Top 12 Quality Control Manager Skills to Put on Your Resume
In the highly competitive field of quality control management, showcasing the right set of skills on your resume can significantly elevate your candidacy. This article highlights the top 12 skills that quality control managers should emphasize to stand out to potential employers, ensuring they project a profile of expertise, efficiency, and leadership.
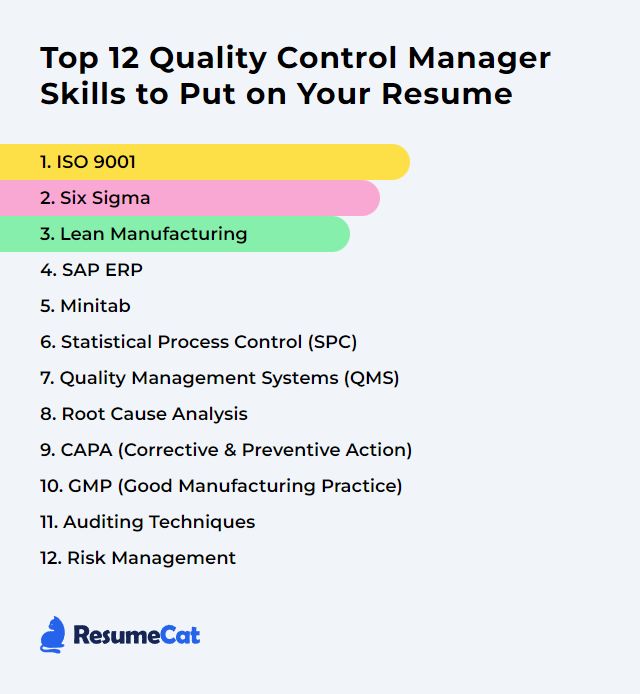
Quality Control Manager Skills
- ISO 9001
- Six Sigma
- Lean Manufacturing
- SAP ERP
- Minitab
- Statistical Process Control (SPC)
- Quality Management Systems (QMS)
- Root Cause Analysis
- CAPA (Corrective and Preventive Action)
- GMP (Good Manufacturing Practice)
- Auditing Techniques
- Risk Management
1. ISO 9001
ISO 9001 is an international standard that specifies requirements for a quality management system (QMS), enabling organizations to ensure consistent quality in their products and services, meet customer and regulatory requirements, and continuously improve. For a Quality Control Manager, it provides a framework for establishing, implementing, maintaining, and improving quality control processes.
Why It's Important
ISO 9001 is important because it provides a framework for Quality Control Managers to ensure consistent quality in processes and products, meet customer requirements, and enhance customer satisfaction through continuous improvement.
How to Improve ISO 9001 Skills
Improving ISO 9001 involves focusing on core areas such as leadership commitment, customer satisfaction, process optimization, and continuous improvement. Here's a concise guide tailored for a Quality Control Manager:
Leadership Commitment: Ensure top management visibly supports and engages in quality initiatives. Leadership should regularly review the quality management system (QMS) to align with organizational goals (ISO - Leadership and Commitment).
Customer Focus: Enhance customer satisfaction by understanding and meeting customer requirements, including gathering and addressing feedback systematically (ISO - Customer Satisfaction).
Process Optimization: Map out all critical processes and their interactions. Apply the Plan-Do-Check-Act (PDCA) cycle to optimize these processes for efficiency and effectiveness, reducing wastage and improving quality (ASQ - The Plan-Do-Check-Act Cycle).
Risk Management: Incorporate risk-based thinking into the QMS. Identify potential risks and opportunities in processes, and take proactive measures to mitigate them (ISO - Risk Management).
Employee Engagement: Involve all employees in quality improvement initiatives. Provide necessary training and encourage open communication to harness their knowledge and skills in enhancing the QMS (ISO - Involvement of People).
Continuous Improvement: Foster a culture of continuous improvement through regular audits, management reviews, and the implementation of corrective actions to address non-conformities (ISO - Improvement).
Performance Measurement: Establish key performance indicators (KPIs) aligned with quality objectives. Regularly monitor and analyze these metrics to inform decision-making and strategic planning (ISO - Monitoring and Measurement).
Supplier Management: Evaluate and select suppliers based on their ability to supply products and services in accordance with the organization’s requirements. Maintain a strong supplier relationship for continual improvement (ISO - Control of Externally Provided Processes, Products, and Services).
Documentation and Record Keeping: Maintain comprehensive documentation of the QMS, including policies, objectives, procedures, and records. This ensures clarity, consistency, and institutional memory (ISO - Documentation).
Internal Audits and Management Review: Regularly conduct internal audits to assess the effectiveness of the QMS and identify areas for improvement. Use findings to drive management review sessions and strategic improvements (ISO - Internal Audit).
For further detailed guidance, refer to the official ISO 9001:2015 documents and resources provided by the International Organization for Standardization (ISO) and the American Society for Quality (ASQ).
How to Display ISO 9001 Skills on Your Resume
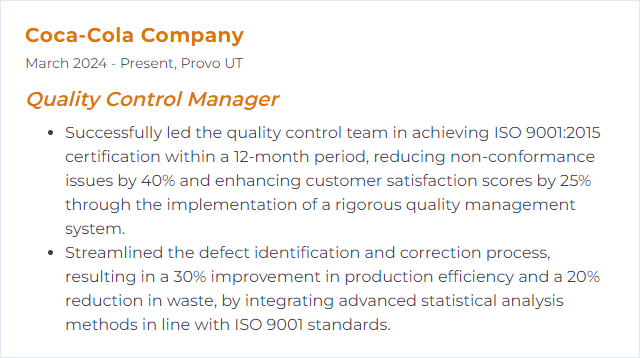
2. Six Sigma
Six Sigma is a data-driven methodology and a set of tools aimed at process improvement by reducing defects and variability, ensuring quality control, and enhancing performance to meet customer satisfaction.
Why It's Important
Six Sigma is important because it provides a rigorous and systematic methodology for improving processes, reducing defects, and enhancing quality, thereby ensuring customer satisfaction and business efficiency, which are critical responsibilities for a Quality Control Manager.
How to Improve Six Sigma Skills
Improving Six Sigma involves enhancing the quality and efficiency of processes by reducing variability and defects. For a Quality Control Manager, here are concise steps to improve Six Sigma:
Continuous Education: Invest in ongoing Six Sigma training for your team to keep skills sharp. ASQ's Six Sigma Training is a valuable resource.
Project Selection: Focus on projects with clear business impact. Utilize tools like Project Charter to define scope and goals.
Data Analysis: Emphasize data-driven decision making. Master statistical tools like Minitab for thorough data analysis.
Process Improvement: Apply DMAIC (Define, Measure, Analyze, Improve, Control) rigorously. iSixSigma's DMAIC Guide offers detailed insights.
Change Management: Foster a culture that embraces change. Resources like Prosci’s Change Management can guide organizational change efforts.
Benchmarking: Regularly benchmark against industry standards to identify areas for improvement. Benchmarking Reports by ASQ can be a starting point.
Customer Feedback: Integrate customer feedback into quality improvement processes. Tools like SurveyMonkey can facilitate gathering insights.
Lean Integration: Combine Six Sigma with Lean principles to speed up processes while maintaining quality. Lean Six Sigma Overview provides a good introduction.
By focusing on these areas, a Quality Control Manager can significantly enhance the effectiveness of Six Sigma initiatives within their organization.
How to Display Six Sigma Skills on Your Resume
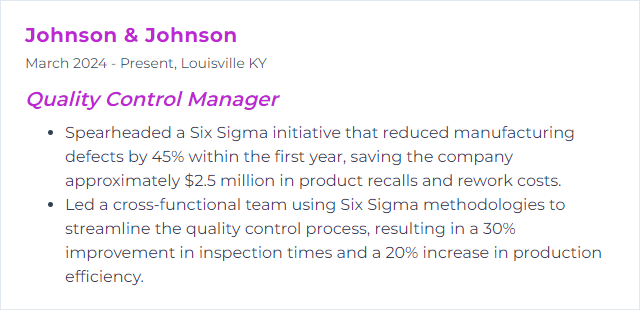
3. Lean Manufacturing
Lean Manufacturing is a systematic approach to identifying and eliminating waste through continuous improvement, focusing on maximizing product value for the customer with fewer resources. For a Quality Control Manager, it emphasizes enhancing product quality and reliability while minimizing defects and production inefficiencies.
Why It's Important
Lean Manufacturing is important because it aims to maximize customer value while minimizing waste, directly contributing to higher product quality and consistency, reduced costs, and improved overall efficiency, aligning with the key responsibilities of a Quality Control Manager to ensure optimal product standards and operational excellence.
How to Improve Lean Manufacturing Skills
Improving Lean Manufacturing, especially from a Quality Control Manager perspective, involves focusing on processes that enhance efficiency, reduce waste, and ensure the highest quality of production. Here are concise steps to achieve this:
- Implement Continuous Improvement: Adopt Kaizen principles to encourage continuous small improvements involving every employee.
- Standardize Processes: Develop and standardize work processes to reduce variability, which improves quality and efficiency.
- Use Visual Management: Implement visual management tools like 5S to organize the workplace, making it easier to identify and eliminate waste.
- Apply Root Cause Analysis: When quality issues occur, use techniques like the 5 Whys to investigate and solve the underlying problems, preventing recurrence.
- Focus on Preventive Maintenance: Implement a Total Productive Maintenance (TPM) strategy to reduce machine downtime and defects.
- Empower Teams: Encourage quality circles or cross-functional teams to identify and solve quality problems, promoting a culture of quality and continuous improvement.
- Leverage Technology: Use Lean Manufacturing Software to track and analyze data for better decision-making and process optimization.
- Supplier Quality Management: Work closely with suppliers to ensure they understand and meet your quality requirements, possibly through Supplier Quality Management practices.
By focusing on these areas, a Quality Control Manager can significantly contribute to the efficiency and effectiveness of Lean Manufacturing initiatives.
How to Display Lean Manufacturing Skills on Your Resume
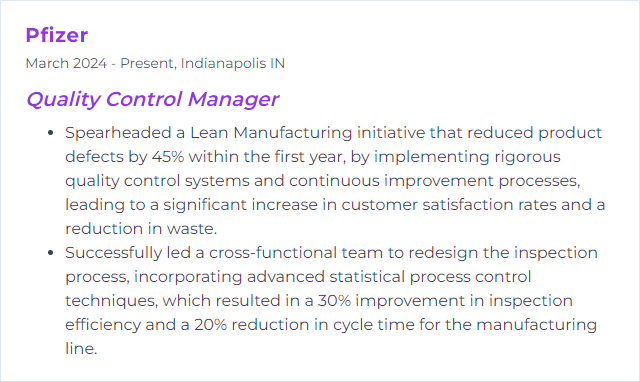
4. SAP ERP
SAP ERP is an integrated enterprise resource planning software that streamlines and automates business processes, including quality management, providing tools for effective monitoring, control, and improvement of product quality standards.
Why It's Important
SAP ERP is crucial for a Quality Control Manager as it integrates all facets of quality management, ensuring consistency, compliance, and continuous improvement in products and processes through real-time data analysis and reporting.
How to Improve SAP ERP Skills
Improving SAP ERP, particularly from a Quality Control Manager's perspective, involves enhancing data accuracy, automation, and integration. Focus on these areas:
- Implement Automation: Use SAP's Quality Management (QM) module to automate routine tasks, reducing human error and improving efficiency.
- Data Accuracy: Ensure high data quality in your ERP system. Leverage SAP Master Data Governance to maintain, validate, and distribute master data.
- Integration with Manufacturing Execution Systems (MES): Enhance operational visibility and control by integrating SAP ERP with MES solutions. This SAP Integration Scenario guide provides insights on system integration.
- Continuous Training: Regularly update the skills of your team on the latest SAP ERP features and best practices. This ensures efficient system use and problem-solving.
- Leverage Analytics: Use SAP Analytics Cloud to gain insights into quality control metrics, enabling data-driven decision-making.
- Feedback Loop: Establish a feedback loop with end-users to continuously identify and implement improvements in the SAP ERP system, enhancing its effectiveness in quality management.
By focusing on these strategies, you can significantly improve the functionality and efficiency of SAP ERP for quality control management.
How to Display SAP ERP Skills on Your Resume

5. Minitab
Minitab is a statistical software tool designed for data analysis and quality improvement, widely used by Quality Control Managers for analyzing quality-related issues, monitoring process performance, and making data-driven decisions to enhance product quality and process efficiency.
Why It's Important
Minitab is important for a Quality Control Manager as it provides powerful statistical analysis, allowing for effective decision-making to improve and maintain product quality and consistency.
How to Improve Minitab Skills
To improve your proficiency in Minitab as a Quality Control Manager, focus on the following steps:
Understand Basic Statistics: A solid foundation in statistics is crucial. Brush up on statistical concepts relevant to quality control. Khan Academy offers comprehensive lessons.
Minitab Training: Enroll in Minitab's official training courses tailored for various expertise levels, from beginner to advanced.
Practice with Real Data: Apply your learning on actual quality control data. This hands-on approach helps reinforce concepts. Utilize sample datasets provided by Minitab or your own data.
Join Minitab Community: Engage with the Minitab Community to exchange knowledge, tips, and tricks with other Quality Control Managers and Minitab users.
Stay Updated: Regularly check Minitab’s blog and support section for updates, tutorials, and case studies relevant to quality control.
Use Minitab Assistant: Leverage the Assistant feature in Minitab, which guides users through various analyses step-by-step, making it easier to apply complex statistical methods.
Feedback and Improvement: Continuously seek feedback from your team on the statistical analysis process and use it to improve your Minitab skills and the overall quality control process.
By systematically following these steps, you'll enhance your Minitab capabilities, contributing to more effective and efficient quality control processes within your organization.
How to Display Minitab Skills on Your Resume
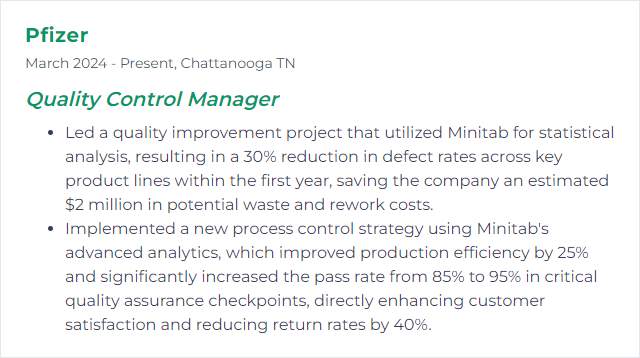
6. Statistical Process Control (SPC)
Statistical Process Control (SPC) is a method used by Quality Control Managers to monitor and control a process using statistical techniques to ensure it operates at its full potential, producing consistent, conforming products with minimal waste. It involves collecting data from production processes and using statistical methods to analyze variations, thereby identifying and eliminating sources of process instability and inefficiency.
Why It's Important
Statistical Process Control (SPC) is crucial for a Quality Control Manager as it provides a data-driven method to monitor, control, and improve process performance and quality in real-time, minimizing variability and defects, and ensuring product consistency and customer satisfaction.
How to Improve Statistical Process Control (SPC) Skills
Improving Statistical Process Control (SPC) involves a focused approach on data accuracy, employee training, and continuous process evaluation. Here's a concise guide for a Quality Control Manager:
Educate and Train Staff: Ensure all team members understand SPC fundamentals. Investing in training enhances data interpretation and process improvement skills.
Implement Real-Time Data Collection: Utilize software solutions for immediate data collection and analysis. This enables prompt identification and correction of process deviations.
Standardize Processes: Develop and enforce consistent methodology for data collection and analysis across all processes. Resources like NIST's Engineering Statistics Handbook provide guidelines for standardizing SPC practices.
Engage in Continuous Improvement: Adopt a culture of ongoing improvement by regularly reviewing SPC data and processes. Methods such as PDCA (Plan-Do-Check-Act) can guide systematic process enhancements.
Utilize Advanced SPC Tools: Beyond basic control charts, explore advanced SPC tools such as Process Capability Analysis to better understand and improve process performance.
Collaborate and Communicate: Foster a collaborative environment where feedback is encouraged. Effective communication tools can streamline discussions around SPC data and improvement strategies.
Improving SPC is a dynamic process that requires commitment to data-driven decision-making, continuous learning, and leveraging technology to enhance process control and quality outcomes.
How to Display Statistical Process Control (SPC) Skills on Your Resume
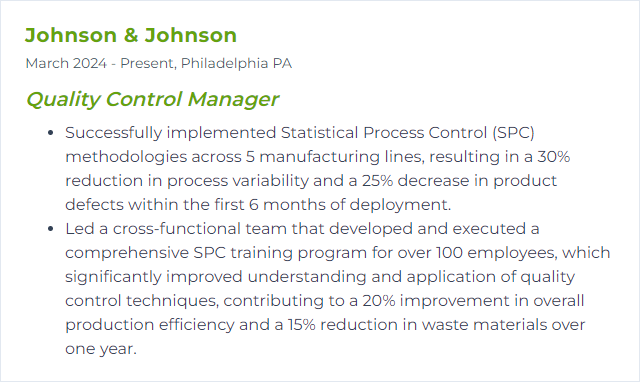
7. Quality Management Systems (QMS)
Quality Management Systems (QMS) are a set of policies, processes, and procedures required for planning and execution in the core business area of an organization. For a Quality Control Manager, QMS involves coordinating activities to direct and control an organization with regard to quality, ensuring products or services meet customer expectations and comply with regulations.
Why It's Important
Quality Management Systems (QMS) are crucial because they provide a structured framework for consistently meeting customer requirements and enhancing their satisfaction by improving processes, preventing errors, and facilitating continuous improvement in quality control. This ensures product/service reliability and compliance with regulations, thereby supporting the Quality Control Manager in achieving and maintaining high standards of quality.
How to Improve Quality Management Systems (QMS) Skills
Improving Quality Management Systems (QMS) requires a strategic approach focusing on continuous improvement, stakeholder engagement, and leveraging technology. Here's a concise guide:
Assess and Analyze Current System: Conduct a thorough audit of your current QMS to identify areas for improvement. Use tools like SWOT analysis for this purpose. ISO 9001 provides guidelines for quality management systems and can serve as a reference point.
Engage Stakeholders: Involve employees, customers, and suppliers in the improvement process. Their feedback is crucial for identifying weaknesses and opportunities. ASQ’s Engagement Strategies offer insights on maximizing stakeholder involvement.
Set Clear Objectives: Define specific, measurable, achievable, relevant, and time-bound (SMART) objectives for your QMS improvement plan. MindTools provides a guide on setting SMART goals.
Implement Technology Solutions: Adopt quality management software (QMS software) to automate processes, ensure compliance, and improve efficiency. Capterra lists and reviews various QMS software options.
Training and Development: Invest in continuous training and development programs for your employees to keep them updated on the latest quality standards and practices. Coursera offers courses on quality management.
Monitor, Review, and Act: Regularly review the performance of your QMS against the set objectives. Use key performance indicators (KPIs) for this purpose. Implement corrective actions for non-conformities and continuously look for opportunities to improve. The Balanced Scorecard Institute provides a framework for monitoring and managing performance.
Embrace Continuous Improvement: Adopt a culture of continuous improvement by integrating methodologies like Kaizen or Six Sigma into your QMS. Lean Enterprise Institute and ASQ’s Six Sigma Resources are valuable resources for understanding and implementing these methodologies.
By following these steps and utilizing the provided resources, a Quality Control Manager can effectively improve their organization's Quality Management System.
How to Display Quality Management Systems (QMS) Skills on Your Resume
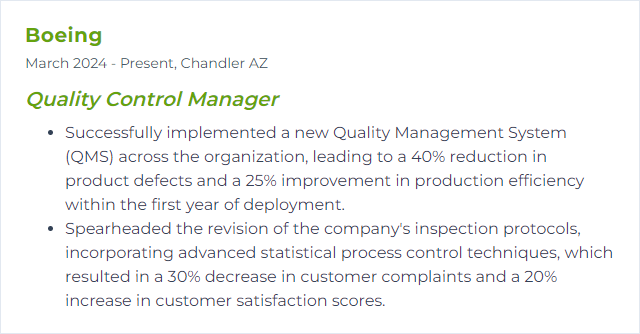
8. Root Cause Analysis
Root Cause Analysis (RCA) is a systematic process used by Quality Control Managers to identify the underlying reasons for defects or problems in a product or process, aiming to implement corrective actions that prevent recurrence.
Why It's Important
Root Cause Analysis (RCA) is crucial for a Quality Control Manager as it identifies the fundamental source of defects or problems, enabling the implementation of effective corrective actions to prevent recurrence, thus ensuring product quality and customer satisfaction.
How to Improve Root Cause Analysis Skills
Improving Root Cause Analysis (RCA) involves a systematic approach to identify the underlying issues that lead to a problem, rather than just addressing its symptoms. As a Quality Control Manager, enhancing RCA can significantly boost problem-solving effectiveness and prevent future occurrences. Here’s a concise guide:
Define the Problem Clearly: Start by accurately describing the issue, including when and where it was observed, to ensure a focused analysis.
Use Structured Methodologies: Employ proven RCA methodologies like the 5 Whys, Fishbone Diagrams (Ishikawa), and Failure Mode and Effects Analysis (FMEA). These tools help break down the problem and identify root causes systematically.
Gather and Analyze Data: Collect data related to the problem and use it to validate the root cause. This might involve reviewing records, performing tests, or analyzing processes.
Engage the Team: Foster a collaborative environment where team members from different departments can provide insights. Diverse perspectives can uncover hidden issues.
Implement Corrective Actions: Once the root cause is identified, develop and implement a corrective action plan. Ensure actions are specific, measurable, and time-bound.
Monitor Effectiveness: After implementing changes, closely monitor the outcomes to ensure the root cause has been effectively addressed. Adjust the plan as necessary.
Document and Share Learnings: Record the problem, the analysis process, and the solution. Sharing these findings helps prevent recurrence and facilitates continuous improvement.
For a deeper understanding and further resources, consider exploring ASQ's Root Cause Analysis resources and The TapRooT® System for root cause analysis, which offer comprehensive insights and tools tailored for Quality Control Managers aiming to enhance their RCA processes.
How to Display Root Cause Analysis Skills on Your Resume
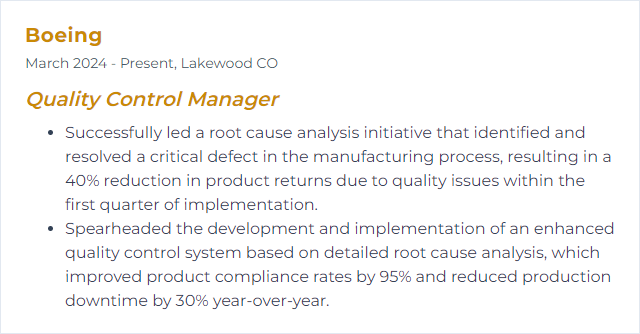
9. CAPA (Corrective and Preventive Action)
CAPA (Corrective and Preventive Action) is a process used by Quality Control Managers to identify, address, and eliminate non-conformities or defects in products and processes. It involves implementing corrective actions to fix immediate issues and preventive actions to prevent recurrence, ensuring continuous improvement and compliance with quality standards.
Why It's Important
CAPA is crucial for a Quality Control Manager because it systematically addresses and rectifies identified product or process deficiencies, preventing recurrence, ensuring compliance, and maintaining product quality and safety.
How to Improve CAPA (Corrective and Preventive Action) Skills
Improving CAPA involves a focused approach to identifying issues, implementing solutions, and preventing their recurrence. Here's a concise guide for a Quality Control Manager:
Identify Root Cause: Use tools like the 5 Whys or Fishbone Diagram to delve deep into the problem and understand its origin.
Risk Assessment: Prioritize CAPA activities based on risk, focusing on preventing issues with the highest impact. Tools like FMEA (Failure Mode and Effects Analysis) can be instrumental.
Develop Action Plan: Create a clear, actionable plan that includes specific actions, responsible parties, and deadlines. Ensure actions are SMART (Specific, Measurable, Achievable, Relevant, Time-bound).
Implement Changes: Execute the action plan effectively, ensuring all team members understand their roles and responsibilities. Communication and training are key.
Monitor and Verify: Use KPIs (Key Performance Indicators) to monitor the effectiveness of CAPAs. Tools like Control Charts can help track progress and verify improvement.
Review and Improve: Regularly review the CAPA process itself for opportunities to improve efficiency and effectiveness. Continuous improvement methodologies like PDCA (Plan-Do-Check-Act) can guide this.
Documentation and Record-Keeping: Maintain comprehensive documentation throughout the CAPA process. This facilitates auditing, tracking, and continual improvement efforts.
By systematically applying these steps, Quality Control Managers can enhance their CAPA processes, leading to improved product quality and customer satisfaction.
How to Display CAPA (Corrective and Preventive Action) Skills on Your Resume
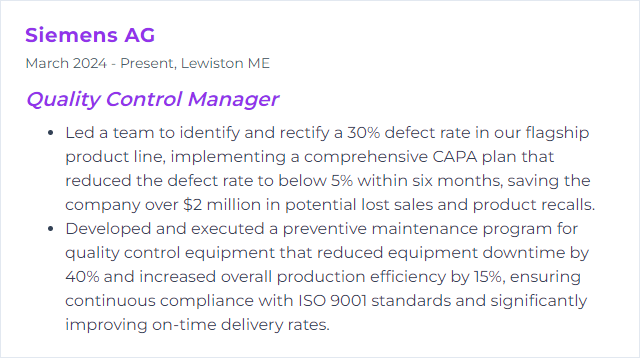
10. GMP (Good Manufacturing Practice)
GMP (Good Manufacturing Practice) is a set of guidelines ensuring that products are consistently produced and controlled according to quality standards, focusing on minimizing risks in production that cannot be eliminated through testing the final product. For a Quality Control Manager, GMP outlines the operational and documentation practices required to ensure product safety and efficacy, including validation, quality control, personnel qualifications, cleanliness, and complaint handling.
Why It's Important
GMP ensures products are consistently produced and controlled to quality standards, minimizing risks involved in production that cannot be eliminated through testing the final product. For a Quality Control Manager, it's crucial for ensuring compliance, product safety, and customer satisfaction.
How to Improve GMP (Good Manufacturing Practice) Skills
Improving GMP (Good Manufacturing Practice) involves a comprehensive approach focusing on adherence to quality standards, continuous training, and robust quality control systems. Here's a concise guide for a Quality Control Manager:
Strict Adherence to Regulatory Standards: Stay updated with the latest GMP guidelines from regulatory bodies like the FDA or EMA and ensure all processes align with these standards.
Continuous Training and Education: Implement ongoing training programs for staff at all levels to ensure they are aware of GMP principles and their roles in maintaining them.
Robust Documentation Practices: Maintain meticulous records of all processes, changes, and quality tests. Tools like MasterControl can help streamline this process.
Regular Audits and Self-Inspections: Conduct frequent internal audits to identify and rectify non-compliance issues before they escalate.
Invest in Quality Control Systems: Utilize advanced quality management systems (QMS) to automate and monitor quality in real time.
Foster a Culture of Quality: Encourage open communication and feedback within teams to promote a proactive approach to quality and compliance.
Implement Continuous Improvement Processes: Adopt methodologies like Lean Six Sigma to continuously analyze and improve manufacturing processes, thereby enhancing quality and efficiency.
By focusing on these key areas, a Quality Control Manager can significantly improve GMP within their organization, ensuring product safety and compliance with regulatory standards.
How to Display GMP (Good Manufacturing Practice) Skills on Your Resume
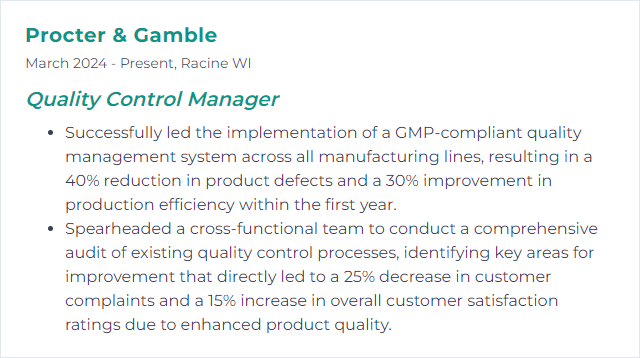
11. Auditing Techniques
Auditing techniques, in the context of a Quality Control Manager, involve systematic processes and procedures used to examine and evaluate the efficiency and effectiveness of a company's quality management system. These methods include interviews, observations, document reviews, and sampling, aiming to ensure compliance with standards, identify areas for improvement, and mitigate risks in product quality and safety.
Why It's Important
Auditing techniques are crucial for a Quality Control Manager as they ensure processes adhere to established standards, identify areas for improvement, and maintain product consistency, thereby safeguarding the organization's reputation and customer satisfaction.
How to Improve Auditing Techniques Skills
Improving auditing techniques as a Quality Control Manager involves a combination of continuous learning, adopting best practices, and leveraging technology. Here’s a concise guide:
Stay Updated with Standards: Keep abreast of the latest ISO standards and industry-specific regulations to ensure your audits are current.
Continuous Training: Invest in continuous training for yourself and your team to sharpen auditing skills and understand new methodologies.
Utilize Technology: Adopt audit management software to streamline processes, improve accuracy, and facilitate real-time reporting.
Risk-based Auditing: Focus on risk-based auditing approaches to prioritize areas that are critical to quality, using resources efficiently. The Institute of Internal Auditors offers insights into this approach.
Peer Review and Feedback: Engage in peer reviews and solicit feedback to uncover areas of improvement. Participating in forums like AuditBoard’s Community can provide valuable insights.
Benchmarking: Compare your auditing practices against those of leaders in your industry to identify improvement areas. ASQ Benchmarking provides resources and tools for effective benchmarking.
By focusing on these areas, a Quality Control Manager can significantly enhance their auditing techniques, leading to more efficient and effective quality control processes.
How to Display Auditing Techniques Skills on Your Resume
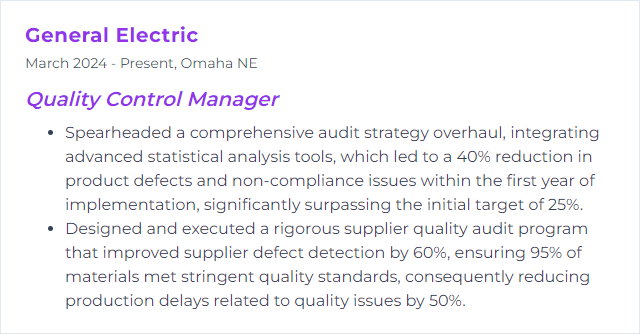
12. Risk Management
Risk management involves identifying, assessing, and mitigating risks to ensure quality and compliance in products or services, aiming to minimize potential negative impacts on the organization's goals.
Why It's Important
Risk management is crucial for a Quality Control Manager as it identifies, assesses, and mitigates potential threats to product quality and compliance, ensuring consistent product integrity and customer satisfaction while minimizing losses and liability.
How to Improve Risk Management Skills
Improving risk management, particularly for a Quality Control Manager, involves a strategic approach focused on identifying, assessing, and mitigating risks that could impact quality performance. Here's a concise guide:
Identify Risks: Start with a comprehensive risk identification process. Tools like SWOT (Strengths, Weaknesses, Opportunities, Threats) analysis can be helpful. ASQ's Risk Management Tools offer insights into various methodologies.
Assess Risks: Evaluate the identified risks based on their potential impact and probability. A Risk Matrix can assist in prioritizing risks by their severity.
Develop Mitigation Strategies: For each high-priority risk, develop and implement mitigation strategies. Techniques such as FMEA (Failure Mode and Effects Analysis) are valuable. The American Society for Quality provides a detailed guide on FMEA.
Monitor and Review: Continuously monitor the risks and the effectiveness of mitigation strategies. Adjust as needed to ensure risks are managed efficiently. The Project Management Institute discusses best practices in risk monitoring and review.
Foster a Risk Management Culture: Encourage open communication and training to ensure that risk management is an integral part of the organizational culture. ISO 31000:2018 provides guidelines on establishing a risk management framework.
By following these steps and utilizing the resources provided, a Quality Control Manager can significantly improve risk management practices within their organization.
How to Display Risk Management Skills on Your Resume
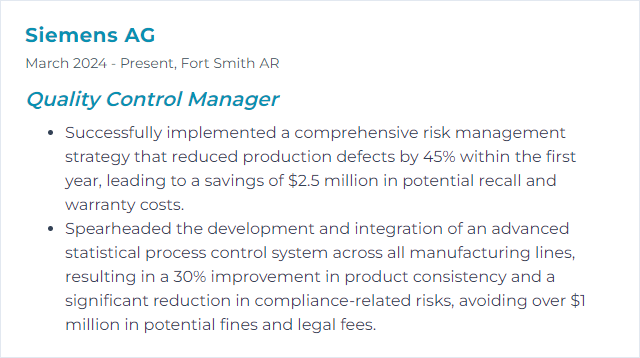