Top 12 Line Leader Skills to Put on Your Resume
In today's competitive job market, standing out as a line leader requires showcasing a unique set of skills on your resume that highlight your leadership and operational efficiency. This article delves into the top 12 line leader skills that can significantly enhance your resume, making you an attractive candidate to potential employers in various industries.
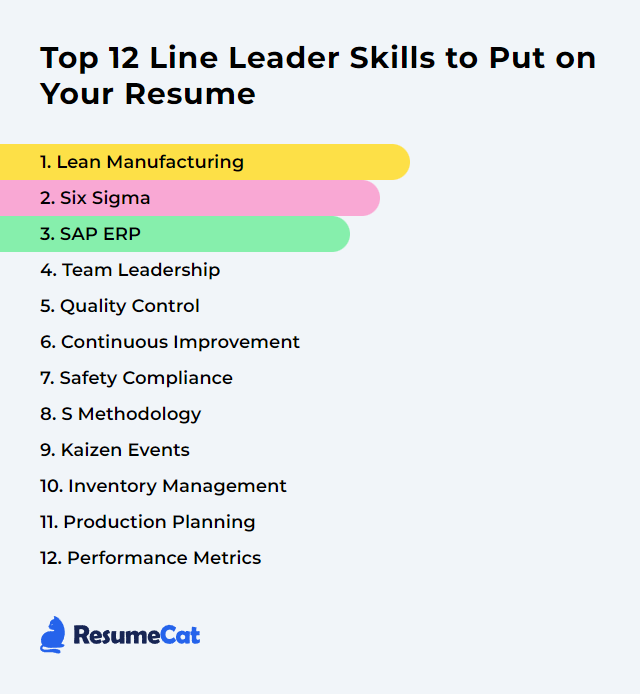
Line Leader Skills
- Lean Manufacturing
- Six Sigma
- SAP ERP
- Team Leadership
- Quality Control
- Continuous Improvement
- Safety Compliance
- S Methodology
- Kaizen Events
- Inventory Management
- Production Planning
- Performance Metrics
1. Lean Manufacturing
Lean Manufacturing is a systematic approach aimed at reducing waste and increasing efficiency in production processes, focusing on maximizing value for the customer. For a Line Leader, it involves overseeing and implementing strategies to improve workflow, ensure quality control, and optimize resource use on the production line.
Why It's Important
Lean Manufacturing is important because it helps minimize waste and maximizes efficiency in production processes, leading to higher quality products, reduced costs, and faster delivery times. For a Line Leader, it enables more effective management of resources and personnel, ensuring smoother operations and increased productivity.
How to Improve Lean Manufacturing Skills
To improve Lean Manufacturing as a Line Leader, focus on the following key strategies:
Continuous Improvement (Kaizen): Encourage and implement small, continuous improvements in your line. Engage your team in identifying inefficiencies and brainstorming solutions. Kaizen Institute
5S Methodology: Implement 5S (Sort, Set in order, Shine, Standardize, Sustain) to organize the workplace, improve efficiency, and reduce waste. This methodology promotes a disciplined approach and a visual workplace. Lean Production
Value Stream Mapping: Use Value Stream Mapping to visualize and understand the flow of materials and information as a product makes its way through the value stream. This helps in identifying and eliminating waste. ASQ
Standard Work: Develop and implement standard work procedures to ensure consistency and efficiency. This includes documenting best practices and training your team to follow them. Lean Enterprise Institute
Problem Solving: Foster a culture of problem-solving where every team member feels responsible for identifying and addressing issues promptly. Utilize problem-solving frameworks like PDCA (Plan-Do-Check-Act). American Society for Quality
Visual Management: Use visual tools and indicators to make the flow of work and the status of tasks clear at a glance, facilitating quicker decision-making and problem-solving. iSixSigma
Empowerment and Engagement: Empower your team by involving them in decision-making processes and recognizing their contributions. This increases engagement and ownership. Gallup
By focusing on these strategies, you can lead your manufacturing line to greater efficiency, productivity, and quality, embodying the principles of Lean Manufacturing.
How to Display Lean Manufacturing Skills on Your Resume
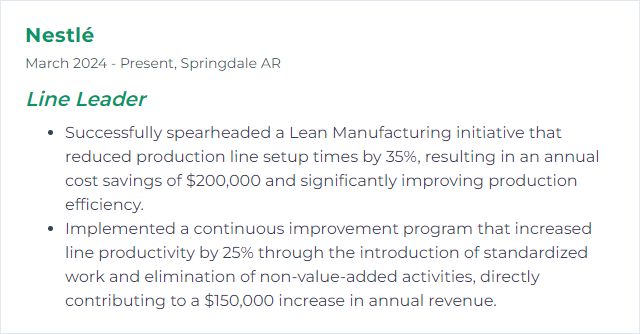
2. Six Sigma
Six Sigma is a data-driven approach and methodology for eliminating defects in any process, aiming to achieve near-perfect quality. For a Line Leader, it involves using specific tools and techniques to improve production efficiency, reduce variability, and ensure the consistent quality of products.
Why It's Important
Six Sigma is important for a Line Leader because it provides a systematic approach to improving production efficiency, reducing defects, and increasing customer satisfaction through data-driven decision-making and problem-solving techniques.
How to Improve Six Sigma Skills
To improve Six Sigma as a Line Leader, focus on these key areas:
1. Understand Core Principles: Deepen your understanding of Six Sigma methodologies by reviewing resources like ASQ's Six Sigma Training.
2. Apply DMAIC Methodology: Consistently apply the Define, Measure, Analyze, Improve, and Control (DMAIC) framework to process improvements. iSixSigma offers detailed guidance.
3. Engage Your Team: Encourage team involvement in Six Sigma projects. The Lean Methods Group provides strategies for team engagement.
4. Leverage Quality Tools: Utilize Six Sigma tools such as Pareto Charts and Control Charts effectively. MoreSteam offers practical tutorials.
5. Continuous Learning: Keep learning through platforms like Coursera that offer Six Sigma courses.
6. Implement Lean Principles: Integrate Lean manufacturing principles to eliminate waste and improve efficiency. Lean Enterprise Institute has resources to get started.
7. Seek Feedback: Regularly solicit feedback from both your team and stakeholders to identify areas for improvement.
8. Monitor and Control: Use Six Sigma's control phase to ensure sustainability of improvements.
By focusing on these areas, you can enhance your Six Sigma efforts and drive significant process improvements within your role as a Line Leader.
How to Display Six Sigma Skills on Your Resume
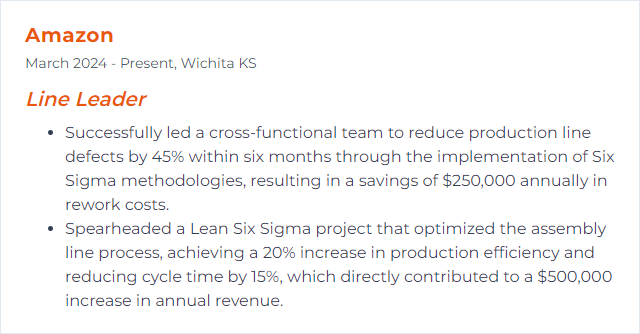
3. SAP ERP
SAP ERP is a comprehensive enterprise resource planning software that integrates key business functions, such as production, sales, and finance, to streamline processes, improve data accuracy, and facilitate decision-making for line leaders and other managers.
Why It's Important
SAP ERP is crucial for a Line Leader as it integrates core business processes, enhancing efficiency, improving decision-making through real-time data, and enabling better management of resources and operations.
How to Improve SAP ERP Skills
To improve SAP ERP for a Line Leader, focus on these key areas:
Training and Skills Enhancement: Ensure Line Leaders are trained on the latest SAP ERP functionalities relevant to their duties. SAP offers specific training courses that can be tailored to their needs.
Process Automation: Utilize SAP's intelligent robotic process automation (RPA) solutions to automate repetitive tasks, increasing efficiency and allowing Line Leaders to focus on more strategic activities.
Real-time Data Access: Implement SAP Fiori apps for immediate access to critical data and KPIs. Visit the SAP Fiori library to find apps that can enhance decision-making for Line Leaders.
Customization and Personalization: Customize the SAP ERP system to suit the unique needs of your production line. SAP’s Custom Development services can help tailor solutions specifically for your business context.
Feedback Loop: Establish a continuous feedback loop between Line Leaders and the SAP ERP system developers. This can be achieved through regular review meetings or by using collaboration tools like SAP Jam Collaboration.
By focusing on these areas, you can significantly improve the effectiveness of SAP ERP for Line Leaders, enhancing productivity and operational efficiency.
How to Display SAP ERP Skills on Your Resume
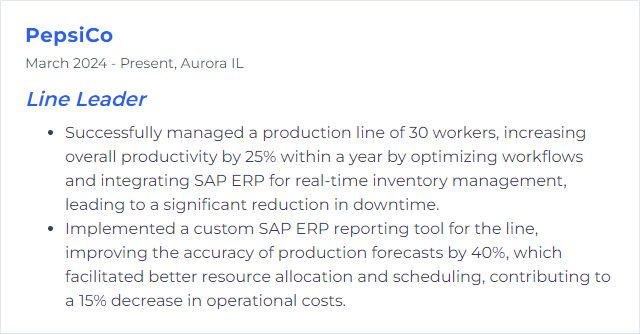
4. Team Leadership
Team leadership, particularly for a Line Leader, involves guiding and coordinating a group of individuals towards achieving specific production or operational goals by effectively managing resources, motivating team members, and resolving conflicts to ensure efficient workflow and high-quality outcomes.
Why It's Important
Team leadership is crucial for a Line Leader because it ensures clear direction, efficient coordination, and effective communication among team members, leading to increased productivity, morale, and the achievement of goals.
How to Improve Team Leadership Skills
Improving team leadership, especially for a Line Leader, involves enhancing communication, fostering collaboration, and promoting a positive team culture. Here are concise strategies:
Enhance Communication Skills: Clearly articulate expectations and provide constructive feedback. MindTools offers resources for improving communication.
Encourage Collaboration: Create an environment where team members feel comfortable sharing ideas and working together. Harvard Business Review discusses strategies for building great teams.
Develop Emotional Intelligence: Understand and manage your emotions, and recognize and influence the emotions of others. Verywell Mind provides tips for using emotional intelligence in the workplace.
Set Clear Goals and Expectations: Ensure that each team member understands their role and the team's objectives. Smartsheet has guidance on setting clear team goals.
Provide Regular Feedback and Recognition: Offer constructive feedback and acknowledge achievements to motivate the team. Forbes explores how to give effective feedback.
Lead by Example: Demonstrate the work ethic, attitude, and behavior you expect from your team. Inc. lists simple ways to lead by example.
Invest in Professional Development: Encourage and facilitate ongoing learning and skill development. LinkedIn Learning offers courses in leadership and management.
Foster a Positive Team Culture: Build a culture of respect, trust, and inclusivity. CultureIQ discusses the importance of a positive work culture.
Implementing these strategies can significantly enhance team leadership capabilities.
How to Display Team Leadership Skills on Your Resume
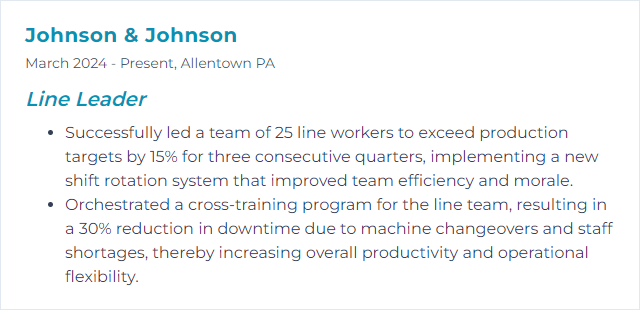
5. Quality Control
Quality Control involves monitoring production processes and outcomes to ensure that the final products meet the established standards of quality specified for them. For a Line Leader, it entails overseeing the operations on the production line to ensure that products are manufactured correctly, meet quality standards, and are free of defects.
Why It's Important
Quality Control is crucial for a Line Leader because it ensures products meet the required standards, reducing waste, minimizing rework, and enhancing customer satisfaction, ultimately leading to improved efficiency and profitability.
How to Improve Quality Control Skills
Improving quality control, especially for a Line Leader, involves a strategic approach focusing on process, people, and technology. Here are concise steps with external resources:
Understand Processes: Get a detailed understanding of the production process. Use process mapping techniques to identify potential quality issues. ASQ Process Mapping.
Implement Standard Operating Procedures (SOPs): Develop and enforce SOPs to ensure consistency. Creating SOPs.
Training and Empowerment: Train your team regularly on quality standards and empower them to identify and correct issues. Effective Training Strategies.
Use Quality Tools: Utilize tools like Six Sigma, 5S, and Kaizen for continuous improvement. Introduction to Quality Tools.
Regular Audits and Inspections: Schedule routine audits to ensure adherence to quality standards. Conducting Effective Audits.
Feedback Loop: Implement a feedback loop from customers and frontline employees to identify areas for improvement. Feedback Strategies.
Leverage Technology: Invest in quality control technologies such as automated inspection systems or AI for real-time monitoring. AI in Quality Control.
Foster a Quality Culture: Cultivate a culture that prioritizes quality over quantity. Building a Quality Culture.
By systematically addressing these areas, a Line Leader can significantly improve the quality control process within their domain.
How to Display Quality Control Skills on Your Resume
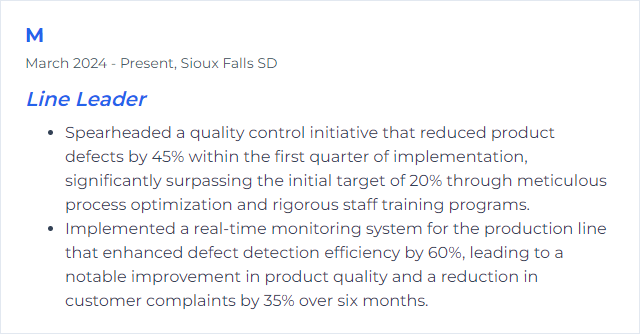
6. Continuous Improvement
Continuous Improvement, in the context of a Line Leader, involves the ongoing effort to enhance products, services, or processes through incremental and breakthrough improvements to increase efficiency, quality, and productivity on the production line.
Why It's Important
Continuous improvement is crucial for a Line Leader as it enhances operational efficiency, reduces waste, fosters innovation, and improves product quality, ensuring competitive advantage and customer satisfaction.
How to Improve Continuous Improvement Skills
To improve Continuous Improvement as a Line Leader, focus on the following concise steps:
Engage Your Team: Motivate and involve your team in the continuous improvement process. Create an environment where every team member feels comfortable sharing ideas and suggestions. Harvard Business Review offers insights on creating a culture that supports continuous improvement.
Implement Lean Principles: Adopt Lean methodologies to streamline processes, reduce waste, and increase efficiency. The Lean Enterprise Institute provides resources and guides on implementing these principles in your operations.
Use the PDCA Cycle: Embrace the Plan-Do-Check-Act (PDCA) cycle for systematic problem solving and continuous improvement. This method encourages a structured approach to problem identification and resolution. The American Society for Quality (ASQ) offers a detailed explanation of the PDCA cycle.
Leverage Technology: Utilize technology and tools for process monitoring and data analysis to identify improvement opportunities. Software like Trello for task management or Tableau for data visualization can be instrumental.
Provide Training and Education: Continuously educate yourself and your team on new methodologies, tools, and skills relevant to continuous improvement. Coursera and edX offer courses on Lean, Six Sigma, and other relevant topics.
Measure and Celebrate Success: Regularly measure the impact of your continuous improvement efforts and celebrate successes with your team to build momentum. MindTools provides strategies for effective performance measurement.
By focusing on these areas, you can enhance your continuous improvement efforts and drive meaningful change within your team and organization.
How to Display Continuous Improvement Skills on Your Resume
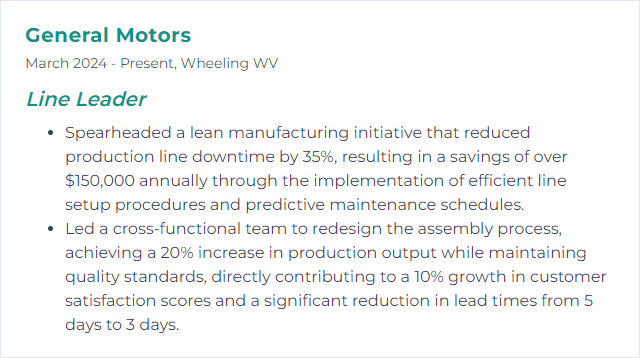
7. Safety Compliance
Safety compliance, in regards to a Line Leader, refers to adhering to established safety regulations and guidelines to ensure a safe working environment for all team members on the production line.
Why It's Important
Safety compliance is crucial for a Line Leader because it ensures the well-being of workers, prevents accidents and injuries, minimizes legal and financial risks, and maintains productivity by avoiding disruptions caused by unsafe practices.
How to Improve Safety Compliance Skills
Improving safety compliance as a Line Leader involves a proactive approach focused on education, communication, and enforcement. Here's a concise guide:
Educate your team: Ensure all members are trained on safety standards and protocols. Utilize resources from OSHA's Training and Education page for standardized materials.
Communicate effectively: Regularly hold safety briefings and encourage open discussions about concerns. The CDC's Health Communication Basics can provide strategies for effective communication.
Enforce safety protocols: Implement a zero-tolerance policy towards safety violations. Use SafetyCulture's iAuditor for regular safety inspections and audits.
Encourage reporting: Make it easy for employees to report safety issues without fear of retribution. Tools like SafeSite can facilitate anonymous reporting.
Review and Revise: Continuously assess and improve safety measures based on feedback and incident reports. The National Safety Council offers resources for workplace safety evaluation and improvement.
By focusing on these key areas, you can foster a culture of safety compliance within your team.
How to Display Safety Compliance Skills on Your Resume
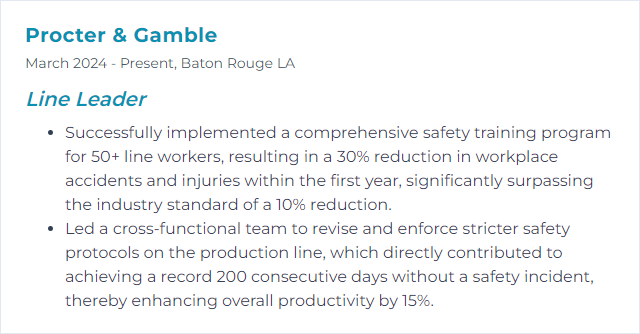
8. S Methodology
S Methodology is a systematic approach used to improve and optimize production processes, focusing on safety, standardization, and efficiency. For a Line Leader, it involves implementing and overseeing these practices to enhance productivity, ensure quality control, and promote a safe working environment on the production line.
Why It's Important
The S Methodology is important for a Line Leader as it provides a systematic approach to optimize production efficiency, improve quality, and ensure safety on the production line, leading to enhanced team performance and product output.
How to Improve S Methodology Skills
Improving S Methodology, particularly for a Line Leader, involves focusing on streamlining operations, enhancing team performance, and ensuring continuous improvement. Here's a concise guide:
Standardize Processes: Establish clear, standardized procedures for all tasks to minimize variability and errors. Institute for Manufacturing, University of Cambridge offers insights into process mapping, a crucial step in standardization.
Skill Development: Invest in training and development to enhance the skills of your team. Continuous learning platforms like LinkedIn Learning can be invaluable.
Simplify Tasks: Identify and eliminate unnecessary steps in processes to increase efficiency. Tools like Lean Six Sigma can be helpful in simplifying tasks.
Safety and Ergonomics: Prioritize workplace safety and ergonomic improvements to prevent injuries and boost productivity. The Occupational Safety and Health Administration (OSHA) provides resources and guidelines.
Sustain Improvements: Implement a culture of continuous improvement with regular reviews and adjustments. The Kaizen Institute offers strategies for sustaining improvements.
Schedule Regular Feedback: Create a feedback loop with your team to identify issues and opportunities for improvement. Officevibe is a tool that can facilitate anonymous feedback.
Set Goals and Metrics: Define clear, achievable goals and track performance with relevant metrics. SMART criteria can guide goal setting, ensuring they are specific, measurable, achievable, relevant, and time-bound.
Supply Chain Collaboration: Work closely with suppliers to ensure smooth operations and quality input materials. SCM World provides insights into effective supply chain collaboration.
By focusing on these areas, a Line Leader can significantly improve the S Methodology in their operations, leading to enhanced efficiency, better team performance, and higher quality outputs.
How to Display S Methodology Skills on Your Resume
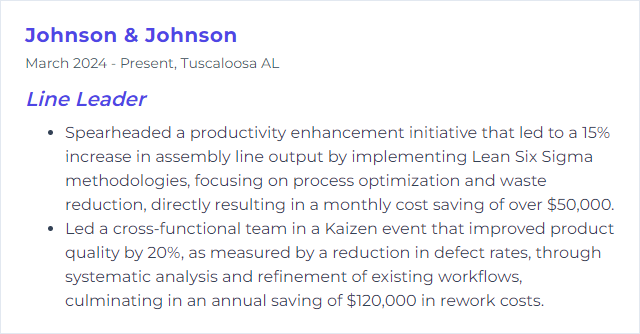
9. Kaizen Events
Kaizen Events are focused, short-term projects aimed at improving specific areas within a process or operation. For a Line Leader, it involves leading a team through a rapid, collaborative effort to identify inefficiencies and implement solutions, ultimately enhancing productivity and quality on the production line.
Why It's Important
Kaizen Events are crucial for Line Leaders as they drive rapid improvements in processes, enhance teamwork and problem-solving skills, and significantly reduce waste, leading to increased efficiency and productivity on the production line.
How to Improve Kaizen Events Skills
To enhance Kaizen Events as a Line Leader, focus on these concise strategies:
Preparation: Ensure thorough preparation by selecting a clear, specific goal and assembling a diverse team. Kaizen Institute emphasizes the importance of clear objectives and team diversity.
Training: Provide training sessions for your team on Kaizen principles and tools before the event to ensure everyone is on the same page. ASQ offers resources on Kaizen principles and methodologies.
Engagement: Actively engage all team members by encouraging participation and valuing their input to foster a sense of ownership. Lean Enterprise Institute discusses strategies for engaging employees in continuous improvement.
Implementation: Swiftly implement action items generated during the event to maintain momentum and demonstrate commitment. iSixSigma offers insights on effective implementation.
Follow-up: Conduct regular follow-ups to assess the impact of the changes, address any issues, and ensure sustainability. SME highlights the importance of follow-up for continuous improvement.
By focusing on these areas, Line Leaders can significantly improve the effectiveness of Kaizen Events.
How to Display Kaizen Events Skills on Your Resume
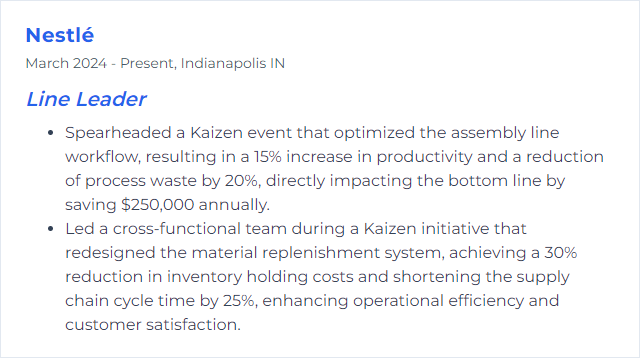
10. Inventory Management
Inventory management is the process of overseeing and controlling the flow of goods, from ordering and storing materials to managing stock levels and fulfilling orders, ensuring a line leader has the right products, in the right quantity, at the right time, to meet production demands efficiently.
Why It's Important
Inventory management is crucial for a Line Leader because it ensures the right materials are available when needed, minimizing downtime and maximizing production efficiency. It also helps in reducing excess inventory and storage costs, thus contributing to the overall profitability of operations.
How to Improve Inventory Management Skills
Improving inventory management, especially for a Line Leader, involves a mix of strategic planning, technology adoption, and efficient communication. Here are concise steps with helpful resources:
Understand Demand: Forecast accurately to match inventory levels with production needs. Utilize tools like demand forecasting software for precision.
Adopt Lean Inventory Techniques: Implement Just-In-Time (JIT) inventory management to reduce waste and increase efficiency.
Use Inventory Management Software: Invest in inventory management systems that provide real-time data, helping in making informed decisions quickly.
Regular Audits: Conduct regular inventory audits to ensure data accuracy and prevent discrepancies.
Improve Supplier Relationships: Build strong relationships with suppliers for better supply chain reliability.
Train Your Team: Ensure your team is well-trained on best practices in inventory management through resources like APICS.
Implement Cross-Training: Cross-train employees to improve flexibility and efficiency in handling inventory tasks.
Continuous Improvement: Adopt a culture of continuous improvement (Kaizen) to constantly seek ways to optimize inventory management processes.
By focusing on these key areas, a Line Leader can significantly improve inventory management, leading to reduced costs, improved production efficiency, and better customer satisfaction.
How to Display Inventory Management Skills on Your Resume
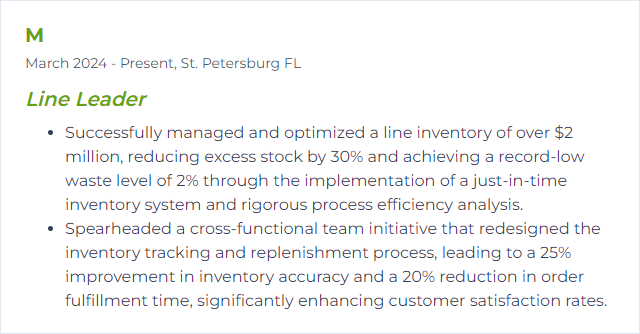
11. Production Planning
Production planning involves organizing and scheduling manufacturing operations to ensure efficient production processes and meet production goals, focusing on aspects like material availability, workforce allocation, and equipment use. For a Line Leader, it means coordinating daily production activities, monitoring progress, and adjusting plans as needed to maintain productivity and meet deadlines.
Why It's Important
Production planning is crucial for a Line Leader as it ensures the efficient use of resources, minimizes production costs, and meets delivery deadlines, leading to increased productivity and customer satisfaction.
How to Improve Production Planning Skills
To improve Production Planning as a Line Leader, focus on the following strategies:
Forecast Demand Accurately: Use historical data and market analysis to forecast demand accurately, enabling better planning of resources and materials. Tools like Forecast Pro can assist in developing more reliable demand forecasts.
Optimize Inventory Management: Implement just-in-time (JIT) inventory practices to reduce excess stock and minimize storage costs, while ensuring materials are available when needed. Fishbowl Inventory offers solutions tailored to optimizing inventory levels.
Implement Lean Manufacturing Principles: Adopt lean manufacturing techniques to eliminate waste, streamline processes, and improve efficiency. The Lean Enterprise Institute provides resources and guides to help you get started.
Use Production Planning Software: Leverage advanced production planning software to schedule, track, and optimize manufacturing processes. MRPeasy is a user-friendly option that supports small to mid-sized manufacturers.
Enhance Communication and Collaboration: Foster a culture of open communication and collaboration between departments to ensure smooth operation and quick resolution of issues. Tools like Slack can facilitate better team coordination.
Continuously Improve Processes: Implement a continuous improvement culture, encouraging feedback and innovative ideas from the team to enhance productivity and reduce inefficiencies. Kaizen methodology can guide this approach.
Train and Empower Your Team: Invest in regular training for your team to keep them updated on best practices and new technologies. Empowering them to make decisions can also improve morale and efficiency.
By focusing on these strategies, you can significantly enhance production planning and overall operational efficiency.
How to Display Production Planning Skills on Your Resume
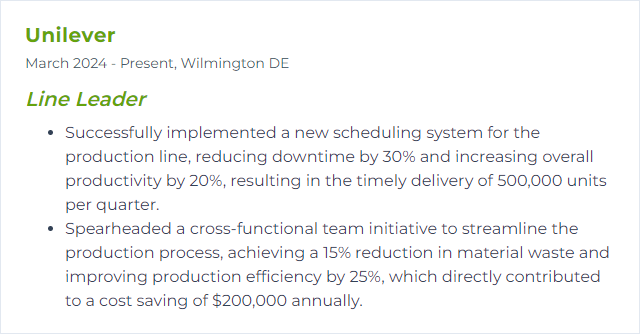
12. Performance Metrics
Performance metrics for a Line Leader are quantifiable measures used to evaluate the effectiveness, efficiency, and productivity of a Line Leader in managing production line operations, including metrics such as line uptime, production output, product quality, team performance, and adherence to safety standards.
Why It's Important
Performance metrics are crucial for a Line Leader as they provide quantitative data to measure, monitor, and improve the efficiency, productivity, and quality of production processes, directly impacting the line's overall performance and success.
How to Improve Performance Metrics Skills
Improving performance metrics as a Line Leader involves a focused approach on key areas such as productivity, quality, and team efficiency. Here's a very short and concise guide:
Set Clear Goals: Define specific, measurable, achievable, relevant, and time-bound (SMART) goals for your team. More on SMART Goals.
Monitor and Analyze Performance: Regularly track performance metrics using tools and software. Identify areas for improvement. Guide to Monitoring Performance.
Improve Processes: Implement Lean manufacturing principles to streamline operations and reduce waste. Lean Manufacturing Basics.
Skill Development: Invest in training and development programs to enhance your team's skills. Effective Training Strategies.
Engage and Motivate Team: Foster a positive work environment. Recognize and reward achievements. Employee Engagement Techniques.
Leverage Technology: Use technology to optimize operations and improve efficiency. Technology in Manufacturing.
Continuous Improvement: Adopt a Kaizen approach for continuous, incremental improvement. Understanding Kaizen.
Effective Communication: Ensure clear, concise, and effective communication within the team and with other stakeholders. Communication in Leadership.
Problem-Solving Skills: Develop your problem-solving skills to quickly address and resolve issues as they arise. Problem-Solving Strategies.
Safety and Wellbeing: Prioritize the safety and wellbeing of your team to maintain high morale and productivity. Workplace Safety Guidelines.
By focusing on these areas, you can significantly improve the performance metrics under your leadership.
How to Display Performance Metrics Skills on Your Resume
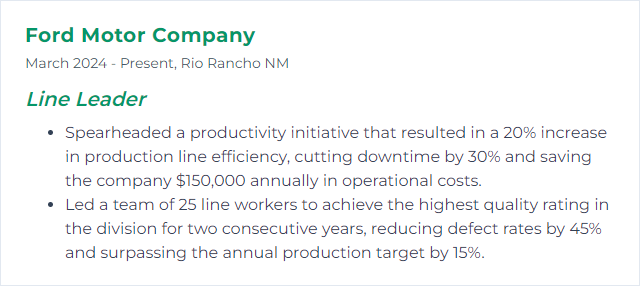