Top 12 Order Puller Skills to Put on Your Resume
In today's competitive job market, standing out as an order puller requires showcasing a blend of technical prowess, efficiency, and soft skills on your resume. Highlighting your top skills not only reflects your competency but also demonstrates your ability to meet the dynamic demands of warehouse and inventory management roles effectively.
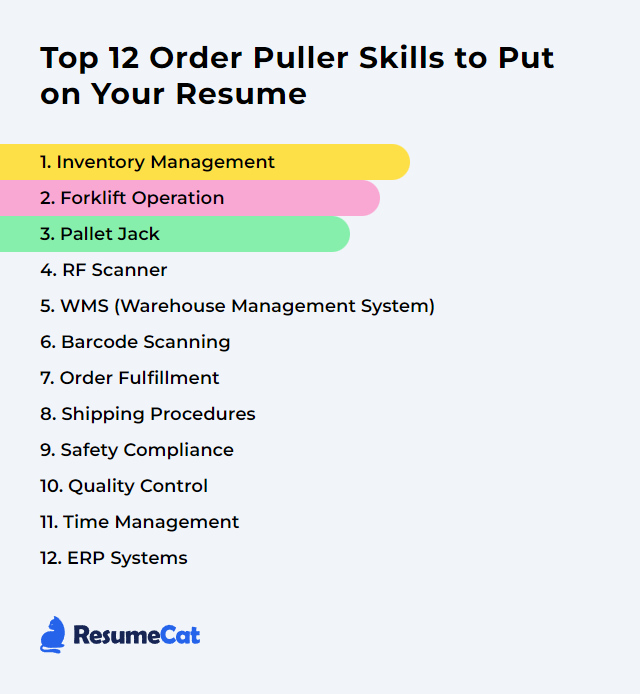
Order Puller Skills
- Inventory Management
- Forklift Operation
- Pallet Jack
- RF Scanner
- WMS (Warehouse Management System)
- Barcode Scanning
- Order Fulfillment
- Shipping Procedures
- Safety Compliance
- Quality Control
- Time Management
- ERP Systems
1. Inventory Management
Inventory Management, in the context of an Order Puller, involves tracking, organizing, and replenishing stock to ensure that items are available for picking and shipping to fulfill customer orders efficiently and accurately.
Why It's Important
Inventory management is crucial for an Order Puller as it ensures the accurate and timely fulfillment of customer orders by maintaining optimal stock levels, minimizing the risk of stockouts or excess inventory, and enhancing overall operational efficiency.
How to Improve Inventory Management Skills
Improving inventory management, especially for an Order Puller, involves enhancing accuracy, efficiency, and response times in pulling orders. Here are concise strategies:
Implement a Real-Time Inventory Tracking System: Use technology to keep track of inventory levels accurately in real-time (Shopify Inventory Management).
Adopt Barcode or RFID Scanning: Streamline the order pulling process and reduce errors by using barcode or RFID scanning for inventory items (BarcodesInc Guide).
Optimize Warehouse Layout: Arrange your warehouse to minimize the time it takes to pull the most frequently ordered items (Wasp Barcode Warehouse Organization Tips).
Use ABC Analysis: Categorize inventory into three categories (A, B, and C) based on their importance and sales frequency to prioritize order pulling efforts (TradeGecko ABC Analysis).
Implement Batch Picking: Group similar orders together to reduce the number of trips needed to pull inventory, increasing efficiency (Veeqo Batch Picking).
Continuous Training and Improvement: Regularly train staff on new technologies and processes, and encourage feedback for continuous improvement (MindTools Training Tips).
Leverage Inventory Management Software: Utilize software that integrates with your sales channels to automatically update inventory levels and assist in order pulling (Cin7 Inventory Management).
By implementing these strategies, an Order Puller can significantly improve inventory management, leading to better customer satisfaction and operational efficiency.
How to Display Inventory Management Skills on Your Resume
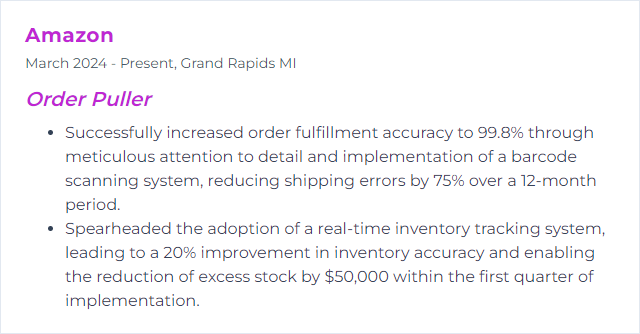
2. Forklift Operation
Forklift operation, in the context of an Order Puller, involves using a forklift to efficiently move, lift, and place goods and materials in a warehouse or storage facility to fulfill orders.
Why It's Important
Forklift operation is crucial for an Order Puller as it enables efficient movement, stacking, and retrieval of goods in a warehouse, ensuring accurate and timely order fulfillment while maintaining safety and minimizing product damage.
How to Improve Forklift Operation Skills
Improving forklift operation, especially for an Order Puller, involves enhancing safety, efficiency, and accuracy. Here are concise steps:
Training & Certification: Ensure all operators are properly trained and certified. Regular refresher courses can keep skills sharp (OSHA Guidelines).
Pre-Operation Checks: Conduct thorough pre-operation inspections to identify and mitigate potential hazards (Daily Checklist).
Equipment Maintenance: Maintain forklifts in top condition to prevent breakdowns and accidents (Maintenance Tips).
Efficiency Practices: Implement best practices for picking orders, like route planning and load management to optimize time and space (Efficiency Tips).
Safety Protocols: Adhere to strict safety protocols, including speed limits, load capacities, and pedestrian awareness (Safety Best Practices).
Technology Use: Utilize technology like warehouse management systems (WMS) for better inventory tracking and task allocation (WMS Benefits).
Communication: Maintain clear communication between order pullers, forklift operators, and other warehouse staff to ensure coordination and efficiency (Effective Communication Tips).
By focusing on these areas, you can significantly improve forklift operation within the context of order pulling, enhancing overall warehouse productivity and safety.
How to Display Forklift Operation Skills on Your Resume
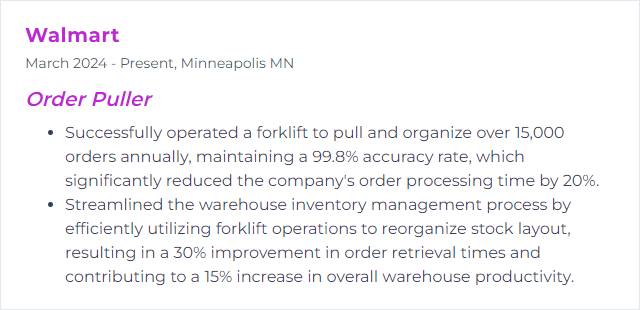
3. Pallet Jack
A pallet jack, in the context of an order puller, is a manual or powered tool used for lifting and moving pallets to efficiently handle materials within a warehouse or distribution center.
Why It's Important
A pallet jack is essential for an Order Puller as it allows for the efficient and safe movement of heavy and bulky goods across the warehouse, minimizing physical strain and increasing productivity.
How to Improve Pallet Jack Skills
To improve a pallet jack for an order puller, consider these concise strategies:
Ergonomic Handles: Enhance comfort and control with ergonomic handle designs. Ergonomics can reduce strain and increase efficiency.
Wheel Material Upgrade: Switch to polyurethane or rubber wheels for smoother, quieter operation and better floor protection. Wheel Types offer insights into material benefits.
Load Capacity Increase: Ensure the pallet jack can handle a higher load capacity to move more goods efficiently. Material Handling Guide details the importance of load management.
Maintenance and Repair Kits: Equip with a comprehensive maintenance and repair kit for on-the-spot adjustments. Maintenance Tips can guide proper upkeep.
Training Programs: Implement training programs focused on safe and efficient operation. OSHA Guidelines provide standards for training and operation.
Add-On Accessories: Consider attachments like a scale to weigh loads on the go, or a brake for improved safety. Pallet Jack Accessories highlight options available.
By focusing on these areas, you can enhance the functionality, safety, and efficiency of a pallet jack for order pullers.
How to Display Pallet Jack Skills on Your Resume
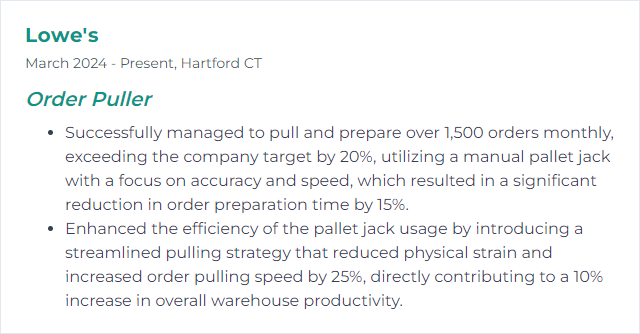
4. RF Scanner
An RF Scanner, in the context of an Order Puller, is a handheld electronic device used for scanning barcodes to track and locate inventory items in a warehouse, facilitating accurate and efficient order fulfillment.
Why It's Important
An RF (Radio Frequency) scanner is essential for an Order Puller as it streamlines the inventory management process, ensuring accurate and efficient picking, packing, and tracking of orders, significantly reducing errors and saving time.
How to Improve RF Scanner Skills
To improve an RF (Radio Frequency) Scanner for an Order Puller, follow these concise steps:
- Software Update: Ensure the RF scanner's software is up-to-date for optimal performance and new features.
- User Training: Provide comprehensive training for users on efficient scanning techniques and shortcuts.
- Customize Settings: Adjust scanner settings for better readability and ease of use, such as sound volume, vibration feedback, and screen brightness.
- Regular Maintenance: Perform regular maintenance to keep the scanner in good working condition, including cleaning and battery checks.
- Accessories: Utilize ergonomic accessories like grips, stands, and holsters for ease of use and to reduce fatigue.
- Network Optimization: Ensure a strong and stable wireless connection by optimizing the warehouse Wi-Fi network.
Implementing these steps will lead to a significant improvement in the efficiency and reliability of RF scanners for order pulling activities.
How to Display RF Scanner Skills on Your Resume
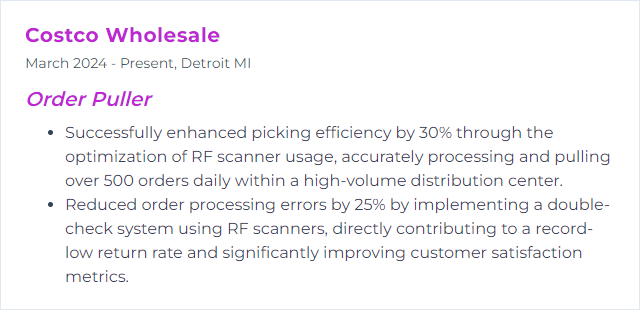
5. WMS (Warehouse Management System)
A Warehouse Management System (WMS) is a software solution designed to optimize and manage the operations within a warehouse, including inventory tracking, picking, receiving, and shipping processes, to enhance efficiency and accuracy for tasks such as order pulling.
Why It's Important
A Warehouse Management System (WMS) is crucial as it optimizes the storage and retrieval processes, ensuring that an Order Puller can quickly and accurately find and dispatch items, improving efficiency and reducing errors in order fulfillment.
How to Improve WMS (Warehouse Management System) Skills
Improving a Warehouse Management System (WMS) for an order puller involves enhancing efficiency, accuracy, and speed in the order fulfillment process. Here are concise strategies:
Integration with Real-Time Inventory: Ensure the WMS is integrated with real-time inventory tracking to enable order pullers to see current stock levels instantly. Real-Time Inventory Integration.
Optimized Picking Routes: Implement features that automatically generate optimized picking routes, reducing travel time and increasing the speed of order pulling. Optimized Picking Routes.
Mobile Compatibility: Make the WMS accessible via mobile devices, allowing order pullers to update and access data on the go. Mobile WMS Solutions.
User-Friendly Interface: Design the interface to be intuitive and easy to use, minimizing training time and errors. User-Friendly WMS Interface.
Training and Support: Provide comprehensive training and ongoing support to ensure that order pullers can fully leverage the WMS capabilities. Effective WMS Training.
Automated Data Capture: Utilize technologies like RFID and barcodes for automated data capture, reducing manual entry errors and speeding up the process. Automated Data Capture Technologies.
By focusing on these key areas, you can significantly improve the functionality and efficiency of your WMS for order pullers, enhancing overall warehouse performance.
How to Display WMS (Warehouse Management System) Skills on Your Resume
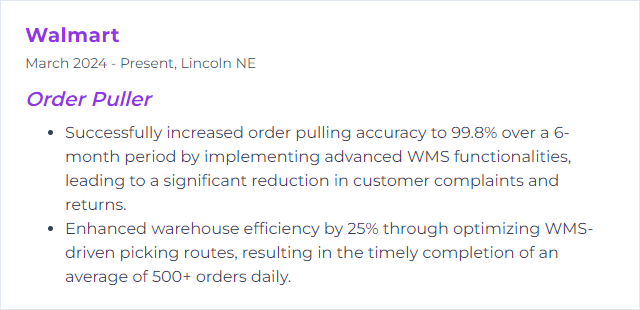
6. Barcode Scanning
Barcode scanning, in the context of an Order Puller, is a process where a handheld or stationary scanner is used to read barcodes on products or packaging, ensuring accurate identification and retrieval of items for orders.
Why It's Important
Barcode scanning is crucial for an Order Puller as it ensures accuracy and efficiency in identifying, tracking, and processing orders, thus minimizing errors and speeding up the fulfillment process.
How to Improve Barcode Scanning Skills
Improving barcode scanning for an Order Puller involves enhancing accuracy, speed, and ergonomic practices. Here’s a concise guide:
Use High-Quality Scanners: Invest in high-quality, durable scanners that can read barcodes quickly and from various angles. Zebra Technologies offers a range of options tailored for warehouse environments.
Implement Barcode Positioning Strategies: Ensure barcodes are placed in easily accessible and consistent locations on products. This reduces the time spent searching for the barcode.
Optimize Lighting: Improve lighting conditions in the warehouse to reduce glare and shadows on barcodes, enhancing scan reliability. OSRAM provides lighting solutions suitable for industrial settings.
Maintain Clean Barcodes: Keep barcodes clean and undamaged. Implement protective measures like laminate overlays to prevent wear and tear.
Train Staff: Provide regular training on the optimal use of scanners and the importance of proper barcode scanning techniques. This can include ergonomic practices to prevent strain or injury.
Use Barcode Scanning Software: Integrate scanning software that can streamline the scanning process and reduce errors. Scandit offers software solutions that can be used on smartphones and industrial scanners alike.
Regular Maintenance: Ensure scanners and related equipment are regularly checked and maintained to keep them in optimal working condition.
By focusing on these areas, an Order Puller can significantly improve the efficiency and accuracy of barcode scanning in their operations.
How to Display Barcode Scanning Skills on Your Resume
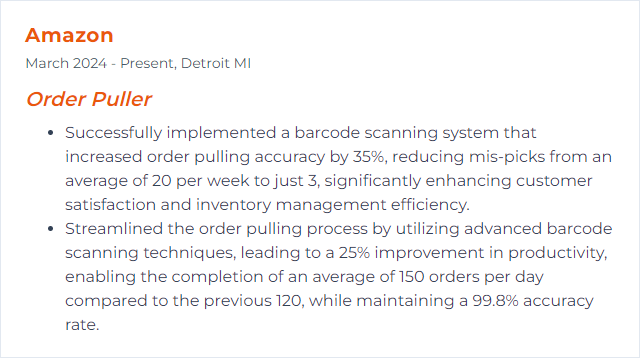
7. Order Fulfillment
Order fulfillment, in the context of an Order Puller, involves retrieving the correct items from inventory to prepare and complete a customer's order for shipping or pickup.
Why It's Important
Order fulfillment is crucial as it ensures accurate and timely delivery of products to customers, directly impacting customer satisfaction and business reputation. For an Order Puller, efficient fulfillment is key to managing inventory accurately and meeting customer expectations consistently.
How to Improve Order Fulfillment Skills
Improving order fulfillment, particularly from the perspective of an Order Puller, involves streamlining processes, enhancing accuracy, and increasing efficiency. Here are concise strategies:
Implement an Efficient Picking Strategy: Opt for batch picking to reduce trips. Batch Picking Guide
Use Technology: Adopt barcode scanners and warehouse management systems (WMS) for real-time inventory tracking. Barcode Scanners Guide
Continuous Training: Regularly train staff on best practices and use of technology. Best Practices for Training
Optimize Warehouse Layout: Ensure the most frequently picked items are easily accessible. Warehouse Layout Optimization
Implement Quality Control Checks: Introduce checks at various stages to reduce errors. Quality Control Tips
Maintain Clear Communication: Use communication tools for real-time updates and coordination. Effective Communication Tools
Employ Ergonomic Practices: Reduce physical strain with ergonomic tools and equipment. Ergonomic Practices
Regularly Review and Adjust Processes: Continuously seek feedback and adjust processes to improve efficiency. Process Improvement Strategies
By focusing on these areas, Order Pullers can significantly contribute to the enhancement of order fulfillment processes.
How to Display Order Fulfillment Skills on Your Resume
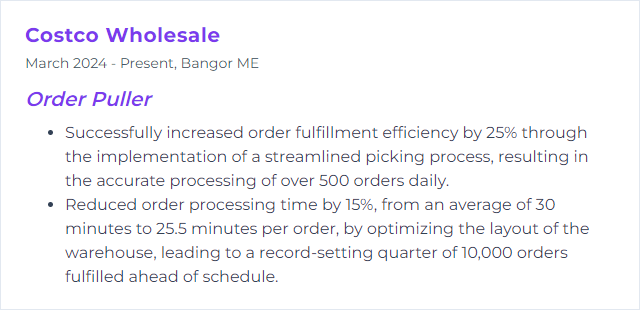
8. Shipping Procedures
Shipping procedures for an Order Puller involve selecting and preparing the correct items from inventory based on customer orders, securely packaging these items, ensuring they are labeled with accurate shipping information, and coordinating with carriers for their timely dispatch.
Why It's Important
Shipping procedures are crucial for an Order Puller because they ensure the accurate, timely, and safe delivery of products to customers, maintaining order integrity and customer satisfaction.
How to Improve Shipping Procedures Skills
Improving shipping procedures, especially from the perspective of an Order Puller, involves streamlining processes, enhancing accuracy, and ensuring timely dispatch. Here are concise steps to achieve this:
Automate the Order Pulling Process: Use warehouse management systems (WMS) to automate order pulling. This reduces human error and speeds up the process. Shopify’s guide on WMS provides a comprehensive look into how such systems can be leveraged.
Implement Barcode Scanning: Equip order pullers with barcode scanners to ensure accuracy in picking items. This reduces mistakes and saves time. Barcodes Inc. offers insights into how barcode technology can improve warehouse efficiency.
Standardize Packing Procedures: Create standardized packing guidelines to ensure consistency and reduce packing time. The U.S. Postal Service provides packing tips that can help in establishing these procedures.
Optimize Warehouse Layout: Arrange the warehouse in a way that minimizes the distance order pullers need to travel. Fast-moving items should be placed closer to the packing area. The Balance Small Business offers strategies for optimizing warehouse layouts.
Use Inventory Management Software: Implement inventory management software to keep track of stock levels in real-time, reducing the chance of picking errors due to stock discrepancies. Capterra’s Inventory Management Software list is a good starting point for finding suitable software solutions.
Continuous Training and Feedback: Regularly train order pullers on new technologies and processes. Encourage feedback to identify bottlenecks and areas for improvement. Chron’s guide on the importance of training emphasizes its value in enhancing operational efficiency.
Implementing these strategies can significantly improve shipping procedures by making the order pulling process more efficient, accurate, and faster.
How to Display Shipping Procedures Skills on Your Resume
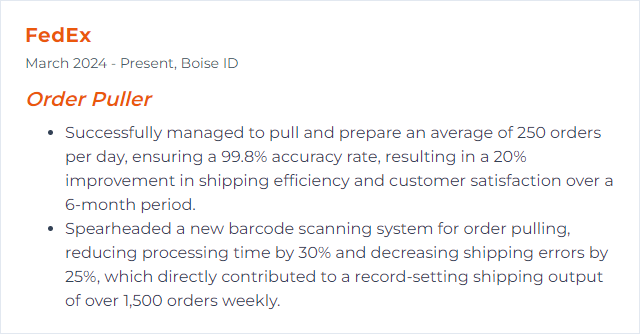
9. Safety Compliance
Safety compliance for an Order Puller involves adhering to established health and safety regulations and company policies to ensure a safe working environment while performing tasks such as retrieving, moving, and managing inventory.
Why It's Important
Safety compliance is crucial for an Order Puller to prevent accidents, ensure a safe working environment, minimize risks of injury, and adhere to legal and regulatory requirements, ultimately promoting efficiency and productivity in operations.
How to Improve Safety Compliance Skills
Improving safety compliance for an Order Puller involves several key steps:
Education and Training: Ensure all staff, especially Order Pullers, receive comprehensive safety training specific to their roles and responsibilities. This includes the proper handling of materials, equipment operation, and emergency procedures.
Regular Safety Audits: Conduct regular safety audits to identify and rectify potential hazards in the workplace. This proactive approach helps in maintaining a safe working environment.
Use of Personal Protective Equipment (PPE): Enforce the use of appropriate PPE such as gloves, safety glasses, and hard hats, ensuring Order Pullers are equipped to handle their tasks safely.
Implement Safety Policies: Develop and implement comprehensive safety policies that are readily accessible to all employees. These policies should be clear, concise, and regularly updated.
Encourage Reporting: Foster a culture where employees feel comfortable reporting safety concerns without fear of retaliation. Prompt attention to reported issues can prevent accidents.
Continual Improvement: Adopt a philosophy of continuous improvement in safety practices, encouraging feedback from staff and incorporating new safety technologies or methodologies as they become available.
By focusing on these areas, an organization can significantly improve safety compliance and create a safer working environment for Order Pullers and all employees.
How to Display Safety Compliance Skills on Your Resume
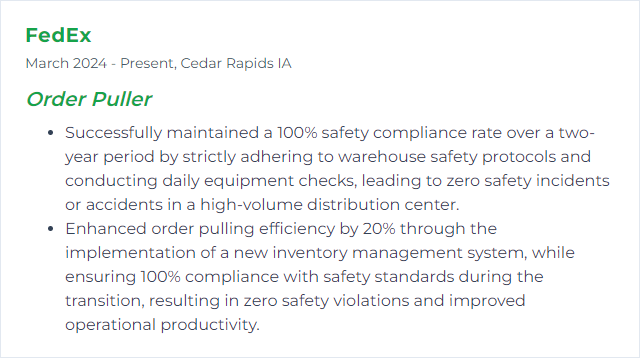
10. Quality Control
Quality Control (QC) for an Order Puller involves verifying the accuracy and quality of picked items against order specifications and ensuring they meet established standards before shipping to customers.
Why It's Important
Quality Control is crucial for an Order Puller to ensure that customers receive the correct and defect-free products, thereby maintaining customer satisfaction, reducing returns and complaints, and upholding the company's reputation for reliability and excellence.
How to Improve Quality Control Skills
To improve Quality Control for an Order Puller, follow these concise steps:
Standardize Processes: Establish clear, standardized procedures for order pulling to ensure consistency. Standardization guidelines can help.
Training: Provide comprehensive training to ensure all order pullers understand quality expectations and procedures. Effective training techniques can be found here.
Use of Technology: Implement technology like barcode scanners and warehouse management systems to minimize errors. Explore warehouse technology solutions.
Continuous Monitoring and Feedback: Regularly monitor performance and provide feedback. Use tools and strategies from continuous improvement processes.
Quality Control Checks: Conduct random quality control checks to ensure accuracy. Learn how to implement effective quality checks.
Customer Feedback: Use customer feedback to identify areas of improvement. Customer feedback strategies can guide improvements.
Reward and Recognition: Motivate staff by recognizing and rewarding quality achievements. Reward systems can enhance motivation.
By adopting these strategies, you can significantly improve quality control in the order pulling process.
How to Display Quality Control Skills on Your Resume
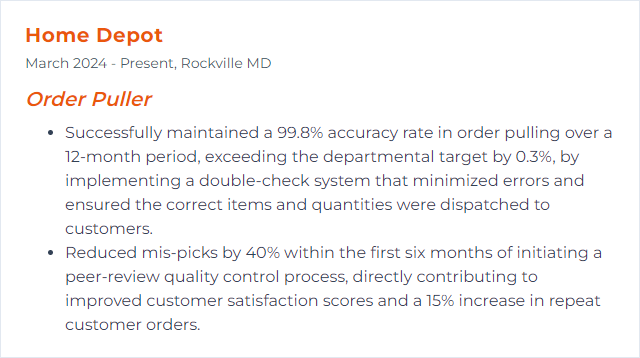
11. Time Management
Time management for an Order Puller involves effectively organizing and prioritizing tasks to efficiently pick and prepare orders within set deadlines, ensuring accurate and timely delivery to customers.
Why It's Important
Time management is crucial for an Order Puller as it ensures efficient processing of orders, maximizes productivity, minimizes delays, and enhances customer satisfaction by delivering orders accurately and on schedule.
How to Improve Time Management Skills
Improving time management as an Order Puller involves prioritizing tasks, minimizing distractions, and optimizing your workflow. Here are concise tips:
Prioritize Tasks: Start your day by identifying the most urgent orders. Use the Eisenhower Box technique to categorize tasks by urgency and importance.
Batch Processing: Group similar tasks together to reduce transition times. Learn more about Batch Processing and its benefits.
Use Technology: Implement inventory management software to streamline the order pulling process. Tools like Fishbowl Inventory can help.
Set Realistic Goals: Break your workday into manageable segments with clear goals. The SMART Goals framework can guide you.
Optimize Workspace: Keep your workspace organized for efficiency. This Workplace Organization guide offers practical tips.
Continuous Learning: Stay updated on best practices in order pulling and time management. LinkedIn Learning offers courses tailored to logistics and warehouse management.
By applying these strategies, you can enhance your efficiency and productivity as an Order Puller.
How to Display Time Management Skills on Your Resume
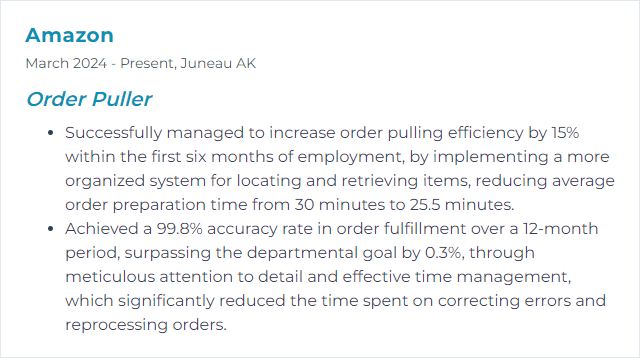
12. ERP Systems
ERP (Enterprise Resource Planning) systems are integrated software platforms that manage core business processes, such as inventory, orders, purchasing, and finance, in a unified system, providing real-time data and insights. For an Order Puller, ERP systems streamline the process of identifying, locating, and pulling the correct items from inventory to fulfill orders efficiently and accurately.
Why It's Important
ERP (Enterprise Resource Planning) systems are important for an Order Puller as they streamline inventory management, automate order processing, and provide real-time data, enabling efficient and accurate order fulfillment.
How to Improve ERP Systems Skills
Improving ERP systems, especially for an Order Puller, involves enhancing efficiency, accuracy, and user experience. Focus on:
Integration: Ensure seamless integration with other systems (inventory, CRM, SCM) for real-time data access. Oracle's Integration Solutions provide robust options.
Customization & Flexibility: Adapt the ERP to specific workflows and user roles to increase productivity. SAP's Customization Options can serve as a guide.
Mobile Accessibility: Implement mobile solutions for on-the-go access to ERP functions, improving order pulling efficiency. Microsoft Dynamics 365 offers mobile ERP applications.
User Training & Support: Regularly update training materials and provide support to ensure users can leverage the ERP system effectively. Epicor's Training and Education Services highlight the importance of user education.
Data Analysis & Reporting: Utilize advanced analytics for better decision-making and to optimize order pulling processes. Infor's Birst features integrated business intelligence.
By focusing on these areas, ERP systems can significantly improve in supporting Order Pullers and overall organizational efficiency.
How to Display ERP Systems Skills on Your Resume
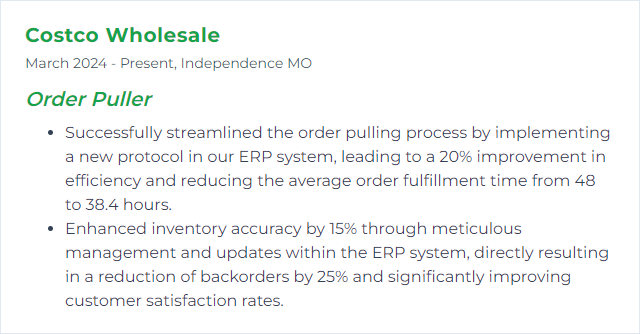