Top 12 Warehouse Loader Skills to Put on Your Resume
In today's highly competitive job market, standing out as a warehouse loader requires a well-crafted resume that highlights your most valuable skills. This guide provides an overview of the top 12 skills essential for warehouse loaders, helping you to showcase your capabilities effectively and increase your chances of landing your desired position.
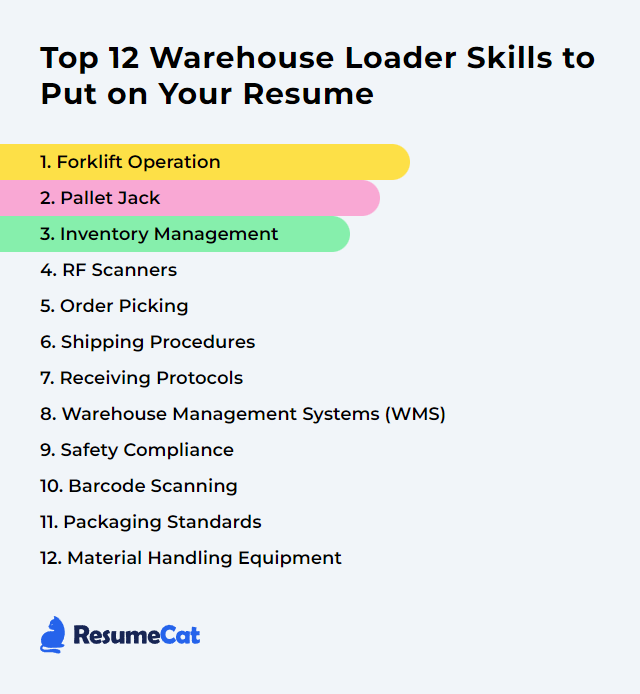
Warehouse Loader Skills
- Forklift Operation
- Pallet Jack
- Inventory Management
- RF Scanners
- Order Picking
- Shipping Procedures
- Receiving Protocols
- Warehouse Management Systems (WMS)
- Safety Compliance
- Barcode Scanning
- Packaging Standards
- Material Handling Equipment
1. Forklift Operation
Forklift operation involves maneuvering a powered industrial truck to move, lift, and stack materials in a warehouse setting, assisting in the loading and unloading of goods.
Why It's Important
Forklift operation is crucial for a Warehouse Loader as it enables efficient, safe handling, and movement of goods and materials, significantly increasing productivity and reducing physical strain and the risk of injury.
How to Improve Forklift Operation Skills
Improving forklift operation involves enhancing safety, efficiency, and operator skills. Here are concise steps:
Training and Certification: Ensure all operators complete OSHA-certified forklift training. Regular refresher courses keep skills sharp.
Pre-Operational Checks: Implement a routine for pre-use inspections to identify and fix potential hazards before operation.
Maintenance Program: Establish a regular maintenance schedule for forklifts to prevent breakdowns and extend equipment life.
Implement Safety Measures: Enhance safety by using safety accessories and equipment such as blue safety lights, mirrors, and warning systems.
Optimize Warehouse Layout: Improve navigation and reduce bottlenecks by designing efficient warehouse layouts that accommodate forklift operation.
Use Technology: Incorporate forklift management software to track usage, maintenance, and efficiency metrics.
Encourage Communication: Foster a culture of safety through regular meetings and open dialogue about forklift operation and safety.
By focusing on training, maintenance, safety, and efficiency, you can significantly improve forklift operations in your warehouse.
How to Display Forklift Operation Skills on Your Resume
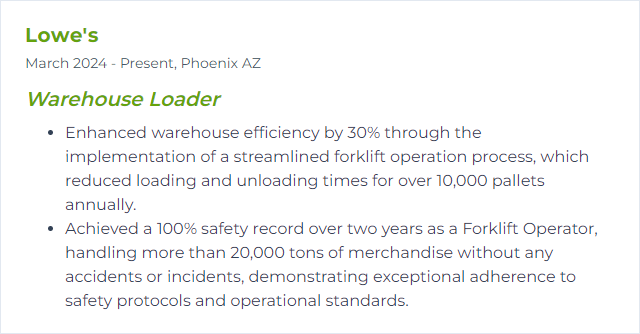
2. Pallet Jack
A pallet jack, in the context of a warehouse loader, is a manual or powered tool used for lifting and moving pallets within a warehouse.
Why It's Important
A pallet jack is crucial for a Warehouse Loader because it allows for efficient, easy movement of heavy or bulky goods, enhancing productivity and reducing physical strain.
How to Improve Pallet Jack Skills
Improving a pallet jack for a warehouse loader involves enhancing its efficiency, durability, and ease of use. Here are concise strategies:
Ergonomics: Opt for models with ergonomic handles and controls to reduce strain on operators. Ergonomics by OSHA provides guidelines on ergonomic solutions for manual material handling.
Maintenance: Implement a regular maintenance schedule to ensure all parts are in good working order, extending the lifespan. Preventive Maintenance Guide offers tips on preventive maintenance.
Capacity Upgrade: Choose pallet jacks with a higher weight capacity if frequently moving heavy loads, to improve efficiency and safety. Material Handling Equipment by MHI gives insights into selecting the right equipment.
Training: Provide comprehensive training for operators on proper usage and safety practices to prevent accidents and improve handling efficiency. Warehouse Safety Principles by OSHA outlines key safety measures.
Technology Integration: Consider pallet jacks with digital features, such as electronic load indicators or GPS tracking, to enhance load management and navigation. Smart Warehousing discusses the impact of technology in warehousing.
By focusing on ergonomics, maintenance, capacity, training, and technology integration, you can significantly improve the performance and reliability of pallet jacks in a warehouse setting.
How to Display Pallet Jack Skills on Your Resume
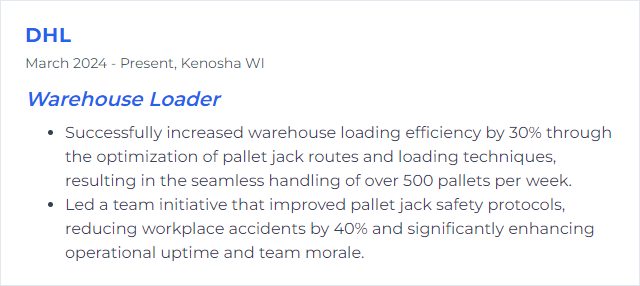
3. Inventory Management
Inventory Management is the process of overseeing and controlling the flow of goods in and out of a warehouse, ensuring accurate tracking, storage, and availability of products.
Why It's Important
Inventory management is crucial for a Warehouse Loader because it ensures the right products are available in the correct quantities when needed, preventing overstocking or stockouts, optimizing storage space, and facilitating efficient order fulfillment.
How to Improve Inventory Management Skills
Improving inventory management, especially from the perspective of a Warehouse Loader, involves several key actions:
Automation and Technology Integration: Utilize inventory management software to automate tasks like stock updates, ordering, and tracking. This reduces errors and saves time.
Regular Audits: Conduct regular inventory audits to ensure the accuracy of what's recorded versus what's physically in stock.
Efficient Organization: Implement an efficient warehouse layout that optimizes space and reduces movement time for loaders, making it easier to locate and manage stock.
Training and Communication: Ensure loaders are properly trained on inventory management practices and maintain clear communication between all members of the warehouse team.
Demand Forecasting: Use historical data to predict future demand, thereby improving inventory accuracy and ensuring you're neither overstocking nor understocking.
By focusing on these areas, a Warehouse Loader can significantly contribute to more efficient and accurate inventory management.
How to Display Inventory Management Skills on Your Resume
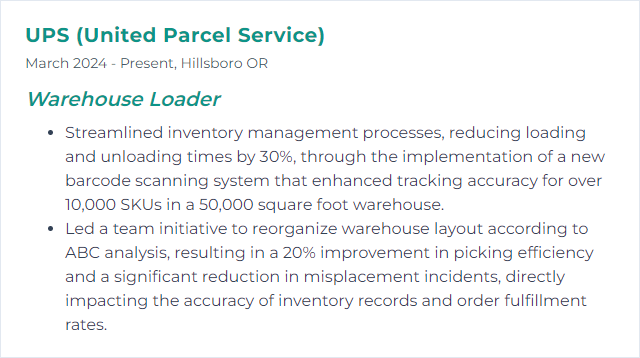
4. RF Scanners
RF scanners, in the context of a warehouse loader, are handheld devices that use radio frequency communication to scan barcodes or RFID tags on items, enabling the tracking, identification, and management of inventory in a warehouse environment.
Why It's Important
RF scanners are crucial for warehouse loaders as they streamline inventory management, enabling accurate and swift tracking of goods, leading to improved efficiency and reduced errors in order fulfillment.
How to Improve RF Scanners Skills
Improving RF (Radio Frequency) scanners for warehouse loaders involves enhancing usability, connectivity, and scanning capabilities. Key strategies include:
Ergonomics and Design: Design lightweight, ergonomic scanners with intuitive interfaces to reduce user fatigue and improve efficiency. Zebra Technologies offers a variety of ergonomic designs.
Battery Life and Charging: Implement long-lasting batteries and fast-charging solutions to ensure minimal downtime. Honeywell Scanners are known for their efficient power management.
Connectivity and Integration: Ensure seamless integration with existing warehouse management systems (WMS) and support for Wi-Fi 6/6E for robust connectivity. Cisco’s Wi-Fi 6 Solutions enhance network performance.
Durability: Utilize rugged designs that withstand drops, dust, and moisture, ensuring reliability in harsh warehouse environments. Datalogic Industrial Scanners provide durable scanning solutions.
Advanced Scanning Capabilities: Adopt scanners with advanced imaging technology for quick and accurate scanning of barcodes in any condition, including damaged or poorly printed codes. Symbol Scanners by Zebra offer high-performance scanning.
Focusing on these areas will significantly improve the efficiency and productivity of warehouse loaders by making RF scanning faster, more accurate, and user-friendly.
How to Display RF Scanners Skills on Your Resume
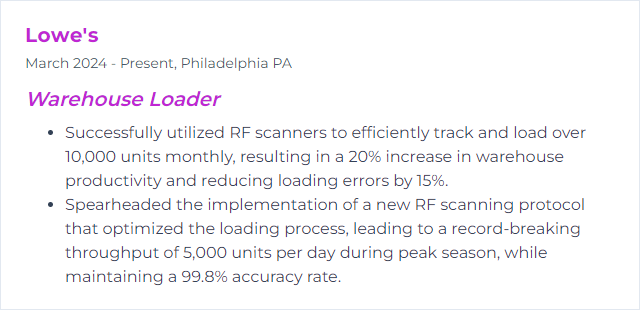
5. Order Picking
Order picking is the process in which a warehouse loader collects and assembles items from stock to fulfill customer orders.
Why It's Important
Order picking is crucial because it directly affects the speed and accuracy of customer order fulfillment, impacting customer satisfaction and operational efficiency in a warehouse.
How to Improve Order Picking Skills
Improving order picking efficiency in a warehouse involves optimizing the process from storage to shipment. Here are concise strategies for a warehouse loader:
Implement a Zone Picking Strategy: Divide the warehouse into zones, and assign loaders to specific areas to minimize travel time. More on Zone Picking.
Use Batch Picking: Group similar orders together to reduce the number of trips needed. Batch Picking Explained.
Optimize Storage Layout: Place high-demand items closer to the packing area. Effective Warehouse Layout.
Leverage Technology: Employ warehouse management systems (WMS) and automated picking tools. Benefits of WMS.
Continuous Training: Regularly train loaders on new techniques and technologies. Importance of Training.
Pick-to-Light Systems: Use light-guided picking for faster item location. Understanding Pick-to-Light.
Evaluate and Refine: Regularly review picking processes and worker performance to identify improvement areas. Performance Evaluation Tips.
By implementing these strategies, a warehouse can significantly improve its order picking efficiency and accuracy, leading to better overall performance.
How to Display Order Picking Skills on Your Resume
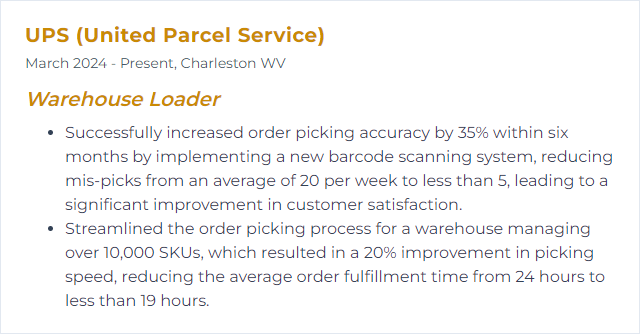
6. Shipping Procedures
Shipping procedures for a warehouse loader involve preparing and loading goods onto delivery vehicles according to scheduled orders, ensuring accuracy and safety, and completing necessary documentation related to the dispatch of items.
Why It's Important
Shipping procedures are crucial for a Warehouse Loader because they ensure the accurate, safe, and timely delivery of goods, minimizing damage, loss, and delays, thereby enhancing overall efficiency and customer satisfaction.
How to Improve Shipping Procedures Skills
Improving shipping procedures, especially from the perspective of a Warehouse Loader, involves streamlining operations, enhancing accuracy, and promoting safety. Here are short and concise strategies to achieve these improvements:
Implement an Inventory Management System: Use technology to track inventory in real-time, reducing errors and speeding up the loading process. Shopify's Guide on Inventory Management Systems offers insights into choosing the right system.
Adopt Lean Warehousing Principles: Apply lean management techniques to minimize waste and optimize efficiency in the shipping process. LeanCor's Lean Warehousing Principles can provide a starting point.
Enhance Safety Training: Regularly train warehouse loaders on safety protocols and proper equipment use to prevent accidents and improve efficiency. OSHA's Warehouse Safety Tips can be a valuable resource.
Implement a Quality Control Check: Before shipment, have a system in place to double-check orders for accuracy, minimizing returns and customer dissatisfaction. ASQ's Quality Control Standards offer guidelines.
Utilize Efficient Packing Methods: Adopt packing techniques and materials that protect goods while optimizing space. Packaging Digest often discusses innovative packing solutions.
Schedule Regular Maintenance: Ensure all loading equipment and vehicles are regularly maintained to prevent downtime. Fleet Maintenance Tips from Geotab can help create a maintenance schedule.
Communicate Effectively: Maintain open lines of communication between warehouse loaders, managers, and transport teams to address issues swiftly. Effective Communication in the Workplace by Indeed highlights communication strategies.
By adopting these strategies, warehouse loaders can contribute significantly to improving shipping procedures, enhancing overall productivity and customer satisfaction.
How to Display Shipping Procedures Skills on Your Resume
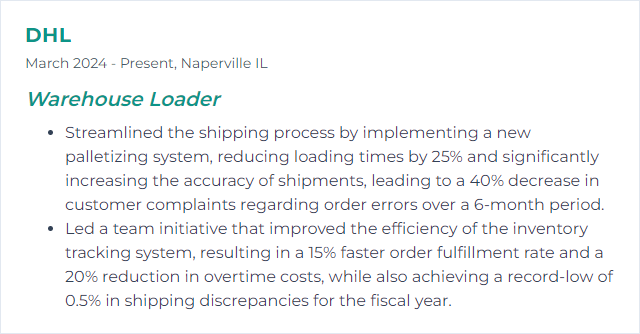
7. Receiving Protocols
Receiving Protocols in a warehouse setting refer to the standardized procedures a Warehouse Loader follows to accept, inspect, document, and store incoming goods to ensure accuracy, integrity, and timely processing of inventory.
Why It's Important
Receiving protocols are crucial for a Warehouse Loader as they ensure accurate, timely, and secure intake of shipments, minimizing errors, damage, and inventory discrepancies. This enhances efficiency and reliability in warehouse operations.
How to Improve Receiving Protocols Skills
Improving receiving protocols in a warehouse involves streamlining processes, enhancing accuracy, and ensuring safety. Here’s a concise guide:
Standardize Processes: Develop clear, standardized procedures for receiving goods. This includes unloading, inspection, documentation, and storage. OSHA provides guidelines on warehouse safety that can integrate with receiving protocols.
Use Technology: Implement a Warehouse Management System (WMS) to automate and track inventory in real-time. Barcode scanners and RFID tags can significantly reduce errors and speed up the receiving process. GS1 US is a resource for barcode and RFID standards.
Train Staff: Regularly train warehouse loaders and staff on updated receiving protocols and the use of technology. This ensures everyone is proficient and can work efficiently. The Warehousing Education and Research Council (WERC) offers resources and training for warehouse operations.
Quality Control Checks: Conduct random quality control checks to ensure the integrity of goods received and adherence to protocols. This step helps to identify and rectify discrepancies early.
Feedback Loop: Create a system for feedback from loaders and receivers on the warehouse floor. This can help in identifying bottlenecks and areas for improvement in the receiving process.
By focusing on standardization, technology integration, staff training, quality control, and feedback, warehouse receiving protocols can be significantly improved, leading to increased efficiency and safety.
How to Display Receiving Protocols Skills on Your Resume
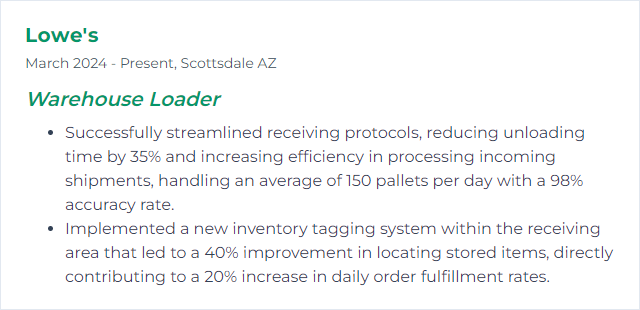
8. Warehouse Management Systems (WMS)
A Warehouse Management System (WMS) is a software solution that helps manage and optimize the operations within a warehouse, including inventory tracking, picking, receiving, and shipping goods, specifically aiming to streamline tasks and increase efficiency for warehouse workers, including loaders.
Why It's Important
Warehouse Management Systems (WMS) are crucial for warehouse loaders because they streamline operations, ensuring efficient and accurate loading processes, optimizing space usage, and enabling real-time inventory tracking, which reduces errors and enhances overall productivity.
How to Improve Warehouse Management Systems (WMS) Skills
Improving Warehouse Management Systems (WMS) involves enhancing efficiency, accuracy, and productivity in warehouse operations. Here's a concise guide:
Integration: Ensure the WMS is fully integrated with other business systems (e.g., ERP, CRM) for seamless data exchange. More on WMS Integration.
Real-time Data: Utilize real-time data tracking for inventory and shipments to improve accuracy and decision-making. Benefits of Real-time Data in WMS.
Automation: Implement automation in repetitive tasks (e.g., picking, packing) to reduce errors and increase efficiency. WMS and Automation.
Training: Regularly train staff on the WMS to ensure they are proficient and can leverage all its features effectively. Importance of WMS Training.
Continuous Improvement: Regularly review and update the WMS based on feedback and evolving business needs. Continuous Improvement in WMS.
By focusing on these areas, a warehouse can significantly enhance its operations, benefiting both the warehouse loader and the overall business.
How to Display Warehouse Management Systems (WMS) Skills on Your Resume
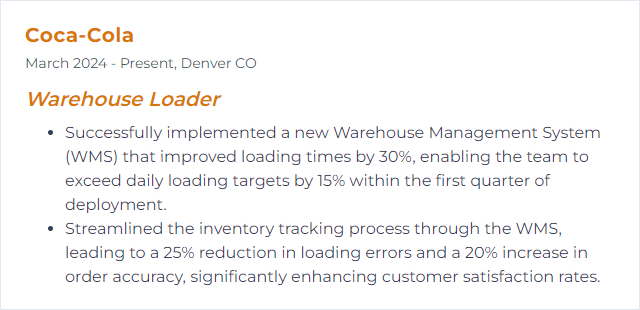
9. Safety Compliance
Safety compliance, in the context of a Warehouse Loader, refers to adhering to established health and safety regulations and guidelines to ensure a safe working environment, minimizing the risk of accidents or injuries.
Why It's Important
Safety compliance is important for a Warehouse Loader to prevent accidents and injuries, ensure a safe working environment, and comply with legal and regulatory requirements, thereby protecting both employees and the organization.
How to Improve Safety Compliance Skills
Improving safety compliance for a Warehouse Loader involves a multi-faceted approach that focuses on training, equipment maintenance, and a culture of safety.
Training: Ensure that all warehouse loaders undergo comprehensive safety training focused on the specific risks and tasks of their job. This includes proper lifting techniques, equipment operation, and emergency procedures. OSHA provides guidelines and resources for safety training.
Equipment Maintenance: Regularly inspect and maintain all loading equipment and machinery to ensure they are in good working condition. This reduces the risk of accidents caused by equipment failure. Guidelines for maintenance can be found at NIOSH.
Safety Culture: Foster a culture of safety where employees feel responsible for their safety and that of their coworkers. Encourage reporting of unsafe conditions without fear of reprisal. Details on building a safety culture can be explored through SafetyCulture.
Regular Audits: Conduct regular safety audits to identify and rectify potential hazards in the warehouse. The American Society of Safety Professionals offers resources on how to conduct effective safety audits.
Personal Protective Equipment (PPE): Ensure all loaders are equipped with the necessary PPE, such as gloves, safety glasses, and steel-toed boots. Guidelines for PPE are available on the OSHA Personal Protective Equipment page.
By focusing on these areas, warehouse loaders can significantly improve their safety compliance, contributing to a safer working environment.
How to Display Safety Compliance Skills on Your Resume
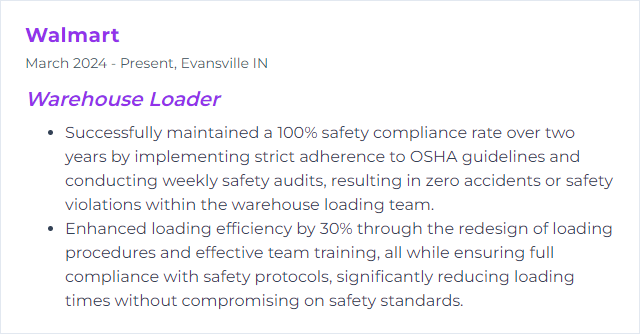
10. Barcode Scanning
Barcode scanning in a warehouse setting involves using a handheld or mounted scanner to read barcodes on items. This process helps in tracking, organizing, and managing inventory efficiently, ensuring accurate loading and unloading of goods.
Why It's Important
Barcode scanning is important for a Warehouse Loader because it ensures accurate tracking and management of inventory, speeds up the process of loading and unloading goods, and reduces the risk of human error, resulting in improved efficiency and productivity.
How to Improve Barcode Scanning Skills
Improving barcode scanning in a warehouse setting involves enhancing both the hardware used for scanning and the processes around scanning. Here are concise steps to do so:
Use High-Quality Scanners: Opt for durable, high-speed scanners that can read barcodes from various distances and angles, and are capable of scanning damaged or poorly printed barcodes.
Implement Wireless Scanning: Consider wireless barcode scanners to allow for more mobility and flexibility, reducing the time taken to scan items across different locations.
Optimize Barcode Placement: Ensure barcodes are placed at easily accessible spots on packages. Guidelines on efficient barcode placement can be found on GS1’s website.
Regular Training: Conduct regular training sessions for warehouse loaders on the optimal use of barcode scanners and updates on scanning technology. AIM provides resources and guidelines on best practices.
Use Barcode Quality Management Software: Implement software that monitors barcode quality, ensuring they are always scannable. Solutions like Barcode Verifiers can help maintain quality standards.
Implement Redundant Scanning Systems: Set up multiple scanning checkpoints to ensure accuracy in inventory tracking, reducing errors. This approach is elaborated on logistics and supply chain management resources like Inbound Logistics.
Regular Maintenance and Calibration: Schedule regular maintenance and calibration of barcode scanners to ensure they operate efficiently. Manufacturer’s guides, like those from Symbol/Motorola, provide maintenance tips.
By following these steps and continuously seeking improvements based on technology advancements and operational feedback, warehouse loaders can significantly enhance the efficiency and accuracy of barcode scanning processes.
How to Display Barcode Scanning Skills on Your Resume
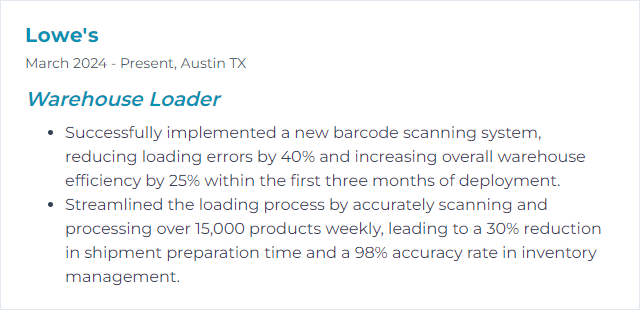
11. Packaging Standards
Packaging standards refer to the set of rules and guidelines used to ensure that products are packaged properly for safe, efficient storage and transportation. For a Warehouse Loader, these standards dictate how items should be securely packed, labeled, and handled to minimize damage, optimize space, and facilitate easy identification and retrieval.
Why It's Important
Packaging standards are crucial for a Warehouse Loader as they ensure the safe, efficient handling and storage of goods, reducing damage, loss, and workplace accidents, while optimizing space and streamlining the loading and unloading processes.
How to Improve Packaging Standards Skills
Improving packaging standards, especially from the perspective of a Warehouse Loader, involves enhancing both the efficiency and safety of packaging processes. Here are concise steps to achieve this:
Understand Packaging Requirements: Familiarize yourself with the specific packaging requirements for different types of goods. Packaging Digest offers insights into industry standards.
Use of Appropriate Materials: Ensure the use of high-quality and suitable packaging materials to protect goods. The International Safe Transit Association (ISTA) provides guidelines on packaging materials and testing.
Efficient Packaging Design: Optimize package design for space-saving and protection. Packworld shares innovative packaging designs and solutions.
Training and Education: Regular training on the latest packaging techniques and standards. The Packaging School offers courses on packaging technology and design.
Quality Control: Implement strict quality control measures to ensure packaging meets required standards. ISO (International Organization for Standardization) provides globally recognized standards for quality management.
Sustainability Practices: Adopt environmentally friendly packaging practices. The Sustainable Packaging Coalition offers resources on sustainable packaging initiatives.
Automation and Tools: Leverage automation and the right tools to improve packaging efficiency. MMH (Modern Materials Handling) discusses technologies and equipment for improving warehouse operations.
By focusing on these areas, a Warehouse Loader can significantly contribute to improving packaging standards, thus ensuring safety, compliance, and efficiency in the packaging process.
How to Display Packaging Standards Skills on Your Resume
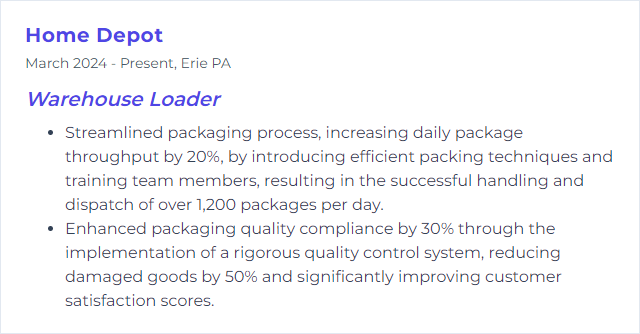
12. Material Handling Equipment
Material Handling Equipment (MHE) for a Warehouse Loader refers to devices specifically designed for moving, controlling, protecting, and storing materials throughout the warehouse, including forklifts, pallet jacks, conveyors, and automated storage and retrieval systems.
Why It's Important
Material handling equipment is crucial for a Warehouse Loader as it significantly enhances efficiency and safety in moving, storing, and retrieving goods, reducing manual labor, minimizing damage, and optimizing the utilization of space.
How to Improve Material Handling Equipment Skills
Improving Material Handling Equipment (MHE) for a Warehouse Loader involves several strategies aimed at enhancing efficiency, safety, and productivity. Here are concise steps to achieve this:
Regular Maintenance: Schedule and conduct regular maintenance checks to prevent breakdowns and extend the lifespan of MHE. This includes checking for wear and tear, ensuring all parts are lubricated, and replacing any faulty components promptly. OSHA’s Maintenance Guidelines
Operator Training: Invest in comprehensive training programs for operators to ensure they are proficient in using the equipment safely and efficiently. This includes handling techniques, safety protocols, and emergency procedures. NIOSH Training for Lift Truck Operators
Upgrade Equipment: Stay abreast of technological advancements and consider upgrading to more efficient, ergonomic, and safer equipment. Newer models often offer better fuel efficiency, higher productivity, and advanced safety features. Material Handling Industry of America (MHI)
Implement Automation: Where possible, automate processes using robotic loaders, conveyor belts, or Automated Guided Vehicles (AGVs) to reduce manual handling, minimize errors, and speed up operations. Automation in Material Handling
Ergonomic Design: Choose equipment with ergonomic designs to reduce strain on operators, which can lead to fewer injuries and more consistent operational performance. Ergonomics in Material Handling Equipment Design
Efficient Layout Planning: Optimize the warehouse layout to ensure smooth flow paths for material handling equipment, reducing travel time and preventing bottlenecks. Warehouse Layout Design Guide
Regular Reviews and Feedback: Regularly review the performance and condition of your material handling equipment. Encourage feedback from operators to identify areas for improvement and implement changes accordingly. Effective Warehouse Feedback Strategies
By focusing on these areas, you'll improve the efficiency, safety, and lifespan of your Material Handling Equipment, leading to a more productive warehouse operation.
How to Display Material Handling Equipment Skills on Your Resume
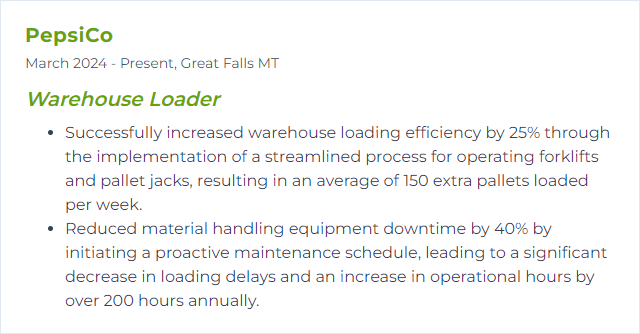