Top 12 Tool Crib Attendant Skills to Put on Your Resume
In the competitive landscape of maintenance and manufacturing industries, a well-crafted resume highlighting essential skills is crucial for tool crib attendants aiming to stand out. This article outlines the top 12 skills that candidates should showcase on their resumes to demonstrate their proficiency in managing tools, ensuring operational efficiency, and supporting the needs of their team.
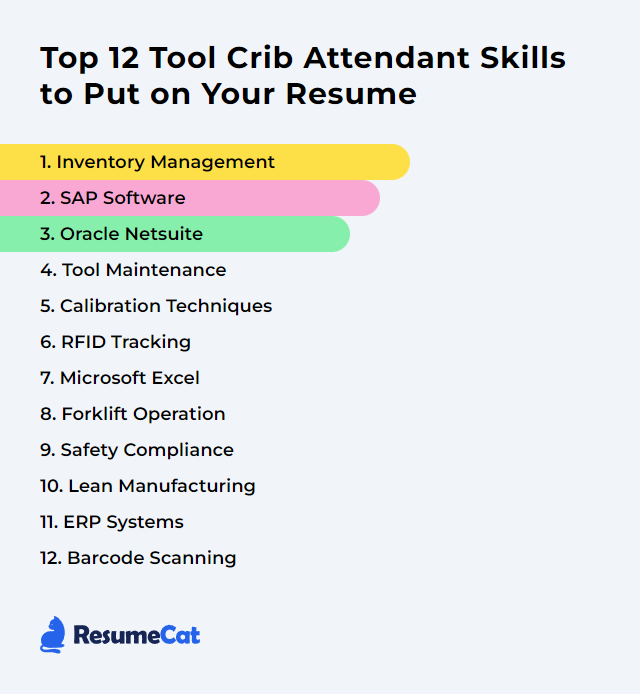
Tool Crib Attendant Skills
- Inventory Management
- SAP Software
- Oracle Netsuite
- Tool Maintenance
- Calibration Techniques
- RFID Tracking
- Microsoft Excel
- Forklift Operation
- Safety Compliance
- Lean Manufacturing
- ERP Systems
- Barcode Scanning
1. Inventory Management
Inventory management, in the context of a Tool Crib Attendant, involves overseeing and controlling the ordering, storage, and distribution of tools and equipment to ensure they are available as needed, while minimizing costs and maintaining optimal stock levels.
Why It's Important
Inventory management is crucial for a Tool Crib Attendant because it ensures the right tools are available when needed, minimizes downtime, controls costs by avoiding overstock or shortages, and maintains accurate records for tracking and accountability.
How to Improve Inventory Management Skills
Improving inventory management, especially for a Tool Crib Attendant, involves a few concise steps:
Implement Inventory Software: Use inventory management software to track tools in real-time, manage check-outs and returns, and monitor inventory levels. Sortly and ToolHound are popular options.
Regular Audits: Schedule regular checks to ensure the inventory records match the actual inventory on hand. This helps in identifying discrepancies early.
Organize the Crib: Keep the tool crib organized with clear labeling and categorization. This Shopify guide provides insights into efficient organization techniques.
Training: Train staff on proper tool handling, check-out procedures, and reporting damages or losses immediately. This reduces mishandling and loss.
Vendor Management: Establish good relationships with suppliers for better deals, reliable supply, and quick replacements. This guide from CIPS offers strategies for effective supplier relationship management.
Adopt Lean Inventory Techniques: Utilize lean inventory principles to minimize waste and ensure you only stock what is necessary. The Lean Enterprise Institute provides resources on adopting lean principles.
Use Data Analytics: Analyze inventory data to predict future tool requirements, understand usage patterns, and optimize stock levels. Tools like Microsoft Power BI can help in visualizing and analyzing inventory data.
Implement Security Measures: Use security measures like CCTV, tool tagging, and controlled access to reduce theft and unauthorized use. Guide to Tool Security offers practical tips.
By focusing on these areas, a Tool Crib Attendant can significantly improve inventory management, ensuring tools are available when needed, reducing losses, and maintaining an efficient workflow.
How to Display Inventory Management Skills on Your Resume
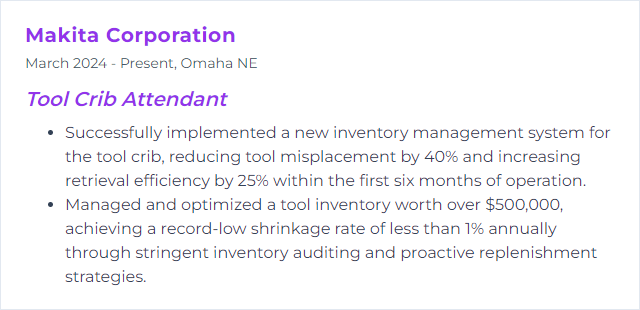
2. SAP Software
SAP software is an enterprise resource planning (ERP) system that helps organizations manage business operations, including inventory and supply chain management, crucial for a Tool Crib Attendant to efficiently track and manage tools and equipment.
Why It's Important
SAP software is important for a Tool Crib Attendant because it streamlines inventory management, tool tracking, and maintenance scheduling, ensuring efficient operation and cost savings.
How to Improve SAP Software Skills
Improving SAP software, especially for a Tool Crib Attendant, involves enhancing inventory management, tool tracking, and reporting capabilities. Here are concise recommendations:
Automate Inventory Management: Implement SAP Inventory Management features to automate reordering processes and manage stock levels efficiently, reducing manual input errors.
Integrate Tool Tracking System: Use SAP Asset Manager to integrate a tool tracking system, enabling real-time tracking of tool location, usage, and maintenance schedules.
Customize Reporting: Leverage SAP Crystal Reports to customize reporting for inventory, usage patterns, and procurement needs, facilitating data-driven decisions.
Enhance User Training: Provide tailored training sessions focused on the specific functionalities used by Tool Crib Attendants, ensuring maximum software utility. SAP offers various training options through their SAP Training and Certification program.
Implement Mobile Solutions: Utilize SAP's mobile solutions like SAP Fiori to enable mobile access to inventory and tool management functions, increasing efficiency and flexibility for attendants.
By focusing on these areas, SAP software can be more effectively tailored to meet the specific needs of Tool Crib Attendants, enhancing operational efficiency and tool management capabilities.
How to Display SAP Software Skills on Your Resume
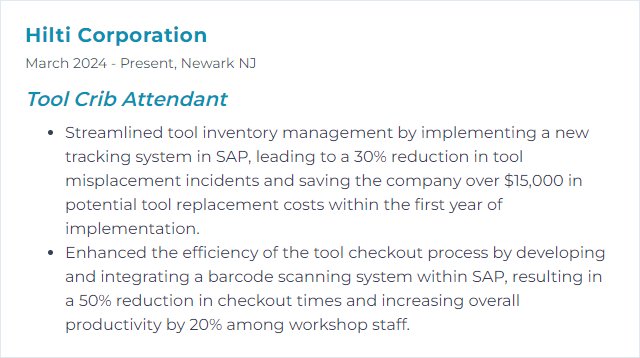
3. Oracle Netsuite
Oracle NetSuite is a cloud-based enterprise resource planning (ERP) software suite that integrates various business functions, including inventory management, which is relevant for a Tool Crib Attendant, as it can help in tracking tools, managing stock levels, and automating reordering processes.
Why It's Important
Oracle NetSuite is important for a Tool Crib Attendant as it automates and streamlines inventory management, enabling efficient tracking, management, and replenishment of tools and equipment, ensuring availability and reducing downtime.
How to Improve Oracle Netsuite Skills
Improving Oracle Netsuite for a Tool Crib Attendant involves leveraging its customization and integration capabilities to streamline inventory management, tracking, and ordering processes. Here are concise steps:
Customize Dashboards: Tailor Netsuite dashboards to display key inventory metrics, alerts for low stock, and maintenance schedules. Netsuite Dashboard Customization.
Implement Barcode Scanning: Integrate barcode scanning for check-in/check-out processes to ensure accurate tracking of tools. Use Netsuite's mobile app for real-time updates. Netsuite Mobile App.
Automate Reordering: Set up automatic reordering based on minimum stock levels to avoid tool shortages. Use Netsuite's inventory management features to automate this process. Netsuite Inventory Management.
Use Reporting Tools: Utilize Netsuite's reporting tools to analyze tool usage patterns, predict future needs, and optimize inventory levels. Netsuite Reporting and Analytics.
Integrate with External Tools: If specific tool management features are missing, integrate third-party tool management solutions with Netsuite via APIs. Netsuite Integration Solutions.
By customizing Netsuite to fit the unique needs of tool crib management, you can significantly enhance efficiency, reduce tool downtime, and maintain optimal inventory levels.
How to Display Oracle Netsuite Skills on Your Resume

4. Tool Maintenance
Tool maintenance, in the context of a Tool Crib Attendant, involves the systematic inspection, cleaning, repairing, and organizing of tools to ensure they are in good working condition and readily available for use.
Why It's Important
Tool maintenance is essential for ensuring the safety, reliability, and longevity of tools, leading to improved efficiency, reduced downtime, and cost savings in operations. It ensures tools are ready and in optimal condition for use, supporting a smooth workflow and high-quality work outcomes.
How to Improve Tool Maintenance Skills
Improving tool maintenance, especially for a Tool Crib Attendant, involves systematic organization, regular inspection, proper cleaning, and timely repair or replacement. Here’s a concise guide:
Organize Tools Efficiently: Use a digital inventory management system to track tool usage, location, and maintenance schedules. This ensures tools are easily accessible and returned to the right place. Tool Inventory Management Software can streamline this process.
Conduct Regular Inspections: Schedule and perform regular inspections to identify wear or damage early. This helps in maintaining tool functionality and safety. Creating an Effective Maintenance Plan offers guidance on planning these inspections.
Clean Tools After Use: Ensure tools are cleaned according to manufacturer guidelines after each use to prevent build-up that can lead to damage or inefficiency. Proper Cleaning Techniques provides tips on cleaning various tools.
Perform Timely Repairs: Initiate repairs or replacement as soon as issues are identified to avoid further damage or downtime. Maintenance, Repair, and Operations outlines the importance of timely maintenance.
Educate Users: Train all users on proper tool use, cleaning, and basic maintenance to minimize misuse and extend tool life. Tool Safety and Maintenance from OSHA offers guidelines that can be incorporated into training.
By implementing these strategies, a Tool Crib Attendant can significantly improve the maintenance and longevity of tools in their care.
How to Display Tool Maintenance Skills on Your Resume
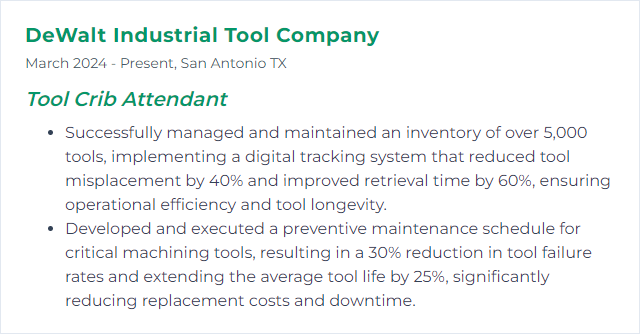
5. Calibration Techniques
Calibration techniques involve the process of verifying and adjusting the accuracy of measurement tools and equipment to ensure they conform to standard values. For a Tool Crib Attendant, this means routinely checking tools and devices against certified measurements to ensure they are delivering accurate readings and outputs, adjusting them as necessary to maintain precision and reliability in their performance.
Why It's Important
Calibration techniques are important for a Tool Crib Attendant because they ensure the accuracy and reliability of tools and equipment, maintaining quality control and safety in operations.
How to Improve Calibration Techniques Skills
Improving calibration techniques, especially for a Tool Crib Attendant, involves ensuring accuracy, consistency, and traceability of measurement tools. Here’s a concise guide:
Standardize Procedures: Develop and adhere to standardized calibration procedures for each tool type. NIST provides guidelines that can help in establishing these standards.
Use Certified Equipment: Utilize calibration equipment that has been certified by reputable organizations. This ensures the accuracy of calibration results. ISO standards are a good reference for certification requirements.
Regular Training: Ensure continuous training for personnel on the latest calibration techniques and standards. ASQ offers resources and training courses.
Maintain Calibration Records: Keep detailed records of all calibration activities, including dates, results, and corrective actions taken for future reference. Software solutions like GAGEpack can help manage these records efficiently.
Perform Routine Checks: Schedule and perform routine calibration checks to catch and correct deviations early. This proactive approach prevents inaccuracies from affecting the quality of work.
By integrating these techniques, a Tool Crib Attendant can significantly enhance the reliability and accuracy of tools, thereby ensuring better performance and compliance with quality standards.
How to Display Calibration Techniques Skills on Your Resume
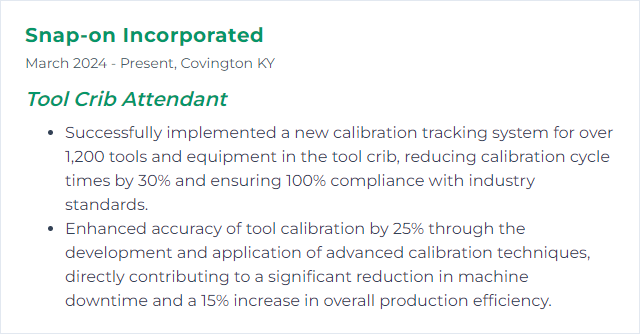
6. RFID Tracking
RFID tracking involves using radio-frequency identification technology to automatically identify and track tools and equipment in a tool crib, enhancing inventory management and reducing loss or misplacement.
Why It's Important
RFID tracking is crucial for a Tool Crib Attendant as it enables efficient, real-time inventory management, reduces tool misplacement or loss, and enhances the accuracy of tool issuance and return processes.
How to Improve RFID Tracking Skills
To improve RFID tracking for a Tool Crib Attendant, follow these concise steps:
Upgrade to UHF RFID Tags: Utilize Ultra-High Frequency (UHF) RFID tags for better range and faster identification. Zebra Technologies offers a variety of options suitable for tool tracking.
Implement RFID Readers at Entry/Exit Points: Install RFID readers at the crib's entrance and exit to automatically track tools without manual scanning. Impinj provides advanced readers that can enhance tracking accuracy.
Use RFID Embedded Tool Cabinets: Employ cabinets with built-in RFID technology to monitor tool check-ins and check-outs in real-time. Lista and Vidmar offer smart storage solutions that can be integrated with RFID systems.
Integrate with Inventory Management Software: Connect RFID system data with inventory management software to maintain up-to-date tool records, automate reordering, and generate usage reports. Fishbowl Inventory is an example of software that can streamline this process.
Conduct Regular Training: Regularly train staff on the proper use of RFID equipment and best practices to ensure the system's effectiveness. Continuous education can significantly enhance the adoption and utility of RFID tracking in tool management.
By following these steps, a Tool Crib Attendant can significantly improve the efficiency and accuracy of RFID tracking for tool management.
How to Display RFID Tracking Skills on Your Resume
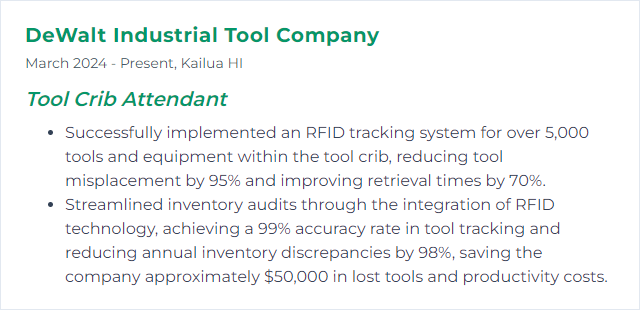
7. Microsoft Excel
Microsoft Excel is a spreadsheet program used for data organization, analysis, and reporting, allowing a Tool Crib Attendant to track inventory, manage tool checkouts, and monitor maintenance schedules efficiently.
Why It's Important
Microsoft Excel is important for a Tool Crib Attendant because it enables efficient tracking, organization, and analysis of tool inventories, maintenance schedules, and usage patterns, ensuring optimal inventory management and operational efficiency.
How to Improve Microsoft Excel Skills
To improve Microsoft Excel for a Tool Crib Attendant, focus on:
Learn Excel Formulas & Functions: Master key formulas (e.g., VLOOKUP, INDEX, MATCH) to manage and analyze inventory efficiently. Excel Formulas & Functions.
Implement Data Validation: Use data validation to ensure accurate data entry and to avoid errors in inventory records. Data Validation Guide.
Use Conditional Formatting: Highlight important information (e.g., low stock levels, expired items) to take timely actions. Conditional Formatting.
Create PivotTables: Summarize tool crib data to analyze trends and make informed decisions. Creating PivotTables.
Automate with Macros: Automate repetitive tasks (e.g., updating inventory, generating reports) using VBA macros. Getting Started with Macros.
Utilize Excel Templates: Use or customize templates designed for inventory management to save time. Excel Templates.
Improve Skills with Training: Continuously improve your Excel skills through courses and tutorials. Excel Training.
By focusing on these areas, a Tool Crib Attendant can significantly enhance their efficiency and accuracy in managing tool crib operations using Microsoft Excel.
How to Display Microsoft Excel Skills on Your Resume
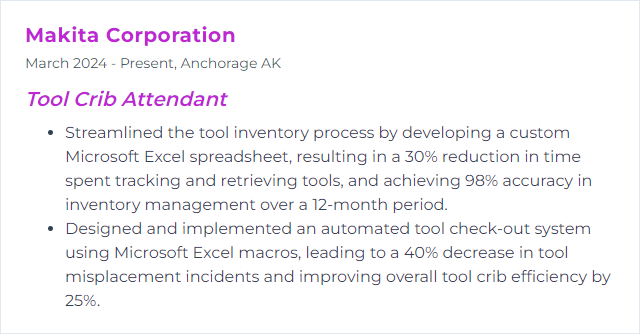
8. Forklift Operation
Forklift operation, in the context of a Tool Crib Attendant, involves the use of a powered industrial truck to lift, move, and position materials and tools within a warehouse or job site, ensuring efficient and safe handling of resources.
Why It's Important
Forklift operation is important for a Tool Crib Attendant because it enables the efficient and safe handling of heavy or bulky tools and materials, facilitating proper inventory management and ensuring timely availability of tools for operational needs.
How to Improve Forklift Operation Skills
Improving forklift operation, especially for a Tool Crib Attendant, involves enhancing safety, efficiency, and maintenance practices. Here’s a concise guide:
Safety Training: Ensure operators complete certified forklift safety training courses. Regular refreshers can keep safety forefront in their minds.
Pre-Operational Checks: Implement a routine for daily pre-operational checks to identify and address potential issues before they lead to accidents or equipment damage.
Efficient Organization: Design the tool crib and storage areas for easy access. Use layout optimization techniques to minimize unnecessary movement and improve picking efficiency.
Maintenance Schedule: Adhere to a strict maintenance schedule based on the manufacturer's recommendation and usage patterns. Preventive maintenance can significantly reduce downtime and extend the life of a forklift.
Use of Technology: Implement technology like RFID tagging for tools and inventory, which can streamline picking processes and reduce errors.
Ergonomics: Adjust forklifts to fit the operator properly and provide accessories that enhance comfort and reduce strain. Ergonomic improvements can boost operator efficiency and attentiveness.
By focusing on these areas, a Tool Crib Attendant can contribute significantly to improving forklift operations, enhancing safety, and optimizing productivity.
How to Display Forklift Operation Skills on Your Resume
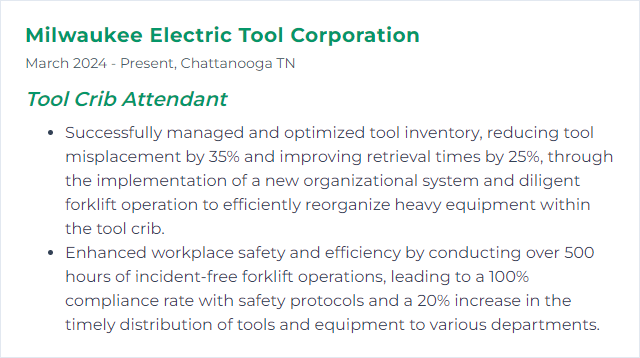
9. Safety Compliance
Safety compliance, in the context of a Tool Crib Attendant, involves adhering to established safety standards and regulations related to the management, maintenance, and distribution of tools and equipment to prevent accidents, injuries, and ensure a safe working environment.
Why It's Important
Safety compliance is crucial for a Tool Crib Attendant to ensure the safe handling and storage of tools, prevent accidents, and comply with legal and workplace safety regulations, thereby protecting both personnel and assets.
How to Improve Safety Compliance Skills
Improving safety compliance for a Tool Crib Attendant involves several key steps aimed at ensuring that all operations and procedures align with safety regulations and best practices. Here's a concise guide:
Regular Training: Ensure that the Tool Crib Attendant undergoes regular safety training sessions. This includes updates on safety protocols, proper handling, and storage of tools.
Safety Audits: Conduct regular safety audits of the tool crib to identify and rectify potential hazards.
Maintenance Checks: Implement a stringent tool maintenance and inspection program to ensure that all tools are in safe working condition.
Clear Signage: Place clear safety signage and instructions in the tool crib area to guide proper tool handling and storage.
Emergency Preparedness: Ensure the presence of emergency response plans and equipment (e.g., first aid kits, fire extinguishers) in the tool crib area.
Feedback Mechanism: Establish a system for workers to report safety concerns or suggestions related to tool handling and storage.
By focusing on these areas, a Tool Crib Attendant can significantly improve safety compliance in their work environment.
How to Display Safety Compliance Skills on Your Resume
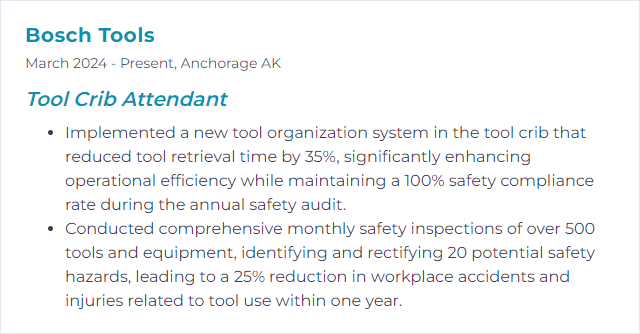
10. Lean Manufacturing
Lean Manufacturing is a systematic approach aimed at minimizing waste without sacrificing productivity. For a Tool Crib Attendant, it means efficiently managing and distributing tools and resources to reduce downtime and enhance workflow on the production floor.
Why It's Important
Lean Manufacturing is important for a Tool Crib Attendant because it ensures the efficient use of tools and materials, reduces waste, and improves workflow, leading to increased productivity and cost savings.
How to Improve Lean Manufacturing Skills
Improving Lean Manufacturing, particularly from the perspective of a Tool Crib Attendant, involves optimizing tool availability, minimizing waste, and enhancing workflow efficiency. Here's a concise guide:
Inventory Management: Implement a Just-In-Time (JIT) inventory system to reduce excess stock and minimize storage costs. Kanban systems can streamline this process by ensuring tools are replenished only as needed.
Tool Organization: Use 5S methodology (Sort, Set in order, Shine, Standardize, Sustain) to organize tools efficiently, making them easily accessible and reducing downtime. Learn more about 5S from Lean Enterprise Institute.
Preventive Maintenance: Schedule regular maintenance to prevent tool failure and production delays. This proactive approach is detailed in Total Productive Maintenance (TPM).
Technology Integration: Incorporate technology for real-time tracking and management of tool cribs. RFID technology can significantly enhance tool tracking efficiency. Explore the benefits of RFID in tool management at RFID Journal.
Continuous Improvement: Adopt a Kaizen mindset for continuous improvement, encouraging feedback from all team members to identify inefficiencies and suggest improvements. The basics of Kaizen can be explored further via the ASQ (American Society for Quality).
Training and Empowerment: Ensure that all personnel, including the Tool Crib Attendant, are well-trained in lean principles and empowered to make decisions that improve efficiency and reduce waste. This empowerment strategy is outlined in Lean Empowerment.
By focusing on these areas, a Tool Crib Attendant can significantly contribute to the lean manufacturing goals of reducing waste, improving productivity, and enhancing the overall efficiency of the manufacturing process.
How to Display Lean Manufacturing Skills on Your Resume
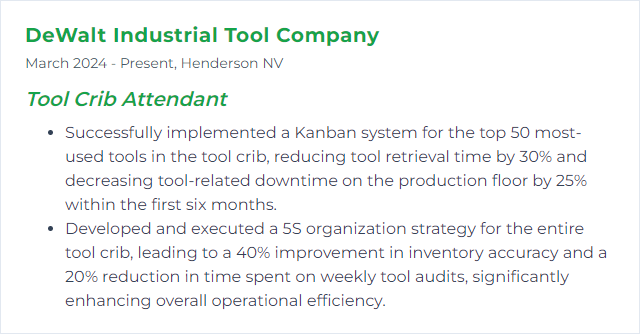
11. ERP Systems
ERP (Enterprise Resource Planning) systems are integrated software platforms that manage and automate core business processes, including inventory management. For a Tool Crib Attendant, an ERP system would streamline the tracking, distribution, and maintenance of tools and equipment, ensuring efficient operations and accurate inventory records.
Why It's Important
ERP systems are crucial for a Tool Crib Attendant because they streamline inventory management, ensuring accurate tracking of tools and materials, reducing the risk of stockouts or excess inventory, and improving the efficiency of issuing and returning items, ultimately enhancing productivity and cost control.
How to Improve ERP Systems Skills
Improving ERP systems, especially for a Tool Crib Attendant, involves enhancing inventory management, streamlining tool tracking, and facilitating real-time communication. Here are concise strategies:
Automate Tool Tracking: Implement RFID or barcode scanning to automate the check-in/out process, reducing manual entry errors (RFID Journal).
Integrate with IoT Devices: Use IoT devices for real-time tool condition monitoring, ensuring timely maintenance and reducing downtime (IoT For All).
Optimize Inventory Management: Leverage advanced analytics within your ERP to predict tool demand, optimizing stock levels and minimizing excess inventory (APICS).
Enhance User Interface: Ensure the ERP system has a user-friendly interface, tailored to the needs of a Tool Crib Attendant, for efficient operation (Nielsen Norman Group).
Ensure Real-Time Communication: Incorporate communication tools within the ERP system to facilitate instant alerts and messages between the tool crib and other departments (Slack).
Offer Training and Support: Provide comprehensive training and ongoing support for the Tool Crib Attendants to maximize the system's utility (Training Industry).
Implement Custom Reporting Tools: Use ERP modules that allow for custom report generation, giving insights into tool usage, costs, and procurement needs (Tableau).
By focusing on these areas, you can significantly enhance the efficiency and effectiveness of ERP systems from the perspective of a Tool Crib Attendant.
How to Display ERP Systems Skills on Your Resume
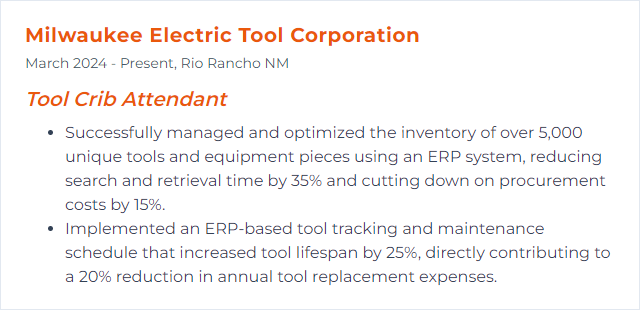
12. Barcode Scanning
Barcode scanning in the context of a Tool Crib Attendant involves using a scanner to read barcodes on tools and equipment for tracking, inventory management, and issuing or returning items efficiently.
Why It's Important
Barcode scanning is important for a Tool Crib Attendant because it ensures accurate tracking and management of tools and equipment, streamlines inventory control, and enhances efficiency by reducing manual data entry errors.
How to Improve Barcode Scanning Skills
To improve barcode scanning for a Tool Crib Attendant, consider the following steps:
Upgrade Scanner: Invest in a high-quality, durable scanner designed for industrial environments. Look for features like long battery life, fast scanning, and the ability to read damaged codes. Zebra Technologies offers a range of suitable scanners.
Optimize Barcode Quality: Ensure barcodes are clear, well-placed, and printed on durable material to withstand handling. Avery provides high-quality label solutions that are resistant to wear and tear.
Implement Mobile Scanning: Use smartphones or tablets with scanning apps for flexibility and efficiency. Scandit offers powerful scanning software that can be integrated into mobile devices.
Training: Provide comprehensive training to staff on optimal scanning techniques and troubleshoot common issues. Regular updates and refresher courses can maintain proficiency.
Software Integration: Ensure your scanning system is fully integrated with your inventory management software for real-time updates and data accuracy. Fishbowl Inventory is an example of software that offers robust barcode scanning integration.
Regular Maintenance: Schedule regular maintenance for scanners and update software to ensure everything operates at peak efficiency. Check manufacturer’s website for guidance.
By following these steps and investing in the right technology, training, and processes, you can significantly improve barcode scanning efficiency and accuracy in a tool crib environment.
How to Display Barcode Scanning Skills on Your Resume
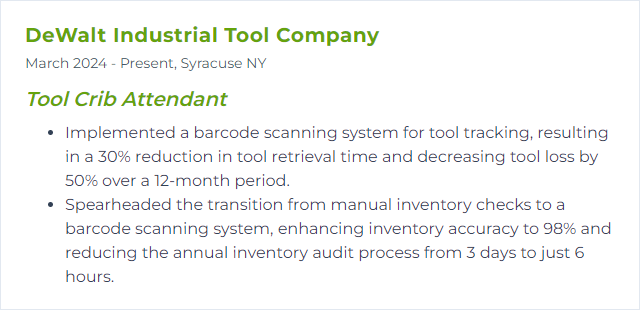