Top 12 Sheet Metal Worker Skills to Put on Your Resume
In the competitive field of sheet metal work, standing out to potential employers requires a strategic showcase of specific skills on your resume. Highlighting the top abilities in the industry not only demonstrates your expertise but also signals your commitment to excellence and adaptability in this dynamic trade.
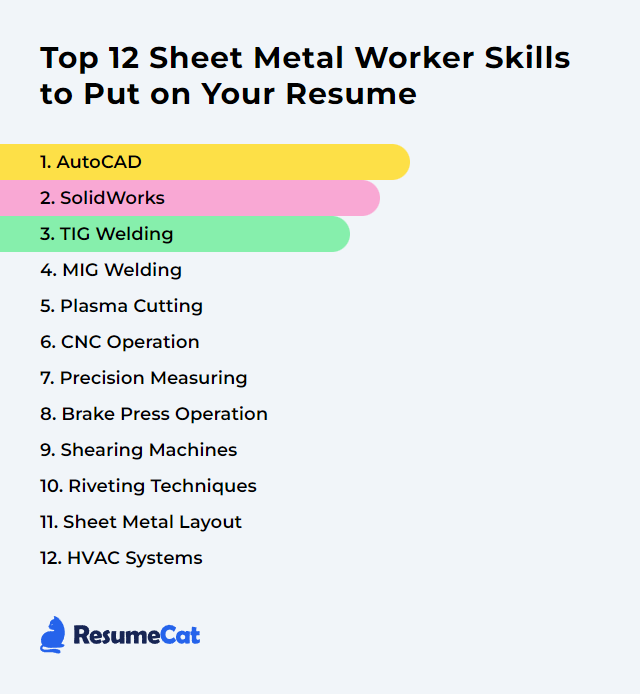
Sheet Metal Worker Skills
- AutoCAD
- SolidWorks
- TIG Welding
- MIG Welding
- Plasma Cutting
- CNC Operation
- Precision Measuring
- Brake Press Operation
- Shearing Machines
- Riveting Techniques
- Sheet Metal Layout
- HVAC Systems
1. AutoCAD
AutoCAD is a computer-aided design (CAD) software used for creating precise 2D and 3D drawings, including detailed fabrication and assembly diagrams for sheet metal projects.
Why It's Important
AutoCAD is crucial for sheet metal workers as it enables precise design, drafting, and modification of 2D and 3D models for fabrication, ensuring accuracy, efficiency, and optimization of materials and costs.
How to Improve AutoCAD Skills
To improve AutoCAD skills for a Sheet Metal Worker, focus on mastering the following areas:
Learn Basic Commands: Start by becoming proficient in basic AutoCAD commands like LINE, CIRCLE, RECTANGLE, and TRIM. Autodesk's official AutoCAD tutorials provide a good starting point.
Understand Sheet Metal Tools: Dive into AutoCAD's specialized tools for sheet metal work. The Sheet Metal Design guide by Autodesk is particularly useful.
Practice 3D Modeling: Develop your skills in 3D modeling since it's crucial for visualizing and designing sheet metal parts. The AutoCAD 3D tutorials by Autodesk can help you get started.
Utilize Sheet Metal-Specific Software: Consider learning software that is specifically designed for sheet metal work, such as Autodesk Inventor or SolidWorks, to complement your AutoCAD skills. Information can be found on the Autodesk Inventor page.
Join Online Communities and Forums: Engage with other professionals in communities such as the Autodesk forums or Reddit's r/AutoCAD to exchange tips and stay updated on industry practices.
By focusing on these areas, you can significantly improve your AutoCAD skills as a sheet metal worker.
How to Display AutoCAD Skills on Your Resume
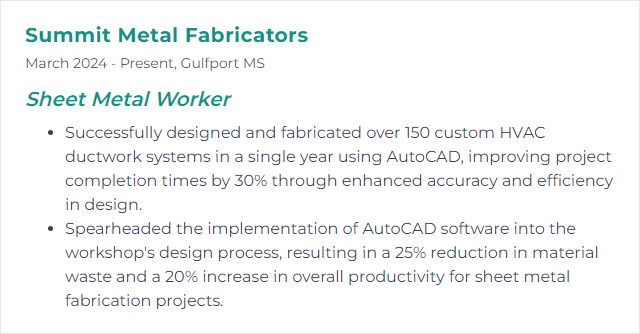
2. SolidWorks
SolidWorks is a computer-aided design (CAD) software used for creating 2D and 3D models, including sheet metal designs, enabling sheet metal workers to plan, visualize, and adjust projects before fabrication.
Why It's Important
SolidWorks is important for a Sheet Metal Worker because it provides precise 3D modeling and simulation tools that streamline the design and fabrication of sheet metal parts, enhancing accuracy, efficiency, and the ability to visualize complex bends and forms before cutting or shaping begins.
How to Improve SolidWorks Skills
Improving your SolidWorks skills, especially as a Sheet Metal Worker, involves focusing on specific functionalities that enhance your ability to design, modify, and optimize sheet metal parts and assemblies. Here’s a short and concise guide:
Master the Sheet Metal Tools: Dive deep into SolidWorks' sheet metal-specific tools like 'Base Flange/Tab', 'Edge Flange', 'Miter Flange', etc. Learning these tools inside out will significantly improve your workflow. SolidWorks provides a Sheet Metal Design guide that is a great starting point.
Utilize SolidWorks Tutorials: SolidWorks offers built-in tutorials specifically aimed at sheet metal design. These are accessible via the SolidWorks Help menu and provide step-by-step instructions on various features.
Practice with Online Courses: Websites like LinkedIn Learning and Udemy offer courses tailored to SolidWorks for sheet metal design. Engaging with these resources can provide new insights and techniques.
Join the SolidWorks Community: Participating in forums and discussion groups, such as the SolidWorks Community, can provide valuable tips, tricks, and insights from other professionals in the field.
Explore Third-Party Tools and Add-Ins: Sometimes, efficiency can be significantly improved by integrating add-ins that automate or simplify specific tasks. Research and experiment with reputable third-party tools that are compatible with SolidWorks for sheet metal work.
Set Up Custom Templates and Libraries: Save time by creating and using custom templates and libraries for your most common projects and parts. This SolidWorks blog post offers guidance on customizing the sheet metal toolbox.
Learn Keyboard Shortcuts: Increase your modeling speed by memorizing and using SolidWorks keyboard shortcuts. A quick reference can be found here.
Stay Updated with New Features: SolidWorks is continuously updated with new features and improvements. Keeping up-to-date with the latest version and its features can provide new ways to streamline your sheet metal design process.
Focusing on these aspects will enhance your proficiency in using SolidWorks for sheet metal design and fabrication, making your workflow more efficient and productive.
How to Display SolidWorks Skills on Your Resume
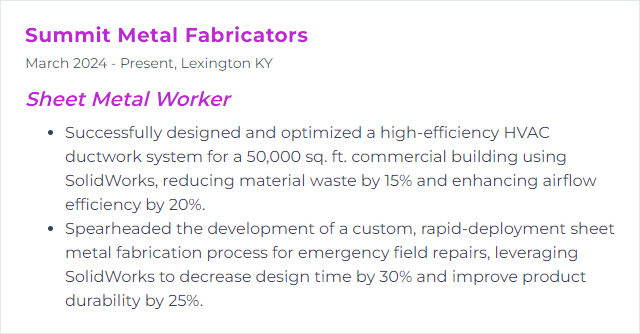
3. TIG Welding
TIG welding, or Tungsten Inert Gas welding, is a precise welding technique using a tungsten electrode to produce high-quality, clean welds on a variety of metals, ideal for thin sheet metal work.
Why It's Important
TIG welding is crucial for sheet metal workers due to its precision, versatility in welding various metals (including thin materials), and ability to produce clean, high-quality welds with minimal distortion, essential for the aesthetics and integrity of sheet metal projects.
How to Improve TIG Welding Skills
Improving TIG welding, especially for a sheet metal worker, involves practice, understanding the fundamentals, and applying best practices consistently. Here are concise tips:
Proper Preparation: Ensure surfaces are clean and free of contaminants. Use a stainless-steel brush for cleaning and acetone for degreasing. Cleaning Tips
Equipment Setup: Choose the right tungsten electrode and grind it to a point. Adjust your welding machine settings according to the thickness of the metal. Tungsten Electrode Guide
Correct Technique: Maintain a consistent angle (about 15-20 degrees) between the electrode and the workpiece. Keep a steady hand and use a filler rod only when necessary. Technique Improvement
Practice: Work on different joints and positions. Start with flat positions and progress to vertical and overhead. Practice Projects
Safety: Always wear appropriate PPE, including a welding helmet with the correct shade, gloves, and protective clothing. Safety Gear
By focusing on these areas, a sheet metal worker can significantly improve their TIG welding skills, leading to cleaner, stronger welds.
How to Display TIG Welding Skills on Your Resume
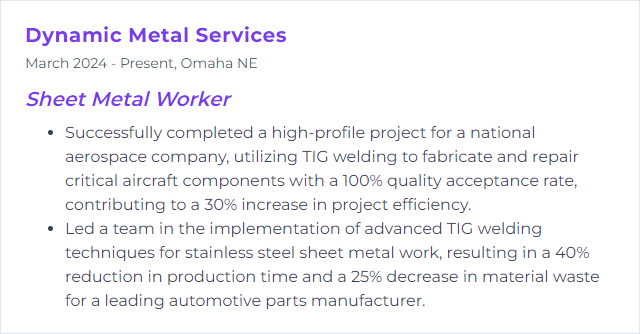
4. MIG Welding
MIG Welding, for a Sheet Metal Worker, is a fast and versatile welding process where an electric arc forms between a consumable wire electrode and the workpiece, melting the metals and joining them as the wire is continuously fed through a welding gun. It's particularly useful for efficiently welding a wide range of metals and thicknesses in sheet metal fabrication.
Why It's Important
MIG welding is crucial for a sheet metal worker because it allows for efficient, strong, and versatile joins in various types and thicknesses of metal, enhancing productivity and ensuring durability in metal fabrications.
How to Improve MIG Welding Skills
Improving MIG welding, especially for sheet metal workers, involves focusing on technique, equipment settings, and proper preparation. Here are concise tips:
Proper Equipment Setup: Ensure your MIG welder is correctly set up for the thickness of the metal you're working with. Use Lincoln Electric's guide for setting up your machine.
Correct Wire and Gas Selection: Choose the right wire type and size for your project. For sheet metal, thinner wire like 0.023” is often better. Also, use a gas mixture that’s appropriate for your metal type, such as 75% Argon and 25% CO2 for steel. Miller Welds provides an in-depth look at wire and gas selection.
Maintain Proper Technique: Keep a consistent travel speed and angle. For thin metals, a push technique can help reduce burn-through. Welding Tips and Tricks offers practical advice on technique.
Control Heat Input: Use lower voltage and amperage settings to prevent warping or burning through. Pulse welding can also be beneficial for controlling heat input on thin metals.
Clean and Prepare Surfaces: Ensure your workpiece is clean and free of any coatings or oxides before welding. This improves weld quality and reduces defects.
Practice and Experiment: Practice different settings and techniques on scrap metal. Experimenting helps you understand how changes affect your welds and improves your skill over time.
Safety First: Always wear appropriate safety gear, including a welding helmet with the correct shade, gloves, and protective clothing. Safety practices are crucial for preventing accidents and health hazards.
By focusing on these areas, sheet metal workers can significantly improve their MIG welding results.
How to Display MIG Welding Skills on Your Resume
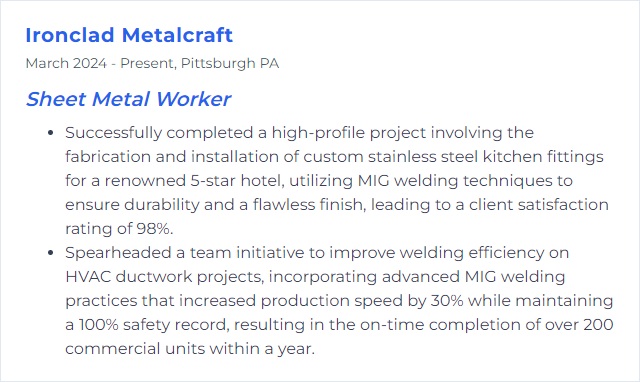
5. Plasma Cutting
Plasma cutting is a process used by sheet metal workers to cut through metal materials by using a plasma torch. This method involves blowing a gas at high speed out of a nozzle while an electrical arc is formed through that gas from the nozzle to the surface being cut, turning some of the gas to plasma. The plasma is hot enough to melt the metal being cut and moves sufficiently fast to blow molten metal away from the cut.
Why It's Important
Plasma cutting is crucial for a Sheet Metal Worker as it provides a fast, precise, and efficient method to cut through various types of metal, including thick and thin sheets, enabling intricate shapes and designs with minimal waste and high-quality edges, significantly enhancing productivity and versatility in metal fabrication tasks.
How to Improve Plasma Cutting Skills
To improve plasma cutting as a sheet metal worker, follow these concise tips:
Select the Right Consumables: Choose the appropriate cutting tips and electrodes for the material and thickness. Hypertherm's Guide offers insights on matching consumables to cutting needs.
Optimize Cutting Speed: Adjust the speed for the material and thickness. Too fast or too slow can affect cut quality. Lincoln Electric's Speed Guide provides a helpful starting point.
Maintain Correct Standoff Distance: Use a roller guide or CNC machine for consistent standoff distance. This Eastwood article explains the importance of standoff distance.
Use a Drag Shield: If your plasma cutter has one, a drag shield can help maintain optimal distance from the workpiece.
Ensure Proper Grounding: A good ground connection is crucial. Miller's Grounding Tips explain how to ensure a solid ground.
Regular Maintenance: Keep your equipment clean and replace consumables as needed. ESAB's Maintenance Checklist provides a detailed guide.
Control the Plasma Arc: For intricate cuts, control the plasma arc's direction with skillful hand movements or a CNC setup. Practice and experience play a significant role here.
Adjust Air Pressure: Follow manufacturer recommendations for air pressure settings based on material and thickness. Incorrect pressure can lead to poor cut quality.
Wear Proper Safety Gear: Protect eyes, ears, and skin from the intense light, noise, and heat generated by plasma cutting. OSHA's Safety Guidelines cover essential safety equipment.
By focusing on these areas, you can enhance the quality, efficiency, and safety of your plasma cutting processes.
How to Display Plasma Cutting Skills on Your Resume
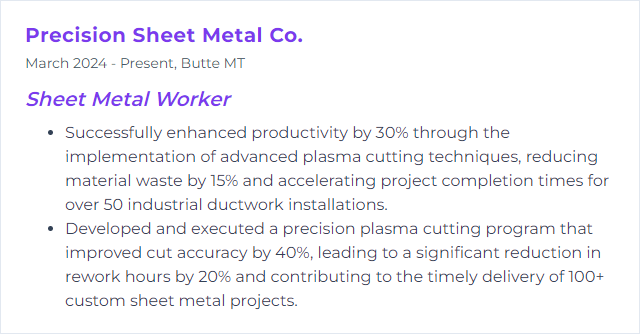
6. CNC Operation
CNC operation, in the context of a sheet metal worker, refers to the use of computer numerical control (CNC) machines to precisely cut, bend, or shape sheet metal according to digital designs.
Why It's Important
CNC operation is crucial for a Sheet Metal Worker because it allows for precise, efficient, and repeatable cutting, bending, and shaping of metal sheets, enhancing quality, productivity, and safety in metal fabrication processes.
How to Improve CNC Operation Skills
Improving CNC operation for a Sheet Metal Worker involves focusing on precision, efficiency, and safety. Here's a concise guide:
Understand Material Properties: Knowing the specifics of the materials you work with can significantly impact cutting speed, feed rate, and tool choice. The Fabricator provides a guide on material properties.
Optimize Tool Paths: Use software to plan and simulate the most efficient tool paths. This reduces machining time and tool wear. Autodesk has resources on optimizing tool paths.
Regular Maintenance: Keep your CNC machine well-maintained. This includes cleaning, lubrication, and checking for wear. Haas Automation offers maintenance tips.
Upgrade Software Regularly: Ensure that the CNC machine's software is up-to-date for new features and improved efficiency. CNC Software Maintenance from Mastercam.
Proper Training: Invest in regular training for operators to stay updated on the latest CNC technologies and techniques. Tooling U-SME offers CNC training courses.
Use Quality Tools: Invest in high-quality cutting tools and replace them before they become too worn. Sandvik Coromant has a selection of cutting tools.
Efficient Nesting: Use nesting software to maximize material usage and reduce waste. SigmaNEST is an example of such software.
Safety First: Ensure all safety protocols are followed to prevent accidents. OSHA provides guidelines for machine shop safety.
By focusing on these areas, sheet metal workers can enhance their CNC operation, leading to increased productivity and quality.
How to Display CNC Operation Skills on Your Resume
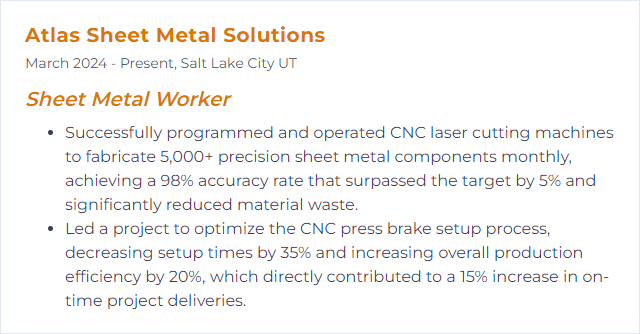
7. Precision Measuring
Precision measuring in the context of a Sheet Metal Worker involves the use of specialized tools (like calipers, micrometers, and gauges) to accurately determine the dimensions, thickness, and angles of metal sheets, ensuring cuts and bends meet specified tolerances and quality standards.
Why It's Important
Precision measuring is vital for a sheet metal worker because it ensures accuracy in cutting, bending, and assembling metal parts, leading to high-quality, fit-for-purpose products and minimizing waste and rework.
How to Improve Precision Measuring Skills
Improving precision in measuring for a Sheet Metal Worker involves a few key steps:
Use High-Quality Tools: Opt for high-precision tools like digital calipers, micrometers, and angle finders. Brands like Mitutoyo and Starrett are well-regarded.
Regular Calibration: Ensure your measuring tools are regularly calibrated to maintain accuracy.
Understand Material Properties: Familiarize yourself with the properties of different metals. The ASM International provides resources on material properties and their impact on precision work.
Practice Proper Technique: Use consistent pressure and angles while measuring. ThomasNet offers tips on using calipers effectively.
Maintain a Clean Workspace: Keep your tools and workspace clean to avoid any measurement errors due to debris or damage. OSHA provides guidelines for maintaining a safe and clean working environment.
By focusing on quality tools, regular calibration, understanding materials, practicing proper technique, and maintaining a clean workspace, a Sheet Metal Worker can significantly improve their precision in measuring tasks.
How to Display Precision Measuring Skills on Your Resume
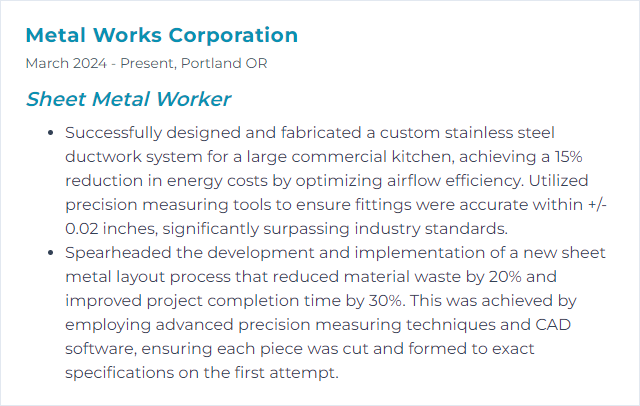
8. Brake Press Operation
Brake press operation, in the context of a sheet metal worker, involves using a brake press machine to bend or shape sheet metal into desired forms or angles by applying force through a punch and die mechanism.
Why It's Important
Brake press operation is crucial for a Sheet Metal Worker as it allows for precise bending and shaping of metal sheets into desired forms and angles, essential for creating accurate and high-quality components in construction and manufacturing.
How to Improve Brake Press Operation Skills
Improving brake press operation involves enhancing safety, precision, and efficiency. Here are key strategies tailored for a sheet metal worker:
Safety First: Always adhere to safety protocols. Use personal protective equipment (PPE) and ensure safety guards are in place and functional. Regular training on safety practices is crucial. Occupational Safety and Health Administration (OSHA) provides guidelines on machine safety.
Proper Training: Comprehensive training on brake press operation, including understanding machine specifics, material handling, and software use, is essential. Manufacturers often provide training resources. Fabricators & Manufacturers Association Intl. (FMA) offers courses and certifications.
Regular Maintenance: Keep the brake press well-maintained to ensure accuracy and longevity. This includes checking hydraulic fluids, tool alignment, and punch and die conditions. Machinery Lubrication offers insights on maintenance practices.
Tool and Die Selection: Use the correct tools and dies for the material and job. This reduces wear and improves bending accuracy. The Fabricator provides guides on tool selection and usage.
Programming Skills: Enhance programming skills for CNC brake presses to improve efficiency and precision. Understanding software options and updates can significantly impact operation quality. LVD Group and other manufacturers offer software tutorials and support.
Material Preparation: Ensure materials are properly prepared and positioned. This includes cleaning, deburring, and correct placement to reduce errors and rework.
Process Optimization: Continuously review and optimize processes. Lean manufacturing principles can be applied to reduce waste and increase throughput. Lean Enterprise Institute offers resources for lean manufacturing.
By focusing on these areas, a sheet metal worker can significantly improve brake press operation, enhancing both productivity and quality.
How to Display Brake Press Operation Skills on Your Resume
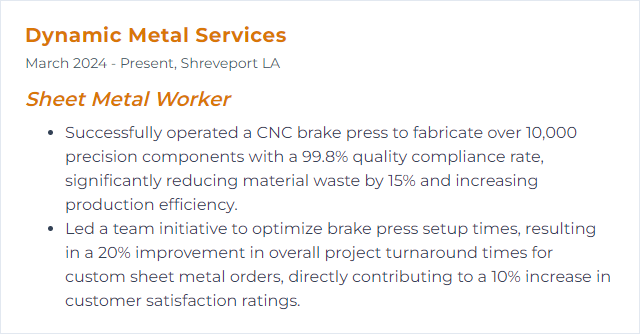
9. Shearing Machines
Shearing machines are tools used by sheet metal workers to cut large sheets of metal precisely and efficiently without forming chips or using heat. These machines utilize a stationary blade and a moving blade to apply shear force and slice the metal into desired sizes or shapes.
Why It's Important
Shearing machines are crucial for sheet metal workers because they efficiently and precisely cut large sheets of metal to size, facilitating the fabrication of various metal components and structures.
How to Improve Shearing Machines Skills
To enhance shearing machines for sheet metal workers, focus on the following aspects:
Upgrade Blades: Install high-quality, durable blades that require less maintenance. Consider materials like high-speed steel for longer life and better performance. Tool Materials.
Enhance Precision: Implement CNC (Computer Numerical Control) technology to improve accuracy and repeatability of cuts. CNC systems can significantly reduce errors and waste. CNC Integration.
Safety Features: Upgrade with advanced safety features like light curtains and emergency stop buttons to protect operators from accidents. Safety Systems.
Regular Maintenance: Establish a routine maintenance schedule to ensure the machine operates at optimal efficiency, which includes lubrication, blade sharpening, and component checks. Maintenance Tips.
Operator Training: Provide comprehensive training for operators on the latest techniques and safety practices to enhance productivity and safety. Training Resources.
Automation: Consider integrating automation for material handling to increase throughput and reduce the physical strain on operators. Automation in Metal Fabricating.
Improving shearing machines involves a combination of upgrading hardware, implementing advanced technologies, prioritizing safety, conducting regular maintenance, educating operators, and embracing automation.
How to Display Shearing Machines Skills on Your Resume
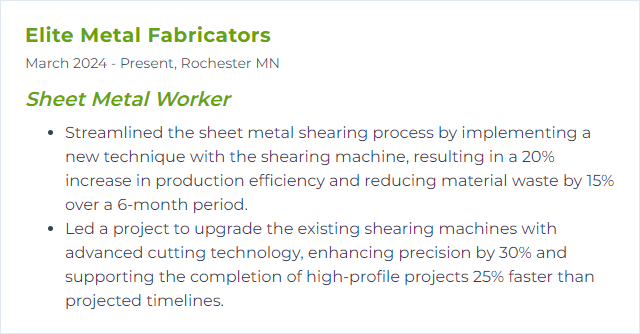
10. Riveting Techniques
Riveting techniques in the context of a sheet metal worker involve the process of joining two pieces of metal together using rivets, which are metal pins or bolts. The process includes drilling or punching holes in the metal pieces, inserting the rivet through the aligned holes, and then deforming the rivet's tail to secure the pieces together. Common techniques include solid riveting, where the tail is deformed with a hammer or rivet gun, and pop riveting, using a specially designed tool to pull and snap off a mandrel, leaving a tight joint. These techniques are essential for creating strong, permanent joints in metal structures or components.
Why It's Important
Riveting techniques are crucial for a Sheet Metal Worker because they provide a strong, durable method for joining metal sheets together without melting the base material, ensuring structural integrity and longevity in construction and repair tasks.
How to Improve Riveting Techniques Skills
Improving riveting techniques for a sheet metal worker involves focusing on precision, tool maintenance, and continual learning. Here are concise tips:
Use the Correct Rivet Size and Material: Match rivet size and material to the job for optimal strength and durability. Rivet Sizing Guide.
Maintain Your Tools: Regularly inspect and maintain your riveting tools to ensure they perform efficiently. Clean and lubricate them as needed. Tool Maintenance Tips.
Practice Proper Technique: Ensure you're using the correct technique for your type of rivet. This includes proper hole sizing, alignment, and rivet setting. Riveting Techniques.
Use the Right Amount of Force: Applying the correct amount of force will ensure a tight fit without damaging the materials or the rivet.
Inspect Your Work: Regularly check your rivets for consistency and quality to prevent future failures.
Stay Informed and Trained: Continuously learn about new materials, tools, and techniques in riveting. Professional Development Resources.
By focusing on these key aspects, sheet metal workers can significantly improve their riveting techniques, leading to higher quality and more durable metal fabrications.
How to Display Riveting Techniques Skills on Your Resume
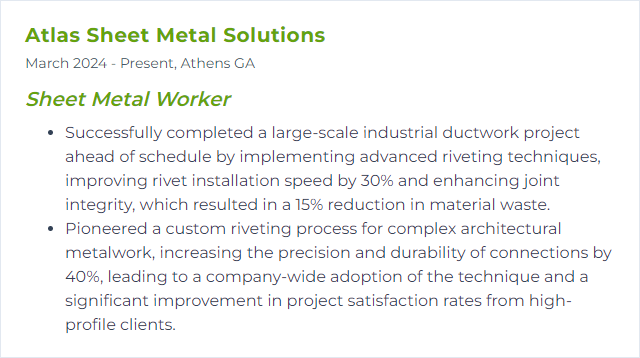
11. Sheet Metal Layout
Sheet metal layout is the process a sheet metal worker uses to plan and mark the cutting and bending lines on a flat sheet of metal before it is cut, formed, or fabricated into its final shape. This layout guides the precise shaping of the metal to fit specific design requirements.
Why It's Important
Sheet metal layout is crucial for a Sheet Metal Worker because it ensures accuracy in cutting and forming processes, minimizes material waste, and optimizes fabrication efficiency, leading to quality finished products and cost savings.
How to Improve Sheet Metal Layout Skills
Improving sheet metal layout involves enhancing precision, efficiency, and material utilization. Here are concise strategies for a Sheet Metal Worker:
Use CAD Software: Adopt Computer-Aided Design (CAD) tools to create accurate and detailed layouts. This reduces errors and allows for easy adjustments.
Optimize Material Use: Implement nesting software to arrange parts in a way that minimizes waste, saving on material costs.
Standardize Processes: Develop standard operating procedures for common tasks to ensure consistency and efficiency.
Continuous Learning: Stay updated with the latest techniques and technologies in sheet metal work through resources like The Fabricator.
Quality Tools: Invest in high-quality tools and equipment to enhance precision and speed in your layouts.
By focusing on technology adoption, process optimization, and continuous improvement, you can significantly enhance your sheet metal layout processes.
How to Display Sheet Metal Layout Skills on Your Resume
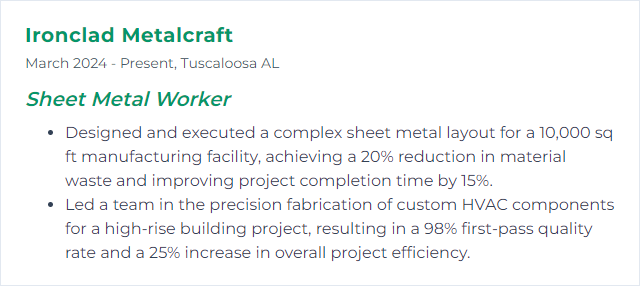
12. HVAC Systems
HVAC systems (Heating, Ventilation, and Air Conditioning) are essential climate control systems designed to regulate the temperature, humidity, and air quality in buildings. For a Sheet Metal Worker, these systems often involve fabricating, installing, and repairing the metal ductwork that channels air throughout the facility.
Why It's Important
HVAC systems are essential because they regulate indoor temperature, humidity, and air quality, ensuring a comfortable and safe environment. For a Sheet Metal Worker, installing and maintaining these systems is crucial for the efficient operation and longevity of buildings, providing vital expertise in fabricating and installing ductwork that is integral to the system's overall performance.
How to Improve HVAC Systems Skills
Improving HVAC systems, especially from a sheet metal worker's perspective, revolves around optimizing airflow, enhancing energy efficiency, and ensuring the durability and integrity of the ductwork. Here are concise strategies:
Enhance Ductwork Efficiency: Ensure all ductwork is properly sealed and insulated to minimize energy loss. Use high-quality, durable materials that match the specific requirements of the HVAC system. Energy Star has valuable guidelines on duct sealing and insulation.
Optimize Airflow: Design and install ductwork that facilitates smooth, unobstructed airflow. This includes considering the size, shape, and layout of ducts to eliminate unnecessary bends and length, which can reduce efficiency. ASHRAE offers resources and standards for HVAC system design and airflow optimization.
Incorporate Automation: Utilize automated dampers and zoning systems to improve the control and efficiency of HVAC systems. These technologies help in directing airflow more effectively and maintaining consistent temperatures throughout the premises. The Sheet Metal and Air Conditioning Contractors’ National Association (SMACNA) provides insights into the latest technologies and practices in HVAC systems.
Regular Maintenance and Cleaning: Encourage routine maintenance and cleaning of HVAC systems to ensure they operate at peak efficiency. This includes checking for leaks, cleaning filters, and ensuring that vents are not obstructed. National Air Duct Cleaners Association (NADCA) highlights the importance of maintenance in improving airflow and system efficiency.
Install Energy-Efficient Components: Recommend the use of energy-efficient HVAC components, such as high-efficiency filters, fans, and motors. This not only improves the system's performance but also contributes to energy savings. ENERGY STAR offers a list of certified energy-efficient HVAC products.
By focusing on these areas, sheet metal workers can significantly contribute to the efficiency, sustainability, and performance of HVAC systems.
How to Display HVAC Systems Skills on Your Resume
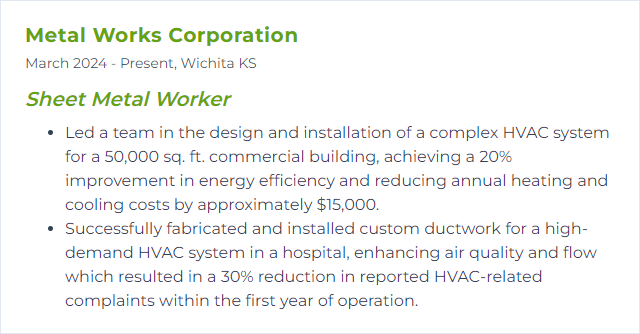