Top 12 Order Builder Skills to Put on Your Resume
In today's highly competitive job market, having a well-crafted resume is crucial for standing out as an order builder. Highlighting the top order builder skills on your resume not only showcases your proficiency in fulfilling and managing orders efficiently but also signals to potential employers your comprehensive understanding and capability in optimizing warehouse operations and customer satisfaction.
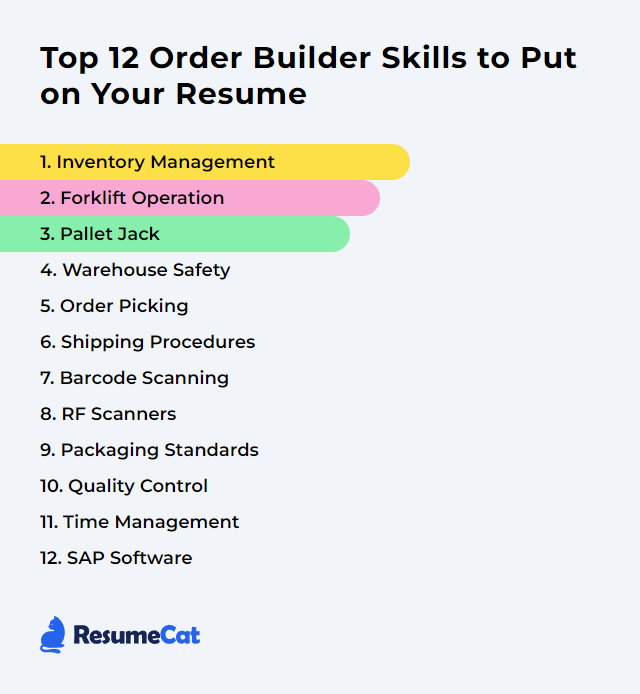
Order Builder Skills
- Inventory Management
- Forklift Operation
- Pallet Jack
- Warehouse Safety
- Order Picking
- Shipping Procedures
- Barcode Scanning
- RF Scanners
- Packaging Standards
- Quality Control
- Time Management
- SAP Software
1. Inventory Management
Inventory management, in the context of an Order Builder, involves overseeing and controlling the order, storage, and fulfillment of products to ensure that the right quantities are available for customer orders without excessive surplus or shortage.
Why It's Important
Inventory management is crucial for an Order Builder as it ensures the right stock levels are maintained to meet demand without overstocking, helping in optimizing order fulfillment processes, reducing costs, and improving customer satisfaction.
How to Improve Inventory Management Skills
Improving inventory management, especially for an Order Builder, involves a few key strategies aimed at enhancing accuracy, efficiency, and responsiveness.
Implement an Inventory Management System: Utilize robust inventory management software to streamline operations, improve real-time tracking, and reduce errors.
Adopt Just-In-Time (JIT) Inventory: By adopting JIT practices, you minimize stock levels and reduce storage costs, focusing on ordering only what's needed.
Regular Audits: Conduct regular inventory audits to ensure data accuracy between your inventory management system and physical stock.
Improve Demand Forecasting: Utilize historical data and demand forecasting tools to predict future inventory needs more accurately, reducing both overstock and stockouts.
Optimize Supplier Relationships: Work closely with suppliers to ensure timely deliveries and negotiate better terms. Quick and reliable supplier communication can improve inventory turnover rates.
Continuous Improvement: Regularly review and optimize inventory processes for continuous improvement, adapting to changes in demand and technology advancements.
By focusing on these strategies, an Order Builder can significantly enhance inventory management, leading to better customer satisfaction, reduced costs, and improved operational efficiency.
How to Display Inventory Management Skills on Your Resume
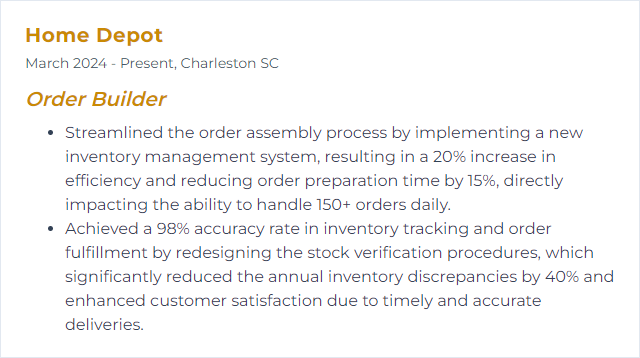
2. Forklift Operation
Forklift operation, in the context of an Order Builder, involves using a forklift to move, lift, and stack goods or materials efficiently in warehouses, storage facilities, or construction sites to prepare and organize orders for shipment or further processing.
Why It's Important
Forklift operation is crucial for an Order Builder as it enhances efficiency and safety in moving, lifting, and organizing large or heavy inventory, ensuring timely and accurate order fulfillment.
How to Improve Forklift Operation Skills
Improving forklift operation, especially for an Order Builder, involves enhancing safety, efficiency, and accuracy. Here's a concise guide:
Training & Certification: Ensure all operators complete a comprehensive forklift training program that meets OSHA standards. Regular refresher courses are also essential to keep skills sharp.
Pre-Operational Checks: Adopt a rigorous pre-operational checklist to inspect forklifts before use, preventing accidents and mechanical failures.
Efficient Layouts: Design warehouse layouts to minimize tight turns and optimize traffic flow. Efficiently organized spaces can significantly improve forklift operation by reducing travel time and potential for accidents.
Implement Technology: Utilize warehouse management systems (WMS) and forklift-mounted tablets for real-time inventory tracking, route planning, and order processing to streamline operations.
Safety Protocols: Enforce strict safety protocols, including speed limits, load capacity adherence, and proper communication methods among operators to prevent collisions and injuries.
Maintenance Program: Establish a routine maintenance program to ensure forklifts are in optimal working condition, reducing downtime and repair costs. Regularly check tires, brakes, steering, and hydraulic systems.
Following these steps will lead to improved forklift operation, enhancing overall productivity and safety in the warehouse environment.
How to Display Forklift Operation Skills on Your Resume
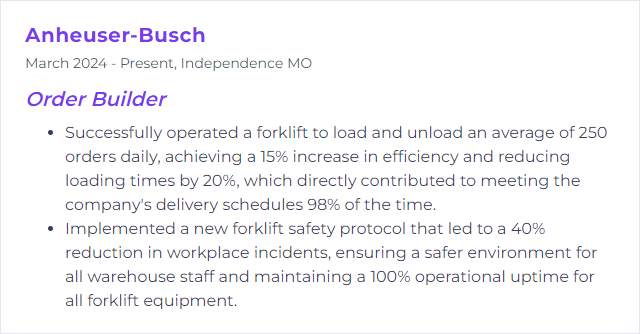
3. Pallet Jack
A pallet jack, in the context of an order builder, is a manual or powered tool used to lift and move pallets, facilitating the assembly and transport of orders within a warehouse or distribution center.
Why It's Important
A pallet jack is crucial for an Order Builder as it allows for efficient movement and handling of heavy loads and pallets within a warehouse, enhancing productivity and reducing physical strain.
How to Improve Pallet Jack Skills
Improving a pallet jack for an Order Builder involves enhancing its efficiency, safety, and ergonomics. Here are concise recommendations:
Ergonomic Handles: Install ergonomic handles to reduce strain on the operator's hands and wrists. Ergonomic Handles Guide
Maintenance: Regularly maintain and lubricate the wheels and bearings for smoother operation. Maintenance Tips
Wheel Material Upgrade: Upgrade to polyurethane wheels for better traction and noise reduction. Wheel Types
Load Capacity: Ensure the pallet jack's load capacity meets or exceeds your typical requirements to prevent overloading. Choosing the Right Pallet Jack
Safety Training: Provide operators with safety training to prevent accidents and improve handling efficiency. Safety Training Resources
Narrow Fork Option: Consider a model with narrow forks for easier maneuverability in tight spaces. Narrow Fork Pallet Jacks
Implementing these improvements can significantly enhance the performance and safety of a pallet jack for Order Builders.
How to Display Pallet Jack Skills on Your Resume
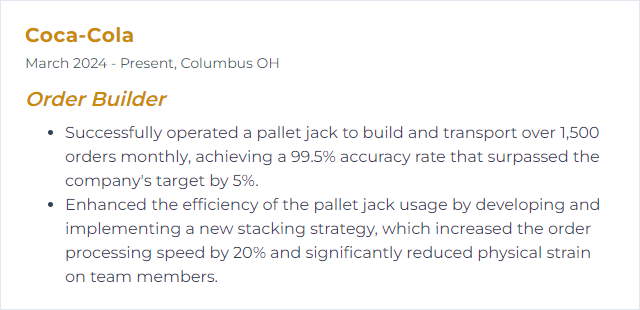
4. Warehouse Safety
Warehouse safety refers to the practices and policies implemented to prevent accidents and injuries within a warehouse setting, specifically focusing on creating a safe environment for order builders who are involved in selecting, assembling, and preparing orders for shipment. This includes proper equipment use, hazard identification, and adherence to safety protocols.
Why It's Important
Warehouse safety is critical to prevent accidents, injuries, and fatalities, ensuring a secure environment for Order Builders who operate in close proximity to heavy machinery, move large quantities of goods, and perform repetitive tasks. It minimizes risks, enhances efficiency, and promotes a culture of well-being.
How to Improve Warehouse Safety Skills
Improving warehouse safety, especially for Order Builders, involves a multifaceted approach focused on training, equipment maintenance, and a tidy environment. Here are concise strategies to enhance safety:
Training: Ensure all employees, particularly Order Builders, receive thorough safety training including handling equipment and understanding potential hazards.
Equipment Maintenance: Regularly check and maintain all warehouse equipment. This includes forklifts, conveyor belts, and personal protective equipment. The Occupational Safety and Health Administration (OSHA) offers guidelines on equipment standards.
Clear Signage: Clearly mark all hazard zones, walkways, and emergency exits to prevent accidents. Information on proper signage can be found on OSHA’s Safety and Health Topics pages.
Housekeeping: Keep aisles and work areas clear of debris to reduce trip hazards. OSHA provides guidelines on walking-working surfaces that detail how to maintain clear workspaces.
Emergency Preparedness: Conduct regular drills for emergencies like fire or chemical spills. Ready.gov has resources for developing an emergency preparedness plan.
By focusing on these areas, you can create a safer environment for Order Builders and all warehouse personnel.
How to Display Warehouse Safety Skills on Your Resume
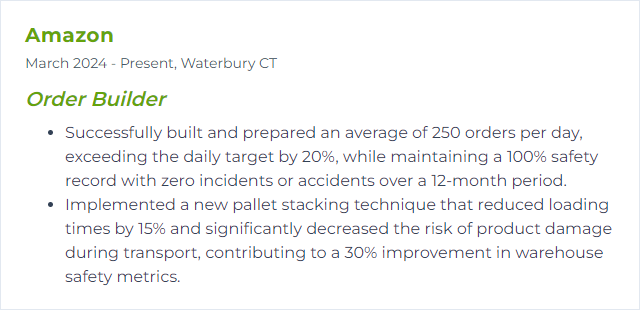
5. Order Picking
Order picking is the process of selecting and gathering items from a warehouse as specified by a customer's order, preparing these items for shipment. For an Order Builder, it involves accurately assembling and preparing the ordered products for delivery.
Why It's Important
Order picking is crucial for an Order Builder as it directly affects the accuracy, efficiency, and speed of fulfilling customer orders, ensuring customer satisfaction and minimizing errors and returns.
How to Improve Order Picking Skills
Improving order picking involves optimizing processes, technology, and ergonomics to increase efficiency and accuracy. Here are concise strategies:
Implement Warehouse Management Systems (WMS): Use WMS to optimize picking routes and inventory placement based on real-time data.
Adopt Pick-to-Light Systems: These systems direct pickers to the correct product locations, reducing errors and speeding up the picking process.
Use Voice Picking Technology: Voice-directed picking enhances accuracy and productivity by allowing hands-free, eyes-free operations.
Batch Picking: Group similar orders to minimize travel time, increasing efficiency especially for multiple small orders.
Optimize Storage and Layout: Align your warehouse layout and storage systems to minimize travel time and improve ergonomics. Helpful insights can be found in layout optimization.
Regular Training and Incentives: Ensure staff are regularly trained on new technologies and processes. Also, consider incentive programs to boost productivity and morale.
Implementing these strategies can significantly improve order picking efficiency and accuracy in a warehouse environment.
How to Display Order Picking Skills on Your Resume

6. Shipping Procedures
Shipping procedures for an Order Builder involve selecting and packing ordered items accurately, preparing and verifying shipping documents, labeling packages correctly for dispatch, and ensuring shipments are loaded onto delivery vehicles in accordance with company protocols and delivery schedules.
Why It's Important
Shipping procedures are important for an Order Builder because they ensure accurate, timely, and secure delivery of products to customers, maintaining order integrity and customer satisfaction.
How to Improve Shipping Procedures Skills
Improving shipping procedures, especially in the context of an Order Builder, involves streamlining operations, enhancing accuracy, and ensuring timely deliveries. Here are concise steps to achieve this:
Automate Order Processing: Implement automation software to reduce manual errors and speed up order processing.
Optimize Packaging: Use smart packaging solutions to minimize shipping costs and improve protection for goods in transit.
Integrate Real-Time Inventory Management: Maintain accurate stock levels with real-time inventory systems to prevent order delays.
Establish Clear Shipping Policies: Develop and communicate clear shipping guidelines to customers to set proper expectations.
Use Reliable Shipping Carriers: Partner with reputable carriers that offer tracking options and dependable delivery services.
Regularly Analyze and Adapt Shipping Strategies: Continuously review your shipping process and adapt based on data analytics and feedback.
By focusing on these areas, an Order Builder can significantly improve shipping efficiency, accuracy, and customer satisfaction.
How to Display Shipping Procedures Skills on Your Resume
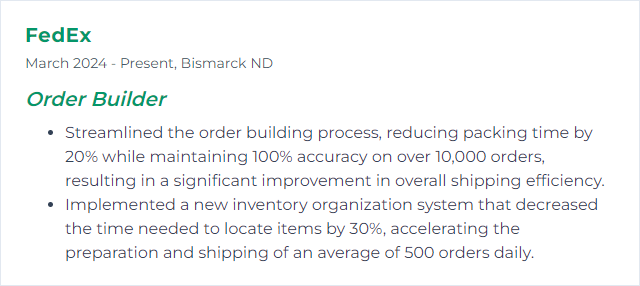
7. Barcode Scanning
Barcode scanning, in the context of an Order Builder, is the process of using a device to read barcodes on items or packaging, automating the identification and tracking of products for accurate and efficient order fulfillment.
Why It's Important
Barcode scanning is crucial for an Order Builder as it ensures accuracy in picking and packing orders, streamlines inventory tracking, and speeds up the order fulfillment process, resulting in increased efficiency and customer satisfaction.
How to Improve Barcode Scanning Skills
Improving barcode scanning, especially for Order Builders, involves enhancing both the hardware and software aspects of your scanning system. Focus on these key areas for optimal performance:
Use High-Quality Scanners: Opt for scanners that are durable, have high resolution, and can read barcodes at various angles and distances. Zebra and Honeywell offer industry-leading options.
Implement Advanced Scanning Software: Software solutions like Scandit can significantly boost scanning efficiency and accuracy, even in challenging conditions.
Train Staff: Ensure all users are properly trained on the best practices for scanning, including optimal angles and distances. Resources are often available on scanner manufacturers' websites.
Regularly Maintain Equipment: Keep scanners clean and regularly check for software updates. Manufacturer guidelines, such as those from Symbol (now part of Zebra), provide maintenance tips.
Optimize Barcode Quality and Placement: Ensure barcodes are high contrast, adequately sized, and placed in easily scannable locations on products. The GS1 General Specifications guide outlines best practices for barcode quality and placement.
Use Mobile Scanning Solutions: Incorporating mobile or wearable scanning solutions can increase flexibility and efficiency. ProGlove offers innovative wearable scanners.
Improving barcode scanning is about leveraging the right technology and training, maintaining your equipment, and ensuring your barcodes are optimized for quick and easy scanning.
How to Display Barcode Scanning Skills on Your Resume
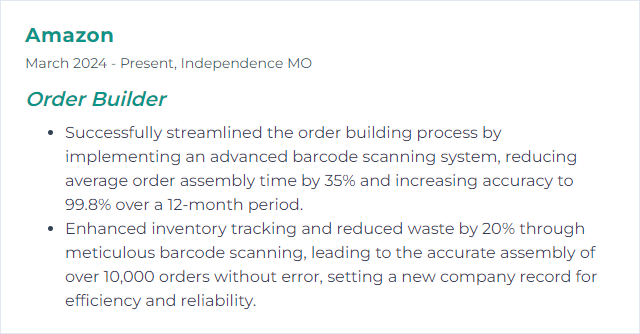
8. RF Scanners
RF scanners, in the context of an Order Builder, are handheld electronic devices used to read barcodes or RFID tags on products and packages. They facilitate accurate order picking, inventory tracking, and data collection in warehouses and distribution centers.
Why It's Important
RF Scanners are crucial for Order Builders because they streamline the picking and inventory tracking process, ensuring accuracy and efficiency in order fulfillment.
How to Improve RF Scanners Skills
Improving RF scanners for an Order Builder involves enhancing efficiency, accuracy, and user-friendliness. Key strategies include:
Upgrade to Latest Technology: Use the most recent RF scanner models that offer better performance, longer battery life, and faster scanning capabilities. Consider devices with advanced features such as image capture and touch screens for versatile use (Zebra Technologies).
Implement Wearable Scanners: Adopt wearable scanners to increase mobility and free up hands for more efficient order building (Honeywell).
Custom Software Solutions: Develop or integrate custom software solutions that optimize workflow, such as real-time inventory tracking and easier item lookup, tailored to your specific needs (Scandit).
Ergonomics and Training: Focus on ergonomics to reduce user fatigue and invest in comprehensive training programs to ensure users can leverage all features effectively (Ergotron).
Maintenance and Support: Establish a robust maintenance and support plan to minimize downtime and keep scanners updated and in optimal condition.
By focusing on these areas, RF scanners can be significantly improved to enhance the efficiency and accuracy of Order Builders, ultimately leading to smoother operations and improved productivity.
How to Display RF Scanners Skills on Your Resume
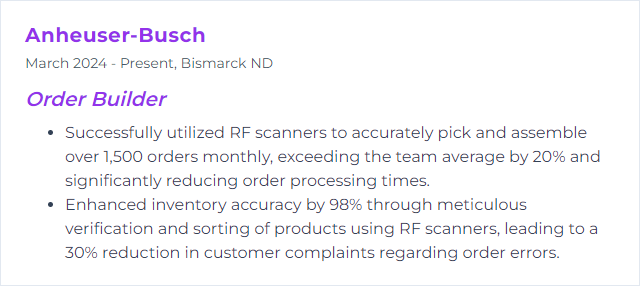
9. Packaging Standards
Packaging standards refer to the predefined guidelines and criteria that dictate how products should be prepared, protected, and presented for shipping and handling, ensuring they reach their destination safely and in good condition. For an Order Builder, these standards guide how to efficiently and securely package products to meet quality and customer satisfaction requirements.
Why It's Important
Packaging standards are crucial for Order Builders because they ensure product safety, maintain quality, facilitate efficient handling and transportation, and enhance customer satisfaction by delivering items in pristine condition.
How to Improve Packaging Standards Skills
Improving packaging standards, especially for an Order Builder, involves several key steps focused on efficiency, sustainability, and safety. Here's a concise guide:
Adopt Sustainable Materials: Choose eco-friendly packaging materials that are recyclable or biodegradable. EcoEnclose and NoIssue offer sustainable packaging solutions.
Standardize Sizes and Materials: Streamline packaging processes by using a limited range of standardized box sizes and packing materials. This reduces waste and improves efficiency. ULINE provides a variety of standardized packaging options.
Implement Multi-Use Packaging: Design packaging that has multiple uses or can be easily repurposed by the customer, encouraging sustainability. Packhelp offers innovative packaging solutions that can be customized for multi-use.
Enhance Product Safety: Use packaging materials that provide adequate protection to the products, minimizing damage during transit. The Packaging Company offers a range of protective packaging solutions.
Adopt Automation: Incorporate automation in the packaging process for efficiency and consistency. Packsize specializes in smart packaging solutions that can automate the packaging process.
Follow Regulatory Standards: Ensure compliance with international and local packaging regulations to avoid legal issues. ASTM International provides a collection of standards for various industries, including packaging.
Continuous Improvement: Regularly review and update packaging standards based on customer feedback and technological advancements. Implementing a feedback loop with customers can provide valuable insights for improvement.
By focusing on these areas, an Order Builder can significantly improve their packaging standards, enhancing customer satisfaction and reducing environmental impact.
How to Display Packaging Standards Skills on Your Resume
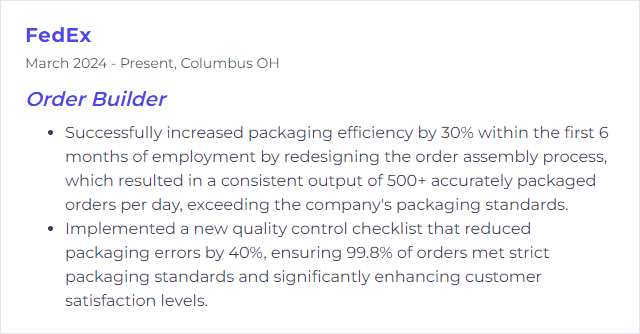
10. Quality Control
Quality Control in the context of an Order Builder involves systematically monitoring and evaluating the order assembly process to ensure that the final product meets the established standards of quality, accuracy, and completeness before delivery to the customer.
Why It's Important
Quality Control is crucial for an Order Builder as it ensures accuracy and completeness in fulfilling orders, leading to customer satisfaction, repeat business, and reduced costs related to returns and corrections.
How to Improve Quality Control Skills
Improving Quality Control for an Order Builder involves several key strategies:
Standardize Processes: Develop and enforce standardized protocols for all order building tasks to ensure consistency. ISO standards can provide a reliable framework.
Training: Regularly train staff on quality standards, new technologies, and efficiency techniques. Incorporate resources from ASQ (American Society for Quality).
Implement Technology: Use technology like ERP (Enterprise Resource Planning) systems for real-time tracking and automation of order processing, reducing human error.
Quality Audits: Conduct frequent quality audits and inspections to identify and rectify issues promptly. Tools like Six Sigma methodologies can be useful here.
Feedback Loop: Establish a robust feedback loop with customers and within the team to continuously gather insights on quality improvement.
Supplier Quality Management: Ensure your suppliers adhere to high-quality standards; assess and monitor their performance regularly. APICS offers resources and certifications on supply chain management.
Continuous Improvement: Adopt a culture of continuous improvement (Kaizen) to perpetually seek ways to enhance quality and efficiency in order building processes.
By systematically applying these strategies, an Order Builder can significantly enhance its quality control efforts.
How to Display Quality Control Skills on Your Resume
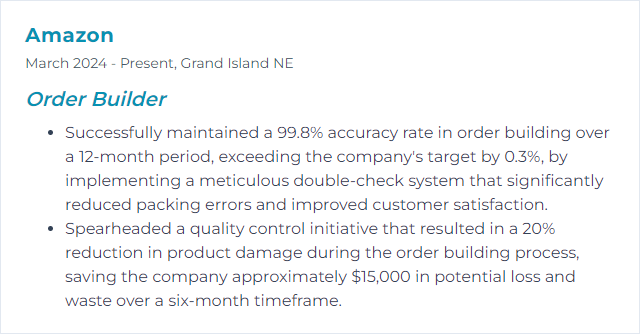
11. Time Management
Time management for an Order Builder involves efficiently organizing and prioritizing tasks to assemble and prepare orders within set deadlines, ensuring smooth operations and customer satisfaction.
Why It's Important
Time management is crucial for an Order Builder as it ensures efficient and accurate order fulfillment, maximizes productivity, and meets delivery deadlines, enhancing customer satisfaction and operational success.
How to Improve Time Management Skills
Improving time management, especially for an Order Builder, involves strategic planning, prioritization, and efficient workflow organization. Here are key steps:
Set Clear Goals: Identify daily, weekly, and monthly objectives. Use the SMART criteria (Specific, Measurable, Achievable, Relevant, Time-bound).
Prioritize Tasks: Determine the urgency and importance of your tasks. Tools like the Eisenhower Box can help.
Plan Your Day: Allocate specific times for tasks, including breaks. Utilize planning tools like Trello or Asana for organization.
Limit Distractions: Identify your main distractions and limit them. Tools like Freedom can block distracting sites/apps.
Use Technology: Implement order management systems (OMS) for efficiency. Explore options like Shopify's OMS for streamlined operations.
Review and Adjust: Regularly review your performance and adjust your strategies as needed.
By following these steps and utilizing the suggested tools, an Order Builder can significantly improve their time management skills.
How to Display Time Management Skills on Your Resume
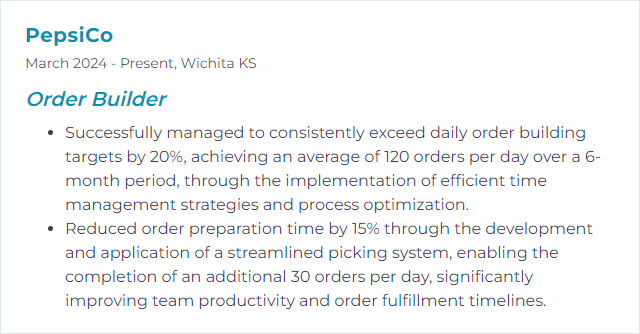
12. SAP Software
SAP software is a comprehensive enterprise resource planning (ERP) system that integrates all aspects of a business, including finance, supply chain, manufacturing, and sales. For an Order Builder, it streamlines the process of creating, processing, and managing customer orders, ensuring efficiency and accuracy from order entry to fulfillment.
Why It's Important
SAP software is important for an Order Builder because it streamlines and automates the order processing, inventory management, and customer relationship functions, ensuring accurate and efficient order fulfillment.
How to Improve SAP Software Skills
Improving SAP software, particularly for an Order Builder, revolves around enhancing user experience, integrating advanced analytics, and ensuring seamless connectivity with external systems. Here are concise ways to achieve these improvements:
Optimize User Interface (UI): Implement SAP Fiori for a more intuitive, responsive, and user-friendly interface, making the order building process smoother.
Leverage SAP Analytics Cloud: Enhance decision-making with real-time analytics by integrating SAP Analytics Cloud, providing insights directly within the order building workflow.
Automate Processes with SAP Intelligent Robotic Process Automation (RPA): Automate repetitive tasks in the order building process using SAP Intelligent RPA, reducing errors and saving time.
Integrate with SAP Business Technology Platform (BTP): Use SAP BTP to connect and extend your SAP applications, enabling more flexible and scalable order management solutions.
Ensure Data Integrity with Master Data Governance: Apply SAP Master Data Governance to maintain accurate and consistent data across all business processes, crucial for effective order management.
Enhance Customization with SAP Cloud Platform SDK for iOS and Android: Develop custom mobile applications for order management using SAP Cloud Platform SDK to facilitate on-the-go access for sales representatives.
Strengthen Collaboration using SAP Ariba Network: Integrate your order building processes with suppliers through SAP Ariba Network, ensuring efficient, transparent, and collaborative procurement operations.
By focusing on these areas, you can significantly improve the functionality and efficiency of SAP software for an Order Builder, enhancing overall business performance.
How to Display SAP Software Skills on Your Resume
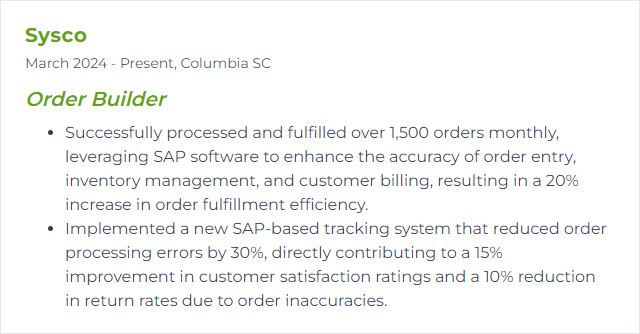