Top 12 Quality Control Supervisor Skills to Put on Your Resume
In the competitive landscape of quality control management, possessing a well-rounded set of skills is crucial for standing out to potential employers. This article highlights the top 12 quality control supervisor skills that, when featured on your resume, can significantly enhance your job application, demonstrating your capability to uphold and drive quality standards within any organization.
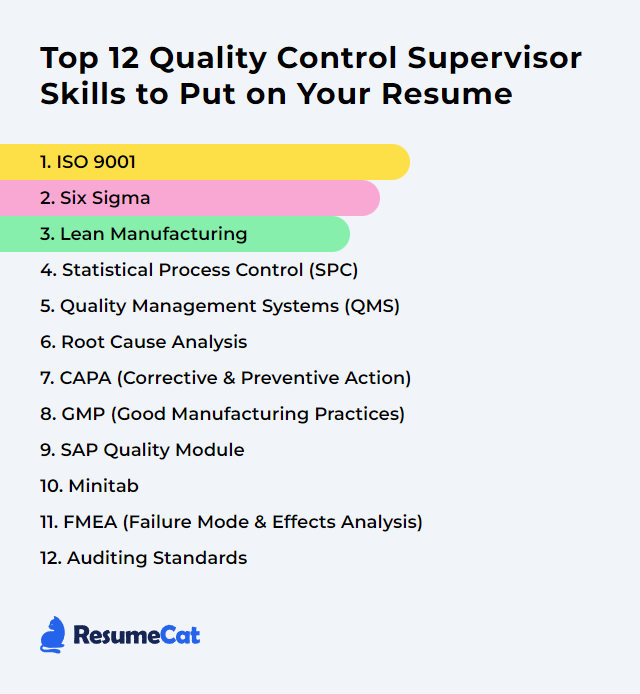
Quality Control Supervisor Skills
- ISO 9001
- Six Sigma
- Lean Manufacturing
- Statistical Process Control (SPC)
- Quality Management Systems (QMS)
- Root Cause Analysis
- CAPA (Corrective and Preventive Action)
- GMP (Good Manufacturing Practices)
- SAP Quality Module
- Minitab
- FMEA (Failure Mode and Effects Analysis)
- Auditing Standards
1. ISO 9001
ISO 9001 is an international standard that specifies requirements for a quality management system (QMS). Organizations use it to demonstrate their ability to consistently provide products and services that meet customer and regulatory requirements. For a Quality Control Supervisor, it guides the implementation and oversight of processes to ensure quality consistency and continuous improvement.
Why It's Important
ISO 9001 is important because it provides a framework for consistent quality management processes, ensuring products meet customer and regulatory requirements, thereby enhancing customer satisfaction and competitive advantage for the organization.
How to Improve ISO 9001 Skills
Improving ISO 9001 within the context of a Quality Control Supervisor role focuses on enhancing the quality management system (QMS) efficiency, effectiveness, and adaptability. Here are concise strategies:
Engage and Train Team: Ensure all team members are fully aware of ISO 9001 standards and their role in maintaining them. Provide regular training to keep the team updated on best practices.
Implement a Strong Audit System: Conduct regular internal audits to identify areas for improvement and ensure compliance with ISO 9001 standards.
Focus on Customer Feedback: Use customer feedback to continuously improve products and services. Establish a clear process for collecting, analyzing, and acting on customer feedback.
Adopt Risk-Based Thinking: Integrate risk management into the QMS to proactively identify and mitigate potential disruptions.
Continual Improvement Process (CIP): Develop and implement a process for continual improvement that aligns with the Plan-Do-Check-Act (PDCA) cycle, focusing on enhancing efficiency and effectiveness.
Utilize Quality Management Tools: Employ quality management tools such as Six Sigma, Kaizen, and 5S to streamline processes and reduce waste.
Strengthen Supplier Relationships: Work closely with suppliers to ensure they meet ISO 9001 standards, which could involve conducting supplier audits.
Embrace Technology: Implement quality management software solutions that facilitate compliance with ISO 9001 and enhance process efficiency.
Monitor and Measure Performance: Establish key performance indicators (KPIs) to monitor the effectiveness of the QMS and identify areas for improvement.
Management Engagement: Ensure top management is actively involved in the QMS, demonstrating leadership and commitment to quality.
By focusing on these areas, a Quality Control Supervisor can drive significant improvements in their organization's ISO 9001 compliance and overall quality performance.
How to Display ISO 9001 Skills on Your Resume
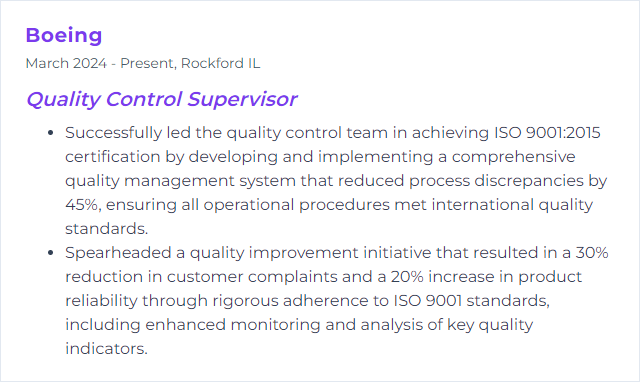
2. Six Sigma
Six Sigma is a data-driven methodology and set of tools aimed at improving business processes by reducing defects and variability to enhance product quality and efficiency, crucial for a Quality Control Supervisor's role in ensuring high-quality outputs.
Why It's Important
Six Sigma is important as it provides a systematic approach to reducing defects and improving quality, directly aligning with a Quality Control Supervisor's goal of enhancing product reliability and customer satisfaction through efficient, error-minimizing processes.
How to Improve Six Sigma Skills
To improve Six Sigma as a Quality Control Supervisor, focus on these concise strategies:
Engage in Continuous Education: Stay updated with the latest Six Sigma methodologies and tools through professional development courses. ASQ Courses and iSixSigma are excellent resources.
Implement DMAIC Rigorously: Ensure the Define, Measure, Analyze, Improve, Control (DMAIC) cycle is strictly followed for problem-solving. ASQ’s DMAIC Guide offers a comprehensive overview.
Leverage Technology: Use Six Sigma software tools for data analysis and project management, enhancing efficiency and accuracy. Minitab is widely recommended.
Foster a Culture of Continuous Improvement: Encourage and train your team in Six Sigma principles. Promote an environment where every member actively identifies improvement opportunities. Six Sigma Daily provides valuable insights and tips.
Monitor and Review Projects Regularly: Regularly review Six Sigma projects to ensure they are on track and aligned with organizational goals. Use KPIs and dashboards for real-time monitoring.
Collaborate Across Departments: Work closely with other departments to ensure Six Sigma projects are integrated company-wide, fostering a holistic approach to quality improvement.
By focusing on these strategies and continuously seeking knowledge and improvement, you can enhance your Six Sigma processes and drive significant quality improvements in your organization.
How to Display Six Sigma Skills on Your Resume
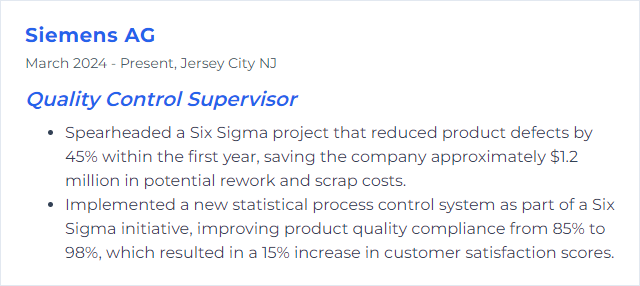
3. Lean Manufacturing
Lean Manufacturing is a systematic approach to minimizing waste within manufacturing systems while maximizing productivity, aimed at improving quality and efficiency, directly impacting a Quality Control Supervisor's focus on ensuring product excellence and process optimization.
Why It's Important
Lean Manufacturing is important because it focuses on eliminating waste, improving process efficiency, and enhancing product quality, directly contributing to achieving higher customer satisfaction and reducing production costs, which are crucial objectives for a Quality Control Supervisor.
How to Improve Lean Manufacturing Skills
Improving Lean Manufacturing, especially from the perspective of a Quality Control Supervisor, involves several key actions focused on eliminating waste, ensuring quality at every stage, and fostering a culture of continuous improvement. Here's a concise guide:
Map the Value Stream: Identify all the steps in your value stream, eliminating anything that doesn't add value to your customer. VSM Guide provides insights into effectively mapping and analyzing your processes.
Implement 5S: Organize and maintain the workplace in good order to improve efficiency and safety. 5S Guide outlines steps to implement this methodology.
Focus on Quality at the Source: Train employees to detect and solve problems at their origin, preventing defects from moving down the line. The Jidoka Principle is central to understanding this concept.
Adopt Kaizen: Foster a culture of continuous, incremental improvement, involving everyone in the process of identifying and solving problems. Kaizen Guide offers strategies for implementing this approach.
Leverage Pull Systems: Control the flow of resources in your production process by implementing a pull system, reducing inventory levels and lead time. An introduction to Pull Systems can provide more details.
Utilize Root Cause Analysis: When problems occur, use tools like the 5 Whys or Fishbone Diagram to identify the root cause, not just the symptoms. The Root Cause Analysis Guide offers techniques for effective analysis.
Implement Standard Work: Develop and use standardized work procedures to ensure consistency and predictability. Standard Work explains how to document and implement these processes.
By focusing on these areas, a Quality Control Supervisor can significantly contribute to enhancing Lean Manufacturing efforts within their organization.
How to Display Lean Manufacturing Skills on Your Resume
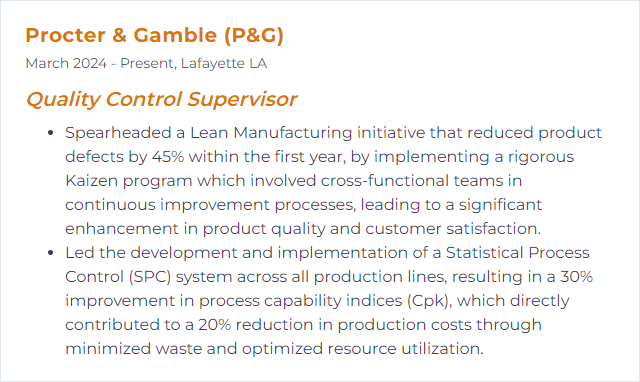
4. Statistical Process Control (SPC)
Statistical Process Control (SPC) is a method used in quality control that employs statistical techniques to monitor and control a process, ensuring that it operates at its full potential to produce conforming product with minimal waste. It involves the collection and analysis of data in real-time, allowing for the early detection of variability or defects, thereby facilitating timely corrective actions to maintain process stability and quality.
Why It's Important
Statistical Process Control (SPC) is crucial as it enables a Quality Control Supervisor to monitor and control process performance using statistical methods, ensuring product quality consistency and minimizing variability, which leads to reducing defects and increasing operational efficiency.
How to Improve Statistical Process Control (SPC) Skills
Improving Statistical Process Control (SPC) involves several steps aimed at enhancing quality control processes. Here are concise strategies for a Quality Control Supervisor:
Educate and Train: Ensure all team members are trained in SPC principles and tools. Continuous education enhances understanding and application. Utilize resources such as ASQ's SPC training.
Implement Real-time Monitoring: Adopt real-time SPC software solutions to monitor processes and detect variations promptly. Explore options like InfinityQS.
Standardize Processes: Develop and enforce standard operating procedures (SOPs) for data collection and analysis. Consistency is key to reliable SPC.
Engage in Routine Analysis: Schedule regular analysis of SPC data to identify trends, shifts, and potential areas of improvement. Use tools such as Minitab for in-depth statistical analysis.
Foster a Quality Culture: Promote a culture where quality and continuous improvement are valued by everyone. Encourage feedback and proactive problem-solving.
Utilize Advanced SPC Techniques: Beyond basic control charts, explore advanced SPC techniques such as Process Capability Analysis and Design of Experiments (DOE) for deeper insights. MoreSteam offers detailed explanations and tools.
Collaborate with Suppliers: Work closely with suppliers to ensure the quality of raw materials, utilizing SPC in supplier quality management. Supplier collaboration tools and guidelines are available on ISM.
Continuous Improvement: Adopt a Kaizen approach, aiming for continuous small improvements in the SPC process itself. Learn more about Kaizen and continuous improvement from Kaizen Institute.
For further detailed strategies and to stay updated with the latest trends in SPC, consider joining professional forums and organizations such as the American Society for Quality (ASQ).
How to Display Statistical Process Control (SPC) Skills on Your Resume
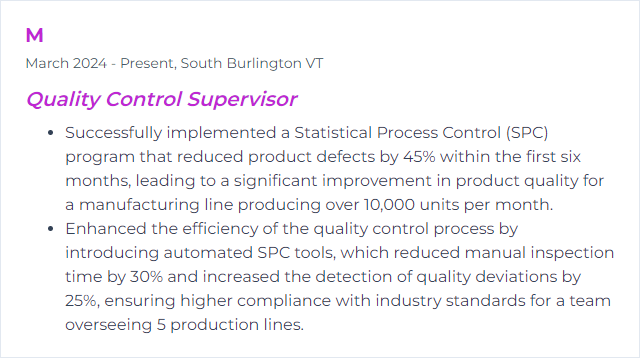
5. Quality Management Systems (QMS)
A Quality Management System (QMS) is a structured framework of policies, procedures, and processes used by an organization to ensure that its products or services meet and maintain the desired level of quality. It aims to enhance customer satisfaction through the effective application of the system, including processes for continuous improvement and assurance of conformity to customer and applicable regulatory requirements. For a Quality Control Supervisor, it serves as the operational backbone, guiding quality control activities, ensuring compliance, and driving the organization's continuous improvement efforts.
Why It's Important
Quality Management Systems (QMS) are crucial for ensuring consistent product quality, reducing production errors, and meeting customer expectations, thereby enhancing customer satisfaction and competitive advantage. For a Quality Control Supervisor, a QMS provides a structured framework for process monitoring, problem-solving, and continuous improvement, leading to increased efficiency and compliance with regulatory standards.
How to Improve Quality Management Systems (QMS) Skills
Improving a Quality Management System (QMS) involves a continuous process of evaluation and optimization. Here's a concise guide tailored for a Quality Control Supervisor:
Assess and Map Current Processes: Begin by thoroughly understanding your current QMS processes. Identify areas of inefficiency or non-compliance by conducting internal audits. ASQ’s guide on quality audits can provide a solid framework.
Engage Your Team: Involvement and buy-in from all team members are crucial. Implement training sessions to ensure everyone understands their role within the QMS. The ISO’s Training page offers resources tailored to various aspects of quality management.
Leverage Technology: Adopt quality management software that integrates into your existing systems to streamline processes, from document control to CAPA (Corrective and Preventive Actions). Explore options like Qualio for life sciences or other industry-specific solutions.
Set SMART Goals: Define Specific, Measurable, Achievable, Relevant, and Time-bound goals for your QMS improvement efforts. This approach ensures clarity and trackability. MindTools offers a comprehensive guide on setting SMART goals.
Implement a Continuous Improvement Culture: Foster an organizational culture that embraces continuous improvement. Techniques like Kaizen can be instrumental. Learn more through ASQ’s Kaizen guide.
Monitor and Measure Performance: Use Key Performance Indicators (KPIs) to track the effectiveness of your QMS improvements. Regularly review these metrics and adjust strategies as needed. KPI.org provides insights into selecting and managing KPIs.
Stay Updated with Industry Standards: Regularly review and update your QMS to comply with the latest quality standards, such as ISO 9001. The ISO’s catalog can keep you informed on current and upcoming standards.
Customer Feedback Loop: Integrate customer feedback into your QMS for continuous improvement. Tools like SurveyMonkey can facilitate gathering and analyzing customer satisfaction data.
Risk Management: Incorporate risk management into your QMS to proactively address potential issues. ISO 31000 provides guidelines on risk management principles and strategies.
Benchmark and Learn: Compare your QMS practices with industry leaders and learn from best practices. Networking through professional associations like ASQ can offer valuable insights.
By following these steps and leveraging the resources provided, a Quality Control Supervisor can significantly improve their organization’s Quality Management System, leading to enhanced efficiency, compliance, and customer satisfaction.
How to Display Quality Management Systems (QMS) Skills on Your Resume
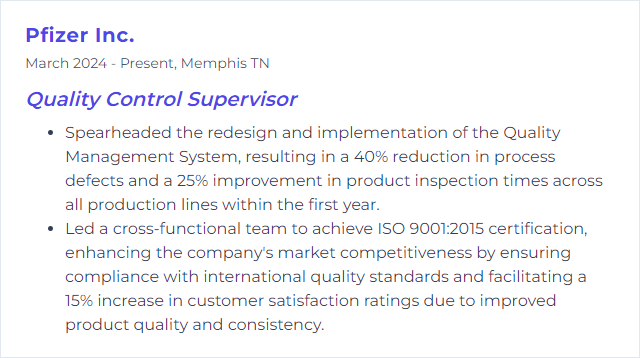
6. Root Cause Analysis
Root Cause Analysis (RCA) is a systematic process used by Quality Control Supervisors to identify the underlying reasons for defects or problems in a product or process, aiming to implement long-term solutions that prevent recurrence.
Why It's Important
Root Cause Analysis (RCA) is crucial for a Quality Control Supervisor because it systematically identifies the underlying reasons for defects or failures, allowing for the implementation of effective corrective actions to prevent recurrence, thereby ensuring product quality and customer satisfaction.
How to Improve Root Cause Analysis Skills
Improving Root Cause Analysis (RCA) as a Quality Control Supervisor involves a systematic process to identify the underlying reasons for a problem. Here’s a very short and concise guide:
Define the Problem Clearly: Start with a clear, concise statement of the issue, including specifics about what, when, where, and the impact.
Gather Data: Collect data relevant to the problem. This can include production data, process maps, and any previous reports on the issue.
Use RCA Tools: Employ RCA tools like the 5 Whys technique, which involves asking "Why?" five times to drill down to the root cause, or the Fishbone Diagram (Ishikawa) to visually map out potential causes.
Identify Root Causes: Analyze the collected data and tool outputs to pinpoint the underlying causes. Look for patterns or repeated issues that point to deeper problems.
Implement Corrective Actions: Develop and implement strategies to address the root causes. This could involve process changes, training, or modifications to equipment.
Monitor and Adjust: After implementing changes, closely monitor the outcomes to ensure the root cause has been adequately addressed. Be prepared to adjust your strategies as necessary.
Document and Share Findings: Document your findings, actions taken, and outcomes. Sharing these results helps prevent recurrence and fosters a culture of continuous improvement.
For a more in-depth understanding and strategies, consider resources from ASQ’s Root Cause Analysis and The Basics of Root Cause Analysis by Reliable Plant. These steps and resources will guide you in enhancing your RCA efforts towards more effective and lasting solutions.
How to Display Root Cause Analysis Skills on Your Resume
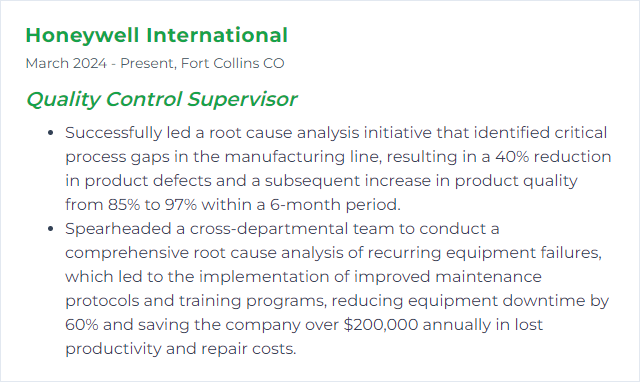
7. CAPA (Corrective and Preventive Action)
CAPA (Corrective and Preventive Action) is a quality management process aimed at identifying, addressing, and preventing the recurrence of non-conformities or issues in products, processes, or quality systems to ensure compliance and enhance product quality and safety.
Why It's Important
CAPA is crucial because it identifies and corrects systemic issues, prevents recurrence of non-conformities, ensures product quality and safety, and maintains compliance with regulatory standards, thereby safeguarding the company's reputation and customer trust.
How to Improve CAPA (Corrective and Preventive Action) Skills
Improving CAPA involves a focused approach to identifying, addressing, and preventing issues in quality control. Here are key steps tailored for a Quality Control Supervisor:
- Define the Problem Clearly: Use tools like the 5 Whys Technique to get to the root cause of the issue.
- Root Cause Analysis (RCA): Implement RCA methodologies such as Fishbone Diagrams to systematically identify underlying causes.
- Develop an Action Plan: Create a detailed action plan that specifies corrective actions (to fix current issues) and preventive actions (to avoid recurrence).
- Implement Actions: Allocate resources and assign responsibilities for action implementation. Use project management tools for tracking.
- Training and Communication: Ensure all relevant staff are trained on the changes. Use communication best practices to keep everyone informed.
- Monitor and Review: Establish KPIs for monitoring the effectiveness of CAPA. Regularly review progress and adjust actions as necessary. ISO 9001 standards can guide effective monitoring.
- Documentation: Maintain comprehensive documentation for all CAPA activities as per FDA guidelines for quality management systems.
For a Quality Control Supervisor, focusing on continuous improvement and leveraging quality management tools are key to enhancing CAPA processes.
How to Display CAPA (Corrective and Preventive Action) Skills on Your Resume
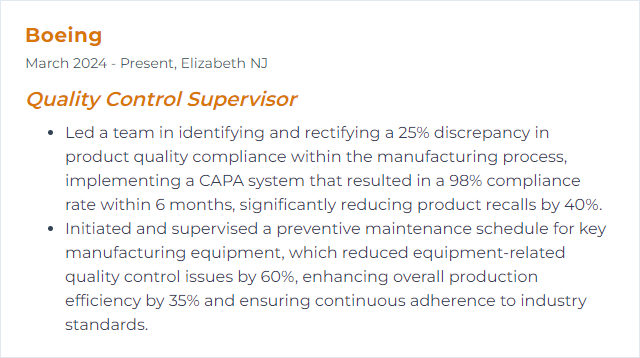
8. GMP (Good Manufacturing Practices)
GMP (Good Manufacturing Practices) are standardized guidelines ensuring products are consistently produced and controlled according to quality standards. For a Quality Control Supervisor, it involves overseeing the adherence to these protocols to guarantee product safety and efficacy throughout the manufacturing process.
Why It's Important
GMP ensures products are consistently produced and controlled according to quality standards, minimizing risks involved in production that cannot be eliminated through testing the final product. For a Quality Control Supervisor, it's crucial for ensuring compliance, product safety, and customer satisfaction.
How to Improve GMP (Good Manufacturing Practices) Skills
Improving GMP (Good Manufacturing Practices) as a Quality Control Supervisor involves a strategic approach focused on compliance, continuous training, and process optimization. Here's a concise guide:
Stay Updated with Regulations: Regularly review and update your knowledge on GMP regulations from authoritative sources like the FDA and EMA.
Implement Continuous Training: Ensure ongoing training programs for staff on GMP standards and updates. Use resources from ISPE for comprehensive training materials.
Enhance Documentation Practices: Adopt clear and thorough documentation procedures. Refer to WHO guidelines for best practices in documentation.
Conduct Regular Audits: Perform regular internal audits to identify and rectify non-compliance issues. Utilize tools and checklists from GMP Publishing for effective auditing.
Optimize Quality Control Processes: Streamline QC processes for efficiency and compliance. Explore ASQ’s resources for quality control improvement strategies.
Foster a Culture of Quality: Encourage a workplace culture that prioritizes quality and compliance. Engage with forums like PharmOut to share knowledge and experiences.
Leverage Technology: Use quality management software to streamline GMP processes. Consider options listed on Capterra for finding the right tool.
By focusing on these areas, you can significantly enhance GMP compliance and quality control in your manufacturing operations.
How to Display GMP (Good Manufacturing Practices) Skills on Your Resume
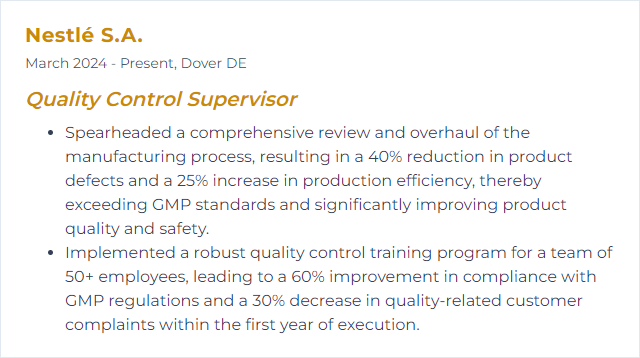
9. SAP Quality Module
The SAP Quality Management (QM) module is a comprehensive software solution designed for managing all aspects of quality control and assurance processes. It enables a Quality Control Supervisor to oversee quality planning, inspection, control, and certification processes integrated with production, procurement, and sales, ensuring compliance with quality standards and enhancing product reliability.
Why It's Important
The SAP Quality Module is crucial for a Quality Control Supervisor because it streamlines and automates quality management processes, ensuring compliance with industry standards, enhancing product quality, and minimizing defects and waste. This leads to improved customer satisfaction and operational efficiency.
How to Improve SAP Quality Module Skills
Improving the SAP Quality Module requires a strategic approach focused on enhancing system utilization, process optimization, and staff training. Here’s a concise guide for a Quality Control Supervisor:
Understand the Basics:Begin with a solid understanding of the SAP Quality Module's capabilities. SAP's official Quality Management (QM) page provides foundational knowledge.
Customize for Your Needs:Tailor the SAP QM to fit your company's specific quality control processes. Utilize the Customizing Guide to adjust settings according to your operational requirements.
Automate Processes:Leverage SAP QM to automate routine tasks, such as data entry and report generation, to increase efficiency. Explore SAP Automation for insights.
Integrate with Other Modules:Ensure seamless data flow between SAP QM and other SAP modules (e.g., Material Management, Production Planning). This integration enhances overall operational visibility and control.
Train Your Team:Invest in comprehensive training for your team to ensure they can effectively use SAP QM. SAP offers specific training courses for various modules, including QM.
Utilize Advanced Analytics:Use SAP's advanced analytics features to gain insights into quality performance, identify trends, and make informed decisions. The SAP Analytics Cloud is a powerful tool for this purpose.
Regularly Update Your System:Keep your SAP system updated to benefit from the latest features and security enhancements. Follow SAP's official release strategy for guidance.
Seek Feedback and Continuously Improve:Regularly solicit feedback from users to identify pain points and areas for improvement. Engage with the SAP community through forums like SAP Community for shared insights and tips.
By focusing on these areas, a Quality Control Supervisor can significantly enhance the efficiency and effectiveness of their SAP Quality Module.
How to Display SAP Quality Module Skills on Your Resume
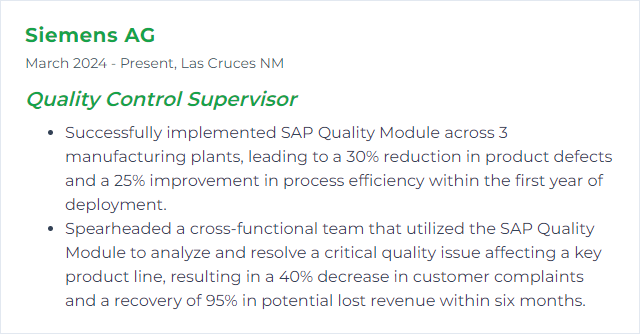
10. Minitab
Minitab is a statistical software package designed for data analysis and quality control, providing tools for statistical analysis, process improvement, and Six Sigma initiatives, helping Quality Control Supervisors to monitor and enhance product quality.
Why It's Important
Minitab is important for a Quality Control Supervisor because it provides powerful statistical analysis, quality improvement, and process control tools, enabling efficient monitoring, analysis, and enhancement of product quality and manufacturing processes.
How to Improve Minitab Skills
To improve your proficiency with Minitab as a Quality Control Supervisor, focus on the following steps:
Engage in Official Training: Enroll in Minitab's official training courses tailored to quality improvement that cover basic to advanced statistical analysis techniques.
Utilize Online Resources: Explore online platforms like LinkedIn Learning for courses on Minitab and quality control principles.
Practice Regularly: Apply your learning on real datasets or simulated projects to cement your understanding of various tools and functions.
Join User Groups: Participate in Minitab User Groups or forums for networking and knowledge exchange with other quality control professionals.
Stay Updated: Regularly check Minitab's official blog for updates, tips, and case studies on how to better utilize the software in quality control.
By focusing on consistent learning, practical application, and community engagement, you can significantly enhance your Minitab skills and thereby improve quality control processes within your organization.
How to Display Minitab Skills on Your Resume
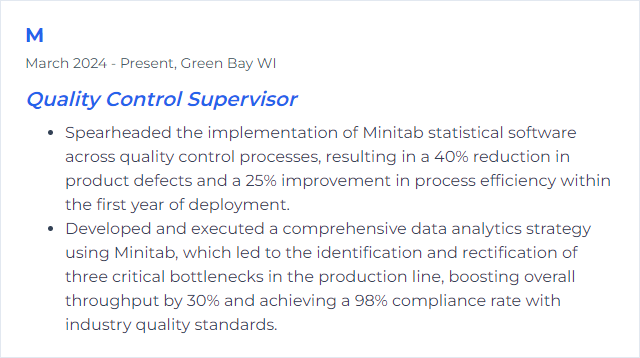
11. FMEA (Failure Mode and Effects Analysis)
FMEA (Failure Mode and Effects Analysis) is a systematic method used to identify, assess, and prioritize potential failures in products, processes, or systems, along with their causes and effects, to prevent defects and enhance quality.
Why It's Important
FMEA is important because it proactively identifies potential failures in products or processes and their possible effects, allowing for preemptive corrective actions to enhance quality, reliability, and safety, ultimately reducing costs and improving customer satisfaction.
How to Improve FMEA (Failure Mode and Effects Analysis) Skills
Improving FMEA involves a strategic approach focused on enhancing the thoroughness, accuracy, and effectiveness of the analysis. Below are concise steps tailored for a Quality Control Supervisor aiming to elevate FMEA processes:
Training and Team Composition: Ensure all team members, including cross-functional ones, are adequately trained in FMEA methodology. Diverse expertise leads to identifying a broader range of failure modes. ASQ offers detailed training resources.
Up-to-Date Information and Tools: Utilize the latest FMEA standards (e.g., AIAG & VDA FMEA Handbook) and software tools to streamline the analysis process. Keeping abreast of advancements ensures best practices are followed. AIAG Resources.
Risk Prioritization: Focus on Criticality Analysis to prioritize efforts on the most significant risks. This involves refining the Risk Priority Number (RPN) calculation or adopting alternative prioritization methods such as the Action Priority (AP) table from the updated FMEA guidelines.
Integrate with Other Quality Systems: Link FMEA with other quality management systems (QMS) like Six Sigma or ISO standards to create a holistic approach to risk management and continuous improvement. ISO 9001 Resources.
Data-Driven Approach: Leverage historical data, warranty claims, and customer feedback to identify potential failure modes proactively. Incorporating real-world data enhances the accuracy of risk assessments.
Regular Reviews and Updates: FMEA is a living document. Regularly review and revise the FMEA to reflect changes in design, process, or the external environment. This ensures the analysis remains relevant and effective.
Effective Communication: Develop clear communication channels to disseminate FMEA findings and actions across relevant departments. Ensuring findings are acted upon is as important as the analysis itself.
Benchmarking and Best Practices: Look beyond the organization to benchmark against industry best practices. This could involve participation in industry forums or workshops to stay updated on FMEA advancements. SAE International often offers relevant courses and materials.
By following these steps, a Quality Control Supervisor can significantly improve the effectiveness of FMEA, leading to enhanced product quality and reliability, reduced risks, and increased customer satisfaction.
How to Display FMEA (Failure Mode and Effects Analysis) Skills on Your Resume
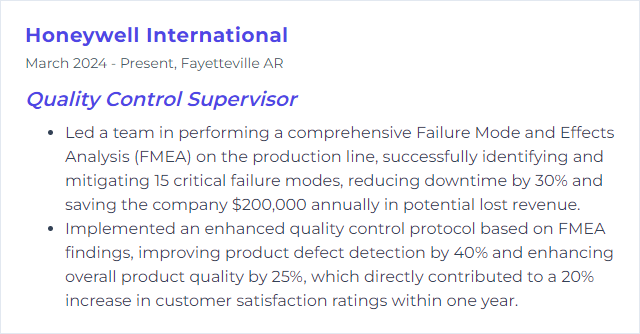
12. Auditing Standards
Auditing Standards are formal guidelines for conducting financial and operational audits, ensuring the accuracy, consistency, and reliability of audit processes and reports. They help Quality Control Supervisors ensure compliance, assess risks, and maintain quality across audit activities.
Why It's Important
Auditing standards are crucial because they ensure the accuracy, consistency, and reliability of audits, providing a framework for auditors to conduct their work effectively. This promotes confidence in the financial reporting process among stakeholders, including the Quality Control Supervisor, by ensuring that audits are performed to a universally high standard, thereby facilitating the identification and rectification of any discrepancies or areas for improvement in the organization's processes and controls.
How to Improve Auditing Standards Skills
Improving auditing standards, particularly from the perspective of a Quality Control Supervisor, involves a multifaceted approach focused on enhancing the quality, reliability, and efficiency of audit processes. Here are key strategies for improvement:
Continuous Education and Training: Ensure that auditors are up-to-date with the latest auditing standards, regulations, and best practices through regular training programs. The American Institute of Certified Public Accountants (AICPA) offers resources and training for auditors.
Leverage Technology: Adopt advanced auditing technologies for data analytics and automation to improve accuracy and efficiency. Tools such as ACL and IDEA can enhance audit processes.
Strengthen Quality Control Systems: Implement robust quality control frameworks that align with standards such as those from the Public Company Accounting Oversight Board (PCAOB) to ensure the integrity and reliability of audit processes.
Peer Review and External Inspections: Participate in peer review programs and welcome external inspections to identify areas for improvement. The AICPA Peer Review Program is a valuable resource for firms to enhance their practice.
Feedback Mechanism: Establish a structured feedback mechanism to gather insights from audited entities and auditors to continually improve auditing processes.
Ethical Standards: Uphold high ethical standards and foster a culture of honesty and integrity. The Institute of Internal Auditors (IIA) provides ethical guidelines and resources for auditors.
By focusing on these areas, a Quality Control Supervisor can significantly contribute to the enhancement of auditing standards, thereby ensuring the highest level of audit quality and reliability.
How to Display Auditing Standards Skills on Your Resume
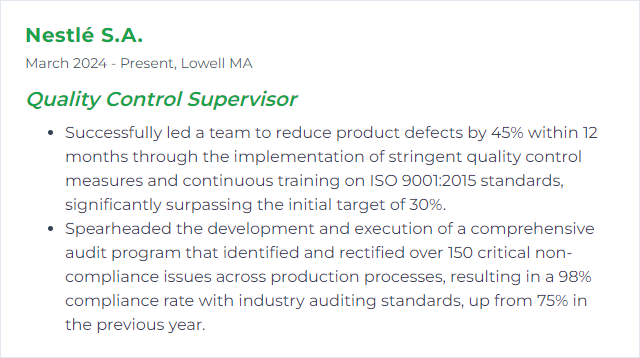