Top 12 Assembly Line Worker Skills to Put on Your Resume
In the fast-paced world of manufacturing, assembly line workers play a crucial role in the production process, and highlighting the right skills on your resume can significantly boost your employment prospects. This article outlines the top 12 skills that demonstrate your proficiency and efficiency as an assembly line worker, helping you stand out to potential employers in a competitive job market.
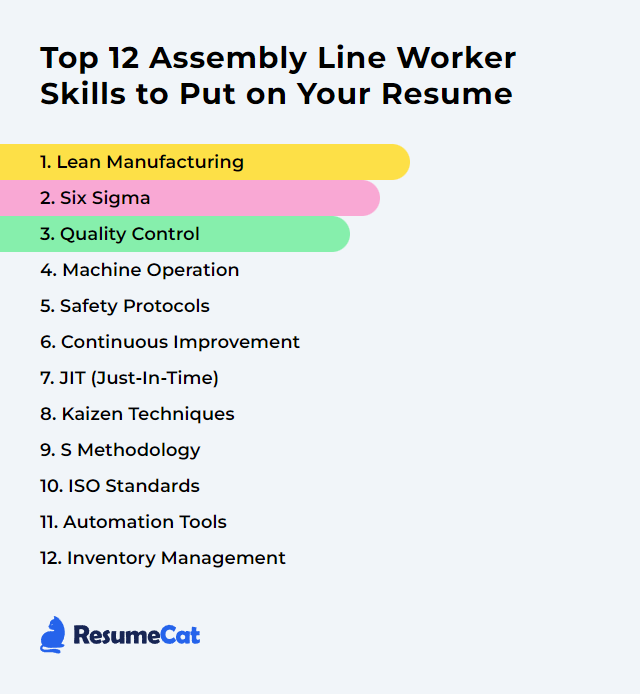
Assembly Line Worker Skills
- Lean Manufacturing
- Six Sigma
- Quality Control
- Machine Operation
- Safety Protocols
- Continuous Improvement
- JIT (Just-In-Time)
- Kaizen Techniques
- S Methodology
- ISO Standards
- Automation Tools
- Inventory Management
1. Lean Manufacturing
Lean Manufacturing is a production approach aimed at minimizing waste and maximizing efficiency on the assembly line, focusing on producing more value for customers with fewer resources.
Why It's Important
Lean Manufacturing is important for an Assembly Line Worker because it streamlines production processes, reduces waste, and increases efficiency, leading to a faster, safer, and more productive work environment.
How to Improve Lean Manufacturing Skills
Improving Lean Manufacturing, especially from the perspective of an Assembly Line Worker, involves focusing on reducing waste, optimizing processes, and enhancing productivity through continuous improvement and employee empowerment. Here are concise strategies:
Continuous Improvement (Kaizen): Embrace the culture of continuous improvement by regularly analyzing and optimizing assembly line processes. Kaizen Institute provides insights into implementing Kaizen effectively.
5S Methodology: Implement the 5S (Sort, Set in order, Shine, Standardize, Sustain) methodology to organize the workplace, ensuring efficiency and safety. Lean Production offers a detailed overview.
Just-In-Time (JIT) Production: Reduce inventory costs and increase efficiency by producing just what is needed, when it’s needed. Lean Manufacturing Tools delves into JIT principles.
Standardized Work: Standardize tasks to ensure consistency and efficiency. This includes creating detailed work instructions and training materials for assembly line workers. Lean.org discusses the importance of standardized work in Lean.
Empower Workers: Encourage assembly line workers to contribute ideas for improvement and empower them to make small changes without extensive approvals. This boosts morale and fosters a culture of ownership and continuous improvement. Harvard Business Review explores strategies for employee empowerment.
Visual Management: Use visual cues to improve communication, reduce errors, and streamline processes. This includes clear labeling, instructions, and performance metrics visible to all workers. The Lean Way offers insights into effective visual management.
Root Cause Analysis: When problems occur, use tools like the 5 Whys or Fishbone Diagram to identify and address the root cause, preventing recurrence. ASQ provides resources on root cause analysis.
By focusing on these strategies, assembly line workers can actively contribute to improving lean manufacturing processes, resulting in increased productivity, reduced waste, and a more engaged workforce.
How to Display Lean Manufacturing Skills on Your Resume
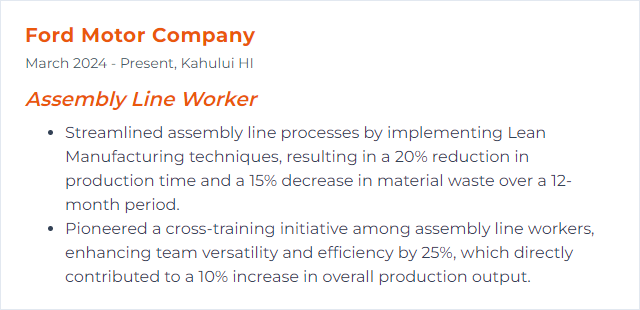
2. Six Sigma
Six Sigma is a quality management strategy aimed at reducing errors and increasing efficiency in manufacturing processes, such as those on an assembly line, by systematically identifying and eliminating defects to improve overall product quality.
Why It's Important
Six Sigma is important for an Assembly Line Worker because it reduces defects and waste, leading to higher quality products, increased efficiency, and customer satisfaction.
How to Improve Six Sigma Skills
To improve Six Sigma as an Assembly Line Worker, focus on the following concise strategies:
Understand Core Processes: Familiarize yourself with the DMAIC (Define, Measure, Analyze, Improve, Control) methodology to identify and eliminate defects. ASQ’s DMAIC.
Quality Training: Enhance your skills through Six Sigma certification courses. iSixSigma Training.
Data Analysis: Use statistical tools to analyze assembly line data for identifying improvement areas. Minitab’s Guide.
Lean Principles: Integrate Lean manufacturing techniques to reduce waste and increase efficiency. Lean Enterprise Institute.
Team Collaboration: Work closely with your team to share insights and implement best practices. Smartsheet on Collaboration.
Continuous Improvement: Actively seek and apply feedback for ongoing process enhancements. Kanbanize on Continuous Improvement.
By focusing on these areas, an Assembly Line Worker can significantly contribute to Six Sigma improvement efforts.
How to Display Six Sigma Skills on Your Resume
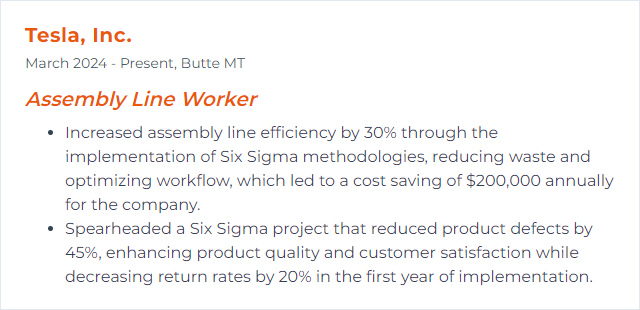
3. Quality Control
Quality Control in the context of an Assembly Line Worker involves inspecting and testing products at various stages of production to ensure they meet established standards of quality and functionality before they reach the consumer.
Why It's Important
Quality control is crucial for an assembly line worker as it ensures the products meet specified standards, reducing errors and defects. This leads to increased customer satisfaction, fewer returns, and maintains the company's reputation for reliability.
How to Improve Quality Control Skills
Improving quality control for an assembly line worker involves several key steps focused on precision, continuous learning, and feedback integration. Here's a concise guide:
- Training: Invest in regular training programs to keep workers updated on the latest quality standards and techniques.
- Standardization: Implement standard operating procedures (SOPs) to ensure consistency in every product assembled.
- Quality Tools: Utilize quality control tools like Pareto Charts and Check Sheets for identifying and addressing defects.
- Feedback Mechanism: Establish a robust feedback system that allows workers to report issues or suggest improvements quickly.
- Continuous Improvement: Adopt a Kaizen mindset, focusing on continuous improvement in quality and efficiency.
- Quality Circles: Form quality circles among workers to collaboratively solve problems and enhance product quality.
- Maintenance: Ensure regular maintenance of machinery to prevent malfunctions that can lead to quality issues.
By focusing on these areas, an assembly line worker can significantly contribute to improving quality control in the manufacturing process.
How to Display Quality Control Skills on Your Resume
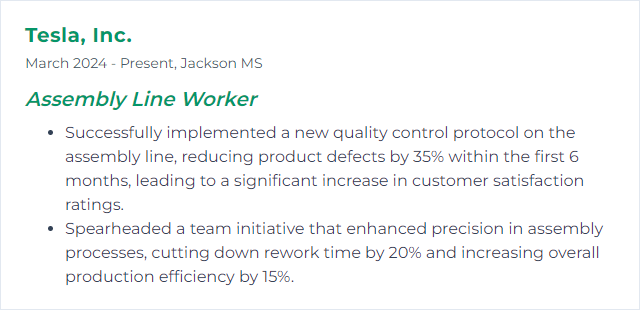
4. Machine Operation
Machine operation, in the context of an assembly line worker, refers to the skilled task of controlling and managing machinery used in the production process to ensure efficient assembly and manufacturing of products.
Why It's Important
Machine operation is crucial for an Assembly Line Worker as it ensures the efficient, precise, and timely production of goods, maintaining high-quality standards and productivity levels.
How to Improve Machine Operation Skills
To improve machine operation as an assembly line worker, focus on the following key areas:
Training and Skills Development: Enhance your understanding of the machinery through ongoing training. This includes safety procedures, operation techniques, and troubleshooting.
Regular Maintenance: Ensure machines are regularly maintained and inspected to prevent breakdowns and ensure efficient operation.
Optimize Workflow: Analyze and optimize the workflow around the machine to reduce unnecessary movements and increase productivity.
Quality Control: Implement quality control measures at various stages of the operation to detect and correct issues early.
Feedback Loop: Establish a feedback loop with supervisors and maintenance teams to report issues and suggest improvements based on your hands-on experience.
By focusing on these areas, you can contribute to the efficiency and reliability of machine operation on the assembly line.
How to Display Machine Operation Skills on Your Resume
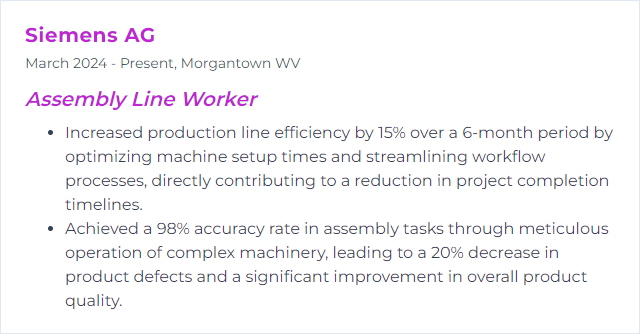
5. Safety Protocols
Safety protocols for an assembly line worker are guidelines and procedures designed to minimize risks and ensure a safe working environment. These include wearing protective gear, following machinery operating instructions, and adhering to emergency response procedures.
Why It's Important
Safety protocols are crucial for assembly line workers to prevent accidents, minimize injury risks, and ensure a secure working environment, leading to improved productivity and worker well-being.
How to Improve Safety Protocols Skills
To improve safety protocols for assembly line workers, follow these concise steps:
Conduct Regular Training: Ensure workers receive ongoing safety training specific to their tasks and the equipment they use. This keeps safety protocols fresh in their minds.
Perform Risk Assessments: Regularly assess risks associated with the assembly line, identifying potential hazards and implementing measures to mitigate them.
Use Proper Personal Protective Equipment (PPE): Ensure workers have access to and use the correct PPE for their specific tasks, such as gloves, goggles, or hearing protection.
Implement Ergonomic Solutions: Address ergonomic concerns to prevent strains and injuries by adjusting workstations to fit the worker and suggesting regular breaks. Ergonomics in the Workplace offers guidelines.
Encourage Reporting of Hazards: Create a culture where workers feel safe to report potential hazards or near-misses without fear of retribution. This can help prevent future incidents.
Regular Equipment Maintenance: Ensure all equipment is regularly maintained and inspected to prevent malfunctions that could lead to accidents.
Emergency Preparedness: Train workers on emergency procedures, including the use of fire extinguishers, and ensure clear, unobstructed emergency exits.
By implementing these measures and fostering a culture of safety, assembly line workers can be better protected from potential hazards.
How to Display Safety Protocols Skills on Your Resume
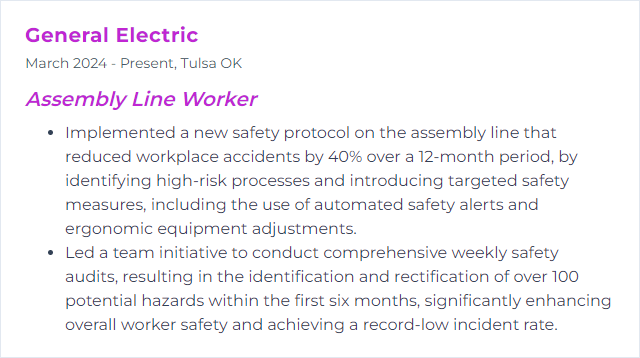
6. Continuous Improvement
Continuous improvement in the context of an assembly line worker refers to the ongoing efforts to enhance processes, reduce waste, and increase efficiency and product quality on the production line.
Why It's Important
Continuous improvement is crucial for an assembly line worker as it enhances efficiency, reduces waste, and increases product quality, ensuring competitiveness and job security.
How to Improve Continuous Improvement Skills
To improve Continuous Improvement as an Assembly Line Worker, focus on the following short steps:
- Engage in Lean Manufacturing: Embrace lean principles to minimize waste and optimize efficiency. Resources like Lean Enterprise Institute offer insights and tools.
- Implement Kaizen: Adopt Kaizen, a Japanese concept of continuous improvement through small, incremental changes. Kaizen Institute provides guidance.
- Use 5S Methodology: Organize and manage your workspace effectively using the 5S system (Sort, Set in order, Shine, Standardize, Sustain). Learn more at ASQ’s 5S page.
- Participate in Team Meetings: Regularly contribute ideas and feedback in team meetings to improve processes and address issues collectively.
- Seek Training: Continuously improve your skills through online courses and training. Websites like Coursera and LinkedIn Learning offer relevant courses.
- Adopt Technology: Be open to using new tools and technologies that can enhance productivity and quality on the assembly line.
By focusing on these steps, you can contribute significantly to continuous improvement processes in your role.
How to Display Continuous Improvement Skills on Your Resume
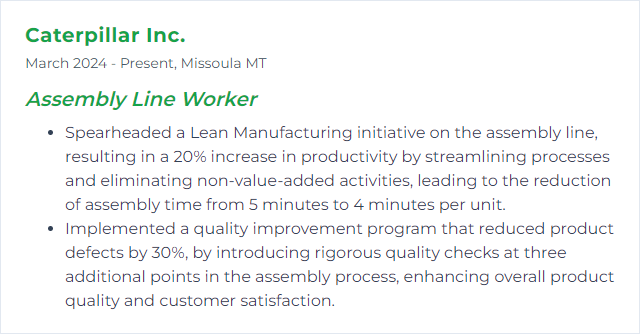
7. JIT (Just-In-Time)
JIT (Just-In-Time) is a production strategy where materials and products are manufactured or delivered exactly when needed, minimizing inventory and reducing waste on the assembly line.
Why It's Important
JIT minimizes inventory, reduces waste, and increases efficiency on the assembly line, allowing workers to focus on producing quality products with fewer delays and lower costs.
How to Improve JIT (Just-In-Time) Skills
Improving JIT (Just-In-Time) for an assembly line worker involves enhancing efficiency, reducing waste, and synchronizing production schedules to meet demand precisely. Here are concise strategies:
Cross-Training Workers: Train assembly line workers in multiple tasks to increase flexibility and adaptability. This enables workers to shift roles as needed to prevent bottlenecks. (Harvard Business Review)
Implementing Lean Techniques: Adopt lean manufacturing principles to eliminate waste, streamline production processes, and reduce inventory levels. (Lean Enterprise Institute)
Strengthen Supplier Relationships: Work closely with suppliers to ensure timely and accurate delivery of materials. Implementing a supplier integration system can improve communication and synchronization. (Supply Chain Quarterly)
Continuous Improvement (Kaizen): Encourage a culture of continuous improvement where assembly line workers are motivated to suggest improvements to the production process. (ASQ)
Use of Technology: Implement advanced planning and scheduling (APS) systems to improve production scheduling and reduce lead times. (APICS)
Quality Management: Focus on quality control at every stage of production to minimize defects and rework, thereby ensuring a smooth flow of operations. (ISO)
By focusing on these areas, an assembly line worker can contribute to a more efficient, responsive, and cost-effective JIT system.
How to Display JIT (Just-In-Time) Skills on Your Resume
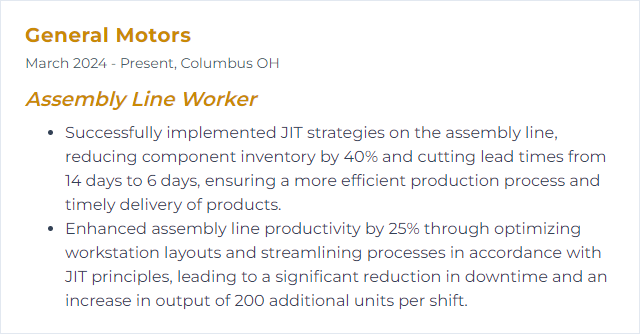
8. Kaizen Techniques
Kaizen is a Japanese term meaning "change for the better" or "continuous improvement." For an assembly line worker, Kaizen techniques involve small, incremental changes to workflow or processes aimed at increasing efficiency, reducing waste, and improving quality and safety on the production line. Workers are encouraged to suggest improvements based on their day-to-day experiences.
Why It's Important
Kaizen techniques are important for an Assembly Line Worker because they focus on continuous, incremental improvements in the work process, enhancing efficiency, reducing waste, and improving productivity and job satisfaction.
How to Improve Kaizen Techniques Skills
To improve Kaizen techniques for an assembly line worker, focus on continuous, incremental improvements by:
Standardizing Processes: Ensure tasks are performed consistently to identify areas for improvement. More on standardization.
5S Framework: Implement the 5S (Sort, Set in order, Shine, Standardize, Sustain) to organize the workplace efficiently, reducing waste and improving productivity. Implementing 5S.
Visual Management: Use visual cues to quickly communicate information, making the process more efficient and identifying issues faster. Visual Management Techniques.
Employee Empowerment: Encourage workers to suggest improvements. Their hands-on experience offers valuable insights for enhancing processes. Empowering Employees.
Problem-solving in Teams: Form small groups to tackle specific issues, fostering a collaborative environment that encourages innovative solutions. Team Problem Solving.
Continuous Learning: Offer training and learning opportunities to keep skills up-to-date and encourage the adoption of new, more efficient methods. Lifelong Learning in the Workplace.
Root Cause Analysis: Use techniques like the 5 Whys to drill down to the root cause of problems, ensuring that solutions are effective and long-lasting. Root Cause Analysis.
By focusing on these areas, assembly line workers can continuously improve their operations, making them more efficient and productive.
How to Display Kaizen Techniques Skills on Your Resume
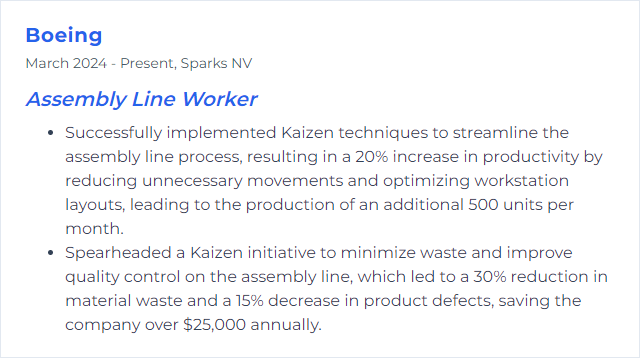
9. S Methodology
S Methodology, in the context of an assembly line worker, refers to a systematic approach aimed at optimizing production efficiency and quality. It involves standardizing work processes, reducing waste, and ensuring safety, thereby enabling workers to perform tasks effectively and consistently.
Why It's Important
The S Methodology is important for an Assembly Line Worker because it enhances efficiency and safety, ensuring tasks are performed systematically and consistently, reducing errors and workplace accidents.
How to Improve S Methodology Skills
Improving the S Methodology, particularly for an Assembly Line Worker, involves focusing on streamlining processes, enhancing efficiency, and reducing waste. Here's a concise guide:
- Standardize Tasks: Ensure all tasks are clearly defined and standardized to reduce variability and improve consistency. More on Standardizing Work
- Simplify Processes: Analyze the assembly line to identify and eliminate unnecessary steps or processes. Simplification Techniques
- Safety First: Prioritize safety to prevent accidents and improve worker morale. Improving Safety
- Skills Development: Invest in training and development to enhance workers' skills. Training Strategies
- Sustain Improvements: Implement a system to maintain and continuously improve the processes. Continuous Improvement
By focusing on these areas, you can significantly improve the efficiency and effectiveness of an assembly line worker within the S Methodology framework.
How to Display S Methodology Skills on Your Resume
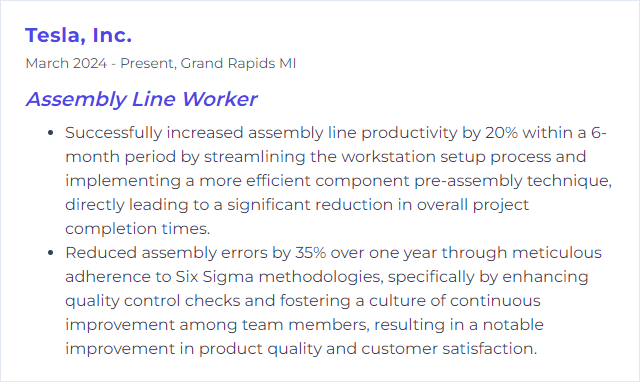
10. ISO Standards
ISO Standards are internationally recognized guidelines that ensure products, services, and systems are safe, reliable, and of good quality. For an Assembly Line Worker, they help in standardizing production processes, enhancing efficiency, and ensuring the quality of products being assembled.
Why It's Important
ISO Standards ensure consistent quality and safety in products, streamline production processes, and improve efficiency on the assembly line, benefiting both workers and consumers.
How to Improve ISO Standards Skills
Improving ISO Standards as an Assembly Line Worker involves focusing on quality, efficiency, and safety. Here are key steps:
Understand ISO Standards: Familiarize yourself with the specific ISO standards applicable to your assembly line work, such as ISO 9001 for quality management systems.
Continuous Improvement: Implement a continuous improvement process, such as Kaizen, to constantly seek ways to enhance quality, reduce waste, and improve efficiency.
Quality Control: Adhere strictly to quality control measures. Use Six Sigma techniques to minimize defects and ensure products meet quality standards.
Safety First: Follow and promote safety protocols in line with ISO 45001, ensuring a safe working environment.
Training and Development: Engage in ongoing training related to ISO standards and assembly line best practices to stay informed about the latest advancements and techniques.
Feedback Loop: Create a feedback mechanism for reporting issues, sharing improvements, and implementing changes to processes based on ISO 9004 guidelines for quality management.
Team Collaboration: Work closely with your team and management to align efforts and share insights on improving adherence to ISO standards.
By focusing on these areas, an Assembly Line Worker can contribute significantly to improving ISO Standards within their scope of work.
How to Display ISO Standards Skills on Your Resume
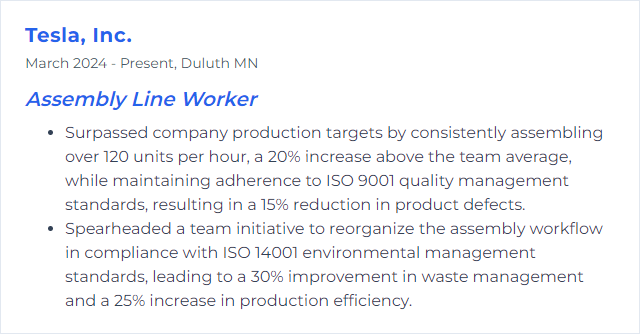
11. Automation Tools
Automation tools in the context of an assembly line worker refer to software and mechanical devices designed to automate repetitive or complex tasks, enhancing efficiency, safety, and productivity on the production line.
Why It's Important
Automation tools are important for an Assembly Line Worker because they enhance efficiency, improve product quality, reduce manual errors, and ensure consistent production output, allowing for safer and more cost-effective operations.
How to Improve Automation Tools Skills
To enhance automation tools for assembly line workers, focus on these key strategies:
Streamline Design: Simplify the interface and processes to reduce complexity. Ergonomics and Design can significantly impact usability and efficiency.
Integrate AI and Machine Learning: Incorporate AI to predict maintenance needs and optimize performance. Machine Learning in Manufacturing offers insights into its applications.
Enhance Connectivity: Use IoT to connect tools and machines for real-time monitoring and control. IoT in Manufacturing provides a comprehensive overview.
Customizable Workflows: Allow workers to adjust automation sequences to match task variability. Customization in Production highlights the importance of flexibility.
Regular Training and Updates: Keep workers informed about new features and best practices. Continuous Learning supports adaptation and mastery of new technologies.
Safety and Ergonomics: Prioritize worker safety and comfort with ergonomic designs. Ergonomics in Manufacturing discusses the impact on worker well-being and productivity.
By focusing on these areas, you can significantly improve the functionality and user experience of automation tools in assembly lines.
How to Display Automation Tools Skills on Your Resume
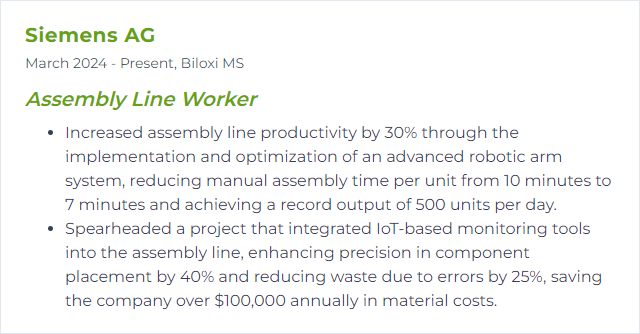
12. Inventory Management
Inventory management involves overseeing and controlling the ordering, storage, and use of components that a company uses in the production of the items it sells. For an Assembly Line Worker, it means ensuring the right parts are available at the right time to maintain uninterrupted production flow.
Why It's Important
Inventory management ensures the right materials are available when needed on the assembly line, minimizing downtime and maintaining productivity.
How to Improve Inventory Management Skills
Improving inventory management, especially for an assembly line worker, involves streamlining processes and ensuring accurate tracking of materials and components. Here are concise strategies:
- Implement Lean Inventory Techniques: Adopt lean inventory management principles to minimize waste and ensure you have just the right amount of inventory on hand.
- Use Automation Tools: Leverage inventory management software that can automate tracking and ordering processes, reducing errors and saving time.
- Regular Audits: Conduct regular inventory audits to ensure records match the physical inventory and identify discrepancies early.
- Adopt Just-In-Time (JIT) Inventory: Implement JIT inventory practices to reduce inventory costs and increase efficiency by receiving goods only as they're needed in the production process.
- Improve Forecasting: Utilize data analytics to improve forecasting accuracy, ensuring you have the right components available when needed without overstocking.
By focusing on these strategies, an assembly line worker can contribute to more efficient and accurate inventory management, supporting overall productivity and cost reduction.
How to Display Inventory Management Skills on Your Resume
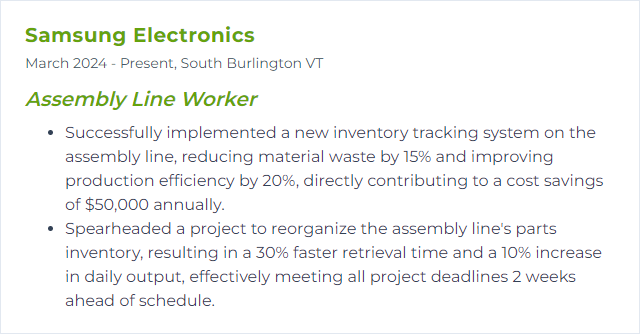