Top 12 Pipe Welder Skills to Put on Your Resume
In the highly specialized field of pipe welding, showcasing a robust set of skills on your resume can significantly elevate your job prospects and set you apart from the competition. Possessing a combination of technical proficiency, industry knowledge, and soft skills is essential for success in this demanding trade, making it crucial to highlight your top abilities effectively.
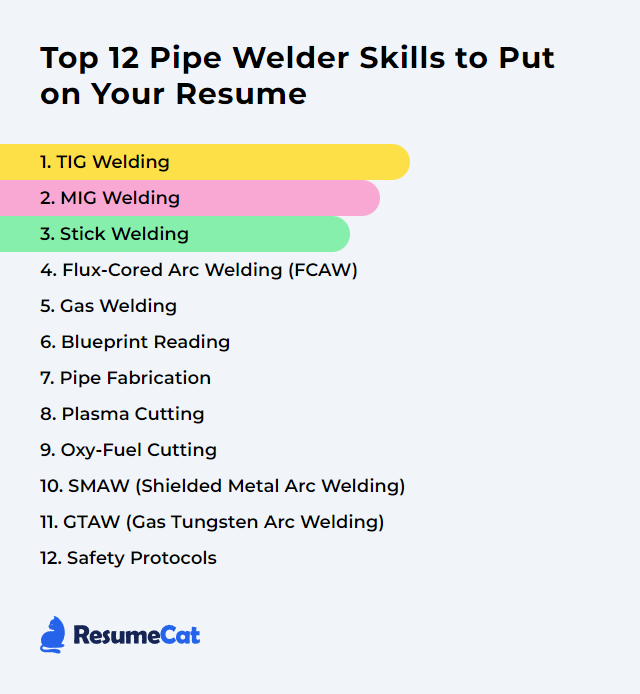
Pipe Welder Skills
- TIG Welding
- MIG Welding
- Stick Welding
- Flux-Cored Arc Welding (FCAW)
- Gas Welding
- Blueprint Reading
- Pipe Fabrication
- Plasma Cutting
- Oxy-Fuel Cutting
- SMAW (Shielded Metal Arc Welding)
- GTAW (Gas Tungsten Arc Welding)
- Safety Protocols
1. TIG Welding
TIG welding, short for Tungsten Inert Gas welding, is a precision welding technique using a tungsten electrode to produce the weld. For pipe welders, it's highly valued for its ability to create strong, high-quality welds on a variety of metals, including thin sections and different shapes of pipes, with great control over heat input and weld bead.
Why It's Important
TIG welding is important for a pipe welder because it allows for precise, high-quality welds on various materials, including thin metals, ensuring strong, clean, and visually appealing joints crucial for pipe integrity and leak prevention in critical applications.
How to Improve TIG Welding Skills
To improve TIG welding, especially for a pipe welder, follow these concise tips:
Proper Preparation: Ensure the pipe surface is clean and free of contaminants. Use a dedicated stainless steel brush for cleaning the metal surface before welding. American Welding Society
Correct Equipment Setup: Choose the right tungsten electrode type and diameter. A commonly used type for steel is 2% thoriated tungsten. Adjust your TIG welder settings according to the material thickness. Miller Welds Equipment Setup
Appropriate Gas and Flow Rate: Use argon or an argon-helium mix for most materials. Ensure the gas flow rate is adequate to protect the weld pool, typically between 15 to 20 cfh. Lincoln Electric Shielding Gas Guide
Consistent Torch Angle: Maintain a torch angle of about 15 to 20 degrees from vertical. This helps control the weld pool and ensures proper penetration.
Steady Travel Speed: Keep a consistent travel speed to ensure an even weld bead. Moving too fast can result in lack of fusion, while too slow can lead to excess heat input.
Practice and Patience: Regular practice on scrap material helps you refine your technique and adjust to different pipe sizes and positions.
Remember, skill improvement comes with understanding the fundamentals, consistent practice, and learning from each welding experience.
How to Display TIG Welding Skills on Your Resume
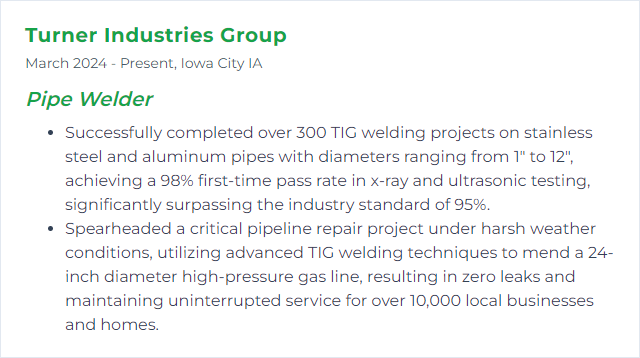
2. MIG Welding
MIG welding, or Metal Inert Gas welding, is a semi-automatic or automatic arc welding process where a continuous and consumable wire electrode and a shielding gas are fed through a welding gun. For a pipe welder, MIG welding offers a fast and versatile method to join pipes, applicable to a wide range of pipe materials and thicknesses.
Why It's Important
MIG welding is important for a pipe welder because it offers a versatile, efficient, and high-quality method for joining metals, crucial for constructing strong, leak-proof piping systems in various industries.
How to Improve MIG Welding Skills
Improving MIG welding, especially for a pipe welder, involves focusing on technique, equipment setup, and practice. Here are concise tips:
Preparation: Clean the pipe thoroughly to remove any contaminants. Good preparation ensures strong welds.
Equipment Setup: Ensure your MIG welder is correctly set up. This includes selecting the right wire type and diameter, adjusting tension, and choosing appropriate gas flow rates. MillerWelds offers detailed setup guidance.
Technique: Use the correct welding technique, which includes the right angle of the welding gun, maintaining a consistent travel speed, and proper body positioning. Practice the whip and pause technique for better bead appearance and penetration. Welding Tips and Tricks has practical advice on technique improvement.
Control Heat Input: Managing heat input is crucial to prevent warping or burn-through, especially on thinner pipes. This can be achieved by adjusting the voltage and wire speed settings on your MIG welder.
Practice: Regular practice on scrap pieces helps refine your skills, including handling different positions and orientations typical in pipe welding.
Safety: Always prioritize safety by wearing appropriate gear and working in a well-ventilated area. OSHA provides safety guidelines for welding, cutting, and brazing.
By focusing on these areas, you can significantly improve your MIG welding quality and efficiency as a pipe welder.
How to Display MIG Welding Skills on Your Resume
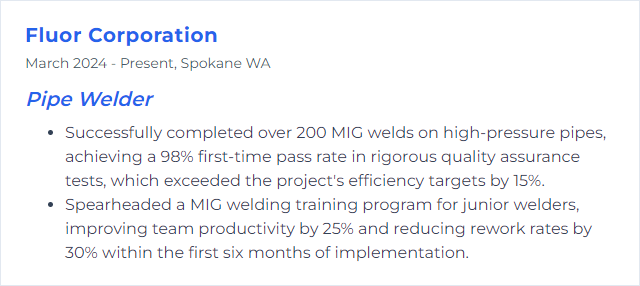
3. Stick Welding
Stick welding, also known as Shielded Metal Arc Welding (SMAW), is a manual arc welding process using a consumable electrode coated in flux to lay the weld. For a pipe welder, it's commonly used due to its versatility in welding various types of metals and positions, being well-suited for outdoor conditions and confined spaces often encountered in pipe welding.
Why It's Important
Stick welding is important for a pipe welder because it allows for versatile and robust welding in various positions and environments, including outdoor or in confined spaces, where precision and reliability in joining metals are crucial for the integrity and safety of piping systems.
How to Improve Stick Welding Skills
Improving stick welding, especially for pipe welders, involves enhancing technique, understanding electrode selection, and practicing consistently. Here are concise tips:
Electrode Selection: Choose the right electrode for the material and position. E6010 and E7018 are commonly used in pipe welding. Lincoln Electric provides detailed guidance on electrode characteristics.
Machine Settings: Adjust amperage based on electrode diameter and material thickness. Miller Welds offers advice on setting up your welder for various conditions.
Angle and Movement: Maintain a 5 to 10-degree drag angle for most positions. For overhead welding, Welding Tips and Tricks suggests a slightly pushing angle.
Clean Joint Preparations: Ensure surfaces are clean and free of contaminants. Proper preparation is crucial for a defect-free weld.
Practice: Consistent practice, including in challenging positions (6G for pipe welders), is essential. Practice on scrap material or in a welding booth to refine your skills.
Watch and Learn: Review tutorials and demonstrations from experienced welders. Platforms like WeldTube offer videos specifically for pipe welders.
Safety: Always prioritize safety by wearing appropriate gear and working in a well-ventilated area. OSHA's Welding, Cutting, and Brazing guidelines provide comprehensive safety advice.
By focusing on these areas, pipe welders can improve their stick welding technique and achieve better results.
How to Display Stick Welding Skills on Your Resume
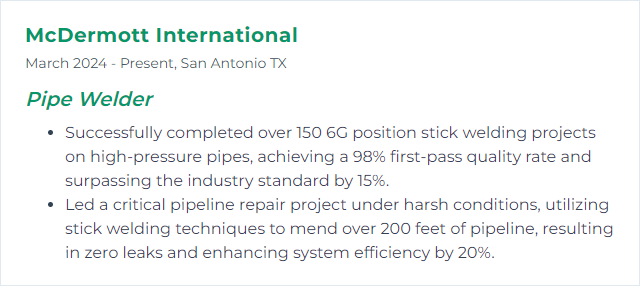
4. Flux-Cored Arc Welding (FCAW)
Flux-Cored Arc Welding (FCAW) is a semi-automatic or automatic arc welding process used by pipe welders, employing a continuous wire-fed electrode shielded by a flux core. This method is favored for its versatility, high deposition rates, and ability to weld in all positions with good penetration and weld quality.
Why It's Important
Flux-Cored Arc Welding (FCAW) is important for a Pipe Welder because it offers high welding speed and efficiency, excellent penetration, and is versatile for welding in all positions, making it ideal for the complex geometries and varying thicknesses encountered in pipe welding.
How to Improve Flux-Cored Arc Welding (FCAW) Skills
Improving Flux-Cored Arc Welding (FCAW) for a pipe welder involves several key practices aimed at enhancing skill, efficiency, and weld quality:
Proper Equipment Setup: Ensure the welding machine settings (voltage, amperage, and wire feed speed) are optimized for the specific pipe material and thickness. Miller Welds provides guidelines on setting up your welding equipment.
Cleanliness: Keep the pipe surface free of contaminants (rust, oil, moisture) for better weld quality. Pre-cleaning methods and importance are detailed on Lincoln Electric.
Correct Electrode Selection: Use the appropriate flux-cored wire type for the material being welded, considering factors like the base material, position of the weld, and the presence of any coatings. Guidance on electrode selection is available at The Fabricator.
Welding Technique: Practice the right welding techniques, including maintaining a consistent work angle and travel speed, which are crucial for achieving good weld penetration and avoiding defects. Welding Tips and Tricks covers various techniques suited for pipe welding.
Regular Practice: Regularly practice welding on scrap pieces to refine your skills, especially in challenging positions common in pipe welding (6G position, for example).
Post-Weld Inspection and Cleanup: Always inspect your welds for defects (e.g., porosity, slag inclusions) and clean the weld area properly to ensure the integrity of the weld. American Welding Society offers resources on weld inspection.
Safety First: Always prioritize safety by using appropriate personal protective equipment (PPE) and following safety guidelines. Occupational Safety and Health Administration (OSHA) provides comprehensive safety standards for welding.
By focusing on these areas, a pipe welder can significantly improve their FCAW skills and outcomes.
How to Display Flux-Cored Arc Welding (FCAW) Skills on Your Resume
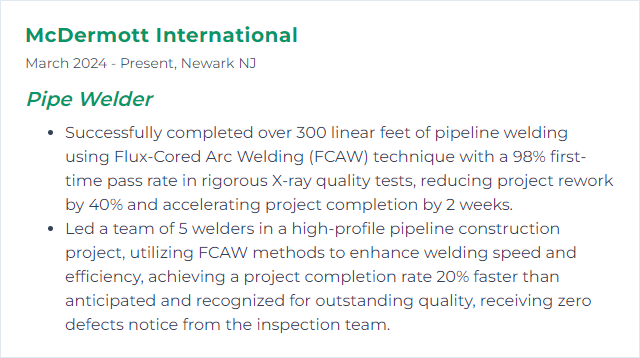
5. Gas Welding
Gas welding, particularly relevant for a pipe welder, is a process that involves using a flame produced by burning a mixture of fuel gas (commonly acetylene) and oxygen to melt and join pieces of metal, typically pipes. This method allows for precise control over the welding flame, making it suitable for welding pipes of various thicknesses and materials.
Why It's Important
Gas welding is crucial for a pipe welder because it offers precise heat control and versatility, allowing for effective welding of pipes in various positions and thicknesses. This technique ensures strong, durable welds essential for the integrity of piping systems.
How to Improve Gas Welding Skills
To improve gas welding, especially for a pipe welder, focus on the following key areas:
Proper Equipment Selection: Use the appropriate welding torch and nozzle size for the type of metal and thickness of the pipe. Hobart Welders provides insights on equipment choices.
Gas Flow Rate: Adjust the gas flow rate to ensure adequate protection from oxidation. This is critical for achieving clean welds. Lincoln Electric offers guidelines on gas flow settings.
Correct Flame Type: Use a neutral flame for most pipe welding applications to prevent oxidation and ensure proper penetration. Miller Welds has resources on flame adjustments.
Preparation and Cleaning: Ensure the pipes are clean and free from contaminants before welding. Proper preparation can significantly improve weld quality. TWI Global offers tips on preparation.
Practice and Skill Development: Continuously practice to improve hand steadiness, flame control, and speed. Online tutorials and courses can help. Welding Tips and Tricks is a valuable resource for practical advice and training.
By focusing on these areas and seeking continuous improvement through education and practice, a pipe welder can significantly enhance their gas welding skills and results.
How to Display Gas Welding Skills on Your Resume
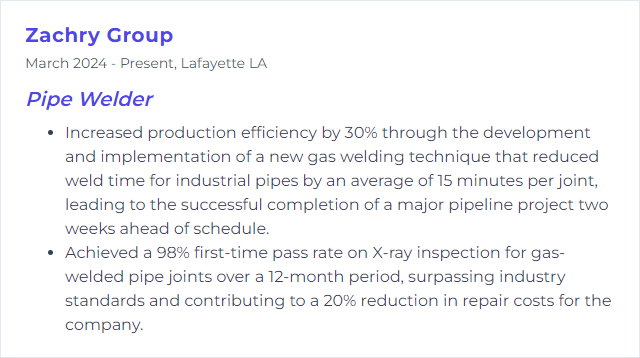
6. Blueprint Reading
Blueprint reading for a pipe welder involves interpreting and understanding technical drawings and specifications related to piping systems. This skill enables the welder to accurately measure, cut, and weld pipes according to the design requirements, ensuring proper installation and functionality.
Why It's Important
Blueprint reading is crucial for a pipe welder as it ensures accurate understanding and execution of welding specifications, measurements, and layouts, thereby guaranteeing the safety, functionality, and quality of the welded structures or systems.
How to Improve Blueprint Reading Skills
Improving blueprint reading as a pipe welder involves enhancing your understanding of symbols, dimensions, and specifications crucial for accurate welding. Here are concise steps:
Familiarize with Basic Symbols: Begin with the basic welding and fitting symbols commonly used in blueprints for pipe welding. Resources like the American Welding Society (AWS) offer guides and standards.
Understand Scales and Dimensions: Practice reading scales and dimensions specific to pipe layouts. This includes understanding diameters, lengths, and angles.
Learn to Interpret Isometric Drawings: Pipe welding often uses isometric drawings. This Isometric Drawing Guide can provide insights into reading and interpreting them effectively.
Study Specifications and Notes: Pay attention to specifications and notes on blueprints. They provide essential details on materials, procedures, and standards.
Hands-On Practice: Apply what you learn on actual blueprints. Websites like Lincoln Electric offer practice blueprints and tutorials.
Continuous Learning: Enroll in courses or workshops focused on blueprint reading for pipe welders. Platforms like Udemy or local vocational schools often offer relevant courses.
By consistently applying these steps and seeking out resources that provide real-world examples, you can significantly improve your blueprint reading skills tailored to pipe welding.
How to Display Blueprint Reading Skills on Your Resume
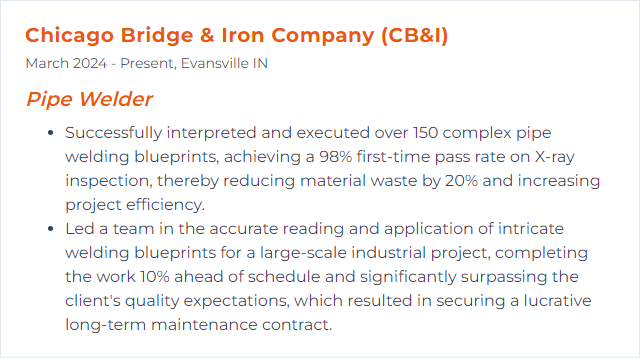
7. Pipe Fabrication
Pipe fabrication is the process of cutting, shaping, and joining pipes to create a piping system, involving activities such as welding, bending, and assembling according to specific blueprints or plans. For a pipe welder, it primarily entails welding segments of pipe to form a system that meets the required specifications for transporting fluids or gases.
Why It's Important
Pipe fabrication is crucial for a pipe welder as it involves cutting, shaping, and joining pipes to exact specifications, ensuring systems are leak-proof, efficient, and safe for transporting fluids or gases in various industrial, commercial, and residential applications.
How to Improve Pipe Fabrication Skills
To improve pipe fabrication, a Pipe Welder can focus on the following areas:
Skill Enhancement: Continuously improve welding skills through courses and certifications. American Welding Society (AWS) offers various resources and certifications relevant to pipe welding.
Technology Adoption: Use advanced welding equipment and technologies. Research the latest in welding automation for efficiency and quality.
Material Knowledge: Understand the properties of different materials being welded. The ASM International website provides valuable material information.
Quality Control: Implement rigorous quality control measures. Familiarize with standards from ASME (American Society of Mechanical Engineers) related to pipe fabrication.
Safety Practices: Always adhere to the best safety practices. OSHA’s Welding, Cutting, and Brazing guidelines are crucial for maintaining a safe work environment.
Efficiency Techniques: Learn and apply efficient pipe fabrication techniques, such as proper pipe preparation and fit-up. Online forums like WeldingWeb can offer practical tips and peer advice.
By focusing on these areas, a pipe welder can significantly improve the quality and efficiency of pipe fabrication.
How to Display Pipe Fabrication Skills on Your Resume
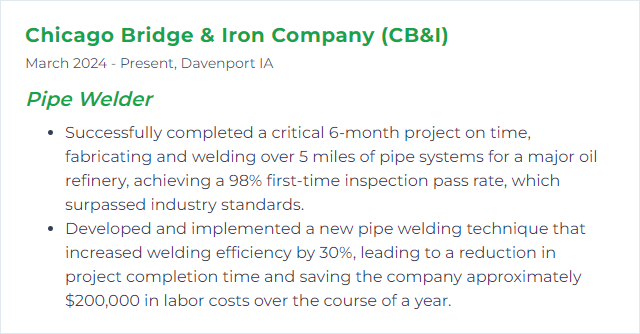
8. Plasma Cutting
Plasma cutting is a process used by pipe welders to cut through electrically conductive materials, including metal pipes, by using a jet of hot plasma. It allows for precise, quick cuts with minimal preparation, ideal for cutting various pipe diameters and materials.
Why It's Important
Plasma cutting is important for a pipe welder because it provides a precise, efficient, and fast method for cutting through various types of metal pipes, enabling accurate fittings and weld preparations, saving time and reducing material waste.
How to Improve Plasma Cutting Skills
To improve plasma cutting, especially for a pipe welder, focus on:
Optimal Equipment Setup: Ensure your plasma cutter settings (amperage, cutting speed, etc.) are optimized for the material and thickness of the pipe. Miller Welds offers detailed guidance on settings and techniques.
Proper Cutting Technique: Maintain a consistent distance between the torch and the workpiece. Use templates or guides for accurate cuts. Lincoln Electric provides insights into effective cutting techniques.
Regular Maintenance: Keep your equipment clean and replace consumables regularly to ensure precision and efficiency. Hypertherm has comprehensive maintenance tips.
Safety Measures: Always wear appropriate safety gear and ensure proper ventilation. OSHA outlines safety practices to prevent accidents.
By focusing on these areas, you can significantly improve the quality and efficiency of your plasma cutting tasks.
How to Display Plasma Cutting Skills on Your Resume
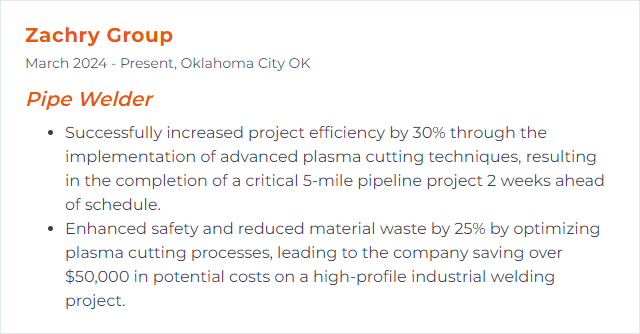
9. Oxy-Fuel Cutting
Oxy-fuel cutting is a process used by pipe welders that involves the use of oxygen and a fuel gas (such as acetylene) to generate a flame hot enough to melt and cut through metal pipes.
Why It's Important
Oxy-fuel cutting is crucial for a pipe welder as it enables precise, efficient cutting and beveling of pipes for fitting and welding, significantly enhancing joint preparation and overall weld quality.
How to Improve Oxy-Fuel Cutting Skills
Improving Oxy-Fuel Cutting for a Pipe Welder involves several key steps:
Select the Right Equipment: Ensure you have the correct size and type of cutting torch and nozzle for the thickness and type of pipe material. Selecting Equipment
Adjust the Flame Correctly: Achieve a neutral flame by adjusting the oxygen and fuel gas to prevent oxidation or insufficient cutting. Flame Adjustment Guide
Maintain a Consistent Speed: Move the torch at a steady pace that allows the cut to go through the pipe without leaving slag. Cutting Speed Tips
Use Proper Techniques for Beveling: When preparing pipe joints for welding, practice making consistent bevels that match the welding specifications. Beveling Techniques
Regular Maintenance: Keep your cutting torch, nozzles, and other equipment clean and in good repair to ensure optimal performance. Equipment Maintenance
By focusing on these areas, pipe welders can improve their oxy-fuel cutting efficiency, quality, and safety.
How to Display Oxy-Fuel Cutting Skills on Your Resume
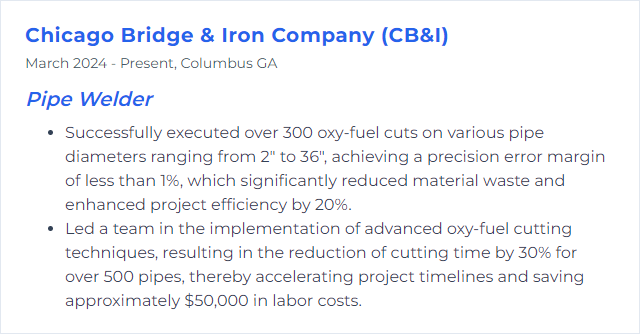
10. SMAW (Shielded Metal Arc Welding)
SMAW, or Shielded Metal Arc Welding, is a manual arc welding process that employs a consumable electrode coated in flux to lay the weld. In the context of a pipe welder, SMAW is commonly used for joining sections of pipe through the creation of strong, durable welds in various positions and environments, utilizing electrodes appropriate for the material and conditions.
Why It's Important
SMAW is important for a Pipe Welder because it offers versatility in welding various pipe materials, strong and durable joints for high-pressure applications, and the capability to work in challenging positions and environments without requiring external shielding gas.
How to Improve SMAW (Shielded Metal Arc Welding) Skills
Improving your skills in SMAW, especially as a pipe welder, involves practice, understanding of techniques, and knowledge updates. Here are concise tips:
Practice Consistently: Regular practice on different pipe positions (1G through 6G) enhances your adaptability and skillset. Focus on maintaining a steady hand and a consistent travel speed.
Understand Electrode Selection: Choose the right electrode for the material and job. Familiarize yourself with electrode classifications and their applications. American Welding Society (AWS) provides detailed guidelines.
Control Heat Input: Master the control of your arc length and welding current to manage the heat input, which is crucial for preventing warping or weakening the weld.
Clean Your Workpiece: Ensure the metal surfaces and welding area are clean before starting. This reduces contamination and improves weld quality.
Study Welding Techniques and Positions: Learn and practice different welding techniques and positions to improve your versatility and skill. Welding Tips and Tricks is a useful resource.
Use the Right Protective Gear: Always use appropriate safety gear to prevent injuries. Proper ventilation is also crucial to avoid exposure to harmful fumes.
Seek Feedback and Continuous Learning: Join forums or communities like Reddit's Welding Community to get feedback on your work and stay updated with new techniques and technologies.
Attend Workshops or Courses: Consider enrolling in advanced welding courses or workshops for hands-on experience and professional guidance. Check offerings at local technical schools or through the AWS.
Focus on Fitness: Physical fitness is important for pipe welders, as the job often requires working in challenging positions. Regular exercise can improve endurance and flexibility.
By incorporating these practices into your routine, you can significantly improve your SMAW skills as a pipe welder.
How to Display SMAW (Shielded Metal Arc Welding) Skills on Your Resume
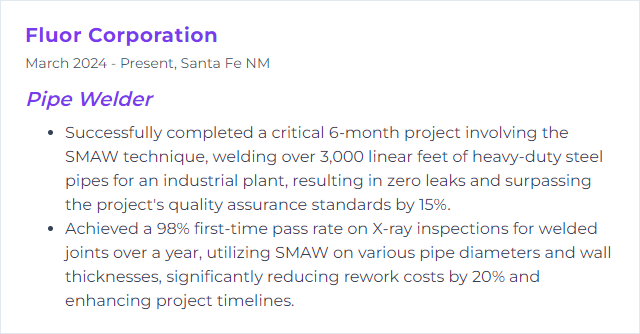
11. GTAW (Gas Tungsten Arc Welding)
GTAW, or Gas Tungsten Arc Welding, is a precision welding process used by pipe welders that utilizes a non-consumable tungsten electrode to produce the weld. It involves the use of a shielding gas, typically argon, to protect the weld area from atmospheric contamination. This method is favored for its ability to produce high-quality, clean welds on a variety of metals, including thin materials and different types of steel and alloy pipes.
Why It's Important
GTAW (Gas Tungsten Arc Welding) is crucial for a Pipe Welder because it offers high-quality, precise welds with superior control over heat input, reducing distortion and allowing for welding of thin materials and complex shapes, essential in critical pipe welds where leak integrity and mechanical properties are paramount.
How to Improve GTAW (Gas Tungsten Arc Welding) Skills
Improving GTAW (Gas Tungsten Arc Welding), especially for a pipe welder, involves focusing on technique, equipment setup, and practice. Here's a concise guide:
Preparation: Ensure the pipe is clean and free of contaminants. Use a stainless steel brush dedicated to the type of metal you're welding.
Equipment Setup: Choose the right tungsten electrode type and size for your application (e.g., 2% lanthanated for steel and stainless, 1.5% lanthanated for aluminum). Set your welding machine to the correct parameters (amperage, AC/DC mode) according to the material and thickness. American Welding Society
Tungsten Electrode Preparation: Sharpen the electrode to a point for steel; a balled tip is preferred for aluminum. The taper length should be 2.5 times the electrode diameter. Miller Welds Guide
Technique: Maintain a consistent angle (15 to 20 degrees) and electrode-to-work distance (about 1/8 inch). Use a tight arc for better control and penetration. For pipe welding, practice walking the cup or use a freehand technique for better support and heat distribution. Welding Tips and Tricks
Shielding Gas: Use pure argon for most materials. For stainless steel or alloy, argon with a 2-5% hydrogen mix can improve weld quality. Adjust gas flow rate to 15-20 cfh to ensure adequate coverage without turbulence. Lincoln Electric Guide
Practice: GTAW on pipes requires skill in handling different positions (1G through 6G). Practice regularly on scrap material to improve handling and control.
Health and Safety: Always use appropriate PPE, including a welding helmet with the correct shade, gloves, and protective clothing. Ensure proper ventilation. OSHA Welding, Cutting, and Brazing
By focusing on these aspects, a pipe welder can significantly improve their GTAW technique, leading to better weld quality and efficiency.
How to Display GTAW (Gas Tungsten Arc Welding) Skills on Your Resume
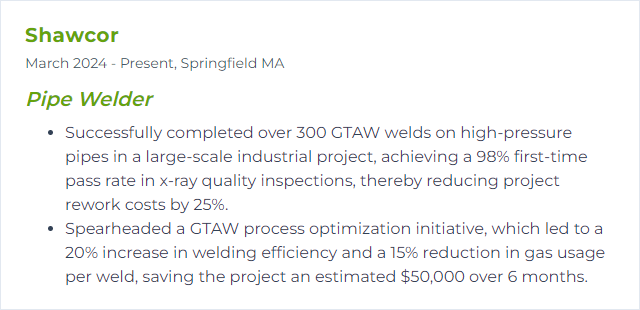
12. Safety Protocols
Safety protocols for a pipe welder are guidelines and measures designed to protect welders from hazards associated with welding activities, such as exposure to harmful fumes, burns, electric shock, and explosions. These protocols include the use of personal protective equipment (PPE), proper ventilation, and adherence to welding procedures to ensure a safe working environment.
Why It's Important
Safety protocols are crucial for a pipe welder to prevent accidents, reduce the risk of injuries from hot surfaces, harmful fumes, and explosive gases, and ensure a safe working environment. Compliance with these protocols safeguards both the welder and the integrity of the welded structures.
How to Improve Safety Protocols Skills
Improving safety protocols for pipe welders involves a multi-faceted approach focusing on training, equipment, and environment. Here’s a concise guide:
Enhanced Training: Ensure all welders undergo comprehensive safety training specific to pipe welding, covering the correct handling of welding equipment, understanding of material safety data sheets (MSDS), and emergency response procedures.
Proper Personal Protective Equipment (PPE): Equip welders with appropriate PPE, including auto-darkening welding helmets, fire-resistant clothing, gloves, and boots, to protect against sparks, spatter, and radiation.
Regular Equipment Maintenance: Implement a routine maintenance schedule for all welding equipment to prevent malfunctions that could pose safety risks.
Ventilation and Fume Extraction: Ensure adequate ventilation and fume extraction systems are in place to minimize welders' exposure to harmful welding fumes and gases.
Safety Signage and Area Markings: Use clear safety signage and area markings around welding areas to warn of potential hazards and ensure compliance with safety protocols.
Emergency Preparedness: Conduct regular emergency drills and have first-aid kits, fire extinguishers, and emergency contacts readily available.
Continuous Safety Audits: Perform regular safety audits to identify and mitigate potential hazards in the welding environment.
By focusing on these key areas, you can significantly improve safety protocols for pipe welders, reducing the risk of accidents and enhancing overall workplace safety.
How to Display Safety Protocols Skills on Your Resume
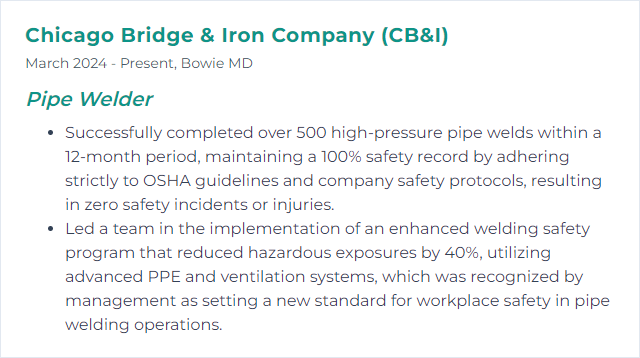