Top 12 Machinist Skills to Put on Your Resume
In today's competitive job market, possessing a well-rounded set of skills is crucial for machinists aiming to stand out. This article highlights the top 12 machinist skills that are essential to showcase on your resume, ensuring you capture the attention of potential employers and secure your position in the manufacturing industry.
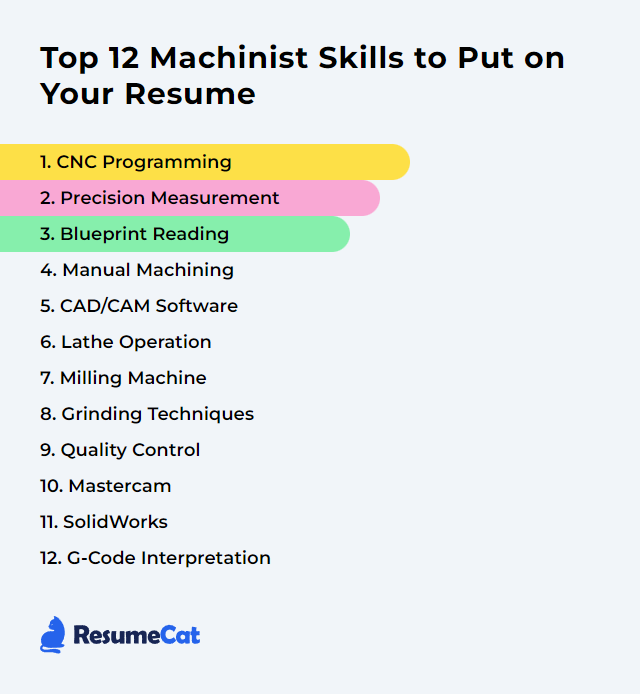
Machinist Skills
- CNC Programming
- Precision Measurement
- Blueprint Reading
- Manual Machining
- CAD/CAM Software
- Lathe Operation
- Milling Machine
- Grinding Techniques
- Quality Control
- Mastercam
- SolidWorks
- G-Code Interpretation
1. CNC Programming
CNC Programming is the process of creating detailed instructions (a program) for a CNC machine to follow, enabling it to precisely cut, shape, or form a piece of material into a specified design. For a machinist, it involves translating engineering designs into a series of commands using a specific language (such as G-code) that the CNC machine interprets to perform the required operations.
Why It's Important
CNC programming is crucial for machinists as it enables the precise control of machine tools to create complex and high-quality parts efficiently, reducing errors, saving time, and increasing productivity.
How to Improve CNC Programming Skills
Improving CNC programming involves enhancing efficiency, accuracy, and the overall quality of the machining process. Here are concise tips aimed at machinists seeking to improve their CNC programming skills:
Master the Basics: Solidify your understanding of CNC fundamentals, including G-code and M-code. Online platforms like Titans of CNC Academy provide free resources.
Use Simulation Software: Before running your program on the actual machine, use simulation software to catch errors and optimize tool paths. Check out Fusion 360 for integrated CAD/CAM.
Continuous Learning: Stay updated with the latest CNC technologies and programming techniques through platforms like Mastercam University.
Optimize Tool Paths: Use efficient tool paths to reduce machining time and wear on tools. Explore advanced strategies such as High Efficiency Milling (HEM).
Standardize Processes: Develop and use a library of standardized processes and routines for common jobs to save time and ensure consistency.
Collaborate and Share Knowledge: Engage in forums and communities like Practical Machinist to share experiences and learn from peers.
Implement Tool Management: Keep an organized tool database and use tool management software to streamline your workflow.
Regular Machine Maintenance: Ensure your CNC machine is regularly maintained for optimal performance. This indirectly improves programming efficiency by reducing the need for adjustments due to machine inaccuracies.
Improving CNC programming is a continuous process of learning, practicing, and adapting to new technologies and methodologies.
How to Display CNC Programming Skills on Your Resume
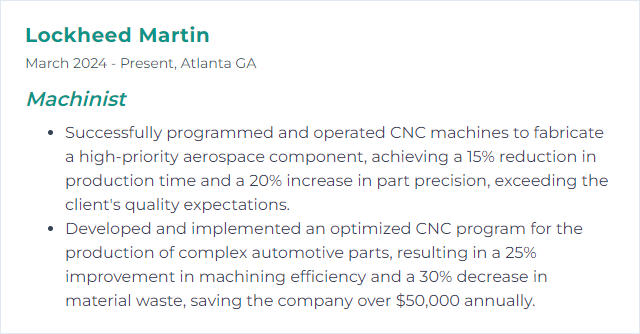
2. Precision Measurement
Precision measurement for a machinist refers to the use of highly accurate instruments to determine the dimensions of a part or material within tight tolerances, ensuring it meets the required specifications for its intended use.
Why It's Important
Precision measurement is crucial for a machinist because it ensures that parts are manufactured to exact specifications, leading to proper fit and function in mechanical assemblies, avoiding waste, and maintaining high-quality standards.
How to Improve Precision Measurement Skills
Improving precision measurement in machining involves several strategies focusing on equipment care, calibration, and technique refinement. Here's a concise guide:
Calibrate Regularly: Ensure all measuring tools and machines are calibrated frequently to maintain accuracy. NIST's Calibration Services provides guidelines and services.
Use Appropriate Tools: Select the right tool for the measurement task. Digital calipers, micrometers, and dial indicators offer varying degrees of precision. For tool recommendations, see Mitutoyo's Tool Selection Guide.
Maintain Environmental Conditions: Temperature, humidity, and vibration can affect measurements. Control the environment as suggested by ASME B89.7.4.
Adopt Best Practices: Use consistent force when measuring and always measure from the same datum points to reduce variability. The Precision Machined Products Association offers best practice guidelines.
Continuous Learning: Stay updated with the latest measurement techniques and tools via workshops and training. IMTS Education is a great resource.
Inspect and Maintain Tools: Regular inspection and maintenance of tools can prevent inaccuracies due to wear or damage. Practical Machinist forums often discuss maintenance tips.
Implement Quality Control Checks: Use statistical quality control methods to monitor and improve the measurement process. ASQ's Quality Resources offer insights into statistical methods.
By focusing on these strategies, machinists can significantly enhance the precision of their measurements, leading to improved product quality and efficiency.
How to Display Precision Measurement Skills on Your Resume
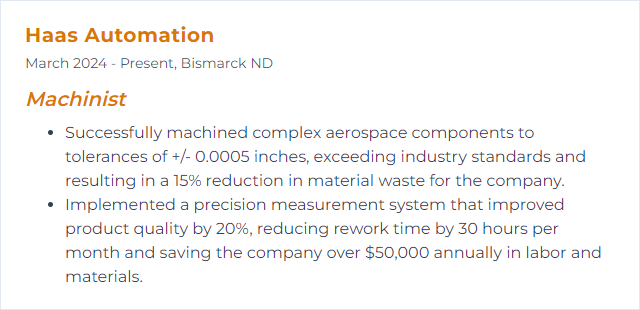
3. Blueprint Reading
Blueprint reading for a machinist involves interpreting and understanding technical drawings and diagrams that detail the specifications, dimensions, and processes required to manufacture mechanical parts or assemblies.
Why It's Important
Blueprint reading is crucial for machinists as it enables them to accurately interpret and follow design specifications, ensuring precise fabrication, assembly, and modification of mechanical components. This skill ensures quality control and adherence to engineering standards.
How to Improve Blueprint Reading Skills
Improving blueprint reading skills, especially for a machinist, involves understanding geometric tolerancing, symbols, and technical drawings specific to machining processes. Here's a concise guide to enhancing your abilities:
Study Basic Symbols: Familiarize yourself with basic machining symbols and their meanings.
Understand Geometric Dimensioning and Tolerancing (GD&T): GD&T is a system for defining and communicating engineering tolerances. A concise guide can be found on ASME's website.
Practice Reading Drawings: Regularly practice with actual machinist blueprints to improve your speed and understanding.
Use Online Courses: Platforms like Udemy and Coursera offer courses specifically on blueprint reading and GD&T.
Reference Books and Manuals: Books such as "Blueprint Reading for Machinists" by David L. Taylor provide a comprehensive look into blueprint reading tailored for machinists.
Join Forums and Groups: Engage with communities on platforms like Reddit’s r/Machinists for advice and experience sharing.
By consistently applying these strategies and seeking feedback on your understanding, your blueprint reading skills as a machinist will improve significantly.
How to Display Blueprint Reading Skills on Your Resume
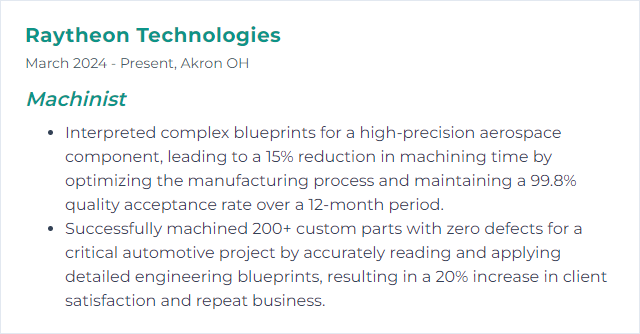
4. Manual Machining
Manual machining is the process of shaping metal or other materials using tools and machines operated directly by a machinist, without computer control, to cut, drill, or shape the material into a desired part or product.
Why It's Important
Manual machining is crucial for machinists as it provides a deep understanding of machining fundamentals, enhances precision skills, and enables the creation or modification of parts when CNC (Computer Numerical Control) is not feasible or practical. It ensures versatility and problem-solving capabilities in various machining scenarios.
How to Improve Manual Machining Skills
Improving manual machining skills involves practice, understanding of materials, and mastery of tooling techniques. Here are key steps:
Practice Precision: Regularly use measuring tools like calipers and micrometers to develop a sense of precision. MIT's Machine Shop Videos offer practical insights.
Understand Materials: Learn the properties of different materials you work with. The ASM International Material Database is a great resource.
Tool Mastery: Familiarize yourself with various cutting tools and their applications. Machinery's Handbook is an essential reference.
Learn from Mistakes: Keep a journal of projects, noting what went wrong and how issues were resolved.
Safety First: Always prioritize safety to prevent accidents and ensure consistent work quality. OSHA provides guidelines on Machine Shop Safety.
Join Forums: Participate in forums like Practical Machinist to exchange tips and advice with peers.
Continuous Learning: Take advantage of online courses and resources. Coursera and MIT OpenCourseWare offer relevant courses.
By integrating these practices, you'll steadily improve your manual machining skills.
How to Display Manual Machining Skills on Your Resume
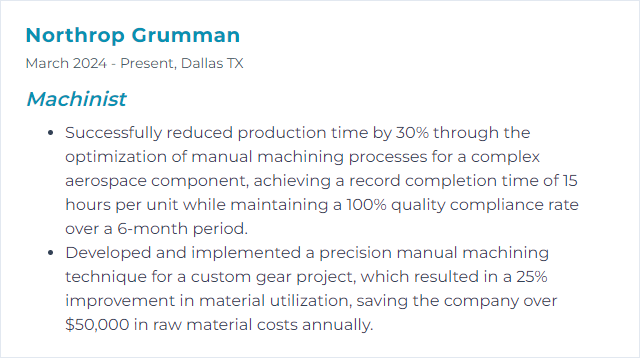
5. CAD/CAM Software
CAD/CAM software is a computer-aided design and manufacturing tool that enables machinists to design parts and create detailed, precise instructions for CNC machines to fabricate those parts.
Why It's Important
CAD/CAM software is crucial for machinists as it streamlines the design and manufacturing process, allowing for precise creation and modification of parts, efficient tool path generation, and reduced production time and material waste.
How to Improve CAD/CAM Software Skills
Improving CAD/CAM software, especially from a machinist's perspective, involves enhancing usability, accuracy, integration, and support. Here's a concise guide:
User-Friendly Interface: Simplify the user interface for ease of use. Offer customizable toolbars and workspaces. Autodesk provides examples of user-friendly design in their software.
Comprehensive Tutorials and Learning Resources: Include in-depth tutorials and accessible learning resources within the software. SolidWorks often integrates tutorials directly into their software suite.
Enhanced Simulation Capabilities: Improve simulation features to predict more accurately how designs will perform in real-world applications. ANSYS is known for its advanced simulation capabilities.
Better Integration with Machining Hardware: Ensure seamless integration with a wide range of CNC machines and 3D printers. This includes supporting a variety of file formats and machine languages. Mastercam excels in providing broad compatibility.
Advanced Toolpath Optimization: Implement smarter algorithms for toolpath optimization to reduce machining time and wear on tools. GibbsCAM offers advanced toolpath strategies.
Real-time Collaboration Tools: Integrate tools that enable real-time collaboration among team members, regardless of their location. Fusion 360 by Autodesk supports cloud-based collaboration.
Customizable Post-Processors: Offer an easily accessible library of customizable post-processors or the ability to easily edit and create new ones. CAMWorks provides flexible post-processing options.
Robust Technical Support: Provide responsive and knowledgeable technical support to assist with both software and machining challenges. PTC is known for strong customer support.
Continuous Updates and Feedback Loop: Regularly update the software based on user feedback and technological advancements. Establish a clear channel for users to submit feedback. Siemens NX demonstrates a commitment to continuous improvement.
Improving CAD/CAM software in these areas can significantly enhance the efficiency, effectiveness, and satisfaction of machinists and their workplaces.
How to Display CAD/CAM Software Skills on Your Resume
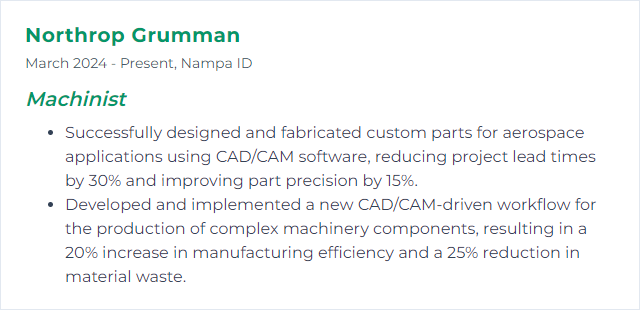
6. Lathe Operation
Lathe operation involves the process of machining a workpiece by rotating it against a cutting tool, allowing a machinist to shape, drill, cut, and perform various operations to produce cylindrical parts with precision.
Why It's Important
Lathe operation is crucial for a machinist as it enables precise shaping, cutting, and finishing of materials, essential for creating accurate and high-quality parts for various mechanical applications.
How to Improve Lathe Operation Skills
Improving lathe operation involves enhancing precision, safety, and efficiency. Here's a concise guide:
Proper Setup: Ensure the lathe is correctly installed, leveled, and that all components are in good condition. This foundational step is crucial for accurate machining. Read more on setup.
Tool Selection and Care: Use the right tooling for your material and operation. Keeping tools sharp and properly stored extends their life and improves performance. Tool selection guide.
Optimize Speed and Feed Rates: Adjust spindle speed and feed rate according to the material and the type of operation for optimal cutting conditions. Speeds and feeds calculator.
Use of Coolants: Proper use of coolants can improve tool life, surface finish, and dimensional accuracy. Selection of the right coolant depends on the material and operation. Coolant selection guide.
Regular Maintenance: Adhere to a maintenance schedule for the lathe to prevent wear and tear and ensure longevity. This includes lubrication, checking alignments, and replacing worn parts. Maintenance tips.
Operator Skill Development: Continuous learning and skill improvement through training and practice are vital. Understanding advanced techniques can significantly enhance operation efficiency. Training resources.
Safety Measures: Always follow safety guidelines to prevent accidents. This includes wearing appropriate protective gear, ensuring proper machine guarding, and keeping the work area clean. Safety tips.
By focusing on these areas, machinists can improve the performance and output of lathe operations effectively.
How to Display Lathe Operation Skills on Your Resume
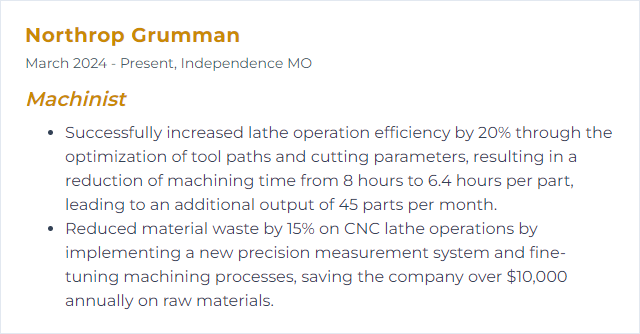
7. Milling Machine
A milling machine is a precision tool used for cutting and shaping solid materials like metal or wood. It operates by rotating a cutting tool against the workpiece, allowing machinists to perform a variety of operations such as drilling, tapping, slotting, and contouring with high accuracy.
Why It's Important
A milling machine is crucial for a machinist because it allows for the precise cutting and shaping of metal and other materials, enabling the creation of complex parts and components with high accuracy and efficiency.
How to Improve Milling Machine Skills
Improving a milling machine's performance and precision involves several key steps. Here's a concise guide for machinists:
- Regular Maintenance: Keep the machine clean and lubricated. This includes cleaning chips, checking for wear, and applying lubricant where needed.
- Upgrade Cutting Tools: Invest in high-quality cutting tools with appropriate coatings for the material being machined. Tool Selection Guide
- Use Proper Workholding: Ensure the workpiece is securely held using the right clamps, vises, or fixtures. This prevents movement during machining. Workholding Basics
- Optimize Speeds and Feeds: Adjust and experiment with your machine’s speed and feed rates for optimal performance based on material and tooling. Speeds and Feeds Calculator
- Implement CNC Software Updates: If your milling machine is CNC, keep the software updated for improvements in functionality and efficiency. CNC Software Updates
- Enhance Rigidity: Strengthen the machine's rigidity through additional supports or by upgrading components to reduce vibration and improve precision.
- Use Coolant Effectively: Proper application of coolant can improve tool life and finish. Choose the right coolant and delivery system for your operations. Coolant Management Guide
- Calibrate Regularly: Perform regular calibrations and alignments to ensure accuracy. This includes checking and adjusting the spindle, gibs, and ways.
By focusing on these areas, machinists can significantly improve the performance, accuracy, and longevity of their milling machines.
How to Display Milling Machine Skills on Your Resume
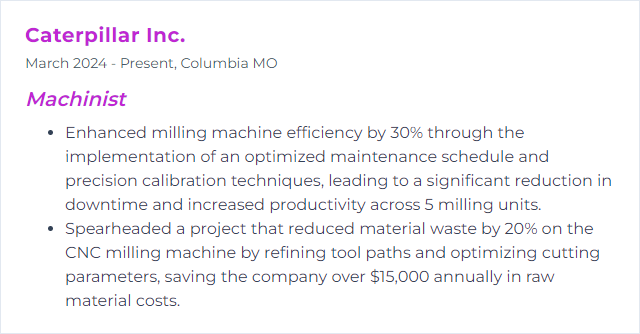
8. Grinding Techniques
Grinding techniques in a machinist context refer to the use of abrasive wheels to remove material from a workpiece, achieving high precision and surface finish. These techniques vary based on the type of grinding machine, workpiece material, and desired final dimensions or surface characteristics.
Why It's Important
Grinding techniques are crucial for a machinist because they ensure precision, surface finish, and dimensional accuracy of parts, enabling the creation of components with tight tolerances and smooth finishes essential for high-performance applications.
How to Improve Grinding Techniques Skills
Improving grinding techniques as a machinist involves several key strategies:
Understand Material Properties: Knowing the material you're working with helps select the right abrasive and grinding parameters. ASM International provides resources on material properties.
Select Proper Abrasives: Choose the right abrasive type and grit size for your workpiece material and desired finish. Norton Abrasives offers a selection guide for abrasives.
Optimize Grinding Parameters: Adjust speed, feed rate, and depth of cut according to the material and the grinding wheel. Machining Handbook provides guidelines on optimal parameters.
Maintain Equipment: Regularly inspect and maintain your grinding machine to ensure accuracy and efficiency. Grinding Technology has maintenance tips.
Use Coolants Effectively: Proper use of coolants can reduce heat and improve surface finish. The Coolant Management Guide offers advice on coolant selection and management.
Implement Dressing and Truing: Properly dress and true your grinding wheels to maintain sharpness and shape. Precision Surfacing Solutions explains dressing and truing techniques.
Adopt Safety Practices: Always follow safety guidelines to protect yourself and your workplace. OSHA outlines safety standards for abrasive wheel equipment grinders.
Focusing on these areas can significantly improve your grinding techniques and outcomes.
How to Display Grinding Techniques Skills on Your Resume
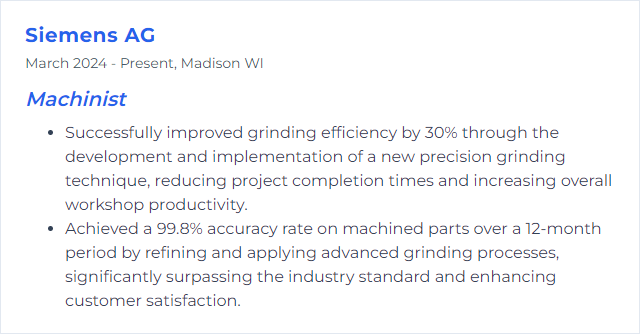
9. Quality Control
Quality Control (QC) for a machinist involves the processes and measures taken to ensure that manufactured parts or products meet defined specifications and standards, ensuring precision, accuracy, and functionality.
Why It's Important
Quality Control is crucial for a machinist to ensure that manufactured parts meet precise specifications and tolerances, reducing waste, enhancing safety, and maintaining customer satisfaction by delivering reliable and high-quality products.
How to Improve Quality Control Skills
Improving Quality Control as a machinist involves precise steps focused on accuracy, consistency, and continuous improvement. Here are key strategies:
Standardize Processes: Implement standardized procedures for tasks to ensure consistency. ISO standards can provide a framework for quality management systems.
Regular Calibration: Ensure all measuring instruments and machines are regularly calibrated to maintain accuracy in measurements.
Proper Training: Continuously train machinists on the latest machining techniques and quality control practices to enhance skills.
Use of Statistical Process Control (SPC): Employ SPC tools to monitor and control machining processes, detecting variations early.
Implement a Quality Management System (QMS): Adopt a QMS like ISO 9001, which focuses on meeting customer requirements and improving satisfaction.
Regular Audits and Inspections: Conduct regular quality audits to ensure adherence to quality standards and identify areas for improvement.
Feedback Loops: Establish mechanisms for collecting and analyzing feedback from both customers and the production floor to identify areas for quality improvements.
By focusing on these strategies, machinists can significantly enhance the quality control of their operations, leading to higher quality products and increased customer satisfaction.
How to Display Quality Control Skills on Your Resume
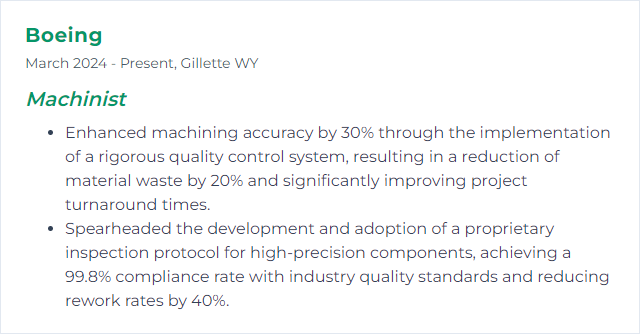
10. Mastercam
Mastercam is a computer-aided manufacturing (CAM) software used by machinists to create machining instructions for CNC machines, enabling precise control over cutting and shaping of materials.
Why It's Important
Mastercam is important for a machinist because it provides powerful and flexible computer-aided manufacturing (CAM) tools for efficiently programming CNC machines, reducing production time, and enhancing precision in machining complex parts.
How to Improve Mastercam Skills
Improving your proficiency in Mastercam as a machinist involves several strategies focused on enhancing both your technical skills and understanding of the software. Here are concise tips:
Understand the Basics: Start with mastering the fundamentals of Mastercam. Visit the Mastercam University for official courses.
Practice Regularly: Consistent practice is key. Utilize the Mastercam Demo/Home Learning Edition for free practice.
Stay Updated: Keep your Mastercam knowledge current by following the Mastercam Blog for updates and tips.
Join Forums: Engage with the Mastercam community in forums like the eMastercam Forum. Sharing experiences and solutions with peers can offer new insights.
Learn from Tutorials: Explore YouTube tutorials and channels dedicated to Mastercam training. Channels like Streamingteacher offer comprehensive guides.
Customize Mastercam: Tailor your workspace and toolbars in Mastercam for efficiency. Learn more about customization in the Mastercam Help Files.
Understand Your CNC Machinery: Deepen your understanding of the specific CNC machines you work with. This knowledge allows you to make more informed decisions when using Mastercam.
Incorporating these strategies into your learning routine will help you leverage Mastercam more effectively, enhancing your capabilities as a machinist.
How to Display Mastercam Skills on Your Resume
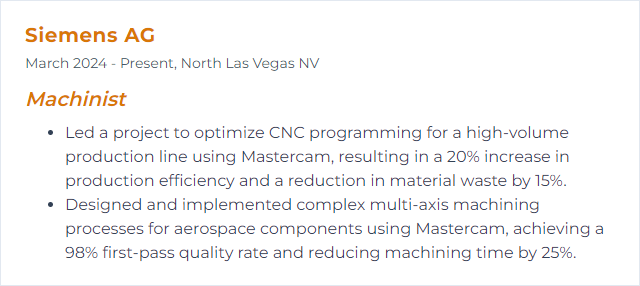
11. SolidWorks
SolidWorks is a computer-aided design (CAD) software used for creating 2D and 3D models, essential for machinists in designing, visualizing, and analyzing parts and assemblies before manufacturing.
Why It's Important
SolidWorks is important for machinists because it allows for precise 3D modeling and drafting of parts, enabling accurate fabrication, reducing errors, and streamlining the manufacturing process.
How to Improve SolidWorks Skills
Improving SolidWorks skills, especially for a machinist, focuses on mastering tools that enhance precision, efficiency, and the ability to generate machinable parts and assemblies. Below is a concise guide:
Learn SolidWorks CAM: Understanding SolidWorks CAM is crucial for machinists to bridge design and manufacturing. It helps in creating CNC machining instructions directly from your designs. SolidWorks CAM Tutorial.
Master 3D Sketching and Part Modeling: Enhance your ability to create complex shapes and designs that can be directly used for machining. 3D Sketching Tutorial.
Understand Assembly Creation: Knowing how to efficiently create assemblies can help in visualizing the final product and making necessary adjustments before machining. Assembly Creation Guide.
Utilize Design for Manufacturing (DFM) principles: Integrating DFM principles with SolidWorks design to ensure manufacturability, reducing production costs, and improving product quality. DFM in SolidWorks.
Practice with Real-world Projects: Applying your skills on real-world projects can significantly improve your proficiency. Look for online resources or community projects. GrabCAD Community offers numerous real-life project files for practice.
Get Certified: Earning a SolidWorks certification can not only validate your skills but also make you familiar with industry standards. SolidWorks Certification.
Use Online Forums and Resources: Engage with the SolidWorks community for tips, tricks, and troubleshooting. SolidWorks Forums are a great place to start.
Improving in SolidWorks as a machinist involves continuous learning and application of both basic and advanced features tailored to the needs of machining processes.
How to Display SolidWorks Skills on Your Resume
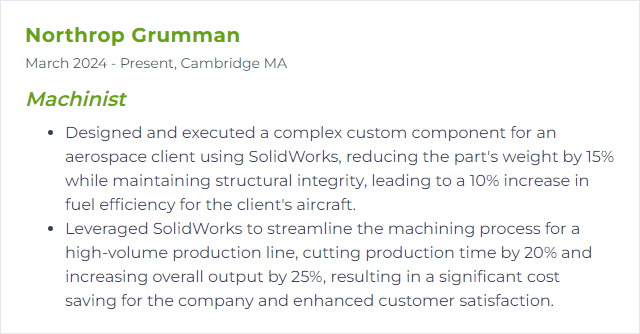
12. G-Code Interpretation
G-Code interpretation for a machinist involves reading and understanding the programmed instructions that control a CNC machine, detailing how to move, shape, or cut a material to create a desired part or component.
Why It's Important
G-Code interpretation is crucial for a machinist as it ensures the precise control and movement of machine tools, enabling the accurate production of parts and components according to specified designs.
How to Improve G-Code Interpretation Skills
Improving G-code interpretation involves understanding the syntax, commands, and structure of G-code to efficiently program CNC machines. Here are concise steps with resources to enhance your skills:
Learn the Basics: Start with understanding the foundational elements of G-code, including common commands and their functions. TITANS of CNC Academy offers free resources to get started.
Practice Regularly: Apply your knowledge by writing and editing G-code for various machining projects. Websites like NC Viewer allow you to visualize G-code in action, helping you catch errors and understand the toolpath.
Use Simulation Software: Before running your G-code on an actual machine, use simulation software to verify the code. CAMotics is an open-source option that can simulate 3-axis CNC machining.
Join Forums and Groups: Engage with communities on platforms like CNCZone or Reddit’s r/Machinists, where you can ask questions, share experiences, and get advice from experienced machinists.
Take Online Courses: Expand your knowledge by taking courses focused on CNC programming and G-code interpretation. Udemy and Coursera offer courses tailored to different levels of expertise.
Read Manuals and Books: Manufacturers often provide detailed manuals and documentation for their machines, which include specific G-code instructions. Books like "CNC Programming Handbook" by Peter Smid provide in-depth insights and practical examples.
By following these steps and utilizing the provided resources, you can significantly improve your G-code interpretation skills, enhancing your effectiveness as a machinist.
How to Display G-Code Interpretation Skills on Your Resume
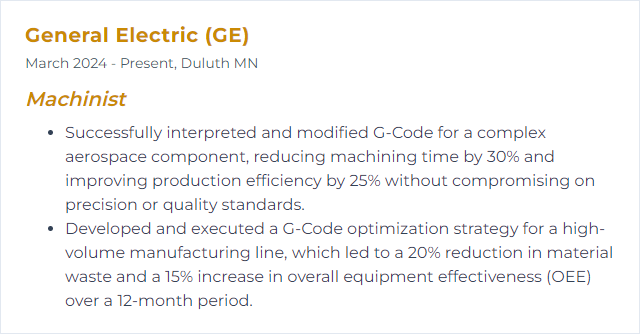