Top 12 Manufacturing Operator Skills to Put on Your Resume
In today's competitive job market, standing out as a manufacturing operator requires more than just basic knowledge and experience. Highlighting a robust set of skills on your resume can distinguish you from other candidates, demonstrating to potential employers your ability to contribute effectively to their operations and adapt to the evolving manufacturing landscape.
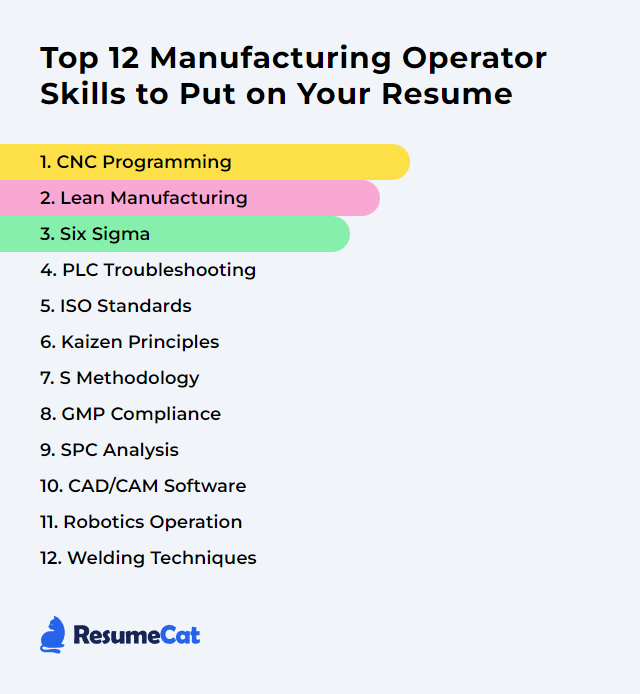
Manufacturing Operator Skills
- CNC Programming
- Lean Manufacturing
- Six Sigma
- PLC Troubleshooting
- ISO Standards
- Kaizen Principles
- S Methodology
- GMP Compliance
- SPC Analysis
- CAD/CAM Software
- Robotics Operation
- Welding Techniques
1. CNC Programming
CNC programming involves creating coded instructions for CNC machines to automate the cutting, shaping, or drilling of materials in manufacturing processes, ensuring precise and efficient production.
Why It's Important
CNC programming is crucial for a Manufacturing Operator as it enables the precise control of machines to produce parts with high accuracy and efficiency, ensuring consistent quality, reducing waste, and increasing productivity in manufacturing processes.
How to Improve CNC Programming Skills
Improving CNC programming involves enhancing efficiency, accuracy, and safety in the manufacturing process. Here are concise strategies tailored for a Manufacturing Operator:
Understand Machine Capabilities: Familiarize yourself with your CNC machine's limits and capabilities to optimize your programming. Haas Automation offers resources on machine capabilities.
Use Simulation Software: Before actual machining, use simulation software to identify and correct errors. This saves time and material costs. Check out Fusion 360 for integrated simulation options.
Implement Standardized Coding Practices: Develop and follow standardized coding practices to maintain consistency and reduce errors. CNCCookbook provides guidelines on G-code programming.
Continuous Learning: Stay updated with the latest CNC technologies and programming techniques. Online platforms like Coursera and Lynda offer courses on CNC and manufacturing technologies.
Optimize Toolpaths: Use software to optimize toolpaths for efficiency and material conservation. Mastercam is a popular choice for toolpath optimization.
Regular Maintenance and Calibration: Ensure your CNC machine is regularly maintained and calibrated for precise operations. Machinery's Handbook is a comprehensive resource for maintenance best practices.
Seek Feedback from Operators: Operators often have firsthand insights into programming inefficiencies. Regularly communicate with them to gather feedback and implement improvements.
By focusing on these areas, a Manufacturing Operator can significantly improve CNC programming efficiency and output quality.
How to Display CNC Programming Skills on Your Resume
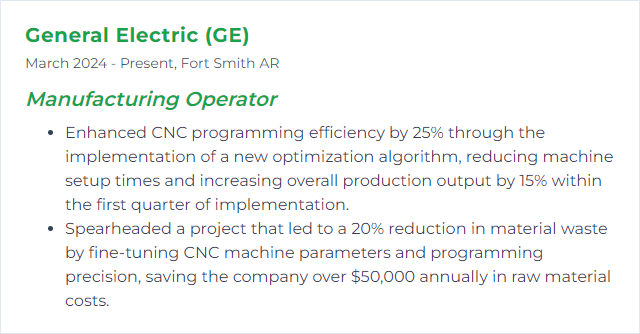
2. Lean Manufacturing
Lean Manufacturing is a methodology aimed at reducing waste and increasing efficiency in production processes, focusing on maximizing product value for the customer. For a Manufacturing Operator, it means performing tasks in the most efficient way, minimizing unnecessary steps, and ensuring quality to prevent rework and waste.
Why It's Important
Lean Manufacturing is important because it helps reduce waste, improve efficiency, and increase productivity, enabling a Manufacturing Operator to produce more high-quality products faster and at a lower cost.
How to Improve Lean Manufacturing Skills
Improving lean manufacturing involves optimizing processes to reduce waste, enhance productivity, and improve quality. For a Manufacturing Operator, here are concise strategies to improve lean manufacturing:
Continuous Improvement: Embrace Kaizen, focusing on continuous, incremental improvements in the manufacturing process.
5S Methodology: Implement the 5S system (Sort, Set in order, Shine, Standardize, Sustain) to organize and maintain a productive work environment.
Value Stream Mapping: Use Value Stream Mapping to visualize and streamline the flow of materials and information.
Just-In-Time (JIT) Production: Adopt JIT practices to reduce inventory costs and increase efficiency by producing only what is needed, when it is needed.
Root Cause Analysis: Apply tools like the 5 Whys to systematically identify and eliminate the root causes of problems.
Standard Work: Develop and adhere to standard work procedures to ensure consistent, efficient operations and quality control.
Employee Empowerment: Foster an environment where every employee is encouraged to suggest improvements. This engagement can lead to innovative solutions and greater ownership of processes.
By focusing on these areas, Manufacturing Operators can play a pivotal role in enhancing lean manufacturing efforts within their organizations.
How to Display Lean Manufacturing Skills on Your Resume
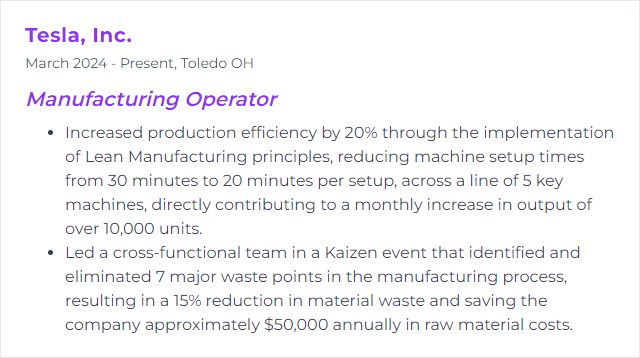
3. Six Sigma
Six Sigma is a data-driven methodology aimed at reducing defects and improving quality in manufacturing processes by identifying and eliminating causes of variation.
Why It's Important
Six Sigma is important for a Manufacturing Operator because it helps reduce defects and improve product quality, leading to increased efficiency, customer satisfaction, and cost savings in production processes.
How to Improve Six Sigma Skills
To improve Six Sigma as a Manufacturing Operator, focus on the following steps:
Understand the Basics: Start by thoroughly understanding Six Sigma principles and methodologies. ASQ's Six Sigma resources offer a comprehensive starting point.
Implement DMAIC: Apply the DMAIC (Define, Measure, Analyze, Improve, Control) framework to identify and solve process inefficiencies. iSixSigma provides a detailed guide.
Utilize Tools and Techniques: Adopt Six Sigma tools such as Statistical Process Control (SPC), 5S, and root cause analysis to improve process stability and efficiency. Explore MoreSteam's toolbox for an extensive array of tools.
Engage in Continuous Learning: Continuously update your knowledge through certifications and training. The Council for Six Sigma Certification offers resources and information.
Embrace Technology: Leverage technology and software designed for Six Sigma projects to enhance data analysis and process management. Minitab is widely used for statistical analysis.
Collaborate and Communicate: Foster a culture of continuous improvement through collaboration and open communication with your team.
By focusing on these steps and utilizing the provided resources, you can significantly improve Six Sigma practices in your role as a Manufacturing Operator.
How to Display Six Sigma Skills on Your Resume
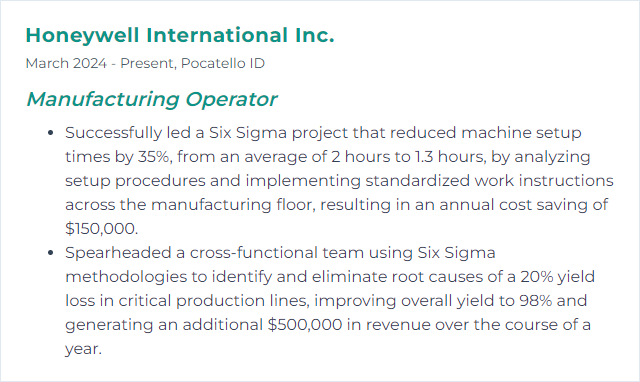
4. PLC Troubleshooting
PLC troubleshooting involves diagnosing and fixing issues within a Programmable Logic Controller (PLC) system, ensuring the automated processes in manufacturing operate correctly and efficiently.
Why It's Important
PLC troubleshooting is crucial for a Manufacturing Operator as it ensures the smooth operation of machinery and production lines, minimizes downtime, and prevents costly disruptions in manufacturing processes.
How to Improve PLC Troubleshooting Skills
Improving PLC (Programmable Logic Controller) troubleshooting, especially for a Manufacturing Operator, involves a combination of understanding the basics of PLC operations, developing systematic troubleshooting skills, and using the right tools and resources. Here's a concise guide:
Learn the Basics: Understand the fundamentals of how PLCs work. PLC Academy offers a good starting point for beginners.
Familiarize with Your PLC: Know the specific PLC model used in your manufacturing process. Manuals and documentation can be invaluable for this.
Use Diagnostic Tools: Leverage built-in diagnostic functions and external software tools for PLC troubleshooting. Rockwell Automation provides a variety of such tools for their PLCs.
Understand Ladder Logic: Grasp the basics of ladder logic, as it's commonly used in PLC programming. Ladder Logic Basics offers a primer on this topic.
Practice Systematic Troubleshooting: Follow a structured approach to identify and solve issues. Begin with verifying power supply, input/output status, and then move onto software and programming errors.
Continuous Learning: Stay updated with the latest in PLC technology and troubleshooting techniques. Websites like Control Automation provide news, tutorials, and forums for continuous learning.
Remember, hands-on practice combined with continuous learning is key to mastering PLC troubleshooting.
How to Display PLC Troubleshooting Skills on Your Resume
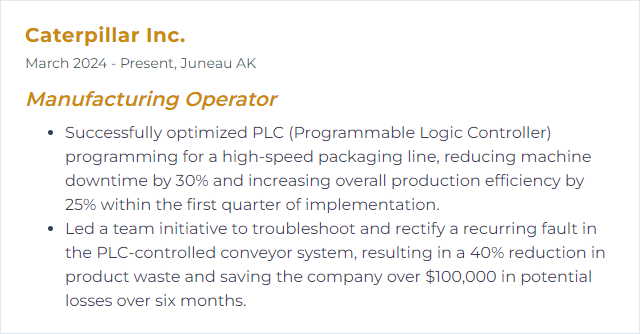
5. ISO Standards
ISO standards are internationally recognized guidelines and specifications developed to ensure the quality, safety, and efficiency of products, services, and systems. For a Manufacturing Operator, they dictate best practices for production processes, quality control, and safety measures to enhance productivity and product consistency.
Why It's Important
ISO Standards ensure quality, safety, and efficiency in manufacturing processes, enabling operators to produce consistent, reliable products while meeting regulatory and customer requirements. They facilitate global trade by providing universally recognized specifications.
How to Improve ISO Standards Skills
Improving ISO standards within a manufacturing context involves a continuous process of evaluation, training, and system enhancement. Here's a concise guide for a Manufacturing Operator:
Undergo Training: Participate in ISO training courses to understand the standards relevant to your operations thoroughly.
Implement Changes: Apply the learned principles to improve processes and quality management systems.
Continuous Improvement: Adopt a Kaizen approach for ongoing improvement, focusing on efficiency and eliminating waste.
Engage in Audits: Regularly participate in internal and external audits to identify areas for improvement.
Feedback Loop: Create mechanisms for feedback from stakeholders to suggest further improvements in compliance with ISO standards.
Stay Updated: Regularly visit the ISO website for updates on standards and best practices.
By focusing on these areas, a Manufacturing Operator can significantly contribute to enhancing the organization's adherence to ISO standards, leading to better quality, efficiency, and market credibility.
How to Display ISO Standards Skills on Your Resume
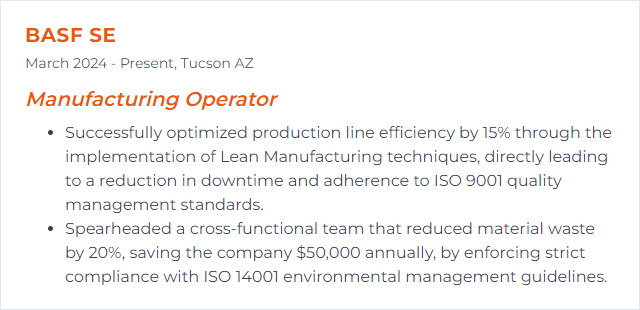
6. Kaizen Principles
Kaizen, in the context of a Manufacturing Operator, refers to continuous, incremental improvement of processes and efficiency in the workplace. It emphasizes eliminating waste, enhancing productivity, and engaging all employees in suggesting and implementing improvements to their work processes and environment.
Why It's Important
Kaizen principles are important for a Manufacturing Operator as they promote continuous improvement, reduce waste, and enhance efficiency and productivity on the production floor. This leads to higher quality products, cost savings, and improved competitiveness.
How to Improve Kaizen Principles Skills
Improving Kaizen principles, especially for a Manufacturing Operator, involves continuous, incremental improvements in efficiency, quality, and safety. Here are concise strategies:
Standardize Operations: Establish clear, standardized procedures for tasks to ensure consistency and efficiency. Learn more.
Use Visual Management: Implement visual aids like signage, labels, and color coding to streamline workflows and reduce errors. Explore techniques.
Empower Employees: Encourage operators to suggest improvements and take ownership of their processes. Read about empowerment.
Implement 5S: Follow the 5S methodology (Sort, Set in order, Shine, Standardize, Sustain) to organize and maintain a productive work environment. Discover 5S.
Solve Problems Systematically: Apply root cause analysis to solve problems permanently instead of applying quick fixes. Understand problem-solving.
Reduce Waste: Identify and eliminate waste in all forms (defects, overproduction, waiting, etc.) using Lean principles. Identify waste.
Continuous Learning: Promote continuous learning and improvement through regular training and education. Benefits of continuous learning.
By focusing on these areas, a Manufacturing Operator can enhance their application of Kaizen principles, leading to significant improvements in all aspects of manufacturing operations.
How to Display Kaizen Principles Skills on Your Resume

7. S Methodology
S Methodology in the context of a Manufacturing Operator refers to a systematic approach aimed at optimizing production processes, ensuring safety, and maintaining quality. It encompasses strategies like standardizing operations, streamlining workflows, and implementing continuous improvement practices to enhance efficiency and productivity on the manufacturing floor.
Why It's Important
The S Methodology is important for a Manufacturing Operator because it provides a structured approach to streamline operations, enhance productivity, and ensure consistent quality. It helps in identifying inefficiencies, reducing waste, and optimizing processes, leading to improved performance and competitiveness.
How to Improve S Methodology Skills
Improving the S Methodology, especially for a Manufacturing Operator, involves enhancing standardization, systematization, and safety practices. Here are concise steps to achieve this:
Standardization: Adopt Lean Manufacturing principles to standardize processes and reduce waste. Focus on creating a uniform way to perform tasks and use equipment. Lean Manufacturing Basics.
Systematization: Implement a 5S System (Sort, Set in order, Shine, Standardize, and Sustain) to organize the workplace efficiently, leading to improved productivity. 5S System Explained.
Safety: Enhance safety protocols by incorporating OSHA guidelines and conducting regular safety training and audits. Focus on creating a culture of safety. OSHA Safety and Health Topics.
Improving these areas will lead to a more efficient, safer, and productive manufacturing environment.
How to Display S Methodology Skills on Your Resume
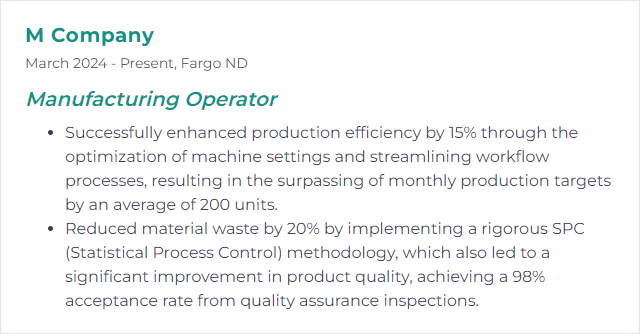
8. GMP Compliance
GMP Compliance refers to adherence to Good Manufacturing Practice regulations, ensuring products are consistently produced and controlled according to quality standards. For a Manufacturing Operator, it means following precise operational procedures, maintaining a clean and safe environment, and documenting processes to ensure product safety and efficacy.
Why It's Important
GMP compliance ensures that products are consistently produced and controlled according to quality standards. It minimizes risks inherent in pharmaceutical production that cannot be eliminated through testing the final product. For a Manufacturing Operator, it is crucial for ensuring the safety, efficacy, and quality of products, thereby protecting public health and maintaining regulatory compliance.
How to Improve GMP Compliance Skills
To improve GMP (Good Manufacturing Practice) compliance as a Manufacturing Operator, follow these concise steps:
Understand GMP Regulations: Start by familiarizing yourself with the specific GMP requirements relevant to your industry. The FDA's GMP Guidelines offer a comprehensive overview for pharmaceuticals.
Regular Training: Ensure continuous training for all operators on GMP standards and updates. The ISPE provides various training programs.
Maintain Cleanliness: Keep the manufacturing area clean and well-organized to prevent contamination. The CDC Guidelines can be a useful resource.
Document Everything: Accurately record all processes, changes, and deviations. This ensures traceability and accountability.
Perform Regular Audits: Conduct internal audits to identify non-compliance issues and implement corrective actions promptly.
Quality Control Checks: Implement thorough quality control procedures at every stage of production.
Feedback Loop: Establish a feedback loop for continuous improvement based on audit findings, employee suggestions, and incident reports.
Invest in Equipment: Ensure all equipment is suitable for its intended use and properly maintained. Regular calibration is crucial.
By following these steps and continuously seeking to improve, you can enhance GMP compliance in your manufacturing operations.
How to Display GMP Compliance Skills on Your Resume
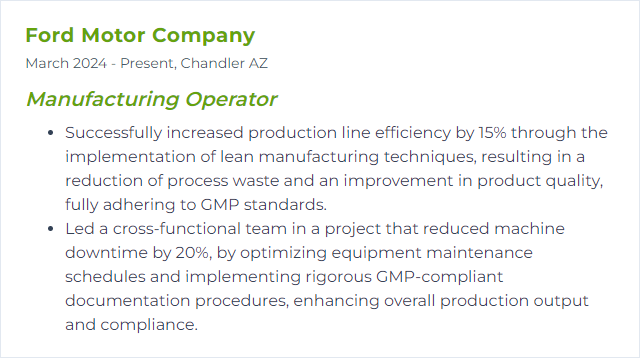
9. SPC Analysis
SPC Analysis, or Statistical Process Control Analysis, is a method used in manufacturing to monitor and control a process using statistical techniques. It helps manufacturing operators identify and correct problems in the production process to ensure products meet quality standards and reduce variability.
Why It's Important
SPC (Statistical Process Control) analysis is important for a Manufacturing Operator because it helps in monitoring and controlling the manufacturing process to ensure product quality and consistency, reduce waste, and increase efficiency by identifying and correcting variations before they result in defects.
How to Improve SPC Analysis Skills
To improve Statistical Process Control (SPC) Analysis in a manufacturing setting, follow these concise steps:
- Educate and Train: Ensure that operators are properly trained in SPC concepts and tools. ASQ’s training resources are a good starting point.
- Select Right Tools: Use appropriate SPC software and tools that fit your manufacturing process. Consider Minitab for statistical analysis.
- Data Accuracy: Emphasize the importance of accurate data collection. Misleading data can lead to incorrect conclusions.
- Continuous Monitoring: Implement real-time monitoring systems to detect deviations early. InfinityQS offers solutions for this purpose.
- Engage Operators: Involve operators in the SPC process. Their insights can be invaluable for identifying process improvements.
- Root Cause Analysis: When variations are detected, use root cause analysis tools to identify and rectify issues. Ishikawa diagrams can be helpful.
- Feedback Loop: Establish a feedback loop for continuous improvement. This ensures that the SPC system evolves with the process.
- Standardize Processes: Develop standard operating procedures (SOPs) based on SPC findings to maintain quality.
By focusing on education, appropriate tool selection, data accuracy, and continuous process improvement, manufacturing operators can significantly enhance SPC analysis, leading to better quality control and efficiency in manufacturing processes.
How to Display SPC Analysis Skills on Your Resume
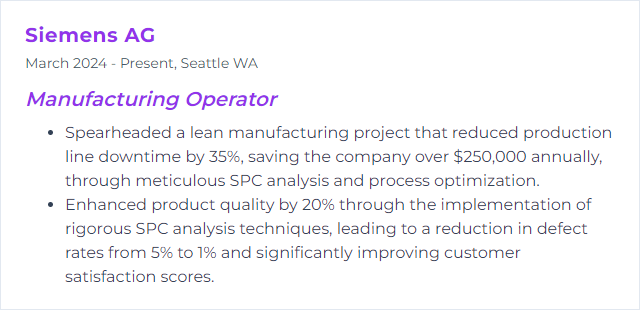
10. CAD/CAM Software
CAD/CAM software is a computer-aided design and manufacturing tool that enables manufacturing operators to design products and control machining processes efficiently, streamlining the production from design to finished product.
Why It's Important
CAD/CAM software is crucial for a Manufacturing Operator as it streamlines the design to production process, enhances precision, reduces material waste, and increases efficiency by automating many manufacturing tasks.
How to Improve CAD/CAM Software Skills
Improving CAD/CAM software for a Manufacturing Operator involves focusing on usability, integration, and functionality to streamline the design-to-production process. Here are concise strategies:
Enhance User Interface (UI): Simplify the user interface for better accessibility and efficiency, focusing on intuitive design and customizable toolbars for frequently used functions. Autodesk offers examples of user-centric design approaches.
Improve Integration Capabilities: Ensure seamless integration with other manufacturing software (ERP, MRP systems) for smoother workflow and data consistency. SOLIDWORKS provides integrated solutions that can be a benchmark.
Expand Compatibility: Support a wide range of file formats and standards to ensure compatibility with clients and suppliers. Mastercam focuses on versatile file import and export options.
Offer Comprehensive Training Resources: Provide easily accessible, up-to-date training materials and tutorials to help operators maximize software utility. Siemens NX includes extensive learning resources.
Enhance Simulation Tools: Develop more advanced simulation tools for real-time feedback on manufacturability, identifying potential issues before production. Fusion 360 showcases the importance of simulation in design and manufacturing.
Foster Community and Support: Build a strong user community for sharing tips, tricks, and custom scripts, complemented by responsive technical support. The Onshape Forums exemplify effective community engagement.
Regular Updates and Feedback Loops: Implement regular software updates based on user feedback and emerging industry trends to ensure the software evolves with the needs of manufacturing operators.
By focusing on these areas, CAD/CAM software can become more effective and user-friendly for Manufacturing Operators, enhancing productivity and innovation in the manufacturing process.
How to Display CAD/CAM Software Skills on Your Resume
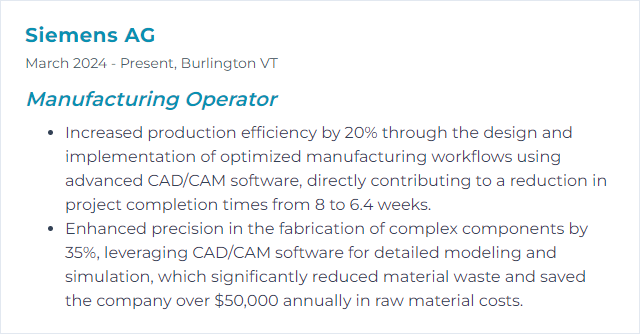
11. Robotics Operation
Robotics operation in manufacturing involves overseeing and managing robots and automated systems that perform tasks in the production process, ensuring they function efficiently, safely, and effectively to meet production goals.
Why It's Important
Robotics operation is crucial for a Manufacturing Operator as it enhances efficiency, ensures precision and consistency in production, reduces operational costs, and improves workplace safety by handling dangerous or repetitive tasks.
How to Improve Robotics Operation Skills
Improving robotics operations in a manufacturing setting involves several key steps aimed at enhancing efficiency, reliability, and overall productivity. Here’s a concise guide:
Regular Maintenance: Ensure regular maintenance schedules are strictly followed to prevent unexpected downtimes. Robotics Industries Association provides guidelines on maintenance practices.
Training: Invest in continuous training for operators to keep them updated on the latest robotics technologies and safety protocols. The Advanced Robotics for Manufacturing Institute offers resources and training programs.
Software Updates: Regularly update the software running your robots to leverage improvements in efficiency and new features. Manufacturers often provide these updates on their official websites.
Process Optimization: Continuously analyze and optimize processes for better integration of robotics into your manufacturing operations. The Manufacturing Extension Partnership can assist in optimizing manufacturing processes.
Data Analysis: Utilize data analytics to monitor robot performance and predict maintenance needs, optimizing operational efficiency. IEEE Xplore offers research materials on the latest in robotics data analysis.
Safety Enhancements: Regularly review and enhance safety measures to protect personnel working alongside robots. OSHA provides safety guidelines for robotics in the workplace.
By focusing on these areas, manufacturing operators can significantly improve the performance and reliability of their robotics operations.
How to Display Robotics Operation Skills on Your Resume
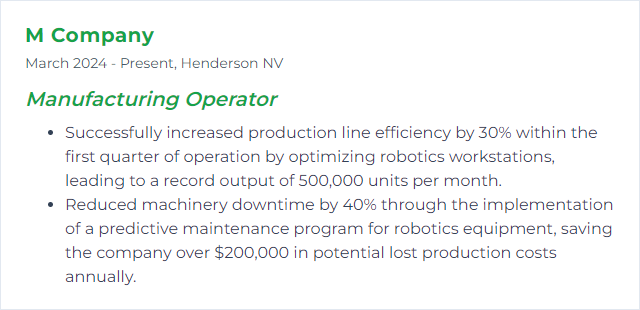
12. Welding Techniques
Welding techniques are methods used to join metal parts together by melting and fusing them at the joining points. Common techniques include MIG (Metal Inert Gas), TIG (Tungsten Inert Gas), and stick welding. Each method varies in equipment, heat source, and material compatibility, crucial for manufacturing operators to understand for efficient and quality production.
Why It's Important
Welding techniques are crucial for a Manufacturing Operator as they ensure strong, durable joins between materials, directly affecting product quality, safety, and manufacturing efficiency. Proper techniques minimize defects, reduce waste, and enhance productivity.
How to Improve Welding Techniques Skills
Improving welding techniques as a Manufacturing Operator involves mastering fundamental skills, staying updated with new technologies, and practicing consistently. Here's a concise guide:
Understand Basics: Ensure a strong grasp of welding fundamentals including different welding processes (MIG, TIG, Stick), materials, and equipment settings.
Safety First: Prioritize safety by wearing appropriate gear and following guidelines. OSHA’s Welding, Cutting, and Brazing page provides essential safety tips.
Practice Consistently: Hands-on practice is crucial. Set aside regular time for welding practice to refine your skills and technique.
Seek Feedback and Training: Participate in workshops or classes offered by welding associations such as the American Welding Society (AWS) to gain feedback and learn advanced techniques.
Stay Updated: Keep abreast of the latest welding technologies and materials by reading industry publications and visiting websites like Fabricating & Metalworking.
Use Quality Equipment: Invest in or ensure access to high-quality welding tools and materials. Proper equipment can significantly influence welding quality. Visit Lincoln Electric or Miller Welds for options.
Analyze and Adjust: Regularly review your welds for defects and areas of improvement. Adjust your techniques, materials, or equipment settings as necessary.
By focusing on these key areas and leveraging resources from trusted welding industry leaders, Manufacturing Operators can significantly improve their welding techniques.
How to Display Welding Techniques Skills on Your Resume
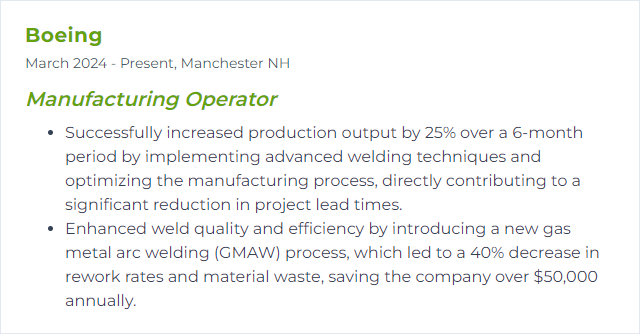