Top 12 Order Filler Skills to Put on Your Resume
In today's competitive job market, distinguishing yourself as an order filler requires more than just basic knowledge of inventory and shipping procedures. Mastering a set of specialized skills and prominently featuring them on your resume can significantly elevate your candidacy, making you a top choice for employers in the logistics and supply chain sectors.
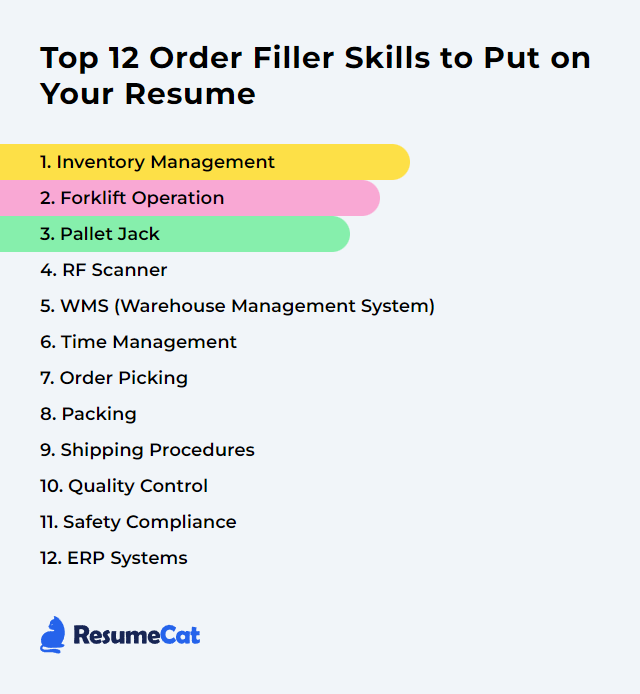
Order Filler Skills
- Inventory Management
- Forklift Operation
- Pallet Jack
- RF Scanner
- WMS (Warehouse Management System)
- Time Management
- Order Picking
- Packing
- Shipping Procedures
- Quality Control
- Safety Compliance
- ERP Systems
1. Inventory Management
Inventory management involves tracking and controlling a company's inventory levels to ensure adequate supply for fulfilling orders, minimizing excess stock, and optimizing storage costs, thereby supporting order fillers in efficiently processing and dispatching customer orders.
Why It's Important
Inventory management is crucial for an Order Filler as it ensures the accurate tracking and availability of products, enabling timely and efficient order fulfillment, reducing errors, and improving customer satisfaction.
How to Improve Inventory Management Skills
Improving inventory management, especially for an Order Filler, involves optimizing the process of storing, ordering, and using inventory to ensure efficiency and reduce waste. Here are concise steps:
Implement an Inventory Management System: Use technology to track inventory levels, orders, sales, and deliveries in real time. Consider systems like QuickBooks Commerce or Fishbowl Inventory.
Regular Auditing: Regularly compare the inventory records with actual stock to maintain accuracy. This can be done through physical counts, spot checking, or cycle counting.
Improve Forecasting: Utilize past sales data and market trends to predict future inventory needs accurately. Tools like Forecast Pro can help.
First In, First Out (FIFO): Prioritize selling older stock first to minimize the risk of obsolescence or spoilage. This is crucial in industries like food and fashion.
Adopt Lean Inventory Practices: Keep stock levels as lean as possible without affecting service quality. Techniques like Just-In-Time (JIT) can be effective. Kanban is a popular method for implementing JIT.
Supplier Management: Build strong relationships with suppliers for reliability, cost-effectiveness, and quality assurance. Negotiate terms that allow for flexibility in inventory levels.
Train Staff: Ensure all team members understand the inventory system and their role in maintaining it. Proper training can improve accuracy and efficiency.
Utilize Inventory Management Software Features: Make full use of features like automated reordering, data analysis, and inventory alerts. Many platforms offer comprehensive tutorials, such as Shopify's Inventory Management Guide.
By following these steps, an Order Filler can significantly improve inventory management, leading to reduced costs, increased efficiency, and better customer satisfaction.
How to Display Inventory Management Skills on Your Resume
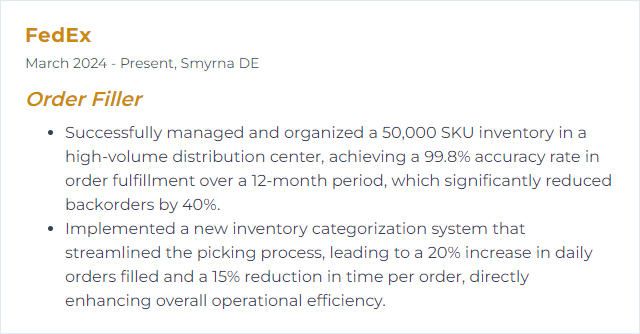
2. Forklift Operation
Forklift operation, in the context of an Order Filler, involves using a forklift to efficiently move, lift, and place goods and materials in a warehouse or storage facility to fulfill orders accurately and safely.
Why It's Important
Forklift operation is crucial for an Order Filler as it significantly enhances efficiency and safety in moving, lifting, and handling large or heavy items within warehouses, thus ensuring timely and accurate order fulfillment.
How to Improve Forklift Operation Skills
Improving forklift operation, especially for an Order Filler, involves a combination of training, safety measures, and efficiency practices. Here are concise tips:
Enhance Training: Ensure comprehensive forklift training that includes both theoretical and practical components, focusing on safe operation and handling techniques specific to order filling tasks.
Implement Regular Maintenance: Keep forklifts in top condition through a regular maintenance schedule, preventing downtime and accidents caused by equipment failure.
Adopt Safety Protocols: Adhere strictly to OSHA's safety guidelines for forklift operation, including wearing seatbelts, ensuring load stability, and maintaining clear visibility.
Use Technology: Incorporate technology like forklift fleet management systems to monitor and improve the efficiency of forklift operations, including tracking maintenance needs and operator performance.
Continuous Learning: Promote a culture of continuous learning and improvement, encouraging operators to stay updated with the latest best practices and safety standards through resources like the National Forklift Safety Day.
By focusing on these key areas, you can significantly improve forklift operation within your order filling processes, enhancing safety, efficiency, and productivity.
How to Display Forklift Operation Skills on Your Resume
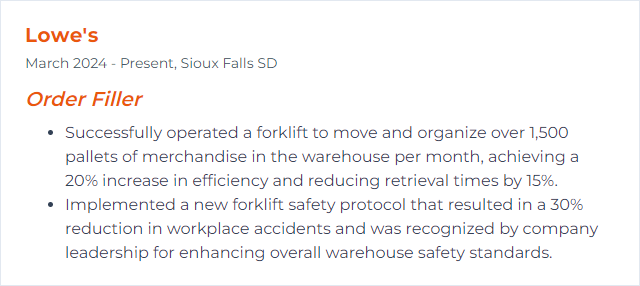
3. Pallet Jack
A pallet jack, for an order filler, is a manual or powered tool used to lift and move pallets for the purpose of organizing, loading, or unloading goods in a warehouse or storage facility.
Why It's Important
A pallet jack is essential for an Order Filler as it allows for the efficient movement and handling of heavy pallets within a warehouse, facilitating the quick and safe transportation of goods for order fulfillment.
How to Improve Pallet Jack Skills
To improve a Pallet Jack for an Order Filler, consider the following steps:
- Ergonomics: Ensure the handle and controls are comfortable for extended use. Ergonomic Guidelines.
- Maintenance: Regularly maintain wheels and hydraulics for smooth operation. Maintenance Tips.
- Training: Provide comprehensive training on efficient maneuvering and safety. Safety Training.
- Wheel Material: Upgrade to polyurethane wheels for better traction and noise reduction. Wheel Types.
- Load Capacity: Choose a model with a suitable load capacity for your needs. Capacity Guide.
Implementing these improvements enhances safety, efficiency, and comfort for Order Fillers using Pallet Jacks.
How to Display Pallet Jack Skills on Your Resume
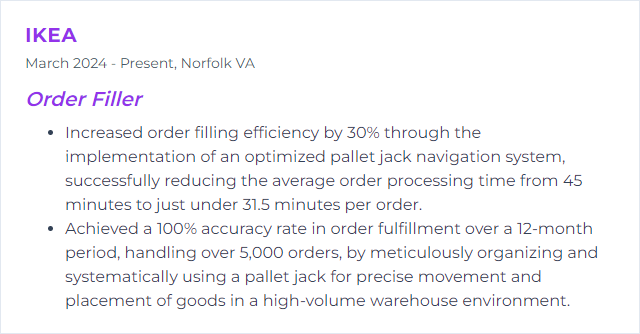
4. RF Scanner
An RF scanner is a handheld device used by order fillers to read barcodes, track inventory, and update order statuses in real time through radio frequency technology.
Why It's Important
An RF (Radio Frequency) Scanner is crucial for an Order Filler as it streamlines inventory management and order picking processes, ensuring accuracy, efficiency, and real-time tracking of goods.
How to Improve RF Scanner Skills
Improving an RF (Radio Frequency) Scanner for an Order Filler involves enhancing both the hardware and software components to boost efficiency, accuracy, and user comfort. Here's a concise guide:
Upgrade Scanner Hardware: Opt for models with longer battery life, robust build for durability, and ergonomic design for ease of use. Honeywell and Zebra offer advanced options.
Enhance Software Integration: Ensure the scanner's software is fully integrated with your inventory management system for real-time updates and tracking. Scandit's software solutions can provide powerful software integration capabilities.
Implement User Training: Regular training sessions can help users utilize the RF scanners more efficiently and leverage all their features. Customized training can be sourced from Barcoding, Inc..
Adopt Wearable Scanners: For hands-free operation, consider wearable scanners that increase mobility and efficiency. ProGlove offers innovative wearable solutions.
Regular Maintenance: Schedule regular maintenance checks to ensure scanners are functioning optimally, which reduces downtime. Manufacturer support or third-party services like Cognex can provide maintenance and support.
Feedback Loop: Create a system for users to report issues or suggest improvements. This feedback can help in making targeted upgrades or changes.
By focusing on these areas, you can significantly improve the functionality and efficiency of RF scanners for order fillers, enhancing overall operational productivity.
How to Display RF Scanner Skills on Your Resume
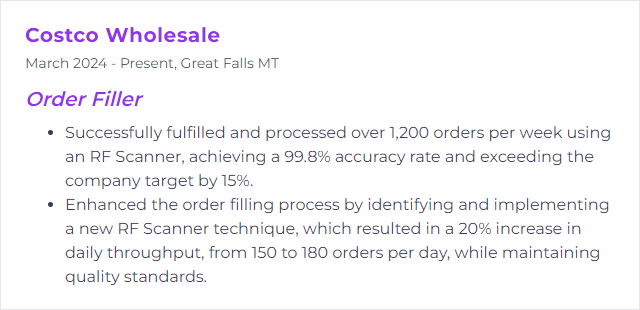
5. WMS (Warehouse Management System)
A Warehouse Management System (WMS) is a software solution designed to optimize and manage the operations within a warehouse. For an Order Filler, it aids in efficiently locating items, managing inventory, and streamlining the picking and packing processes, ensuring accurate and timely order fulfillment.
Why It's Important
A WMS (Warehouse Management System) is crucial for an Order Filler as it streamlines the picking and packing processes, enhances inventory accuracy, and reduces order fulfillment times, ensuring efficient and accurate order processing.
How to Improve WMS (Warehouse Management System) Skills
Improving a Warehouse Management System (WMS) to enhance efficiency, particularly for an Order Filler role, involves incorporating technology, optimizing processes, and focusing on data accuracy. Here's a concise guide:
Integration with Automation Tools: Integrate your WMS with automation tools like robotic picking systems to reduce manual errors and speed up order filling processes.
Enhanced Training Programs: Implement comprehensive training programs focusing on the specific functionalities of the WMS, ensuring that Order Fillers can utilize the system to its full potential.
Real-Time Data Analysis: Utilize real-time data analysis tools within your WMS to make immediate adjustments to inventory, orders, and staffing, enhancing decision-making and operational efficiency.
Optimize Picking Paths: Use your WMS to optimize picking paths in the warehouse, reducing travel time for Order Fillers and increasing the speed of order processing.
Mobile Technology Integration: Equip Order Fillers with mobile devices that are integrated with the WMS, allowing for real-time updates, scanning capabilities, and immediate access to inventory data.
Regular System Updates and Maintenance: Ensure your WMS is always running smoothly by conducting regular updates and maintenance, incorporating new features and fixing any bugs that could slow down operations.
Feedback Loop Implementation: Create a system for collecting and analyzing feedback from Order Fillers on the WMS usability and functionality, using this input to make targeted improvements.
By focusing on these areas, you can significantly improve the efficiency and effectiveness of your Warehouse Management System, directly benefiting the role of an Order Filler and the overall operational success.
How to Display WMS (Warehouse Management System) Skills on Your Resume
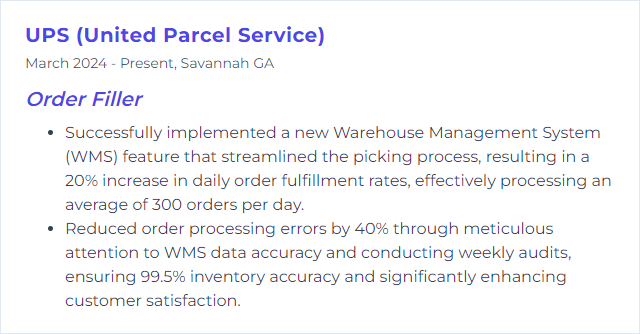
6. Time Management
Time management for an Order Filler involves efficiently organizing and prioritizing tasks to accurately and quickly process orders within deadlines, ensuring optimal productivity and customer satisfaction.
Why It's Important
Time management is crucial for an Order Filler to efficiently process orders, minimize delays, and ensure timely deliveries, directly impacting customer satisfaction and operational productivity.
How to Improve Time Management Skills
Improving time management, especially for an Order Filler, involves prioritizing tasks, batching similar activities, and minimizing distractions. Here’s a concise guide:
Prioritize Tasks: Use the Eisenhower Box method to differentiate between urgent and important tasks. Todoist offers a simple explanation and implementation strategy.
Batch Processing: Group similar tasks together to reduce the time spent switching between different types of activities. Asian Efficiency provides insights on how batching can increase efficiency.
Minimize Distractions: Identify what commonly distracts you and use strategies to reduce these interruptions. Freedom offers tips on minimizing digital and environmental distractions.
Implementing these strategies can significantly enhance time management skills, making an Order Filler more efficient and productive.
How to Display Time Management Skills on Your Resume
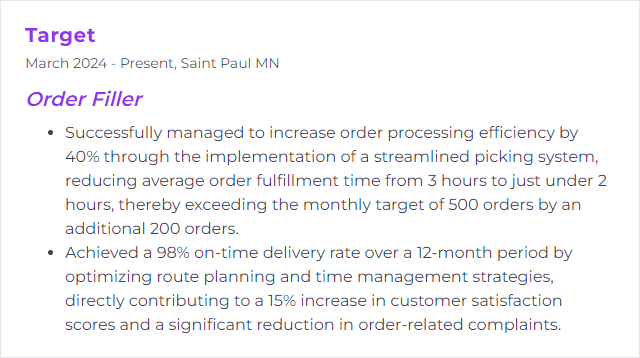
7. Order Picking
Order picking involves selecting and gathering items from a warehouse or storage location to fulfill customer orders, a key task performed by an Order Filler.
Why It's Important
Order picking is crucial because it directly affects an Order Filler's ability to accurately and efficiently fulfill customer orders, ensuring timely deliveries and maintaining customer satisfaction.
How to Improve Order Picking Skills
Improving order picking involves streamlining processes, reducing travel time, and ensuring accuracy. Implement these strategies:
Zone Picking: Assign pickers to specific areas to reduce travel time. More on Zone Picking.
Batch Picking: Group similar orders to pick multiple orders simultaneously. Batch Picking Explained.
Use of Technology: Implement barcode scanners and wearable tech to reduce errors and increase speed. Technology in Order Picking.
Optimize Warehouse Layout: Arrange items based on popularity and create efficient picking paths. Warehouse Layout Optimization.
Continuous Training: Regularly train staff on new techniques and technologies. Importance of Training.
By focusing on these areas, you can significantly improve the efficiency and accuracy of your order picking processes.
How to Display Order Picking Skills on Your Resume
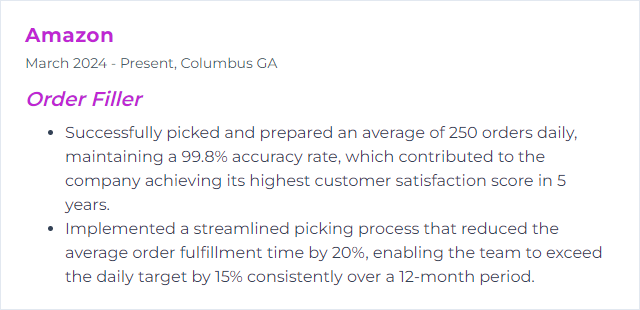
8. Packing
Packing, in the context of an Order Filler, involves selecting the appropriate packaging materials and securely enclosing items in a box or container for safe transportation to the customer.
Why It's Important
Packing is crucial for an Order Filler as it ensures the safe and secure transportation of products to customers, maintains product quality, and enhances customer satisfaction by delivering items in good condition.
How to Improve Packing Skills
Improving packing efficiency as an Order Filler involves several key strategies. Here's a short and concise guide:
Organize Packing Materials: Keep all necessary packing materials (boxes, tape, bubble wrap) within easy reach. This reduces the time spent searching for supplies. Uline offers a variety of packing materials suitable for any need.
Use the Right Box Size: Selecting the appropriate box size reduces waste and shipping costs. It also protects items better during transit. The Packaging Company provides a guide to choosing the right box size.
Implement a Packing Station: Designate a specific area for packing. This station should have ample space and be organized efficiently. Packaging Digest often features insights on setting up efficient packing stations.
Streamline Packing Process: Develop a systematic packing process. This might include packing items in a specific order or pre-assembling boxes. FedEx offers tips on streamlining your packing process.
Use Packing Software: Consider using packing software to automate the selection of packaging materials and box sizes. Packsize is known for their on-demand packaging solutions.
Continuous Training: Regularly train and update staff on new packing techniques and tools. Continuous improvement is key to efficiency. APICS provides resources and certifications in supply chain and logistics operations, which include aspects of efficient packing and order fulfillment.
By applying these strategies, Order Fillers can significantly improve their packing efficiency, leading to faster order processing, reduced costs, and happier customers.
How to Display Packing Skills on Your Resume
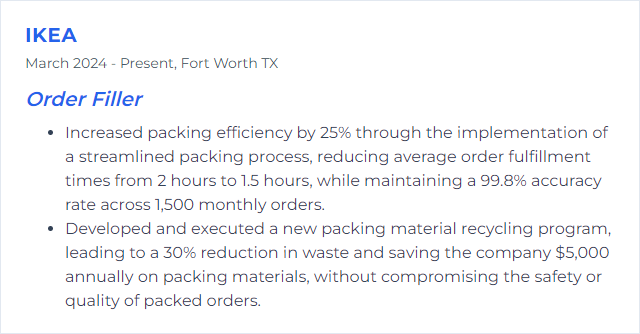
9. Shipping Procedures
Shipping procedures for an Order Filler involve the following key steps:
- Picking: Selecting the ordered items from the inventory.
- Packing: Safely packaging the selected items for transport.
- Labeling: Attaching shipping labels and necessary documentation to the package.
- Dispatching: Handing off the packaged items to the delivery service or shipping carrier.
These steps ensure that the correct products are securely and efficiently delivered to the customer.
Why It's Important
Shipping procedures are crucial for an Order Filler as they ensure accurate, timely, and secure delivery of goods, directly impacting customer satisfaction and operational efficiency.
How to Improve Shipping Procedures Skills
Improving shipping procedures requires a strategic approach focused on efficiency, accuracy, and reliability. Here are concise steps an Order Filler can take:
Streamline Packaging: Optimize packaging methods to ensure both protection and speed. Use standardized boxes and pre-set packaging materials to minimize decision-making time. Packaging Strategies
Implement Inventory Management Software: Adopt an inventory management system that updates in real-time, helping you locate items faster. This reduces the picking time significantly. Inventory Management Guide
Automate Processes: Where possible, automate repetitive tasks such as labeling and invoicing to reduce human error and speed up the shipping process. Automation in Logistics
Regular Training: Ensure all staff are regularly trained on the latest shipping procedures and technologies to maintain high efficiency. Effective Training Techniques
Maintain Clear Communication with Carriers: Establish a direct line of communication with your shipping carriers to quickly resolve any issues that may arise, ensuring timely deliveries. Carrier Communication Tips
Analyze and Adjust: Regularly review shipping data to identify bottlenecks or inefficiencies in the shipping process and adjust procedures accordingly. Shipping Analytics
By focusing on these key areas, an Order Filler can significantly improve shipping procedures, leading to faster turnaround times and higher customer satisfaction.
How to Display Shipping Procedures Skills on Your Resume
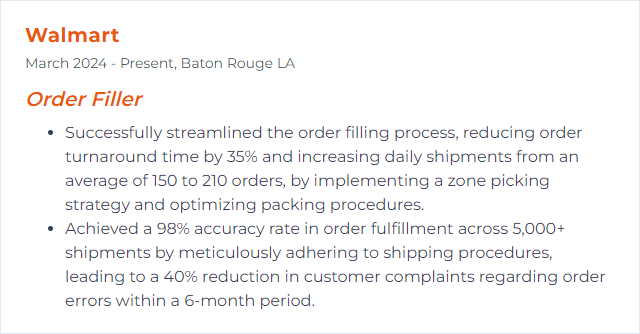
10. Quality Control
Quality Control, in the context of an Order Filler, involves the systematic process of verifying and checking orders to ensure that products meet the required standards and specifications before they are dispatched to customers. This includes checking item accuracy, quantity, and condition.
Why It's Important
Quality control ensures that products meet required standards and specifications before they reach customers, minimizing errors, enhancing customer satisfaction, and maintaining the company's reputation. For an Order Filler, it ensures accurate, defect-free orders, reducing returns and complaints.
How to Improve Quality Control Skills
Improving Quality Control (QC) for an Order Filler involves several key steps. Focus on these strategies for enhanced accuracy and efficiency:
Standardize Processes: Develop clear, standardized procedures for all order filling tasks. ISO standards can provide guidelines for establishing consistent workflows.
Training: Ensure all staff are thoroughly trained on QC measures. Regular training sessions can keep skills sharp and up-to-date.
Technology Integration: Use technology like barcode scanners and management software for error reduction. Explore options at GS1.
Regular Audits: Conduct frequent quality audits to identify and correct process flaws. Tools and tips for effective audits can be found through ASQ.
Feedback Loops: Implement a system for collecting and acting on feedback from stakeholders to continuously improve QC practices. Harvard Business Review offers insights on effective feedback.
Focusing on these areas can significantly enhance the quality control processes within order filling operations.
How to Display Quality Control Skills on Your Resume
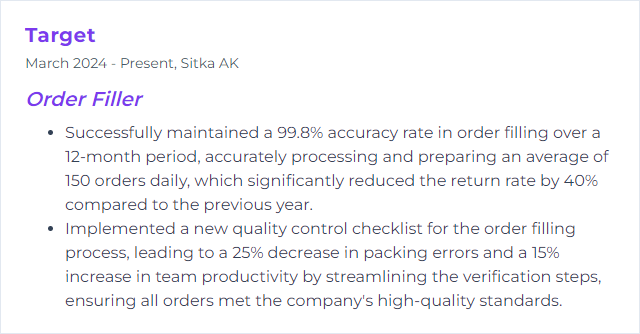
11. Safety Compliance
Safety compliance, in the context of an Order Filler, refers to adhering to established safety standards and regulations to ensure a safe work environment while performing tasks such as picking, packing, and handling goods in a warehouse or distribution center.
Why It's Important
Safety compliance ensures that order fillers work in a secure environment, minimizing the risk of accidents and injuries. It protects employees and the organization from legal issues and enhances productivity by maintaining a safe, efficient workplace.
How to Improve Safety Compliance Skills
Improving safety compliance for an Order Filler involves a multi-faceted approach focused on training, workplace adjustments, and continuous monitoring. Here’s a concise guide:
Regular Training: Conduct regular safety training sessions to ensure that Order Fillers are up-to-date with the latest safety protocols and procedures. OSHA offers guidelines and resources for workplace training.
Ergonomic Workspace: Adjust workstations to fit the Order Filler’s needs to prevent strains and injuries. Implement ergonomic solutions based on recommendations from NIOSH.
Use of Personal Protective Equipment (PPE): Ensure that all Order Fillers have access to and use the necessary PPE. Guidelines on PPE can be found through OSHA’s PPE page.
Regular Safety Audits: Conduct safety audits to identify and mitigate potential hazards in the workplace. OSHA’s Safety and Health Management Systems can provide a framework for these audits.
Encourage Reporting of Hazards: Create an environment where Order Fillers feel comfortable reporting safety concerns without fear of reprisal. Information on establishing a reporting system can be found in OSHA’s Worker Rights section.
Continuous Improvement: Implement a continuous improvement process to regularly review and improve safety protocols based on feedback and incident reports.
By focusing on these areas, you can significantly improve safety compliance in the workplace for Order Fillers, creating a safer and more productive environment.
How to Display Safety Compliance Skills on Your Resume
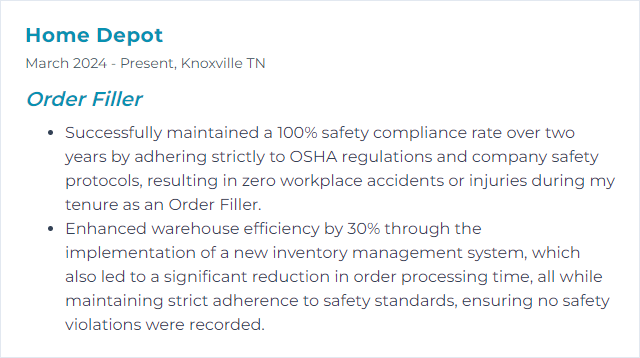
12. ERP Systems
ERP (Enterprise Resource Planning) systems are integrated software platforms that manage and automate core business processes, including order fulfillment, by streamlining operations, data flow, and resource allocation across various departments within an organization.
Why It's Important
ERP systems are crucial for Order Fillers as they streamline inventory management, automate order processing, and ensure accurate, real-time data flow, improving order fulfillment efficiency and customer satisfaction.
How to Improve ERP Systems Skills
Improving ERP (Enterprise Resource Planning) systems, especially for an Order Filler role, involves enhancing efficiency, accuracy, and user experience. Below are concise strategies to achieve this:
Integration and Automation: Streamline order processing by integrating ERP with e-commerce platforms and CRM, automating data entry, and reducing manual errors.
Real-Time Data Access: Ensure real-time inventory visibility to improve order accuracy and fulfillment speed.
Customization and Scalability: Tailor the ERP system to fit specific business needs and ensure it can scale with business growth.
User Training and Support: Provide comprehensive training and support for users to maximize ERP functionalities efficiently.
Mobile Accessibility: Implement mobile-friendly ERP solutions to allow order fillers to access and update data on the go.
Continuous Feedback Loop: Establish a feedback mechanism for users to suggest improvements, leading to ongoing ERP optimization.
By focusing on these key areas, ERP systems can be significantly improved to support the dynamic needs of Order Fillers and enhance overall operational efficiency.
How to Display ERP Systems Skills on Your Resume
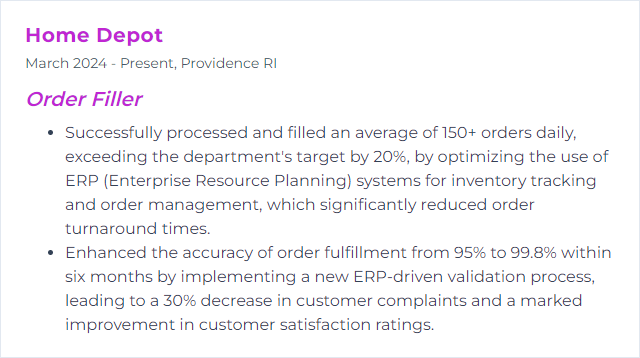