Top 12 Tool Maker Skills to Put on Your Resume
In today's highly competitive job market, showcasing the right set of skills on your resume can significantly enhance your chances of landing a position as a tool maker. A concise list of your top capabilities not only demonstrates your expertise in the field but also highlights your commitment to excellence and continuous learning in this specialized craft.
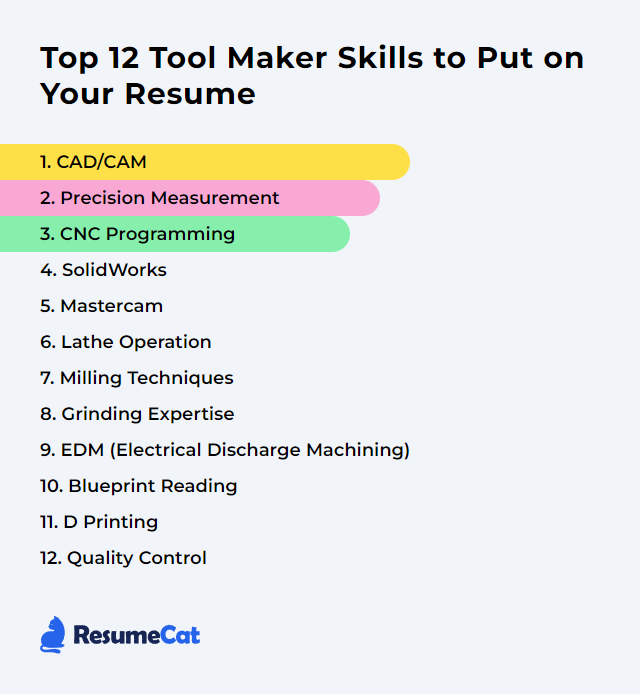
Tool Maker Skills
- CAD/CAM
- Precision Measurement
- CNC Programming
- SolidWorks
- Mastercam
- Lathe Operation
- Milling Techniques
- Grinding Expertise
- EDM (Electrical Discharge Machining)
- Blueprint Reading
- D Printing
- Quality Control
1. CAD/CAM
CAD/CAM stands for Computer-Aided Design and Computer-Aided Manufacturing. It refers to the use of computer software to both design parts (CAD) and automate the manufacturing processes (CAM), including planning, managing, and executing production operations. For a tool maker, CAD/CAM enables the precise design and efficient production of tools, molds, and dies, enhancing accuracy, reducing manual labor, and increasing productivity.
Why It's Important
CAD/CAM is crucial for a Tool Maker because it streamlines the design and manufacturing process, allowing for precise creation of complex tools and molds, reduces production time, and enhances overall efficiency and quality of the final products.
How to Improve CAD/CAM Skills
Improving CAD/CAM for a Tool Maker involves focusing on precision, efficiency, and integration of advanced technologies. Here are concise strategies:
Upgrade Software Regularly: Ensure you're using the latest version of your CAD/CAM software which often includes improvements in speed, capabilities, and bug fixes.
Utilize High-Quality Hardware: Invest in high-performance computing hardware that can handle complex models and simulations without lag.
Integrate Additive Manufacturing: Incorporate additive manufacturing techniques into your tool design and production process for complex geometries and reduced material waste.
Adopt Simulation Tools: Use simulation software to predict how designs will perform under real-world conditions, reducing the need for physical prototypes.
Continuous Learning: Stay updated with online courses and certifications on CAD/CAM advancements to leverage new features and methodologies effectively.
Implement Data Management Solutions: Use Product Data Management (PDM) systems to efficiently manage and track all versions of your CAD files and related documents.
Collaborate Closely: Foster a collaborative environment with easy-to-use collaboration tools for sharing designs and feedback seamlessly among team members.
Each of these steps contributes to enhancing the precision, speed, and quality of tool making processes, aligning them with current technological capabilities and industry standards.
How to Display CAD/CAM Skills on Your Resume
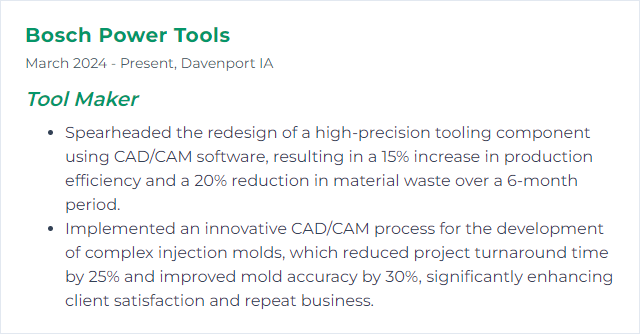
2. Precision Measurement
Precision measurement in the context of a tool maker refers to the use of highly accurate instruments and techniques to determine the dimensions, angles, or surface quality of parts and tools, ensuring they meet exact specifications with minimal error.
Why It's Important
Precision measurement is crucial for a Tool Maker to ensure the accuracy and quality of tools, achieve exact specifications, minimize errors, and maintain high standards in manufacturing processes.
How to Improve Precision Measurement Skills
To improve precision measurement as a Tool Maker, follow these concise strategies:
Calibration: Regularly calibrate your measuring instruments to maintain accuracy. Consider using calibration services accredited by recognized bodies.
Environmental Control: Maintain a stable environment (temperature, humidity) to reduce measurement errors. National Institute of Standards and Technology (NIST) provides guidelines on environmental conditions for precision measurement.
Proper Tool Selection: Use the right measurement tool for the task. Higher precision tools like micrometers or coordinate measuring machines (CMMs) offer greater accuracy than standard rulers or calipers.
Training: Ensure that you and any employees are properly trained in using measurement tools and understanding measurement techniques. MIT OpenCourseWare offers free courses that can improve understanding of measurement principles.
Use of Fixtures and Jigs: Employ fixtures and jigs to hold the part securely and in the correct orientation during measurement to improve repeatability and accuracy.
Minimize Handling: Reduce handling of the parts to be measured to prevent alteration of dimensions or introduction of contaminants.
Digital Tools: Where possible, use digital measurement tools with data output to reduce reading errors. Tools with digital readouts can directly interface with data collection systems to reduce human error.
Regular Maintenance: Keep all measuring tools and equipment well-maintained according to the manufacturer's recommendations to ensure sustained accuracy.
By implementing these strategies, you can significantly improve the precision of your measurements, leading to better quality and consistency in tool making.
How to Display Precision Measurement Skills on Your Resume
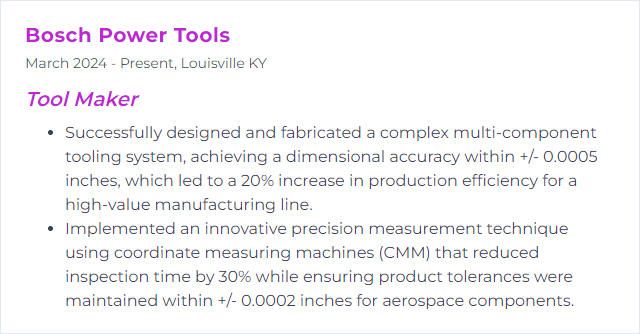
3. CNC Programming
CNC programming involves creating coded instructions that control the movements and operations of computer numerical control (CNC) machines to manufacture parts or products, tailored for tool makers to precisely cut, shape, and finish metal or other materials.
Why It's Important
CNC programming is crucial for a Tool Maker because it enables the precise and efficient creation of complex tools and components, ensuring high accuracy, repeatability, and productivity in the manufacturing process.
How to Improve CNC Programming Skills
Improving CNC Programming, especially for a Tool Maker, involves enhancing precision, efficiency, and adaptability. Here are concise strategies:
Master the Basics: Solidify your understanding of CNC fundamentals. MIT's Introduction to CNC Programming offers a comprehensive start.
Leverage CAD/CAM Software: Invest time in learning and utilizing advanced CAD/CAM software for more efficient programming. Fusion 360 is a popular choice for toolmakers.
Stay Updated with G-Code: Enhance your G-code proficiency by using resources like GCodeTutor, which offers tutorials and tips.
Optimize Toolpaths: Focus on optimizing toolpaths for efficiency and longevity of tools. Mastercam's Dynamic Motion technology is an example of how software can assist in this area.
Implement Simulation Software: Use simulation software to predict and prevent errors, saving time and resources. VERICUT is widely used for CNC machine simulation.
Continuous Learning and Adaptation: The field is always evolving. Platforms like Lynda.com (now LinkedIn Learning) offer courses on CNC and manufacturing technologies.
Implementing these strategies will significantly improve the efficiency, accuracy, and quality of CNC programming in tool making.
How to Display CNC Programming Skills on Your Resume
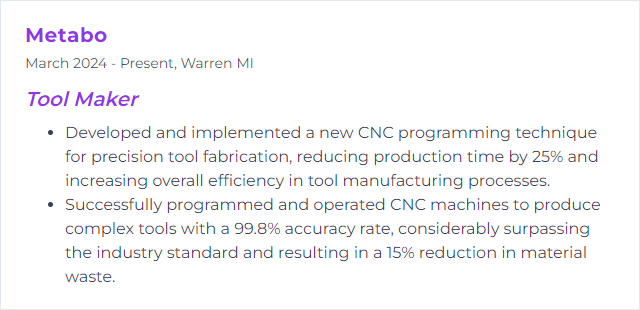
4. SolidWorks
SolidWorks is a computer-aided design (CAD) and engineering software used extensively by toolmakers for designing and simulating molds, dies, and other precision tools with 3D modeling capabilities, enabling detailed visualization, modification, and optimization of tool designs before manufacturing.
Why It's Important
SolidWorks is important for a Tool Maker because it enables precise 3D modeling and simulation of tools, facilitating design optimization, reducing errors, and streamlining the manufacturing process.
How to Improve SolidWorks Skills
Improving SolidWorks proficiency, especially for a Tool Maker, involves focusing on specific skills that enhance precision, efficiency, and the ability to handle complex designs. Here’s a concise guide:
Master Sketching and Part Modeling: Efficiently create detailed sketches and parts, focusing on accuracy and design intent. SolidWorks Tutorials offer step-by-step guidance.
Utilize Advanced Assembly Techniques: Learn to manage large assemblies for better performance and easier modifications. Assembly Tips can be particularly helpful.
Leverage Surface Modeling: For complex shapes and high-quality tooling designs, mastering surface modeling is crucial. Explore Surface Modeling Resources.
Understand Mold Design Tools: SolidWorks offers specialized tools for mold design. Familiarize yourself with them for efficient tool creation. Check out Mold Design.
Optimize with SolidWorks CAM: Integrate manufacturing processes early in design with SolidWorks CAM to ensure manufacturability and reduce production time. Learn through SolidWorks CAM Tutorials.
Stay Updated and Train Regularly: New features and updates can significantly improve efficiency. Keep your skills sharp with ongoing Training.
Participate in SolidWorks Forums: Engage with other professionals to share tips, tricks, and solutions. Visit SolidWorks Forums.
Customize Your Workspace: Tailor your SolidWorks environment to suit your workflow for increased productivity. Guidance can be found in Workspace Customization.
Each of these steps, supported by consistent practice and exploration of SolidWorks’ extensive resources, will contribute significantly to improving proficiency and efficiency as a Tool Maker using SolidWorks.
How to Display SolidWorks Skills on Your Resume
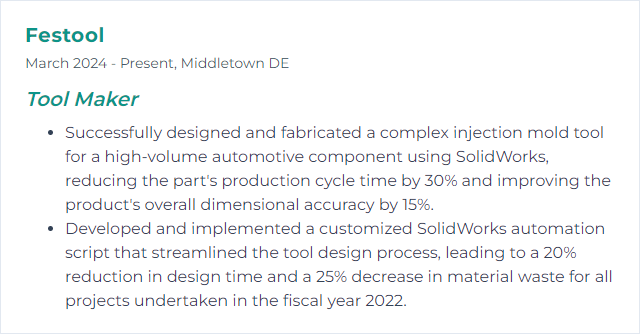
5. Mastercam
Mastercam is a computer-aided manufacturing (CAM) software program used by toolmakers and machinists to design and generate machining paths for milling, drilling, and turning processes in manufacturing tools, dies, and molds.
Why It's Important
Mastercam is important for a Tool Maker because it provides advanced CAD/CAM software solutions for designing, simulating, and manufacturing precise and efficient molds, dies, and other tooling components, enhancing productivity and ensuring high-quality outputs.
How to Improve Mastercam Skills
Improving your proficiency in Mastercam as a Tool Maker involves enhancing your skills in software operation, understanding machining processes deeply, and staying updated with the latest software updates and industry practices. Here are concise steps to improve in Mastercam:
Take Official Mastercam Training: Enroll in Mastercam University for official courses or find local training centers offering specialized tool making modules.
Practice Regularly: Hands-on experience is crucial. Set personal projects or practice with exercises from the Mastercam tutorials.
Join Forums and Communities: Engage with other professionals on platforms like the Mastercam Forum to share knowledge and solve challenges.
Stay Updated: Regularly check for software updates and new features on the Mastercam What's New page to ensure you're using the software to its full potential.
Learn from YouTube Tutorials: Subscribe to channels like Mastercam for visual learning on specific features and tips.
Read Relevant Books: Books like "Mastercam X8-X9 3D Advanced Mill" by MATTHEW MANCINI provide in-depth knowledge and practical exercises specific to tool making and advanced machining.
Utilize the Mastercam Tech Exchange: Visit the Mastercam Tech Exchange to download useful tool libraries, post processors, and project files.
By combining these resources and committing to continuous learning and practice, you can significantly improve your Mastercam skills tailored to tool making.
How to Display Mastercam Skills on Your Resume
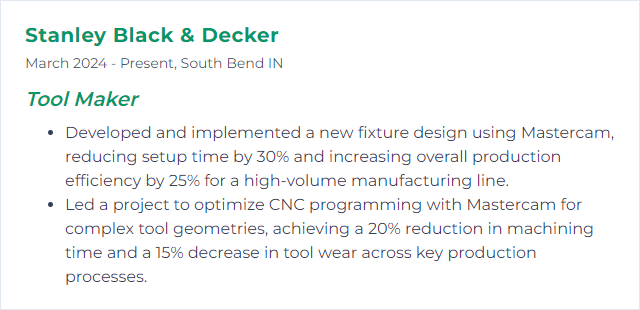
6. Lathe Operation
Lathe operation, for a tool maker, involves the precise machining of materials by rotating the workpiece against a cutting tool, enabling the creation or modification of parts with cylindrical shapes and detailed features.
Why It's Important
Lathe operation is essential for a Tool Maker as it enables precise shaping, cutting, and finishing of metal components, crucial for creating accurate and high-quality tools and dies.
How to Improve Lathe Operation Skills
Improving lathe operation, especially for a tool maker, involves a blend of technique, tool maintenance, and process optimization. Here are concise steps to enhance lathe operation:
Select Appropriate Tools: Choose the right cutting tools for the material and job. High-quality, purpose-specific tools reduce wear and improve precision.
Maintain Sharp Tools: Regularly sharpen lathe tools to ensure clean cuts and reduce material wastage.
Optimize Cutting Parameters: Adjust speed, feed, and depth of cut according to the material and desired outcome. Use manufacturers' guidelines or machining calculators to fine-tune these parameters.
Use Coolants Appropriately: Proper use of coolants can extend tool life and improve surface finish. Selecting the right coolant and application method is key.
Minimize Tool Overhang: Keep the tool overhang as short as possible to reduce vibration and improve stability.
Regularly Check Alignment: Ensure the lathe and its components are properly aligned. Misalignment can lead to inaccuracies and tool wear. Machine alignment is critical for precision.
Practice Proper Lubrication: Regular and correct lubrication of lathe parts prevents wear and tear, enhancing the machine's lifespan and operation efficiency.
Implement Process Control: Use micrometers and other measuring tools to consistently check the workpiece against specifications. This quality control ensures standards are met and reduces rework.
By focusing on these areas, tool makers can significantly improve the efficiency, accuracy, and outcome of lathe operations.
How to Display Lathe Operation Skills on Your Resume
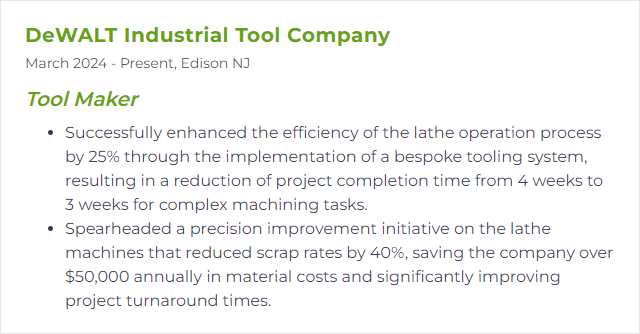
7. Milling Techniques
Milling techniques for a tool maker involve the use of cutting machines to shape metal parts with precision. These techniques include selecting appropriate cutting tools, speeds, and feeds to remove material efficiently, achieving desired shapes, surfaces, and features on workpieces. Key methods include face milling, peripheral milling, and end milling, tailored to create slots, contours, and complex geometries with accuracy.
Why It's Important
Milling techniques are crucial for a Tool Maker as they enable precise shaping and cutting of materials to create or modify tools and parts with high accuracy, ensuring optimal performance and longevity of the tools produced.
How to Improve Milling Techniques Skills
To enhance milling techniques as a tool maker, focus on the following strategies:
Optimize Cutting Parameters: Adjust cutting speed, feed rate, and depth of cut to balance efficiency and surface finish. Sandvik Coromant offers insights on parameter optimization.
Tool Selection: Use the correct end mill type and material for the job. Harvey Performance Company provides guidance on selecting the right tool.
Tool Path Strategies: Implement advanced toolpath strategies like trochoidal milling or High Efficiency Milling (HEM) to reduce load on the tool. Autodesk has resources on toolpath strategies.
Coolant Use: Properly apply coolant to improve tool life and part finish. MachiningCloud advises on coolant practices.
Machine Maintenance: Regularly maintain your milling machine to ensure precision. Haas Automation offers maintenance tips.
Rigidity: Increase work holding and tool holding rigidity to improve precision and finish. Big Kaiser specializes in high-precision tool holders.
By focusing on these areas, tool makers can significantly improve their milling techniques.
How to Display Milling Techniques Skills on Your Resume
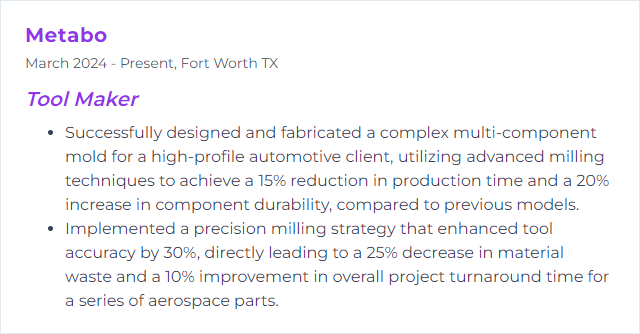
8. Grinding Expertise
Grinding Expertise, in the context of a Tool Maker, refers to the specialized knowledge and skill in using grinding machines and techniques to shape, sharpen, and finish tools and components with precision and accuracy.
Why It's Important
Grinding expertise is crucial for a Tool Maker as it ensures the precision and quality of tools, enhancing their performance and lifespan by achieving exact dimensions and fine finishes critical for their intended applications.
How to Improve Grinding Expertise Skills
To improve Grinding Expertise as a Tool Maker:
Understand the Basics: Grasp the fundamentals of grinding processes, materials, and machinery. Tooling U-SME offers courses that cover these essentials.
Learn from Experts: Watch tutorial videos and read articles from experienced toolmakers. Websites like Practical Machinist provide a wealth of knowledge through forums and expert columns.
Practice Safety: Always prioritize safety by following guidelines from OSHA on grinding operations.
Experiment with Materials: Work with various materials to understand their properties and how they affect grinding processes. ASM International has resources on material properties.
Use Simulation Software: Utilize CAD/CAM software to simulate and plan your grinding processes before actual implementation. Autodesk offers tools that can help in planning and simulation.
Attend Workshops and Seminars: Keep an eye out for industry workshops and seminars. Websites like Eventbrite can be a source to find relevant events.
Practice and Reflect: Regularly practice your skills and reflect on your progress and areas of improvement. Keep a journal or log of your experiences to track your development over time.
By combining these strategies, you can steadily improve your grinding expertise in toolmaking.
How to Display Grinding Expertise Skills on Your Resume
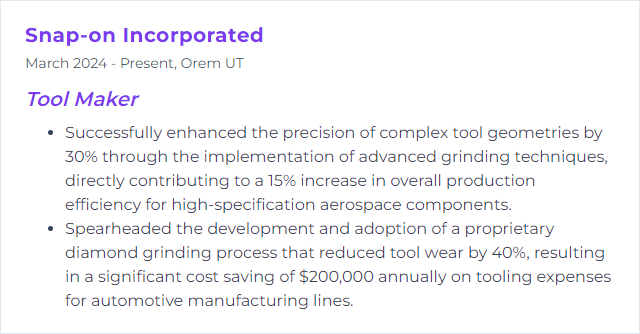
9. EDM (Electrical Discharge Machining)
EDM (Electrical Discharge Machining) is a manufacturing process that uses electrical discharges or sparks to remove material from a workpiece, creating precise shapes and intricate details. It is particularly useful for tool makers in machining complex or hard materials that are difficult to shape with traditional techniques.
Why It's Important
EDM (Electrical Discharge Machining) is important for a Tool Maker because it allows for the precise machining of complex shapes and hard materials that are difficult to work with using traditional machining methods, enhancing tool quality and functionality.
How to Improve EDM (Electrical Discharge Machining) Skills
Improving EDM (Electrical Discharge Machining) involves several key strategies aimed at enhancing efficiency, precision, and surface quality. Here's a concise guide for a Tool Maker:
Optimize Parameters: Adjust pulse duration, current, and voltage to suit the material and desired outcome. Optimizing EDM Parameters offers insights into parameter adjustment.
Use High-Quality Electrodes: Select appropriate electrode materials and ensure they are manufactured to high standards for better performance and durability. Electrode Material Selection provides guidelines on choosing the right materials.
Maintain Fluids: Regularly replace and maintain dielectric fluids to improve cutting efficiency and prevent contamination. Dielectric Fluid Management outlines best practices for fluid management.
Implement Advanced Technologies: Consider technologies like AI and CAD/CAM integration for improved accuracy and reduced setup time. AI in EDM discusses the application of artificial intelligence in EDM optimization.
Routine Maintenance: Regularly check and maintain machinery to prevent breakdowns and ensure consistent performance. EDM Maintenance Tips highlights essential maintenance practices.
Train and Update Skills: Continuously train to stay updated on the latest EDM technologies and techniques. EDM Training Resources offer opportunities for skill enhancement.
By focusing on these areas, a Tool Maker can significantly improve EDM processes, leading to better quality, efficiency, and productivity.
How to Display EDM (Electrical Discharge Machining) Skills on Your Resume
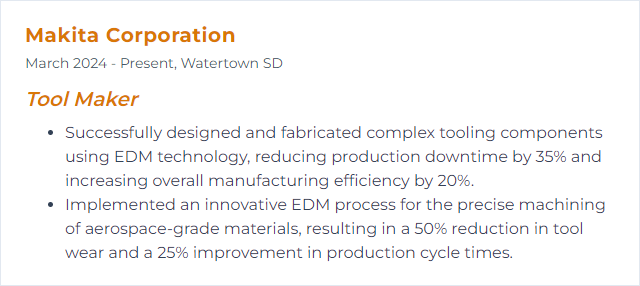
10. Blueprint Reading
Blueprint reading for a Tool Maker involves interpreting detailed technical drawings and diagrams that outline the specifications, dimensions, and processes required to manufacture tools and parts. It includes understanding symbols, measurements, and material specifications to accurately produce or modify tools as designed.
Why It's Important
Blueprint reading is crucial for a Tool Maker as it enables the precise interpretation of engineering designs and specifications necessary for accurately manufacturing, assembling, and repairing tools, ensuring they meet exacting standards and function correctly.
How to Improve Blueprint Reading Skills
Improving blueprint reading skills, especially for a Tool Maker, involves understanding geometric tolerances, symbols, and conventions specific to tool design and manufacturing. Here are concise steps with resources for enhancing these skills:
Learn the Basics: Familiarize yourself with the foundational knowledge of blueprint reading, including understanding scales, lines, and symbols commonly used. Tooling U-SME offers a variety of courses that cater to the basics of blueprint reading.
Study Geometric Dimensioning and Tolerancing (GD&T): GD&T is crucial for precision in tool making. ASME's GD&T Training provides comprehensive resources.
Practice with Real Blueprints: Apply your knowledge by interpreting real tool design blueprints. Engineering Drawings has a collection for practice.
Join Online Forums and Groups: Engage with communities such as Practical Machinist where you can ask questions, share insights, and learn from experienced professionals.
Continuous Learning: Stay updated with new standards and technologies in tool making and blueprint reading by following relevant publications and websites like Modern Machine Shop.
By following these steps and utilizing the provided resources, you can significantly improve your blueprint reading skills tailored to tool making.
How to Display Blueprint Reading Skills on Your Resume
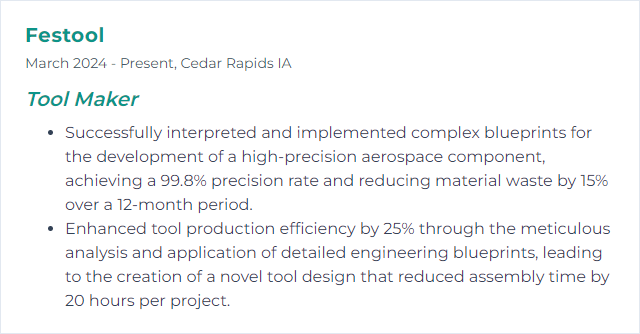
11. D Printing
D Printing, likely a typo for 3D Printing, is a manufacturing process that creates physical objects from digital designs by layering materials. For a Tool Maker, it offers rapid prototyping, custom tool production, and the ability to create complex shapes that are difficult or impossible to achieve with traditional manufacturing methods.
Why It's Important
3D printing is important for a Tool Maker because it allows for rapid prototyping, customization, and production of complex tools with high precision, reducing both the time and cost involved in tool manufacturing.
How to Improve D Printing Skills
Improving 3D printing, especially for a Tool Maker, involves enhancing precision, material compatibility, and printing speed. Focus on these key areas:
Precision: Upgrade to high-resolution printers and use software like Cura for better slicing accuracy. Calibrate your printer regularly.
Material Compatibility: Invest in printers capable of handling a variety of materials. Explore advanced materials and their applications through resources like 3D Printing Industry’s material guide.
Speed: Optimize your printer settings for faster printing without compromising quality. Techniques and tips can be found at All3DP.
By focusing on these aspects, a Tool Maker can significantly enhance their 3D printing capabilities, leading to more efficient and higher quality tool production.
How to Display D Printing Skills on Your Resume
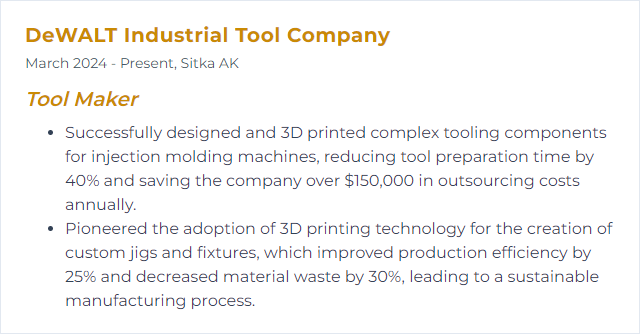
12. Quality Control
Quality control for a Tool Maker involves systematically monitoring and evaluating the production processes and finished tools to ensure they meet specified quality standards and requirements.
Why It's Important
Quality control is important for a Tool Maker to ensure tools meet precise specifications, guarantee consistent performance, reduce manufacturing errors, and maintain customer satisfaction by delivering reliable and high-quality products.
How to Improve Quality Control Skills
Improving Quality Control (QC) for a Tool Maker involves several focused strategies aimed at enhancing the precision, efficiency, and reliability of the tools produced. Here’s a concise guide:
Implement Standardized Procedures: Adopt ISO 9001 standards to ensure consistent quality and continuous improvement in your processes.
Regular Training: Ensure your team is up-to-date with the latest techniques and technologies through continuous training programs.
Adopt Lean Manufacturing: Integrate Lean manufacturing principles to minimize waste and optimize production efficiency, directly impacting quality.
Utilize Precision Equipment: Invest in high-quality, precision manufacturing equipment to enhance the accuracy and reliability of your tools.
Perform Routine Inspections: Conduct regular inspections and testing of tools to identify and correct defects early in the manufacturing process.
Feedback Loops: Establish a system for collecting and analyzing customer feedback to continuously improve product quality based on user experience.
Quality Control Software: Utilize QC software to efficiently manage and analyze quality data, improving decision-making and traceability.
By focusing on these areas, a Tool Maker can significantly enhance their Quality Control processes, leading to the production of superior tools and higher customer satisfaction.
How to Display Quality Control Skills on Your Resume
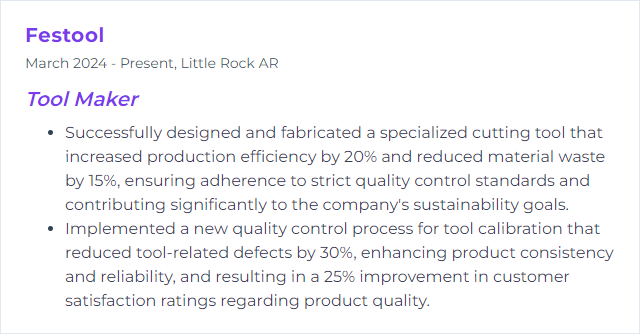