Top 12 Stockroom Clerk Skills to Put on Your Resume
In today's competitive job market, standing out as a stockroom clerk requires showcasing a unique set of skills on your resume that distinguishes you from other candidates. Mastering and highlighting these top skills not only demonstrates your proficiency in stockroom management but also signals to employers your capability to contribute effectively to their operations.
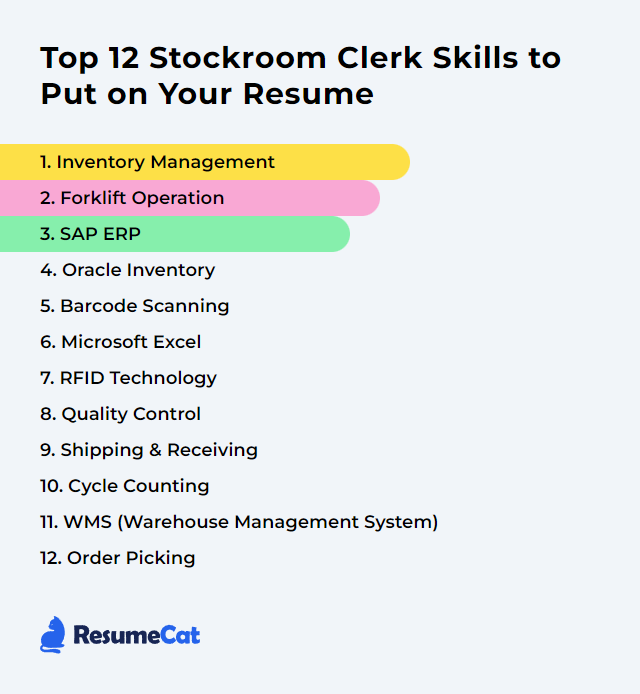
Stockroom Clerk Skills
- Inventory Management
- Forklift Operation
- SAP ERP
- Oracle Inventory
- Barcode Scanning
- Microsoft Excel
- RFID Technology
- Quality Control
- Shipping & Receiving
- Cycle Counting
- WMS (Warehouse Management System)
- Order Picking
1. Inventory Management
Inventory management, in the context of a Stockroom Clerk, involves tracking, organizing, and controlling stock levels to ensure adequate supply without overstocking, optimizing storage space, and maintaining accurate inventory records.
Why It's Important
Inventory management is crucial for a Stockroom Clerk as it ensures accurate tracking and control of stock levels, minimizes storage costs, prevents stockouts or overstocking, and improves order fulfillment efficiency, directly impacting customer satisfaction and the company's financial health.
How to Improve Inventory Management Skills
Improving inventory management, especially for a Stockroom Clerk, involves a few key strategies that can streamline operations and ensure efficiency:
Implement an Inventory Management System: Utilize software that allows for real-time tracking of stock levels, order management, and forecasting. Square and Zoho Inventory are popular options.
Regular Audits: Periodically compare physical stock counts with recorded inventory to identify discrepancies. This practice ensures data accuracy.
FIFO (First In, First Out): Ensure older stock is used or sold before newer stock, reducing the risk of obsolescence. Shopify's guide on FIFO provides insights on implementing this method.
Set Reorder Points: Establish minimum stock levels that trigger reordering to prevent stockouts without overstocking. Tools like TradeGecko can help calculate and manage these points.
Supplier Management: Develop strong relationships with suppliers for reliable lead times and possibly negotiate better terms. QuickBooks offers strategies for managing supplier relationships effectively.
Continuous Improvement: Regularly review and adjust inventory practices based on performance analytics and feedback. Online resources like APICS provide continuous learning and improvement strategies in supply chain and inventory management.
By adopting these strategies, a Stockroom Clerk can significantly improve the efficiency and accuracy of inventory management.
How to Display Inventory Management Skills on Your Resume
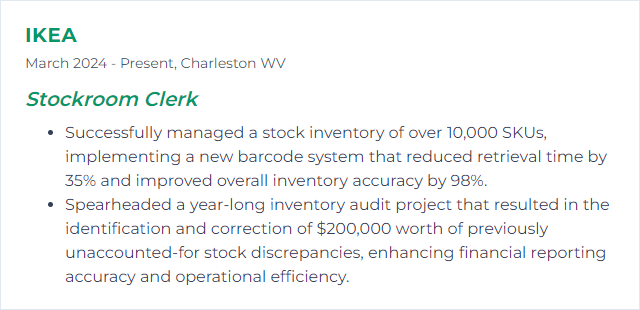
2. Forklift Operation
Forklift operation for a stockroom clerk involves safely using a forklift to move, lift, and position large and heavy inventory items within a storage facility, ensuring efficient handling and organization of stock.
Why It's Important
Forklift operation is vital for a Stockroom Clerk as it enables efficient movement, stacking, and retrieval of large or heavy inventory, enhancing productivity and ensuring safety in the storage area.
How to Improve Forklift Operation Skills
Improving forklift operation, especially for a Stockroom Clerk, involves focusing on safety, efficiency, and ongoing training. Here are concise strategies:
Prioritize Safety: Ensure adherence to OSHA's safety guidelines for forklift operation. This includes wearing proper safety gear and performing pre-operation checks.
Efficiency in Organization: Streamline stockroom layout for optimal forklift maneuverability. Efficient layout planning can significantly reduce operation time.
Regular Maintenance: Keep forklifts in top condition by following the manufacturer's maintenance schedule. This maintenance checklist offers a good starting point.
Continuous Training: Enroll in ongoing training programs to stay updated on the latest operation techniques and safety standards. Free online courses can be a valuable resource.
Use Technology: Implement technology like RFID for inventory tracking, which can reduce loading and unloading times. Explore RFID benefits for warehouse operations.
By focusing on these areas, a Stockroom Clerk can significantly improve forklift operation, contributing to a safer and more efficient workplace.
How to Display Forklift Operation Skills on Your Resume
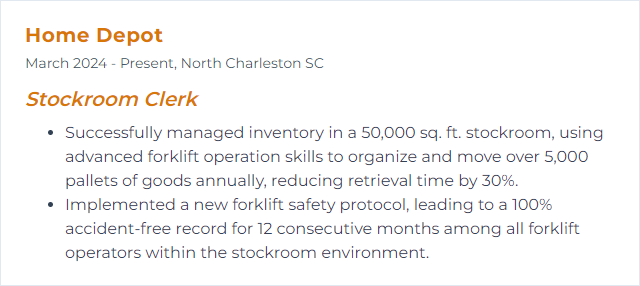
3. SAP ERP
SAP ERP is a comprehensive enterprise resource planning software that helps organizations manage and integrate their business processes, including inventory and stock management, facilitating efficient and accurate tracking, ordering, and distribution of materials for Stockroom Clerks.
Why It's Important
SAP ERP is important for a Stockroom Clerk because it streamlines inventory management, ensuring accurate tracking of stock levels, orders, and deliveries, leading to efficient operations and cost savings.
How to Improve SAP ERP Skills
Improving SAP ERP for a Stockroom Clerk involves enhancing inventory management, data accuracy, and process efficiency. Here are concise strategies:
Implement Barcode Scanning: Integrate barcode scanning to expedite data entry, reduce errors, and improve inventory tracking. SAP Extended Warehouse Management supports this feature.
Automate Reordering: Set up automatic reordering levels within SAP to maintain optimal inventory levels at all times. This minimizes stockouts and overstock situations. SAP Inventory Management can facilitate this process.
Customize Dashboards: Customize SAP dashboards to display critical stockroom metrics (e.g., inventory levels, pending orders) for real-time decision-making. SAP Fiori offers user-friendly interfaces for personalized dashboards.
Use SAP Fiori Apps: Implement SAP Fiori apps for intuitive and mobile-friendly access to SAP ERP functions, enabling stockroom clerks to perform tasks efficiently on the go. SAP Fiori for SAP ERP enhances user experience.
Enhance Training: Ensure continuous training on SAP ERP updates and best practices for stockroom clerks to maximize the system's utility. SAP offers training and certification programs.
Implement IoT for Real-Time Tracking: Utilize IoT devices to track stock movement in real-time, improving inventory accuracy and visibility. SAP's Internet of Things (IoT) solutions can be integrated for this purpose.
By focusing on these strategies, a Stockroom Clerk can significantly improve efficiency and accuracy in inventory management using SAP ERP.
How to Display SAP ERP Skills on Your Resume
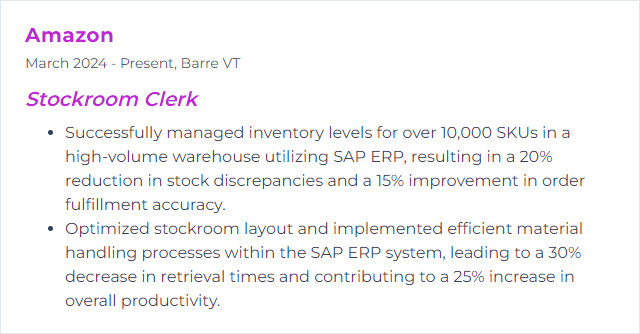
4. Oracle Inventory
Oracle Inventory is a comprehensive system that allows stockroom clerks to manage and track all aspects of inventory, including stock levels, transactions, and locations, ensuring accurate and efficient inventory control and management.
Why It's Important
Oracle Inventory is important for a Stockroom Clerk as it provides real-time, accurate inventory data, streamlining stock management, optimizing stock levels, and improving order fulfillment efficiency.
How to Improve Oracle Inventory Skills
To improve Oracle Inventory as a Stockroom Clerk, focus on the following key areas:
Data Accuracy: Ensure all inventory transactions are accurately recorded in real-time. This includes proper documentation of receipts, issues, and adjustments. Oracle's Inventory Management offers tools for precise tracking.
Training: Enhance your understanding of Oracle Inventory functionalities through official Oracle Training and certification programs. This enables more efficient use of the system's features.
Cycle Counting: Regularly participate in cycle counts to maintain inventory accuracy. Oracle Inventory supports cycle counting processes which can be scheduled and managed for efficiency. Learn more about cycle counting.
Inventory Optimization: Utilize Oracle Inventory's optimization tools to maintain optimal stock levels, reducing excess and shortages. This involves understanding and setting proper min-max levels based on historical data. Oracle Inventory Optimization can guide you.
Reporting and Analysis: Regularly generate and analyze reports for inventory performance, discrepancies, and trends. Oracle Inventory provides comprehensive reporting tools that can help identify areas for improvement. Oracle BI Documentation may offer insights into leveraging data for decision-making.
Collaboration: Coordinate with other departments (e.g., purchasing, sales) to ensure inventory data aligns with business needs. Oracle Inventory's integration capabilities facilitate communication across different business functions.
Technology Utilization: Embrace new technologies such as RFID or barcode scanning to streamline inventory tracking and reduce manual errors. Oracle Inventory supports integration with various technologies for efficient data capture. Explore Oracle Technologies.
By focusing on these areas and leveraging Oracle Inventory's capabilities, you can significantly improve inventory management as a Stockroom Clerk.
How to Display Oracle Inventory Skills on Your Resume
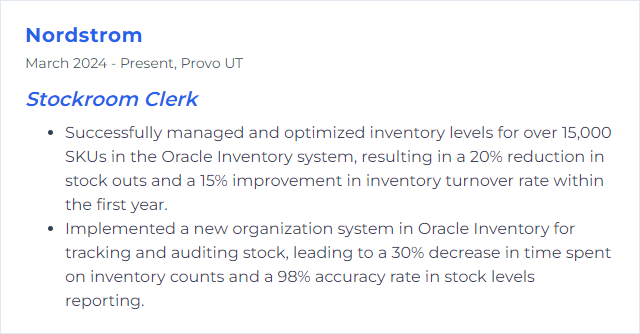
5. Barcode Scanning
Barcode scanning is the process of using a barcode reader to capture and decode information from a barcode label attached to an item, enabling efficient inventory tracking and management in a stockroom.
Why It's Important
Barcode scanning is crucial for a Stockroom Clerk as it streamlines inventory management, ensures accurate tracking of stock levels, and speeds up the processing of incoming and outgoing goods, reducing errors and saving time.
How to Improve Barcode Scanning Skills
To enhance barcode scanning efficiency for a stockroom clerk, follow these concise steps:
Choose the Right Scanner: Select a scanner that suits the size and type of barcodes used in your inventory. Handheld scanners are versatile for various environments.
Optimize Barcode Quality: Ensure barcodes are clear and undamaged. Printing high-quality labels can be achieved with specialized label printers.
Improve Lighting: Proper lighting can significantly increase scanning accuracy. Installing LED lights in the stockroom can help.
Train Staff: Proper training on the optimal angles and distances for scanning can reduce errors. Quick reference guides or online tutorials can be beneficial.
Implement Software Solutions: Use inventory management software that integrates smoothly with your scanning system for real-time updates. Solutions like Fishbowl Inventory can streamline operations.
Regular Maintenance: Keep your scanners clean and check for software updates regularly. Manufacturer's guidelines, found on their official websites, are a great resource for maintenance tips.
By following these steps, stockroom clerks can significantly improve the efficiency and accuracy of barcode scanning operations.
How to Display Barcode Scanning Skills on Your Resume
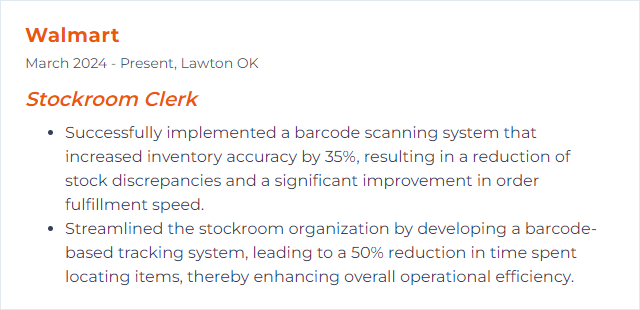
6. Microsoft Excel
Microsoft Excel is a spreadsheet program used for organizing, tracking, and managing data, ideal for tasks like inventory management and order tracking in a stockroom environment.
Why It's Important
Microsoft Excel is essential for a Stockroom Clerk as it enables efficient inventory tracking, data analysis, and reporting, facilitating accurate stock management and operational decision-making.
How to Improve Microsoft Excel Skills
To improve Microsoft Excel skills as a Stockroom Clerk, focus on mastering the following areas:
Inventory Management: Learn to create and manage inventory lists efficiently. Utilize formulas for automatic calculations of stock levels, reorder points, and inventory valuation. Excel Inventory Management Techniques
Data Analysis: Enhance your ability to analyze stock movement, forecast future inventory needs, and identify trends using PivotTables and charts. Getting Started with PivotTables
Conditional Formatting: Apply conditional formatting to highlight critical inventory levels, expired products, and other key indicators at a glance. Conditional Formatting Basics
Barcode Integration: Learn to generate and integrate barcodes for efficient stock management. This simplifies tracking and reduces errors. Generating Barcodes in Excel
Excel Shortcuts: Become proficient with keyboard shortcuts to navigate and perform tasks faster, significantly boosting your productivity. Excel Keyboard Shortcuts
Excel Training Courses: Invest time in Excel training courses tailored to inventory and stock management for a comprehensive skill upgrade. Excel for Inventory Management Course
By focusing on these areas, you’ll enhance your efficiency and accuracy in managing stockroom operations with Microsoft Excel.
How to Display Microsoft Excel Skills on Your Resume
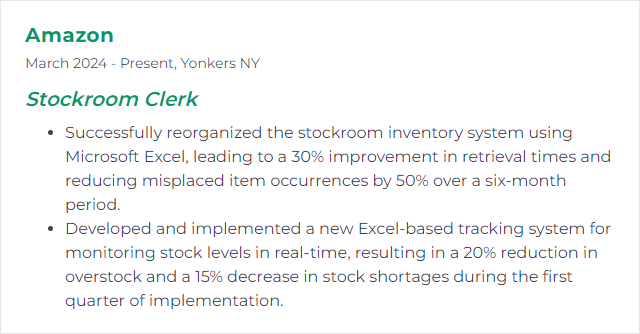
7. RFID Technology
RFID technology, or Radio-Frequency Identification, uses electromagnetic fields to automatically identify and track tags attached to objects, such as inventory in a stockroom. These tags contain electronically stored information that can be read from a distance, streamlining the process of managing and locating stock for a Stockroom Clerk.
Why It's Important
RFID technology is crucial for a Stockroom Clerk as it enables efficient, real-time tracking and management of inventory, significantly reducing manual counting errors and saving time on stock audits.
How to Improve RFID Technology Skills
To enhance RFID technology for a Stockroom Clerk, focus on the following concise strategies:
Upgrade to UHF RFID: Utilize Ultra High Frequency (UHF) RFID tags and readers for greater read range and faster data transfer, improving inventory tracking across larger stockrooms.
Integrate Software Solutions: Adopt advanced inventory management software that is compatible with RFID technology for real-time tracking and automated stock updates, reducing manual entry errors.
Enhance RFID Tag Quality: Invest in high-quality, durable RFID tags that are suitable for your stockroom environment, ensuring reliable performance over time.
Implement Multi-Antenna Systems: Set up RFID systems with multiple antennas to cover all angles in the stockroom, ensuring no blind spots and improving overall scanning efficiency.
Regular Training and Updates: Provide ongoing training for staff on the latest RFID technologies and best practices, ensuring the system is used to its full potential.
These steps will significantly improve RFID technology effectiveness for stockroom management, enhancing inventory accuracy and operational efficiency.
How to Display RFID Technology Skills on Your Resume
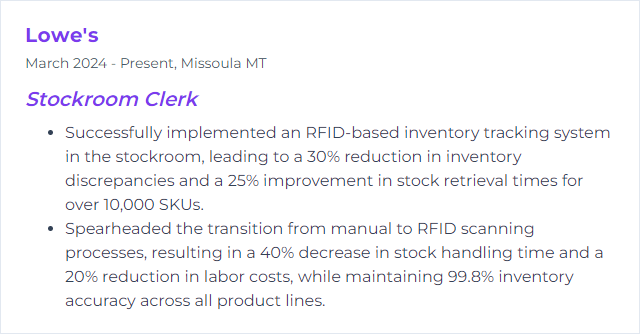
8. Quality Control
Quality Control for a Stockroom Clerk involves ensuring that incoming stock meets specified standards, accurately recording inventory levels, and maintaining the organization and cleanliness of the storage area to prevent damage or loss.
Why It's Important
Quality control is crucial for a Stockroom Clerk as it ensures that inventory is accurate, in good condition, and meets the required standards, thus minimizing errors, reducing waste, and enhancing customer satisfaction.
How to Improve Quality Control Skills
Improving Quality Control for a Stockroom Clerk involves a few key strategies:
Implement a Standard Operating Procedure (SOP): Establish clear guidelines for handling, storing, and managing inventory. Quality Control SOPs ensure consistency and minimize errors.
Use Inventory Management Software: Adopt software that tracks inventory in real-time, reducing the risk of overstocking or stockouts. This Inventory Management Guide can help choose the right tool.
Regular Training: Ensure ongoing training for stockroom clerks on best practices in inventory management and quality control. Training Resources from ASQ are invaluable.
Conduct Regular Audits: Periodic audits help identify discrepancies and areas for improvement. Learn how to perform effective audits with these Audit Guidelines.
Implement Quality Control Checks: Introduce random sampling and quality checks to ensure products meet standards before they leave the stockroom. Quality Control Basics provide a foundation for these checks.
Feedback Loop: Create a system for receiving and implementing feedback from staff and customers to continuously improve processes. This Feedback Guide offers insights into effective feedback mechanisms.
By focusing on these strategies, a stockroom clerk can significantly enhance quality control within their domain.
How to Display Quality Control Skills on Your Resume
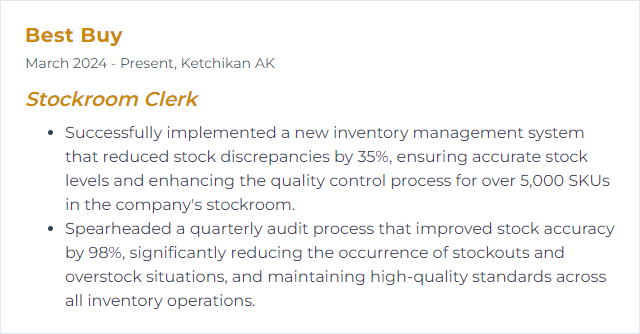
9. Shipping & Receiving
Shipping & Receiving refers to the processes of handling goods being delivered to a facility (receiving) and preparing and sending goods out of a facility (shipping). For a Stockroom Clerk, it involves tasks such as verifying incoming shipments, organizing stock, maintaining inventory levels, and preparing items for dispatch.
Why It's Important
Shipping and Receiving is crucial for a Stockroom Clerk as it ensures that the correct products arrive and are dispatched on time, maintaining inventory accuracy, order fulfillment, and customer satisfaction.
How to Improve Shipping & Receiving Skills
Improving Shipping & Receiving for a Stockroom Clerk involves enhancing efficiency, accuracy, and organization in handling inventory. Here are concise steps to achieve this:
Implement a Digital Management System: Transition from manual tracking to a digital inventory management system for real-time inventory updates and tracking.
Standardize Processes: Create standard operating procedures for handling shipments and returns to ensure consistency and reduce errors.
Use Barcode Scanning: Incorporate barcode scanning technology for quick, accurate recording of stock movements.
Regular Training: Provide ongoing training for staff on new technologies, procedures, and best practices to improve efficiency.
Implement Quality Checks: Integrate quality control checks at receiving to catch errors early and reduce future problems.
Optimize Layout: Organize the stockroom for efficient material handling and easy access to frequently used items.
Schedule Regular Audits: Conduct regular inventory audits to ensure accuracy in stock levels and identify areas for improvement.
By focusing on these areas, a Stockroom Clerk can significantly improve the efficiency and reliability of Shipping & Receiving operations.
How to Display Shipping & Receiving Skills on Your Resume
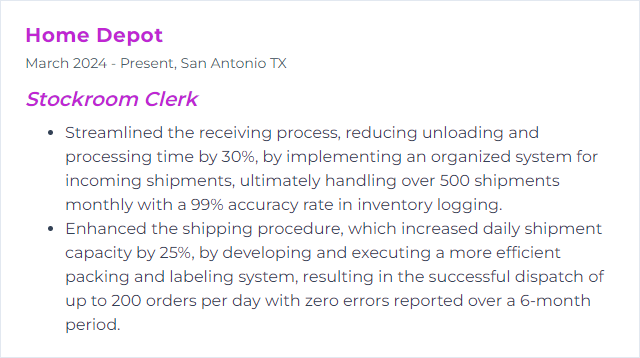
10. Cycle Counting
Cycle counting is a periodic inventory counting method where a stockroom clerk counts a small portion of the inventory regularly, instead of conducting a full inventory count at once. This process helps maintain accurate inventory records, identify discrepancies early, and minimize disruption to operations.
Why It's Important
Cycle counting is important for a Stockroom Clerk because it ensures inventory accuracy, helps identify discrepancies promptly, reduces the need for large, disruptive full inventory counts, and supports effective stock management, thus improving order fulfillment and customer satisfaction.
How to Improve Cycle Counting Skills
To improve cycle counting as a Stockroom Clerk, follow these concise strategies:
Prioritize Items: Focus on counting high-value or frequently used items more regularly. ABC analysis is a useful method to categorize items based on their importance.
Use Technology: Implement barcode or RFID scanning systems to reduce errors and speed up the counting process. This guide on barcode systems offers a good starting point.
Schedule Counts Regularly: Establish a regular schedule that doesn't interfere with peak operational hours. Here’s how to create a cycle count schedule that works.
Train Staff: Ensure all personnel involved in cycle counting are properly trained on procedures and the use of any technology. Effective training strategies can be found here.
Review and Adjust: Regularly review cycle count results and adjust strategies as needed to improve accuracy and efficiency. This article offers insights on adjusting inventory management techniques.
By focusing on these areas, you can enhance the effectiveness of cycle counting in your stockroom.
How to Display Cycle Counting Skills on Your Resume
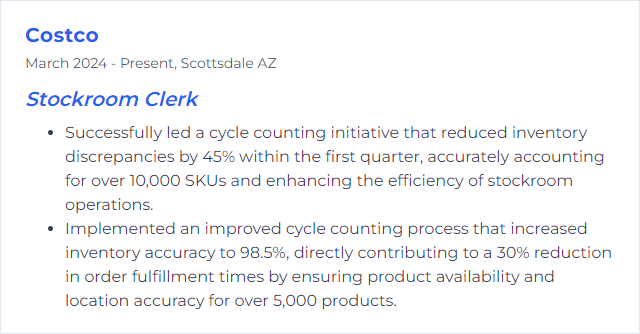
11. WMS (Warehouse Management System)
A Warehouse Management System (WMS) is a software application designed to support and optimize warehouse or stockroom operations. It helps stockroom clerks in managing inventory, tracking products' locations, and processing orders efficiently.
Why It's Important
A Warehouse Management System (WMS) is crucial for a Stockroom Clerk as it optimizes inventory control, enhances order fulfillment accuracy, and increases operational efficiency by automating and organizing stock management tasks.
How to Improve WMS (Warehouse Management System) Skills
Improving a Warehouse Management System (WMS) involves optimizing processes, integrating technology, and enhancing accuracy. Here are concise strategies tailored for a Stockroom Clerk:
Leverage Real-time Data: Implement RFID or barcode scanning to update inventory levels instantly. Zebra Technologies offers solutions that can be integrated into existing WMS for real-time tracking.
Adopt Mobile Solutions: Use mobile WMS applications to streamline operations. This allows clerks to access inventory data and update records on the go. Oracle WMS Cloud provides a comprehensive mobile solution.
Implement Voice Picking: Enhance picking efficiency and accuracy with voice-directed picking technologies. Honeywell Voice Solutions can significantly reduce errors and improve productivity.
Automate Inventory Replenishment: Set up automatic reordering based on predefined inventory levels to prevent stockouts or overstocking. Systems like NetSuite offer inventory management with automation capabilities.
Continuous Training and Feedback: Regularly train staff on new features and updates in the WMS. Encourage feedback for continuous improvement. Establishing a culture of continuous learning can be supported by platforms like LinkedIn Learning.
Analyze and Act on Data: Regularly review reports and analytics to identify bottlenecks or opportunities for improvement. Tools like Tableau can help visualize WMS data to make informed decisions.
Collaborate with Suppliers: Ensure your WMS can integrate with systems used by suppliers for smoother restocking processes. SAP Extended Warehouse Management offers features for better collaboration.
By focusing on these areas, a Stockroom Clerk can significantly contribute to the efficiency and accuracy of a Warehouse Management System.
How to Display WMS (Warehouse Management System) Skills on Your Resume
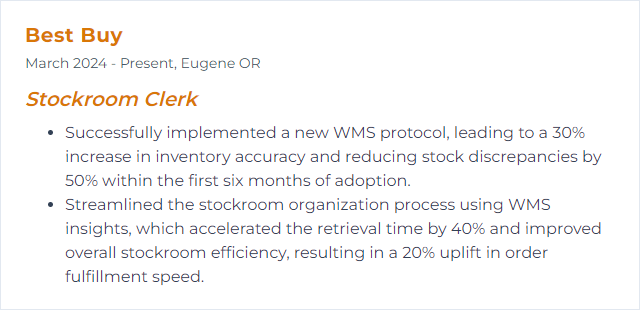
12. Order Picking
Order picking is the process of retrieving and collecting items from a stockroom or warehouse to fulfill customer orders.
Why It's Important
Order picking is crucial for a Stockroom Clerk because it directly impacts the accuracy, efficiency, and speed of fulfilling customer orders, ensuring customer satisfaction and maintaining inventory accuracy.
How to Improve Order Picking Skills
Improving order picking involves optimizing processes and utilizing technology to increase efficiency and accuracy. Here are concise strategies:
- Implement an Efficient Layout: Design the stockroom layout to minimize travel time. Arrange items based on their picking frequency.
- Use Barcode Scanning: Employ barcode scanning technology to reduce errors and speed up the picking process.
- Adopt Batch Picking: Group similar orders to reduce the number of trips. This method is effective for handling multiple orders simultaneously.
- Install Pick-to-Light Systems: A pick-to-light system guides pickers to the correct item locations, improving speed and accuracy.
- Regular Training: Continuously train staff on best practices and tool usage to enhance their efficiency.
- Optimize Inventory Management: Use an Inventory Management System to maintain optimal stock levels and reduce out-of-stock situations.
- Continuous Improvement: Regularly review and analyze the order picking process to identify and implement improvements.
Implementing these strategies can significantly improve the efficiency and accuracy of the order picking process in a stockroom.
How to Display Order Picking Skills on Your Resume
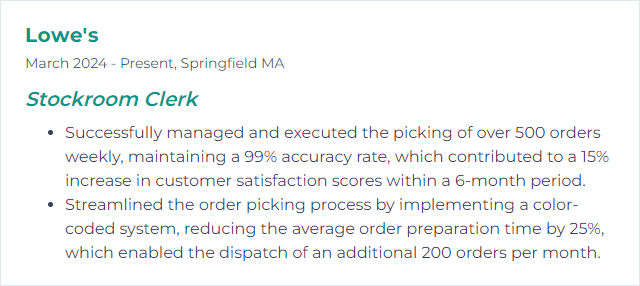