Top 12 Quality Control Technician Skills to Put on Your Resume
In the competitive field of quality control, showcasing the right blend of technical skills and personal attributes on your resume can significantly enhance your marketability to potential employers. This article outlines the top 12 skills every quality control technician should include on their resume, emphasizing the importance of a comprehensive skill set that combines technical expertise with critical soft skills for success in this crucial industry role.
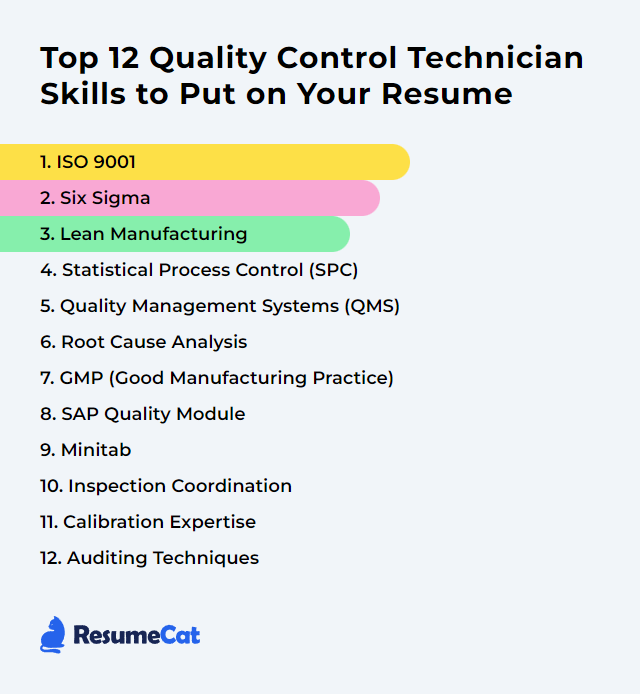
Quality Control Technician Skills
- ISO 9001
- Six Sigma
- Lean Manufacturing
- Statistical Process Control (SPC)
- Quality Management Systems (QMS)
- Root Cause Analysis
- GMP (Good Manufacturing Practice)
- SAP Quality Module
- Minitab
- Inspection Coordination
- Calibration Expertise
- Auditing Techniques
1. ISO 9001
ISO 9001 is an international standard that specifies requirements for a quality management system (QMS), ensuring consistent quality in products and services and continuous improvement, relevant for a Quality Control Technician to guide and measure quality control processes and practices.
Why It's Important
ISO 9001 is important because it ensures consistent quality in products and services, leading to higher customer satisfaction and continuous improvement in processes, which are crucial for a Quality Control Technician's work in maintaining and enhancing product quality and operational efficiency.
How to Improve ISO 9001 Skills
To improve ISO 9001 as a Quality Control Technician, focus on the following steps:
Understand the Standard: Thoroughly understand ISO 9001 requirements. The ISO Organization provides resources and guides.
Engage in Training: Participate in ISO 9001 training courses to enhance your knowledge and skills. Check out resources like ASQ for relevant courses.
Implement a Quality Management System (QMS): Develop or enhance your organization's QMS focusing on continuous improvement, customer satisfaction, and adherence to the standard. The ISO 9001 Checklist can guide you through the necessary steps.
Conduct Internal Audits: Regularly perform internal audits to identify areas for improvement. ISO 19011 guidelines can help in conducting effective audits.
Gather and Analyze Data: Use quality control data to identify trends, issues, and areas for improvement. Tools and techniques like Six Sigma can be particularly effective, as highlighted by resources like iSixSigma.
Engage with Suppliers: Ensure your suppliers understand and meet ISO 9001 requirements, as their performance directly impacts your quality. The ISO 9001 Supply Chain Guide offers insights on managing supplier relationships.
Continuous Improvement: Adopt the Plan-Do-Check-Act (PDCA) cycle for continuous improvement in all processes. The ASQ’s PDCA Cycle guide provides a detailed approach.
Customer Feedback: Actively seek and incorporate customer feedback to improve product quality and customer satisfaction.
Employee Training and Involvement: Ensure all employees are trained on ISO 9001 principles and are involved in the QMS process. This enhances overall compliance and improvement.
Stay Updated: ISO standards evolve, so stay informed about the latest updates and best practices through official ISO communications and quality management forums.
By focusing on these steps, a Quality Control Technician can significantly contribute to improving an organization’s ISO 9001 compliance and overall quality performance.
How to Display ISO 9001 Skills on Your Resume
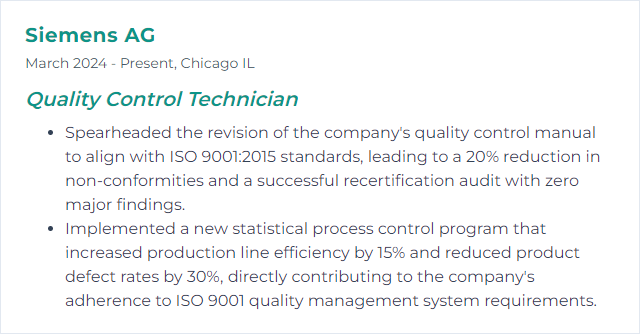
2. Six Sigma
Six Sigma is a data-driven methodology and set of tools aimed at process improvement by identifying and eliminating defects to enhance quality control and operational efficiency.
Why It's Important
Six Sigma is important for a Quality Control Technician because it provides a systematic approach to reducing defects, improving processes, and enhancing product quality, thereby ensuring customer satisfaction and cost savings for the organization.
How to Improve Six Sigma Skills
Improving Six Sigma as a Quality Control Technician involves continuous learning, practical application, and leveraging technology. Here are concise steps to enhance your Six Sigma skills:
Enhance Your Knowledge Base: Continually update your Six Sigma methodologies and tools knowledge. Participate in Six Sigma certification programs at various levels (Yellow Belt, Green Belt, Black Belt, Master Black Belt).
Apply Six Sigma in Real-world Scenarios: Implement Six Sigma projects within your organization. This practical application helps in understanding the nuances and complexities better. iSixSigma Case Studies provide real-world examples across industries.
Use Statistical Software: Become proficient in statistical analysis software like Minitab, which is widely used in Six Sigma projects for data analysis.
Participate in Six Sigma Forums and Communities: Engage with other professionals through forums and communities. The iSixSigma Discussion Forum is a good place to start.
Stay Updated with Quality Control Technologies: Embrace new technologies and methodologies that can streamline Six Sigma processes. This includes learning about automation tools and quality control software.
Continuous Improvement: Adopt the Kaizen philosophy of continuous improvement in your work and Six Sigma practices. This mindset fosters ongoing personal and professional development.
By focusing on these areas, a Quality Control Technician can significantly improve their effectiveness in applying Six Sigma methodologies.
How to Display Six Sigma Skills on Your Resume
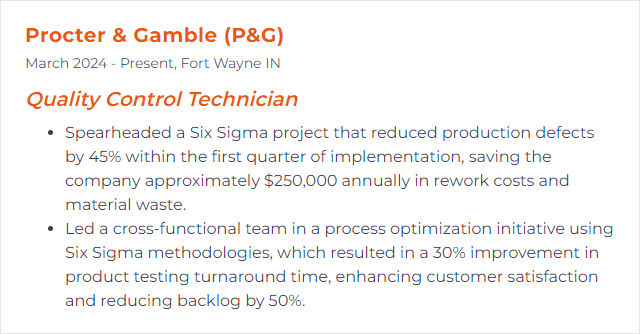
3. Lean Manufacturing
Lean Manufacturing is a systematic approach aimed at minimizing waste and maximizing efficiency in the production process, focusing on enhancing product quality and customer satisfaction. For a Quality Control Technician, it involves rigorous attention to detail to identify and eliminate defects and non-value-added activities, ensuring the production of high-quality products with fewer resources.
Why It's Important
Lean Manufacturing is important for a Quality Control Technician because it focuses on reducing waste and improving process efficiency, leading to higher quality products, lower costs, and increased customer satisfaction.
How to Improve Lean Manufacturing Skills
Improving Lean Manufacturing, especially from a Quality Control Technician perspective, involves focusing on waste reduction, quality enhancement, and continuous improvement. Here are concise strategies:
Implement Kaizen: Encourage continuous, incremental improvements in the manufacturing process. Kaizen helps in identifying and eliminating waste, leading to more efficient production processes.
Utilize 5S Methodology: Organize and maintain a clean, efficient workspace. 5S (Sort, Set in order, Shine, Standardize, Sustain) improves safety, work efficiency, and product quality.
Adopt Poka-Yoke Techniques: Implement error-proofing methods to reduce defects. Poka-Yoke ensures that the right conditions exist before a process step is executed, preventing errors.
Apply Six Sigma Principles: Focus on reducing process variation and improving product quality. Integrating Six Sigma with lean manufacturing can lead to significant quality and efficiency improvements.
Engage in Value Stream Mapping: Analyze and design the flow of materials and information required to bring a product to a customer. Value Stream Mapping helps identify waste and opportunities for improvement in the production process.
Regularly Conduct Gemba Walks: Walk the shop floor to observe the actual work process, engage with employees, and identify inefficiencies. Gemba Walks can uncover issues not apparent from afar and foster a culture of continuous improvement.
Foster a Culture of Quality: Encourage every employee to take responsibility for quality control. A quality culture ensures that quality is not just the domain of inspectors or technicians but a shared responsibility.
Implementing these strategies requires a commitment to continuous improvement and a proactive approach to identifying and solving quality and efficiency issues in the manufacturing process.
How to Display Lean Manufacturing Skills on Your Resume
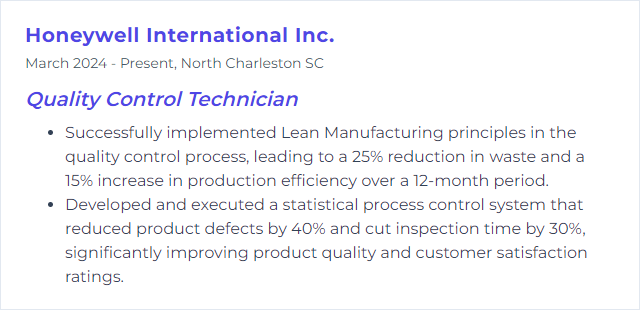
4. Statistical Process Control (SPC)
Statistical Process Control (SPC) is a method used by Quality Control Technicians to monitor and control a process to ensure it operates at its fullest potential. By using statistical techniques to analyze data, SPC identifies trends, variations, and signals that indicate deviations from the intended process performance, enabling proactive quality control and continuous improvement.
Why It's Important
Statistical Process Control (SPC) is crucial for a Quality Control Technician because it enables the monitoring and control of process variations, ensuring product quality consistency and minimizing defects, leading to improved operational efficiency and customer satisfaction.
How to Improve Statistical Process Control (SPC) Skills
Improving Statistical Process Control (SPC) involves a few key steps aimed at enhancing quality control processes. Here’s a concise guide:
Educate and Train: Ensure all team members understand SPC fundamentals and tools. ASQ offers a comprehensive overview of SPC.
Select Appropriate Tools: Use the right SPC tools (e.g., control charts, Pareto charts) for your specific processes. The NISS website provides insights into various statistical methods.
Data Quality: Collect high-quality, relevant data. Accurate data collection is foundational to effective SPC. The Data Quality Campaign offers strategies for improving data quality.
Continuous Monitoring: Regularly monitor processes using SPC charts to detect any variations. MoreSteam provides practical tips on continuous monitoring.
Root Cause Analysis: When variations occur, use root cause analysis to identify and address the underlying causes. MindTools outlines techniques for effective root cause analysis.
Implement Corrective Actions: Based on your analysis, implement corrective actions to improve processes. The ASQ offers resources on corrective action processes.
Continuous Improvement: Adopt a culture of continuous improvement (Kaizen). The Kaizen Institute provides insights into implementing continuous improvement strategies.
By focusing on education, selecting the right tools, ensuring data quality, monitoring continuously, analyzing root causes, implementing corrective actions, and fostering a culture of continuous improvement, Quality Control Technicians can significantly enhance their SPC efforts.
How to Display Statistical Process Control (SPC) Skills on Your Resume
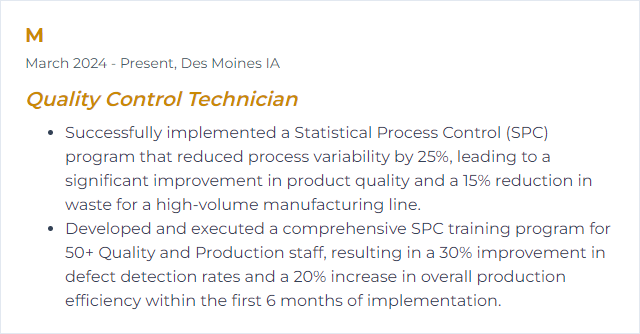
5. Quality Management Systems (QMS)
A Quality Management System (QMS) is a structured framework of procedures and processes designed to ensure that products and services meet customer expectations and comply with regulatory requirements, focusing on continuous improvement. For a Quality Control Technician, a QMS guides daily tasks to monitor and verify product quality and process effectiveness, ensuring standards are consistently met.
Why It's Important
Quality Management Systems (QMS) are vital because they ensure consistency, efficiency, and compliance in production processes, directly impacting product quality. For a Quality Control Technician, a QMS provides clear guidelines and tools for monitoring, inspecting, and improving product quality, reducing errors, and enhancing customer satisfaction.
How to Improve Quality Management Systems (QMS) Skills
Improving a Quality Management System (QMS) involves a continuous process of assessment, feedback, and refinement to ensure the highest standards of quality are met. For a Quality Control Technician focusing on practical steps, here are concise strategies:
Conduct Regular Audits: Regularly auditing your QMS can identify areas of non-compliance and opportunities for improvement. ASQ provides guidelines on how to effectively conduct audits.
Engage in Continuous Training: Ensure all team members, especially those in quality control, are continuously trained on the latest quality standards and practices. Training resources can be found at Coursera.
Implement Corrective and Preventive Actions (CAPA): When issues are identified, promptly implement corrective actions and, equally important, preventive measures to avoid recurrence. Guidelines on CAPA can be explored through FDA’s CAPA Guidance.
Utilize Quality Management Software: Invest in quality management software to streamline processes, improve documentation, and enhance data analysis. An overview of software options is available at Capterra.
Foster a Culture of Quality: Encourage a company-wide culture that prioritizes quality at every level and in every process. Insights on building this culture can be found on ISO’s page.
Customer Feedback Integration: Actively seek and integrate customer feedback into your QMS for continuous improvement. Methods and strategies for this can be learned through Harvard Business Review’s article on customer feedback.
Benchmarking and Best Practices: Compare your processes and performance against industry leaders to identify areas for improvement. APQC offers resources for benchmarking and identifying best practices.
Regular Review and Update of QMS Documentation: Keep all QMS documentation up-to-date to ensure compliance and efficiency. Guidance on managing QMS documentation can be found at ISO.
By applying these strategies, a Quality Control Technician can significantly contribute to enhancing the effectiveness and efficiency of a Quality Management System.
How to Display Quality Management Systems (QMS) Skills on Your Resume
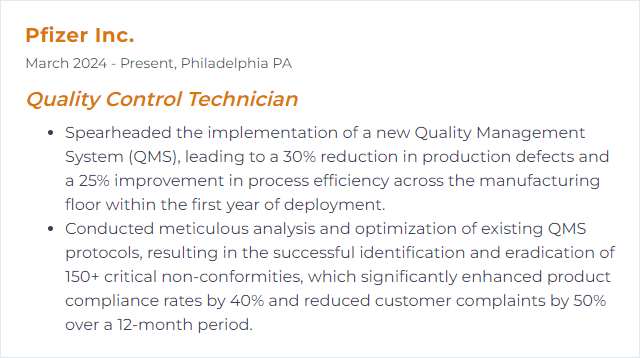
6. Root Cause Analysis
Root Cause Analysis (RCA) is a systematic process used by Quality Control Technicians to identify the underlying reasons for defects or problems in products or processes, aiming to implement solutions that prevent recurrence.
Why It's Important
Root Cause Analysis (RCA) is crucial for a Quality Control Technician as it allows for the identification and resolution of the underlying issues causing defects or failures in products or processes, ensuring the delivery of high-quality products and the improvement of production efficiency.
How to Improve Root Cause Analysis Skills
Improving Root Cause Analysis (RCA) involves a systematic approach to identify the true source of a problem and addressing it rather than merely treating the symptoms. For a Quality Control Technician, enhancing the effectiveness of RCA can significantly improve product quality and process efficiency. Here are concise steps to improve RCA:
Define the Problem Clearly: Start with a precise definition of the issue, focusing on what is observed, including discrepancies in product quality or process failures. ASQ’s problem statement guide is a helpful resource.
Gather Data: Collect data related to the problem's occurrence, including when, where, and under what conditions the issue arises. This can involve reviewing production data, quality control reports, and machine logs.
Use RCA Tools: Employ RCA tools such as the 5 Whys, Fishbone Diagram (Ishikawa), and Pareto Analysis to drill down to the root cause. The Mind Tools Fishbone Diagram Guide offers a straightforward explanation on how to use this technique.
Identify Potential Causes: List possible causes for the problem. Be thorough and consider all factors, including human, method, materials, machines, and environment.
Analyze and Prioritize Causes: Evaluate the likelihood of each cause contributing to the problem. Tools like Pareto charts can help prioritize issues based on their impact. Refer to Pareto Analysis by ASQ for a deeper understanding.
Develop and Implement Solutions: Propose solutions to address the root causes. These should be actionable, measurable, and capable of preventing recurrence. Implement the solutions while monitoring for effectiveness.
Verify Solution Effectiveness: After implementation, verify if the solution effectively addresses the root cause without introducing new problems. Continuous monitoring and feedback are vital.
Document: Throughout the process, document findings, actions taken, and outcomes. This not only provides a record for future reference but also helps in sharing knowledge across the organization.
For continuous improvement in RCA, Quality Control Technicians should seek feedback, engage in regular training, and stay updated with best practices in quality management and problem-solving techniques.
How to Display Root Cause Analysis Skills on Your Resume
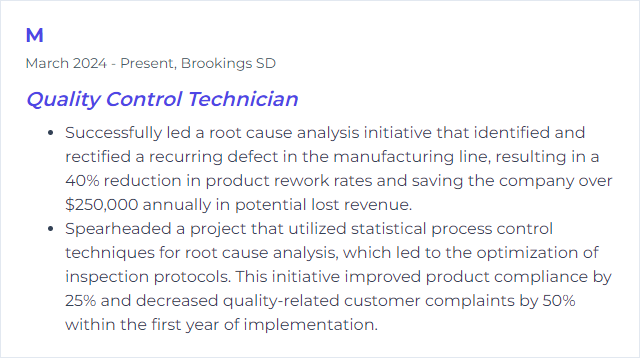
7. GMP (Good Manufacturing Practice)
GMP (Good Manufacturing Practice) refers to a set of guidelines ensuring products are consistently produced and controlled according to quality standards. For a Quality Control Technician, it involves adhering to procedures that guarantee the identity, strength, quality, and purity of products by monitoring manufacturing processes, validating equipment and processes, and conducting rigorous testing and inspection of materials and products.
Why It's Important
GMP ensures products are consistently produced and controlled to quality standards, minimizing risks such as contamination, mix-ups, and errors, critical for a Quality Control Technician to guarantee product safety and efficacy.
How to Improve GMP (Good Manufacturing Practice) Skills
Improving GMP (Good Manufacturing Practice) involves enhancing the efficiency, compliance, and quality assurance processes in manufacturing. For a Quality Control Technician, focusing on the following aspects can lead to significant improvements:
Continuous Training: Ensure ongoing training programs for staff to stay updated on the latest GMP guidelines and quality control techniques.
Regular Audits: Conduct regular audits of manufacturing processes to identify and rectify non-compliance issues.
Documentation: Improve documentation practices, ensuring accuracy and completeness. This includes batch records, test results, and quality control procedures. The FDA provides guidance on documentation.
Equipment Maintenance: Implement a strict maintenance schedule for equipment to ensure they are functioning correctly and producing quality products.
Quality Control Tests: Enhance the reliability and frequency of quality control testing to ensure products meet the required standards consistently.
Feedback Loop: Establish a robust feedback mechanism between quality control, manufacturing, and warehouse departments to quickly address any GMP-related issues.
Improving GMP is a continuous process that requires commitment and attention to detail. By focusing on these areas, a Quality Control Technician can significantly contribute to the overall quality and compliance of the manufacturing process.
How to Display GMP (Good Manufacturing Practice) Skills on Your Resume
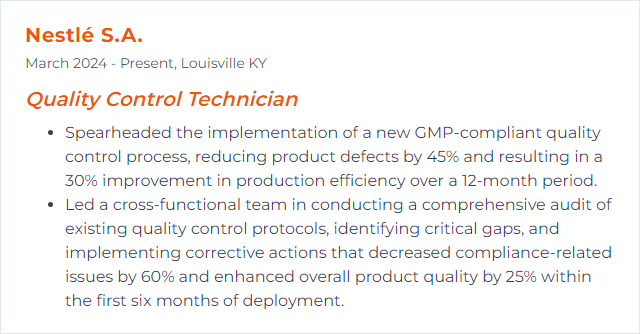
8. SAP Quality Module
The SAP Quality Module, also known as SAP QM (Quality Management), is a component of the SAP ERP system that supports various aspects of quality management. For a Quality Control Technician, it facilitates tasks related to planning, executing, and recording quality control processes, inspections, and tests on materials and products to ensure compliance with quality standards and specifications.
Why It's Important
The SAP Quality Module is essential for a Quality Control Technician as it streamlines quality management processes, ensures compliance with industry standards, enables efficient defect tracking and resolution, and facilitates continuous improvement in product quality and safety.
How to Improve SAP Quality Module Skills
Improving the SAP Quality Module for a Quality Control Technician involves several steps focused on optimizing processes, enhancing data quality, and leveraging advanced features. Here's a brief guide:
Enhance Data Quality: Ensure that master data (material master, inspection plans, etc.) is accurate and up-to-date. This improves reliability in quality processes. SAP Master Data Governance can be a useful tool.
Automate Processes: Use the Quality Management (QM) module to automate routine tasks, such as generating quality certificates or triggering inspections. This increases efficiency and reduces human error. SAP QM Automation offers guidance.
Implement Quality Notifications: Leverage the quality notification feature to track defects, customer complaints, and internal problems. This facilitates faster resolution and continuous improvement. SAP Quality Notifications provides detailed information.
Utilize Reporting and Analytics: Use SAP's reporting tools to analyze quality data, identify trends, and make informed decisions. SAP Business Warehouse and SAP Analytics Cloud offer comprehensive analytics capabilities. SAP Analytics Cloud is a resource for advanced analytics.
Continuous Training: Ensure that all users, especially Quality Control Technicians, receive ongoing training on new features, best practices, and process optimizations within the QM module. SAP Training and Certification can help in staying updated.
Engage with SAP Community: Join the SAP QM community to share experiences, challenges, and solutions with peers. This can provide valuable insights and practical tips. SAP Community is a platform for engagement.
By focusing on these areas, a Quality Control Technician can significantly improve the efficiency and effectiveness of the SAP Quality Module within their organization.
How to Display SAP Quality Module Skills on Your Resume
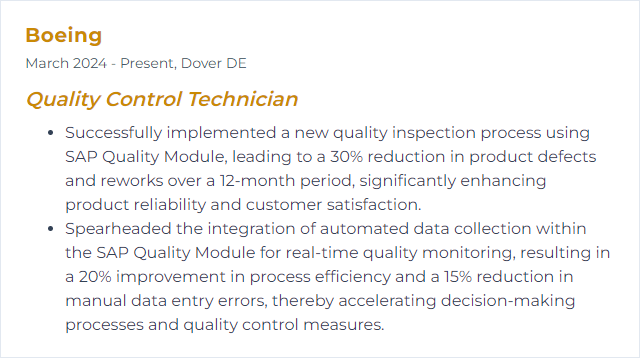
9. Minitab
Minitab is a statistical software tool used for data analysis, particularly useful for Quality Control Technicians in monitoring and improving manufacturing processes through statistical process control, hypothesis testing, and process optimization.
Why It's Important
Minitab is important for a Quality Control Technician because it provides powerful statistical analysis tools to monitor, improve, and control manufacturing processes, ensuring product quality and consistency.
How to Improve Minitab Skills
Improving your proficiency with Minitab as a Quality Control Technician involves a combination of expanding your statistical knowledge, harnessing the power of Minitab's features, and integrating best practices into your workflow. Here’s a concise guide:
Enhance Statistical Knowledge: A strong foundation in statistics will help you make the most of Minitab's capabilities. Consider resources like Khan Academy's Statistics and Probability for a free way to build your knowledge.
Master Minitab Features: Dive deep into Minitab's wide array of features. Focus on mastering tools that are most relevant to Quality Control, such as Control Charts, Capability Analysis, and Regression Analysis. Minitab offers Quick Start Guides to help you get familiar with various functionalities.
Utilize Minitab Support: Take advantage of the Minitab Support page for tutorials, FAQs, and technical support. This can be particularly helpful for troubleshooting or learning new features.
Practice with Real Data: Apply what you've learned by practicing with real or simulated quality control data. This hands-on experience is invaluable and will improve your proficiency with the software.
Join Minitab User Community: Engage with the Minitab User Community to exchange knowledge, tips, and best practices with other Quality Control professionals. Sharing experiences can provide new insights and techniques.
Continuous Learning: Stay updated with new features and best practices by subscribing to Minitab Blog, which provides helpful articles, case studies, and tips for users across various proficiency levels.
By following these steps, you can significantly improve your Minitab skills, thereby enhancing your effectiveness and efficiency as a Quality Control Technician.
How to Display Minitab Skills on Your Resume
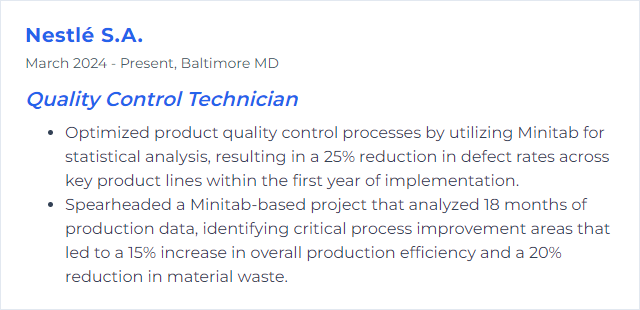
10. Inspection Coordination
Inspection Coordination, in the context of a Quality Control Technician, involves organizing and overseeing the process of evaluating products, components, or materials against defined standards to ensure they meet quality specifications. This includes scheduling inspections, ensuring the right tools and criteria are used, and coordinating with relevant teams to address any identified issues.
Why It's Important
Inspection coordination is crucial for a Quality Control Technician as it ensures that all inspection activities are systematically organized and executed in a timely manner, leading to the consistent identification and rectification of defects, maintaining product quality, and meeting compliance standards.
How to Improve Inspection Coordination Skills
Improving Inspection Coordination as a Quality Control Technician involves enhancing the efficiency and effectiveness of inspection processes. Here are concise steps to achieve this:
Standardize Processes: Develop and adhere to standardized inspection protocols to ensure consistency. ASTM provides standards that can be adapted.
Leverage Technology: Utilize inspection software and tools for better scheduling, real-time data collection, and reporting. Tools like iAuditor can streamline these tasks.
Continuous Training: Ensure ongoing training programs for staff to stay updated with the latest inspection techniques and technologies. Online platforms like Coursera offer relevant courses.
Effective Communication: Establish clear communication channels among all stakeholders to facilitate the seamless flow of information. Tools like Slack can enhance team collaboration.
Feedback Mechanism: Implement a robust feedback system to learn from past inspections and continuously improve processes. Software like SurveyMonkey can be used for gathering feedback efficiently.
Pre-Inspection Planning: Allocate sufficient time for planning before each inspection to review standards, checklists, and ensure all necessary equipment is ready and calibrated.
Post-Inspection Review: Conduct reviews after each inspection to discuss findings, challenges, and areas for improvement, fostering a culture of continuous learning and development.
By focusing on these areas, a Quality Control Technician can significantly enhance the coordination and outcome of inspections, leading to improved product quality and compliance.
How to Display Inspection Coordination Skills on Your Resume
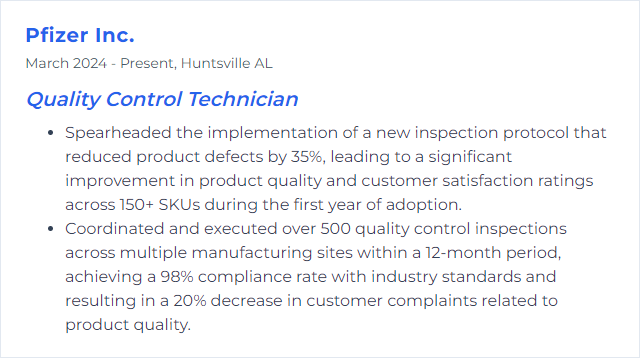
11. Calibration Expertise
Calibration expertise, for a Quality Control Technician, involves the skill and knowledge needed to accurately adjust, test, and certify the performance and measurements of instruments and equipment against known standards, ensuring they produce reliable and precise results in quality control processes.
Why It's Important
Calibration expertise is crucial for a Quality Control Technician because it ensures measuring instruments are accurate and reliable, guaranteeing product quality meets specified standards and regulatory requirements. This prevents errors, maintains consistency, and supports customer trust and safety.
How to Improve Calibration Expertise Skills
Improving calibration expertise as a Quality Control Technician involves a combination of formal education, hands-on experience, and continuous learning. Follow these concise steps:
Educational Foundation: Start with a solid foundation in metrology, the science of measurement. Consider courses or certifications from recognized bodies such as ASQ (American Society for Quality) or NCSL International.
Practical Training: Gain hands-on experience with calibration equipment and procedures. Seek opportunities within your organization or through apprenticeships. Manufacturers often provide training for their specific equipment.
Standards and Regulations: Familiarize yourself with relevant standards and regulations such as ISO/IEC 17025. Resources like ISO offer detailed guidelines.
Continuous Learning: Stay updated with the latest in calibration technology and practices through webinars, workshops, and conferences by organizations like Fluke Calibration.
Networking: Join professional forums and social media groups focused on calibration and quality control. LinkedIn groups and Reddit communities can be great places to start.
Software Proficiency: Learn to use calibration management software. Many vendors offer training on their platforms.
By integrating these steps into your career development, you can effectively enhance your calibration expertise as a Quality Control Technician.
How to Display Calibration Expertise Skills on Your Resume
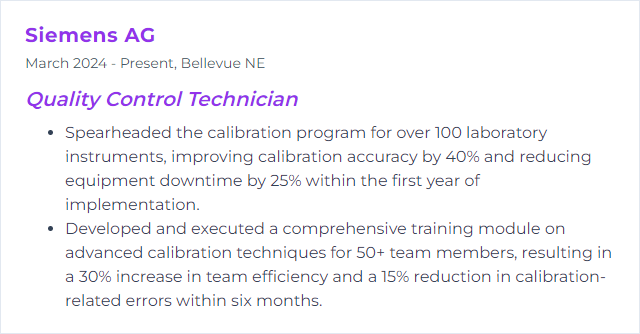
12. Auditing Techniques
Auditing techniques for a Quality Control Technician involve systematic methods used to inspect and validate the effectiveness of quality control processes within an organization. These techniques include reviewing documents, observing operations, interviewing staff, sampling products or processes, and analyzing data to ensure compliance with established standards and identify areas for improvement.
Why It's Important
Auditing techniques are crucial for a Quality Control Technician as they ensure the manufacturing processes and products meet established quality standards, identify areas for improvement, and maintain compliance with regulatory requirements, thereby safeguarding product integrity and customer satisfaction.
How to Improve Auditing Techniques Skills
Improving auditing techniques for a Quality Control Technician involves enhancing skills, staying updated with industry standards, and incorporating technology for more effective audits. Here are concise ways to achieve this:
Continuous Education: Stay updated with the latest ISO standards and quality control methodologies through webinars and online courses. Platforms like Coursera or Udemy offer relevant courses.
Utilize Technology: Adopt audit management software to streamline the audit process, ensure compliance, and maintain records efficiently.
Practice Risk-Based Thinking: Incorporate risk-based thinking to identify areas that pose the greatest threat to quality and focus your auditing efforts there. The ASQ offers resources on implementing risk-based strategies.
Develop Soft Skills: Enhance communication and problem-solving skills to effectively interact with team members and resolve issues. Resources like MindTools offer guidance on improving these essential skills.
Peer Review and Feedback: Participate in peer reviews and seek feedback on your auditing techniques. Engaging in forums on platforms like LinkedIn can provide valuable insights from experienced professionals.
By focusing on these areas, a Quality Control Technician can significantly improve their auditing techniques, leading to more effective quality assurance processes.
How to Display Auditing Techniques Skills on Your Resume
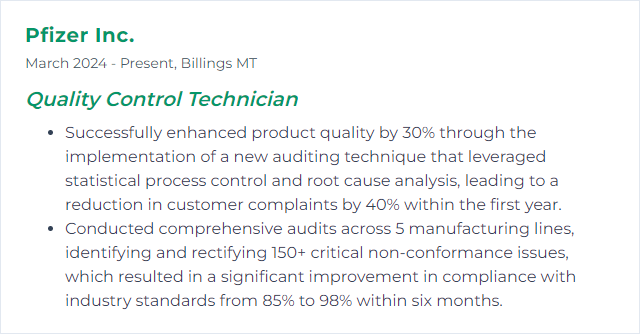