Top 12 Loader Skills to Put on Your Resume
In today's competitive job market, having a well-crafted resume is crucial for loader positions in industries ranging from construction to logistics. Highlighting the top loader skills on your resume can significantly enhance your chances of standing out to employers by showcasing your proficiency and readiness to contribute effectively to their operations.
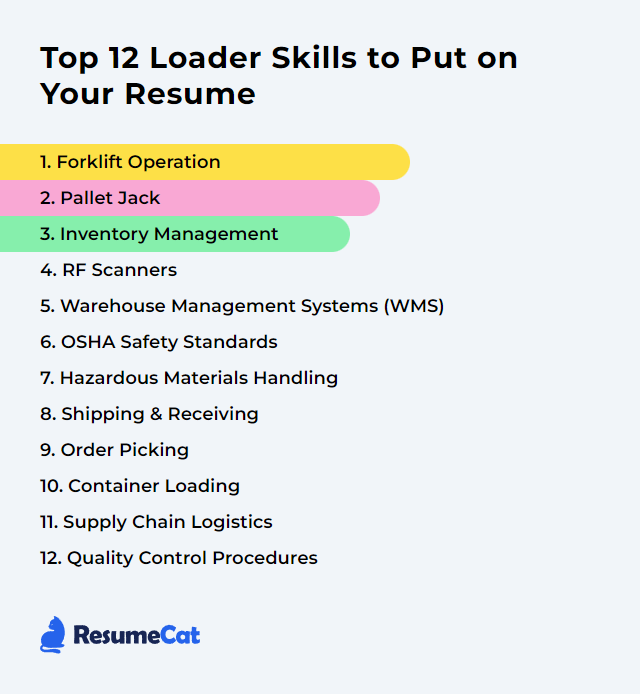
Loader Skills
- Forklift Operation
- Pallet Jack
- Inventory Management
- RF Scanners
- Warehouse Management Systems (WMS)
- OSHA Safety Standards
- Hazardous Materials Handling
- Shipping & Receiving
- Order Picking
- Container Loading
- Supply Chain Logistics
- Quality Control Procedures
1. Forklift Operation
Forklift operation, in the context of a loader, involves the use of a powered industrial truck equipped with a front-mounted forked platform to lift, move, and place materials over short distances within warehouses, construction sites, or industrial settings.
Why It's Important
Forklift operation is crucial for a loader because it enables efficient, safe, and precise movement of goods, significantly enhancing productivity and reducing the risk of injury or damage to materials.
How to Improve Forklift Operation Skills
Improving forklift operation, particularly for a loader, involves enhancing safety, efficiency, and operator competency. Here are concise strategies to achieve this:
Training and Certification: Ensure all operators complete a comprehensive training program that meets OSHA standards, emphasizing hands-on practice.
Routine Maintenance: Implement a regular maintenance schedule to keep the forklift in optimal condition, reducing breakdowns and accidents.
Safety Protocols: Develop and enforce strict safety protocols, including pre-operation inspections and safe loading techniques, to minimize risks.
Ergonomic Considerations: Adjust the forklift design or add accessories to enhance operator comfort and reduce fatigue, thereby increasing productivity and reducing errors.
Technology Integration: Incorporate advanced technologies such as telematics systems to monitor forklift operations, maintenance needs, and improve overall efficiency.
By focusing on these key areas, you can significantly improve forklift operation for loaders, enhancing safety, efficiency, and performance.
How to Display Forklift Operation Skills on Your Resume
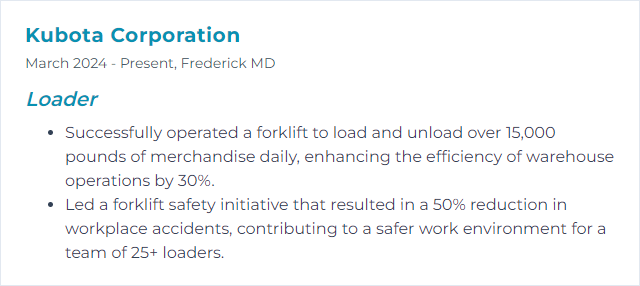
2. Pallet Jack
A pallet jack, also known as a pallet truck, is a manual or powered tool used in warehouses and loading areas to lift and move pallets.
Why It's Important
A pallet jack is crucial for a loader as it significantly enhances efficiency and safety in moving heavy palletized goods, reducing manual labor and risk of injury.
How to Improve Pallet Jack Skills
To improve a pallet jack for a loader, consider the following concise steps:
Upgrade Wheels: Switch to high-quality, durable wheels for smoother operation and better maneuverability. Uline offers a variety of wheel options.
Ergonomic Handle: Ensure the handle is ergonomically designed to reduce strain. Grainger has ergonomic options.
Regular Maintenance: Perform regular maintenance checks for hydraulic fluid, wheel integrity, and fork condition. OSHA's guidelines can help establish a maintenance routine.
Load Capacity: Consider upgrading to a model with a higher load capacity if current limits are frequently exceeded. Crown Equipment provides a range of capacities.
Training: Ensure operators are properly trained for efficient and safe use. National Safety Council offers training resources.
By implementing these improvements, you can enhance performance, safety, and longevity of a pallet jack.
How to Display Pallet Jack Skills on Your Resume
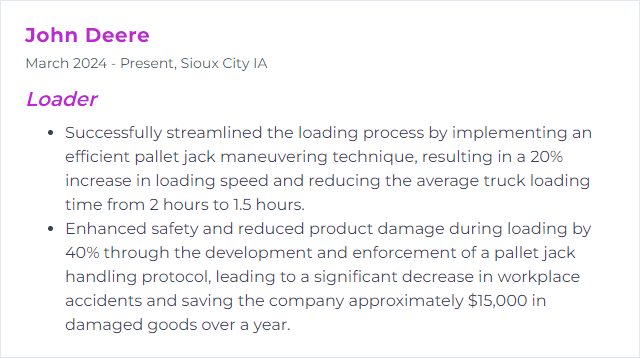
3. Inventory Management
Inventory management, in the context of a loader, refers to the systematic control and oversight of the quantities, locations, and movements of the materials or goods being loaded, ensuring they are accurately accounted for, efficiently organized, and readily accessible for loading operations.
Why It's Important
Inventory management is crucial for a Loader to ensure the right products are available when needed, minimizing delays, reducing storage costs, and improving overall efficiency and customer satisfaction.
How to Improve Inventory Management Skills
Improving inventory management, especially for a loader, involves streamlining processes to ensure accuracy, efficiency, and responsiveness. Here are concise steps:
Implement an Inventory Management System: Use technology to track inventory levels, orders, sales, and deliveries. Shopify and QuickBooks Commerce are examples of platforms that offer inventory management solutions.
Regular Auditing: Periodically compare the inventory records with the actual stock through physical counts to identify discrepancies. This is crucial for maintaining accuracy. Learn more about inventory auditing from Deloitte.
Improve Forecasting: Use historical data and market trends to predict future inventory needs, minimizing overstock and stockouts. Tools like Forecast Pro can assist in improving forecasting accuracy.
Adopt Just-in-Time (JIT) Inventory: This strategy minimizes inventory costs by receiving goods only as they are needed in the production process. Toyota's JIT approach is a notable example, which you can explore here.
Supplier Management: Build strong relationships with suppliers for reliable lead times and flexibility. This includes negotiating better terms and improving communication. The Institute for Supply Management offers resources on supplier relationship management.
Use ABC Analysis: Categorize inventory into three categories (A, B, and C) based on importance and value. This helps in focusing efforts and resources on the most valuable items. The Corporate Finance Institute provides an in-depth look at ABC analysis.
Train Staff: Ensure your team is knowledgeable about inventory management practices and the use of any related systems. LinkedIn Learning offers courses on inventory management.
Continuous Improvement: Regularly review and adjust inventory management practices based on performance data and feedback. Lean methodologies and Six Sigma can guide continuous improvement efforts; information is available through the American Society for Quality.
By following these steps and utilizing the resources provided, loaders can significantly improve their inventory management processes.
How to Display Inventory Management Skills on Your Resume
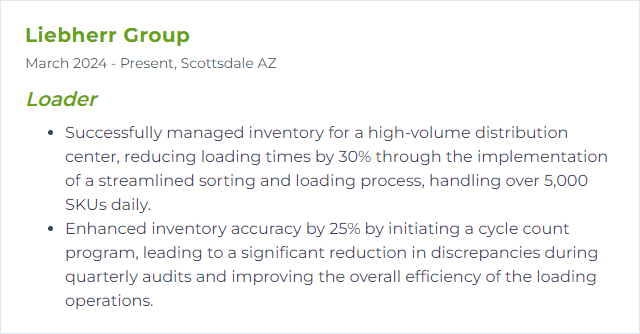
4. RF Scanners
RF Scanners, in the context of a Loader's work, are handheld devices used to wirelessly capture and transmit data about products or packages, facilitating real-time tracking and inventory management during the loading and unloading process.
Why It's Important
RF scanners are important for loaders because they enable accurate and efficient tracking of inventory and shipments, ensuring the right items are loaded onto the correct transport vehicles, thereby minimizing errors and improving overall logistics efficiency.
How to Improve RF Scanners Skills
To improve RF (Radio Frequency) scanners for loaders, focus on enhancing hardware robustness, software efficiency, and user ergonomics.
- Hardware Robustness: Use durable materials and water-resistant designs to withstand harsh loading environments.
- Software Efficiency: Integrate fast decoding algorithms for quicker scans and real-time data synchronization to improve inventory tracking.
- User Ergonomics: Incorporate lightweight designs and intuitive interfaces for ease of use during long shifts.
By addressing these key areas, RF scanners can become more effective tools for loaders, enhancing productivity and accuracy in logistics operations.
How to Display RF Scanners Skills on Your Resume
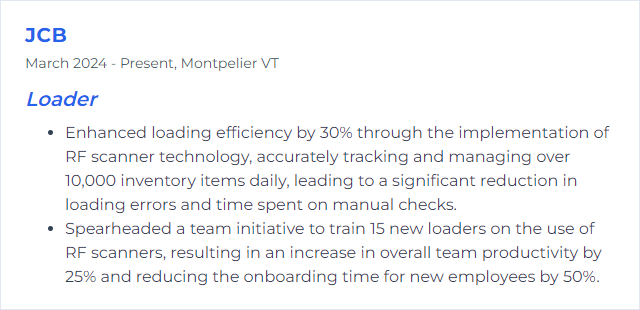
5. Warehouse Management Systems (WMS)
A Warehouse Management System (WMS) is a software solution designed to optimize and manage the operations within a warehouse, including inventory tracking, picking, receiving, and shipping processes, specifically aiding loaders in efficiently locating and moving goods within the facility.
Why It's Important
A Warehouse Management System (WMS) is essential for a loader because it streamlines the process of receiving, storing, and shipping goods efficiently, minimizing manual errors, and improving productivity and accuracy in fulfilling orders.
How to Improve Warehouse Management Systems (WMS) Skills
Improving Warehouse Management Systems (WMS) for a loader involves several key strategies, aimed at enhancing efficiency, accuracy, and productivity. Here's a concise guide:
Integration with Automation Tools: Integrate your WMS with automation tools like conveyors and robotic systems to streamline loading processes.
Real-Time Inventory Tracking: Implement RFID or barcode scanning to update inventory levels in real-time, reducing errors and improving loading accuracy.
Optimize Storage Layout: Use your WMS to analyze and optimize the storage layout for quicker and more efficient loading processes.
Enhanced Training Programs: Invest in comprehensive training programs for loaders on the latest WMS features and best practices to maximize system utilization.
Implement Mobile Solutions: Equip loaders with mobile devices that access the WMS, enabling better communication and quicker decision-making on the go.
Regular System Updates and Maintenance: Ensure your WMS is always running optimally by scheduling regular updates and maintenance, incorporating new features and fixing any bugs.
Data Analysis and Continuous Improvement: Utilize the WMS's data analytics tools to track performance metrics, identifying areas for improvement and implementing changes accordingly.
By focusing on these strategies, you can substantially enhance the efficiency and productivity of your warehouse management system.
How to Display Warehouse Management Systems (WMS) Skills on Your Resume
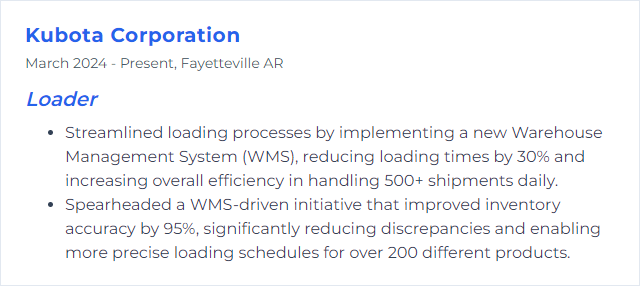
6. OSHA Safety Standards
OSHA (Occupational Safety and Health Administration) safety standards for loaders are regulations designed to protect workers involved in loading operations. These standards cover proper equipment use, maintenance, training, and procedures to minimize risks such as falls, equipment accidents, and other hazards associated with loading tasks.
Why It's Important
OSHA safety standards are crucial for loaders as they ensure a safe working environment, minimizing the risk of accidents, injuries, and fatalities by providing guidelines on proper handling techniques, equipment usage, and hazardous material management.
How to Improve OSHA Safety Standards Skills
Improving OSHA safety standards, especially for loaders, involves a multi-faceted approach focused on constant evaluation, training, and the integration of advanced technology.
Regular Evaluations and Audits: Conduct frequent safety audits and risk assessments to identify potential hazards and areas for improvement. Utilize the OSHA Self-Inspection Checklist as a guide.
Enhanced Training Programs: Implement ongoing training programs that are job-specific and include hands-on simulations. OSHA offers training resources, which can be found here.
Adoption of New Technologies: Integrate wearable technology to monitor workers' physical conditions and fatigue levels. Explore OSHA's recommendations on Innovative Workplace Safety Accommodations.
Engagement and Communication: Establish a culture of safety by actively involving employees in safety discussions and decisions. OSHA's Worker Participation Guide provides strategies for effective engagement.
Emergency Preparedness: Develop and regularly update emergency action plans. Training on these plans should be conducted periodically. Refer to OSHA's guidelines on Emergency Action Plans.
By focusing on these key areas, businesses can work towards not just meeting but exceeding OSHA safety standards for loaders, ensuring a safer working environment for all employees.
How to Display OSHA Safety Standards Skills on Your Resume
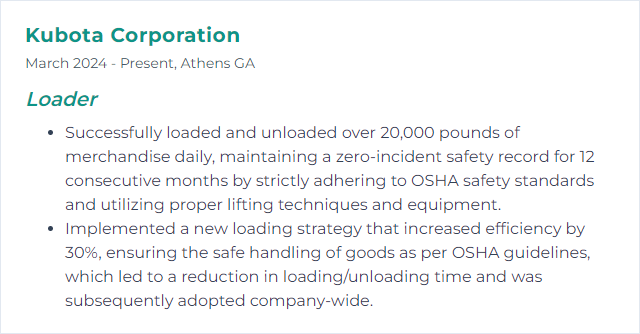
7. Hazardous Materials Handling
Hazardous Materials Handling, in the context of a Loader, involves the safe and compliant loading, unloading, securing, and transporting of materials that are deemed hazardous (such as chemicals, explosives, flammable liquids, radioactive items, etc.) according to regulatory standards, to prevent accidents or harm to people, property, and the environment.
Why It's Important
Hazardous materials handling is crucial for a loader to ensure personal safety, prevent environmental contamination, and comply with legal regulations, thereby safeguarding public health and avoiding legal consequences.
How to Improve Hazardous Materials Handling Skills
Improving hazardous materials handling, especially for a loader, involves a combination of proper training, equipment, and procedures. Here’s a concise guide:
Training: Ensure comprehensive training on hazardous materials handling, including identification, risks, and safety measures as per OSHA guidelines.
Use of Proper Equipment: Invest in appropriate PPE (Personal Protective Equipment) such as gloves, goggles, and respirators to protect against specific hazards.
Material Safety Data Sheets (MSDS): Always refer to MSDS/SDS for specific handling, storage, and disposal instructions. NIOSH provides resources for understanding chemical risks.
Emergency Procedures: Familiarize with and follow emergency response procedures in case of accidental spills or exposure.
Proper Labeling and Storage: Ensure all materials are correctly labeled and stored in accordance with DOT guidelines.
Regular Inspections and Maintenance: Conduct regular inspections of handling equipment and storage areas to identify and rectify potential hazards.
Improving hazardous materials handling is crucial for safety and compliance, requiring ongoing attention to training, equipment, and procedures.
How to Display Hazardous Materials Handling Skills on Your Resume
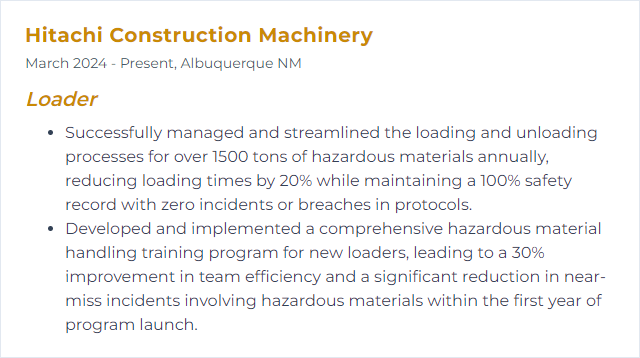
8. Shipping & Receiving
Shipping and Receiving, in the context of a Loader, involves the process of loading goods onto transport vehicles for dispatch (shipping) and unloading goods from incoming vehicles for storage or processing (receiving).
Why It's Important
Shipping and Receiving is crucial as it ensures the accurate and timely dispatch of goods to customers and the proper receipt of incoming goods for inventory. For a Loader, this process is vital for managing the physical movement and documentation of products, preventing errors, delays, and damage, thereby maintaining operational efficiency and customer satisfaction.
How to Improve Shipping & Receiving Skills
Improving Shipping & Receiving for a Loader involves streamlining processes, ensuring accurate labeling, and communicating effectively. Here's a concise guide:
Streamline Processes: Adopt lean management techniques to minimize waste and reduce loading times. Implement tools that automate and optimize workflow.
Accurate Labeling: Use barcode scanning and RFID tags for accurate tracking and to minimize errors. Labeling best practices can significantly reduce misshipments.
Effective Communication: Utilize communication tools to ensure real-time updates between loaders, drivers, and warehouse management. Collaboration tools can enhance coordination.
Safety Training: Ensure all loaders are trained on safety protocols to reduce accidents and improve efficiency. OSHA’s guidelines offer a comprehensive approach to safety in warehousing.
Equipment Maintenance: Regularly maintain and upgrade loading equipment to keep operations running smoothly. Preventive maintenance reduces downtime.
Feedback Loop: Establish a system for feedback from loaders to management to continually refine processes. Feedback systems can drive continuous improvement.
Implementing these steps can significantly improve efficiency and accuracy in Shipping & Receiving for loaders.
How to Display Shipping & Receiving Skills on Your Resume
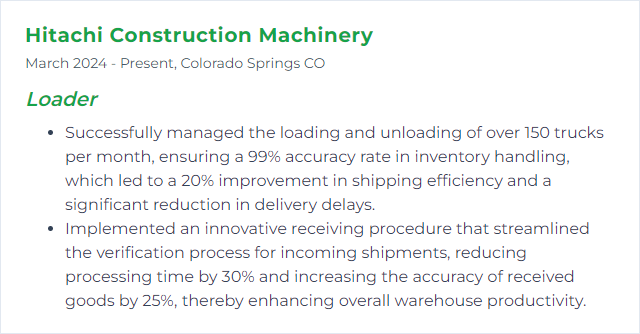
9. Order Picking
Order picking is the process of selecting and gathering items from a warehouse as specified in customer orders, preparing them for shipment. For a loader, it involves accurately collecting the specified products from storage locations to fulfill these orders for packing and delivery.
Why It's Important
Order picking is crucial for a Loader because it directly affects the accuracy and efficiency of fulfilling customer orders, ensuring the right products are delivered on time, thereby maintaining customer satisfaction and operational productivity.
How to Improve Order Picking Skills
Improving order picking involves enhancing accuracy, speed, and efficiency in the process of selecting and assembling products for shipment. Here's a concise guide for a loader to enhance order picking:
Optimize Warehouse Layout: Rearrange the warehouse to ensure fast-moving items are closer to the packing area. Utilize vertical space and consider the implementation of zoning and batch picking strategies.
Implement Technology: Use Warehouse Management Systems (WMS) to automate processes and reduce manual errors. Barcode scanning and RFID tags can significantly speed up item verification and reduce picking errors.
Adopt Picking Strategies: Implement picking methods like zone picking, batch picking, or wave picking based on your warehouse operations. Each has its benefits and can be researched further through logistics resources.
Train and Equip Your Staff: Regular training on best practices and providing the right tools, such as comfortable scanning devices, can improve efficiency. Consider gamifying the process to boost morale and productivity.
Continuous Improvement: Regularly review picking processes and feedback from staff to identify bottlenecks and areas for improvement. Implement lean management techniques to reduce waste and improve workflows.
By focusing on these areas, loaders can significantly impact the efficiency and accuracy of order picking operations.
How to Display Order Picking Skills on Your Resume
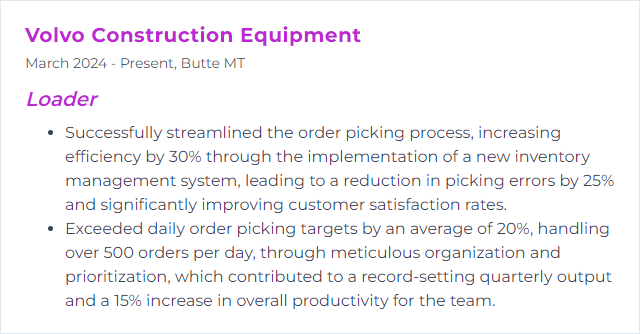
10. Container Loading
Container loading involves the process of efficiently arranging and securing goods within a shipping container for transport, ensuring optimal space utilization and safety of the items during the journey.
Why It's Important
Container loading is crucial because it ensures the safe, efficient, and optimal use of space, reducing shipping costs and minimizing the risk of damage during transit. This directly impacts the loader's ability to meet delivery schedules and maintain cargo integrity.
How to Improve Container Loading Skills
To improve container loading, follow these concise steps:
- Plan Ahead: Use container loading software for efficient space utilization.
- Load Heavy Items First: This ensures stability. Distribute weight evenly across the container floor.
- Use Loading Equipment: Equipments like forklifts and pallet jacks speed up the process.
- Stack Smartly: Stack items in tiers, placing heavier boxes at the bottom. Use loading diagrams as guides.
- Secure the Cargo: Use straps and load bars to prevent movement during transport.
- Maximize Space: Fill in gaps with smaller items to maximize space and minimize shifting.
- Check Weight Limits: Ensure you're within the container's weight limit to avoid penalties.
By planning, using the right tools, and following these practices, you can significantly improve container loading efficiency.
How to Display Container Loading Skills on Your Resume
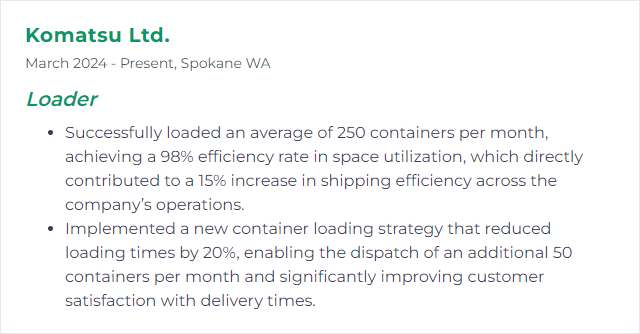
11. Supply Chain Logistics
Supply Chain Logistics involves the planning, implementation, and control of the movement and storage of goods, services, and related information from the point of origin to the point of consumption to meet customer requirements. For a Loader, it specifically refers to the physical handling, loading, and unloading of goods within this process, ensuring that items are efficiently, safely, and accurately moved and tracked through the supply chain.
Why It's Important
Supply chain logistics is crucial because it ensures the efficient and timely movement and storage of goods from suppliers to customers. For a loader, it means organizing and managing the loading process effectively to minimize delays, reduce costs, and ensure products reach their destination safely and on time, directly impacting customer satisfaction and business success.
How to Improve Supply Chain Logistics Skills
Improving supply chain logistics, especially from the perspective of a loader, involves optimizing loading processes, ensuring accurate and timely inventory tracking, and enhancing communication and collaboration across the supply chain. Here are concise strategies:
Implement Efficient Loading Techniques: Adopt methods like cross-docking and containerization to reduce handling and improve loading speed. Learn more about loading techniques.
Use Advanced Tracking Systems: Employ RFID or IoT-based systems for real-time tracking of goods, improving inventory accuracy and visibility. Explore advanced tracking systems.
Optimize Route Planning: Utilize intelligent route planning software to ensure the most efficient transportation routes, saving time and reducing costs. Read about route optimization.
Enhance Communication: Implement collaborative platforms that allow seamless communication between loaders, drivers, warehouse staff, and management, improving coordination and efficiency. Discover communication tools.
Continual Training and Development: Regular training for loaders on best practices, safety, and new technologies ensures a skilled workforce capable of adapting to changing demands. Understand the importance of training.
Implement Lean Principles: Adopt lean management techniques to minimize waste and streamline operations, focusing on adding value for the customer. Lean principles in logistics.
By focusing on these areas, a loader can significantly contribute to enhancing the efficiency and effectiveness of supply chain logistics.
How to Display Supply Chain Logistics Skills on Your Resume
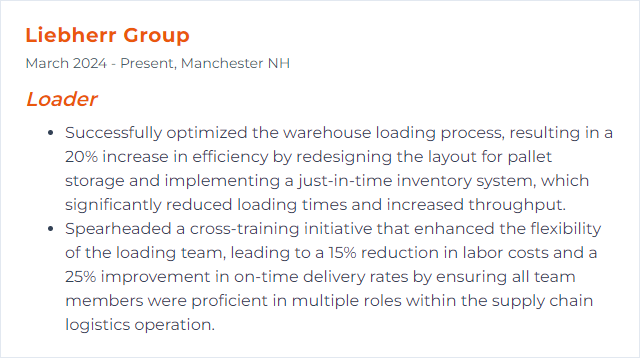
12. Quality Control Procedures
Quality Control Procedures for a Loader involve systematic processes and checks designed to ensure the loader operates safely and efficiently, meets specified standards, and performs its intended functions without failures or defects. These procedures include routine inspections, maintenance, verification of operational capabilities, and adherence to safety and performance guidelines.
Why It's Important
Quality Control Procedures are important for a Loader to ensure the correct, safe, and efficient handling of materials, minimizing the risk of damage, accidents, and delays, thereby guaranteeing customer satisfaction and maintaining operational standards.
How to Improve Quality Control Procedures Skills
Improving Quality Control (QC) procedures for a loader involves a series of steps aimed at enhancing the efficiency and effectiveness of the loading process, ensuring that goods are handled safely, and minimizing errors. Here’s a very short and concise guide to improving QC procedures for a loader:
Standardize Processes: Establish clear, standardized operating procedures for loading operations. ISO offers guidelines that can help in setting these standards.
Training and Certification: Ensure all operators are properly trained and certified. Continuous training programs can be facilitated through platforms like Coursera which offers courses on quality control and operations management.
Implement Checklists: Use checklists for pre-loading, loading, and post-loading inspections. Tools like SafetyCulture (iAuditor) provide customizable checklists.
Adopt Technology: Use technology like RFID tags and barcode scanners for accurate tracking and management of goods. Information on such technologies can be found through GS1.
Regular Maintenance: Schedule regular maintenance checks for the loader and other equipment to prevent breakdowns. Guidelines for maintenance can be found on manufacturers' websites, such as Caterpillar.
Feedback Loop: Establish a feedback loop with all stakeholders to continuously identify areas for improvement. Tools like SurveyMonkey can facilitate gathering feedback efficiently.
Quality Audits: Conduct regular quality audits to ensure adherence to QC procedures. Organizations like ASQ provide resources and guidelines on how to conduct effective quality audits.
By following these steps, you can significantly improve the quality control procedures for a loader, ensuring safer, more efficient operations.
How to Display Quality Control Procedures Skills on Your Resume
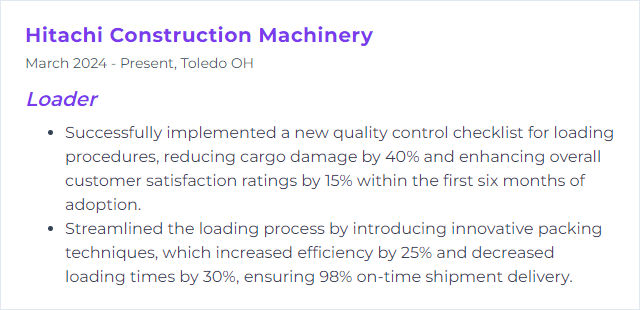