Top 12 Manual Machinist Skills to Put on Your Resume
In today's competitive job market, standing out as a manual machinist requires showcasing a blend of technical prowess and soft skills that highlight your expertise and adaptability in the field. Crafting a resume that effectively communicates these skills is paramount, ensuring you capture the attention of potential employers by demonstrating your capability to excel in precision manufacturing environments.
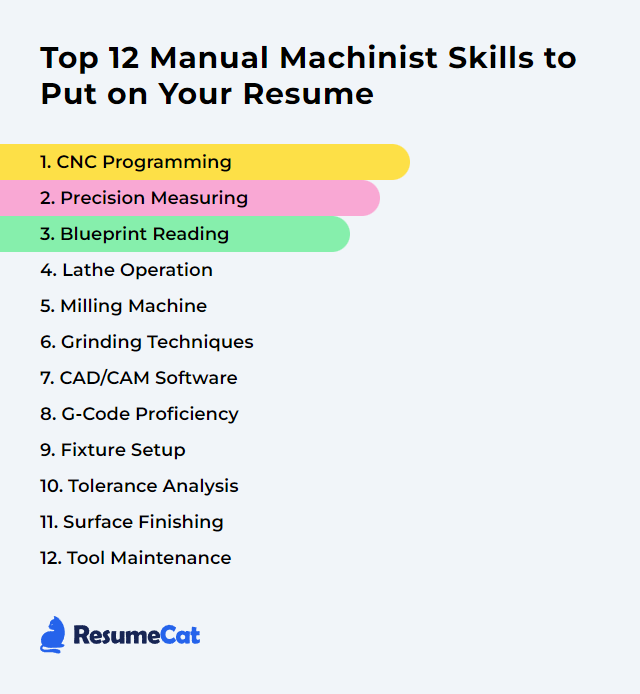
Manual Machinist Skills
- CNC Programming
- Precision Measuring
- Blueprint Reading
- Lathe Operation
- Milling Machine
- Grinding Techniques
- CAD/CAM Software
- G-Code Proficiency
- Fixture Setup
- Tolerance Analysis
- Surface Finishing
- Tool Maintenance
1. CNC Programming
CNC programming involves creating code to control automated machines that cut, shape, and finish metal or other materials, allowing for precise and repeatable parts production. For a manual machinist, it's a transition from hand-operated to computer-guided machining processes.
Why It's Important
CNC programming is crucial for a manual machinist as it enables the precise and efficient control of machine tools, automating complex and repetitive tasks, and ensuring high accuracy and consistency in production, thus expanding capabilities and productivity.
How to Improve CNC Programming Skills
Improving CNC programming, especially for a manual machinist transitioning to CNC, involves a few focused steps. Emphasize understanding CNC machine basics, mastering CAD/CAM software, learning G-code, practicing on simulators, and engaging with online communities and resources. Here's a concise guide:
Learn the Basics: Start with fundamental concepts of CNC machining. Titans of CNC Academy offers free, comprehensive tutorials from basics to advanced techniques.
Master CAD/CAM Software: Familiarize yourself with popular CAD/CAM tools. Fusion 360 is user-friendly for beginners and has extensive tutorials on its official website.
Understand G-Code: G-code is the language that controls CNC machines. CNCCookbook’s G-Code Tutorial is an excellent resource to start with.
Practice with Simulators: Before running programs on actual machines, use simulators. CAMotics, a free, open-source simulator available on CAMotics.org, can help you visualize and test your programs.
Stay Engaged with Communities: Online forums like CNC Zone and Practical Machinist are great places to ask questions, share experiences, and learn from professionals.
Continuous Learning: Always be updating your skills with new software updates, machining techniques, and industry standards. Online platforms like LinkedIn Learning offer courses on CNC programming and related topics.
By focusing on these areas, a manual machinist can efficiently transition to and improve their CNC programming skills.
How to Display CNC Programming Skills on Your Resume
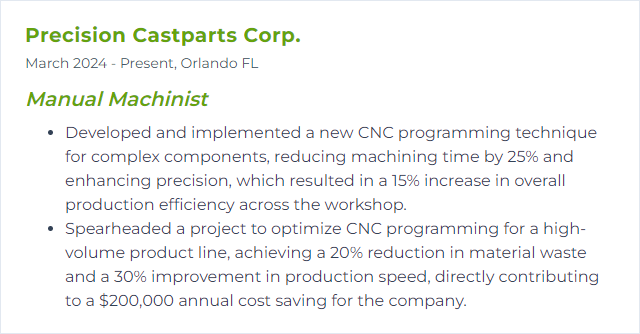
2. Precision Measuring
Precision measuring in the context of a manual machinist refers to the use of specialized tools (such as micrometers, calipers, and gauges) to accurately measure the dimensions of machined parts to ensure they meet specified tolerances and quality standards.
Why It's Important
Precision measuring is critical for a manual machinist because it ensures the accuracy and quality of machined parts, meeting specific tolerances required for the parts to function correctly in their intended applications.
How to Improve Precision Measuring Skills
Improving precision measuring for a manual machinist involves several key steps focused on tool selection, care, and technique. Here’s a concise guide:
Select the Right Tools: Choose high-quality micrometers, calipers, and dial indicators that meet your precision requirements. Opt for digital tools for higher accuracy and easier reading.
Regular Calibration: Ensure your measuring tools are regularly calibrated according to the manufacturer's recommendations. This maintains their accuracy over time. NIST Guidelines on Calibration
Proper Handling and Storage: Handle measuring tools with care to prevent damage. Store them in a clean, dry place, preferably in their original cases to protect them from dust and moisture. Mitutoyo Care Tips
Temperature Consideration: Materials expand or contract with temperature changes. Measure in a controlled environment or compensate for temperature differences. Engineering Toolbox - Thermal Expansion
Use of Measurement Techniques: Apply consistent force when using tools, and always take multiple measurements to verify results. Practice and refine your technique for consistent outcomes.
Education and Training: Continually improve your skills through training and staying updated with the latest precision measuring practices. Tooling U-SME Training
By focusing on these areas, a manual machinist can significantly improve the precision of their measurements, leading to better quality and efficiency in their work.
How to Display Precision Measuring Skills on Your Resume
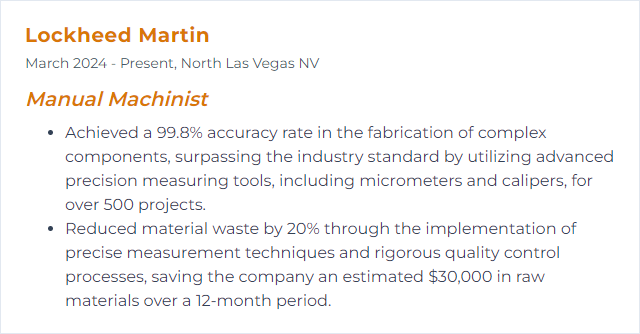
3. Blueprint Reading
Blueprint reading for a manual machinist involves interpreting and understanding detailed technical drawings that specify the dimensions, geometry, and finishing processes required to manufacture a part or component. This skill is essential for accurately setting up and operating manual machining equipment to produce the specified item.
Why It's Important
Blueprint reading is crucial for a manual machinist as it enables them to accurately understand and follow the technical specifications and dimensions of parts to be machined, ensuring precision in manufacturing and adherence to design requirements.
How to Improve Blueprint Reading Skills
Improving blueprint reading as a manual machinist involves enhancing your ability to understand and interpret the graphical symbols, dimensions, and notations used in mechanical engineering drawings. Here's a concise guide:
Familiarize with Basic Symbols and Notations: Start by learning the standard symbols and notations for materials, finishes, and tolerances. The American Society of Mechanical Engineers (ASME) provides standards like ASME Y14.5 that are essential.
Understand Orthographic Projections: Grasp the concept of how 3D objects are represented in 2D drawings, including views (front, top, side) and sections. This resource offers a good overview.
Dimension Reading and Tolerance Interpretation: Precision is key in machining. Learn how to accurately read dimensions and understand tolerance symbols. The International Organization for Standardization (ISO) sets many relevant standards, including those for dimensional tolerances.
Study Geometric Dimensioning and Tolerancing (GD&T): GD&T provides a comprehensive system for defining and communicating engineering tolerances. ASME's GD&T standards are a crucial learning area.
Practice Regularly: Like any skill, proficiency comes with practice. Work on interpreting different types of blueprints, gradually increasing complexity. Websites like Tooling U-SME offer courses and exercises tailored for machinists.
Seek Feedback: Consult with experienced machinists or engineers who can provide insights and correct misunderstandings. Engaging in forums like Practical Machinist can be beneficial for peer advice.
Use Supplemental Resources: Books such as "Blueprint Reading for Machinists" by David L. Taylor offer in-depth knowledge and practice exercises tailored specifically for machinists.
By consistently applying these strategies and leveraging the provided resources, you'll significantly improve your blueprint reading skills, essential for precision and success in manual machining.
How to Display Blueprint Reading Skills on Your Resume
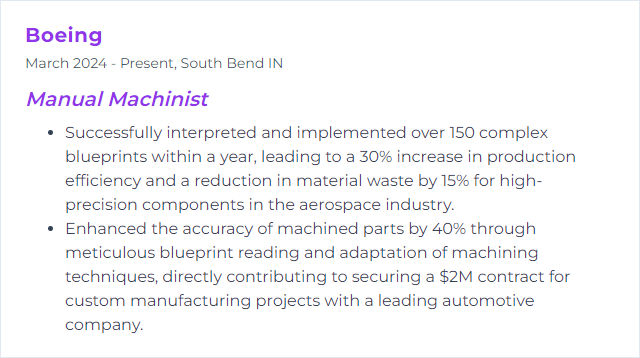
4. Lathe Operation
Lathe operation, for a manual machinist, involves using a lathe machine to rotate a workpiece on its axis while various tools are applied to it to perform operations such as cutting, sanding, knurling, drilling, or deformation to create an object with symmetry about an axis of rotation.
Why It's Important
Lathe operation is crucial for a manual machinist because it enables the precise shaping, cutting, and finishing of various materials into cylindrical or symmetrical components, essential for manufacturing and repair tasks across numerous industries.
How to Improve Lathe Operation Skills
Improving lathe operation for a manual machinist involves focusing on precision, safety, and efficiency. Here are concise strategies:
Regular Maintenance: Keep the lathe clean and lubricated. Check alignment regularly. Machine Maintenance Guide.
Proper Tool Selection: Use the correct cutting tool for the material and job. Sharp tools reduce chatter and improve finishes. Tool Selection Guide.
Optimal Speed and Feed: Adjust spindle speed and feed rate according to material and tooling specifications. Speed and Feed Calculator.
Use of Coolants: Proper use of coolants can improve tool life and surface finish. Coolant Management.
Skill Development: Practice and continuous learning are key. Focus on mastering techniques like facing, turning, and threading. Machining Techniques.
Quality Measuring Tools: Use precision instruments like micrometers and calipers to ensure dimensions are accurate. Measuring Tools Guide.
Safety First: Always wear appropriate PPE and follow safety protocols. Lathe Safety Tips.
By applying these practices, a manual machinist can enhance lathe operation, leading to better work quality and efficiency.
How to Display Lathe Operation Skills on Your Resume
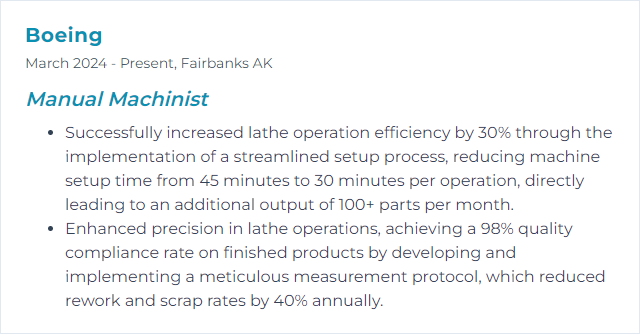
5. Milling Machine
A milling machine is a tool used by manual machinists to cut and shape solid materials like metal or wood. It operates by rotating a cutting tool against a stationary workpiece, allowing for precise removal of material to create parts with complex shapes and features.
Why It's Important
For a manual machinist, a milling machine is crucial because it allows for the precise shaping and cutting of materials into custom parts or tools, enabling the creation of complex geometries that are essential in manufacturing and engineering tasks.
How to Improve Milling Machine Skills
Improving a milling machine for a manual machinist involves enhancing precision, efficiency, and safety. Here are key ways to achieve these improvements:
Upgrade Cutting Tools: Use high-quality carbide end mills and inserts for better performance and longer tool life.
Enhance Stability: Add vibration dampers and ensure the machine is level to reduce vibrations and improve cut quality.
Improve Workholding: Invest in a high-precision vice or clamping system for better workpiece stability.
Regular Maintenance: Follow a strict maintenance schedule to keep the machine in top condition, focusing on lubrication, cleaning, and inspection.
Digital Readout (DRO) Upgrade: Install a DRO system for improved accuracy and ease of use in measurements.
Training and Techniques: Continuously learn advanced milling techniques and tooling strategies to optimize performance and tool life.
Implementing these improvements will significantly enhance the capabilities and efficiency of a milling machine for manual machinists.
How to Display Milling Machine Skills on Your Resume
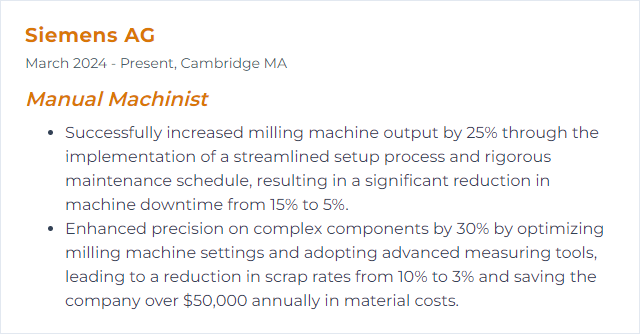
6. Grinding Techniques
Grinding techniques refer to the use of abrasive wheels to shape, sharpen, or finish metal parts to precise dimensions and surface quality. In manual machining, it involves the skilled operation of grinding machines, selecting appropriate grinding wheels, and applying specific movements and pressures to achieve the desired outcome on the workpiece.
Why It's Important
Grinding techniques are crucial for a manual machinist as they ensure precision in shaping and finishing parts, enable the creation of complex geometries with tight tolerances, and improve surface finish quality, directly impacting the functionality and lifespan of machined components.
How to Improve Grinding Techniques Skills
Improving grinding techniques as a manual machinist involves focusing on precision, equipment maintenance, and process optimization. Here are concise tips with useful resources for further reading:
Understand Material Properties: Know the material you're working with to choose the correct grinding wheel and parameters. ASM International offers resources on material properties.
Select the Right Grinding Wheel: Match the wheel type, grit, and grade to your workpiece material and the desired finish. Norton Abrasives provides detailed guidance on selecting grinding wheels.
Maintain Equipment: Keep your grinding machine well-maintained. This includes regular inspections and ensuring that all components are properly aligned. Modern Machine Shop has tips on maintaining grinding machines.
Use Coolants Wisely: Appropriate use of coolants can reduce heat, prevent workpiece burn, and improve surface finish. Machinery Lubrication offers advice on coolant use.
Adopt Proper Technique: Ensure you're using the correct feed rates and speeds for your application. Slow and steady often yields the best results. The American Machinist provides insights into various machining techniques, including grinding.
Practice Safety: Always wear appropriate personal protective equipment and follow safety guidelines. OSHA has resources on machine shop safety, including for grinding operations.
Seek Continuous Improvement: Stay updated with new technologies and techniques in machining and grinding through continuous learning. Websites like Practical Machinist offer forums and articles where professionals share tips and advice.
By focusing on these areas, a manual machinist can improve their grinding techniques, leading to better efficiency, accuracy, and surface finishes.
How to Display Grinding Techniques Skills on Your Resume
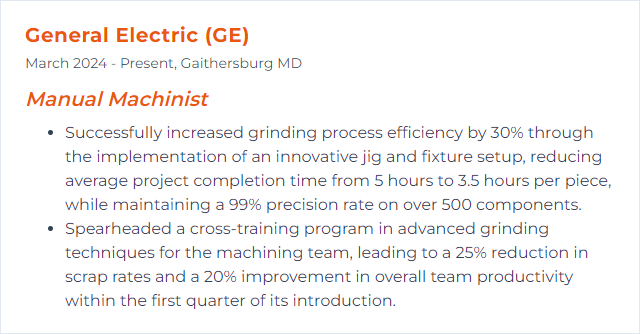
7. CAD/CAM Software
CAD/CAM software is a computer-aided design and manufacturing tool that allows manual machinists to design parts and create detailed machining instructions digitally, improving precision and efficiency in the fabrication process.
Why It's Important
CAD/CAM software is important for a manual machinist because it streamlines the design and manufacturing process, allowing for more precise and complex parts to be made faster, reducing errors and material waste, and enhancing productivity and efficiency in the workshop.
How to Improve CAD/CAM Software Skills
Improving CAD/CAM software for a manual machinist involves focusing on usability, integration, and functionality tailored to streamline the transition from manual to digital processes. Here’s how:
User Interface Simplification: Design an intuitive, user-friendly interface that minimizes the learning curve for manual machinists. Autodesk offers resources on user interface design in CAD software.
Enhanced Integration: Ensure seamless integration with popular machine tools and digital fabrication methods. Integration guides, like those from SolidWorks, can serve as a good reference.
Customizable Tool Paths: Develop features that allow machinists to customize tool paths with ease, mirroring the flexibility of manual machining. Mastercam provides examples of customizable toolpath technology.
Comprehensive Tutorials: Include easy-to-follow tutorials and guides specifically designed for manual machinists transitioning to CAD/CAM. The Fusion 360 Learning Library is a good example of comprehensive learning resources.
Feedback Mechanism: Implement a system to collect feedback from manual machinists to continuously improve the software based on user experience.
Simulation Features: Offer advanced simulation features that allow users to test and adjust their designs and machining processes virtually. Check out Siemens NX for simulation capabilities.
Affordability and Accessibility: Ensure the software is affordable and accessible to individual machinists and small shops. Some companies like FreeCAD focus on providing free, open-source solutions.
By focusing on these areas, CAD/CAM software can become more accessible and useful to manual machinists, facilitating a smoother transition to digital manufacturing technologies.
How to Display CAD/CAM Software Skills on Your Resume
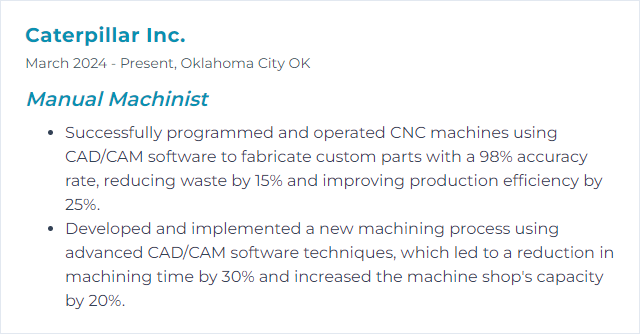
8. G-Code Proficiency
G-code proficiency for a manual machinist refers to the ability to understand and write G-code, the programming language used to control CNC machines, enabling the machinist to precisely create parts by instructing the machine on movements, speeds, and tool changes.
Why It's Important
G-Code proficiency is crucial for a manual machinist because it enables the accurate programming of CNC machines for precise machining tasks, increases productivity by streamlining workflow, and enhances the ability to troubleshoot and optimize manufacturing processes.
How to Improve G-Code Proficiency Skills
Improving G-code proficiency as a manual machinist involves understanding the basics, practicing coding, and continuously learning. Here’s how to enhance your skills:
Grasp the Basics: Start with understanding the foundational elements of G-code, including common commands (G00, G01, etc.), coordinate systems, and programming structure. TITANS of CNC Academy offers free resources to get started.
Practice Writing G-Code: Manually write out simple programs to get a feel for the syntax and commands. Tools like NC Viewer allow you to simulate and visualize G-code.
Learn from Examples: Study existing G-code examples to understand how different machining operations are programmed. Websites like CNC Cookbook provide ample examples and references.
Use Simulation Software: Before running your code on a machine, use simulation software to test and troubleshoot. Fusion 360 includes a feature for simulating tool paths and G-code.
Continuously Update Your Knowledge: Stay informed about new G-code functionalities and CNC technologies. Practical Machinist forums and discussions can keep you updated on industry practices.
Experiment on Projects: Apply your skills on small projects to build confidence and understand practical applications of G-code.
Remember, proficiency comes with practice and continuous learning.
How to Display G-Code Proficiency Skills on Your Resume
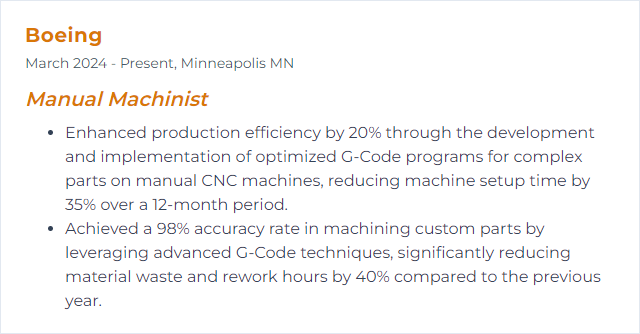
9. Fixture Setup
Fixture setup in manual machining involves preparing and securing the workpiece in a device (fixture) on a machine tool to ensure it is held firmly in place during machining operations. This setup is crucial for achieving precise dimensions and shapes as per the machining requirements.
Why It's Important
Fixture setup is crucial for a manual machinist because it ensures accuracy, repeatability, and safety by securely holding and precisely positioning the workpiece for machining operations, reducing errors and waste.
How to Improve Fixture Setup Skills
Improving fixture setup for a manual machinist involves optimizing accuracy, efficiency, and safety. Here are concise strategies:
Standardize Components: Use standardized fixture components when possible to reduce setup time and increase repeatability. Carr Lane Manufacturing offers a wide range of standard fixture components.
Plan and Visualize: Before setup, plan the process. Use CAD software like Fusion 360 to visualize the fixture setup and part orientation.
Use Modular Fixturing: Implement modular fixturing systems that can be quickly assembled, disassembled, and reconfigured. Bluco Corporation provides modular fixturing solutions.
Implement Quick-Change Systems: Adopt quick-change systems for tools and fixtures to drastically reduce setup times. Jergens Inc. offers quick-change fixturing solutions.
Check for Parallelism and Squareness: Regularly use precision instruments like dial indicators and squares to ensure fixture components are parallel and square to the machine's axes. Mitutoyo provides high-quality measuring tools.
Maintain a Clean Workspace: Keep the machine and work area clean to prevent inaccuracies caused by debris. Simple practices can significantly impact precision and efficiency.
Educate and Train: Continuously educate yourself on new fixture technologies and strategies. Websites like Practical Machinist offer valuable insights and forums for machinists.
Document Setups: Keep detailed records of setups for future reference. This can significantly reduce setup time for repeat jobs.
By implementing these strategies, a manual machinist can improve fixture setup in terms of accuracy, efficiency, and safety.
How to Display Fixture Setup Skills on Your Resume
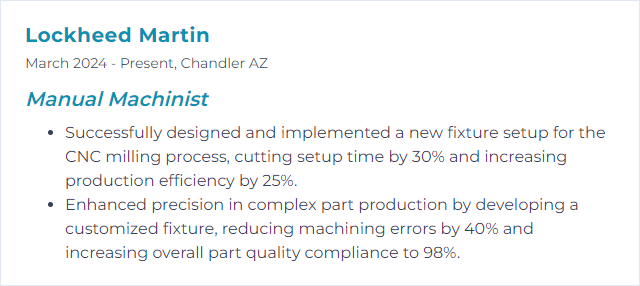
10. Tolerance Analysis
Tolerance analysis is the process of evaluating the cumulative effect of part dimension variations on the final assembly to ensure the finished product meets design specifications and functions correctly, even with manufacturing variations. For a manual machinist, it involves calculating and accommodating for the allowable deviation in each part's dimensions to guarantee the assembled product operates as intended.
Why It's Important
Tolerance analysis is important for a manual machinist because it ensures parts fit together properly and function as intended, minimizing waste, rework, and ensuring product quality and reliability.
How to Improve Tolerance Analysis Skills
Improving tolerance analysis for a manual machinist involves understanding how to measure and control the variability in manufacturing processes accurately. Here's a very short, concise guide:
Understand Tolerances: Begin by thoroughly understanding the types of tolerances (dimensional, geometric, etc.) and their impacts on part fit and function. ASME provides standards and guidelines.
Precision Measuring Tools: Use precision measuring tools (micrometers, calipers, gauges) correctly. Ensure they are calibrated. Mitutoyo offers detailed guides on using measuring instruments.
Material Consideration: Account for material properties and how they may vary or change during machining processes. MatWeb is a resource for material properties.
Machining Practices: Implement best machining practices that reduce errors, such as maintaining tool sharpness and proper machine maintenance. Practical Machinist is a community and resource with tips and advice.
Statistical Process Control (SPC): Use SPC to monitor and control the machining process to ensure consistency. NIST/SEMATECH e-Handbook of Statistical Methods provides a comprehensive guide to SPC.
Continuous Learning: Stay informed about new technologies, materials, and machining techniques that can impact tolerances. Online forums, webinars, and machining courses are valuable resources.
By focusing on these areas, a manual machinist can significantly improve their tolerance analysis, leading to higher quality parts and more efficient production processes.
How to Display Tolerance Analysis Skills on Your Resume
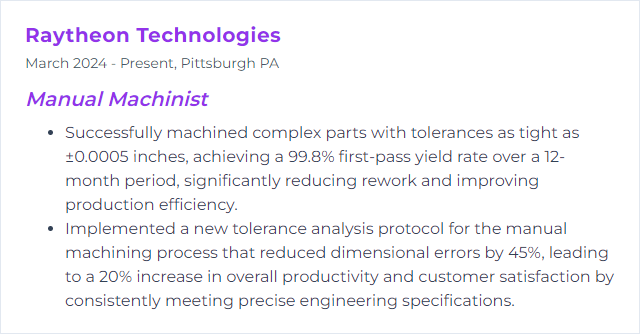
11. Surface Finishing
Surface finishing refers to the process of altering a workpiece's exterior surface to achieve a desired texture or appearance. For a manual machinist, this involves techniques like sanding, grinding, polishing, or applying coatings to improve the part's aesthetics, functionality, or surface integrity.
Why It's Important
Surface finishing is crucial for enhancing the appearance, corrosion resistance, and wear resistance of machined parts, ensuring better fit and function in assemblies, and achieving precise tolerances and smoother surfaces for improved performance and longevity.
How to Improve Surface Finishing Skills
Improving surface finishing in manual machining involves several techniques and considerations to achieve a desired surface quality. Here are concise strategies:
Correct Tool Selection: Use the appropriate cutting tool material and geometry for the material being machined. Carbide tools often provide a better surface finish than high-speed steel tools.
Optimal Cutting Parameters: Adjust cutting speed, feed rate, and depth of cut to minimize tool wear and vibration. Machinery's Handbook provides guidelines for setting these parameters.
Tool Path Strategy: Implement climb milling where possible to improve surface finish due to reduced tool deflection. Haas Automation's Tips offer practical advice on milling strategies.
Proper Lubrication and Cooling: Use appropriate coolants or cutting fluids to reduce heat and prevent material sticking to the tool. Mobil’s Cutting Fluids guide helps in selecting the right fluid.
Maintain Equipment: Regularly check and maintain machine alignment, spindle condition, and tool sharpness to prevent vibration and ensure accuracy. Practical Machinist is a valuable resource for maintenance tips.
Fine Finishing Techniques: After machining, use fine finishing techniques like honing, polishing, or buffing to enhance surface quality. Precision Surfacing Solutions offers insights into various finishing processes.
Measurement and Adjustment: Continuously measure and adjust machining parameters based on surface finish results using surface finish gauges. Mitutoyo Surface Roughness Testers provide precision measurement tools.
By focusing on these areas, manual machinists can significantly improve the surface finishing of their parts.
How to Display Surface Finishing Skills on Your Resume
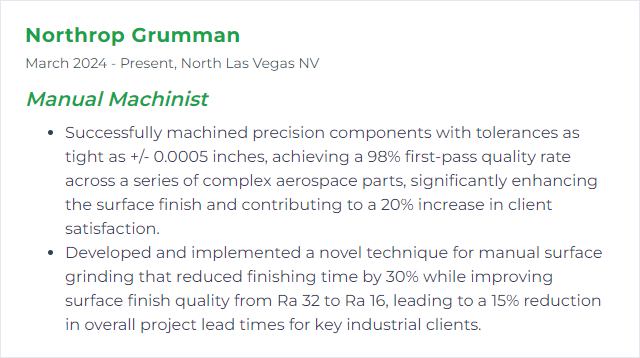
12. Tool Maintenance
Tool maintenance for a manual machinist involves regularly inspecting, cleaning, sharpening, and properly storing hand tools and machine tool components to ensure they remain in good working condition and produce accurate workpieces.
Why It's Important
Tool maintenance is crucial for a manual machinist because it ensures precision and accuracy in machining tasks, prolongs the lifespan of tools, reduces the risk of tool breakage, and maintains operational safety by preventing accidents caused by tool failure.
How to Improve Tool Maintenance Skills
Improving tool maintenance for a manual machinist involves several straightforward steps aimed at ensuring tools perform optimally and have an extended life span. Here are concise, essential strategies:
Regular Cleaning: Always clean tools after use to prevent build-up of materials and corrosion. This basic step can significantly extend tool life. Cleaning Metalworking Tools.
Proper Storage: Store tools in a dry, organized environment to prevent damage and rust. Using toolboxes or storage systems designed for specific tools helps maintain their condition. Tool Storage Tips.
Lubrication: Regularly lubricate moving parts to reduce wear and tear. Use the correct lubricants as specified by tool manufacturers. Lubrication of Tools.
Sharpening: Keep cutting tools sharp. Dull tools require more force to use, leading to possible damage and poor workmanship. Learn the correct sharpening techniques for each tool. Sharpening Tools.
Routine Inspection: Frequently inspect tools for wear, damage, or alignment issues. Early detection of problems can prevent further damage and costly replacements. Inspecting Hand Tools.
Follow Manufacturer’s Guidelines: Always adhere to the maintenance schedule and procedures recommended by the tool’s manufacturer. This ensures that tools are maintained according to the standards that will help preserve their longevity and efficiency. Manufacturer’s Maintenance Guidelines.
Implementing these practices will significantly improve the maintenance of tools for a manual machinist, ensuring durability, reliability, and precision in their work.
How to Display Tool Maintenance Skills on Your Resume
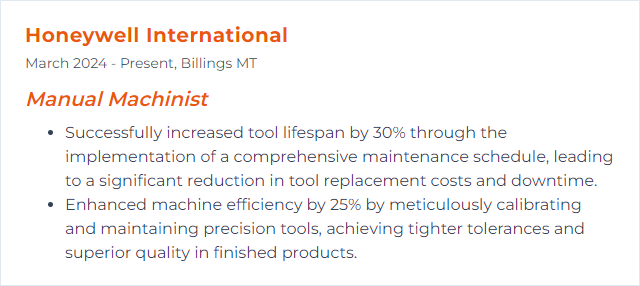