Top 12 Stockroom Associate Skills to Put on Your Resume
In today's competitive job market, standing out as a stockroom associate requires showcasing a blend of technical know-how and soft skills on your resume. Highlighting the top skills that demonstrate your efficiency, organization, and ability to contribute to seamless operations can significantly elevate your candidacy and catch the attention of potential employers.
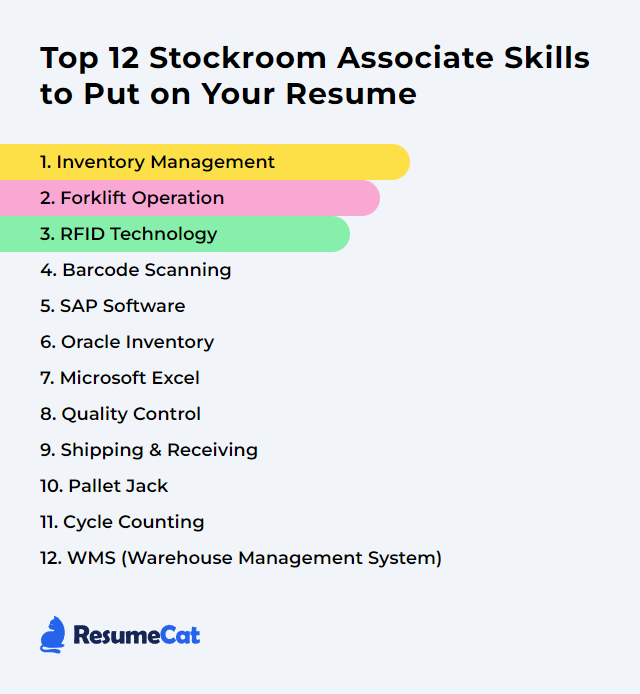
Stockroom Associate Skills
- Inventory Management
- Forklift Operation
- RFID Technology
- Barcode Scanning
- SAP Software
- Oracle Inventory
- Microsoft Excel
- Quality Control
- Shipping & Receiving
- Pallet Jack
- Cycle Counting
- WMS (Warehouse Management System)
1. Inventory Management
Inventory management involves tracking, organizing, and controlling stock levels and movements in a stockroom to ensure adequate supply meets demand, minimize excess, and maintain accurate records.
Why It's Important
Inventory management is crucial for a Stockroom Associate as it ensures accurate tracking of stock levels, optimizes storage space utilization, facilitates timely restocking, and minimizes excess inventory, leading to improved efficiency and customer satisfaction.
How to Improve Inventory Management Skills
Improving inventory management, especially for a Stockroom Associate, involves a few key strategies focused on accuracy, efficiency, and organization. Here are succinct tips to enhance your inventory management process:
Implement an Inventory Management System: Use software solutions to automate tracking and manage stock levels efficiently.
Regular Audits: Conduct regular audits (cycle counting) to ensure the inventory records match the physical stock.
FIFO Method: Adopt the First-In, First-Out (FIFO) method, especially for perishable goods, to reduce waste and increase stock rotation.
Organize the Stockroom: Maintain a well-organized stockroom for easy access and to expedite the inventory process.
Training: Ensure continuous team training on inventory management best practices to improve accuracy and efficiency.
Use of Barcodes/RFID: Implement barcode or RFID technology for quicker inventory tracking and updates.
Analyze Data for Forecasting: Regularly review inventory data to forecast demand and adjust stock levels accordingly.
By incorporating these strategies, a Stockroom Associate can significantly enhance inventory management practices, leading to improved operational efficiency and customer satisfaction.
How to Display Inventory Management Skills on Your Resume
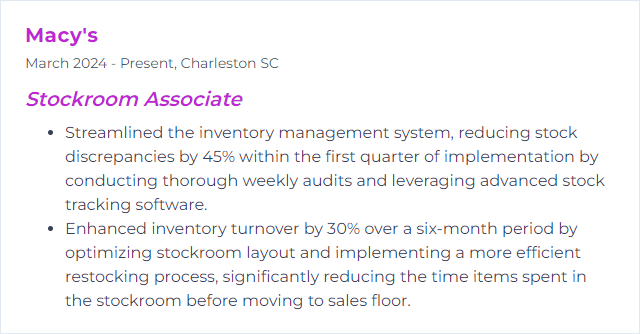
2. Forklift Operation
Forklift operation, in the context of a Stockroom Associate, involves the use of a powered industrial truck to lift and move materials, goods, or products within a warehouse or storage area, facilitating the organization, retrieval, and transportation of stock efficiently and safely.
Why It's Important
Forklift operation is crucial for a Stockroom Associate as it enables efficient, safe handling and movement of heavy inventory, optimizing storage space and improving the speed of stock retrieval and organization.
How to Improve Forklift Operation Skills
Improving forklift operation, especially for a Stockroom Associate, involves enhancing safety, efficiency, and skill set. Here are concise strategies:
Training and Certification: Ensure all operators are properly trained and certified. Regularly refresh skills with updated courses. OSHA Forklift Training offers comprehensive guidelines.
Pre-Operational Checks: Conduct daily inspections of the forklift to identify and fix issues early. Checklist Guide provides a detailed pre-use checklist.
Implement Safety Protocols: Follow strict safety guidelines, including speed limits, load capacities, and pedestrian awareness. NIOSH Safety Practices outlines essential safety practices.
Efficient Stockroom Layout: Design the storage area for easy access and navigation. Consider aisle width, stacking height, and designated pedestrian areas. Warehouse Layout Tips can help optimize the space.
Regular Maintenance: Keep the forklift in top condition with a routine maintenance schedule. Maintenance Checklist provides a template for regular upkeep.
Use of Technology: Incorporate technology such as RFID or barcode systems for inventory management, and consider advanced forklift features like automatic stopping sensors. RFID in Inventory Management explores technology applications.
By focusing on these areas, a Stockroom Associate can enhance forklift operation, contributing to a safer and more productive workplace.
How to Display Forklift Operation Skills on Your Resume
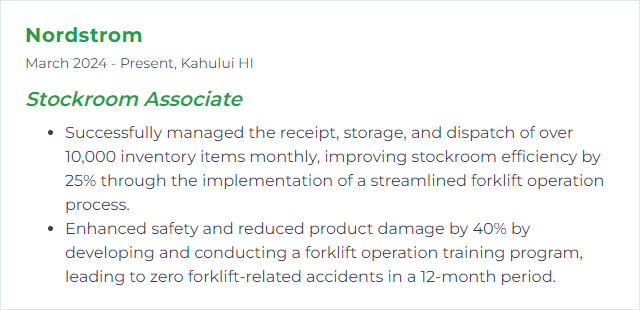
3. RFID Technology
RFID (Radio-Frequency Identification) technology uses electromagnetic fields to automatically identify and track tags attached to objects, such as inventory in a stockroom. This allows a Stockroom Associate to quickly and accurately monitor stock levels, track item locations, and manage inventory without manual counting or visual inspection.
Why It's Important
RFID technology is important for a Stockroom Associate because it enables efficient inventory management by allowing for quick, accurate tracking and locating of items in real-time without direct line-of-sight, reducing manual labor and minimizing errors.
How to Improve RFID Technology Skills
Improving RFID technology, especially for the use case of a Stockroom Associate, involves enhancing accuracy, speed, and integration capabilities. Here are concise strategies:
Enhance Read Rates: Employ advanced algorithms and antenna designs to improve the accuracy and speed of RFID tag reads, reducing inventory errors. AIM Global provides resources on the latest advancements.
Increase Tag Durability: Use more durable materials for tags to ensure they withstand rough handling and environmental conditions within the stockroom. RFID Journal often discusses innovations in tag durability.
Improve Software Integration: Ensure the RFID system seamlessly integrates with existing inventory management software for real-time tracking and updates. Explore API solutions on GS1 US for standards and integration guidance.
Expand Frequency Ranges: Utilize a broader range of frequencies to reduce interference and improve the system's versatility across different environments. Information on frequency standards is available through IEEE Xplore.
Implement Multi-Reader Coordination: Deploy algorithms that allow multiple RFID readers to work together without interference, enhancing the speed and efficiency of inventory checks. Research on multi-reader environments can be found via academic resources like Google Scholar.
Enhance Data Security: Adopt advanced encryption and authentication techniques to protect sensitive data on RFID tags from unauthorized access. The International Journal of RFID Security and Cryptography provides insights into the latest security technologies.
Train Staff: Regularly train stockroom associates on the optimal placement of tags and the best practices for using RFID equipment to maximize system effectiveness. Educational resources and courses are available at RFID4U.
By focusing on these areas, RFID technology can be significantly improved, leading to more efficient and accurate stockroom operations.
How to Display RFID Technology Skills on Your Resume
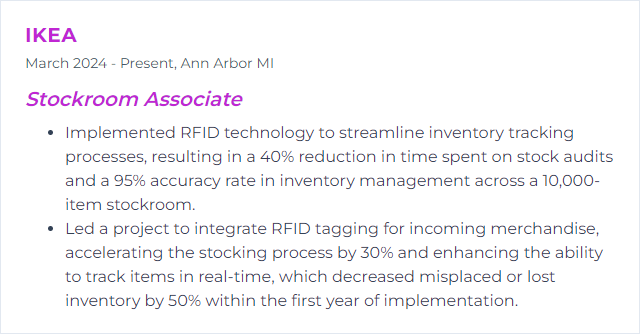
4. Barcode Scanning
Barcode scanning is a process used by Stockroom Associates to quickly capture and read information encoded in barcodes on items, enabling efficient tracking, inventory management, and easy retrieval of product data.
Why It's Important
Barcode scanning is crucial for a Stockroom Associate as it ensures accurate tracking and management of inventory, speeds up the process of locating and moving items, and minimizes errors in stock levels, thus improving overall efficiency and productivity in the stockroom.
How to Improve Barcode Scanning Skills
To improve barcode scanning as a Stockroom Associate, follow these concise strategies:
Ensure Proper Lighting: Adequate lighting enhances barcode readability. Consider adding more or adjustable lights in scanning areas.
Use High-Quality Scanners: Invest in high-quality barcode scanners that can read barcodes quickly and from varying distances. Zebra and Honeywell offer robust options.
Regularly Clean Scanners: Keep the scanner lens clean using a soft, lint-free cloth to ensure optimal performance.
Optimize Barcode Labels: Use high-contrast, undamaged labels. Printing quality matters; consider thermal printers for durability. Avery provides reliable label solutions.
Train Staff: Regularly train staff on optimal scanning techniques and ergonomics to prevent scanning errors and reduce physical strain. OSHA offers guidelines on ergonomics.
Implement Barcode Positioning Standards: Establish standards for barcode placement on items to streamline the scanning process.
Use Scanning Software Updates: Keep your scanning software updated to ensure compatibility with various barcode formats and improve scanning efficiency.
By integrating these strategies, you can significantly enhance barcode scanning efficiency in a stockroom environment.
How to Display Barcode Scanning Skills on Your Resume
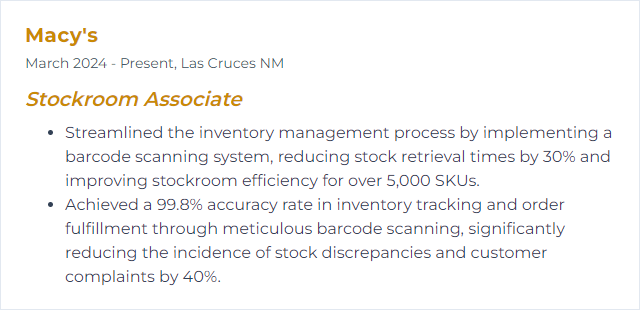
5. SAP Software
SAP software is a comprehensive enterprise resource planning (ERP) system that helps businesses manage and integrate their core processes. For a Stockroom Associate, it would facilitate inventory management, tracking, and order processing efficiently.
Why It's Important
SAP software is important for a Stockroom Associate because it streamlines inventory management, ensuring accurate tracking of stock levels, facilitating efficient order processing, and optimizing warehouse organization. This leads to improved productivity and reduced errors in stock handling.
How to Improve SAP Software Skills
Improving SAP software for a Stockroom Associate involves enhancing user experience, streamlining inventory management, and integrating mobile solutions. Here are concise steps and resources:
User Training and Support: Offer comprehensive training tailored for Stockroom Associates to improve proficiency. SAP's User Experience Learning Journey is a valuable resource.
Customize User Interface: Utilize SAP Fiori to customize and simplify the user interface, making it more intuitive for stockroom operations. Explore SAP Fiori for user-friendly designs.
Implement Mobile Solutions: Integrate SAP with mobile inventory management apps for real-time tracking and access. SAP's Mobile Services can enhance operational efficiency.
Automate Processes: Utilize SAP's automation features to streamline stockroom tasks such as inventory counting and order processing. Learn about automation in SAP through SAP Intelligent Robotic Process Automation.
Regular Data Analysis: Use SAP's analytics tools to regularly analyze stock levels, predict future inventory needs, and reduce overstock or stockouts. Explore SAP Analytics Cloud for data insights.
Feedback Loop: Establish a feedback loop with Stockroom Associates to continually identify pain points and areas for improvement within the SAP system.
How to Display SAP Software Skills on Your Resume

6. Oracle Inventory
Oracle Inventory is a comprehensive software solution designed for managing and tracking inventory levels, orders, sales, and deliveries within a business. It helps stockroom associates efficiently monitor and control stock quantities, ensuring accurate inventory records and streamlined stockroom operations.
Why It's Important
Oracle Inventory is important for a Stockroom Associate as it enables efficient management of stock levels, ensures accurate tracking of inventory movements, and streamlines order fulfillment processes, leading to improved operational efficiency and customer satisfaction.
How to Improve Oracle Inventory Skills
Improving Oracle Inventory, especially for a Stockroom Associate, involves optimizing data accuracy, streamlining processes, and leveraging Oracle Inventory's features effectively. Here are concise strategies:
Enhance Data Accuracy: Regularly audit and update inventory data to ensure accuracy. Accurate data is crucial for effective inventory management and decision-making.
Utilize Barcode Scanning: Implement barcode scanning to reduce manual data entry errors and speed up transactions. Oracle Inventory Management supports barcode scanning for efficient inventory tracking.
Leverage Mobile Applications: Use Oracle's mobile inventory management applications to perform transactions on-the-go, enhancing efficiency and flexibility. Explore Oracle Mobile Inventory Management for options.
Implement Cycle Counting: Regular cycle counting improves inventory accuracy and reduces the need for extensive physical counts. Oracle Inventory offers features to manage and schedule cycle counts effectively. Learn more about Cycle Counting in Oracle Inventory.
Optimize Replenishment Strategies: Use Oracle Inventory's advanced replenishment methods to ensure stock levels meet demand without overstocking. Strategies like Just-In-Time (JIT) can be efficiently managed within Oracle Inventory.
Enhance User Training: Ensure that Stockroom Associates are well-trained on Oracle Inventory features and best practices. Continuous training enhances user competency and inventory management efficiency.
Utilize Reports and Analytics: Take advantage of Oracle Inventory's reporting and analytics tools to make informed decisions. Regular analysis can help identify trends, inefficiencies, and opportunities for improvement.
By implementing these strategies, Stockroom Associates can significantly improve inventory management processes, making them more efficient and accurate.
How to Display Oracle Inventory Skills on Your Resume
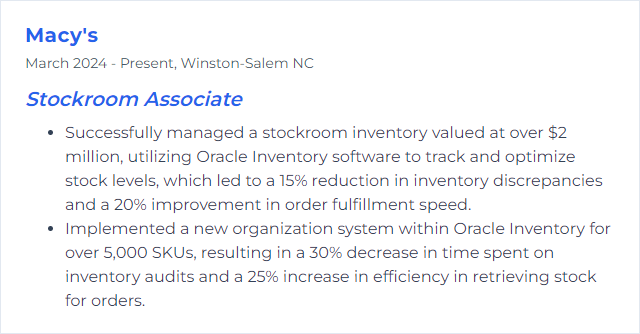
7. Microsoft Excel
Microsoft Excel is a spreadsheet program used for organizing, analyzing, and storing data, ideal for tracking inventory, orders, and sales in a stockroom.
Why It's Important
Microsoft Excel is crucial for a Stockroom Associate as it enables efficient inventory tracking, data analysis for optimizing stock levels, and facilitates the creation of reports and forecasts, ensuring accurate and streamlined stock management.
How to Improve Microsoft Excel Skills
To improve Microsoft Excel skills as a Stockroom Associate, focus on mastering the following areas:
Learn Excel Formulas and Functions: Understand how to use key formulas like
SUM
,VLOOKUP
,INDEX/MATCH
, andIF
statements for managing inventory, tracking stock levels, and calculating reorder points. Excel Formulas and Functions TutorialExplore Data Analysis Tools: Get familiar with Excel's data analysis tools such as PivotTables, which help in summarizing and analyzing large datasets to make informed inventory decisions. PivotTables Guide
Practice Data Visualization: Learn to create charts and graphs to visualize stock levels, sales trends, and inventory needs, making it easier to communicate insights with your team. Data Visualization in Excel
Understand Inventory Management Templates: Use or customize Excel templates designed for inventory management to streamline your stockroom operations. Inventory Templates
Automate Repetitive Tasks with Macros: Learn how to record and use macros for automating repetitive tasks, saving time for more critical stockroom operations. Getting Started with Macros
By focusing on these areas, you'll enhance your Excel proficiency, making you more effective in your role as a Stockroom Associate.
How to Display Microsoft Excel Skills on Your Resume
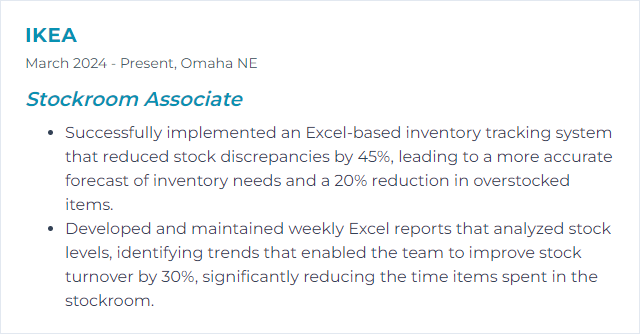
8. Quality Control
Quality Control (QC) for a Stockroom Associate involves inspecting and verifying the condition and quantity of items received, stored, and dispatched, ensuring they meet the specified standards and requirements.
Why It's Important
Quality Control is crucial for a Stockroom Associate because it ensures that inventory is accurate and in optimal condition, reducing errors and customer dissatisfaction, and maintaining the company's reputation for reliability and excellence.
How to Improve Quality Control Skills
Improving Quality Control for a Stockroom Associate involves several key steps focused on accuracy, organization, and continuous improvement. Here’s a concise guide:
Standardize Procedures: Establish clear, documented procedures for all stockroom activities to ensure consistency. OSHA provides guidelines that can help in setting up safe and efficient processes.
Implement an Inventory Management System: Use technology to track inventory accurately. Systems like Fishbowl Inventory can automate and streamline inventory management, reducing errors.
Regular Training: Ensure all stockroom associates undergo regular training on best practices, new technologies, and process improvements. LinkedIn Learning offers courses on inventory management and quality control.
Quality Checks: Conduct regular quality audits and checks to identify and rectify issues promptly. Tools like Trello can help manage and track audit schedules and findings.
Feedback Loop: Create a system for feedback from staff and customers to identify areas for improvement. Survey tools like SurveyMonkey can facilitate gathering and analyzing feedback.
Continuous Improvement: Adopt a culture of continuous improvement, using methodologies like Lean or Six Sigma, to streamline processes and eliminate waste. ASQ offers resources and certifications in these areas.
By focusing on these areas, a Stockroom Associate can significantly enhance quality control in their operations.
How to Display Quality Control Skills on Your Resume
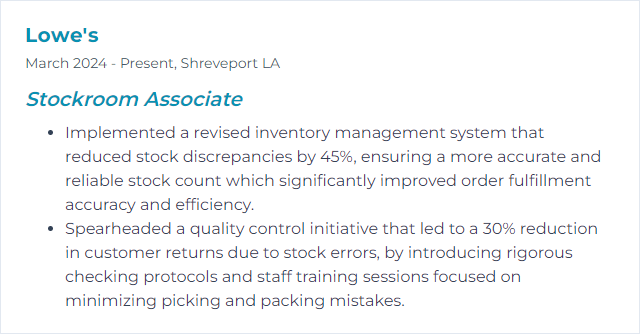
9. Shipping & Receiving
Shipping & Receiving involves handling the inflow and outflow of goods in a stockroom, including preparing items for shipment, managing incoming deliveries, and maintaining accurate inventory records.
Why It's Important
Shipping & Receiving is crucial for a Stockroom Associate as it ensures accurate tracking and management of inventory, enabling timely fulfillment of orders and maintaining stock levels to meet demand efficiently.
How to Improve Shipping & Receiving Skills
Improving Shipping & Receiving as a Stockroom Associate involves enhancing accuracy, efficiency, and organization. Here's a concise guide:
Implement an Inventory Management System: Use software to track stock levels, orders, and deliveries in real-time. Square and Zoho Inventory are good examples.
Standardize Processes: Create standard operating procedures (SOPs) for both shipping and receiving tasks to minimize errors. Resources like Bizmanualz can help in developing SOPs.
Use Barcode Scanning: Employ barcode scanning to quickly and accurately process incoming and outgoing goods. Barcodes Inc. offers a variety of scanning solutions.
Organize the Stockroom: Maintain a clean and organized stockroom. Use shelving and labeling systems to easily locate items. Uline provides various storage solutions.
Train Continuously: Regular training sessions on the latest best practices, technology, and equipment use are vital. LinkedIn Learning offers courses relevant to logistics and inventory management.
Monitor and Improve: Regularly review processes, solicit feedback from the team, and implement improvements. Tools like Trello can help in tracking tasks and projects.
By focusing on these areas, you can significantly improve the efficiency and accuracy of your shipping and receiving operations.
How to Display Shipping & Receiving Skills on Your Resume
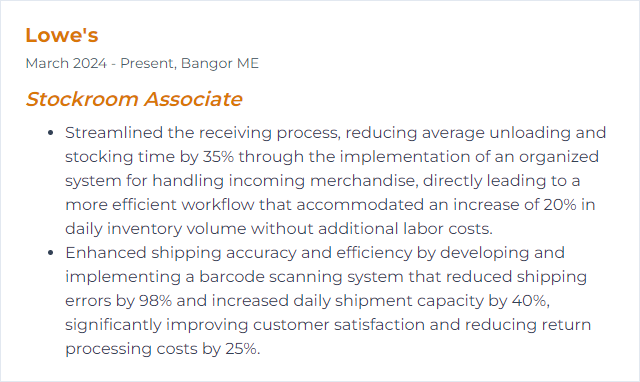
10. Pallet Jack
A pallet jack is a manual or powered tool used by stockroom associates to lift and move pallets of goods, facilitating easier transport and organization of inventory within a warehouse or stockroom.
Why It's Important
A pallet jack is crucial for a Stockroom Associate because it allows for the efficient and safe movement of heavy loads and pallets within the stockroom, optimizing space utilization and enhancing productivity.
How to Improve Pallet Jack Skills
Improving the efficiency and safety of using a pallet jack in a stockroom involves a blend of proper training, maintenance, and ergonomic practices. Here are concise tips for a Stockroom Associate:
Get Proper Training: Ensure you're trained on the specific model of pallet jack you're using. Understanding its capacity, controls, and safety features is crucial. Many manufacturers offer online manuals and guides.
Regular Maintenance: Conduct regular checks and maintenance on the pallet jack. Look for issues like hydraulic leaks, worn wheels, or structural damage. Manufacturers like Crown provide maintenance guidelines.
Use Correctly: Always push (rather than pull) the pallet jack when moving it to reduce strain on your back. For more ergonomic tips, reference OSHA’s guidelines.
Keep Pathways Clear: Ensure aisles and pathways are free of obstacles before moving loads. This reduces the risk of accidents and increases efficiency.
Wear Appropriate Safety Gear: Use gloves for better grip and steel-toed shoes for foot protection.
Load Properly: Distribute weight evenly on the pallet and ensure it's secure before moving. This prevents tipping and product damage.
Upgrade Equipment: If often handling heavy or oversized loads, consider upgrading to a more robust model or one with power-assist features. Check Uline for a variety of options.
By focusing on training, maintenance, proper usage, and safety, a Stockroom Associate can significantly improve their efficiency and reduce the risk of injury when using a pallet jack.
How to Display Pallet Jack Skills on Your Resume
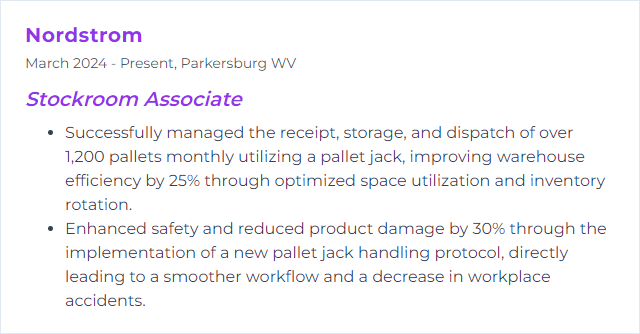
11. Cycle Counting
Cycle counting is a periodic inventory auditing process where a stockroom associate counts a small subset of inventory items on a regular basis to ensure accuracy in stock levels without having to do a complete inventory count at once.
Why It's Important
Cycle counting is important for a Stockroom Associate because it ensures inventory accuracy, helps identify discrepancies early, minimizes stockouts and overstock, and supports efficient order fulfillment and inventory management.
How to Improve Cycle Counting Skills
To improve Cycle Counting as a Stockroom Associate, follow these concise strategies:
Prioritize Items: Focus on high-value or fast-moving items first. This targeted approach ensures accuracy where it impacts the most. APICS offers guidelines on prioritizing inventory.
Use Technology: Implement barcode scanners or RFID technology for faster and more accurate counts. Zebra Technologies provides efficient scanning solutions.
Train Regularly: Ensure all team members are trained on the latest inventory management practices. LinkedIn Learning offers courses on inventory management.
Schedule Counts: Schedule regular cycle counts to avoid disruptions in daily operations. The Balanced Scorecard Institute Balanced Scorecard suggests strategic planning for inventory activities.
Analyze Results: Review discrepancies to identify and correct systemic issues. Six Sigma methodologies can help in analyzing and improving counting processes.
Adjust Strategies: Be flexible and ready to adjust counting strategies based on what works best for your operation. Continuous improvement is key.
By focusing on these strategies and utilizing resources effectively, you can significantly improve the accuracy and efficiency of cycle counting in your stockroom.
How to Display Cycle Counting Skills on Your Resume
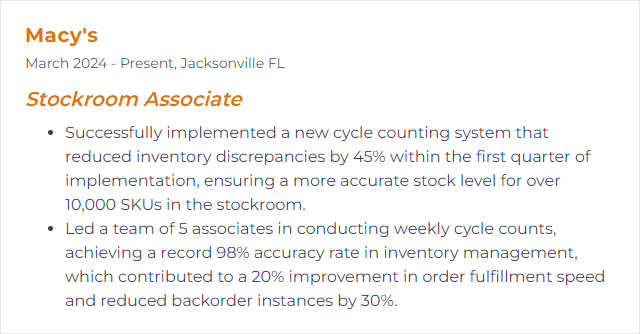
12. WMS (Warehouse Management System)
A Warehouse Management System (WMS) is a software tool designed to optimize and manage warehouse operations, helping Stockroom Associates track, locate, and manage inventory efficiently.
Why It's Important
A Warehouse Management System (WMS) is important for a Stockroom Associate because it streamlines inventory tracking, optimizes storage space, and accelerates order fulfillment processes, leading to improved accuracy, efficiency, and productivity in managing stockroom operations.
How to Improve WMS (Warehouse Management System) Skills
Improving a Warehouse Management System (WMS) for a Stockroom Associate involves several key steps focused on enhancing accuracy, efficiency, and productivity. Here are concise strategies:
Integrate with RFID Technology: Use Radio-Frequency Identification (RFID) for real-time inventory tracking, reducing manual scanning and improving accuracy.
Implement Mobile Solutions: Equip staff with mobile devices that have WMS access, enabling real-time updates and information retrieval on the go.
Optimize Layout and Picking Paths: Use WMS analytics to optimize warehouse layout and picking paths, reducing travel time and increasing productivity.
Regular Training and Feedback Loops: Invest in regular training for staff on WMS functionalities and establish a feedback loop for continuous improvement suggestions.
Adopt Lean Inventory Practices: Implement lean inventory management practices within the WMS to minimize waste and ensure stock levels are just right, avoiding overstocking or stockouts.
Implement Automation Where Possible: Integrate automation tools, like conveyor belts or automated retrieval systems, to reduce manual tasks. Learn more about warehouse automation.
Data Analysis and Forecasting: Utilize the WMS’s data analysis tools to forecast demand and adjust inventory levels accordingly, preventing bottlenecks. Data analysis in WMS can significantly enhance decision-making.
Regular System Updates and Maintenance: Ensure the WMS is regularly updated and maintained to benefit from the latest features and security patches, enhancing overall system performance.
By focusing on these areas, a Stockroom Associate can significantly contribute to the improvement of a Warehouse Management System, leading to a more efficient, accurate, and productive warehouse operation.
How to Display WMS (Warehouse Management System) Skills on Your Resume
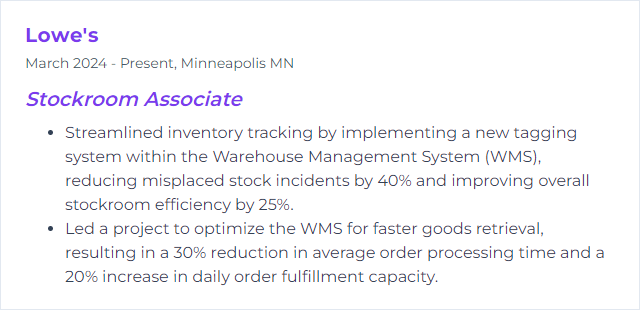