Top 12 Toolmaker Skills to Put on Your Resume
In the precision-driven world of toolmaking, showcasing a diverse set of skills on your resume is crucial to standing out in a competitive job market. This article outlines the top 12 toolmaker skills that employers value most, helping you to highlight your expertise and secure your next opportunity in the field.
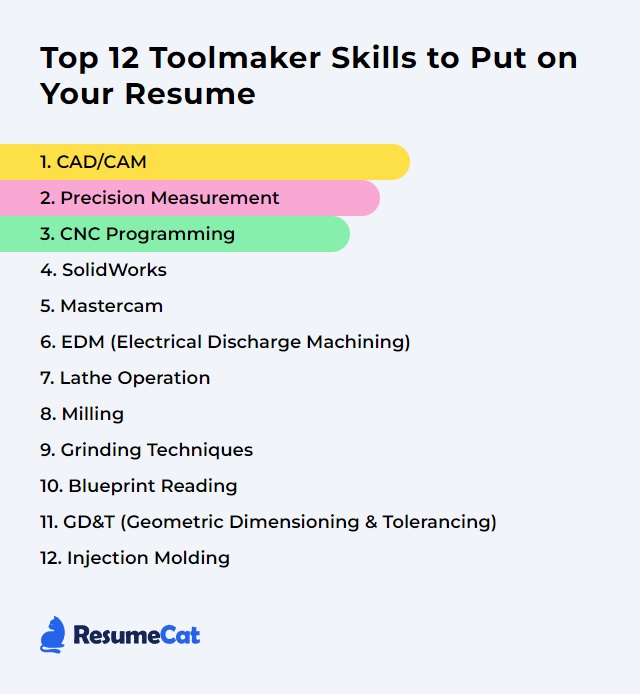
Toolmaker Skills
- CAD/CAM
- Precision Measurement
- CNC Programming
- SolidWorks
- Mastercam
- EDM (Electrical Discharge Machining)
- Lathe Operation
- Milling
- Grinding Techniques
- Blueprint Reading
- GD&T (Geometric Dimensioning and Tolerancing)
- Injection Molding
1. CAD/CAM
CAD/CAM stands for Computer-Aided Design/Computer-Aided Manufacturing. It is a technology used by toolmakers to design products and control manufacturing processes precisely. CAD software is used for designing the tools, molds, and dies, while CAM software translates these designs into instructions for the machinery to produce the physical parts. This integration streamlines the toolmaking process, enhancing accuracy, efficiency, and the ability to create complex geometries.
Why It's Important
CAD/CAM is crucial for a toolmaker because it enables precise design and manufacturing of tools, enhances efficiency, reduces errors, and allows for complex geometries and customization, improving overall quality and productivity.
How to Improve CAD/CAM Skills
Improving CAD/CAM for a Toolmaker involves enhancing precision, speed, and integration of design and manufacturing processes. Here's a concise guide:
Upgrade Software and Hardware: Ensure you're using the latest CAD/CAM software and that your hardware can handle its demands. This can significantly improve both design capabilities and processing speed.
Continuous Learning: Stay updated with new features and techniques by accessing online tutorials and courses specific to your CAD/CAM software.
Implement Standardized Processes: Develop and follow standardized design and programming processes to improve efficiency and accuracy. ISO standards for CAD data exchange can be a useful reference.
Utilize Simulation Tools: Before moving to the manufacturing phase, use simulation tools to identify and resolve potential issues. This can save time and reduce material waste.
Integrate CAD/CAM with ERP: Integrating your CAD/CAM system with an Enterprise Resource Planning (ERP) system can streamline workflow, from design to production planning and inventory management.
Collaborate and Communicate: Use platforms for collaborative CAD/CAM that allow team members to work together in real-time, regardless of location.
Custom Tools and Macros: Develop custom tools and macros for repetitive tasks within your CAD/CAM software to save time and increase consistency.
Regular Maintenance: Keep your CAD/CAM systems in top condition with regular maintenance, including software updates and hardware checks.
Feedback Loop: Establish a feedback loop with the manufacturing floor to continuously improve CAD/CAM processes based on real-world production experiences.
By following these steps and leveraging the right resources, a Toolmaker can significantly improve their CAD/CAM capabilities, leading to better designs, faster turnaround times, and reduced costs.
How to Display CAD/CAM Skills on Your Resume
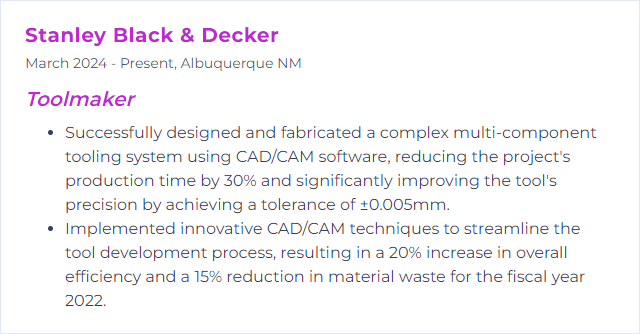
2. Precision Measurement
Precision measurement in toolmaking refers to the use of highly accurate instruments to ascertain the dimensions, angles, and surface quality of tools and components, ensuring they meet specified tolerances and standards with minimal error.
Why It's Important
Precision measurement is crucial for a toolmaker because it ensures that tools and parts are manufactured to exact specifications, guaranteeing high-quality, consistency, and compatibility, leading to optimal performance and reliability of the final products.
How to Improve Precision Measurement Skills
Improving precision measurement in toolmaking involves several key strategies:
Calibration: Regularly calibrate measuring instruments to ensure accuracy. Use calibration services that adhere to national or international standards. National Institute of Standards and Technology (NIST)
Environment Control: Maintain a controlled environment (temperature, humidity, and cleanliness) to reduce measurement errors. ASHRAE
Use of High-Quality Tools: Invest in high-quality, precision measurement tools from reputable manufacturers. Mitutoyo
Training: Continuously train on measurement techniques and tool handling to reduce human error. Precision Measurement Professionals Association (PMPA)
Digital Measurement Tools: Utilize digital tools and software for more accurate and repeatable measurements. FARO Technologies
Regular Maintenance: Perform regular maintenance and checks on tools to ensure they are in perfect working condition. Machinery's Handbook
Incorporating these strategies will significantly enhance precision in measurements for toolmakers.
How to Display Precision Measurement Skills on Your Resume
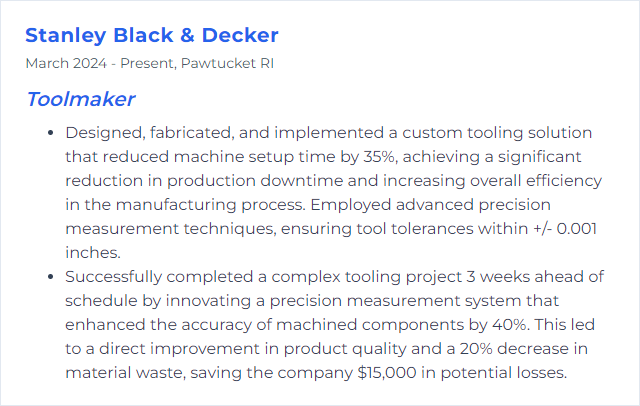
3. CNC Programming
CNC programming for a toolmaker involves creating detailed instructions for computer numerically controlled (CNC) machines to fabricate precise and complex tool components. This process includes defining tool paths, selecting appropriate cutting tools, and setting operational parameters to ensure accurate and efficient manufacturing.
Why It's Important
CNC programming is crucial for a toolmaker as it enables the precise and efficient creation of complex tools, dies, and molds. This digital programming ensures high accuracy, repeatability, and material optimization, significantly enhancing productivity and product quality in tool manufacturing processes.
How to Improve CNC Programming Skills
Improving CNC programming, particularly for a toolmaker, involves enhancing precision, efficiency, and adaptability. Here are short, concise strategies with relevant resources:
Master CAD/CAM Software: Deepen your understanding of your CAD/CAM software through tutorials and advanced training. Mastering software features optimizes programming time and tool paths. Fusion 360 and Mastercam offer extensive resources and tutorials.
Utilize Simulation Software: Before actual machining, use simulation software to anticipate and rectify potential issues, saving time and reducing waste. VERICUT is a leader in this space.
Optimize Tool Paths: Focus on optimizing tool paths for efficiency, including minimizing travel time and choosing the most effective cutting strategies. Mastercam's Dynamic Motion technology is an example of tool path optimization.
Stay Updated with Trends: CNC technology and techniques evolve rapidly. Stay updated through forums, publications, and continuing education. Websites like Modern Machine Shop provide valuable insights.
Apply Lean Manufacturing Principles: Incorporate lean manufacturing principles into your programming process to eliminate waste and improve productivity. The Lean Enterprise Institute offers resources on lean principles.
Use High-Quality Tooling: Invest in high-quality cutting tools and holders to improve performance and reduce errors. Companies like Sandvik Coromant provide advanced tooling solutions.
Implement G-Code Optimization Tools: Use G-code optimization software to refine your programs for maximum efficiency. G-Wizard Editor is an example of a tool that can help with this.
Feedback Loop: Create a feedback loop with the machine operators to get insights on the shop floor's real-world challenges and adjust programming accordingly.
By focusing on these areas, toolmakers can significantly improve their CNC programming capabilities, leading to more efficient, accurate, and cost-effective manufacturing processes.
How to Display CNC Programming Skills on Your Resume
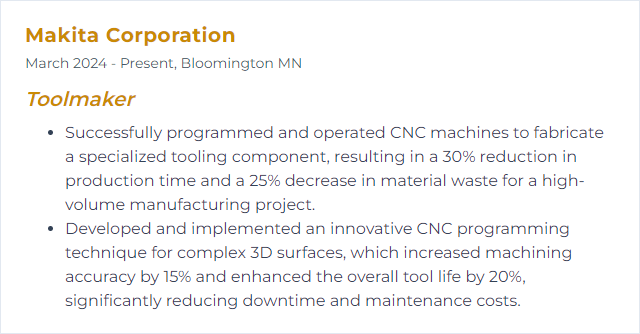
4. SolidWorks
SolidWorks is a computer-aided design (CAD) and engineering software used by toolmakers for designing and simulating tools, molds, and dies, enabling precision in manufacturing processes.
Why It's Important
SolidWorks is important for a Toolmaker because it enables precise 3D modeling and simulation of tools and molds, facilitating efficient design, modification, and optimization, thereby reducing production errors and saving time and resources.
How to Improve SolidWorks Skills
Improving SolidWorks skills, especially for a Toolmaker, involves a combination of learning best practices, leveraging SolidWorks' advanced features, and continuously updating your knowledge. Here’s a short guide:
Master the Basics: Ensure a strong foundation by mastering basic SolidWorks functions and commands. SolidWorks Tutorials offer a great starting point.
Learn Advanced Features: Dive into advanced features relevant to toolmaking, such as mold design, sheet metal, and weldments. The SolidWorks Help Center provides detailed guides and how-tos.
Utilize Simulation Tools: Enhance design accuracy and efficiency by using SolidWorks Simulation for stress analysis and material selection. Explore Simulation Solutions for more insights.
Customize Your Workflow: Customize SolidWorks to suit your specific toolmaking needs. Learn about custom tools and macros to streamline your workflow on the SolidWorks API Help page.
Stay Updated: SolidWorks frequently updates its software. Stay informed about new features and enhancements through the SolidWorks Blog.
Join the Community: Engage with the SolidWorks community through forums and user groups for tips, tricks, and networking. The SolidWorks Forums are a great place to start.
Continuous Learning: Consider official training courses and certifications to deepen your expertise and recognition in the field. Check out SolidWorks Certification programs for more information.
By following these steps and actively seeking out new learning opportunities, you can significantly improve your SolidWorks proficiency and efficiency as a Toolmaker.
How to Display SolidWorks Skills on Your Resume
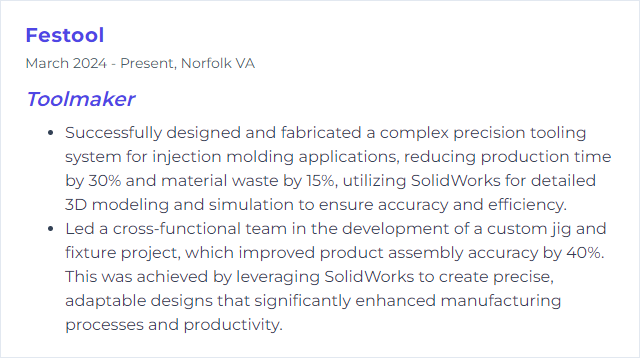
5. Mastercam
Mastercam is a computer-aided manufacturing (CAM) software used by toolmakers and machinists for designing and producing precision parts and tools, enabling efficient programming of CNC machines for milling, turning, and cutting operations.
Why It's Important
Mastercam is important for a toolmaker because it provides advanced CAD/CAM software solutions for designing, simulating, and programming efficient machining processes, significantly enhancing precision, productivity, and the overall quality of tools and molds.
How to Improve Mastercam Skills
Improving your Mastercam skills as a toolmaker involves a focus on precision, efficiency, and the effective use of advanced features. Here's a concise guide:
Master Fundamentals: Ensure a solid understanding of Mastercam basics. Use Mastercam's Tutorials to reinforce foundational skills.
Explore Advanced Features: Dive into advanced functions relevant to toolmaking. The Mastercam University offers specialized courses.
Customize Your Workspace: Tailor your Mastercam environment for toolmaking efficiency. Mastercam's Documentation provides insights on customization.
Join Forums: Engage with the Mastercam community in forums like eMastercam for tips, tricks, and problem-solving strategies.
Practice with Real-World Projects: Apply your skills on actual toolmaking projects. This hands-on approach solidifies learning and uncovers areas for improvement.
Stay Updated: Regularly update your software and explore new features. Mastercam's What’s New section keeps you informed.
Consistent practice, alongside leveraging these resources, will markedly improve your Mastercam proficiency in toolmaking contexts.
How to Display Mastercam Skills on Your Resume
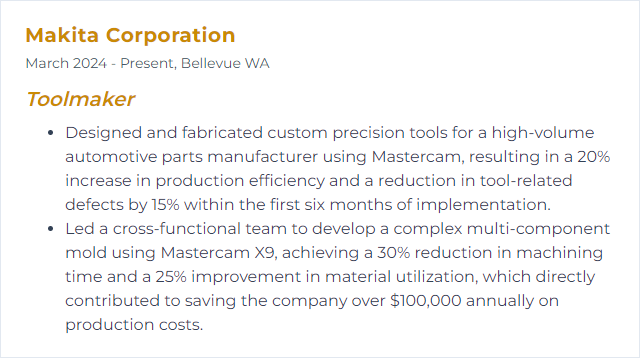
6. EDM (Electrical Discharge Machining)
EDM (Electrical Discharge Machining) is a manufacturing process where a desired shape is obtained using electrical discharges (sparks). Material is removed from the workpiece by a series of rapidly recurring current discharges between two electrodes, the tool and the workpiece, in the presence of a dielectric fluid. This method is particularly useful for hard materials or complex shapes that are difficult to machine with traditional techniques.
Why It's Important
EDM (Electrical Discharge Machining) is important for a toolmaker because it allows for the precise machining of complex shapes and hard materials with minimal physical stress on the tool, enabling the creation of intricate tool and die components that are difficult or impossible to produce with conventional machining techniques.
How to Improve EDM (Electrical Discharge Machining) Skills
Improving EDM (Electrical Discharge Machining) involves optimizing several factors to enhance efficiency, accuracy, and surface finish, while minimizing wear and tear on the tool and workpiece. Here are concise strategies for a toolmaker:
Material Selection: Choose materials for the electrode and workpiece that provide good electrical conductivity and thermal stability. Material Properties.
Parameter Optimization: Adjust parameters such as current, voltage, pulse on-time, and off-time for optimal performance. Optimizing EDM Parameters.
Fluid Selection and Management: Use appropriate dielectric fluids and ensure proper flushing to remove particles and reduce thermal stress. Dielectric Fluids in EDM.
Tool Design and Fabrication: Design electrodes with minimal wear characteristics and precise geometry for better accuracy. Use materials like graphite or copper for their excellent electrical and thermal properties. Electrode Design.
Maintenance and Cleanliness: Regular maintenance of EDM machines and cleanliness in the working environment to prevent contamination and ensure consistent performance. EDM Machine Maintenance.
Advanced Technologies: Incorporate advanced technologies like adaptive control and process simulation to optimize machining conditions in real-time. Adaptive Control in EDM.
Training and Experience: Continuous learning and gaining experience are crucial. Understanding the intricacies of EDM processes allows for better decision-making and innovation. EDM Training.
By focusing on these areas, a toolmaker can significantly enhance the performance and outcomes of EDM processes.
How to Display EDM (Electrical Discharge Machining) Skills on Your Resume
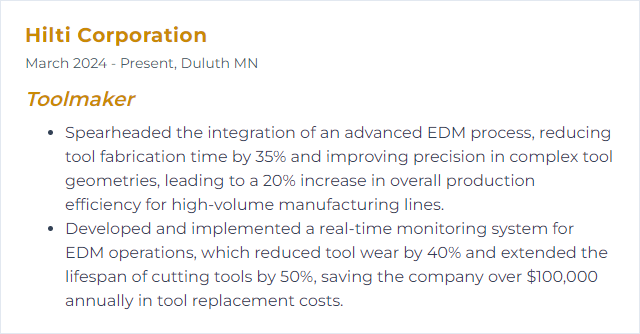
7. Lathe Operation
Lathe operation in toolmaking involves the use of a lathe machine to shape and modify metal components by rotating the workpiece against a cutting tool, allowing for precision manufacturing of tools and parts through processes like turning, facing, and threading.
Why It's Important
Lathe operation is crucial for a Toolmaker because it enables precise shaping, cutting, and finishing of metal components, essential for creating custom tools and parts with high accuracy and quality.
How to Improve Lathe Operation Skills
Improving lathe operation, especially for a toolmaker, involves enhancing precision, efficiency, and safety. Here are concise strategies:
Regular Maintenance: Keep the lathe properly lubricated and clean. Regularly check and adjust alignments. Lathe Maintenance Guide.
Use the Right Tooling: Select the correct cutting tools for the material and job. High-quality tools reduce wear and improve accuracy. Tool Selection Guide.
Optimize Cutting Conditions: Adjust speed, feed rate, and depth of cut according to the material and tooling. Use manufacturer guidelines for optimal conditions. Machining Calculator.
Implement Proper Workholding: Secure workpieces effectively to prevent movement during operations. Consider the use of chucks, clamps, or fixtures designed for the task. Workholding Basics.
Sharpen Tools Regularly: Keep cutting tools sharp to ensure clean cuts and reduce the force required. This also extends tool life. Tool Sharpening Techniques.
Upgrade Equipment: Consider investing in modern lathe attachments or features that can improve precision and efficiency, such as digital readouts (DROs) or CNC technology. Lathe Upgrades.
Educate and Train: Continuously learn new techniques and stay updated with the latest trends in toolmaking and machining. Online courses and workshops can be beneficial. Machining Education.
Implement Quality Control: Use precision measuring tools and establish a routine for checking dimensions frequently during operations to maintain accuracy. Quality Control Tools.
By focusing on these areas, a toolmaker can significantly improve lathe operation, leading to better quality work, increased productivity, and enhanced safety.
How to Display Lathe Operation Skills on Your Resume
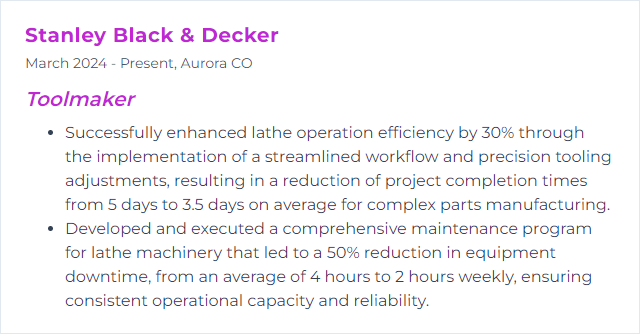
8. Milling
Milling is a machining process in which a rotating cutting tool removes material from a workpiece to create features such as slots, holes, and contours, commonly used in toolmaking for shaping metal parts with precision.
Why It's Important
Milling is important for a toolmaker because it allows for the precise shaping and cutting of materials to create complex parts and tools with high accuracy and fine finishes, essential for manufacturing and engineering applications.
How to Improve Milling Skills
Improving milling efficiency and quality involves several strategies focused on tool selection, machine settings, and material handling. Here are concise recommendations:
Tool Selection: Use the right end mill for the material and job. Carbide end mills are preferred for their hardness and heat resistance, especially for metals like stainless steel and aluminum. Harvey Tool offers a wide selection of material-specific end mills.
Optimize Cutting Parameters: Adjust the spindle speed, feed rate, and depth of cut according to the tool manufacturer's recommendations and material properties. Machining Doctor provides a calculator for optimizing these parameters.
Tool Path Optimization: Implement strategies such as trochoidal milling or High Efficiency Milling (HEM) to distribute wear evenly and reduce tool failure. Autodesk Fusion 360 has features to help design efficient toolpaths.
Use of Coolants and Lubricants: Proper use of coolants or lubricants can reduce heat and improve tool life, especially in materials that are difficult to machine. Machinery Lubrication offers insights into selecting the right type for your application.
Regular Maintenance: Ensure the milling machine is regularly calibrated and maintained. This includes checking spindle alignment, fixing any loose components, and ensuring the workpiece is securely clamped.
Invest in Quality Tool Holders: High-quality tool holders can reduce vibrations and improve precision. BIG KAISER provides a variety of tool holding solutions.
Stay Informed: Continuously learn about new tools, materials, and strategies. Websites like Modern Machine Shop offer valuable insights and updates on advancements in milling and machining practices.
By focusing on these aspects, toolmakers can achieve more efficient and precise milling operations.
How to Display Milling Skills on Your Resume
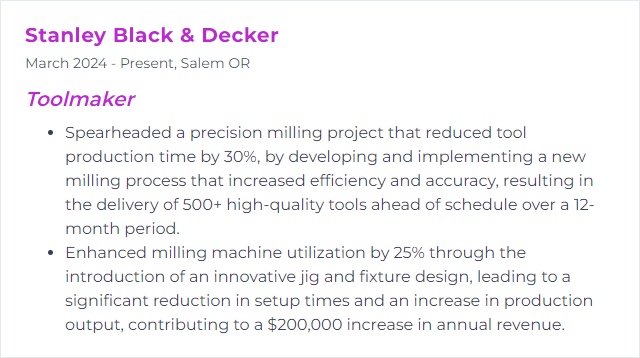
9. Grinding Techniques
Grinding techniques for a toolmaker involve using abrasive processes to shape, sharpen, or finish tools and components, ensuring precision and smooth surfaces. This includes operations like surface, cylindrical, and centerless grinding, tailored to achieve the desired geometry and finish on tooling materials.
Why It's Important
Grinding techniques are crucial for a toolmaker as they ensure precision and fine surface finishes on tools, enabling accurate and efficient cutting, shaping, or forming operations on various materials. This directly impacts the quality and functionality of the manufactured parts.
How to Improve Grinding Techniques Skills
Improving grinding techniques for toolmakers involves focusing on precision, efficiency, and safety. Here are concise tips:
Choose the Right Grinding Wheel: Match the wheel composition and grade to the material being ground. Understanding Grinding Wheel Applications can guide you in making the right choice.
Wheel Dressing: Regularly dress the wheel to maintain its shape and sharpness. This guide on wheel dressing offers practical insights.
Optimize Grinding Parameters: Adjust speed, feed, and contact areas to reduce heat and improve finish. This parameter adjustment reference can help.
Coolant Use: Properly apply coolant to reduce heat and improve surface finish. Coolant strategies for grinding are crucial for toolmakers.
Precision Fixturing: Use high-quality fixtures to hold the workpiece firmly and accurately. This discussion on fixturing could be insightful.
Inspect and Measure: Frequently inspect and measure your work to ensure it meets specifications. Tools and techniques for measuring in grinding are key to quality.
Safety Practices: Always follow safety guidelines to protect yourself and your workplace. OSHA’s guidelines on grinding safety are mandatory reading.
Each of these tips is aimed at refining your grinding process to achieve better results in your toolmaking projects.
How to Display Grinding Techniques Skills on Your Resume
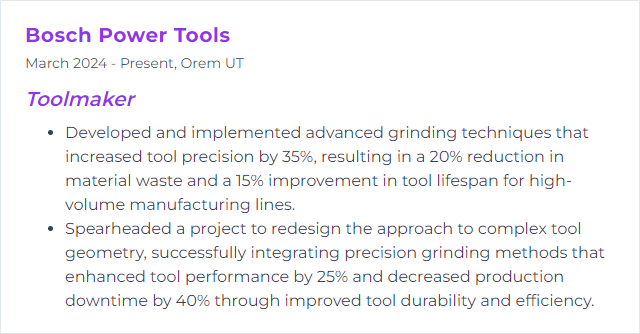
10. Blueprint Reading
Blueprint reading for a toolmaker involves interpreting detailed technical drawings that specify the design, dimensions, and materials required to manufacture tools, parts, or equipment. It includes understanding symbols, tolerances, and specifications essential for precision toolmaking.
Why It's Important
Blueprint reading is crucial for a Toolmaker because it enables precise understanding and interpretation of technical drawings, ensuring accurate fabrication, assembly, and modification of tools and dies according to specifications.
How to Improve Blueprint Reading Skills
Improving blueprint reading, especially for a toolmaker, involves enhancing your ability to understand and interpret detailed technical drawings and specifications used in manufacturing tools. Here's a concise guide:
Familiarize with Basic Symbols and Notations: Start by understanding the basic symbols, lines, and notations commonly used in blueprints. The Engineering Toolbox offers a good starting point.
Learn Geometric Dimensioning and Tolerancing (GD&T): GD&T provides a clear way to communicate design intent. ASME has resources to get you started.
Practice Regularly: Like any skill, practice is key. Use resources such as Tooling U-SME for courses specifically designed for toolmakers.
Use Software Tools: Familiarize yourself with CAD (Computer-Aided Design) software like AutoCAD or SolidWorks, which can help you visualize blueprints in 3D. AutoDesk offers tutorials and learning paths.
Join Workshops and Seminars: Participate in industry workshops and seminars. Organizations like NIMS (National Institute for Metalworking Skills) often hold relevant training sessions.
Refer to Books and Manuals: Books like "Print Reading for Industry" by Walter C. Brown provide a comprehensive look into blueprint reading. Visit your local library or bookstore.
By engaging with these resources and consistently applying yourself to learning and practice, you can significantly improve your blueprint reading skills as a toolmaker.
How to Display Blueprint Reading Skills on Your Resume
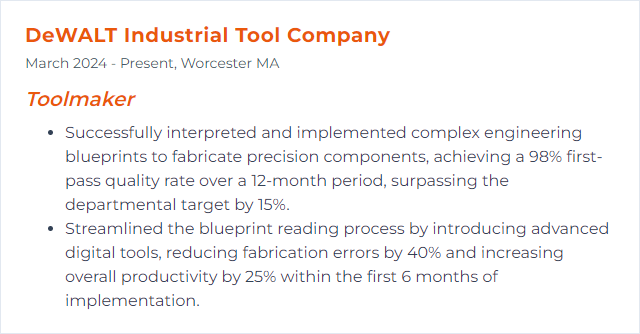
11. GD&T (Geometric Dimensioning and Tolerancing)
GD&T (Geometric Dimensioning and Tolerancing) is a system for defining and communicating engineering tolerances through symbolic language on engineering drawings, specifying the size, form, orientation, and location of part features with precision. For a toolmaker, it provides a clear and concise method for interpreting complex design requirements, ensuring accuracy and functionality in tool creation.
Why It's Important
GD&T is important for a Toolmaker because it ensures precise and consistent manufacturing of parts by clearly defining geometric forms, sizes, and tolerances, minimizing errors, and enhancing interchangeability and functionality of components.
How to Improve GD&T (Geometric Dimensioning and Tolerancing) Skills
Improving your skills in Geometric Dimensioning and Tolerancing (GD&T) as a Toolmaker involves understanding its fundamental concepts, applying them to real-world scenarios, and staying updated with the latest standards. Here’s a concise guide:
Understand the Basics: Start with a solid grasp of GD&T principles, symbols, and rules. Online resources like ENGINEERING.com offer introductory articles and tutorials.
Practice Application: Apply GD&T concepts to your toolmaking projects. Use CAD software that supports GD&T, such as SolidWorks or AutoCAD, to practice creating and interpreting drawings.
Use Standards: Familiarize yourself with the ASME Y14.5 standard, which governs GD&T practices. You can purchase the standard at the ASME website.
Continuous Learning: Enroll in GD&T training courses. Websites like Udemy and LinkedIn Learning offer courses tailored to different expertise levels.
Join Forums and Groups: Engage in discussions and seek advice from professionals in forums such as Eng-Tips GD&T Forum to gain insights and share experiences.
Improving in GD&T is a continuous process of learning, practicing, and applying these skills in your toolmaking projects.
How to Display GD&T (Geometric Dimensioning and Tolerancing) Skills on Your Resume
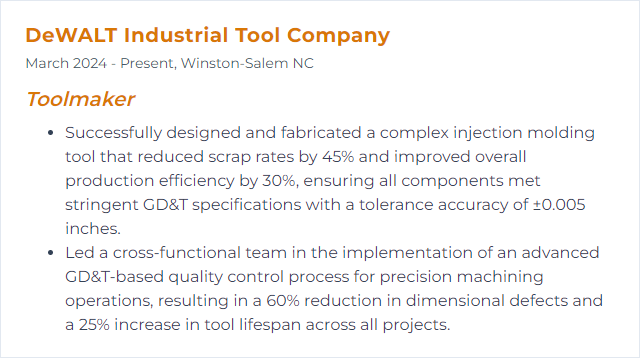
12. Injection Molding
Injection molding is a manufacturing process used by toolmakers to produce parts by injecting molten material into a mold, where it cools and solidifies into the desired shape.
Why It's Important
Injection molding is important for a toolmaker because it enables the mass production of complex and precise parts with high consistency, efficiency, and cost-effectiveness, utilizing molds crafted by the toolmaker.
How to Improve Injection Molding Skills
Improving injection molding, especially from a toolmaker's perspective, involves a focus on precision tool design, material selection, and process optimization. Here are some concise strategies:
Design Optimization: Ensure molds are designed for uniform cooling and easy material flow. Use simulation software like Moldflow to anticipate and rectify potential issues in the design phase.
Material Selection: Choose the correct steel for molds considering durability and wear resistance. Refer to ASSAB’s tool steel selection guide for recommendations.
Precision Machining: Employ advanced CNC machines and EDM technology for precise mold manufacturing. Familiarize with the latest machining solutions at Haas Automation's resource hub.
Surface Treatment: Improve mold longevity and performance with appropriate coatings. Explore options at Oerlikon Balzers’ surface solutions.
Process Control: Use sensors and IoT technology for real-time monitoring and control of molding parameters. Learn about smart manufacturing solutions at Siemens’ Digital Enterprise Suite.
Maintenance Practices: Implement a rigorous maintenance schedule to avoid unplanned downtimes. MoldTrax offers management software specifically for tracking mold performance and maintenance.
By focusing on these areas, toolmakers can significantly improve the efficiency, quality, and reliability of injection molding processes.
How to Display Injection Molding Skills on Your Resume
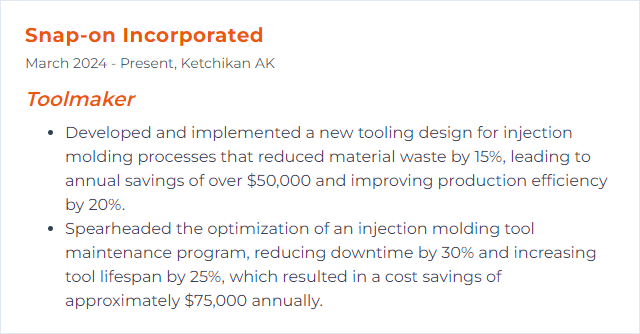