Top 12 Quality Control Specialist Skills to Put on Your Resume
In today's competitive job market, standing out as a quality control specialist requires a compelling resume that showcases a blend of technical expertise and soft skills. Highlighting the top quality control specialist skills on your resume can significantly increase your chances of catching the eye of potential employers and securing your next role in ensuring product excellence and safety.
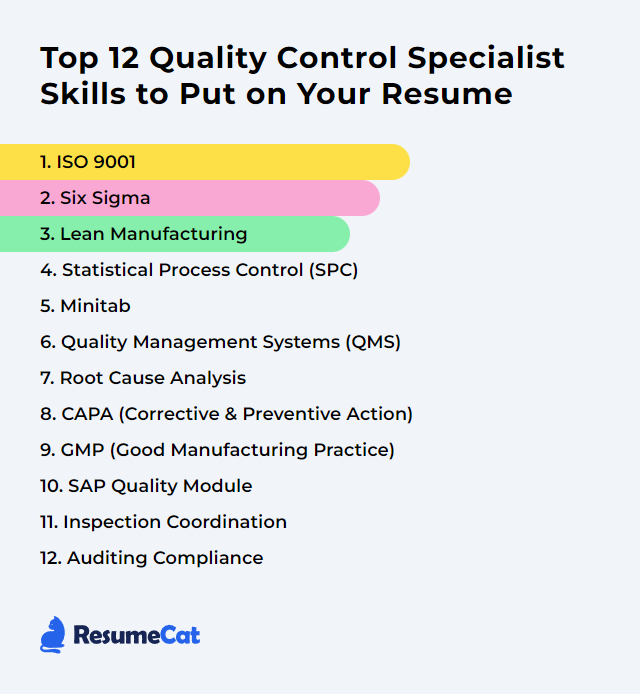
Quality Control Specialist Skills
- ISO 9001
- Six Sigma
- Lean Manufacturing
- Statistical Process Control (SPC)
- Minitab
- Quality Management Systems (QMS)
- Root Cause Analysis
- CAPA (Corrective and Preventive Action)
- GMP (Good Manufacturing Practice)
- SAP Quality Module
- Inspection Coordination
- Auditing Compliance
1. ISO 9001
ISO 9001 is an international standard for quality management systems (QMS), providing a framework for companies to ensure their products and services consistently meet customer and regulatory requirements through effective quality control and continuous improvement practices.
Why It's Important
ISO 9001 is important because it provides a framework for establishing, implementing, maintaining, and continuously improving a quality management system, ensuring that products and services consistently meet customer and regulatory requirements, enhancing customer satisfaction and operational efficiency for a Quality Control Specialist.
How to Improve ISO 9001 Skills
Improving ISO 9001 involves a continuous process of evaluating and enhancing your quality management system (QMS) to meet and exceed the standard's requirements. As a Quality Control Specialist, focus on:
Engage Leadership: Ensure management demonstrates leadership and commitment to the QMS. ISO 9001:2015 Clause 5 emphasizes leadership involvement.
Risk Management: Implement a risk-based thinking approach to proactively address potential issues. ISO 9001:2015 Clause 6 details planning for risk and opportunities.
Continuous Improvement: Make continuous improvement a part of your organization's culture. Utilize the Plan-Do-Check-Act (PDCA) cycle and quality improvement tools like Six Sigma. ASQ's page on Continuous Improvement offers strategies and tools.
Employee Engagement: Ensure all employees are aware of their role in the QMS and are trained appropriately. Engaged employees contribute to the effectiveness of the QMS. ISO's page on Training provides guidelines on enhancing employee competence.
Customer Focus: Regularly gather and analyze customer feedback to improve product quality and customer satisfaction. ISO 9001:2015 Clause 9 discusses performance evaluation, including customer satisfaction.
Internal Audits: Conduct regular internal audits to assess compliance with ISO 9001 standards and identify areas for improvement. ISO 19011:2018 provides guidelines for auditing management systems.
Document Control: Maintain comprehensive documentation and records as evidence of your QMS's conformance to ISO 9001 requirements. ISO 9000:2015 covers the fundamentals and vocabulary, including documentation principles.
Supplier Management: Evaluate and select suppliers based on their ability to supply products and services in accordance with your requirements. ISO 9001:2015 Clause 8 touches on operation controls, including external providers.
By focusing on these areas, you can enhance your organization's quality management practices, leading to improved performance, customer satisfaction, and ISO 9001 compliance.
How to Display ISO 9001 Skills on Your Resume
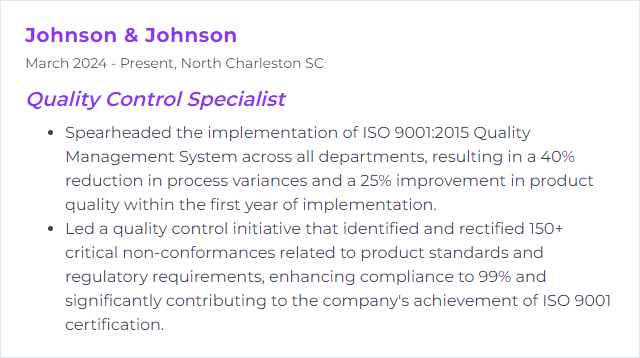
2. Six Sigma
Six Sigma is a data-driven methodology aimed at improving business processes by minimizing defects and variability, ensuring quality control and operational efficiency.
Why It's Important
Six Sigma is important because it provides a systematic and data-driven approach to reducing defects and improving quality, ensuring consistent, high-quality products and services, which is crucial for a Quality Control Specialist focused on maximizing efficiency and customer satisfaction.
How to Improve Six Sigma Skills
Improving Six Sigma involves a continuous effort to enhance process efficiency, reduce variability, and eliminate defects. For a Quality Control Specialist, focusing on the following key areas can help:
Education and Training: Continuously enhance your knowledge and skills in Six Sigma methodologies. Engage in certification programs such as Green Belt or Black Belt. ASQ offers a range of Six Sigma certification options.
Data Analysis: Sharpen your data analysis skills using statistical software tools. Understanding data deeply helps in identifying the root causes of defects. Tools like Minitab are widely used in Six Sigma projects.
Project Selection: Focus on selecting projects that align with business goals and have clear, measurable objectives. This ensures that your Six Sigma efforts contribute to overall organizational success.
Cross-functional Teamwork: Foster collaboration across different departments. Six Sigma projects often require input and cooperation from various parts of the organization. Effective teamwork leads to better problem-solving.
Continuous Improvement: Adopt the philosophy of Kaizen, or continuous improvement. This involves always looking for ways to make processes more efficient and eliminate waste. Lean Enterprise Institute provides resources on integrating lean principles with Six Sigma.
Benchmarking: Compare your processes and performance metrics against industry leaders. This can provide insights into areas for improvement and innovation. Benchmarking resources can be found through professional associations related to your industry.
By focusing on these areas, a Quality Control Specialist can significantly contribute to enhancing the effectiveness of Six Sigma initiatives within their organization.
How to Display Six Sigma Skills on Your Resume
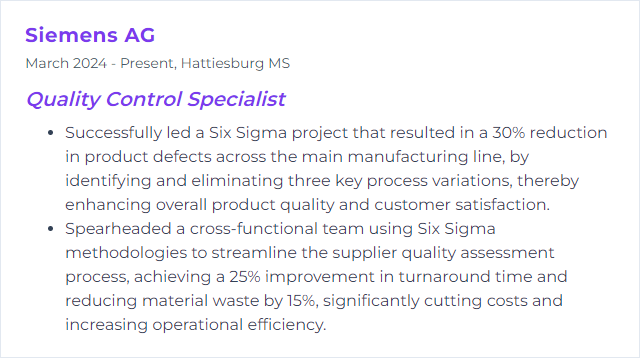
3. Lean Manufacturing
Lean Manufacturing is a systematic approach to minimizing waste within manufacturing systems while maximizing productivity, focusing on enhancing quality, cost, and delivery for the customer. For a Quality Control Specialist, it emphasizes preventing defects, reducing variability, and improving overall product quality through continuous improvement and efficient processes.
Why It's Important
Lean Manufacturing is important for a Quality Control Specialist because it focuses on eliminating waste and optimizing processes, leading to higher quality products, reduced defects, and increased customer satisfaction.
How to Improve Lean Manufacturing Skills
Improving Lean Manufacturing, particularly from a Quality Control Specialist perspective, involves a few focused strategies aimed at enhancing efficiency, reducing waste, and ensuring high-quality output. Here’s a concise guide:
Implement Continuous Improvement (Kaizen): Encourage a culture of continuous improvement by identifying inefficiencies and suggesting improvements. Kaizen fosters a proactive approach to quality and productivity enhancements. More on Kaizen
Adopt Poka-Yoke (Error Proofing): Utilize error-proofing techniques to prevent defects and ensure products are made right the first time. This involves designing processes that make it impossible or at least extremely difficult to make mistakes. Learn about Poka-Yoke
Utilize 5S Methodology: Maintain an organized and efficient workplace using the 5S system (Sort, Set in order, Shine, Standardize, Sustain) to reduce waste, optimize productivity, and achieve higher quality standards. 5S Explained
Implement Standard Work: Develop and follow standardized working methods to ensure each task is performed efficiently and consistently, leading to higher quality products and services. Standard Work Basics
Practice Jidoka (Autonomation): Enable machines and operators to detect when an abnormal condition has occurred and immediately stop work. This allows for immediate action to prevent the production of defective products. Understanding Jidoka
Engage in Root Cause Analysis: When defects occur, don’t just address the symptoms; dig deeper to identify and address the root cause to prevent recurrence. Tools like the 5 Whys or Fishbone Diagram can be effective. Root Cause Analysis Techniques
Lean Six Sigma: Incorporate Lean Six Sigma methodologies to minimize waste and variability in manufacturing processes, thereby improving quality and efficiency. Lean Six Sigma Overview
Employee Empowerment and Training: Empower employees with the training and resources they need to identify quality issues and inefficiencies. Well-informed and equipped staff can significantly contribute to lean objectives. Importance of Training
By focusing on these areas, a Quality Control Specialist can drive significant improvements in Lean Manufacturing, leading to more efficient processes, higher quality products, and reduced waste.
How to Display Lean Manufacturing Skills on Your Resume
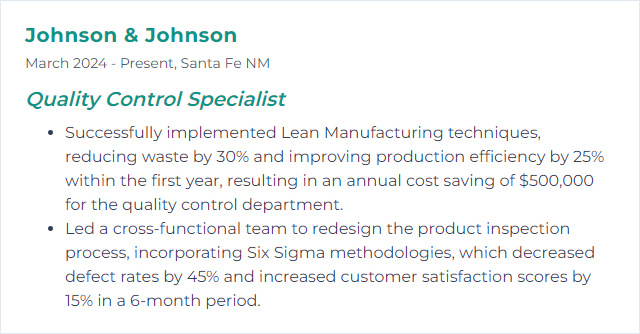
4. Statistical Process Control (SPC)
Statistical Process Control (SPC) is a method used in quality control that employs statistical techniques to monitor and control a process, ensuring that it operates at its full potential to produce conforming product with minimal waste. It involves using control charts to detect and prevent problems in the process before they occur, thereby maintaining process stability and improving process capability.
Why It's Important
Statistical Process Control (SPC) is important because it enables Quality Control Specialists to use statistical methods to monitor and control production processes. This ensures products meet quality standards consistently, reduces variability, and minimizes defects, leading to higher customer satisfaction and lower costs.
How to Improve Statistical Process Control (SPC) Skills
Improving Statistical Process Control (SPC) involves enhancing data collection, analysis, and process adjustment strategies to maintain product quality within desired specifications. Here are concise steps for a Quality Control Specialist:
Educate the Team: Ensure all team members understand SPC fundamentals and their roles in maintaining quality. Online resources like ASQ's SPC guide can provide valuable information.
Utilize Appropriate SPC Software: Select SPC software that fits your process needs and is user-friendly. Review options on Capterra's SPC software list.
Enhance Data Collection: Implement automated data collection systems for real-time, accurate data. Explore technologies such as IoT (Internet of Things) for efficient data gathering.
Regular Training and Refreshers: Conduct ongoing SPC training sessions and refreshers for the team. Online courses from platforms like Coursera or edX can be very useful.
Implement a Continuous Improvement Culture: Encourage a culture of continuous improvement where feedback is actively sought and implemented. Tools like Kaizen can be explored for continuous improvement methodologies.
Conduct Regular Audits: Regular SPC system audits help identify areas for improvement. Auditing guides can be found on ISO's website for standardized approaches.
Customize SPC for Your Needs: Tailor SPC tools and methods specifically for your manufacturing process. Industry-specific guidelines can be found through professional associations related to your field.
Leverage Statistical Tools: Beyond standard SPC charts, utilize advanced statistical tools for deeper insights. Resources for statistical tools can be found on NIST's Engineering Statistics Handbook.
By focusing on these areas, Quality Control Specialists can significantly improve their SPC practices, leading to better quality control and product consistency.
How to Display Statistical Process Control (SPC) Skills on Your Resume
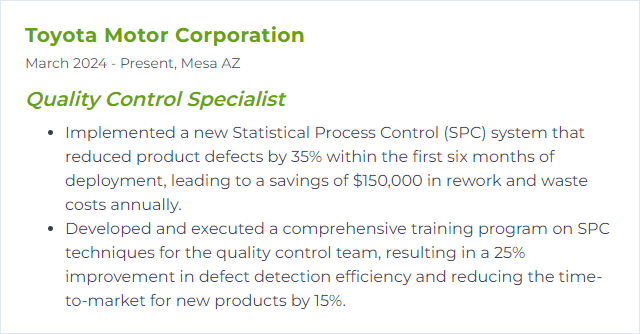
5. Minitab
Minitab is a statistical software package designed for data analysis and improvement in quality control processes, widely utilized by Quality Control Specialists for its powerful tools in analyzing, visualizing data, and monitoring quality performance.
Why It's Important
Minitab is important for a Quality Control Specialist because it provides powerful statistical analysis, quality improvement tools, and graphical capabilities to analyze and interpret quality data, enabling the identification of trends, patterns, and insights critical for maintaining and improving product quality and manufacturing processes efficiently.
How to Improve Minitab Skills
Improving your Minitab skills as a Quality Control Specialist involves a blend of enhancing your statistical knowledge, learning through practice, and leveraging Minitab's resources. Here are concise steps to achieve this:
Understand Statistical Concepts: Begin with a solid foundation in the statistical methods relevant to quality control. Khan Academy offers a comprehensive Statistics and Probability course.
Minitab Tutorials: Utilize the official Minitab Support page, which offers tutorials, case studies, and guidance on various functions and features.
Online Courses: Enroll in specialized courses for Quality Control using Minitab on platforms like Udemy or Coursera. These platforms often have courses tailored to enhancing your Minitab skills.
Practice with Real Data: Apply your learning on actual quality control data. This hands-on approach solidifies understanding and skills. Websites like Kaggle offer datasets for practice.
Join Forums and Groups: Engage with the Minitab community through forums and groups. The Minitab Community is a great place to ask questions, share knowledge, and learn from experienced users.
Feedback and Continuous Learning: Regularly seek feedback on your Minitab projects from peers or mentors. Embrace continuous learning by staying updated with the latest Minitab features and quality control trends.
By following these steps, you can significantly improve your Minitab skills, making you more effective in your role as a Quality Control Specialist.
How to Display Minitab Skills on Your Resume
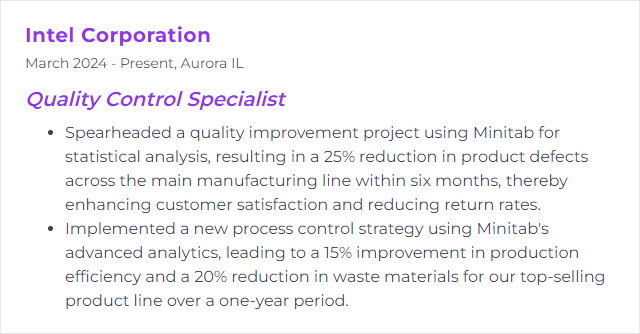
6. Quality Management Systems (QMS)
A Quality Management System (QMS) is a structured framework of procedures and processes used by an organization to ensure that its products or services meet and maintain the desired standards of quality. For a Quality Control Specialist, it serves as a guide for quality assessment and improvement, focusing on meeting customer requirements and enhancing their satisfaction.
Why It's Important
Quality Management Systems (QMS) are crucial as they provide a structured framework for consistently meeting customer requirements and enhancing their satisfaction. For a Quality Control Specialist, QMS is vital for standardizing processes, reducing errors, and ensuring continuous improvement in product quality and compliance.
How to Improve Quality Management Systems (QMS) Skills
Improving a Quality Management System (QMS) involves several key steps that ensure processes are efficient, compliant, and continuously improving. Here’s a concise guide for a Quality Control Specialist:
Assess and Analyze Current QMS: Regularly review your current processes to identify areas of improvement. Use tools like SWOT analysis to evaluate strengths, weaknesses, opportunities, and threats.
Engage Stakeholders: Involve all relevant stakeholders in the QMS improvement process. This includes employees, suppliers, and customers. Collect feedback through surveys or meetings to understand their needs and expectations. ISO’s guidelines on stakeholder engagement offer a good framework.
Implement a Continuous Improvement Culture: Adopt methodologies like Kaizen which focus on continuous, incremental improvements. Encourage innovation and feedback from all levels of the organization.
Training and Development: Ensure all team members are adequately trained on the latest quality standards and processes. Resources like ASQ’s Training Courses can be helpful.
Utilize Technology: Implement QMS software that automates processes, ensures compliance, and helps in managing documentation efficiently. Capterra’s list of QMS software provides a good starting point for research.
Regular Audits and Reviews: Conduct regular internal and external audits to ensure compliance with industry standards and regulations. Use these findings to make necessary adjustments. The ISO Auditing Practices Group offers valuable insights.
Benchmarking: Compare your QMS practices with those of leading organizations in your industry. This helps in identifying best practices and setting realistic improvement targets. Benchmarking resources from ASQ can guide you through this process.
Risk Management: Implement a proactive approach to identify, assess, and mitigate risks. ISO 31000:2018 provides guidelines for risk management principles and strategies.
By focusing on these areas, a Quality Control Specialist can significantly contribute to the enhancement of their organization's QMS, ensuring it not only meets but exceeds the required standards for quality and efficiency.
How to Display Quality Management Systems (QMS) Skills on Your Resume
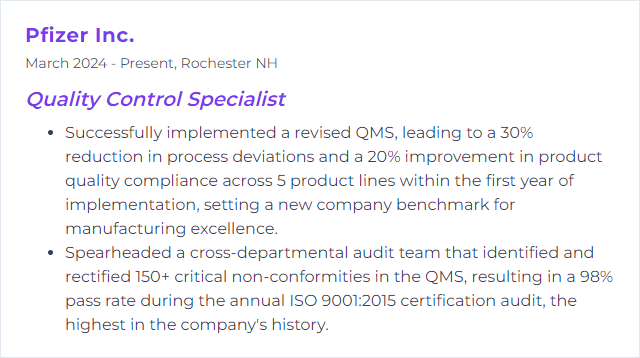
7. Root Cause Analysis
Root Cause Analysis (RCA) is a systematic process used by Quality Control Specialists to identify the underlying reasons for defects or problems in products or processes, aiming to implement long-term solutions that prevent recurrence.
Why It's Important
Root Cause Analysis (RCA) is crucial for a Quality Control Specialist because it identifies the underlying reasons for defects or problems, enabling the implementation of effective corrective actions to prevent recurrence, thereby ensuring product quality and customer satisfaction.
How to Improve Root Cause Analysis Skills
Improving Root Cause Analysis (RCA) as a Quality Control Specialist involves a systematic approach to identify the underlying reasons for a problem and implementing effective solutions. Here are concise steps with resources for further reading:
Clearly Define the Problem: Use precise language to describe the issue, focusing on what, where, when, and its magnitude. ASQ Problem Statement
Collect Data: Gather relevant data around the problem to understand its extent and impact. This includes historical data, process documentation, and stakeholder interviews. Data Collection Techniques
Identify Possible Causal Factors: List all potential causes that could lead to the problem. Techniques like the 5 Whys or Fishbone Diagram can be helpful. Fishbone Diagram Guide
Determine the Root Cause(s): Analyze the identified causes to pinpoint the root cause(s) using tools like Pareto Charts or Failure Mode and Effects Analysis (FMEA). FMEA Tool
Implement Corrective Actions: Develop and implement strategies to eliminate the root cause(s) and prevent recurrence. This step should involve action plans, responsibilities, and timelines. Corrective Action Guide
Monitor the Results: After implementing corrective actions, closely monitor the situation to ensure the problem is resolved and to verify the effectiveness of the solution. Monitoring and Evaluation
Document and Share Findings: Document the entire process and findings. Share the insights with relevant stakeholders to foster organizational learning and improvement. Knowledge Sharing Tips
Improving RCA is a continuous learning process. Always seek feedback and look for ways to refine your approach based on new insights and outcomes.
How to Display Root Cause Analysis Skills on Your Resume
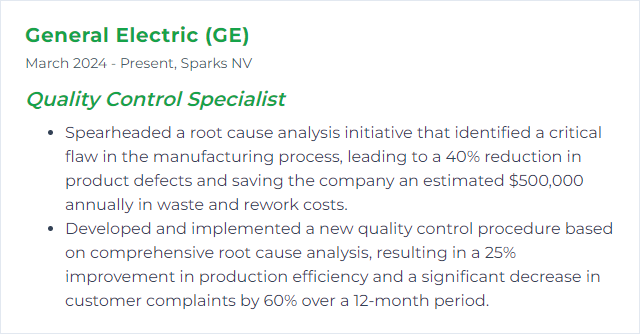
8. CAPA (Corrective and Preventive Action)
CAPA (Corrective and Preventive Action) is a process used by Quality Control Specialists to identify, address, and prevent the recurrence of errors or issues in products or processes, ensuring compliance and continuous improvement in quality management systems.
Why It's Important
CAPA is crucial for a Quality Control Specialist because it systematically addresses and rectifies identified deficiencies, ensuring product quality and compliance while preventing recurrence of issues, thus safeguarding consumer safety and maintaining regulatory standards.
How to Improve CAPA (Corrective and Preventive Action) Skills
Improving CAPA involves a focused approach to identify, assess, and correct non-conformities while preventing their recurrence. For a Quality Control Specialist, consider the following steps:
Identify and Document Issues Clearly: Clearly identify the root cause of non-conformities. Use tools like the 5 Whys technique to drill down to the underlying cause.
Risk Assessment: Prioritize actions based on a risk assessment. Tools like FMEA (Failure Mode and Effects Analysis) can help in assessing the potential impact of failures.
Develop Action Plans: Design corrective actions for immediate issues and preventive actions to avoid recurrence. Ensure actions are specific, measurable, achievable, relevant, and time-bound (SMART).
Implement Actions: Allocate resources and assign responsibilities for the implementation of the actions.
Training and Communication: Train relevant staff on the new procedures or changes implemented. Effective communication is key to ensuring compliance. Effective Communication Strategies can be useful.
Monitor and Review: Regularly monitor the effectiveness of the CAPA implemented using key performance indicators (KPIs). Modify the action plan based on the results.
Documentation and Record Keeping: Maintain thorough documentation of the CAPA process for accountability and future reference. ISO 9001:2015 emphasizes the importance of documentation.
Continuous Improvement: Adopt a culture of continuous improvement, using tools like PDCA (Plan-Do-Check-Act) to systematically improve the CAPA process.
For more detailed guidance, the Global Harmonization Task Force (GHTF) guidance document on CAPA and FDA’s Quality System Regulation provide comprehensive insights specific to medical devices but applicable across various sectors for improving CAPA processes.
How to Display CAPA (Corrective and Preventive Action) Skills on Your Resume
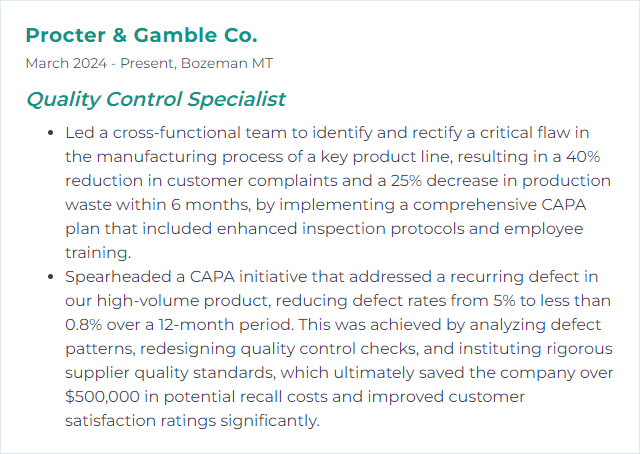
9. GMP (Good Manufacturing Practice)
GMP (Good Manufacturing Practice) refers to a system of guidelines that ensure products are consistently produced and controlled according to quality standards. For a Quality Control Specialist, it means adhering to established manufacturing protocols to guarantee the safety, quality, and efficacy of products.
Why It's Important
GMP ensures products are consistently produced and controlled according to quality standards, minimizing risks that cannot be eliminated through product testing. For a Quality Control Specialist, it's crucial for ensuring product safety, efficacy, and quality, and for meeting regulatory requirements.
How to Improve GMP (Good Manufacturing Practice) Skills
Improving Good Manufacturing Practice (GMP) involves a focus on compliance, quality, and continuous improvement. Here are concise steps tailored for a Quality Control Specialist:
Stay Updated: Regularly review GMP regulations and guidelines to ensure current practices align with the latest standards.
Training: Implement ongoing GMP training for all employees to reinforce the importance of quality and compliance.
Audit: Conduct regular internal and external audits to identify areas for improvement and ensure compliance with GMP standards.
Documentation: Maintain accurate and detailed documentation for all processes, which is crucial for tracking, analysis, and verification purposes.
Quality Control Testing: Enhance testing procedures by incorporating advanced analytical methods and equipment to detect and correct deviations from quality standards promptly.
Continuous Improvement: Employ a continuous improvement strategy, such as Six Sigma or Kaizen, to systematically refine manufacturing processes and increase efficiency.
Feedback Loop: Establish a robust mechanism for capturing feedback from audits, inspections, and quality control testing to inform process improvements.
By focusing on these areas, a Quality Control Specialist can significantly contribute to enhancing GMP within their organization.
How to Display GMP (Good Manufacturing Practice) Skills on Your Resume
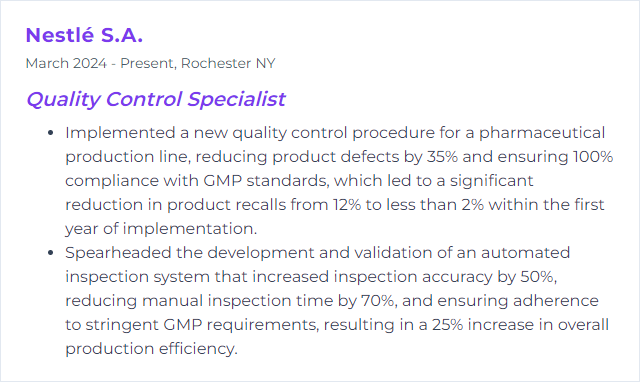
10. SAP Quality Module
The SAP Quality Module, officially known as SAP Quality Management (QM), is a comprehensive software tool designed to facilitate various aspects of quality control and assurance. It integrates with other SAP modules to support tasks such as quality planning, inspection, and control, as well as the management of certificates and quality notifications. It aids Quality Control Specialists in ensuring product compliance with quality standards and regulatory requirements, thereby enhancing product quality and customer satisfaction.
Why It's Important
The SAP Quality Module (QM) is crucial for a Quality Control Specialist as it streamlines and automates the entire quality management process, ensuring compliance with industry standards, reducing defects, and enhancing product quality and customer satisfaction.
How to Improve SAP Quality Module Skills
Improving the SAP Quality Module involves enhancing process efficiency, data accuracy, and integration across operations. Here's a concise guide for a Quality Control Specialist:
Streamline Process Flows: Customize the SAP QM to align with your specific quality control processes, minimizing manual data entry and reducing errors. SAP Process Improvement provides tools for automation and optimization.
Enhance Data Quality: Implement data validation rules within SAP QM to ensure accuracy and consistency of quality data. SAP's Master Data Governance can help establish a framework for quality data management.
Integrate with Manufacturing and Supply Chain: Ensure SAP QM is fully integrated with other SAP modules like Materials Management (MM) and Production Planning (PP) for a seamless flow of quality-related information. This can be achieved through SAP Integration Suite.
Leverage Reporting and Analytics: Utilize SAP's analytics and reporting tools to gain insights into quality performance, identifying trends and areas for improvement. SAP Analytics Cloud offers advanced analytics capabilities.
Continuous Training and Support: Regularly train staff on the latest SAP QM functionalities and best practices. SAP's Learning Hub offers resources for ongoing education.
Feedback and Continuous Improvement: Implement a feedback loop with end-users to continuously collect insights and suggestions for improving the SAP QM experience. SAP's Customer Influence program allows users to suggest and vote on improvements.
By focusing on these areas, a Quality Control Specialist can significantly enhance the effectiveness and efficiency of their organization's use of SAP Quality Module.
How to Display SAP Quality Module Skills on Your Resume
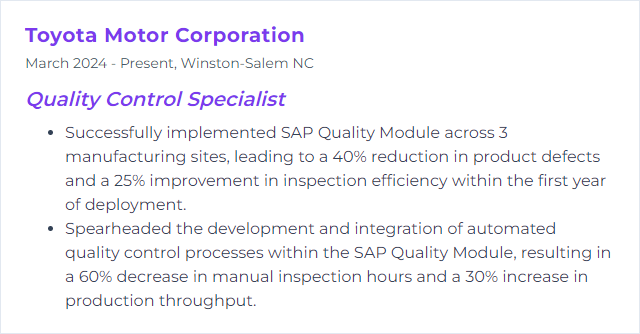
11. Inspection Coordination
Inspection Coordination, in the context of a Quality Control Specialist, involves organizing, scheduling, and overseeing inspection activities to ensure that products or services meet established quality standards. It includes coordinating with various departments, managing inspection teams, and ensuring compliance with regulations and specifications.
Why It's Important
Inspection coordination is crucial for a Quality Control Specialist as it ensures systematic examination and verification of processes and products, enabling early detection of defects, compliance with standards, and ultimately safeguarding product quality and customer satisfaction.
How to Improve Inspection Coordination Skills
Improving Inspection Coordination involves enhancing communication, organization, and technology use. Here’s a concise guide:
Streamline Communication: Utilize centralized communication platforms (e.g., Slack or Microsoft Teams) to ensure clear and timely communication among all stakeholders.
Implement Project Management Tools: Use project management software like Trello or Asana to organize tasks, schedules, and responsibilities, enhancing transparency and accountability.
Standardize Processes: Create standardized inspection checklists and procedures available through shared drives (like Google Drive or Dropbox) to maintain consistency and efficiency.
Leverage Quality Management Software (QMS): Adopt a QMS like Qualio or TrackWise to integrate all quality control processes, including inspection coordination, in one platform.
Continuous Training: Ensure ongoing training for the team on the latest inspection techniques and technologies through e-learning platforms like LinkedIn Learning or Coursera.
Feedback Loops: Establish regular feedback sessions with the team and external stakeholders to identify bottlenecks and areas for improvement in the inspection process.
By focusing on these strategies, a Quality Control Specialist can significantly enhance the efficiency and effectiveness of Inspection Coordination.
How to Display Inspection Coordination Skills on Your Resume
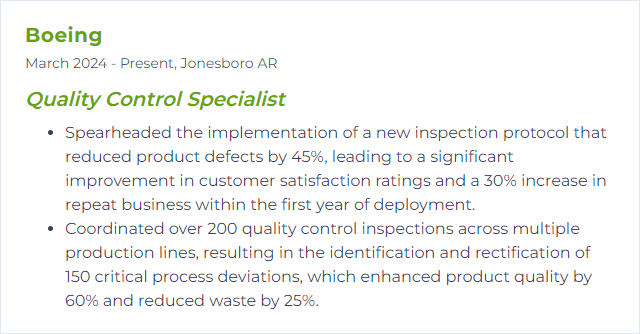
12. Auditing Compliance
Auditing compliance, in the context of a Quality Control Specialist, involves systematically reviewing and evaluating the extent to which processes and procedures adhere to internal standards and external regulatory requirements to ensure quality and efficacy in products or services.
Why It's Important
Auditing compliance is crucial for a Quality Control Specialist as it ensures that processes, products, and systems meet established quality standards, regulatory requirements, and customer expectations, thereby minimizing risks, enhancing efficiency, and maintaining the organization's credibility and competitive edge.
How to Improve Auditing Compliance Skills
Improving auditing compliance, especially for a Quality Control Specialist, involves a focused approach on understanding regulatory standards, implementing robust documentation processes, and fostering a culture of continuous improvement. Here are concise steps to achieve better auditing compliance:
Educate and Train: Ensure all team members, including management, are regularly educated on the latest compliance standards and auditing techniques. Compliance Online offers a variety of training resources.
Implement Strong Documentation Practices: Maintain detailed and organized records of all processes, changes, and quality control checks. This aids in transparency and accountability. Tools like DocuWare can streamline document management.
Conduct Regular Internal Audits: Regular self-assessments can help identify and rectify compliance issues before they escalate. Resources like AuditBoard offer solutions for managing internal audit processes effectively.
Engage in Continuous Improvement: Utilize feedback from audits to refine and improve processes continuously. Implementing a Quality Management System (QMS) like ISO 9001 can guide you in establishing a framework for continuous improvement.
Leverage Technology: Utilize compliance management software to streamline compliance processes, ensuring that all regulatory requirements are met efficiently. Qualio is a cloud-based quality management system designed for the life sciences industry.
Foster a Culture of Compliance: Encourage an organizational culture where compliance is valued and rewarded, ensuring that it becomes a part of the everyday workflow and not just a requirement. Insights on building this culture can be found through ASQ (American Society for Quality).
By focusing on education, documentation, regular audits, continuous improvement, leveraging technology, and fostering a compliant culture, a Quality Control Specialist can significantly improve auditing compliance.
How to Display Auditing Compliance Skills on Your Resume
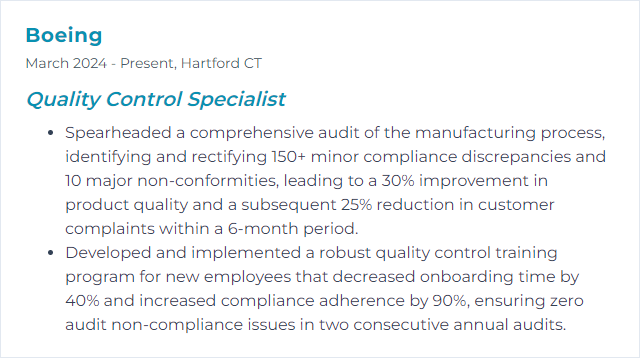