Top 12 Line Operator Skills to Put on Your Resume
In the highly competitive manufacturing and production industries, a line operator's resume that showcases a robust set of skills can significantly enhance their job prospects. Highlighting the top 12 line operator skills on your resume not only demonstrates your capability to potential employers but also positions you as a valuable asset to their operations, making you stand out in a crowded field of candidates.
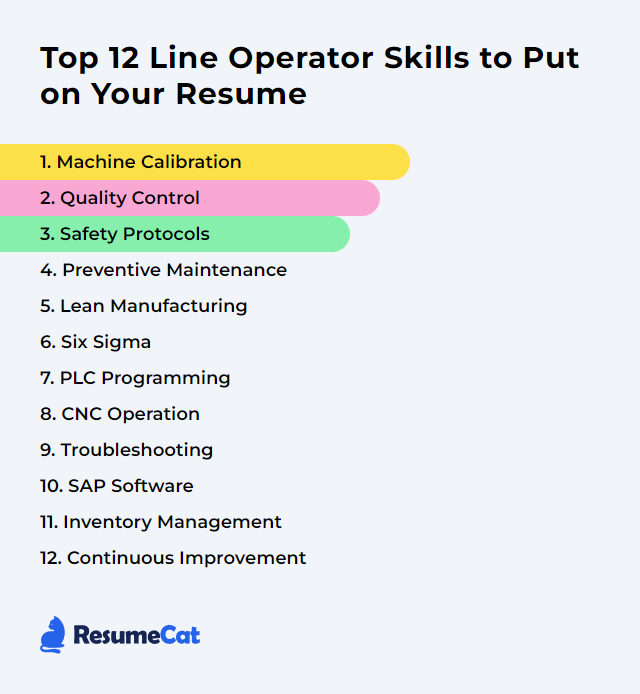
Line Operator Skills
- Machine Calibration
- Quality Control
- Safety Protocols
- Preventive Maintenance
- Lean Manufacturing
- Six Sigma
- PLC Programming
- CNC Operation
- Troubleshooting
- SAP Software
- Inventory Management
- Continuous Improvement
1. Machine Calibration
Machine calibration for a Line Operator involves adjusting and setting machinery to ensure it operates within specified parameters and produces products that meet quality and accuracy standards.
Why It's Important
Machine calibration is crucial for ensuring accurate and consistent production outcomes, minimizing errors, and maintaining product quality standards.
How to Improve Machine Calibration Skills
Improving machine calibration involves ensuring your equipment operates accurately and consistently. Here are concise steps tailored for a Line Operator:
Understand Your Machine: Read the manual to grasp calibration procedures and requirements. Machine Manuals
Regular Checks: Schedule and perform regular calibration checks, even if the machine appears to be running smoothly. Preventive Maintenance
Use Correct Tools: Employ appropriate and well-calibrated tools for the calibration process. Calibration Tools Guide
Record Data: Keep detailed records of all calibration activities, noting any deviations or adjustments made. Importance of Record Keeping
Training: Stay updated with training to understand the latest calibration techniques and technologies. Online Calibration Training
Environmental Control: Ensure the calibration environment is stable, considering factors like temperature and humidity. Environmental Conditions
Seek Expertise: When in doubt, consult with the machine manufacturer or a professional calibration service. Professional Calibration Services
By following these steps, you can maintain the precision and reliability of your machinery, ensuring optimal operational performance.
How to Display Machine Calibration Skills on Your Resume
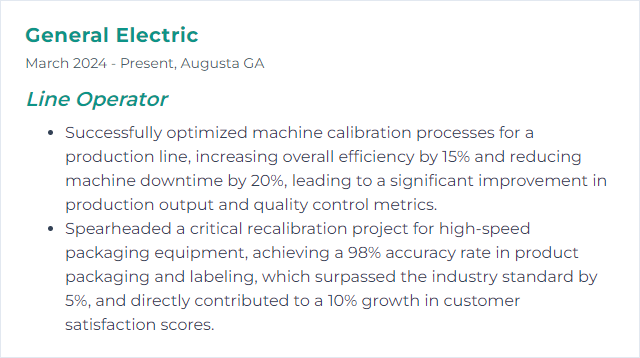
2. Quality Control
Quality control, in the context of a Line Operator, involves monitoring and adjusting the production process to ensure the final product meets predefined standards and specifications.
Why It's Important
Quality control is crucial for a Line Operator as it ensures the consistency and safety of products, minimizes waste and operational costs, and sustains customer satisfaction and trust.
How to Improve Quality Control Skills
Improving quality control as a Line Operator involves a focused approach on precision, consistency, and continuous improvement. Here’s a concise guide:
Understand Specifications: Clearly understand the product specifications and quality requirements. ASQ's quality resources offer comprehensive guides and standards.
Regular Training: Keep skills updated with regular training. OSHA’s training resources can provide guidelines on maintaining workplace safety and quality.
Use of Technology: Utilize technology for accuracy and efficiency. Tools like SPC software help in monitoring processes in real-time.
Routine Maintenance: Ensure equipment is regularly maintained to prevent defects. Guidelines on maintenance can be found through SME’s maintenance resources.
Continuous Improvement: Adopt a Kaizen or continuous improvement mindset. Lean Manufacturing Tools offers insights into lean practices.
Quality Checks: Perform regular quality checks and document results. Quality Control Check Sheets by ASQ can be a starting point.
Feedback Loop: Create a feedback loop for immediate rectification of issues. MindTools’ Feedback Loop explains the importance and implementation of feedback loops.
Each of these steps, when implemented diligently, can significantly improve the quality control process for a Line Operator.
How to Display Quality Control Skills on Your Resume
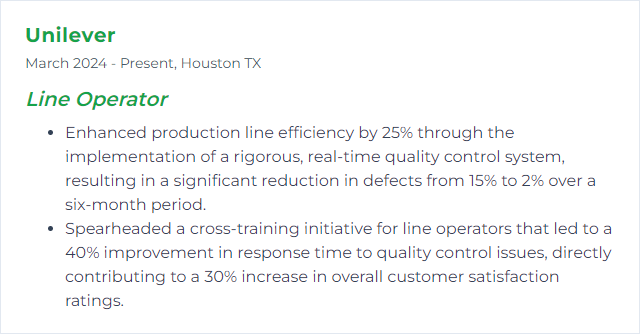
3. Safety Protocols
Safety protocols for a Line Operator are a set of guidelines and procedures designed to prevent accidents and injuries, ensuring a safe working environment around machinery and production lines. These include equipment handling, personal protective equipment (PPE) use, emergency response, and adherence to safety regulations.
Why It's Important
Safety protocols are crucial for a Line Operator as they minimize workplace hazards, prevent accidents and injuries, ensure compliance with regulations, and maintain a safe and efficient production environment.
How to Improve Safety Protocols Skills
Improving safety protocols for a Line Operator involves a multi-step approach focused on assessment, training, engagement, and continuous improvement. Here's a concise guide:
Assess Risks: Conduct a thorough risk assessment to identify potential hazards specific to line operations. Tools like OSHA's guidelines can help (OSHA Risk Assessment).
Standardize Procedures: Develop and implement standardized operating procedures (SOPs) for all tasks, ensuring they include safety measures. Reference ANSI standards for guidance (ANSI Standards).
Training: Provide comprehensive safety training, including emergency response and proper equipment use. Utilize resources from the National Safety Council (National Safety Council Training).
Engage Employees: Foster a safety culture by actively involving line operators in safety meetings, discussions, and decision-making processes. Encourage reporting of hazards without fear of reprisal.
Personal Protective Equipment (PPE): Ensure all line operators have access to and understand the importance of using appropriate PPE. Guidelines on PPE can be found on OSHA's website (OSHA PPE).
Regular Reviews: Conduct regular safety protocol reviews and updates in response to new risks, technologies, or after incidents to learn and improve. ISO standards can offer a framework for continuous improvement (ISO 45001).
Emergency Preparedness: Develop and regularly drill emergency response plans tailored to potential incidents, such as chemical spills or equipment malfunctions.
By systematically addressing these areas, line operators can significantly enhance their safety protocols, leading to a safer and more efficient workplace.
How to Display Safety Protocols Skills on Your Resume
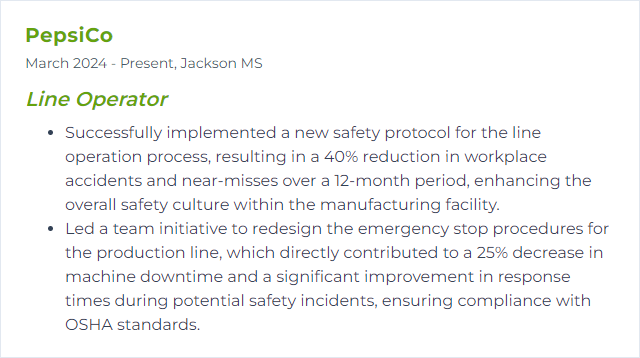
4. Preventive Maintenance
Preventive maintenance for a Line Operator involves regular, scheduled maintenance tasks on machinery and equipment to prevent unexpected breakdowns and ensure smooth operation, optimizing productivity and minimizing downtime.
Why It's Important
Preventive maintenance is crucial for a Line Operator as it ensures the smooth operation of machinery, minimizes unexpected downtime due to breakdowns, and extends the lifespan of equipment, ultimately saving time and reducing costs.
How to Improve Preventive Maintenance Skills
Improving preventive maintenance for a Line Operator involves several key steps aimed at enhancing machine uptime, reducing unexpected breakdowns, and ensuring safety. Here’s a concise guide:
Schedule Regular Inspections: Establish a routine inspection schedule based on the manufacturer's recommendations and past maintenance data. Fiix Software offers insights on setting up a preventive maintenance plan.
Use a Computerized Maintenance Management System (CMMS): Implement a CMMS to automate maintenance scheduling, manage work orders, and track equipment history efficiently.
Train Operators: Ensure line operators are well-trained on the basics of machine maintenance and troubleshooting. Continuous training is crucial, as outlined by Reliable Plant.
Implement Predictive Maintenance Techniques: Incorporate predictive maintenance tools, such as vibration analysis and thermography, to identify issues before they lead to failure. Fluke provides a good starting point for understanding vibration monitoring.
Optimize Spare Parts Inventory: Maintain an optimized inventory of critical spare parts to reduce downtime. Plant Services discusses strategies for effective spare parts management.
Review and Improve: Regularly review maintenance records to identify trends and areas for improvement. Adjust the preventive maintenance plan based on these findings.
By following these steps, Line Operators can significantly improve the effectiveness of their preventive maintenance routines, ensuring that equipment runs more reliably and efficiently.
How to Display Preventive Maintenance Skills on Your Resume
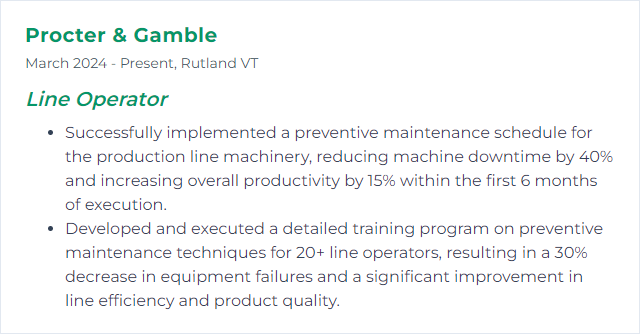
5. Lean Manufacturing
Lean Manufacturing is a systematic approach to reduce waste and improve efficiency in production processes, focusing on maximizing value for the customer by optimizing workflow and eliminating non-value-added activities. For a Line Operator, it means consistently working smarter, not harder, by following streamlined processes and actively participating in identifying and solving problems to keep the production line running smoothly and efficiently.
Why It's Important
Lean Manufacturing is important because it helps in reducing waste, improving quality, and increasing efficiency on the production line, directly contributing to smoother operations and a safer, more productive work environment for a Line Operator.
How to Improve Lean Manufacturing Skills
To improve Lean Manufacturing, a Line Operator can focus on the following key areas:
Waste Reduction: Identify and eliminate waste in all forms (overproduction, waiting, transportation, over-processing, inventory, motion, and defects) by observing processes and using tools like 5S to organize and manage the workspace efficiently.
Continuous Improvement (Kaizen): Embrace the concept of continuous improvement by regularly participating in Kaizen events or initiatives, aiming for small, incremental changes in processes to enhance efficiency and quality.
Standardized Work: Develop and follow standardized work procedures to ensure consistency in production, reduce variability, and increase efficiency.
Visual Management: Use visual management tools like Kanban boards or Andon systems to communicate information clearly and promptly, enabling quick decision-making and response to issues.
Teamwork and Communication: Actively engage in team meetings and communication to share ideas, problems, and solutions. Collaborate with colleagues to optimize processes and resolve issues quickly, enhancing overall productivity.
For a Line Operator, focusing on these areas can significantly contribute to the efficiency and effectiveness of Lean Manufacturing practices in their day-to-day operations.
How to Display Lean Manufacturing Skills on Your Resume
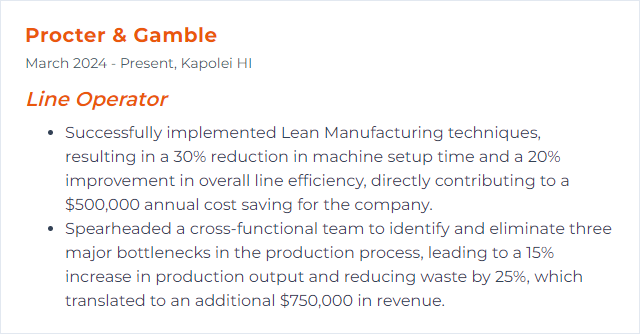
6. Six Sigma
Six Sigma is a set of techniques and tools aimed at improving processes by reducing errors and increasing quality, leading to better productivity and efficiency for line operators.
Why It's Important
Six Sigma is important for a Line Operator because it focuses on reducing errors, improving quality, and increasing efficiency in production processes, leading to higher customer satisfaction and cost savings.
How to Improve Six Sigma Skills
To improve Six Sigma as a Line Operator, focus on the following concise strategies:
Understand DMAIC Process: Familiarize yourself with the Define, Measure, Analyze, Improve, and Control (DMAIC) methodology to systematically improve operations. ASQ's DMAIC Overview provides a solid starting point.
Engage in Continuous Learning: Enhance your Six Sigma knowledge through continuous education. Websites like iSixSigma offer resources tailored for all levels.
Implement Quality Tools: Utilize Six Sigma tools like Pareto Charts, Cause and Effect Diagrams, and Control Charts to analyze and improve the production line. The Mind Tools website introduces these tools.
Participate in Problem-Solving Teams: Actively engage in team efforts to solve quality issues, using structured problem-solving techniques. Collaboration can lead to innovative solutions.
Embrace Lean Principles: Combine Six Sigma with lean manufacturing principles to eliminate waste and increase efficiency. The Lean Enterprise Institute provides insights into lean thinking.
Seek Feedback and Act: Regularly solicit feedback from supervisors and peers on performance and use it to guide improvements.
By focusing on these areas, a Line Operator can significantly contribute to enhancing Six Sigma processes within their operations.
How to Display Six Sigma Skills on Your Resume
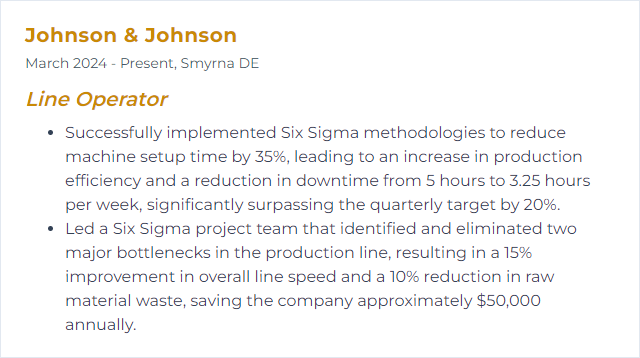
7. PLC Programming
PLC programming involves creating instructions for a Programmable Logic Controller (PLC) to automate machinery and processes on a production line. It helps in controlling equipment, ensuring precise operations, and enhancing efficiency.
Why It's Important
PLC programming is crucial for a Line Operator because it allows for the precise control and automation of machinery on the production line, ensuring efficient, safe, and consistent operations.
How to Improve PLC Programming Skills
Improving PLC programming, especially for a Line Operator, involves enhancing efficiency, understanding, and troubleshooting skills. Here are concise tips with resources:
Understand Basics Thoroughly: Grasp the fundamentals of PLCs, including ladder logic, function block diagrams, and structured text. PLC Academy offers a clear overview.
Practice Problem-Solving: Regularly work on real-world problems. RealPars provides practical examples and scenarios.
Learn from Manuals and Datasheets: Familiarize yourself with the specific PLC models you're working with by studying their manuals and datasheets. Manufacturers like Siemens provide comprehensive guides.
Use Simulation Software: Before implementing, use simulation software to test and validate your programs. PLCSim by Siemens is an example.
Stay Updated with Trends and Tools: Subscribe to PLC-related forums and publications to stay informed about the latest trends and tools. PLC Talk is a useful forum for discussions and advice.
Master Troubleshooting: Develop skills to quickly identify and rectify errors in PLC programs. AutomationDirect offers a basic guide on troubleshooting.
Understand Safety and Best Practices: Always prioritize safety by following industry best practices for programming and system design. Rockwell Automation has extensive safety documentation.
Seek Feedback and Collaborate: Share your programs with peers for feedback and collaborate on complex projects to enhance learning and efficiency.
By focusing on these areas, a Line Operator can significantly improve their PLC programming skills, leading to more efficient and reliable system operations.
How to Display PLC Programming Skills on Your Resume
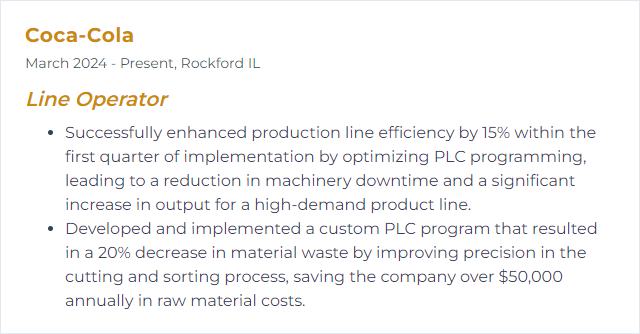
8. CNC Operation
CNC operation involves programming, setting up, and operating computer numerical control (CNC) machines to manufacture precision parts and components, ensuring adherence to specifications and quality standards. For a Line Operator, it typically means overseeing the production process, making adjustments as necessary, and ensuring the smooth functioning of the CNC equipment.
Why It's Important
CNC operation is crucial for a Line Operator because it ensures precision, efficiency, and repeatability in manufacturing processes, allowing for the production of high-quality parts with minimal waste and increased productivity.
How to Improve CNC Operation Skills
Improving CNC operation involves enhancing precision, efficiency, and safety. Here are concise strategies a Line Operator can employ:
Regular Maintenance: Schedule and conduct regular maintenance checks to prevent machine wear and ensure accuracy. MachineMetrics outlines preventative maintenance for CNC machines.
Proper Tooling: Use the correct tooling and replace worn tools to maintain quality and efficiency. Sandvik Coromant provides insights on tool selection and machining calculations.
Optimize Cutting Parameters: Adjust speed, feed, and depth of cut according to material and tooling for optimal performance. CNCCookbook offers guidance on adjusting CNC speeds and feeds.
Use High-Quality Material: Ensure material quality to prevent machining issues and improve final product quality. ThomasNet is a platform to source quality materials and components.
Implement CNC Software Updates: Regularly update CNC software to leverage the latest features and improvements. Mastercam provides CNC software that is regularly updated.
Training and Education: Continuously improve skills and knowledge through training. Tooling U-SME offers courses on CNC operation and programming.
Safety Practices: Follow best safety practices to prevent accidents and machine damage. OSHA provides guidelines for workplace safety, including CNC operation.
By focusing on these areas, a Line Operator can significantly improve CNC operation in terms of productivity, product quality, and safety.
How to Display CNC Operation Skills on Your Resume
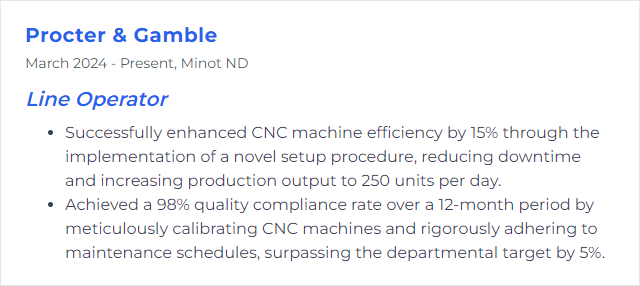
9. Troubleshooting
Troubleshooting, in the context of a Line Operator, refers to the process of identifying, diagnosing, and resolving problems or malfunctions within a production line to ensure its smooth and efficient operation.
Why It's Important
Troubleshooting is crucial for a Line Operator as it enables quick identification and resolution of issues, ensuring the production line runs efficiently and minimally interrupted, thus maintaining productivity and product quality.
How to Improve Troubleshooting Skills
Improving troubleshooting skills, particularly for a Line Operator, involves developing systematic problem-solving techniques, enhancing technical knowledge, and refining observational skills. Here are concise steps:
Learn the System: Understand how the line operates under normal conditions. Machine Manuals and Training Materials can be invaluable resources.
Identify the Problem: Clearly define what is wrong. Use 5 Whys Technique to drill down to the root cause.
Develop a Plan: Prioritize potential solutions based on impact and feasibility. Resources like MindTools offer strategic planning tools.
Implement and Test: Apply the most promising solution, then observe if it corrects the issue. The Plan-Do-Check-Act cycle is a structured approach for this phase.
Document and Learn: Record your process and outcomes for future reference. Platforms like Evernote or OneNote can be used for documentation.
Continuous Learning: Enhance your technical skills and stay updated with new technologies. LinkedIn Learning and Udemy offer courses relevant for Line Operators.
Practice Critical Thinking: Engage with problem-solving games and puzzles regularly. Lumosity and Project Euler can help sharpen your analytical skills.
By methodically approaching problems, leveraging resources for learning, and continuously honing your skills, you can significantly improve your troubleshooting abilities as a Line Operator.
How to Display Troubleshooting Skills on Your Resume
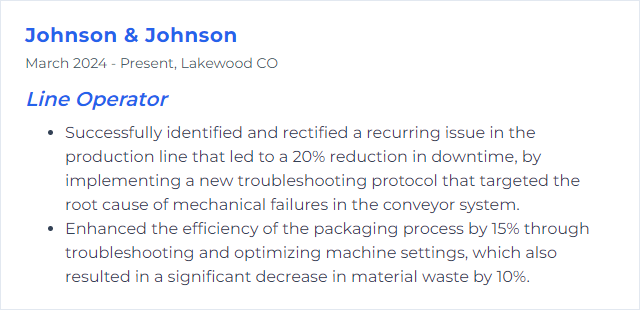
10. SAP Software
SAP software is an enterprise resource planning (ERP) system used to manage business operations and customer relations, streamlining processes such as inventory management, order processing, and financials for efficiency and real-time data access. For a Line Operator, it can help in scheduling production, monitoring equipment maintenance, and ensuring materials are available for production.
Why It's Important
SAP software is crucial for a Line Operator as it streamlines production processes, ensures timely access to critical data, and enhances operational efficiency, directly impacting productivity and decision-making on the factory floor.
How to Improve SAP Software Skills
Improving SAP software for a Line Operator involves focusing on user interface simplicity, real-time data access, and training enhancement. Here are concise strategies:
User Interface Customization: Simplify the SAP interface specifically for Line Operators. Utilize SAP Fiori to create role-based, responsive access across devices, improving efficiency and user experience.
Real-Time Data Integration: Integrate SAP MII (Manufacturing Integration and Intelligence) to provide Line Operators with real-time manufacturing data and KPIs, enabling quicker decision-making and problem resolution.
Enhanced Training Resources: Develop concise, role-specific training materials and leverage SAP Enable Now to provide in-context, on-demand assistance, reducing learning curves and improving software adoption.
Automation of Repetitive Tasks: Implement SAP Intelligent Robotic Process Automation (RPA) to automate routine tasks, allowing Line Operators to focus on more critical operations.
Feedback Loop Implementation: Establish a structured feedback loop with Line Operators using SAP Experience Management solutions, to continually adapt and improve the software based on user experiences and needs.
By focusing on these areas, SAP software can become more intuitive, efficient, and valuable for Line Operators.
How to Display SAP Software Skills on Your Resume
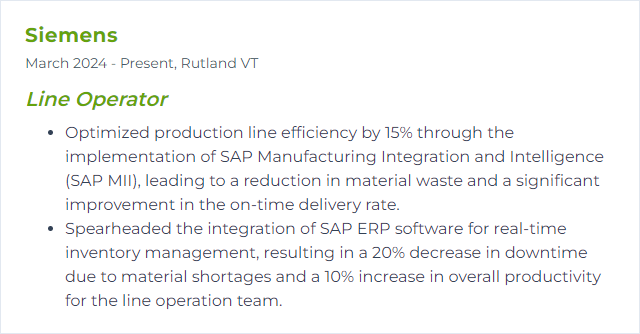
11. Inventory Management
Inventory management, in the context of a Line Operator, involves overseeing and controlling the supply, storage, and accessibility of components and materials required for production line operations, ensuring they are available as needed to maintain continuous and efficient production flow.
Why It's Important
Inventory management is crucial for a Line Operator as it ensures the timely availability of materials and parts required for production, minimizing downtime and maintaining consistent workflow for optimal efficiency and productivity.
How to Improve Inventory Management Skills
Improving inventory management, especially for a Line Operator, involves a few key steps focused on efficiency, accuracy, and minimal downtime. Here's a concise guide:
Implement Real-time Tracking: Use technology to monitor inventory levels in real time. RFID tags and barcoding systems can significantly improve accuracy and speed in tracking materials.
Adopt Lean Inventory Techniques: Implement Just-In-Time (JIT) inventory management to minimize waste and reduce storage costs by receiving goods only as they are needed in the production process.
Use Inventory Management Software: Employ software solutions that can forecast demand, automate ordering, and provide valuable insights into inventory trends, helping prevent overstocking or stockouts.
Regularly Review and Optimize Inventory Levels: Conduct cycle counts and adjust inventory levels based on demand patterns and lead times, ensuring optimal stock levels at all times.
Improve Supply Chain Visibility: Foster strong relationships with suppliers and use supply chain management tools to gain better visibility and control over the entire supply chain, enabling more responsive inventory management.
Train Your Team: Ensure all team members, especially line operators, are trained in best practices for inventory management. This includes proper handling, reporting discrepancies immediately, and understanding the importance of inventory accuracy.
By implementing these strategies, a Line Operator can significantly contribute to more efficient and effective inventory management.
How to Display Inventory Management Skills on Your Resume
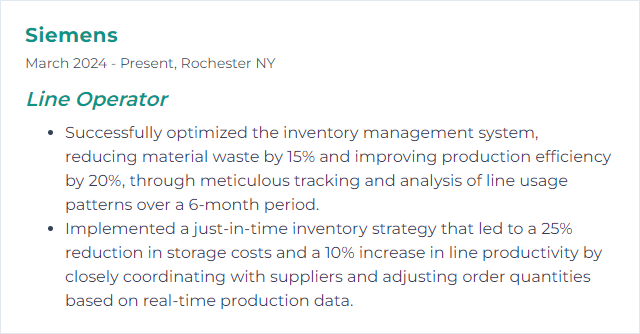
12. Continuous Improvement
Continuous Improvement, regarding a Line Operator, involves ongoing efforts to enhance processes, efficiency, and quality on the production line, aiming for incremental enhancements over time to optimize operations and reduce waste.
Why It's Important
Continuous improvement is crucial for a Line Operator as it enhances efficiency, reduces waste, and increases product quality, leading to higher customer satisfaction and better operational sustainability.
How to Improve Continuous Improvement Skills
Improving Continuous Improvement for a Line Operator involves a focused approach on enhancing skills, embracing feedback, and leveraging technology. Here are concise steps:
Skill Enhancement: Invest time in training and workshops to master new techniques and technologies relevant to your line work. Platforms like Coursera and Udemy offer industry-specific courses.
Feedback Loop: Establish a routine for giving and receiving constructive feedback with your team and supervisors. This practice identifies areas for improvement and innovation.
Leverage Technology: Embrace digital tools and software that streamline operations, such as process automation and real-time data analysis. Websites like Smartsheet provide solutions for process improvement.
Kaizen Methodology: Adopt the Kaizen approach, focusing on continuous, incremental improvements. This mindset can lead to significant enhancements over time. Learn more about Kaizen at ASQ.
5S System: Implement the 5S system (Sort, Set in order, Shine, Standardize, Sustain) to organize and optimize the workplace for efficiency. Detailed guidelines can be found on Lean Manufacturing Tools.
By focusing on these areas, a Line Operator can significantly contribute to and enhance Continuous Improvement practices within their operations.
How to Display Continuous Improvement Skills on Your Resume
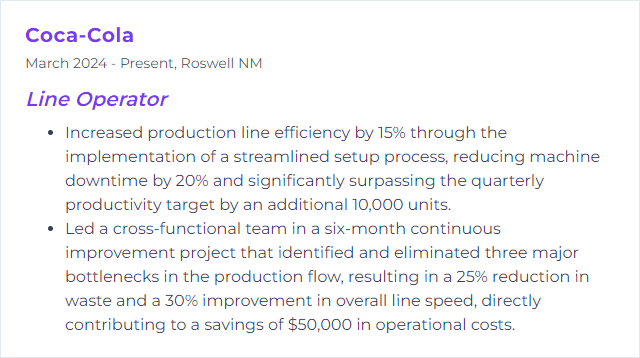