Top 12 Tool Designer Skills to Put on Your Resume
In today's competitive job market, having a standout resume is crucial for tool designers aiming to secure their dream positions. Highlighting the top skills that showcase your expertise and adaptability can significantly enhance your appeal to potential employers, setting you apart from other candidates.
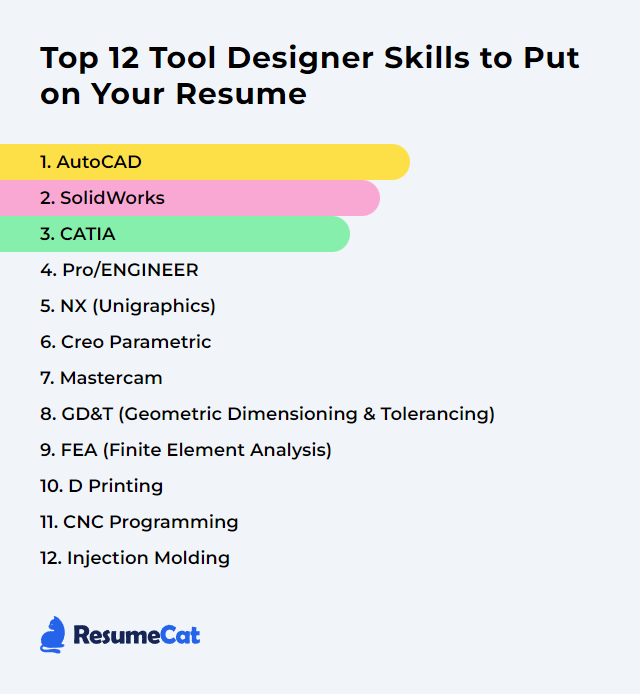
Tool Designer Skills
- AutoCAD
- SolidWorks
- CATIA
- Pro/ENGINEER
- NX (Unigraphics)
- Creo Parametric
- Mastercam
- GD&T (Geometric Dimensioning and Tolerancing)
- FEA (Finite Element Analysis)
- D Printing
- CNC Programming
- Injection Molding
1. AutoCAD
AutoCAD is a computer-aided design (CAD) software used by tool designers for creating precise 2D and 3D drawings and models of tools and mechanical parts.
Why It's Important
AutoCAD is essential for a Tool Designer because it enables precise and efficient creation, modification, and optimization of tool designs, ensuring accuracy, compatibility with manufacturing processes, and reducing production errors.
How to Improve AutoCAD Skills
Improving your AutoCAD skills, especially as a Tool Designer, involves a blend of learning, practice, and leveraging the right resources. Here's a concise guide:
Master the Basics: Ensure you understand AutoCAD's core functions – drawing commands, modifying tools, layer management, and block usage. Autodesk's official tutorials are a great starting point.
Practice Regularly: Hands-on practice is key. Challenge yourself with real-life projects or exercises specifically for tool design. Websites like CAD Exercises offer practice drawings.
Customize Your Workspace: Tailor AutoCAD's interface and toolsets to suit your specific needs as a Tool Designer. Autodesk offers guidance on customization.
Learn Advanced Features: Dive into advanced features relevant to tool design such as 3D modeling, parametric constraints, and the use of AutoLISP for automation. The AutoCAD blog provides updates and tips on advanced functionalities.
Use Online Resources and Forums: Engage with communities on platforms like the AutoCAD Forums and Reddit’s r/AutoCAD. Here, you can ask questions, share experiences, and get feedback on your work.
Stay Updated: AutoCAD is continually updated with new features and improvements. Keep abreast of these changes by reviewing Autodesk’s What’s New section.
Attend Workshops and Webinars: Participate in workshops and webinars that focus on tool design and AutoCAD advancements. Websites like LinkedIn Learning offer courses tailored to various aspects of AutoCAD.
Utilize YouTube Tutorials: YouTube is a rich resource for learning specific AutoCAD techniques. Channels like CAD Intentions and Lynn Allen's Tips and Tricks are excellent for both beginners and advanced users.
By focusing on these areas, you'll not only improve your AutoCAD skills but also enhance your efficiency and effectiveness as a Tool Designer.
How to Display AutoCAD Skills on Your Resume
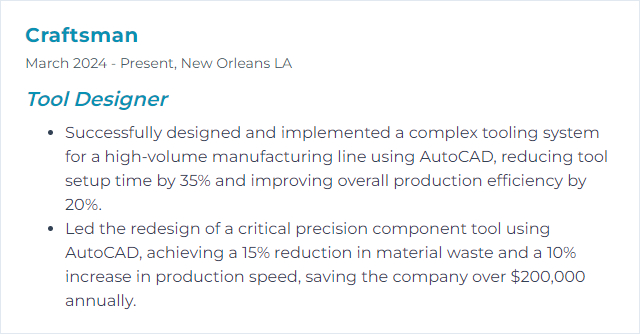
2. SolidWorks
SolidWorks is a computer-aided design (CAD) and computer-aided engineering (CAE) software program used by tool designers for creating 3D models and detailed drawings of tools and machinery parts, facilitating design, simulation, and manufacturing processes.
Why It's Important
SolidWorks is essential for a Tool Designer as it facilitates precise 3D modeling and simulation, enabling the creation of detailed tool designs with accuracy and efficiency, optimizing functionality and manufacturability.
How to Improve SolidWorks Skills
Improving your SolidWorks skills as a tool designer involves mastering several core areas: precision modeling, efficient use of assembly tools, and effective application of design automation. Here are concise strategies to enhance your SolidWorks proficiency:
Master Precision Modeling: Dive into advanced sketching and part modeling techniques to ensure accuracy in your tool designs. The SolidWorks Tutorials on MySolidWorks are a great place to refine these skills.
Efficient Use of Assembly Tools: Understanding how to effectively use mates, patterns, and assembly features can significantly speed up your design process. Explore the Assembly Modeling section in the SolidWorks Help Center.
Design Automation: Familiarize yourself with SolidWorks API and DriveWorks to automate repetitive tasks and configurations. This SolidWorks API Fundamentals guide is a helpful starting point.
Utilize Simulation Features: Apply SolidWorks Simulation to validate and optimize your tool designs for performance and durability. The SolidWorks Simulation Training provides comprehensive learning materials.
Keep Up-to-Date: Stay current with the latest SolidWorks features and updates. The What's New section in SolidWorks documentation highlights the latest enhancements.
Focusing on these areas can significantly enhance your capabilities and efficiency in using SolidWorks for tool design.
How to Display SolidWorks Skills on Your Resume
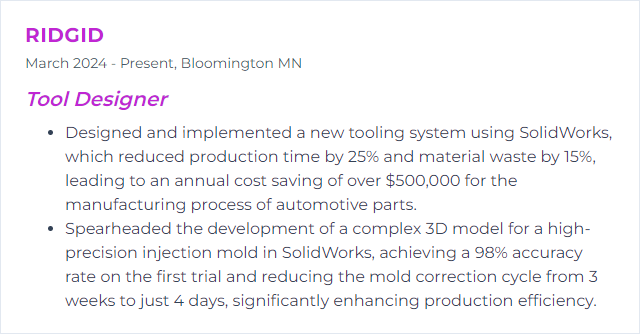
3. CATIA
CATIA (Computer-Aided Three-dimensional Interactive Application) is a powerful CAD (Computer-Aided Design) software tool used by tool designers for designing complex models and tools, including 3D modeling, simulation, and manufacturing analysis, facilitating precision and efficiency in tool design projects.
Why It's Important
CATIA is crucial for Tool Designers because it offers advanced 3D modeling capabilities, enabling precise design, simulation, and optimization of complex tools and equipment, thus ensuring high-quality outputs and efficiency in the manufacturing process.
How to Improve CATIA Skills
Improving your CATIA skills as a Tool Designer involves a blend of enhancing your technical knowledge, practical application, and staying updated with the latest industry trends. Here's a concise guide:
Official Training and Certification: Start with Dassault Systèmes’ official CATIA training to ensure you have a solid foundation and to learn advanced techniques.
Online Courses and Tutorials: Platforms like LinkedIn Learning and Udemy offer extensive CATIA courses tailored to different levels and specialties, including tool design.
Practice with Real-world Projects: Apply your skills to real-world problems or personal projects. This hands-on approach solidifies learning and improves problem-solving skills.
Join Forums and Communities: Engage with communities on platforms like COE (Community of Experts of Dassault Systèmes Solutions) to exchange knowledge, tips, and stay updated with the latest in CATIA developments.
Explore Advanced Modules: Dive deeper into CATIA’s specialized modules relevant to tool design, such as the Mold Tooling Design (MTD) and Sheet Metal Design (SMD) workbenches. Practicing these modules can significantly enhance your capabilities.
Read Books and Guides: Books such as "CATIA for Designers" by Sham Tickoo provide comprehensive learning material. Find the latest editions to stay current.
Stay Updated with Software Updates: Regularly check for updates on CATIA’s official website and explore new features and tools that can streamline your design process.
By combining these resources and continuously applying your skills, you can significantly improve your proficiency in CATIA as a Tool Designer.
How to Display CATIA Skills on Your Resume
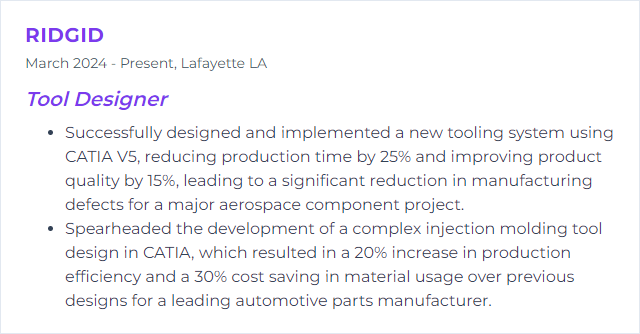
4. Pro/ENGINEER
Pro/ENGINEER, now known as PTC Creo, is a 3D CAD software that provides advanced tools for product design, engineering, and manufacturing, enabling tool designers to create precise models, simulations, and detailed drawings for tooling and fixtures.
Why It's Important
Pro/ENGINEER, now known as PTC Creo, is important for a Tool Designer because it offers advanced 3D CAD capabilities, enabling precise tool design, simulation, and manufacturing process planning. This enhances design accuracy, reduces time-to-market, and improves tool performance and durability.
How to Improve Pro/ENGINEER Skills
Improving your proficiency in Pro/ENGINEER (now known as PTC Creo) as a Tool Designer involves leveraging its robust features for design efficiency, accuracy, and innovation. Here’s a concise guide:
Master the Basics: Ensure a strong grasp of fundamental Pro/ENGINEER functionalities. PTC offers official training courses that are invaluable for beginners to advanced users.
Utilize Advanced Modules: Explore and integrate advanced modules like Tool Design Option (TDO) for specialized tool and die design capabilities, enhancing your design process.
Customize Your Workspace: Tailor your workspace and toolbars for efficiency. Customizing your environment to suit your workflow can significantly improve productivity.
Incorporate Add-Ons and Extensions: Utilize PTC-approved add-ons and extensions to expand the software’s capabilities, focusing on those offering enhanced tool design features.
Practice Design Optimization: Engage with features like parametric modeling and simulation to iterate designs quickly. This optimization guide can help understand how to make designs more efficient and robust.
Stay Updated: Regularly update your software to the latest version to access improved features and bug fixes. Keeping up-to-date with PTC’s latest releases ensures access to the newest tools and improvements.
Join the Community: Participate in PTC Community forums to share insights, ask questions, and learn from experienced Pro/ENGINEER users.
Utilize Keyboard Shortcuts: Learning and using keyboard shortcuts can drastically reduce design time. A list of shortcuts can be found in the PTC Creo Help Center.
By focusing on these areas, you can significantly improve your Pro/ENGINEER skills, leading to more efficient and innovative tool designs.
How to Display Pro/ENGINEER Skills on Your Resume
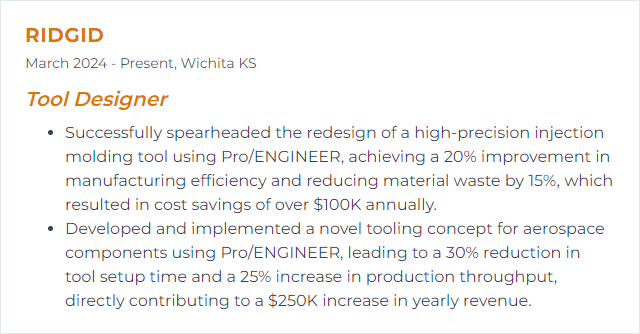
5. NX (Unigraphics)
NX (Unigraphics) is a high-end, integrated CAD/CAM/CAE software suite used for product design, engineering, and manufacturing, offering advanced capabilities for tool design, including mold design, progressive die design, and fixture design, enabling efficient creation, simulation, and verification of tooling and machining processes.
Why It's Important
NX (Unigraphics) is important for a Tool Designer because it provides advanced, integrated CAD/CAM/CAE solutions, enabling efficient design, simulation, and manufacturing of complex tools with precision and reduced time-to-market.
How to Improve NX (Unigraphics) Skills
Improving your skills in NX (Unigraphics) as a Tool Designer involves focusing on mastering key features relevant to tool design, integrating best practices, and continuously updating your knowledge with the latest software developments. Here are concise steps to help you enhance your NX proficiency:
Online Tutorials and Courses: Begin with Siemens Learning Tracks, which offer structured courses from beginner to advanced levels. Specialized courses for Tool Design can significantly improve your command over specific NX functionalities.
Practice with Real Projects: Apply your skills to real-world projects as often as possible. Websites like GrabCAD provide a vast library of CAD files that you can use for practice and inspiration.
Use Siemens Community Forums: Engage with the Siemens NX Design Community to ask questions, share knowledge, and learn from experienced professionals.
Stay Updated with New Features: NX is constantly updated with new features and improvements. Regularly visit the Siemens NX Blog to stay informed about the latest updates and how they can be applied to tool design.
Shortcuts and Customization: Learning and customizing keyboard shortcuts can significantly speed up your workflow. Refer to the NX documentation within the software for a list of shortcuts and instructions on customization.
Master NX CAM: For tool designers, understanding the CAM (Computer-Aided Manufacturing) capabilities of NX can be crucial. Explore resources and tutorials focused on NX CAM to enhance your designs for manufacturability.
Feedback and Review Sessions: Regularly review your work with peers or mentors. Constructive feedback is invaluable for improvement.
Certification: Consider obtaining a Siemens Certification in NX for Tool Design. It not only validates your skills but also keeps you motivated to learn and understand the software's deeper functionalities.
By integrating these resources and strategies into your learning plan, you can significantly enhance your NX skills tailored to the nuances of tool design.
How to Display NX (Unigraphics) Skills on Your Resume
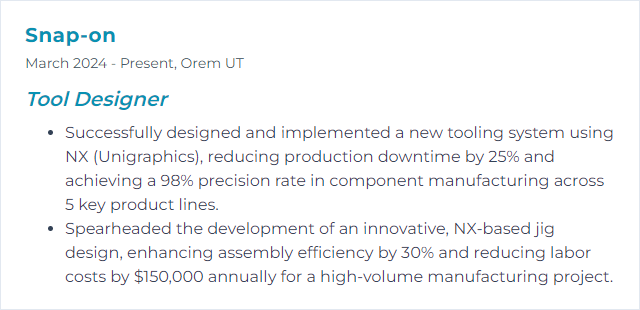
6. Creo Parametric
Creo Parametric is a powerful 3D CAD software tool used by tool designers for product design and development, enabling the creation, analysis, and modification of complex geometries and assemblies with parametric and direct modeling capabilities.
Why It's Important
Creo Parametric is important for a Tool Designer because it offers powerful and flexible 3D CAD capabilities for designing complex tools, enabling efficient development, simulation, and modification of tool designs to meet precise specifications and manufacturing requirements.
How to Improve Creo Parametric Skills
Improving your skills in Creo Parametric as a Tool Designer involves mastering key functionalities, leveraging advanced features, and staying updated with the latest advancements. Here are concise tips:
Master the Basics: Start with a strong foundation in the basics of Creo Parametric. Focus on understanding sketching, part modeling, assembly, and drawing generation. PTC’s Learning Exchange offers tutorials.
Utilize Advanced Modeling Techniques: Dive into advanced features such as surfacing for complex shapes, and utilize top-down design for effective assembly management. Explore Vertanux1’s Creo tutorials for practical insights.
Learn Sheet Metal Design: As a tool designer, mastering sheet metal features in Creo will be invaluable. Creo’s sheet metal design guide provides a good starting point.
Incorporate Mold Design: Utilize Creo's mold design capabilities to streamline the design of molds for manufacturing. PTC offers resources specifically for mold design.
Embrace Automation with Mapkeys: Create mapkeys to automate repetitive tasks, increasing efficiency. Here’s a guide on how to create mapkeys in Creo.
Customize the Interface: Tailor your workspace by customizing the ribbon interface to better suit your workflow. This customization guide from PTC can help.
Stay Updated: Creo undergoes continuous improvement. Stay abreast of new features and updates through PTC’s Creo Blog.
Participate in Forums: Join the PTC Community Forums to ask questions, share knowledge, and learn from the experiences of others.
Practice and Experiment: Finally, the key to mastery is consistent practice and experimentation. Challenge yourself with new projects that push the limits of your current capabilities.
By focusing on these areas, you can significantly improve your proficiency and efficiency in Creo Parametric as a Tool Designer.
How to Display Creo Parametric Skills on Your Resume
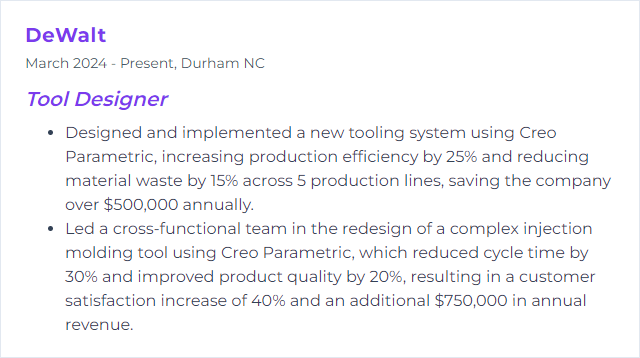
7. Mastercam
Mastercam is a computer-aided manufacturing (CAM) software used by tool designers and engineers for creating machining paths and plans for CNC (Computer Numerical Control) machines, facilitating the design and manufacturing of tools, dies, and molds with precision and efficiency.
Why It's Important
Mastercam is important for a Tool Designer because it provides powerful and versatile CAM software solutions for efficiently designing and programming precision tool paths, ensuring optimal machining and manufacturing of tools with accuracy and speed.
How to Improve Mastercam Skills
Improving your Mastercam skills as a Tool Designer involves focusing on efficient design practices, learning advanced features, and staying updated with the latest software enhancements. Here are concise suggestions to enhance your Mastercam proficiency:
Explore Mastercam University: Official online training for Mastercam users, offering a range of courses from basics to advanced techniques. Mastercam University.
Participate in Webinars and Workshops: Regularly attend Mastercam webinars and workshops for insights on new features and tool design-specific applications. Mastercam Events.
Utilize Online Forums: Engage with the Mastercam community in forums. Share experiences and get solutions from peers and experts. Mastercam Forum.
Practice with Mastercam Tutorials: Practice various tool design projects using Mastercam tutorials to understand diverse functionalities. Mastercam Tutorials.
Stay Updated with Software Updates: Regularly update your Mastercam software to utilize the latest features and improvements. Check updates at Mastercam Support.
By focusing on these areas, you can enhance your Mastercam skills relevant to tool design, ensuring efficient and innovative tool creation.
How to Display Mastercam Skills on Your Resume
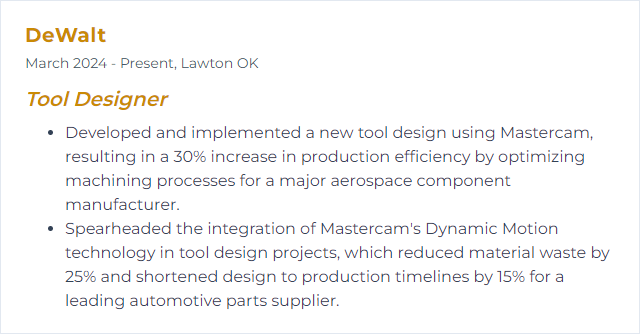
8. GD&T (Geometric Dimensioning and Tolerancing)
GD&T (Geometric Dimensioning and Tolerancing) is a system for defining and communicating engineering tolerances. It uses a symbolic language on engineering drawings and computer-generated three-dimensional solid models that explicitly describes nominal geometry and its allowable variation. For a Tool Designer, it provides a clear and precise way to communicate how parts fit and function within complex tools and dies, ensuring accuracy, consistency, and manufacturability.
Why It's Important
GD&T is crucial for a Tool Designer as it ensures precision and consistency in manufacturing by defining exact geometrical requirements for parts. This facilitates the production of interchangeable components, reduces errors, and minimizes waste, leading to cost-effective and reliable tooling processes.
How to Improve GD&T (Geometric Dimensioning and Tolerancing) Skills
Improving your skills in Geometric Dimensioning and Tolerancing (GD&T) as a Tool Designer involves understanding the system's principles deeply and applying them effectively to create precise, functional designs. Here’s a short guide to get you started:
Educate Yourself: Begin with foundational GD&T courses or tutorials. ASME offers comprehensive GD&T training, including the basics and advanced concepts.
Practice Regularly: Apply what you learn on actual design projects. Use simulation software to see how changes in tolerancing affect your design.
Use GD&T Resources: Refer to the GD&T Hub for free resources, articles, and tutorials to strengthen your understanding.
Join Forums and Groups: Engage with communities such as the Eng-Tips GD&T Forum to exchange knowledge and solve doubts with peers.
Stay Updated: GD&T standards evolve, so keep yourself updated with the latest editions of ASME Y14.5 and other relevant documents through the ASME website.
Feedback and Review: Request feedback on your designs from experienced colleagues and learn from the review process.
Certification: Consider obtaining a GD&T certification from a recognized body such as ASME to validate your skills and knowledge.
By following these steps and consistently applying GD&T principles to your tool designs, you can enhance the accuracy, efficiency, and functionality of your projects.
How to Display GD&T (Geometric Dimensioning and Tolerancing) Skills on Your Resume
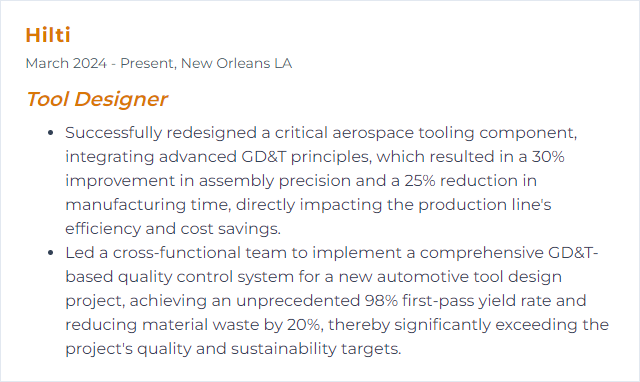
9. FEA (Finite Element Analysis)
Finite Element Analysis (FEA) is a computer-based method used by tool designers to simulate and predict how tool designs will respond to physical forces, such as stress, vibration, heat, and other physical effects, by breaking down the tool into smaller, finite elements for detailed analysis. This helps in optimizing design, enhancing performance, and ensuring safety and reliability before manufacturing.
Why It's Important
FEA (Finite Element Analysis) is crucial for a Tool Designer as it enables the simulation and assessment of the tool's design under various conditions without the need for physical prototypes, thus optimizing performance, durability, and cost-effectiveness in the design process.
How to Improve FEA (Finite Element Analysis) Skills
Improving Finite Element Analysis (FEA) as a Tool Designer involves enhancing model accuracy, computational efficiency, and result interpretation. Here are concise strategies:
Mesh Refinement: Optimize mesh size and quality for balance between accuracy and computational time. Use adaptive meshing when possible. ANSYS provides insights on meshing techniques.
Material Properties: Accurately define material properties relevant to the analysis. For material data, MatWeb is a comprehensive resource.
Boundary Conditions and Loadings: Clearly define and apply realistic boundary conditions and loadings. SimScale’s Documentation offers guidance on setting these parameters.
Solver Selection and Settings: Choose the appropriate solver and settings for your analysis type. COMSOL's Solver Guide helps in selecting the right solver.
Validation and Verification: Validate and verify your model against analytical solutions or experimental data. NAFEMS provides resources on best practices.
Software Proficiency: Stay updated with your FEA software capabilities and training. Tool vendors like Autodesk offer tutorials and guides.
Improving FEA requires a combination of good practice, continuous learning, and using the right resources.
How to Display FEA (Finite Element Analysis) Skills on Your Resume
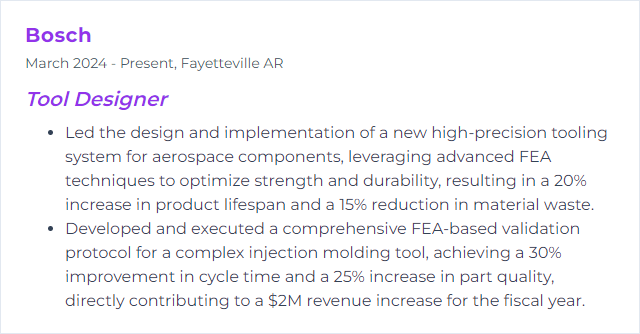
10. D Printing
3D printing, for a Tool Designer, is a manufacturing process that creates physical objects from digital designs by laying down successive layers of material until the object is formed. It allows for rapid prototyping, complex geometries, and customized tooling designs with reduced lead time and cost.
Why It's Important
3D printing is crucial for a Tool Designer as it allows for rapid prototyping, customization, and testing of tools, significantly reducing development time and costs while improving design flexibility and innovation.
How to Improve D Printing Skills
Improving 3D printing as a Tool Designer involves focusing on design optimization, material selection, and printing technology. Here are the key areas for enhancement:
Design Optimization: Utilize software to simulate and refine designs for better functionality and printability. Tools like Fusion 360 or SolidWorks are beneficial for creating efficient designs that reduce material usage and printing time.
Material Selection: Choose the appropriate material for the tool's intended use. Research materials for their strength, flexibility, and suitability for the end application. The 3D Printing Material Guide on 3D Hubs offers insights into different materials' properties.
Printing Technology: Select the correct 3D printing technology (e.g., FDM, SLA, SLS) based on the tool's complexity and required precision. Each technology has its pros and cons, described well in Formlabs' guide to Selecting the Right 3D Printing Process.
Post-Processing Techniques: Improve the finished product's surface finish and mechanical properties through post-processing. Techniques can vary widely, so consulting resources like the PostProcessing Guide by 3D Hubs can offer specific methods suited to your material and technology choice.
Continuous Learning and Experimentation: Stay updated with the latest advancements in 3D printing technologies, materials, and software. Engage with communities and forums (like r/3Dprinting) to share knowledge and learn from other professionals' experiences.
By focusing on these areas, a Tool Designer can significantly improve the quality, efficiency, and applicability of 3D printed tools.
How to Display D Printing Skills on Your Resume
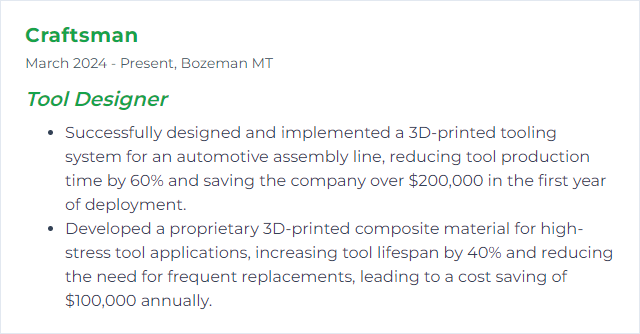
11. CNC Programming
CNC programming is the process of creating detailed instructions (code) for a CNC (Computer Numerical Control) machine, enabling it to perform precise cutting, milling, or drilling operations on a material as specified by a tool designer, to create or modify tools, dies, and molds.
Why It's Important
CNC programming is crucial for a Tool Designer as it enables the precise and efficient translation of tool designs into physical parts, ensuring accuracy, repeatability, and optimal material usage in manufacturing processes.
How to Improve CNC Programming Skills
Improving CNC programming, especially for a Tool Designer, involves enhancing efficiency, accuracy, and the quality of the machining process. Here are concise strategies:
Enhance Skills and Knowledge: Continuously update your knowledge about CNC programming languages (e.g., G-code), software updates, and machining techniques. Online courses and tutorials from platforms like Coursera and Udemy can be invaluable.
Utilize CAD/CAM Software Efficiently: Mastering CAD/CAM software allows for the efficient design and programming of machining processes. Explore software like Fusion 360 or Mastercam for advanced functionalities.
Simulation Software: Use simulation software to preemptively identify and correct errors in your CNC programs, saving time and resources. Tools like CGTech's VERICUT are industry standards for simulation.
Optimize Toolpaths: Improving the toolpath strategy can significantly reduce machining time and tool wear. Explore techniques like High-Efficiency Milling (HEM) and resources from specialized websites such as Modern Machine Shop.
Tool Selection and Management: Proper selection and management of cutting tools can drastically improve machining efficiency. Utilize tool management software and databases from suppliers like Sandvik Coromant for optimal tool selection.
Stay Updated with Industry Trends: Follow industry blogs, forums, and publications to stay informed about the latest trends and technologies in CNC programming and tool design. Websites like Practical Machinist offer a wealth of information and community advice.
Implement Lean Manufacturing Principles: Apply lean manufacturing techniques to the CNC programming process to minimize waste and improve productivity. The Lean Enterprise Institute offers resources on lean principles and practices.
By focusing on these areas, a Tool Designer can significantly improve their CNC programming skills, leading to more efficient and effective manufacturing processes.
How to Display CNC Programming Skills on Your Resume
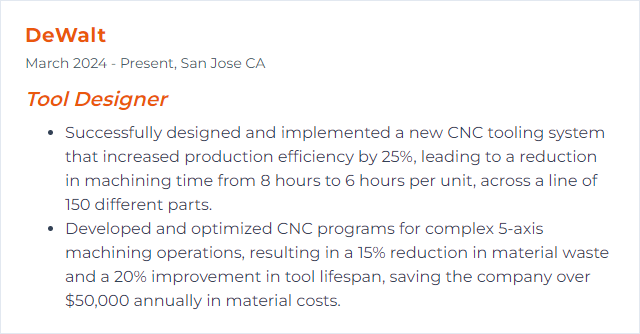
12. Injection Molding
Injection molding is a manufacturing process used to produce parts by injecting molten material into a mold, where it cools and solidifies into the final part shape. For a Tool Designer, it involves designing the molds (tools) required for the precise and efficient production of these parts, considering factors like material flow, cooling, and ejection mechanisms.
Why It's Important
Injection molding is important for a Tool Designer because it enables the mass production of precise, complex shapes with high repeatability, efficiency, and cost-effectiveness, crucial for meeting the demands of modern manufacturing and product development.
How to Improve Injection Molding Skills
Improving injection molding, from a Tool Designer's perspective, involves optimizing the mold design and manufacturing process to enhance product quality, efficiency, and performance. Here are concise strategies:
Optimize Mold Design: Use simulation software to predict and address potential defects. This involves optimizing gate location, runner systems, and cooling channels to ensure uniform material flow and cooling. Autodesk Moldflow offers comprehensive tools for simulation.
Material Selection: Choose appropriate mold materials and coatings that match the production volume and plastic material to minimize wear and corrosion. MatWeb provides a searchable database of material properties.
Enhance Cooling System: Design efficient cooling systems to reduce cycle times and improve part quality. The goal is to achieve uniform cooling for minimal distortion. ToolingDocs offers insights and training on mold maintenance, including cooling system efficiency.
Use Rapid Prototyping: Implement rapid prototyping techniques like 3D printing to quickly test and modify mold designs before final production. This can significantly reduce development time and costs. Stratasys is a leader in 3D printing solutions for tooling.
Incorporate Ejector System Efficiency: Design an ejector system that ensures smooth part ejection and minimizes cycle times, considering the size and location of ejector pins for balanced force distribution. HASCO provides a wide range of components for mold making.
Implement Preventive Maintenance: Establish a regular maintenance schedule for the mold to prevent defects and downtime. This includes cleaning, inspection, and lubrication of moving parts. MoldTrax offers maintenance management software specifically for molds.
Continuous Learning and Improvement: Stay updated with the latest trends, technologies, and methodologies in injection molding and mold design. Join forums, attend workshops, and participate in webinars. Society of Plastics Engineers is a great resource for continuous education in the plastics industry.
By focusing on these areas, tool designers can significantly contribute to improving the injection molding process, leading to more efficient operations and higher-quality products.
How to Display Injection Molding Skills on Your Resume
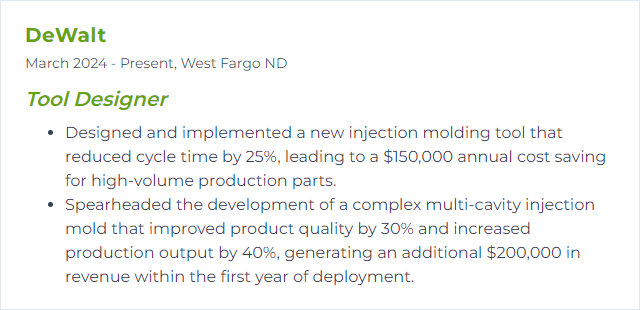