Top 12 Quality Control Analyst Skills to Put on Your Resume
In the competitive field of quality control, showcasing a robust set of skills on your resume can significantly enhance your marketability to potential employers. A well-crafted list of quality control analyst skills demonstrates your expertise and readiness to ensure products meet the highest standards of excellence and safety.
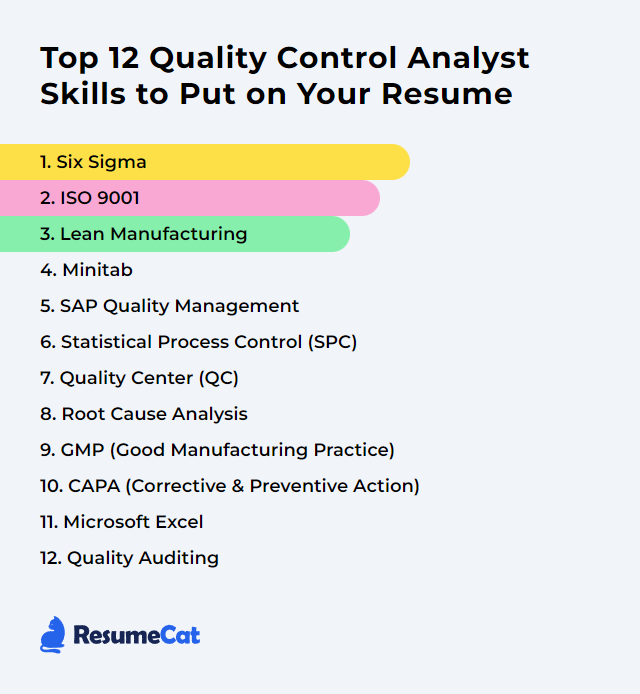
Quality Control Analyst Skills
- Six Sigma
- ISO 9001
- Lean Manufacturing
- Minitab
- SAP Quality Management
- Statistical Process Control (SPC)
- Quality Center (QC)
- Root Cause Analysis
- GMP (Good Manufacturing Practice)
- CAPA (Corrective and Preventive Action)
- Microsoft Excel
- Quality Auditing
1. Six Sigma
Six Sigma is a data-driven, methodology aimed at improving business processes by minimizing defects and variability in manufacturing and business operations, focusing on quality control and continuous improvement. For a Quality Control Analyst, it involves using statistical tools to analyze and improve product quality, efficiency, and effectiveness.
Why It's Important
Six Sigma is important for a Quality Control Analyst as it provides a systematic and data-driven methodology for reducing defects, improving processes, and enhancing quality, ultimately leading to increased customer satisfaction and reduced costs.
How to Improve Six Sigma Skills
Improving Six Sigma as a Quality Control Analyst involves enhancing your understanding and application of its methodologies to optimize processes, reduce defects, and ensure quality control. Here are concise steps for improvement:
Educate Yourself Further: Deepen your knowledge in Six Sigma methodologies by pursuing higher belts or specialized courses. ASQ’s Six Sigma Training offers comprehensive resources.
Apply DMAIC Rigorously: Ensure strict adherence to the DMAIC (Define, Measure, Analyze, Improve, Control) framework in every project to systematically improve processes. iSixSigma provides detailed insights on DMAIC.
Leverage Statistical Tools: Master statistical tools and software like Minitab for data analysis to identify process improvements. Explore resources at Minitab’s Support for learning.
Enhance Soft Skills: Improve communication, leadership, and problem-solving skills to effectively lead projects and teams. MindTools offers valuable resources on leadership and communication.
Stay Updated: Keep abreast of the latest trends and innovations in Six Sigma and quality control by regularly visiting industry-leading websites, such as Quality Magazine.
Participate in Forums: Engage in Six Sigma forums and communities to exchange ideas, solve problems, and share best practices. The Lean Six Sigma Community is a great platform.
Real-world Application: Apply Six Sigma projects in real-world scenarios within your organization to solve actual problems, thus gaining practical experience and showcasing your skills.
Mentorship and Networking: Seek mentorship from Six Sigma Black Belts or Master Black Belts and network with professionals through platforms like LinkedIn.
By focusing on these areas, a Quality Control Analyst can significantly improve their Six Sigma proficiency, leading to enhanced quality control and process efficiency within their organization.
How to Display Six Sigma Skills on Your Resume
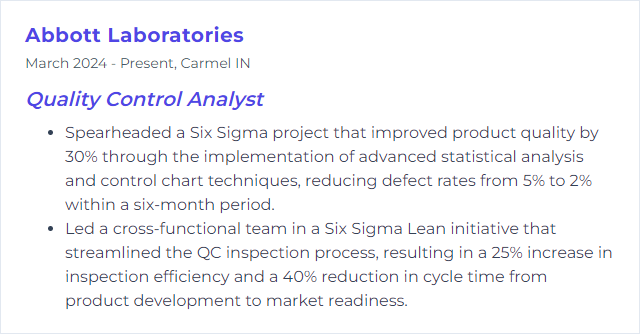
2. ISO 9001
ISO 9001 is an international standard that specifies requirements for a quality management system (QMS). Organizations use the standard to demonstrate their ability to consistently provide products and services that meet customer and regulatory requirements. For a Quality Control Analyst, it provides a framework and set of principles to ensure product quality and continuous improvement in processes.
Why It's Important
ISO 9001 is important because it provides a framework for consistent quality management practices, ensuring products and services meet customer and regulatory requirements, enhancing customer satisfaction and continuous improvement in processes, which is crucial for a Quality Control Analyst to maintain high standards of quality assurance.
How to Improve ISO 9001 Skills
Improving ISO 9001 within the context of a Quality Control Analyst role entails a focus on continuous process enhancement, effective documentation, and active engagement in the quality management system (QMS). Here are concise steps for improvement:
Engage in Continuous Learning: Stay updated on the latest quality control techniques, ISO 9001 revisions, and industry best practices. The ASQ (American Society for Quality) offers resources and training courses that can be beneficial.
Enhance Documentation: Ensure all processes, anomalies, and corrective actions are thoroughly documented. Utilize ISO 9001 Quality Management Systems as a guideline to maintain and improve documentation standards.
Implement a Robust Feedback Loop: Actively seek feedback from internal and external stakeholders to identify areas for improvement. Tools such as SurveyMonkey can facilitate gathering this feedback.
Conduct Regular Audits: Perform regular internal audits to assess compliance with ISO 9001 standards and identify areas for improvement. The ISO 19011:2018 provides guidelines for auditing management systems.
Foster a Culture of Quality: Encourage a company-wide culture that prioritizes quality and continuous improvement. Involvement in forums like Elsmar Cove Quality Assurance and Business Standards Discussions can provide insights and strategies for fostering this culture.
Utilize Quality Management Tools: Adopt various quality management tools and techniques such as Six Sigma, Kaizen, and 5S methodology to drive improvements. The iSixSigma portal offers extensive resources on these methodologies.
Improve Communication: Ensure clear and concise communication within the team and with other departments regarding quality standards, objectives, and performance. Tools like Slack can enhance team communication.
Leverage Technology for Quality Improvement: Implement quality management software systems that align with ISO 9001 requirements to streamline processes and maintain quality standards. Intelex and Qualio are examples of software that can support these efforts.
Engaging in these practices not only improves the QMS but also contributes to the overall performance and competitiveness of the organization.
How to Display ISO 9001 Skills on Your Resume
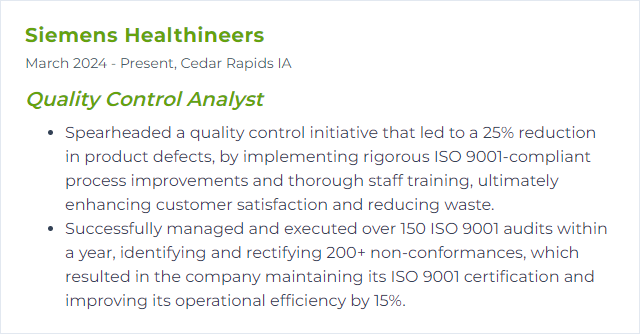
3. Lean Manufacturing
Lean Manufacturing is a systematic approach to minimizing waste within manufacturing systems while maximizing productivity, aimed at enhancing quality and efficiency, thereby directly impacting the work of a Quality Control Analyst by streamlining processes for improved product consistency and reduced defects.
Why It's Important
Lean Manufacturing is important for a Quality Control Analyst because it emphasizes reducing waste, improving quality, and enhancing efficiency in production processes, leading to higher product quality and customer satisfaction.
How to Improve Lean Manufacturing Skills
Improving Lean Manufacturing, especially from a Quality Control Analyst perspective, involves focusing on reducing waste, enhancing quality, and streamlining processes to deliver value to customers efficiently. Here are concise strategies:
Implement Continuous Improvement (Kaizen): Foster a culture of ongoing improvement where every team member, including those in quality control, actively seeks ways to enhance processes. Kaizen Institute offers insights on implementing this principle.
Utilize the 5S System: Streamline the workplace environment (Sort, Set in order, Shine, Standardize, Sustain) to reduce errors and improve safety and efficiency. This directly supports quality control efforts. Lean Production provides a detailed explanation.
Apply the Six Sigma Methodology: Although distinct from Lean, integrating Six Sigma can significantly improve quality by reducing variability and defects. Quality control analysts can use its tools for process improvements. ASQ Six Sigma is a valuable resource.
Standardize Work Processes: Develop and follow standardized work procedures to ensure consistency, which is key to maintaining high quality. This includes detailed documentation and training for all relevant employees. Lean Enterprise Institute discusses the importance of standard work.
Leverage Technology and Data Analysis: Implement quality management systems (QMS) and utilize data analytics for real-time monitoring and improvement of manufacturing processes. This approach allows for identifying trends and preventing defects before they occur. LNS Research often covers advancements in QMS and analytics.
Root Cause Analysis (RCA): Empower the quality control team to conduct thorough RCA using tools such as the 5 Whys or Fishbone Diagrams to eliminate the sources of defects or process inefficiencies. ASQ Problem Solving provides techniques and tools.
Engage in Supplier Quality Management: Ensure suppliers adhere to quality standards and work collaboratively to improve materials and components quality, impacting the overall product quality. ISM offers resources on supplier management.
Cross-Functional Team Collaboration: Promote teamwork between quality control, production, and other departments to foster a holistic approach to lean manufacturing and quality improvement. Smartsheet highlights the benefits of cross-functional collaboration.
By embracing these strategies, a Quality Control Analyst can significantly contribute to the enhancement of Lean Manufacturing practices, leading to improved product quality, efficiency, and customer satisfaction.
How to Display Lean Manufacturing Skills on Your Resume
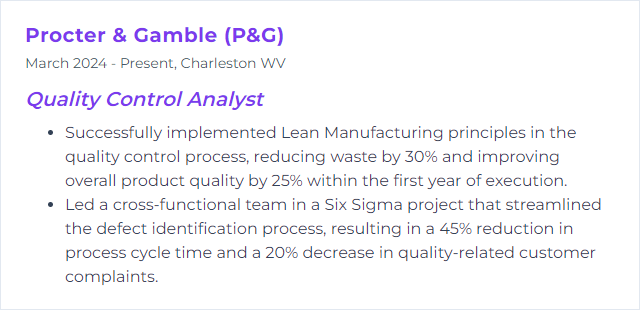
4. Minitab
Minitab is a statistical software package widely used by quality control analysts for analyzing data, performing statistical quality control, and facilitating process and product improvement through various tools such as control charts, regression analysis, and design of experiments.
Why It's Important
Minitab is important for a Quality Control Analyst because it provides powerful statistical analysis, graphical tools, and detailed reports to identify trends, solve problems, and improve processes, ensuring product quality and consistency.
How to Improve Minitab Skills
Improving your proficiency with Minitab as a Quality Control Analyst involves a combination of enhancing your statistical analysis skills, understanding the specific tools Minitab offers for quality control, and continuously updating your knowledge with the latest features and best practices. Here are concise steps to achieve that:
Master the Basics: Ensure you have a strong foundation in the statistical methods that are commonly used in quality control. Minitab offers a free resource center with tutorials and case studies.
Understand Minitab's Quality Tools: Dive deep into tools specifically designed for quality control such as Control Charts, Capability Analysis, and Design of Experiments. Minitab's official blog provides insights and examples on using these tools effectively.
Get Certified: Consider obtaining a Minitab certification to validate your skills. Details about certification and training can be found on the Minitab Training page.
Join Forums and Communities: Engage with other Minitab users in forums and communities. The Minitab Community is a place to ask questions, share knowledge, and connect with peers.
Keep Updated with New Features: Minitab regularly updates its software. Stay informed about new features and improvements by checking the Minitab Release Notes.
Practice: Apply what you learn in real-world scenarios. The more you use Minitab for actual quality control projects, the better you will understand its capabilities and limitations.
Incorporating these steps into your professional development will enhance your efficiency and effectiveness as a Quality Control Analyst using Minitab.
How to Display Minitab Skills on Your Resume
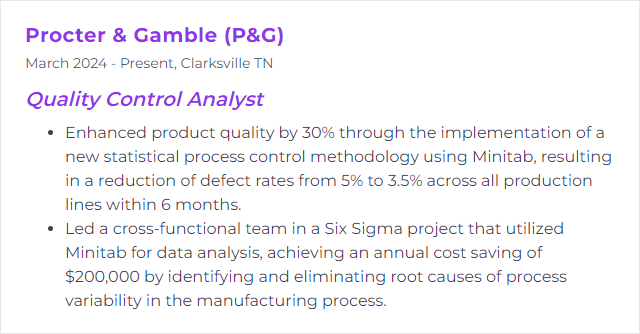
5. SAP Quality Management
SAP Quality Management (QM) is a component of the SAP ERP system designed to help businesses manage their quality control processes. It supports tasks such as planning, inspection, and control of products and processes to ensure compliance with quality standards, facilitating defect identification, and implementation of corrective actions for Quality Control Analysts.
Why It's Important
SAP Quality Management is important because it ensures consistent quality in products and processes by integrating quality control measures across the production lifecycle, enabling Quality Control Analysts to identify and mitigate defects, ensure compliance with standards, and maintain customer satisfaction efficiently.
How to Improve SAP Quality Management Skills
Improving SAP Quality Management (QM) involves streamlining processes, enhancing data quality, and leveraging SAP's capabilities effectively. Here's a concise guide for a Quality Control Analyst:
Streamline Inspection Processes: Utilize SAP's QM module to standardize inspection procedures. This ensures consistency and efficiency in quality checks. SAP Inspection Lot Processing provides a comprehensive guide.
Leverage Data Analytics: Use SAP Analytics Cloud to analyze quality data. This helps in identifying trends and areas for improvement. SAP Analytics Cloud offers insights.
Automate Quality Notifications: Implement automation for creating and managing quality notifications. This speeds up the resolution of issues. Quality Notifications in SAP details the process.
Enhance Skills Through Training: Invest in SAP QM training for the team. Knowledge of advanced features and best practices ensures more effective use of the system. SAP Training and Certification offers various courses.
Integrate with Other Modules: Ensure seamless integration with other SAP modules like Material Management (MM) and Production Planning (PP) for a holistic approach to quality. SAP Module Integration provides an overview.
Regularly Update Your SAP System: Keep your SAP system up-to-date with the latest updates and patches. This ensures you have access to the latest features and security improvements. SAP Support Portal is the place to start.
Feedback Loop: Establish a feedback loop with stakeholders to continuously collect and incorporate feedback on quality management practices. This helps in making iterative improvements to processes.
By focusing on these areas, a Quality Control Analyst can significantly improve the efficiency and effectiveness of SAP Quality Management within their organization.
How to Display SAP Quality Management Skills on Your Resume
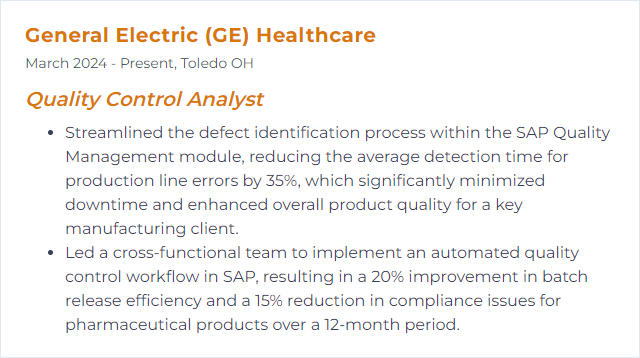
6. Statistical Process Control (SPC)
Statistical Process Control (SPC) is a method used by Quality Control Analysts to monitor and control a process using statistical techniques, ensuring that it operates at its full potential to produce consistent, high-quality products. It involves collecting and analyzing data to detect and prevent deviations from the production process, aiming to reduce variability and improve efficiency.
Why It's Important
Statistical Process Control (SPC) is crucial for a Quality Control Analyst as it enables the monitoring and control of process variability, ensuring product quality consistency, and identifying areas for process improvement, thereby reducing waste and increasing customer satisfaction.
How to Improve Statistical Process Control (SPC) Skills
Improving Statistical Process Control (SPC) can significantly enhance quality control processes. Here are concise steps tailored for a Quality Control Analyst:
Education and Training: Invest in continuous education and training in SPC techniques and tools for yourself and your team. Understanding the fundamentals and advanced concepts of SPC is crucial. ASQ’s Training Courses offer comprehensive insights.
Data Collection and Management: Ensure accurate and consistent data collection methods. Use software that facilitates real-time data capture and analysis. Minitab is widely recognized for its statistical analysis capabilities.
Process Mapping: Identify and map out all processes. This helps in understanding the flow and identifying areas of improvement. Lucidchart is a useful tool for creating process maps.
Implement SPC Charts: Utilize SPC charts like control charts to monitor process stability. This helps in early detection of variations. Learn to interpret these charts correctly to make informed decisions.
Root Cause Analysis: When variations are detected, use root cause analysis techniques to identify the underlying reasons. Tools like the 5 Whys or Fishbone Diagram are effective. MindTools provides a good overview of these techniques.
Continuous Improvement: Adopt a Kaizen or continuous improvement mindset. Regularly review processes, identify inefficiencies, and implement improvements. The Kaizen Institute offers resources and training on adopting Kaizen principles.
Leverage Technology: Use advanced SPC software that offers real-time monitoring, analysis, and reporting capabilities. Statistical Process Control Software by InfinityQS is designed to improve quality and reduce costs.
Collaboration and Communication: Foster a culture of open communication and collaboration within your team and across departments. Engage everyone in quality initiatives for collective success.
By focusing on these areas, a Quality Control Analyst can significantly improve the effectiveness of SPC in their organization, leading to enhanced product quality and operational efficiency.
How to Display Statistical Process Control (SPC) Skills on Your Resume
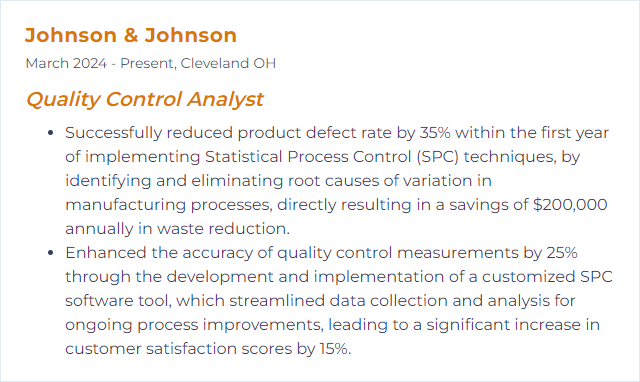
7. Quality Center (QC)
Quality Center (QC), also known as HP ALM (Application Life Cycle Management), is a comprehensive test management tool used by Quality Control Analysts for planning, executing, and tracking software testing processes. It facilitates requirements management, test planning, test execution, defect tracking, and reporting, aimed at ensuring software quality and reliability.
Why It's Important
Quality Center (QC) is important for a Quality Control Analyst because it centralizes test management, enhances defect tracking, and facilitates seamless communication within teams, ensuring higher product quality and reliability.
How to Improve Quality Center (QC) Skills
Improving Quality Center (QC) effectiveness involves optimizing processes, enhancing skills, and leveraging technology. Here are concise strategies:
Streamline Test Management: Consolidate test cases, requirements, and defects in one place for better visibility and control. Utilize HP ALM (Application Lifecycle Management) to integrate all aspects of the testing lifecycle.
Automate Testing: Implement automated testing tools to increase test coverage and efficiency. Tools like UFT (Unified Functional Testing) can automate functional and regression testing tasks.
Enhance Reporting: Use QC's reporting and analytics features to generate insightful reports. Customized dashboards can provide real-time visibility into quality metrics. Explore QC reporting capabilities for more.
Implement Best Practices: Adopt industry best practices for test management, such as test case reuse, proper test environment configuration, and regular review cycles. The ISTQB (International Software Testing Qualifications Board) offers guidelines and certifications.
Continuous Learning: Stay updated with the latest QC features and testing methodologies. Micro Focus offers Quality Center training and certification programs.
Feedback Loop: Establish a feedback loop with stakeholders to continuously improve test processes based on the team's and users' experiences.
Integrate with Other Tools: Leverage QC's integration capabilities with other tools (e.g., JIRA for issue tracking) to enhance collaboration and efficiency. Check out the Micro Focus Marketplace for integrations.
By focusing on these areas, a Quality Control Analyst can significantly improve the effectiveness and efficiency of Quality Center in their organization.
How to Display Quality Center (QC) Skills on Your Resume
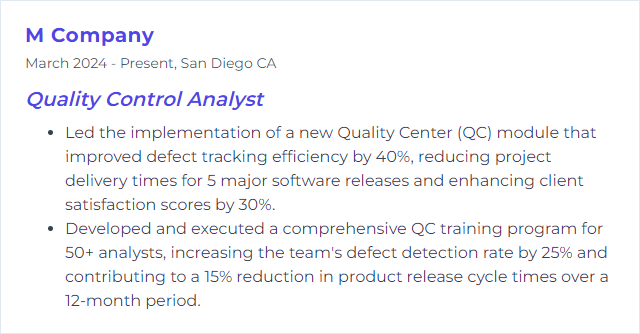
8. Root Cause Analysis
Root Cause Analysis (RCA) is a methodical approach used by Quality Control Analysts to identify the underlying reasons for defects or problems in a process or product, aiming to implement solutions that prevent recurrence.
Why It's Important
Root Cause Analysis (RCA) is crucial for a Quality Control Analyst because it enables the identification and resolution of the fundamental issues causing defects or failures in products or processes, thereby ensuring quality improvement, minimizing errors, and enhancing customer satisfaction.
How to Improve Root Cause Analysis Skills
Improving Root Cause Analysis (RCA) involves a systematic process aimed at identifying the underlying reasons for a problem or defect in Quality Control. Here's a very short and concise strategy:
Define the Problem Clearly: Begin with a clear, concise statement of the issue, focusing on specific symptoms. ASQ's problem statement guidance offers insights into formulating a precise problem statement.
Use Structured Methodologies: Utilize structured RCA methods such as the 5 Whys, Fishbone Diagram (Ishikawa), or Failure Mode and Effects Analysis (FMEA). Each method offers a different approach to trace the problem back to its root cause. Learn more about these methods from MindTools.
Gather and Analyze Data: Collect data related to the problem to identify patterns or anomalies. Quantitative analysis can be complemented with tools such as Pareto Charts, which are explained in ASQ's Pareto Chart guide.
Engage the Team: Collaborate with team members who have direct knowledge about the process or system in question. Diverse perspectives can often illuminate overlooked aspects of a problem. Harvard Business Review's article on teamwork emphasizes the value of collaboration in solving complex problems.
Implement and Monitor Solutions: After identifying the root cause(s), develop and implement corrective actions. It's critical to monitor these solutions over time to ensure they effectively resolve the issue. The Project Management Institute offers strategies on creating effective corrective action plans.
Review and Reflect: Regularly review the RCA process and its outcomes to identify opportunities for improvement. Continuous learning from each RCA can enhance future analyses.
By following these steps and leveraging the resources provided, Quality Control Analysts can refine their RCA processes, leading to more effective problem-solving and continuous improvement in quality control efforts.
How to Display Root Cause Analysis Skills on Your Resume
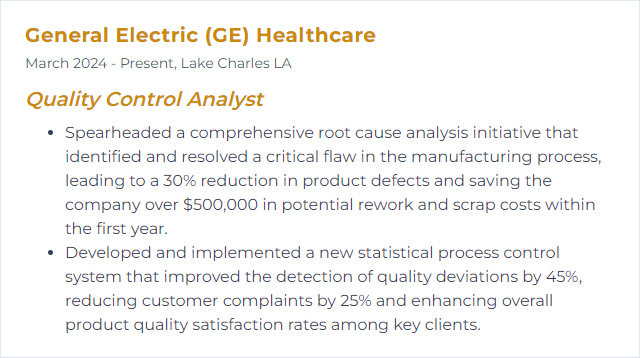
9. GMP (Good Manufacturing Practice)
GMP (Good Manufacturing Practice) is a system for ensuring that products are consistently produced and controlled according to quality standards. For a Quality Control Analyst, GMP involves adhering to strict procedures and documentation processes to guarantee the quality, safety, and efficacy of products, from raw materials to finished goods.
Why It's Important
GMP ensures products are consistently produced and controlled according to quality standards, minimizing risks involved in pharmaceutical production that cannot be eliminated through testing the final product. For a Quality Control Analyst, GMP is crucial as it provides a structured environment for testing, ensuring reliability and accuracy in results, thereby safeguarding consumer health.
How to Improve GMP (Good Manufacturing Practice) Skills
Improving Good Manufacturing Practice (GMP) as a Quality Control Analyst involves several key steps focused on ensuring product quality and safety. Here are concise strategies:
Stay Updated with Regulations: Regularly review and stay current with the latest GMP regulations and guidelines from authoritative sources like the FDA or EMA.
Continuous Training: Invest in ongoing training programs for yourself and your team to keep everyone updated on best practices and regulatory requirements.
Implement Quality Management Systems (QMS): Utilize comprehensive QMS tools that align with GMP standards to manage documentation, processes, and quality control measures effectively. Tools like MasterControl can be particularly useful.
Conduct Regular Audits: Routinely perform internal audits and gap analyses to identify areas for improvement. Utilize the findings to enhance processes and ensure compliance. Resources like ASQ can guide effective audit practices.
Foster a Culture of Quality: Encourage open communication and a proactive approach towards quality and compliance within the team. Highlight the importance of GMP not just as a regulatory requirement but as a commitment to customer safety and product integrity.
Leverage Technology: Implement state-of-the-art equipment and software for quality control testing and documentation to enhance accuracy and efficiency. Explore options on platforms like LabX for laboratory equipment.
Maintain Robust Documentation: Ensure all procedures, tests, and changes are thoroughly documented in a clear, organized manner to facilitate audits and traceability. Guidelines on documentation best practices can be found through ISPE.
Act on Feedback and Incidents: Promptly address any quality issues or feedback from audits, regulatory inspections, and customer complaints. Implement corrective and preventive actions (CAPA) to prevent recurrence.
Improving GMP compliance is an ongoing process that requires dedication, continuous learning, and proactive management of quality systems.
How to Display GMP (Good Manufacturing Practice) Skills on Your Resume
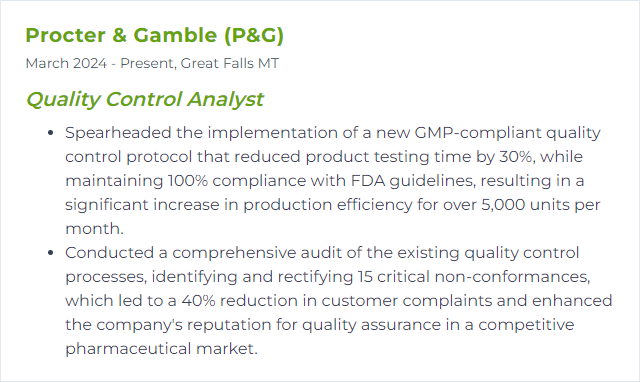
10. CAPA (Corrective and Preventive Action)
CAPA (Corrective and Preventive Action) is a quality management process used by a Quality Control Analyst to identify, address, and eliminate non-conformities or defects in products and processes. It involves implementing corrective actions to rectify immediate issues and preventive actions to avoid their recurrence, ensuring continuous improvement and compliance with quality standards.
Why It's Important
CAPA is crucial for a Quality Control Analyst as it identifies, addresses, and prevents the recurrence of errors, ensuring the continuous improvement of product quality and compliance with regulatory standards.
How to Improve CAPA (Corrective and Preventive Action) Skills
Improving CAPA involves a systematic approach to identify issues, implement solutions, and ensure effectiveness over time. Here are concise steps tailored for a Quality Control Analyst:
Identify and Document Issues: Use data analysis tools to identify trends that indicate underlying problems. Root Cause Analysis (RCA) helps in identifying the fundamental cause of a problem.
Evaluate the Risk: Prioritize issues based on their potential impact on product quality and safety. Risk Management Principles from ISO 31000 can guide this process.
Develop a CAPA Plan: Design corrective actions to address current issues and preventive actions to avoid future occurrences. Ensure actions are SMART (Specific, Measurable, Achievable, Relevant, Time-bound).
Implement the Plan: Allocate resources and assign responsibilities for implementing the CAPA plan. Use project management tools for effective implementation.
Monitor and Review: Use Quality Management Systems (QMS) principles to monitor the effectiveness of CAPA. Regular reviews should be conducted to ensure the actions remain effective over time.
Documentation and Communication: Maintain thorough documentation of the CAPA process and communicate progress and outcomes to relevant stakeholders.
Continuous Improvement: Incorporate lessons learned into your quality system for ongoing improvement. PDCA (Plan-Do-Check-Act) methodology can facilitate a culture of continuous improvement.
By following these steps, a Quality Control Analyst can enhance the effectiveness of CAPA processes, leading to improved product quality and compliance.
How to Display CAPA (Corrective and Preventive Action) Skills on Your Resume
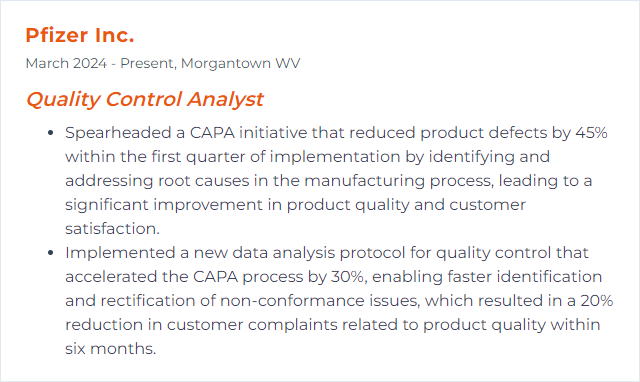
11. Microsoft Excel
Microsoft Excel is a spreadsheet software used for data analysis, manipulation, and visualization, essential for Quality Control Analysts to track, organize, and evaluate quality metrics and performance data.
Why It's Important
Microsoft Excel is crucial for a Quality Control Analyst because it enables efficient data organization, analysis, and visualization, facilitating the identification of trends, errors, and opportunities for quality improvement.
How to Improve Microsoft Excel Skills
Improving Microsoft Excel skills, especially for a Quality Control Analyst, involves focusing on advanced features, automation, and data analysis techniques. Here are concise recommendations:
Master Advanced Formulas: Understand complex formulas like
INDEX(MATCH())
,ARRAY
, andSUMIFS
to manipulate and analyze data efficiently. ExcelJet offers a comprehensive guide.Learn PivotTables and PivotCharts: These tools are crucial for summarizing, analyzing, sorting, and sharing data. Microsoft's guide provides a solid foundation.
Utilize Data Analysis ToolPak: For statistical analysis, enabling and using the Data Analysis Toolpak is essential. Excel Easy breaks down how to use this feature.
Explore Power Query: Automate the process of gathering and transforming data from various sources. Microsoft's Power Query documentation is a great starting point.
Implement Macros and VBA: Automate repetitive tasks and create custom functions with Visual Basic for Applications (VBA). Start with Excel Macros Tutorial for the basics.
Enhance Visualization Skills: Beyond basic charts, learn to create dynamic and interactive dashboards for data storytelling. Chandoo.org offers excellent tutorials on dashboards.
Practice Data Validation and Error Checking: Guarantee data integrity by mastering Excel’s data validation and error-checking tools. Microsoft's guide covers these topics in detail.
By focusing on these areas, a Quality Control Analyst can significantly improve their proficiency in Excel, leading to more efficient and effective data analysis and reporting.
How to Display Microsoft Excel Skills on Your Resume
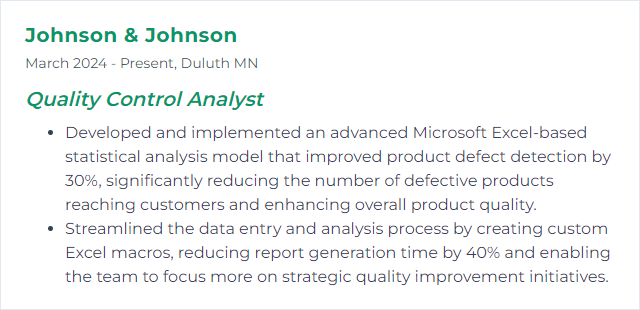
12. Quality Auditing
Quality auditing is the systematic examination of a quality system carried out by an internal or external quality auditor or audit team to assess whether the system complies with established standards, regulations, and procedures, and to identify areas for operational improvement from the perspective of a Quality Control Analyst.
Why It's Important
Quality auditing is crucial as it systematically evaluates and verifies a Quality Control Analyst's adherence to defined standards and procedures, ensuring the consistency, reliability, and effectiveness of products or services, thereby safeguarding customer satisfaction and compliance with regulatory requirements.
How to Improve Quality Auditing Skills
Improving Quality Auditing involves a structured approach focusing on continuous improvement, skill enhancement, and effective communication. Here's a concise guide:
Stay Updated with Standards: Regularly update your knowledge on the latest ISO standards and industry-specific regulations to ensure your auditing practices are up-to-date.
Enhance Auditing Skills: Invest in professional development courses for auditors to improve their skills in critical thinking, attention to detail, and objective evaluation.
Implement Technology: Utilize auditing software to streamline the process, ensure compliance, and manage audit data efficiently.
Foster Open Communication: Encourage a culture of open dialogue between auditors and auditees to facilitate cooperation and understanding. Effective communication is key to identifying and addressing issues promptly.
Continuous Improvement: Adopt a Kaizen approach to auditing by continuously seeking ways to improve processes and reduce waste, enhancing the overall quality of audits.
By focusing on these key areas, a Quality Control Analyst can significantly improve the effectiveness and efficiency of Quality Auditing.
How to Display Quality Auditing Skills on Your Resume
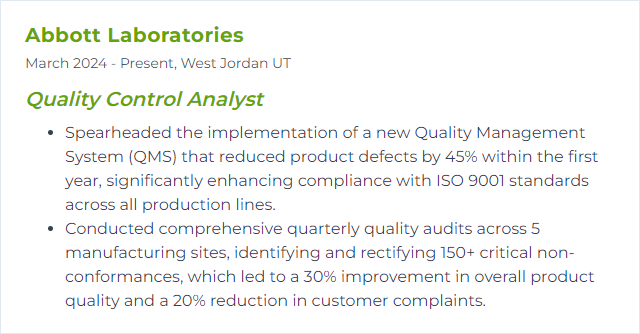