Top 12 Semiconductor Process Engineer Skills to Put on Your Resume
In the rapidly evolving field of semiconductor manufacturing, a process engineer's skill set is crucial for innovation and efficiency. Highlighting the top 12 skills on your resume can significantly enhance your marketability, positioning you as a standout candidate in this competitive industry.
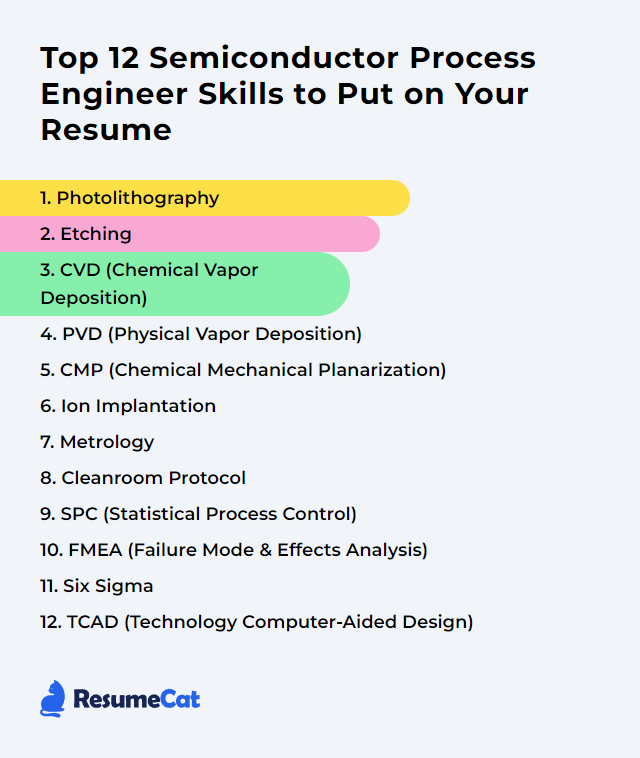
Semiconductor Process Engineer Skills
- Photolithography
- Etching
- CVD (Chemical Vapor Deposition)
- PVD (Physical Vapor Deposition)
- CMP (Chemical Mechanical Planarization)
- Ion Implantation
- Metrology
- Cleanroom Protocol
- SPC (Statistical Process Control)
- FMEA (Failure Mode and Effects Analysis)
- Six Sigma
- TCAD (Technology Computer-Aided Design)
1. Photolithography
Photolithography is a semiconductor fabrication technique used to transfer geometric patterns onto a substrate or wafer. It involves coating the substrate with a light-sensitive material (photoresist), exposing it to ultraviolet light through a patterned mask, and developing the image to create a physical mask on the substrate for subsequent etching or deposition processes. This method is crucial for defining the intricate features of integrated circuits at the nanometer scale.
Why It's Important
Photolithography is crucial in semiconductor manufacturing as it enables the precise patterning and scaling of electronic circuits on silicon wafers, essential for producing smaller, faster, and more efficient integrated circuits.
How to Improve Photolithography Skills
To improve photolithography in the context of semiconductor manufacturing, focus on the following key areas:
Resolution Enhancement: Utilize advanced techniques such as Immersion Lithography and Multiple Patterning to achieve finer feature sizes.
Photoresist Optimization: Develop or select photoresists with higher sensitivity and contrast. Information on advancements can be often found in specialized publications like SPIE.
Exposure Control: Improve exposure uniformity and precision through better mask alignment and exposure systems calibration.
Process Control: Employ advanced process control techniques to reduce variability in lithography steps.
Light Source Optimization: Use higher coherence light sources like Extreme Ultraviolet (EUV) Lithography for smaller feature sizes.
Computational Lithography: Apply computational techniques such as Source Mask Optimization (SMO) and Inverse Lithography Technology (ILT) for better pattern fidelity.
Equipment Maintenance: Regularly maintain and calibrate lithography tools to ensure optimal performance. Relevant guidelines can be found through equipment manufacturers' manuals and technical support.
Improving photolithography in semiconductor manufacturing involves a multi-faceted approach, incorporating advancements in technology, materials, and process control.
How to Display Photolithography Skills on Your Resume
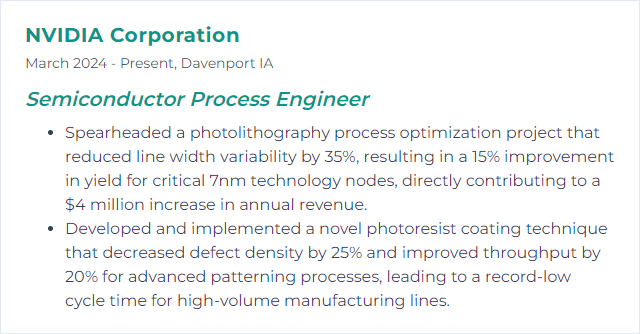
2. Etching
Etching in semiconductor processing is a technique used to remove material selectively from the surface of a wafer. It involves chemical or physical means to pattern specific areas of the substrate or layers on the substrate, following the design of integrated circuits. This process is crucial for creating the intricate structures and connections within semiconductor devices.
Why It's Important
Etching is crucial in semiconductor manufacturing as it precisely removes layers from the silicon wafer, creating the intricate patterns required for integrated circuits. This step defines the microscale features that form transistors and interconnects, essential for device functionality.
How to Improve Etching Skills
Improving etching in semiconductor processing involves optimizing parameters, selecting appropriate etching techniques, and employing advanced monitoring and control methods. Here are concise strategies:
Optimize Etching Parameters: Fine-tune parameters such as pressure, power, gas flow rates, and temperature to enhance etch rate, uniformity, and selectivity. MicroChemicals Etching Basics.
Choose Appropriate Etching Techniques: Select between wet and dry etching techniques based on the required precision, material, and feature size. Advanced deep reactive-ion etching (DRIE) is ideal for high-aspect-ratio structures. AZoM Etching Techniques.
Employ Advanced Masking Materials: Utilize high-resolution masking materials and techniques to achieve precise pattern transfer. ScienceDirect - Etching Process.
Integrate Real-Time Monitoring: Implement real-time etch rate and endpoint detection systems to ensure process consistency and accuracy. Semiconductor Engineering - Etch.
Utilize Computational Modeling: Leverage computational fluid dynamics (CFD) and other modeling tools to predict etching behavior and outcomes, optimizing the process before actual implementation. CFD Online.
Continuous Learning and Experimentation: Stay updated with the latest advancements in etching technology and materials science. Experiment with new chemistries and techniques to find improvements. IEEE Xplore.
By carefully analyzing each aspect of the etching process and leveraging the latest technology and research, semiconductor process engineers can significantly enhance etching performance.
How to Display Etching Skills on Your Resume
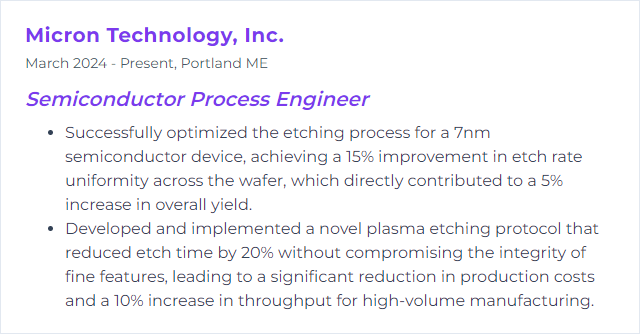
3. CVD (Chemical Vapor Deposition)
CVD (Chemical Vapor Deposition) is a semiconductor fabrication technique where gaseous reactants form solid thin films on a substrate through chemical reactions at elevated temperatures, enabling precise control over the film's thickness and composition for various device applications.
Why It's Important
CVD is crucial for a Semiconductor Process Engineer because it enables the precise deposition of thin films with uniform thickness and high purity on semiconductor wafers, essential for fabricating multilayered microelectronic devices, ensuring their performance and reliability.
How to Improve CVD (Chemical Vapor Deposition) Skills
Improving Chemical Vapor Depression (CVD) processes, especially in the context of semiconductor manufacturing, involves optimizing various parameters to enhance film quality, uniformity, and throughput, while minimizing defects and costs. Here are concise strategies:
Precursor Selection: Choose high-purity precursors with appropriate reactivity and volatility. SAMCO Inc. offers insights on precursor selection.
Temperature Control: Precisely control the substrate and chamber temperatures to influence deposition rates and film properties. Lam Research discusses the importance of temperature management in CVD processes.
Pressure and Flow Rates: Adjust the chamber pressure and gas flow rates to optimize deposition uniformity and film quality. Applied Materials provides technology solutions that include advanced flow control mechanisms.
Plasma Enhancement: For PECVD, optimizing plasma parameters (power, frequency) can improve film properties and deposition rates. Oxford Instruments has extensive resources on plasma-enhanced CVD.
In-situ Monitoring and Control: Implement real-time monitoring and control systems for process parameters to ensure consistent results. KLA Corporation offers advanced metrology and inspection systems suitable for in-situ process control.
Chamber Maintenance: Regular and thorough cleaning of the deposition chamber to reduce contamination and defects. ASM International discusses maintenance strategies for semiconductor equipment.
R&D and Simulation Tools: Use modeling and simulation tools for process optimization before practical implementation. Coventor provides software tools for semiconductor process simulation.
Remember, every CVD system and process may require a unique combination of these strategies for optimal improvement. Continuous experimentation and process tuning are key.
How to Display CVD (Chemical Vapor Deposition) Skills on Your Resume
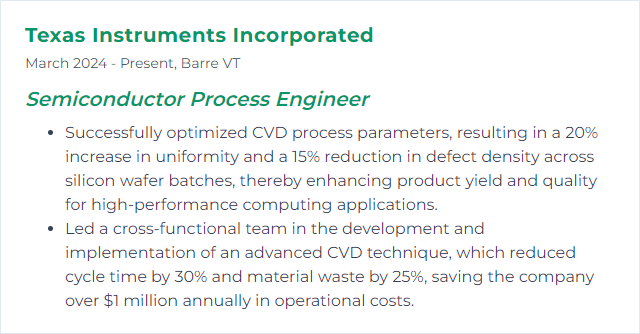
4. PVD (Physical Vapor Deposition)
PVD (Physical Vapor Deposition) is a vacuum coating process used in semiconductor manufacturing to deposit thin films of material onto a substrate by condensation of a vaporized form of the desired film material onto the substrate surface.
Why It's Important
PVD is crucial for a Semiconductor Process Engineer because it allows for the precise and uniform deposition of thin films on semiconductor wafers, essential for fabricating integrated circuits with high performance, reliability, and miniaturization.
How to Improve PVD (Physical Vapor Deposition) Skills
Improving Physical Vapor Deposition (PVD) in semiconductor processing primarily involves optimizing deposition parameters, enhancing equipment performance, and adopting advanced materials and techniques. Here are concise strategies:
Optimize Deposition Parameters: Fine-tune parameters like substrate temperature, deposition rate, and chamber pressure for uniform films and high-quality deposition. Reference: Semiconductor Engineering.
Utilize Advanced Targets: Employ high-purity, high-density targets to improve film quality and consistency. Research on advanced materials can be found at ScienceDirect.
Equipment Upgrades: Upgrade to advanced PVD systems with better process control and uniformity capabilities. For equipment options, see IOPscience.
In-situ Monitoring and Control: Implement real-time monitoring and control systems for process optimization. Techniques and tools are detailed at MDPI.
Adopt New Technologies: Explore novel PVD techniques like High Power Impulse Magnetron Sputtering (HiPIMS) for improved film properties. A comprehensive overview can be found at Elsevier.
Each strategy aims to enhance the efficiency, quality, and applicability of PVD coatings in semiconductor manufacturing, addressing specific process challenges and product requirements.
How to Display PVD (Physical Vapor Deposition) Skills on Your Resume
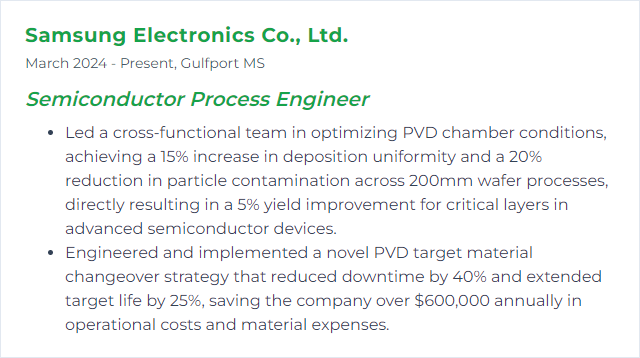
5. CMP (Chemical Mechanical Planarization)
CMP, or Chemical Mechanical Planarization, is a critical semiconductor manufacturing process that utilizes chemical slurry and mechanical polishing to flatten and smooth the wafer surface, ensuring uniform layer thickness and preparing the wafer for subsequent lithography steps, thereby enhancing device performance and yield.
Why It's Important
CMP (Chemical Mechanical Planarization) is crucial in semiconductor manufacturing because it ensures the surface of wafers is flat and uniform, essential for creating reliable and high-performance multilayered semiconductor devices. This process enables the successful patterning of fine features, critical for advancing chip miniaturization and enhancing device functionality.
How to Improve CMP (Chemical Mechanical Planarization) Skills
To enhance Chemical Mechanical Planarization (CMP) in a semiconductor fabrication process, focus on optimizing slurry composition, pad conditioning, process parameters, and post-CMP cleaning.
Optimize Slurry Composition: Adjust the abrasive particle size and concentration, along with the chemical additives, to improve removal rates and surface finish. Slurry Optimization.
Pad Conditioning: Regularly condition the CMP pad to maintain its effectiveness. This involves adjusting the conditioning disk properties and parameters to ensure a consistent pad surface. Pad Conditioning Effects.
Process Parameters Tuning: Precisely control pressure, velocity, and temperature during the CMP process to achieve uniform material removal and minimize defects. Process Parameters Influence.
Enhance Post-CMP Cleaning: Improve the cleaning process to remove slurry residues and prevent contamination, utilizing optimized cleaning solutions and techniques. Post-CMP Cleaning.
By focusing on these areas, a Semiconductor Process Engineer can significantly improve the CMP process's efficiency and outcomes.
How to Display CMP (Chemical Mechanical Planarization) Skills on Your Resume
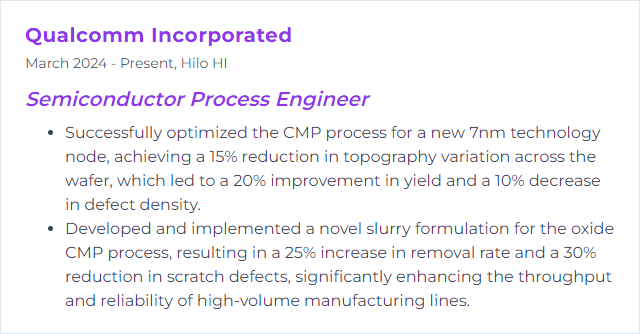
6. Ion Implantation
Ion implantation is a semiconductor manufacturing process used to dope silicon wafers with precise amounts of impurities. By accelerating ions of dopant materials and directing them into the substrate, desired electrical characteristics are achieved by altering the semiconductor's conductivity in specific regions. This process allows for the precise control of dopant concentration and distribution, essential for the fabrication of semiconductor devices.
Why It's Important
Ion implantation is crucial for semiconductor process engineering because it allows for precise doping of semiconductor materials, enabling the controlled modification of electrical properties necessary for fabricating integrated circuits with specific functionalities.
How to Improve Ion Implantation Skills
Improving ion implantation, a critical process in semiconductor manufacturing, involves enhancing precision, minimizing defects, and increasing throughput. Here are concise strategies tailored for a Semiconductor Process Engineer:
Optimize Dose and Energy: Precisely control dopant dose and energy to achieve desired junction depth and concentration profiles. Simulation tools can aid in predicting implantation profiles and optimizing parameters.
Implanter Maintenance: Regular maintenance and calibration of the implanter ensure stable beam current and energy, reducing variability. Implanter maintenance guidelines can offer detailed procedures.
Advanced Implantation Techniques: Utilize cluster ion implantation or plasma immersion ion implantation (PIII) for better surface conformity and lower defect generation. Research on advanced techniques provides insights into their benefits.
Process Monitoring: Implement real-time monitoring and feedback systems to adjust parameters promptly, reducing deviations. In-situ monitoring technologies offer options for enhancing process control.
Damage Recovery: Post-implantation annealing can repair implantation-induced damage and activate dopants. Explore advanced annealing techniques like laser or flash annealing for better results. Annealing studies highlight different methods' effectiveness.
By focusing on these areas, Semiconductor Process Engineers can significantly improve the outcomes of ion implantation processes.
How to Display Ion Implantation Skills on Your Resume
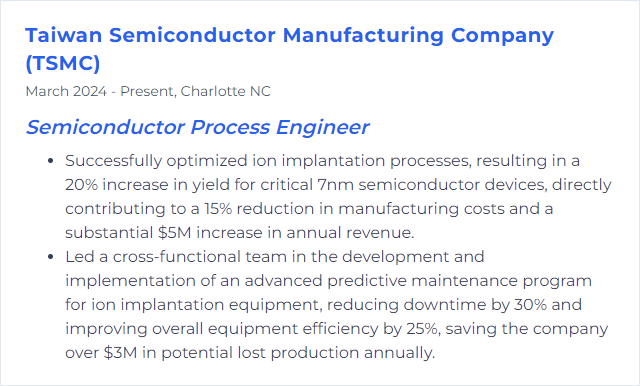
7. Metrology
Metrology, in the context of a Semiconductor Process Engineer, refers to the science of measurement applied to the precise quantification and characterization of physical dimensions, properties, and parameters crucial to semiconductor fabrication and processing, ensuring quality control, repeatability, and device performance.
Why It's Important
Metrology is crucial for a Semiconductor Process Engineer because it ensures the precision and accuracy of semiconductor device dimensions and properties, which are fundamental for device performance, yield, and reliability in the highly exacting semiconductor manufacturing process.
How to Improve Metrology Skills
Improving metrology for a Semiconductor Process Engineer involves focusing on precision, accuracy, and repeatability in measurements. Here are concise steps to enhance metrology in semiconductor processes:
Invest in Advanced Equipment: Utilize state-of-the-art metrology tools like atomic force microscopes (AFM) and scatterometry (Woollam) for enhanced resolution and accuracy.
Regular Calibration: Ensure all metrology equipment is regularly calibrated against standards to maintain measurement accuracy. Calibration services like those offered by NIST can be invaluable.
Implement Statistical Process Control (SPC): Use SPC tools to monitor and control the process variations. Software like MINITAB can help in analyzing data for better process understanding.
Training and Education: Continuously train staff on the latest metrology techniques and principles. Resources like SEMI offer courses tailored for semiconductor professionals.
Collaborate with Metrology Experts: Engage with metrology experts and institutions for insights into cutting-edge practices and technologies. Joining forums such as IEEE can facilitate networking and knowledge exchange.
Optimize Measurement Procedures: Streamline measurement protocols to minimize human error and enhance repeatability. Documentation of best practices is crucial.
Leverage Machine Learning: Employ machine learning algorithms to predict and adjust for process deviations, enhancing the predictive maintenance of metrology tools. Explore resources at Coursera for machine learning courses.
By focusing on these areas, Semiconductor Process Engineers can significantly improve the metrology aspect of their work, leading to more consistent and reliable semiconductor manufacturing processes.
How to Display Metrology Skills on Your Resume
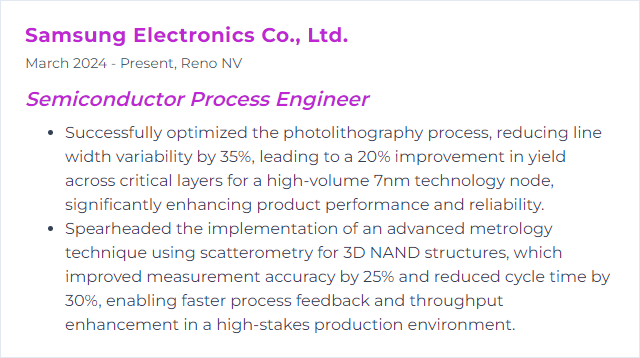
8. Cleanroom Protocol
Cleanroom Protocol for a Semiconductor Process Engineer involves strict procedures to minimize contamination in the semiconductor manufacturing environment. This includes wearing specialized garments, controlling air quality, and adhering to cleanliness and process guidelines to prevent particle, chemical, and microbial contamination of semiconductor wafers.
Why It's Important
Cleanroom protocol is crucial for a Semiconductor Process Engineer because it minimizes contamination, ensuring the high precision and quality required for semiconductor manufacturing, directly impacting yield, reliability, and performance of semiconductor devices.
How to Improve Cleanroom Protocol Skills
Improving cleanroom protocol, especially for Semiconductor Process Engineers, involves a series of methodical steps to minimize contamination and enhance the manufacturing environment. Here's a concise guide:
Regular Training: Ensure all personnel undergo regular training on cleanroom protocol, including updates on new procedures or technologies.
Strict Adherence to Dress Code: Enforce a strict cleanroom dress code to minimize human-borne contamination.
Equipment Maintenance: Implement a routine maintenance schedule for cleanroom equipment to prevent malfunctions that could introduce contaminants.
Air Filtration Systems: Upgrade and regularly maintain HEPA/ULPA filters to ensure the highest air purity levels.
Contamination Control: Adopt strict contamination control measures including proper cleaning protocols and minimizing material ingress and egress.
Process Optimization: Continuously review and optimize manufacturing processes to reduce opportunities for contamination.
Regular Audits: Conduct regular cleanroom audits to identify and rectify potential contamination sources.
Investment in Technology: Invest in state-of-the-art cleanroom technology and monitoring systems for real-time contamination tracking.
By focusing on these areas, Semiconductor Process Engineers can significantly improve cleanroom protocols, leading to higher yields, reduced defects, and improved product quality.
How to Display Cleanroom Protocol Skills on Your Resume
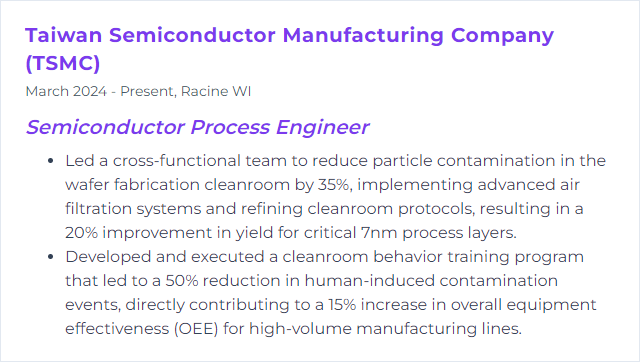
9. SPC (Statistical Process Control)
Statistical Process Control (SPC) is a method used by semiconductor process engineers to monitor and control a manufacturing process using statistical techniques, ensuring that the process operates at its maximum potential to produce high-quality products with minimal waste and variability.
Why It's Important
SPC is crucial for a Semiconductor Process Engineer because it enables precise monitoring and control of manufacturing processes, ensuring product quality, reliability, and yield optimization while minimizing defects and production costs.
How to Improve SPC (Statistical Process Control) Skills
Improving SPC (Statistical Process Control) in the context of a Semiconductor Process Engineer involves enhancing data quality, analysis techniques, and response strategies. Here’s a concise guide:
Enhance Data Collection: Ensure accurate and real-time data collection by utilizing advanced sensors and IoT devices. Semiconductor Engineering often discusses the latest in sensor technology and data acquisition methods relevant to semiconductor manufacturing.
Implement Advanced SPC Software: Use advanced SPC software that offers comprehensive analysis tools, real-time monitoring, and predictive analytics capabilities. Companies like Siemens provide solutions tailored to semiconductor manufacturing.
Educate and Train Staff: Continuously train staff on SPC concepts, software usage, and data interpretation. Resources like ASQ offer courses and certifications in SPC.
Adopt Multivariate Analysis: Move beyond univariate SPC to multivariate analysis to capture the complex interactions between process variables, enhancing fault detection and process understanding. The Journal of Quality Technology often publishes research on advanced SPC techniques suitable for the semiconductor industry.
Integrate Machine Learning: Implement machine learning algorithms to predict process deviations and optimize control parameters dynamically. Platforms like TensorFlow provide tools to develop and deploy machine learning models.
Foster a Culture of Continuous Improvement: Encourage a company culture that actively seeks process improvements based on SPC data, fostering innovation and efficiency. Lean Manufacturing Tools provides insights into creating a continuous improvement culture.
Regularly Review and Optimize SPC Strategies: Periodically review the effectiveness of your SPC strategies and make adjustments based on new data, technology advancements, and changing production goals.
By focusing on these areas, Semiconductor Process Engineers can significantly improve the efficacy of their SPC efforts, leading to higher product quality, reduced waste, and increased manufacturing efficiency.
How to Display SPC (Statistical Process Control) Skills on Your Resume
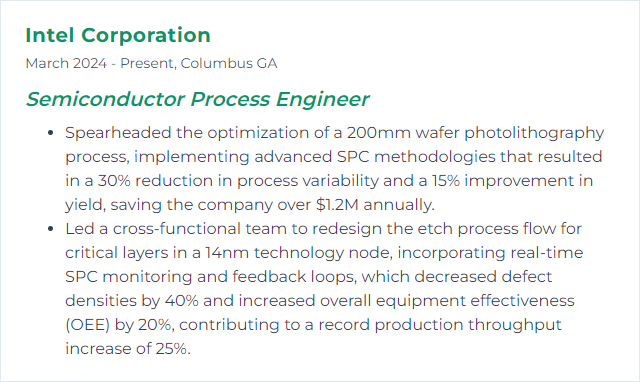
10. FMEA (Failure Mode and Effects Analysis)
FMEA (Failure Mode and Effects Analysis) is a systematic, step-by-step approach used by semiconductor process engineers to identify potential failure modes in a manufacturing process, assess the risks associated with these failures, and prioritize measures to mitigate or eliminate the risks, thereby enhancing reliability and quality in semiconductor production.
Why It's Important
FMEA is crucial for a Semiconductor Process Engineer because it systematically identifies potential failure modes in the manufacturing process, assesses their impact on product quality and reliability, and prioritizes actions to mitigate risks, ensuring high yield, performance, and customer satisfaction in semiconductor production.
How to Improve FMEA (Failure Mode and Effects Analysis) Skills
Improving FMEA (Failure Mode and Effects Analysis) involves systematically enhancing the process to identify potential failures in semiconductor manufacturing. Here’s a concise guide for a Semiconductor Process Engineer:
Increase Cross-Functional Participation: Involve a diverse team from design, manufacturing, quality, and maintenance to provide comprehensive perspectives. ASQ’s Guide offers insights into effective team collaboration.
Utilize Up-to-Date Data and Tools: Implement the latest semiconductor process data and FMEA software tools to ensure accurate analysis. SEMI Standards can provide relevant guidelines.
Prioritize Risks: Use the Risk Priority Number (RPN) effectively to prioritize issues and allocate resources efficiently. The IEEE Xplore database may have studies on optimizing RPN usage.
Implement Continuous Learning: Regularly update the FMEA process with lessons learned from past failures and near-misses. The Semiconductor Industry Association offers resources for continuous industry learning.
Integrate with Other Quality Tools: Combine FMEA with other quality tools like SPC (Statistical Process Control) and Root Cause Analysis for a comprehensive approach. NIST’s Engineering Statistics Handbook provides a good overview.
Conduct Regular Reviews and Updates: Periodically review and update FMEAs to reflect changes in processes, materials, or technology. Journal of Quality in Maintenance Engineering often publishes relevant research on maintenance strategies.
Focus on Preventive Actions: Shift the focus towards preventive actions rather than corrective measures to enhance reliability and reduce costs. The Lean Enterprise Institute discusses principles that can be applied in this context.
By following these steps and leveraging the provided resources, a Semiconductor Process Engineer can significantly improve the effectiveness of FMEA in identifying and mitigating potential failures.
How to Display FMEA (Failure Mode and Effects Analysis) Skills on Your Resume
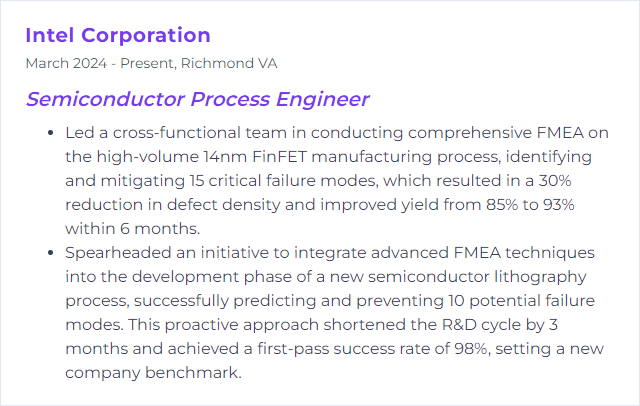
11. Six Sigma
Six Sigma is a data-driven methodology and set of tools aimed at process improvement, focusing on identifying and eliminating defects, reducing variability, and improving quality in manufacturing processes, including those in semiconductor engineering.
Why It's Important
Six Sigma is crucial for a Semiconductor Process Engineer because it provides a systematic methodology to reduce defects, improve process efficiency, and ensure consistent quality in the highly complex and precise semiconductor manufacturing process, leading to enhanced product reliability and competitiveness in the market.
How to Improve Six Sigma Skills
To enhance Six Sigma methodology as a Semiconductor Process Engineer, focus on the following concise steps:
Understand the Basics: Ensure a solid grasp of Six Sigma principles and methodologies. ASQ’s Six Sigma resources are a great starting point.
Data-Driven Approach: Emphasize collecting and analyzing data specific to semiconductor manufacturing processes. Utilize statistical software like Minitab for data analysis.
Continuous Training: Engage in ongoing Six Sigma training and certification, such as Lean Six Sigma Green Belt or Black Belt to stay updated with advanced techniques.
Cross-Functional Teams: Foster collaboration across different departments. Tools like Slack can facilitate communication and project management.
Implement DMAIC Rigorously: Apply the Define, Measure, Analyze, Improve, and Control (DMAIC) cycle meticulously to semiconductor processes. The Semiconductor Industry Association (SIA) provides resources and case studies specific to the industry.
Benchmarking: Regularly compare processes against industry standards and best practices. IEEE Xplore offers access to the latest research and developments.
Customer Feedback: Integrate feedback from end-users of semiconductor products to identify areas for improvement. Tools like SurveyMonkey can facilitate this process.
Innovate and Adapt: Stay abreast of technological advancements and incorporate innovative solutions into the Six Sigma methodology. Resources like Semiconductor Engineering can keep you informed.
By focusing on these areas, a Semiconductor Process Engineer can effectively improve Six Sigma processes, leading to higher quality, efficiency, and customer satisfaction in semiconductor manufacturing.
How to Display Six Sigma Skills on Your Resume
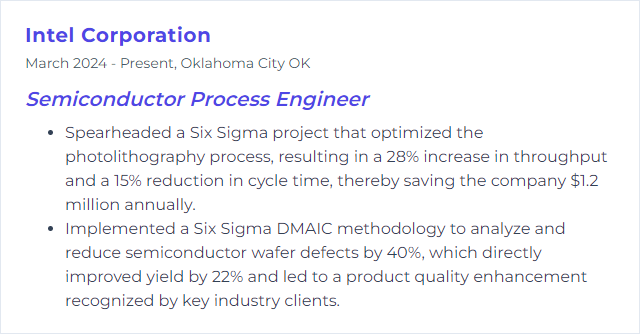
12. TCAD (Technology Computer-Aided Design)
TCAD (Technology Computer-Aided Design) is a simulation software used by semiconductor process engineers to model and analyze the fabrication processes and device performance of semiconductor devices, enabling the prediction and optimization of semiconductor manufacturing processes and device designs before physical prototypes are made.
Why It's Important
TCAD is crucial for a Semiconductor Process Engineer because it enables the simulation and optimization of semiconductor processing and device operation, reducing the need for costly experimental prototypes and accelerating the development of more efficient and reliable semiconductor devices.
How to Improve TCAD (Technology Computer-Aided Design) Skills
Improving TCAD for a Semiconductor Process Engineer involves a blend of enhancing software capabilities, increasing simulation accuracy, and optimizing computational efficiency. Here are concise strategies:
Upgrade Software and Tools: Regularly update TCAD software to leverage the latest features and improvements. Consider Synopsys TCAD or Silvaco TCAD for advanced simulation capabilities.
Enhance Model Accuracy: Integrate experimental data and real-world measurements to refine and validate TCAD models, ensuring simulations closely mirror actual semiconductor processes.
Optimize Computational Resources: Utilize high-performance computing (HPC) environments to reduce simulation times. Explore cloud-based solutions like AWS for Semiconductor Design, which can offer scalable computational resources.
Skill Development: Stay abreast of the latest TCAD methodologies through continuous learning. Online courses and webinars by TCAD software providers or platforms like Coursera and edX can be valuable.
Collaboration and Networking: Engage with the TCAD community through forums, online groups, or seminars. Platforms like ResearchGate or LinkedIn groups dedicated to semiconductor research can provide insights and peer support.
Automate and Integrate: Develop scripts to automate repetitive tasks and integrate TCAD simulations into larger design and verification workflows. This approach improves efficiency and reduces the potential for human error.
By focusing on these areas, a Semiconductor Process Engineer can significantly improve the effectiveness and efficiency of TCAD simulations, leading to more accurate designs and faster development cycles.
How to Display TCAD (Technology Computer-Aided Design) Skills on Your Resume
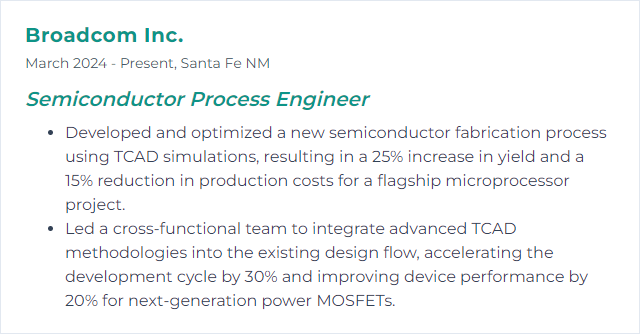