Top 12 Order Picker Skills to Put on Your Resume
In the fast-paced world of warehousing and inventory management, having a standout resume as an order picker is essential to securing your next job opportunity. Highlighting your top order picker skills not only demonstrates your proficiency and efficiency in selecting and managing orders but also showcases your ability to contribute significantly to the smooth operation of the supply chain.
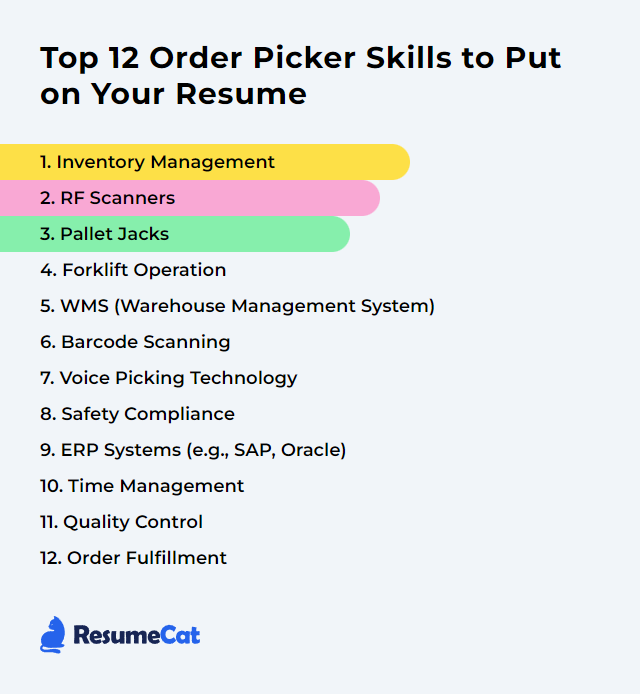
Order Picker Skills
- Inventory Management
- RF Scanners
- Pallet Jacks
- Forklift Operation
- WMS (Warehouse Management System)
- Barcode Scanning
- Voice Picking Technology
- Safety Compliance
- ERP Systems (e.g., SAP, Oracle)
- Time Management
- Quality Control
- Order Fulfillment
1. Inventory Management
Inventory management involves tracking and controlling a company's inventory levels to ensure the efficient handling, storing, and supply of products. For an Order Picker, it means ensuring the correct items are accurately picked from inventory for processing and delivery based on customer orders.
Why It's Important
Inventory management is crucial because it ensures that the right quantity of products is available when needed, minimizing overstock or stockouts, thus enabling an Order Picker to efficiently fulfill orders accurately and promptly, leading to higher customer satisfaction and reduced operational costs.
How to Improve Inventory Management Skills
Improving inventory management, especially from the perspective of an Order Picker, can be pivotal for operational efficiency and customer satisfaction. Here are concise strategies:
Implement a Robust Inventory Management System: Utilize software that offers real-time tracking and automated restocking alerts. Shopify's Inventory Management is a good example.
Use Barcode Scanning: Incorporate barcode or RFID scanning to reduce errors and speed up the order picking process. Barcodes, Inc. offers solutions tailored for various industries.
Employ Efficient Picking Strategies: Adopt methods like zone picking or batch picking to minimize time spent on movement. The Council of Supply Chain Management Professionals (CSCMP) provides resources and case studies on best practices.
Continuous Training and Feedback: Regularly train staff on new technologies and strategies, and encourage feedback for continuous improvement. LinkedIn Learning offers courses on inventory management and order picking.
Regular Inventory Audits: Conduct cycle counts and physical inventories periodically to ensure system data matches actual stock. QuickBooks Commerce has features supporting inventory auditing.
Optimize Warehouse Layout: Arrange inventory to minimize travel time for pickers, with high-demand items more accessible. WERC offers warehouse layout optimization insights.
Implementing these strategies can significantly enhance the efficiency and accuracy of inventory management from an order picker's perspective, leading to better overall operational performance.
How to Display Inventory Management Skills on Your Resume
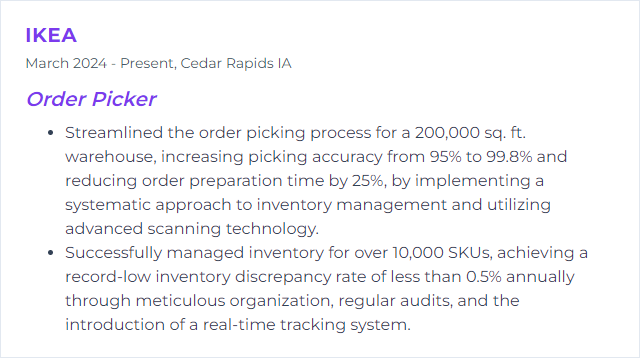
2. RF Scanners
RF scanners, in the context of order picking, are handheld or wearable devices that use radio frequency technology to scan barcodes or RFID tags on items, enabling the quick and accurate identification and tracking of products for order fulfillment in warehouses and distribution centers.
Why It's Important
RF (Radio Frequency) scanners are crucial for Order Pickers as they streamline the picking process by providing real-time inventory tracking, ensuring accuracy in order fulfillment, and significantly reducing the likelihood of errors, thus enhancing efficiency and productivity in warehouse operations.
How to Improve RF Scanners Skills
Improving RF scanners for order pickers involves enhancing usability, speed, accuracy, and integration capabilities. Consider the following strategies:
Ergonomics: Optimize the design for comfortable, one-handed operation over long periods. Ergonomic RF scanners reduce fatigue and increase productivity.
Display and Interface: Incorporate large, clear displays and intuitive interfaces. Touch screens with customizable user interfaces can speed up operations.
Connectivity: Ensure robust wireless connectivity for real-time data access and updates. Advanced connectivity options keep the system responsive and up-to-date.
Battery Life: Use long-lasting batteries or easily swappable battery packs for continuous operation. Innovative battery technologies support extended use.
Scanning Technology: Employ scanners with quick, accurate scanning capabilities, including in challenging conditions. Look for devices with advanced imaging technology for reliable performance.
Software Integration: Ensure the scanner software integrates seamlessly with your warehouse management system (WMS) for efficient data handling. Comprehensive WMS integration streamlines operations.
Training and Support: Provide thorough training and easy access to technical support to maximize the efficiency of order pickers. Effective training programs and support services minimize downtime.
By focusing on these areas, you can significantly improve the efficiency and effectiveness of RF scanners for order pickers, leading to faster, more accurate order fulfillment.
How to Display RF Scanners Skills on Your Resume
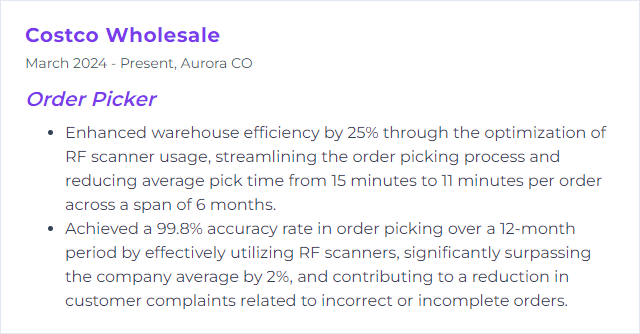
3. Pallet Jacks
Pallet jacks, in the context of order picking, are manual or powered tools used for lifting and moving pallets within warehouses, facilitating the transport of goods for order fulfillment.
Why It's Important
Pallet jacks are crucial for order pickers as they enable efficient and safe movement of heavy loads across the warehouse floor, significantly enhancing productivity and reducing physical strain on workers.
How to Improve Pallet Jacks Skills
Improving pallet jacks, especially for order pickers, involves enhancing ergonomics, safety, and efficiency. Here are concise strategies:
Ergonomics: Implement adjustable handles to suit operators of different heights, reducing strain. Ergonomic Guidelines
Safety: Add automatic braking systems to prevent accidents in busy warehouses. Occupational Safety and Health Administration (OSHA) Guidelines
Efficiency: Integrate electronic lifting mechanisms for quicker load handling. Consider smart pallet jacks with IoT connectivity for real-time tracking. Internet of Things (IoT) Applications
Durability: Use high-quality materials for the frame and wheels to increase the lifespan and reduce maintenance costs. Material Selection Guide
Customization: Offer modular designs allowing for attachments like scales for weighing loads on-the-go or barcode scanners for inventory management. Material Handling Industry of America (MHIA)
By focusing on these areas, pallet jacks can be significantly improved to meet the demands of modern order picking operations more effectively.
How to Display Pallet Jacks Skills on Your Resume
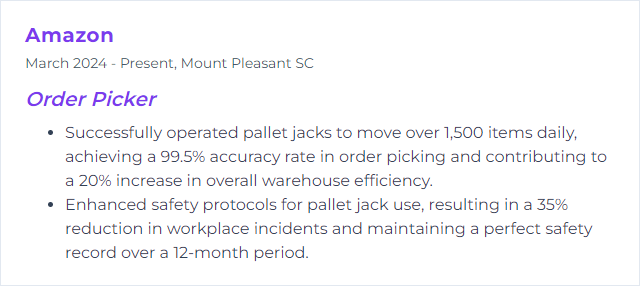
4. Forklift Operation
Forklift operation, in the context of an Order Picker, involves maneuvering a specialized lift truck designed to pick and transport materials from high shelving units within warehouses, ensuring safe and efficient handling of goods for order fulfillment.
Why It's Important
Forklift operation is crucial for an Order Picker because it significantly enhances the efficiency and safety of moving, lifting, and organizing heavy loads in warehouses, ensuring timely and accurate order fulfillment.
How to Improve Forklift Operation Skills
Improving forklift operation, particularly for an Order Picker, involves focusing on safety, training, and efficiency. Here's a concise guide:
Enhance Safety: Ensure operators are familiar with all safety features of the Order Picker. Conduct regular safety checks and maintenance. OSHA provides comprehensive guidelines on forklift safety.
Operator Training: Invest in comprehensive training programs for operators, emphasizing hands-on practice, safety protocols, and efficient handling techniques.
Equipment Maintenance: Regularly maintain and service the Order Picker to prevent breakdowns. Refer to the manufacturer's maintenance guidelines for specifics.
Optimize Warehouse Layout: Ensure the warehouse layout is optimized for smooth operation, with clear aisles and properly marked zones. Cisco-Eagle offers strategies for warehouse optimization.
Implement Technology: Use technology like Warehouse Management Systems (WMS) for efficient order picking and inventory management. Barcoding, Inc. provides insights into technology integration for forklift operations.
By focusing on these areas, you can significantly improve the operation of an Order Picker forklift, enhancing safety, efficiency, and productivity.
How to Display Forklift Operation Skills on Your Resume
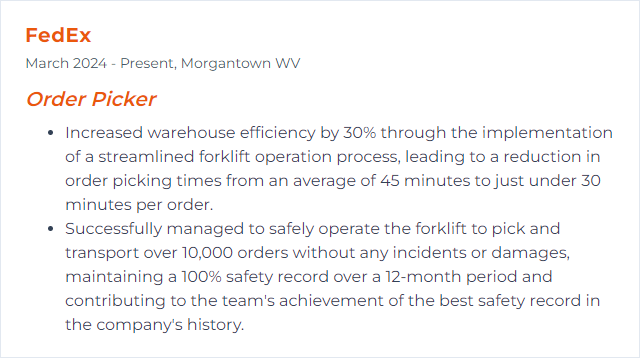
5. WMS (Warehouse Management System)
A Warehouse Management System (WMS) is a software application designed to optimize and manage warehouse operations, including inventory tracking, order picking, receiving, and shipping, thereby enhancing efficiency and accuracy for order pickers and other warehouse personnel.
Why It's Important
A WMS (Warehouse Management System) is crucial for an Order Picker as it optimizes the picking process by efficiently directing them to the exact locations of items, ensuring accurate and timely order fulfillment, and reducing errors and operational costs.
How to Improve WMS (Warehouse Management System) Skills
Improving a Warehouse Management System (WMS) for an Order Picker involves several focused strategies aimed at enhancing efficiency, accuracy, and productivity. Here are concise suggestions:
Integration with Advanced Technologies: Incorporate technologies like RFID and voice picking systems to streamline order picking processes, reducing errors and increasing speed.
Optimize Picking Routes: Utilize WMS software capabilities to plan optimal picking routes, minimizing travel time and improving order picker efficiency.
Implement Mobile Solutions: Equip order pickers with mobile devices integrated with the WMS for real-time data access and updates, enhancing decision-making and flexibility.
Continuous Training and Feedback: Provide ongoing training programs for order pickers on WMS functionalities and encourage feedback for system improvements, fostering a culture of continuous improvement.
Data Analysis and Reporting: Leverage the WMS's data analysis and reporting tools to identify bottlenecks and areas for improvement, enabling data-driven decisions to enhance performance.
Regular System Updates and Maintenance: Ensure the WMS is up to date with the latest software updates and maintenance practices, keeping the system efficient and reducing downtime.
By focusing on these areas, a WMS can be significantly improved, benefiting order pickers through enhanced efficiency, accuracy, and job satisfaction.
How to Display WMS (Warehouse Management System) Skills on Your Resume
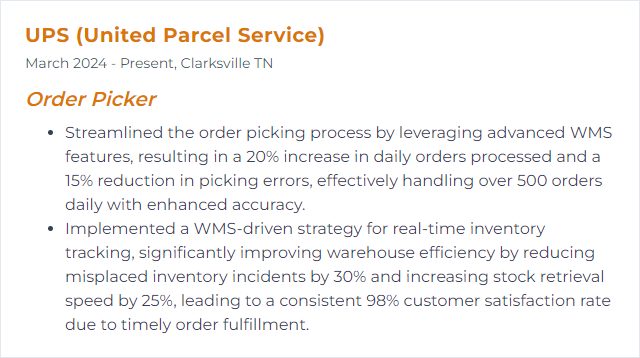
6. Barcode Scanning
Barcode scanning is the process of using a barcode scanner to read and input the unique code on a product's label into a system, enabling order pickers to quickly and accurately verify and track inventory during the picking process.
Why It's Important
Barcode scanning is essential for an order picker because it ensures accuracy and efficiency in identifying, tracking, and processing items quickly, reducing errors and saving time during order fulfillment.
How to Improve Barcode Scanning Skills
To enhance barcode scanning efficiency for an Order Picker, follow these concise strategies:
Use High-Quality Scanners: Opt for scanners with high resolution and fast decoding capabilities to ensure quick and accurate scans. Zebra Technologies and Honeywell offer a range of reliable options.
Optimize Barcode Placement: Ensure barcodes are placed at easily accessible spots on products or shelves to facilitate quick scanning. GS1 provides guidelines on effective barcode placement and standards.
Implement Barcode Quality Control: Regularly check and maintain the quality of printed barcodes to prevent scanning issues. ISO/IEC standards outline quality requirements for barcodes.
Train Staff: Offer comprehensive training on the optimal use of scanners and problem-solving techniques for scanning issues. Resources like Barcoding, Inc. can be useful for training materials.
Use Scanning Software Enhancements: Implement software solutions that can enhance scanning accuracy and speed, such as error correction and quick-scan algorithms. Scandit offers advanced scanning software options.
Regular Maintenance: Keep scanners clean and in good repair to ensure consistent performance. Refer to the manufacturer’s maintenance guidelines for best practices.
By following these strategies, order pickers can significantly improve barcode scanning efficiency and accuracy.
How to Display Barcode Scanning Skills on Your Resume

7. Voice Picking Technology
Voice picking technology is a hands-free, voice-activated system used by order pickers in warehouses and distribution centers to receive verbal instructions through a headset about which items to pick and where to find them, improving accuracy and efficiency in the picking process.
Why It's Important
Voice picking technology is important because it allows order pickers to work hands-free and eyes-free, improving accuracy, speed, and safety in fulfilling orders, thus enhancing overall productivity and efficiency in the warehouse operations.
How to Improve Voice Picking Technology Skills
Improving voice picking technology for an order picker involves enhancing accuracy, efficiency, and user comfort. Implement these strategies:
Upgrade Software: Regularly update the voice recognition software to improve its understanding of various accents and speech patterns. Vocollect by Honeywell is a leading example, known for its adaptability and accuracy.
Invest in High-Quality Headsets: Use noise-cancelling headsets to minimize background noise, ensuring clear communication. The 3M Peltor series is renowned for its durability and noise reduction capabilities.
Customize Voice Commands: Tailor the voice commands to match the common phrases and terminology used in your operation, making the system more intuitive for users. Ivanti Wavelink offers customizable voice solutions that can adapt to specific operational needs.
Implement Multimodal Systems: Combine voice picking with other technologies like RFID or barcode scanning for verification, increasing accuracy and efficiency. Zebra Technologies provides solutions that integrate voice with other data capture methods.
Train and Support Users: Provide comprehensive training and ongoing support to ensure users are comfortable and proficient with the technology. This includes offering materials in multiple languages if necessary.
Analyze and Optimize: Regularly review performance data to identify bottlenecks or areas for improvement. Tools like Lucas Systems offer analytics capabilities to optimize workflow and increase productivity.
By focusing on these key areas, you can significantly enhance the performance and user experience of your voice picking technology.
How to Display Voice Picking Technology Skills on Your Resume
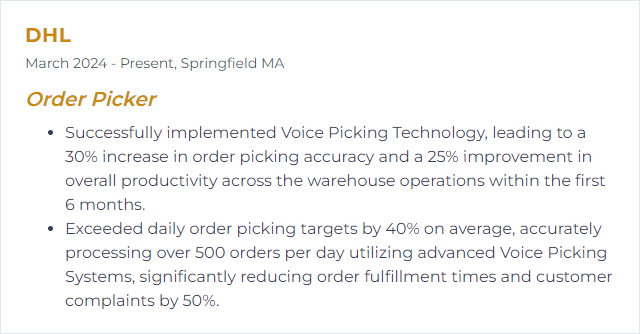
8. Safety Compliance
Safety compliance, in regard to an Order Picker, involves adhering to established health and safety standards and regulations to ensure the well-being of individuals operating or working near order picking equipment, minimizing risks of accidents and injuries.
Why It's Important
Safety compliance is crucial for an Order Picker to prevent accidents, ensure a safe working environment, protect against legal liabilities, and maintain operational efficiency.
How to Improve Safety Compliance Skills
Improving safety compliance for an Order Picker involves a multi-faceted approach focusing on training, equipment maintenance, and adherence to regulatory standards. Here’s a concise guide:
Training and Certification: Ensure all operators undergo comprehensive training specific to order pickers, including operational techniques and safety protocols. Certification should be updated regularly.
Routine Equipment Checks: Implement a strict schedule for equipment maintenance and safety inspections to identify and rectify potential hazards like mechanical failures or malfunctions.
Adherence to OSHA Standards: Familiarize with and adhere to OSHA standards for order pickers, including the use of safety equipment, load handling, and operating procedures.
Safety Gear and Equipment: Provide and enforce the use of appropriate safety gear, such as helmets, harnesses, and safety shoes. Ensure the order picker is equipped with necessary safety features like guardrails and emergency stop functions.
Emergency Preparedness: Conduct regular emergency drills and ensure all operators are trained in emergency response techniques, including equipment shutdown and evacuation procedures.
By focusing on these key areas, safety compliance for order picker operations can be significantly improved, leading to a safer working environment.
How to Display Safety Compliance Skills on Your Resume
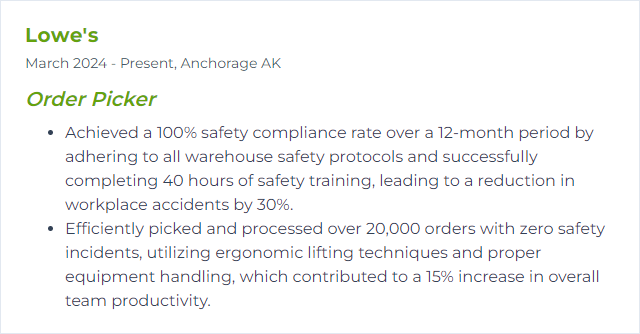
9. ERP Systems (e.g., SAP, Oracle)
ERP (Enterprise Resource Planning) systems, such as SAP and Oracle, are integrated software platforms that manage and automate many core business processes, including inventory management, order processing, and supply chain operations. For an order picker, ERP systems streamline and optimize the picking process by providing real-time inventory data, guiding efficient picking routes, and ensuring accurate order fulfillment.
Why It's Important
ERP systems, like SAP and Oracle, centralize data, streamline operations, and optimize inventory management. For an Order Picker, this ensures accurate, real-time information on stock levels and locations, facilitating efficient picking, reducing errors, and improving order fulfillment speed.
How to Improve ERP Systems (e.g., SAP, Oracle) Skills
Improving ERP systems like SAP and Oracle, especially from the perspective of an order picker, involves enhancing efficiency, accuracy, and user-friendliness. Here are concise strategies:
Integration of Advanced Technologies: Incorporate RFID and IoT devices for real-time inventory tracking and management, significantly reducing manual input errors and speeding up the order picking process.
Customization and User Training: Customize the ERP interface to fit the specific needs of order pickers, including simplified screens and workflows. Offer regular user training to ensure users are proficient and can leverage all relevant features efficiently.
Mobile Solutions: Deploy mobile ERP applications that allow order pickers to access information and perform tasks directly from the warehouse floor, improving accuracy and speed.
Data Analytics and AI: Utilize AI and machine learning for predictive analytics to forecast inventory needs and optimize order picking routes, reducing time wasted on unnecessary movements.
Process Optimization: Continuously review and optimize warehouse processes through ERP system feedback and analytics, identifying bottlenecks and areas for improvement.
Implementing these strategies requires a holistic approach, focusing on technology integration, user-centric customization, and continuous process evaluation for effective improvements.
How to Display ERP Systems (e.g., SAP, Oracle) Skills on Your Resume
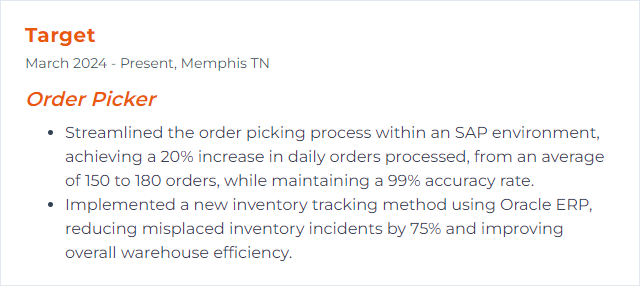
10. Time Management
Time management for an Order Picker involves efficiently organizing and prioritizing tasks to pick and prepare orders accurately and swiftly, ensuring timely deliveries while optimizing productivity and reducing downtime.
Why It's Important
Time management is crucial for an Order Picker as it enhances efficiency and accuracy in fulfilling orders, ensures timely deliveries, and maximizes productivity, directly impacting customer satisfaction and operational success.
How to Improve Time Management Skills
Improving time management, especially for an Order Picker, involves prioritizing tasks, minimizing distractions, and using tools effectively. Focus on:
Prioritizing Tasks: Start with the most critical orders first, considering deadlines and complexity. MindTools offers strategies on prioritizing effectively.
Batch Processing: Group similar tasks together to minimize the time spent switching between different types of tasks. The American Psychological Association explains how multitasking can reduce productivity.
Use of Technology: Utilize warehouse management systems (WMS) or order picking apps to streamline the picking process and reduce errors. Shopify discusses the benefits of WMS.
Continuous Learning: Regularly seek feedback and learn new techniques to improve efficiency. LinkedIn Learning offers courses on time management and productivity.
Physical Organization: Keep the warehouse and picking areas organized to reduce search time. The 5S System is a methodology that can help maintain an efficient, safe, and clean workplace.
By focusing on these areas, an Order Picker can significantly improve their time management skills, leading to increased productivity and job satisfaction.
How to Display Time Management Skills on Your Resume
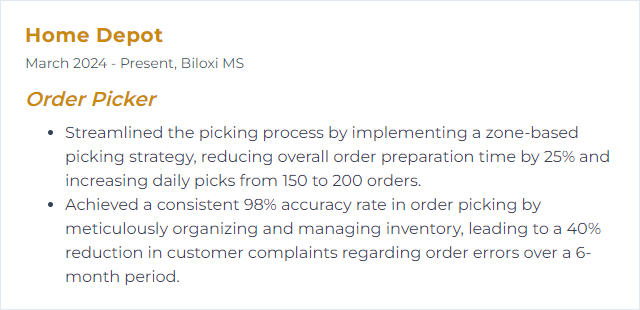
11. Quality Control
Quality Control, in the context of an Order Picker, involves the systematic process of ensuring that the products picked and prepared for shipping meet the company's standards for quality, accuracy, and completeness.
Why It's Important
Quality Control is crucial for an Order Picker to ensure the accuracy and integrity of orders, minimize errors, enhance customer satisfaction, and maintain the reputation of the business.
How to Improve Quality Control Skills
Improving Quality Control for an Order Picker involves adopting precise strategies to enhance accuracy and efficiency in selecting orders. Here are succinct steps to achieve this:
Training and Education: Continuously train staff on best practices and the importance of quality control. Use resources like OSHA’s Training for guidelines on safety and efficiency.
Implement Technology: Incorporate advanced technologies such as RFID systems and barcode scanning to minimize human errors and streamline the picking process.
Standardize Processes: Create and enforce standard operating procedures (SOPs) for order picking. Helpful guidelines can be found on ASQ’s site.
Quality Control Checks: Conduct regular quality control checks at different stages of the order picking process. Techniques and tools for this can be explored through ISO’s Quality Management Principles.
Feedback Loop: Establish a feedback loop with employees to continuously identify and rectify errors. Resources like SurveyMonkey can be used to gather employee feedback efficiently.
Performance Metrics: Utilize performance metrics to track and improve order accuracy and efficiency. Learn more about setting up effective KPIs from KPI.org.
By focusing on these key areas, you can significantly improve the quality control in the order picking process.
How to Display Quality Control Skills on Your Resume
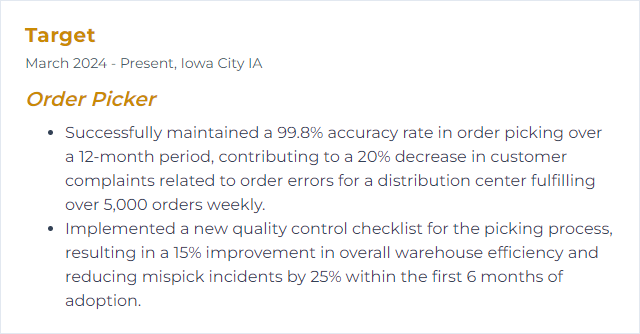
12. Order Fulfillment
Order fulfillment is the process of receiving, processing, and delivering orders to customers, involving tasks such as picking, packing, shipping, and handling returns. For an Order Picker, it specifically refers to selecting and gathering the correct items in the right quantities to fulfill customer orders from a warehouse or storage facility.
Why It's Important
Order fulfillment is crucial because it directly impacts customer satisfaction by ensuring timely, accurate, and reliable delivery of products, which is essential for maintaining trust and encouraging repeat business. For an Order Picker, it's their primary responsibility to execute this process efficiently, affecting the overall success of the supply chain.
How to Improve Order Fulfillment Skills
Improving order fulfillment, particularly from the perspective of an Order Picker, involves enhancing accuracy, speed, and overall efficiency. Here are concise strategies:
Optimize Warehouse Layout: Arrange items based on their picking frequency to minimize travel time. More on warehouse layout optimization.
Implement Batch Picking: Group similar orders to reduce the number of trips. Learn about batch picking.
Adopt Technology: Use barcode scanners and wearable devices to speed up picking and reduce errors. Explore wearable technology in warehousing.
Continuous Training: Regularly train staff on best practices and use of new technologies. Training tips for warehouse staff.
Implement Quality Control: Introduce checks at various stages of the fulfillment process to ensure accuracy. Understanding quality control in fulfillment.
By focusing on these areas, an Order Picker can significantly contribute to the efficiency and accuracy of the order fulfillment process.
How to Display Order Fulfillment Skills on Your Resume
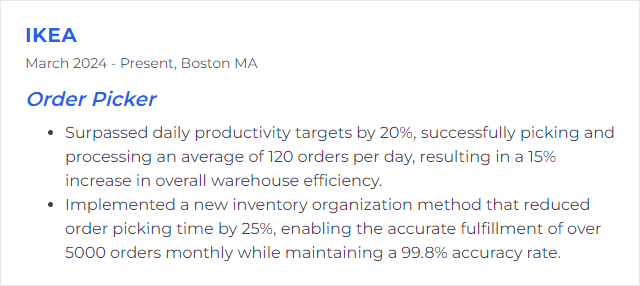