutoCAD Electrical
AutoCAD Electrical is a specialized CAD software for designing and documenting electrical control systems, offering a comprehensive library of electrical symbols and tools specifically tailored for controls engineers to efficiently create accurate wiring diagrams, schematics, and panel layouts.
Why It's Important
AutoCAD Electrical is important for a Controls Engineer because it streamlines the creation of accurate and standardized electrical control systems designs, enhancing productivity, reducing errors, and ensuring compliance with industry standards.
How to Improve AutoCAD Electrical Skills
To improve your proficiency in AutoCAD Electrical as a Controls Engineer, focus on the following concise steps:
Understand the Basics: Ensure a solid understanding of electrical design principles and AutoCAD basics. Autodesk's official AutoCAD Electrical Toolset provides comprehensive resources.
Leverage Templates: Use and customize AutoCAD Electrical templates for consistency and efficiency in your projects. Autodesk offers guidance on creating and using templates.
Utilize Manufacturer Libraries: AutoCAD Electrical includes extensive libraries of electrical symbols and components. Familiarize yourself with these and add custom components as needed. Information on adding components to the catalog is available on Autodesk's component libraries guide.
Automate Tasks: Learn to use AutoCAD Electrical's automation features for tasks like numbering wires and generating reports to save time. Autodesk's Electrical Design page discusses these features.
Stay Updated: Continuously update your skills with the latest versions and features of AutoCAD Electrical. Autodesk provides resources and updates on its What's New section.
Join Forums and Communities: Engage with AutoCAD Electrical forums and communities for tips, tricks, and troubleshooting. The Autodesk Community is a valuable resource.
Hands-on Practice: Regularly apply your skills to real-world projects and simulations to reinforce learning and discover innovative solutions.
By following these steps and leveraging available resources, you can significantly improve your AutoCAD Electrical skills and efficiency in control engineering projects.
How to Display AutoCAD Electrical Skills on Your Resume
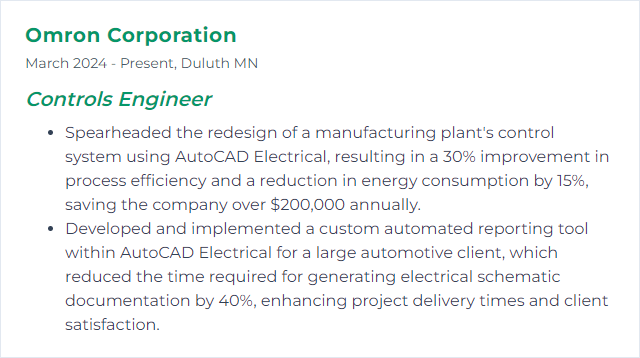
6. MATLAB/Simulink
MATLAB/Simulink is a computational software and graphical programming environment used by control engineers for modeling, simulating, and analyzing dynamic systems, designing control algorithms, and implementing these algorithms for testing and validation purposes.
Why It's Important
MATLAB/Simulink is crucial for Controls Engineers due to its comprehensive environment for designing, simulating, and analyzing dynamic systems and control algorithms. It streamlines the process of modeling complex systems, designing control strategies, and testing them through simulations, significantly reducing development time and improving system performance and reliability.
How to Improve MATLAB/Simulink Skills
Improving your MATLAB/Simulink skills, especially as a Controls Engineer, involves a combination of learning advanced techniques, practicing modeling and simulation, and staying updated with the latest features and tools. Here are concise recommendations:
Master Advanced Features: Dive into advanced MATLAB/Simulink functionalities like automated tuning of PID controllers, model predictive control, and custom block creation. The MathWorks documentation is an excellent place to start.
Practice with Real-world Projects: Apply your knowledge to real-world control systems projects. Sites like Coursera and edX offer practical courses with industry-relevant projects.
Utilize Model-Based Design (MBD): Embrace MBD for designing and testing complex control systems. Learn about it through the Model-Based Design MATLAB & Simulink page.
Stay Updated: MATLAB and Simulink are constantly updated. Keep abreast of the latest features and tools by frequently visiting the MathWorks Blog and subscribing to MathWorks newsletters.
Join the Community: Engage with the MATLAB and Simulink user community through MATLAB Central. Here, you can ask questions, share your knowledge, and learn from others' experiences.
Learn from Online Tutorials and Webinars: MathWorks and other educational platforms offer free tutorials and webinars. Check out the MathWorks Webinars for the latest instructional content.
Dive into Control Systems Toolbox™ and Simulink Control Design™: These toolboxes offer extensive functions and blocks for designing and analyzing control systems. Explore them through their respective Control Systems Toolbox™ and Simulink Control Design™ pages.
Use the MATLAB Answers and File Exchange: For specific problems or to find useful custom functions and scripts, utilize MATLAB Answers and the MATLAB File Exchange.
By following these recommendations and making the most of the resources provided, you can significantly enhance your MATLAB/Simulink skills and apply them effectively in control engineering projects.
How to Display MATLAB/Simulink Skills on Your Resume
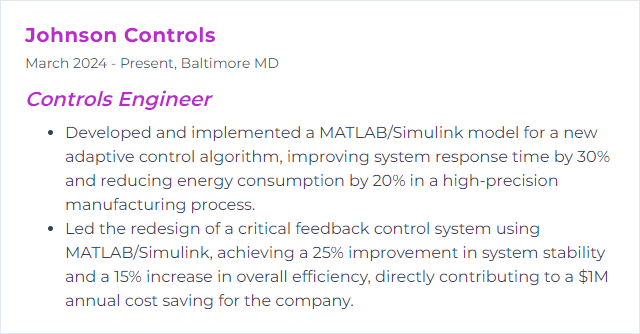
7. Motion Control
Motion control is a subfield of automation involving the use of control systems to manage the position, speed, and acceleration of mechanical components precisely, often used in robotics and CNC machinery.
Why It's Important
Motion control is crucial for a Controls Engineer because it enables precise and efficient management of the movement and positioning of machinery and devices, ensuring accuracy, speed, and reliability in automated systems.
How to Improve Motion Control Skills
Improving motion control requires optimizing system performance, enhancing precision, and ensuring smooth operations. Here are concise strategies:
System Analysis: Begin with a thorough analysis of your current motion control system. Identify any performance bottlenecks or inefficiencies. Tools like MATLAB or Simulink can be instrumental for modeling and simulation (MATLAB and Simulink).
Component Upgrade: Evaluate and upgrade key components such as motors, drives, and sensors. Modern, high-performance parts can significantly enhance system responsiveness and accuracy. Consider resources like AutomationDirect for components.
Feedback Loops: Implement or improve feedback loops. Use high-quality encoders to provide accurate position and speed feedback, enhancing control precision (Encoder Products Company).
Control Algorithms: Optimize or redesign control algorithms. Advanced algorithms like PID (Proportional, Integral, Derivative) control can be fine-tuned for better performance. Adaptive control and model predictive control are also worth exploring for complex systems (Control Global).
Software Tools: Utilize software tools for better tuning and analysis. Tools like Rockwell Automation’s Studio 5000 help in fine-tuning control systems for optimal performance (Rockwell Automation).
Training and Resources: Stay updated with the latest in motion control technologies and strategies through continuous learning. Websites like ISA (International Society of Automation) offer courses and certifications.
Networking: Engage with professional communities and forums such as Control.com to exchange knowledge and experiences with peers.
Improving motion control is an ongoing process of system evaluation, component upgrades, and optimization of control strategies to meet the evolving demands of precise and efficient motion systems.
How to Display Motion Control Skills on Your Resume
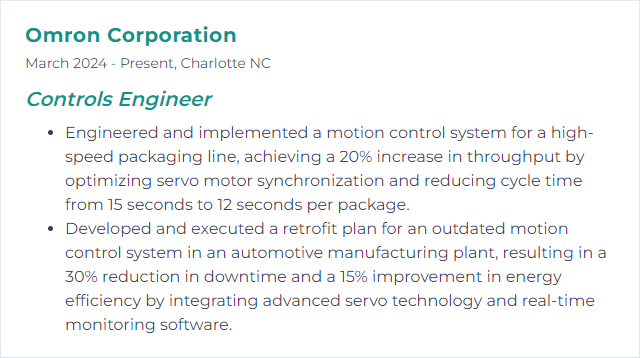
8. Robotics Integration
Robotics Integration, for a Controls Engineer, involves designing, programming, and implementing control systems to enable robots to perform specific tasks within an automated system, ensuring seamless operation and interaction with other machinery and software within the production or operational environment.
Why It's Important
Robotics integration is crucial for a Controls Engineer as it ensures seamless communication and coordination between automated systems, optimizing efficiency, enhancing precision, and enabling adaptability to complex manufacturing processes.
How to Improve Robotics Integration Skills
Improving Robotics Integration as a Controls Engineer involves a combination of staying updated with the latest technologies, understanding system design, and continuous learning. Here’s a concise guide:
Stay Updated: Follow leading robotics integration resources like IEEE Robotics and Automation Society for the latest research and trends in robotics.
Understand System Design: Grasp the fundamentals of system design and integration. The Robot Operating System (ROS) is a flexible framework for writing robot software.
Learn from Courses: Enroll in specialized courses to enhance your skills. Coursera and edX offer courses on robotics and controls engineering.
Hands-on Practice: Apply your knowledge through projects. Platforms like Arduino and Raspberry Pi are great for prototyping.
Networking: Join forums and communities such as Robotics Stack Exchange to share knowledge and solve challenges.
Software Proficiency: Improve proficiency in essential software tools such as MATLAB/Simulink for simulation and SolidWorks for CAD design.
Collaborative Robots (Cobots): Understand the integration of cobots into production environments. Websites like Universal Robots provide insights into collaborative robot applications.
Safety Standards: Familiarize yourself with safety standards and best practices in robotics integration. ISO Robotics has essential standards for robot safety.
By following these steps and continuously exploring new technologies and methodologies, you can enhance your capabilities in robotics integration effectively.
How to Display Robotics Integration Skills on Your Resume
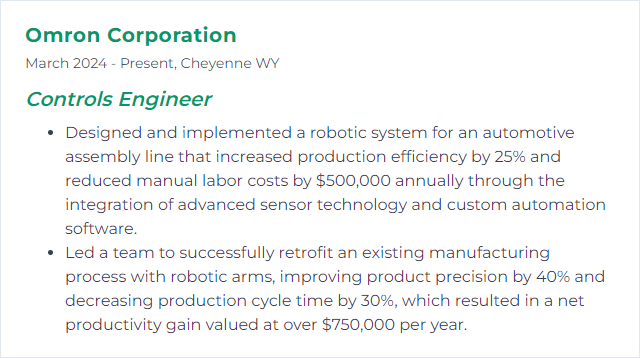
9. Industrial Networking
Industrial networking refers to the integration and communication between industrial systems and devices, such as PLCs, HMI, sensors, and actuators, using standardized protocols and networking technologies to facilitate real-time data exchange, control, and monitoring within industrial environments. For a Controls Engineer, it enables efficient system control, process automation, and operational efficiency.
Why It's Important
Industrial networking is crucial for a Controls Engineer because it enables seamless communication and integration between various control systems and machinery, ensuring efficient, real-time monitoring and management of industrial processes.
How to Improve Industrial Networking Skills
Improving industrial networking for a Controls Engineer involves enhancing network reliability, security, and efficiency. Here's a concise guide:
Assess and Plan: Evaluate current network infrastructure. Identify bottlenecks, security vulnerabilities, and areas for improvement. Cisco's Guide offers insights into assessing industrial networks.
Standardize Protocols: Use standard industrial protocols like EtherNet/IP, Profinet, or Modbus TCP to ensure compatibility and simplify troubleshooting. The ODVA has resources on EtherNet/IP.
Implement Network Segmentation: Divide the network into smaller, manageable segments to improve performance and security. Rockwell Automation offers solutions and guidelines on network segmentation.
Enhance Security: Apply industrial cybersecurity best practices, including regular updates, use of firewalls, and VPNs for remote access. ISA/IEC 62443 standards provide a framework for industrial cybersecurity.
Redundancy and Resilience: Implement redundant network paths and devices to ensure network reliability. Techniques such as Rapid Spanning Tree Protocol (RSTP) can be crucial. Belden's Guide explains redundancy strategies.
Real-time Monitoring and Maintenance: Use network monitoring tools to detect and address issues promptly. Siemens' Industrial Security services offer monitoring solutions.
Continuous Learning: Stay updated with the latest technologies and best practices in industrial networking. Platforms like ISA and IEEE provide valuable resources and training.
By focusing on these areas, Controls Engineers can significantly improve the performance, security, and reliability of industrial networks.
How to Display Industrial Networking Skills on Your Resume
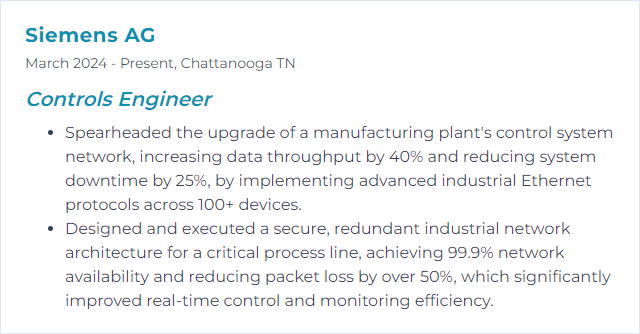
10. Safety Systems
Safety systems are integrated sets of engineered processes and controls designed to prevent accidents and protect people, equipment, and the environment from harm, particularly in industrial settings. They are critical for minimizing risks and ensuring safe operations, often involving fail-safe mechanisms, alarms, interlocks, and emergency shutdown procedures.
Why It's Important
Safety systems are crucial for a Controls Engineer because they ensure the protection of human life, prevent equipment damage, and ensure compliance with regulatory standards, enabling reliable and secure operation of machinery and processes.
How to Improve Safety Systems Skills
Improving safety systems as a Controls Engineer involves a multifaceted approach focused on design, implementation, and continuous improvement. Here's a concise guide:
Risk Assessment: Begin with a thorough risk assessment to identify potential hazards. Use standards such as ISO 12100 for guidance.
Design & Redundancy: Design safety systems with redundancy and fail-safe mechanisms. Incorporate principles from IEC 61508 for functional safety of electrical/electronic systems.
Safety PLCs: Use Safety PLCs for critical control functions. These offer better diagnostics and fault tolerance. Rockwell Automation provides examples.
Regular Testing & Maintenance: Implement a schedule for regular testing and maintenance of safety systems. Reference OSHA’s guidelines for maintaining workplace safety equipment.
Training: Ensure staff are trained on the operation and emergency procedures related to safety systems. ISA offers training programs.
Stay Updated: Keep abreast of the latest safety standards and technology advancements. Participate in forums like Control Engineering for the latest trends.
Feedback Loops: Establish feedback loops for continuous improvement. Incident investigations should inform safety system enhancements.
By systematically addressing these areas, Controls Engineers can significantly improve the effectiveness and reliability of safety systems.
How to Display Safety Systems Skills on Your Resume
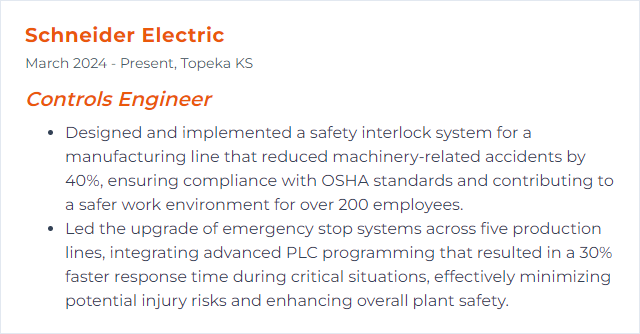
11. VFD Setup
A VFD (Variable Frequency Drive) setup in controls engineering involves configuring a device to control the speed, torque, and direction of an electric motor by varying the frequency and voltage supplied to the motor. This setup includes parameter adjustments, input/output programming, and integration with control systems for precise motor operation management.
Why It's Important
VFD setup is crucial for a Controls Engineer because it allows precise control of motor speed, leading to optimized process control, energy savings, and reduced mechanical stress on equipment.
How to Improve VFD Setup Skills
Improving a Variable Frequency Drive (VFD) setup involves optimizing performance, efficiency, and reliability. Here's a concise guide tailored for Controls Engineers:
Parameter Setup: Begin by ensuring that the VFD parameters are correctly set according to the motor and application requirements. This includes motor full load amperage, voltage, power factor, and control method (e.g., V/f, Sensorless Vector Control). ABB's Guide provides detailed setup instructions.
Control Wiring and Signals: Verify that control wiring (start/stop, direction) and feedback signals (current, voltage) are correctly connected and shielded to minimize electromagnetic interference (EMI). Proper grounding practices are crucial. Rockwell Automation offers comprehensive wiring guidelines.
PID Control Tuning: If using the VFD's built-in PID controller for process control (e.g., pressure, flow), ensure the PID parameters (Proportional, Integral, Derivative) are tuned for the specific process dynamics to avoid oscillation or slow response. Siemens' PID Tuning Guide is a helpful resource.
Harmonics Mitigation: Implement harmonic filtering solutions, such as line reactors or harmonic filters, to reduce the harmonic distortion caused by the VFD. This improves power quality and extends equipment life. Schneider Electric provides insights into harmonic mitigation techniques.
Thermal Management: Ensure adequate cooling for the VFD and associated electrical equipment, considering ambient temperature and enclosure ratings. Thermal management prevents overheating and extends component lifespan. Hoffman's Cooling Solutions outline effective cooling strategies.
Preventive Maintenance: Schedule regular inspections and maintenance to identify and rectify issues such as loose connections, worn components, and dust accumulation. Yaskawa's Preventive Maintenance checklist is a practical reference.
Firmware Updates: Keep the VFD firmware updated to the latest version to benefit from improvements and new features. Check the manufacturer's website for updates and installation instructions.
Network Security: If the VFD is part of a networked control system, ensure that appropriate cybersecurity measures are in place to protect against unauthorized access. ISA/IEC 62443 standards provide guidelines for industrial network security.
By carefully addressing these aspects, you can significantly improve the performance and reliability of your VFD setup.
How to Display VFD Setup Skills on Your Resume
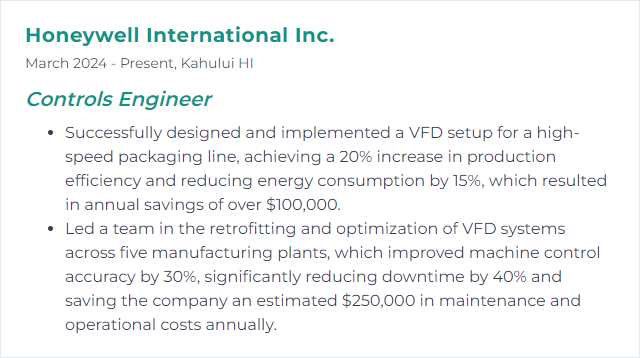
12. IoT Solutions
IoT Solutions for a Controls Engineer involve integrating sensors, actuators, and network connectivity into control systems to enable remote monitoring, automation, and data analysis, enhancing efficiency and predictive maintenance in industrial processes.
Why It's Important
For a Controls Engineer, IoT solutions are crucial because they enable remote monitoring and control of systems, enhance predictive maintenance through real-time data analytics, and improve system efficiency and reliability by enabling smart, interconnected devices. This leads to reduced downtime and operational costs while optimizing performance.
How to Improve IoT Solutions Skills
Improving IoT solutions, especially from a Controls Engineer's perspective, involves enhancing connectivity, security, data management, and device interoperability. Here's a concise guide:
Enhance Connectivity: Optimize network protocols and technologies for reliable data transmission. Consider using MQTT or CoAP for lightweight and efficient communication.
Strengthen Security: Implement robust security measures including encryption, secure boot, and regular firmware updates. The OWASP IoT Project provides best practices and guidelines.
Optimize Data Management: Leverage edge computing to preprocess data locally, reducing latency and bandwidth use. Explore EdgeX Foundry for open-source edge computing frameworks.
Ensure Device Interoperability: Adopt standard communication protocols and data models to ensure devices from different manufacturers can interact seamlessly. oneM2M is a global standards initiative for IoT interoperability.
By focusing on these areas, Controls Engineers can significantly improve the performance, reliability, and security of IoT solutions.
How to Display IoT Solutions Skills on Your Resume
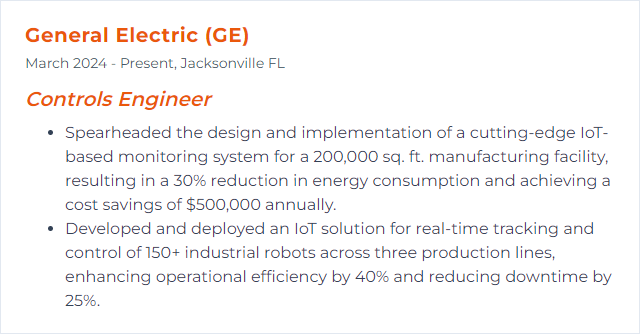